
книги / Расчёт потребного количества технологического и транспортного обрудования в курсовом и дипломном проектах
..pdf2.1.Способ получения заготовки.
Заготовка - поковка в обточенном состоянии.
2.2.Характер выбранного оборудования.
Для обработки данной детали выбрано оборудование, предложенное в базовом ТП.
2.3. Трудоемкость типового представителя (деталь «Кольцо»).
Ведомость трудоемкости детали «Кольцо» представлена в табл. 2 .
Номер |
Наименование |
i |
Тип оборудо |
||
операции |
операции |
вания |
230 |
Токарная |
Токарно |
|
|
винторезный |
|
|
1М63 |
250 |
|
Токарно |
|
|
карусельный |
290 |
|
1516 |
Сверлильная |
Радиально |
|
|
|
сверлильный |
|
|
2М53 |
310 |
Резьбонарезная Вертикально |
|
|
|
сверлильный |
|
|
2Н135 |
|
Таблица 2 |
|
Общее время |
Время |
Т по типораз |
Г, мин |
меру оборудо |
|
вания, мин |
3,1 |
3,1 |
13,7 |
13,7 |
8,2 |
8,2 |
2,2 |
2,2 |
Итого |
27,2 |
27,2 |
В том числе станочное время |
27,2 |
27,2 |
2.4. Определение коэффициента закрепления операций.
Коэффициент закрепления операций Къ0 - 21 - мелкосе рийное производство.
2.5. Определение приведенной программы.
Количество деталей программы
*пр = |
V •60 90000-60 |
= 198 529 шт. |
|
^игг^ |
27,2 |
|
|
|
|
||
|
|
|
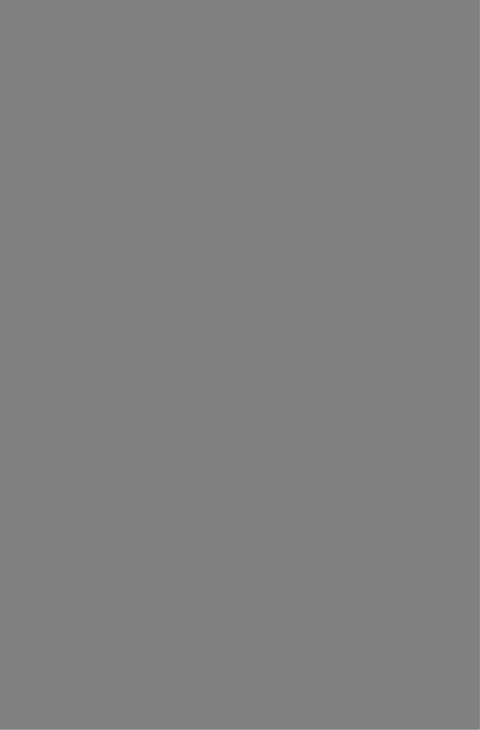
3.5. Определение среднего коэффициента загрузки обо рудования:
|
Лзаг.ср |
Срасч |
23,13 = 0,96. |
|
|
|
|
||
|
|
Спр |
24 |
|
|
|
|
|
|
|
3.6. |
Расчет количества оборудования участка. |
|
||||||
|
Ведомость оборудования участка приведена в табл. 3. |
|
|||||||
|
|
|
|
|
|
|
Таблица 3 |
||
№ |
Наименование |
Модель |
^ШТэ |
|
|
|
|||
оборудо |
Срасч |
С„р |
Л заг |
||||||
п/п |
оборудования |
МИН |
|||||||
вания |
|
|
|
||||||
|
Токарно-винторезный |
|
|
|
|
||||
1 |
1М63 |
3,1 |
2,64 |
3 |
0,88 |
||||
2 |
Токарно-карусельный |
1516 |
13,7 |
11,65 |
12 |
0,97 |
|||
3 |
Радиально-сверлиль |
2М53 |
8,2 |
6,97 |
7 |
0,99 |
|||
|
ный |
|
|
2Н135 |
|
|
|
0,94 |
|
4 |
Вертикально-свер- |
2,2 |
1,87 |
2 |
|||||
|
лильный |
|
|
|
|
|
|
||
|
|
Итого |
|
27,2 |
23,13 |
24 |
0,96 |
4.Расчет количества участков
4.1.Определение количества участков:
у _ |
_ 150 _ g 25 - 7 |
С„р |
24 |
Минимальное количество станков в цехе CCTmjn= 150 шт.
