
книги / Новые конструкционные материалы низкоуглеродистые мартенситные и порошковые стали
..pdf№ |
Уравнение |
Значение параметров, |
||
п/п |
входящих в формулу |
|||
|
||||
4 По данным Г.М. Ждановича, |
0 - относительная |
пористость; Р - |
||
|
р = рк (вп - e g x i - e " ) , |
текущее давление; |
По - пористость |
|
|
* = i + A |
порошка в состоянии засыпки; Рк - |
||
|
давление, необходимое для получе |
|||
|
По |
ния компактного материала; п - по |
казатель степени
В табл. 5.2 представлены основные уравнения прессования. Их анализ показывает, что давление прессования зависит от ряда факторов: контакт ного давления при достижении в прессовке нулевой пористости, предела текучести материала частиц, предела прочности, коэффициента трения, модуля упругости, коэффициента Пуассона, геометрических размеров прессовки, хода пуансона в процессе прессования, модуля упругости мате риала порошка.
Простейшая пресс-форма состоит из матрицы, верхнего и нижнего пуансона. Порошок засыпают в матрицу между верхним и нижним пуан соном. Технические порошки характеризуются достаточно высокой под вижностью, занимают место между жидкостью и твердыми телами. Уже при засыпании порошка в форму поверхностные слои частиц воспринима ют контактную нагрузку.
Под контактной поверхностью имеют в виду ту часть общей внешней поверхности всех частиц порошка или брикета, которая характеризуется соприкосновением частиц между собой и через которую передается на пряжение. Контактная поверхность может быть измерена при помощи электросопротивления по формуле
где Su - номинальное сечение образца; SK- контактная поверхность в но минальном сечении образца; X - удельная электропроводность компактно го материала; Хк - контактная удельная электропроводность пористого тела.
Порошок под воздействием пуансонов растекается в стороны, созда вая давление, действующее на стенки пресс-формы. В результате взаимно го трения частиц, заклинивания и других факторов, затрудняющих боковое перемещение частиц, давление на стенки матрицы передается меньшее,
чем в направлении прессования. Между наружным слоем порошка и стен ками пресс-формы возникает таким образом трение, возрастающее с уве личением бокового давления прессования. В результате сил трения образу ется значительный перепад давления по высоте орикета. Трение возникает также между порошком и поверхностью пуансонов.
В теории прессования существуют два основных направления вывода основного уравнения прессования, связывающего давление и плотность. Первое решает задачу элементарным путем, во многих случаях с помощью достаточно простых уравнений. Второе направление характеризуется большей математической точностью и физической обоснованностью ре шения. Однако математические зависимости здесь очень сложные и не всегда приводят к практическим результатам. К этому направлению отно сятся теории, основанные на изучении контактных явлений при взаимо действии частиц. Первые уравнения зависимости плотности от давления прессования предложены М.Ю. Балыниным (см. табл. 5.2). Для идеального процесса прессования уравнение имеет вид:
Р$т = -Ртах = Рк = const. |
(5-2) |
в практике прессования это уравнение применяют чаще других.
Боковое давление. Коэффициент бокового давления представляет со бой отношение бокового давления (Рбок) к давлению прессования (Л>сев)’
6 = / W Росев- |
(5-3) |
В общем случае е характеризует пластичность уплотняемого мате риала.
Трение. Различают трение внешнее и межчастичное. Потери давления на преодоление сил трения между частицами порошков и стенками прессформы могут составлять 60-90 %. Внешнее трение определяет усилие, не обходимое для выталкивания брикета, оно обычно составляет 0,2-0,35 от давления прессования и тем больше, чем выше брикет и меньше площадь его поперечного сечения.
5.3. Особенности спекания железных и легированных порошков
Спекание заключается в нагреве исходной порошковой массы или прессовки в защитной атмосфере до температуры, не превышающей тем пературу точки плавления основного компонента. В практике ПМ имеются еще два главных вида спекания. При горячем прессовании порошковая масса или прессовка подвергается воздействию как повышенной темпера туры, так и внешнего давления: в данном случае температура также оста ется ниже температуры точки плавления материала. Этот метод широко
используют для получения керамических материалов и тугоплавких ме таллов, но редко - для получения изделий на основе железного порошка. Обычно при спекании материал находится в твердом состоянии, т.е. рас плавленная или жидкая фаза отсутствует. При жидкофазном спекании температура спекания достаточно высока, чтобы один или более компо нентов материала присутствовали в виде жидкости в течение всего процес са спекания или его части. К этому виду спекания относится пропитка ме талла жидкостью в сочетании со спеканием: массу металла с более низкой температурой плавления расплавляют, и металл затекает в поры неспеченной прессовки. Жидкофазное спекание обеспечивает достижение высоких плотностей материала в спеченном состоянии. Однако пропитка позволяет уплотнить материал без какой-либо усадки исходной прессовки: поры за полняются пропитывающей жидкостью. В большинстве других случаев уплотнение означает усадку, обусловленную устранением пористости.
