
книги / Новые конструкционные материалы низкоуглеродистые мартенситные и порошковые стали
..pdfКонтрольные вопросы к главе 7
1. Основные методы улучшения эксплуатационных характеристик по рошковых материалов.
2. Структура и свойства порошковых сталей после горячей штампов
ки.
3.Особенности легирования, технология получения, структура и свойства порошковых мартенситно-стареющих сталей.
4.Применение ВТМО для порошковых сталей.
5.Новые технологические процессы массового производства (теплое
прессование, спекание в a -фазе, высокоскоростное прессование).
6. Новые технологические процессы мелкосерийного и серийного производства (Синта-Фодж, ROC, САР, Лус-Пэк).
7. Получение, структура и свойства мартенситно-бейнитных концен трационно-неоднородных сталей.
8. Получение, структура и свойства метастабильных аустенитных концентрационно-неоднородных сталей.
9. Композиционные материалы на основе тристалей.
Список литературы к главе 7
1. Hayens R Development of sintered low alloy steels // Powder Met. 1989. Vol. 32, № 2. P. 140-146.
2.Железные и стальные порошки для спеченных изделий: Проспект фирмы Хегенас. Швеция. 1990. 21 с.
3.Клименко В.И. Никель-молибденовая сталь марки Н2М на основе частично-легированного порошка / В.И. Клименко, С.Г. Напара-Волгина, А.Н. Костырко // Порошковая металлургия. 1994. № 1/2. С. 31-35.
4.Волчек А.Я. Структура и свойства порошковой медь-никель- молибденовой стали / А.Я. Волчек, Н.П. Гребнев, Л.Я. Воронецкая // По рошковая металлургия. Минск: Высш. шк., 1992. Вып. 16. С. 11-14.
5.Дорофеев Ю.Г. Влияние добавок карбонильного порошка железа на
свойства материалов, полученных методом ДТП / Ю.Г. Дорофеев, А.Г. Мариненко, В.Н. Устименко // Порошковая металлургия. 1990. № 6. С. 8-12.
6. Dilfic fovecast // Powder Metall. 1992. Vol. 25. № 4. P. 259-260.
7. Формирование структуры и свойств мартенситно-стареющих по рошковых сталей, полученных экструзией / С.Г. Агбалян, Б.Ф. Бадеян, С.А. Ассила и др. //Порошковая металлургия. 1994. № 1 1/12. С. 85.
8. Получение порошков мартенситно-стареющих сталей / С.Г. Агбалян, Б.Ф. Бадеян, Р.Г. Самвелян и др. // Порошковая металлургия. 1994.
№9/10. С. 86-93.
9.Анциферов В.Н. Спеченные мартенситно-стареющие стали / В.Н. Анциферов, Ю.М. Колбенев. Пермь, 1975. 53 с.
10.Низколегированные порошковые стали, полученные по металло оксидной технологии / С.Г. Агбалян, Б.Ф. Бадеян, С.А. Ассила и др. // По рошковая металлургия. 1995. № 1/2 . С. 5-11.
11 . Iandeska W.T. Strenth and ductility enhercement of low temperature // SAE Techn. Pap. Ser., 1982. № 820232. 7 p.
12.Rueckl R.U. The loos-pack PM process // Intern. J. Powder Metall and Powder Technol. 1975. Vol. 11. № 3. P. 209-220.
13.Новое в технологии получения материалов / Под ред. Ю.А. Осипяна и А. Хауффа. М.: Машиностроение. 1990. 448 с.
14.Dennis М. Hoegenas unveils higher green strength powder family // MPR. 1997. №9. P. 26-27.
15.Engstrom U. Properties and Tolerances of Warm Compacted High Density PM Steels / U. Engstrom, B. Johansson, S. Andersson // Euro PM97 Mechanical Properties. 1997. P. 265-272.
16. Effects of sintering parameters on the mechanical properties of a Fe- 2Cu-2Ni-0.9 M0-O.8C steel / C.N. Degoix, A. Griffo, R.M. German // Int.
J.Powder Met. 1998. Vol. 34, № 6. P. 57-62, 64-67.
17.Пат. 716744 Япония. МПК6 В 32 F S/12. Method for producing fer rous sintered alloy having quenched structure.