4.2. Определение общего количества станков в цехе:
Сц = У • Спр = 7 24= 168 шт.
4.3. Расчет количества оборудования механического
цеха.
Ведомость оборудования механического цеха представлена в табл. 4.
|
|
|
|
|
|
Таблица 4 |
|
№ |
Наименова |
Мо |
Количе |
Ремонтная |
Мощность, |
||
ние оборудо |
сложность, РЕ |
кВт |
|||||
п/п |
вания |
дель |
ство |
един. |
общ. |
един. |
общ. |
|
1М63 |
|
|||||
1 |
Токарно |
3x7 = 21 |
18 |
378 |
13 |
273 |
|
|
винторезный |
|
|
15 |
|
30 |
2520 |
2 |
Токарно |
1516 |
12x7 = 84 |
1260 |
|||
|
карусельный |
|
|
|
|
|
|
3 |
Радиально |
2М53 |
7x7 = 49 |
19 |
931 |
3 |
147 |
|
сверлильный |
|
|
|
|
4 |
|
4 |
Вертикально 2Н135 |
2x7= 14 |
10 |
140 |
56 |
||
|
сверлильный |
|
|
|
|
|
|
|
Итого |
|
168 |
|
2709 |
|
2996 |
5. Расчет грузооборота механического цеха
5.1. Грузооборот заготовок
0,„ = 9 *,г ЛГпр У = 17,6 198 259 7 = 24 458 772 кг (24 438,77 т).
Масса заготовки qMr = 17,6 кг.
5.2. Грузооборот готовых деталей |
|
|||
0ГОтд = ?гОТд |
Упр |
У = 5,8 |
198 259 |
7 = 80 602 774 кг |
(8060,28 т). |
|
|
|
|
Масса заготовки qMr = 5,8 кг. |
|
|
||
5.3. Общая масса транспортируемых грузов в промежу |
||||
точный склад и обратно |
|
|
||
0 проск = 9 п/ф |
Nnp |
У ( / - ! ) • |
* = 11,7 |
198 259-7 7-0,3 = |
= 34 145 002 кг (34145 т). |
|
|
||
Средняя масса полуфабрикатов типовой детали, транспор |
||||
тируемых в ПРОСК, |
= 11,7 кг. |
|
|
Количество операций по ТП детали i = 8 .
Коэффициент, учитывающий выполнение операций без за воза в ПРОСК, к = 0,3.
5.4. Определение массы заготовок, отправляемых на об дувку, химическую пассивацию, покраску:
0хп = О,6 - ^ ф Nnp У = 0,6-11,7 198259 -7 = = 9 755 715,06 кг (9755,72 т).
где 0 ,6 - доля деталей, отправляемых на операции (обдувку, хи мическую пассивацию, покраску).
5.5. Определение массы производственных отходов:
бш х = бзаг - £>гОТ.д = 24 458 772 - 8 0 6 0 277,4 = 16 398 494,6 кг (16 398,5 т).
5.6. Определение общего грузооборота цеха:
С?общ = (Цех получает + Цех отправляет) = qUT + qT01A+ <7™ +
+ «7ПР0СК + ?хим пас + ? проск + 9опеР = 24 458,7 + 8060,28 + 16 398,5
+ 34 145 + 9755,72 + 34145 + 9755,72 = 136 719 т.
5.7. Расчет грузооборот цеха.