Движущие силы спекания. Избыток поверхностной энергии приво дит в действие термодинамическую силу, обеспечивающую перенос веще ства в процессе спекания, что уменьшает общую межфазную энергию.
Изменение свободной поверхностной энергии (d£) в том случае, когда система частиц теряет площадь поверхности в размере dS, выражается уравнением
dE = ydS, |
(5.4) |
где у - поверхностное натяжение.
Изменение объема dV в процессе изменения &Е описывается уравнением
dE ydS _ П |
+ 0 = 1 |
(5.5) |
|
d V ~ dV ” V i |
+ r2 J ” Y Л ’ |
||
|
где r\ и Г2 - радиусы кривизны; R - радиус кривизны шейки.
Установив, что R > 0 для выпуклой поверхности и R < 0 для вогнутой поверхности, можно отметить следующее:
а) если заполняется вогнутая поверхность, то свободная энергия сис
темы уменьшается; |
|
б) если поток массы направлен на выпуклую |
поверхность, то сво |
бодная энергия системы увеличивается. |
|
Поскольку dE/dV соответствует давлению сжатия а, уравнение (5.5) |
|
примет вид |
|
cr = Y-jr. |
(5.6) |
R |
|
Следовательно, под вогнутой поверхностью действуют силы растяже ния (о < 0), а под выпуклой поверхностью - силы сжатия (а > 0).
Итак, вещество переносится на вогнутую поверхность с выпуклой для уменьшения свободной энергии.
Консолидация порошкового материала начинается на стадии прессо вания, а структура и свойства формируются в процессе спекания.
Теория рассматривает шесть возможных механизмов увеличения площади контакта между частицами, при этом во всех случаях площадь контакта в степени п = 2 ... 7 пропорциональна продолжительности спека ния [4, 5, 6]. В качестве модели используют схему спекания двух сфериче ских частиц. Различают следующие механизмы роста площади контакта между сферическими крупинками: вязкого течения; объемной диффузии, при котором стоком избыточных вакансии является выпуклая поверхность крупинок; объемной диффузии, при котором стоком избыточных вакансий служит граница или дислокации; поверхностной диффузии; переноса ве щества через газовую фазу; граничной диффузии [5].
При реализации механизма вязкого течения, описываемого законом Френкеля [4], происходит кооперативное перемещение молекул вещества в
зону контакта, сопровождающееся сближением центров частиц: |
|
х 2 |
(5.7) |
где У] - коэффициент вязкости спекаемого материала (пропорционален ко эффициенту диффузии); у - поверхностное натяжение или свободная по верхностная энергия; t - продолжительность спекания; г - радиус сфериче ской частицы; х - радиус зоны контакта.
При спекании кристаллических материалов сжатые области (выпук лые поверхности) действуют как стоки вакансий, а вогнутые - как источ ники. В случае миграции атомов путем объёмной диффузии рост контак тов подчиняется установленному Кучинским закону:
кТ
где D - коэффициент объёмной диффузии; VQ- объем вакансий; к - посто янная Больцмана; Т- температура, К.
Когда атомы мигрируют в площадь контакта по механизму объёмной диффузии, то происходит сближение центров частиц, и тогда х5 - г, если стоком вакансий является граница зерна, то показатель степени п = 4 [4]. Сток атомов по механизму поверхностной диффузии от выпуклых участ ков к вогнутым не сопровождается сближением центров частиц, при реа лизации этого механизма п = 7 [4, 5, 6]. Если вещество переносится через газовую фазу (х5 ~ г), то сближения центров при этом не происходит. При-
пекание частиц под действием внешнего давления приводит к сближению их центров (п = 4) [4].
В реальных материалах рост площади и числа межчастичных контак тов совпадает во времени с рекристаллизацией, гомогенизацией, усадкой и другими процессами формирования структуры. Объемная деформация частиц под действием силы поверхностного натяжения вызывает усадку
прессовок, кинетику которой отражает уравнение Ивенсена [7]: |
|
V = V0(qmt + \)~Х/т, |
(5.9) |
где V- объем пор через время t; VQ- начальный объём пор; q - |
начальная |
относительная скорость сокращения объёма пор в момент начала изотер мической выдержки; т - параметр, характеризующий интенсивность паде ния скорости сокращения объёма пор.