18.Lasday S.B. Improved properties of 718 alloy faskioned by P/m process and breat treatment // Industrial Heating. 1982. Vol. 49. June. P. 22-26.
19.Svilar M. / High impact strengh copper infiltrated PM Steels / M. Svilar, D. Berry, E. Klar // Metall Powder Report, 1987. № 4. P. 278-282.
20.Шацов A.A. Оптимизация состава и режима термообработки ком позиционного материала сталь - медь // Известия вузов. Цветная метал лургия. 1998. № 5. С. 52-56.
21.Структурная наследственность порошковых сталей / В.Н. Анцифе ров, Н.Н. Масленников, С.Н. Пещеренко и др. / Перм. гос. техн. ун-т. Пермь, 1996. 122 с.
22.Порошковая металлургия сталей и сплавов / Ж.И. Дзнеладзе,
Р.П. Щеголева, Л.С. Голубева и др. М.: Металлургия, 1978. 264 с.
23.Tracey V.A. Nickel sintered steels. Development, status and prospects
//Adv. Powder Met. and Particul. Mater.: World Congress. San Francisco. June 21-26. 1992. Vol. 5. Princeton (N.J). 1992. P. 227-237.
24.Microstructure-property relationship of a high strength sintered steel / H. Danninger, D. Spoljaric, B. Weiss, I. Preitfellrer // Adv. Powder Met and Par-
ticul. Mater.: World Congr. San Francisco. June 21-26, 1992. Vol. 5. Princeton (N.J), 1992. P. 227-237.
25.Низколегированные порошковые стали, полученные по металло оксидной технологии / С.Г. Агбалян, С.А. Ассила, Н.Н. Манукян и др. // Порошковая металлургия. 1995. № 1/2 . С. 5-11.
26.Masazum Н. Development of ultrahigh strength sintered steel / H. Masazum, M. Naok, H. Tadatoshi // Adv. Powder Met. and Particul. Mater.: World Congr. San Francisco. June 21-26. 1992. Vol. 5 Princeton (N.J.). 1992. P. 215— 226.
27.Lindbera C. Sintered high strength materials / C. Lindbera, U. Engstrom, P. Engdabe // Adv.:Proc. Powder Met. and Particul Mater.: Proc. Powder Met. World Congr., San Francisco, Calif. June 21-26, 1992. Vol. 5.Princeton (N.J.). 1992. P. 107-114.
28.Влияние структуры на трещиностойкость стали СП50ХЗНМ / В.Н. Анциферов, Н.Н. Масленников, А.А. Шацов, В.Б. Платонова // МиТОМ. 1991. № 8. С. 32-34.
29.Furukimi О. Ultrahigh strength ferrous sintered component / О. Furukimi, K. Yano, S. Takajo // Int. J. Powder Met. 1991. Vol. 27. № 4. P. 331-
337.
30. Takajo S. Obtaing high strength steel powder/ / MRP. № 7/8. 1991.
P.33.
31.Анциферов В.Н. Особенности трип-эффекта в порошковых кон центрационно-неоднородных сталях с невысоким содержанием никеля /
B.Н. Анциферов, М.Г. Латыпов, А.А. Шацов // МиТОМ. 1997. № 8.
C.15-19.
32.Коршунов Л.Г. Контактная прочность металлических сплавов.
Свердловск: Изд-во УПИ, 1972. С. 72-85
33.Филиппов М.А. Стали с метастабильным аустенитом / М.А. Фи липпов, В.С. Литвинов, Ю.Р. Немировский. М.: Металлургия, 1988. 256 с.
34.Влияние углерода на деформационное упрочнение и износостой кость литых марганцевых аустенитных сталей / Л.Г. Коршунов, Ю.И. Аве рин, В.Е. Луговых и др. // Термическая обработка и физика металлов: Тр.
вузов РСФСР. Пермь, 1977. С. 24-30.
35.Литвинов В.С. Анализ перераспределения атомов компонентов хромомарганцевой стали методами мессбауэровской спектроскопии и по левой ионной микроскопии / В.С. Литвинов, М.Е. Попцов, В.А. Ивченко // ФММ. 1986. Т. 61. Вып. 2. С. 361-364.