Ведомость грузооборота цеха представлена в табл. 5.
|
|
|
|
Таблица 5 |
Цех получает |
|
Цех отправляет |
||
Грузы |
Масса, т |
Грузы |
Масса, т |
|
Заготовки |
24 458,77 Готовые детали |
8060,28 |
||
П/ф из ПРОСК |
34 145 |
П/ф из ПРОСК |
34 145 |
|
П/ф после |
обдувки, |
9755,72 |
П/ф на обдувку, хим. |
9755,72 |
хим. пассивации, по |
|
пассивацию, покра |
||
краски |
|
|
ску |
|
|
|
|
Отходы |
16 398,5 |
Итого |
|
68 359,5 |
Итого |
68 359,5 |
6.Выбор и расчет подъемно-транспортных средств
6.1.Выбор подъемно-транспортных средств для перево зок внутри цеха.
Применяем электрокары, т.к. они имеют малый вес, габари ты, размер платформы 1750x1150 мм, грузоподъемность 2 т, скорость движения 6-15 км/ч. Для перевозки мелких грузов ис
пользуем ручные тележки.
6.2. Выбор подъемно-транспортных средств для перево
зок внутри участка.
Применяем специальные тележки, оборудованные стелла жами разной формы, грузоподъемностью 0,1 т.
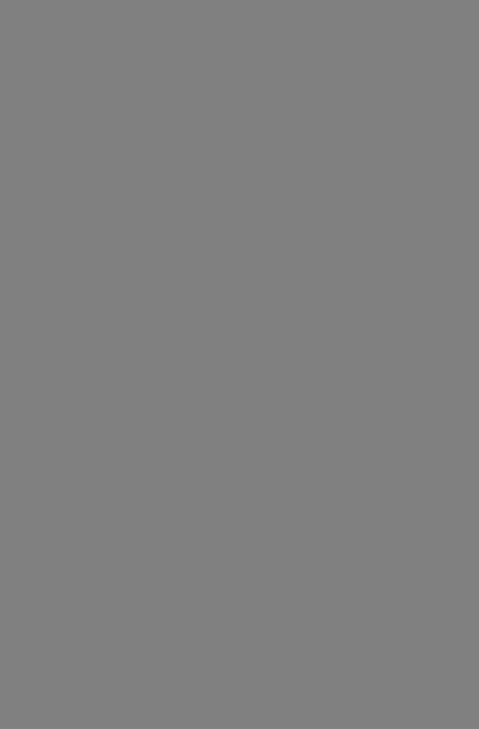
7.1.2. Определенве площади заточного отделения (ук рупнено):
*!>зат = S» • Сзат= 10 • 4 = 40 м2, где SH= 10м2норма площа ди на станок.
7.2.Отделение РЕМПРИ.
7.2.1.Определение количества станков РЕМПРИ:
с ремПРИ= 3 шт.
7.2.2.Определение площади РЕМПРИ:
*$РЕмпри = 5н • Сремпри = 22 3 = 66 м2
7.3.Цеховые ремонтные базы (ЦРБ).
7.3.1.Определение количества оборудования ЦРБ:
СЦРБ = 6 шт.
7.3.2.Определение площади ЦРБ (укрупненно):
5црб = |
Сцрб = 35 6 = 210 м2, где S» = 35 м2 - норма пло |
щади на станок. |
|
7.3.3. Определение площади мастерской по ремонту |
|
электрооборудованни: |
^м.зл = 0,2 • 5црб = 0,2 210 = 42 м2
7.3.4. Определение площади отделения по ремонту
вентиляции: |
|
|
SKm = 0,15 |
5 ц РБ = 0,15 |
2 1 0 = 32 м2 |
7.4. Определение площади инструментально-раздаточ |
||
ной кладовой (ИРК): |
|
|
S'HPK = SH Собщ = 0,5 |
105 + 0,5 |
168 = 136,5 м2, где SH= |
= 0,5 м2 - норма площади на станок; S„ = 0,5 м2 - норма площади |
||
на станок (абразив). |
|
|
К площади ИРК добавляют площадь склада абразивов, как |
отдельное помещение он не создается, а его функцию выполня ет ИРК.
'абразив —SH*С^щ “ 0,5 3 —1,5 М
S„р = 6 м2
Итого общая площадь ИРК: 5 и рКобщ = ■S'H PK + ^абразив = 136,5 + + 6 = 142,5 м2
7.5. Определение площади контрольного отделении.