С увеличением площади и числа межчастичных контактов зерна на чинают прорастать из одной частицы в другую до образования зерен неко торого среднего размера, при этом окислы, метастабильные фазы, поры и включения препятствуют росту зерен аустенита. Особенно сильно замед ляют рост зерна включения и поры неправильной формы [6], поэтому зер но порошковых сталей намного меньше, чем традиционных.
Неравновесные составляющие структуры наряду с порами являются концентраторами напряжения, они повышают общий уровень термических и структурных напряжений в материалах, так как их физические характе ристики существенно отличаются от свойств твердых растворов на основе железа.
В работе [8] сопоставлены результаты исследований различных вари антов исходного состояния структуры. Образцы получали напяливанием порошка из закаленной стали и последующим прессованием. Такой способ обеспечивает высокую концентрацию дефектов в связи с разветвленно стью поверхности частиц, неравномерностью деформаций, содержанием избыточных вакансий. Независимо от предшествующей термообработки кинетика образования аустенита существенно отличалась от кинетики а -> у-превращения образцов, изготовленных без применения напялива ния. Влияние дефектов прежде всего проявлялось в ускорении образования аустенита и последующем распаде (J = 750 °С).
Повышенная дефектность прессовки существенно ускоряет спекание. Дислокационные структуры в диффузионной зоне формируются вследст вие релаксации напряжений и перемещения их с поверхности образца в его объем. В процессе спекания многокомпонентных композиций дислокации несоответствия следуют за изоконцентрационными поверхностями, спо собствуя релаксации напряжений, что вызывает рост эффективного коэф фициента объемной диффузии и может служить причиной ускорения го
могенизации. Заметные изменения коэффициента диффузии наблюдаются при плотности дислокации примерно 10 0 см”2 [5].
Возможность активирования процесса спекания вследствие появления избыточных вакансий (из-за различия парциальных коэффициентов диф фузии компонентов) доказана экспериментально. Опыты со смесями по рошков медь - никель, хром - молибден, хром - вольфрам показали, что локальное разрыхление структуры из-за концентрации избыточных вакан сий в диффузионной зоне способствует ускорению переноса вещества только в первый час отжига. Примером практичного использования этого эффекта является введение легирующих элементов в состав химических соединений, разлагаемых на стадии спекания [5], что ускоряет усадку и гомогенизацию материалов.
Взаимодействие элементов структуры металла в процессе спекания приводит к тому, что неоднородная плотность чаще всего способствует ус корению массопереноса и гомогенизации за счет увеличения эффективного коэффициента диффузии, а отличие парциальных коэффициентов диффу зии компонентов вызывает, в свою очередь, образование новых пор (эф фект Френкеля) и трансформацию пористой структуры. Диффузионная го могенизация может сопровождаться как ускорением усадки, так и замед лением. В зависимости от уровня пористости и концентрационной неодно родности при охлаждении стали с температуры спекания или после термо обработки формируется структура материала, определяющая его свойства. Высокая негомогенность структуры порошковых поликомпонентных ста лей сохраняется даже при их длительном спекании, горячей или холодной штамповке и последующей продолжительной гомогенизации [9]. Поэтому важное практическое значение имеет выбор технологических процессов и легирующих элементов, обеспечивающих наибольшую однородность структуры сталей.
Рассмотрим далее влияние основных легирующих элементов на фор мирование структуры и свойств порошковых сталей.
Наиболее широко в качестве легирующего элемента порошковых ста лей используют медь (до 20 %). При содержании 1,5-3 % медь компенси рует усадку брикетов. Это позволяет получать детали сложной формы, для изготовления которых требуется калибровка или допрессовка с использо ванием одного и того же инструмента [10, 11]. Аномальные изменения объема брикета, содержащего медь, объясняются проникновением рас плавленной меди по благоприятно ориентированным границам кристалли тов. Растворяясь, медь увеличивает объем частиц вещества, что приводит к увеличению объема заготовки [10, 12, 13].
Повышение концентрации меди от 1 до 7 % при содержании углерода примерно 0,5 % (оптимальное для конструкционных порошковых сталей) [2, 14] вызывает монотонный рост прочности и понижение пластичности, а
при содержании меди выше 7 % снижается и прочность. Ударная вязкость монотонно понижается при увеличении содержания меди [15] во всем ин тервале ее концентраций, используемых для легирования конструкцион ных сталей.