36.Влияние мартенситного у-а-превращения на кинетику упрочнения
исопротивление разрушению поверхности трения аустенитных сталей при полидеформационном характере изнашивания / Л.Г. Коршунов, И.Н. Бога чев, Ю.И. Аверин и др. // ФММ. 1980. Т. 49. Вып. 1. С. 113-120.
37. Износостойкие стали с нестабильным аустенитом для деталей га зопромыслового оборудования / В.Н. Виноградов, Л.С. Лифшиц, С.Н. Пла това и др. // Вестник машиностроения. 1982. № 1. С. 26-29.
38.ПотакЯ.М. Высокопрочные стали. М.: Металлургия, 1972. 208 с.
39.Малинов Л.С. Абразивная износостойкость высокоуглеродистых марганцево-ванадиевых сталей / Л.С. Малинов, Е.Я. Харланова, Е.Л. Малинова // МиТОМ. 1993. № 2. С. 25-23.
40.Дорохов В.В. Абразивная износостойкость высокоуглеродистой хромоникелевой стали / В.В. Дорохов, И.В. Киселева, А.А. Рыжиков // МиТОМ. 1993. № 2. С. 30-33.
41.Характеристики легированных стальных порошков KIP
SIGMALOY 2010 для ультравысокопрочных спеченных материалов и ме ханизм их упрочнения / F. Osami, М. Kerichi, М. Yoshiaki И Kawasaki Steel Giho. 1992. Vol. 24, № 4. С. 273-278. (Цитируется по: Металлургия, РЖ, 1993. № 6. Реферат Е55).
42. Порошковая сталь со структурой метастабильного аустенита / В.Н. Анциферов, Н.Н. Масленников, А.А. Шацов, Т.В. Смышляева // Порошко вая металлургия. 1994. № 3/4. С. 42-47.
43.Шацов А.А. Инфильтрированные медью карбидостали со струк турно-неустойчивой матрицей / А.А. Шацов, Т.В. Смышляева // Трение и износ. 1998. Т. 19. № 1. С. 109-115.
44.Анциферов В.Н. Высокопрочные трещиностойкие концентраци онно-неоднородные порошковые никелевые стали / В.Н. Анциферов, М.Г. Латыпов, А.А. Шацов // МиТОМ. 1999. № 11. С. 28-32.
45.Анциферов В.Н. Ферротики с метастабильной матрицей / В.Н. Ан циферов, М.Г. Латыпов, А.А. Шацов // Трение и износ. 1996. Т. 17. № 5.
С.644-652.
46.Масленников Н.Н. Карбидостали с повышенной трещиностойко-
стью / Н.Н. Масленников, М.Г.Латыпов, А.А. Шацов // МиТОМ. 1993. № 8.
С.20-23.
47.Пат. 2120352 РФ, 6 В 22 F 7/04, 3/26. Способ соединения деталей из порошковых материалов/ В.Н. Анциферов, А.А. Шацов, Т.В. Смышляе
ва и др.
48.Capus J. М. PM shakes claims in the automotive world // Metal Powder Report. 2002. № 5. P. 24-25.
49.Анциферов В.Н. Усталостное и ударное разрушение порошковых
концентрационно-неоднородных никелевых сталей / В.Н. Анциферов, М.Г. Латыпов, А.А. Шацов // МиТОМ. 2001. № 6. С. 29-34.
50. Анциферов В.Н. Термическая и термомеханическая обработка концентрационно-неоднородных трипсталей / В.Н. Анциферов, М.Г. Ла тыпов, А.А. Шацов // МиТОМ. № 9. 2002. С. 20-23.
51. Skoglund P. High Density PM Components by High Velocity Compac tion / P. Skoglund, M. Kejzelman, I. Hauer. // Proceeding of the 2002 World Congress on Powder Metallurgy & Particulate Materials. June 16-21. Orlando, 2002. Vol. 4. P. 85-95.
52. High Velocity Compaction / P. Doremus, F. Duwa, p. Francois et al. // Proceeding of the 2002 World Congress on Powder Metallurgy & Particulate Materials. June 16-21. Orlando, 2002. Vol. 4. P. 96-110.
8. ПЕРСПЕКТИВЫ ПРИМЕНЕНИЯ ТВЕРДЫХ СПЛАВОВ
Твердые сплавы были изобретены К. Шротером в 1923 г. в Германии [1, 2]. С того времени и по сей день они находятся в центре внимания ма териаловедов. Так, на Международном конгрессе по порошковой метал лургии (декабрь 1998 г.) две первые награды Европейской ассоциации по рошковой металлургии (ЕРМА) были вручены за разработки в области карбидсодержащих материалов [3]. К моменту изобретения сплавы систе мы WC-Co были вторым (после стали Гатфильда) материалом, находя щимся в структурно-неустойчивом состоянии, и в настоящее время они яв ляются одним из первых материалов с нанокристаллической структурой. Исходные компоненты твердых сплавов с нанофазной структурой обычно получают по золь-гель-технологии. В научной литературе обсуждают два пути реализации наноструктуры: введение ингибиторов, замедляющих рост зерен (для WC - Со это главным образом карбиды ванадия и хрома), и низкотемпературное спекание с приложением давления, при этом возмо жен одновременный синтез алмазов. По-видимому, структурно градиентные материалы WC - Со - алмаз станут самыми износостойкими промышленными материалами ближайшего будущего.
Первое внедрение твердых сплавов осуществлено Ф. Круппом в 1927 г., торговая марка «Widia» (wie Diamant - как алмаз). Первоначальное применение материалов системы WC - Со связано с инструментом для протяжки проволоки и износостойкими деталями. Только после исследо вания роли карбида вольфрама в формировании структуры и свойств твер дых сплавов совершен прорыв в области создания режущего инструмента на базе системы карбид вольфрама - кобальт. В современном машино строении 80 % твердых сплавов используют для изготовления режущего инструмента, который существенно превосходит любой известный инст румент из быстрорежущих сталей, но при этом доля режущего инструмен та из твердых карбидовольфрамовых сплавов среди других видов инстру мента составляет всего 3 % [5].
Несмотря на столь длительный период промышленного использова ния композитов WC - Со, еще и сегодня не ясны все причины их высокой прочности и все материалы, созданные на основе карбида или карбонит-
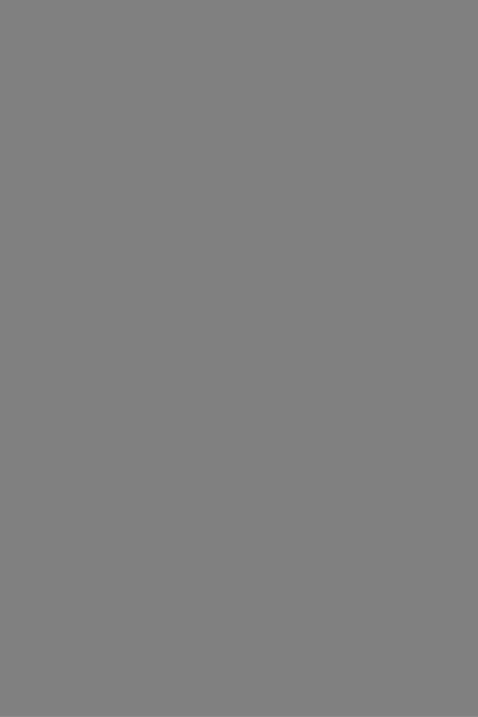
- формование деталей в стальных пресс-формах при давлении 50-
200МПа;
-предварительное спекание (выжигание пластификатора) деталей при температуре порядка 900 °С;
-окончательное спекание деталей в вакууме или восстановительной
атмосфере при температуре 1350-1700 °С.
Продолжительность окончательного спекания обычно стремятся ми нимизировать с целью уменьшения размера зерна, растворения твердой фазы в матрице, диффузионной пористости, искажений формы деталей и др.
Некоторые преимущества (отсутствие остаточной пористости, более мелкое зерно, менее значительные изменения размеров и формы) возмож но получить благодаря изостатическому горячему прессованию и спека нию под давлением, но в этом случае резко возрастает стоимость изделий. Указанные технологические приемы используют лишь при изготовлении ответственных крупногабаритных изделий [7], при этом цена 1 кг деталей типа «втулка» достигает 60 долларов США.
Технологические процессы, включающие в себя инфильтрацию, за редким исключением не нашли промышленного использования для компо зитов с высокой концентрацией твердой фазы из-за сложности их практи ческой реализации и более высокой стоимости изделий по сравнению со стоимостью изделий, изготовляемых по принятой технологии порошковой металлургии.