Другим распространенным легирующим элементом является никель. Сохраняя или даже увеличивая уровень прочности и облегчая термообра ботку, никель повышает пластичность и ударную вязкость спеченного ма териала [16]. Благодаря небольшому сродству никеля и кислорода, пригод ные для спекания железа среды успешно применяют и для спекания желе зоникелевых сплавов. В одном из исследований показано, что электроли тический порошок железа, легированного 5 % никеля, спрессованный при 550 МПа и спеченный при 1300 °С в течение 1 ч, имел предел прочности 380 МПа и относительное удлинение 22 %, а без присадок никеля механи ческие свойства были 330 МПа и 10 % соответственно [16]. Большое влия ние на формирование структуры и свойств оказывает не только содержа ние легирующего элемента, но и размер, форма и способ получения частиц порошка основного компонента и легирующей присадки [10,13]. Из элек тролитического, карбонильного и восстановленного порошков никеля предпочтительно использовать два последних. Переход от электролитиче ского никеля к восстановленому приводит к повышению предела прочно сти в 1 ,1-1,3 раза, относительного удлинения в 2 ,0- 2 ,5 раза, ударной вяз кости более чем в 1,5 раза [17].
При концентрациях до 3-4 % влияние никеля на свойства порошко вых сталей неоднозначно. Например, выявлено снижение механических характеристик термообработанных хромоникельмолибденовых сталей при увеличении концентрации никеля от 1 до 3 % [2]. При легировании тради ционных материалов этого не наблюдается. Такой эффект могут объяснить только данные исследования структуры и концентрационной неоднород ности распределения легирующих элементов. Так, распад негомогенного переохлажденного аустенита приводит к образованию структурных со ставляющих, существенно отличающихся по прочности и разрушающей деформации, что негативно сказывается на физико-механических свойст вах стали [18]. При дальнейшем увеличении концентрации никеля до 5-6 % неоднородность его распределения оказывает меньшее влияние, так как концентрация никеля становится, по-видимому, достаточной для пре вращения аустенита в мартенсит во всех микрообъемах. При концентраци ях никеля 3,5-4,0 % крутой участок зависимости упрочнения феррита сме няется пологим [19]. Это свидетельствует о том, что относительная невы сокая неоднородность распределения слабо влияет на свойства стали (со держание никеля в карбидной фазе 1,0-1,3 % [20]). Следовательно, при ле гировании активным карбонильным никелем, способствующим ускорению усадки, сталь может не уступать по свойствам материалам из легирован
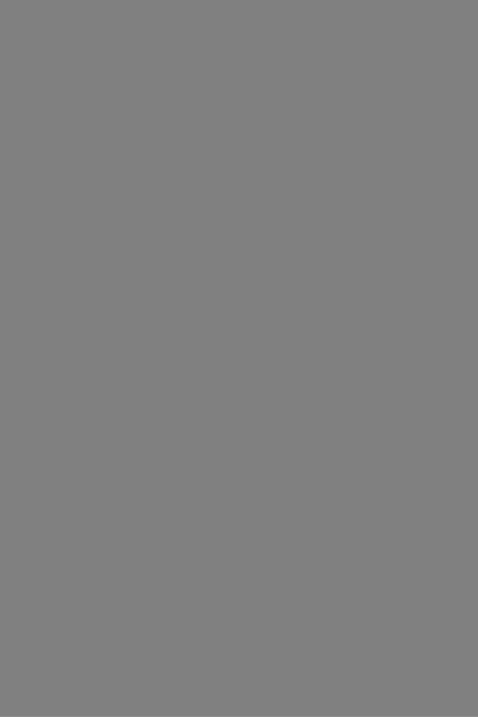
(Fe,Cr)7C3, обладающий исключительно устойчивостью к растворению в аустените.
Спеченные стали с концентрацией хрома до 3 % содержат карбидную фазу (Fe,Cr)3C, а при 5 % - (Fe,Cr)3C, (Fe,Cr)23C6, (Fe,Cr)7C3. Хромсодер жащие карбиды образуются уже при 900-950 °С, а карбиды молибдена при температурах выше 1100 °С [20, 23]. Взаимодействие между компонентами сталей, включающих в себя карбиды хрома и молибдена, начинается при 900-950 °С и протекает более интенсивно, чем в сталях, легированных од ним хромом и молибденом. Молибден и хром в отдельности выклинивают у-фазу, а углерод растворяется в Of-фазе очень незначительно, поэтому слой о^-фазы, образующейся вокруг частиц карбидов хрома или молибдена, за трудняет диффузию углерода и препятствует растворению карбидов. Со вместная диффузия в сталь хрома и молибдена расширяет и стабилизирует у-фазу, что приводит к более интенсивному растворению карбидов. По этому совместное легирование порошковой стали хромом и молибденом способствует получению гомогенной структуры [23, 24] и позволяет ис пользовать порошок хрома, это значительно удешевляет сталь.