Важнейшими факторами, определяющими свойства и области приме нения твердых сплавов, являются: механические и коррозионные свойства упрочняющей фазы и матрицы, угол смачивания матрицей карбидов или других тугоплавких соединений, термодинамическая стабильность и со вместимость компонентов, остаточная пористость, возможность реализа ции структурно-неустойчивого состояния матрицы при весьма незначи тельном растворении твердой фазы.
Поскольку об эксплуатационных свойствах обсуждаемых материалов судят по их твердости и вязкости, то несколько подробнее следует остано виться на связи твердости и вязкости с износостойкостью. В трибологии твердые сплавы пока не нашли широкого применения из-за их относитель но высокой стоимости и плохой механической обрабатываемости, а также из-за отсутствия возможности в большинстве случаев найти инженерные решения, повышающие до требуемого уровня износостойкость пар трения. Но по мере развития техники, повышения требований к надежности и дол говечности машин и механизмов области применения твердых сплавов расширяются, они становятся незаменимыми в случае высоких нагрузок, ограниченной подачи смазки и особенно в случае абразивного износа.
При скольжении в присутствии абразива объем изношенного мате
риала можно оценить из выражения, полученного М.М. Хрущевым, кото рое устанавливает пропорциональную зависимость объема износа от на грузки, пути трения, размера зерна абразива и обратно пропорциональную от начальной твердости металла или другого исследуемого материала.
Износ линейно возрастает с увеличением размера зерна только до не которой критической величины, а затем не изменяется, скорость скольже ния, если не она приводит к заметному нагреву контакта, тоже мало влияет на величину абразивного износа [8]. С твердостью дело обстоит сложнее, следует рассматривать отношение твердости металла Нм к твердости абра зива # а. В диапазоне Нм/ # а = 0,7 1,0 износ относительно невелик, при отношении Ям /Я а = 1,0 ... 1,3 он возрастает с повышением твердости час то по линейной зависимости, но если отношение Ям / Яа достигает 1,3-1,7, то износ перестает зависеть от твердости абразива. Исключение составля ют материалы, имеющие деформационные фазовые переходы при трении.
Более общим случаем является коррозионно-механический износ, при котором разрушение поверхности происходит под влиянием механическо го и коррозионного факторов; интенсивность износа в этом случае опреде ляется природой контактирующих материалов, их коррозионной стойко стью, воздействием окружающей среды и т.д.
Таким образом, наиболее важными контролируемыми показателями работоспособности твердых сплавов являются твердость, вязкость и кор розионная стойкость.
8.2. Структура и механические свойства твердых сплавов
При изготовлении современных твердых сплавов стремятся реализо вать один из четырех подходов:
1) измельчить зерно (этот подход традиционен для поликристаллических материалов); принято разделять твердые сплавы на супертонкие (0,2-0,3 мкм), ультратонкие (0,4-0,5 мкм), тонкие (0,6-0,7 мкм) и стан дартные (0,9-1,4 мкм) [4, 5];
2)заменить кобальтовую матрицу более коррозионно-стойкой или из носостойкой;
3)исключить или частично заменить карбид вольфрама другим кар бидом с целью повышения эксплуатационных характеристик и/или сниже ния цен на изделия;
4)создать материалы с карбидным упрочнением, более технологич ные, чем современные твердые сплавы.
Последний подход представляется наиболее перспективным в плане быстрого получения экономического эффекта. Так, типичная цена твердо сплавной пластинки для режущего инструмента находится на уровне пяти
рублей, а производство изделий сложной конфигурации или тонкостенных деталей на несколько порядков повышает стоимость и зачастую делает ис пользование твердых сплавов экономически нецелесообразным. Быстрый рост цен на вольфрам и кобальт (до 170 % в год) [9], характерный для на чала и середины восьмидесятых годов, в девяностых и двухтысячных го дах сменился небольшим монотонным повышением. На первом плане опять оказалась задача создания экономичных технологий изготовления деталей заданной конфигурации.
Две основные характеристики обсуждаемых сплавов - твердость и вязкость. В промышленности качество материалов чаще всего оценивают по твердости, которую можно вычислить из выражения
Ям = #w с *Vc к + Нъ( \ - Fwc к \ |
(8.1 ) |
где Нм - твердость материала по Виккерсу; #у/с - твердость карбида вольфрама по Виккерсу; Pwc - объемная доля карбидной фазы; к - коэф фициент, характеризующий взаимодействие между карбидами и связкой («прилегание» [1]); Яв - твердость связки по Виккерсу.
tfwc = 1382 + 23,ПеГт , |
(8.2) |
где d - средний размер карбидной частицы, мм. |
|
Я в = 304 + \2,П Гт , |
(8.3) |
где / - средняя толщина прослойки связки, мм.
Другое известное соотношение между твердостью и микроструктурой
предложил А. Мерц [4]: |
|
Ям = 8777 фсГ)-т |
(8.4) |
Это соотношение подходит для традиционных твердых сплавов, но может быть использовано для материалов с субмикронным размером час тиц. У субмикронных сплавов наблюдается аномальное повышение твер дости (порядка 10 %) и эксплуатационных характеристик [4, 10], но неза висимо от размера частиц прочность и твердость изменяются согласованно
[4].
С другой характеристикой - вязкостью - для традиционных твердых сплавов, на первый взгляд, все относительно ясно: чем больше доля связки и размер зерна, тем выше вязкость [1]. Однако не ясно, существует ли кор реляция между содержанием связки и размером зерна. Этот вопрос не ис следован. Сведения о влиянии размера зерна на трещиностойкость К\с> важнейшую характеристику вязкости не только твердых сплавов, но и в целом порошковых материалов, весьма ограничены. Для компактных ма териалов и керамики получены данные, согласно которым АГю растет с увеличением зерна [1 1 - 20], не зависит от размера зерна [1 1 , 20, 2 1 ],
уменьшается с уменьшением размера зерна [22]. Бели изменение размера зерна увеличивает долю транскристаллитного разрушения, то K\Q возрас тает. В случае разрушения по межзеренному механизму трещиностойкость К\С линейно связана с dta (размер зерна) [20]. В какой-то мере ответ на вышеприведенный вопрос дали последние исследования Института техно логии в Вене. В работе [24] показано, что повышение твердости за счет из мельчения зерна в системе WC - Со приводит к падению вязкости, но нельзя сказать, что вязкость очень тонкого зерна существенно ниже вязко сти грубого зерна. Таким образом, ясно только то, что необходимо стре миться к внутризеренному разрушению, этот фактор остается преобла дающим независимо от размера зерна. Знание о влиянии размера зерна на эксплуатационные и технологические свойства принципиально важно для активно развиваемых в настоящее время способов инжекционного формо вания твердых сплавов [25, 26 27], поскольку сам метод требует примене ния мелких частиц.
Итак, уменьшение размера зерна всегда обеспечивает рост твердости, но может способствовать понижению вязкости твердых сплавов. Для дос тижения наибольшей вязкости необходимо обеспечить разрушение по внутризеренному механизму.
8.3.Основные добавки к твердым сплавам и их роль
вформировании структуры
Для замедления роста зерен и упрочнения твердых сплавов к WC ча ще всего добавляют TiC (так же, как и в быстрорежущие стали [28]), VC, NbC, ТаС, СГ2С3 [29, 30, 31]. В работе [29] приведены результаты исследо вания влияния малых добавок V2O5 и V8C7 на вязкость твердых сплавов. В случае использования карбида ванадия при равной твердости вязкость ис следованных сплавов оказалась существенно выше, чем системы WC - Со (средний размер частиц 1,28 мкм), несмотря на присутствие a -фазы. По нашему мнению, установленный эффект обусловлен дестабилизацией ва надием кобальтовой связки. Судя по всему, аналогично действует и хром [30]. В обоих случаях наблюдается также измельчение зерна, так как мел кие тугоплавкие карбиды хрома и ванадия являются стопорами. Более то го, вычисленные значения энергии активации роста зерен Q показывают, что Q за счет добавок 0,5-1,0 % карбидов может возрасти вдвое. Предпо ложительным механизмом роста энергии активации является образование в жидкой фазе кластеров W - V - Сг/С, затрудняющих транспорт атомов вольфрама и углерода [32].
На первый взгляд несколько отличаются от вышерассмотренных ре зультаты работы [24], в которой доказана большая выгода легирования