Кремний является недефицитным и дешевым легирующим элементом. Он сильно повышает прочность стали, а его малые присадки не уменьша ют ударную вязкость. Однако близкую к критической концентрацию кремния может содержать уже порошок железа. Кроме того, у кремния большое сродство к кислороду и порошковые стали трудно получить из композиций из-за сложности их спекания.
Наибольший эффект достигают, используя порошки сплавов. Их по лучают методом распыления и диффузионного насыщения, однако из-за отсутствия промышленного производства порошков, легированных крем нием, конструкционные стали продолжают изготовлять из смесей метал лических порошков. Важной особенностью легирования кремнием являет ся большая разница между его коэффициентом диффузии в железе и коэф фициентом самодиффузии железа. В результате области с повышенным содержанием кремния окаймлены порами. Наряду с этим даже двухчасо вое спекание при 1200 °С не может обеспечить однородного распределе ния кремния, его концентрация внутри контура в 5-10 раз превышает кон центрацию за пределами контура [12 ].
Широкое применение кремний нашел благодаря графитизирующему воздействию в антифрикционных материалах [13]. Порошковые стали имеют пониженные пластические свойства. Введение кремния повышает их прочность, но еще более понижает пластичность.
Таким образом, дополнительное легирование кремнием не приводит к повышению физико-механических свойств стали, но примеси кремния в порошковым железе оказывают положительное влияние на ее свойства.
В качестве легирующего элемента сталей широко применяют марга нец. В порошках технического железа содержание марганца достигает 0,7 %. В 3 %-й марганцовистой стали количество марганца в карбиде при мерно 16 % [20]. При содержании до 3 % марганец упрочняет феррит сла бее, чем никель, а при содержании 3 % - сильнее. Максимальное значение ударной вязкости достигается при содержании марганца в феррите, близ ком к 1 %, но затем ударная вязкость резко понижается и при концентра ции марганца около 1,5 % соответствует ударной вязкости нелегированно го феррита. Легирование 5%-й никелевой стали дополнительно 0,5 % С и 0,5 % Мп приводит к росту ее прочности с 370 до 550 МПа и одновремен ному уменьшению пластичности с 22 % до 8 % [10]. При увеличении со держания марганца с 2 до 6 % происходит почти двукратный рост прочно сти и понижение пластичности в 2,5 раза. Замена в низколегированных по рошковых сталях никеля марганцем незначительно увеличивает проч ность, но при этом пластичность и ударная вязкость уменьшаются в 1,5— 2,0 раза, поэтому легирование никелем предпочтительнее, чем марганцем.
Вместе с тем примеси марганца, содержащиеся в порошке технического железа, благоприятно влияют на свойства стали.
Анализ влияния легирующих элементов на свойства порошковых ста лей показывает, что высокие механические свойства имеют стали, легиро ванные хромом, никелем и молибденом. При выборе композиций необхо димо также учитывать факторы, влияющие на прессуемость брикетов на стадии их формования, и возможности образования диффузионной порис тости и труднорастворимых соединений при спекании. Поэтому в шихту предпочтительно вводить компоненты, имеющие близкие по величине парциальные коэффициенты диффузии, не образующие термодинамически устойчивые фазы и обеспечивающие достаточную для получения заданной пористости прессуемость шихты.
Пористость конструкционного материала выбирают в зависимости от условий эксплуатации; регулируя плотность, получают детали оптималь ной массы с заданным запасом прочности. Так как пористость - важней шая структурная характеристика, то ее влияние на все физико механические свойства изучено наиболее полно. Прочность материалов малой и средней пористости и их физические константы: электросопро тивление, теплопроводность, модуль упругости и другие, чаще всего опи сывают эмпирическим выражением [25,26, 27]
Х = Хк(1- П)т, |
(5.10) |
где Х и Х к - свойства пористого и компактного материала соответственно; П - пористость; т - показатель степени. В узком интервале изменения по ристости используют зависимость