ISOTK = 0,045 • 3360 = 151,2 м2.
7.6. Служба сбора и переработки стружки.
7.6.1. Определение системы сбора стружки. Система с ра стружки определяется по количеству производимой в цехе
стружки за час работы: К = -^222L= * — |
=4,22 т/ч. |
|
Ел |
3890 |
|
При таком количестве стружки необходимо применять ав томатизированный способ сбора стружки с применением непре рывного транспорта (магистральных конвейеров), также в цехе необходимо организовать и переработку стружки.
7.6.2. Определение площади отделения по сбору и п реработке стружки:
Scjp = 0,04 • 5пр = 0,04 3360 = 134,4 м2
7.7. Определение площади склада СОТС:
Score = 70 м2 •
7.8. Определение площади склада ГСМ:
•SCTCM = S„ ■Сн = 0,12 168 —20,16 м2
7.9. Определение площади трансформаторной подстан
ции:
S,р = 50 м2
7.10. Определение площади аккумуляторного отделе
ния:
iS'aic = 60 M2.
7.11. Определение площади стоянки электрокаров:
•^С ТО Я Н КИ ~ 6 0 М .
7.12. Определение площадей цеховых складов.
7.12.1. Определение площади склада металлов и за готовок:
5 |
Л О , г |
8-24 458,77 |
= 767,3 м2, |
СШ |
q k - m |
3,36 0,3-253 |
где А = 8 дн. - время хранения грузов на складе; q = 3,36 т/м2 - допустимая грузонапряженность площади склада; к = 0,25 - ко эффициент использования площади склада; т = 253 дн. - коли чество рабочих дней в году.
7.12.2. Определение площади промежуточного склада (ПРОСК):
. бпроск __ 34145
к-т 0,25-253 = 539,8 м2
7.12.3.Определение площади склада готовых деталей:
A Qr от.д |
8-8060,28 |
= 252,85 м2 |
^СТД - q k - m |
3,36-0,3-253 |
7.13. Определение площади слесарного отделения:
/>слесар = К SH" Ссдеодр = 1,2 8 20 = 192 м2
7.14. Определение площадей вспомогательных служб.
Ведомость площадей вспомогательных служб приведена в табл. 6 .
|
|
Таблица 6 |
|
№ |
Наименование служб |
Площадь, |
|
п/п |
м2 |
||
|
|||
1 |
Заточное отделение |
40 |
|
2 |
РЕМПРИ |
66 |
|
3 |
ЦРБ |
210 |
|
4 |
Мастерская по ремонту электрооборудования |
42 |
|
5 |
Мастерская по ремонту вентиляции |
32 |
|
6 |
ИРК |
145 |
|
7 |
ОТК |
155 |
|
8 |
Служба сбора и переработки стружки |
135 |
|
9 |
СГСМ |
25 |
|
10 |
Склад СОТС |
70 |
|
|
Окончание табл. 6 |
№ |
Наименование служб |
Площадь, |
п/п |
|
м2 |
11 |
Трансформаторная подстанция |
50 |
12 |
Склад металлов и заготовок |
770 |
13 |
ПРОСК |
540 |
14 |
Склад готовых деталей |
255 |
15 |
Слесарное отделение |
2 0 0 |
16 |
Стоянка для электрокаров |
60 |
17 |
Аккумуляторная |
60 |
|
Итого вспомогательных площадей |
2855 |
|
Площадь магистральных проездов |
720 |
|
Площадь поперечных проездов |
1080 |
|
итого |
4655 |
8.Определенве численности работающих.
8.1.Расчет численности производственных рабочих:
РпР = Рс т + Рс л = 353 + 8 = 361 чел.,
где Рст - число рабочих станочников,
С |
-F -n |
168-3890 0,96 = 352,26 = 353 чел., |
|
Р = ^ц ех |
* д |
Чзаг.ср |
|
F |
к |
17811 |
|
г др |
К мс |
где кмс= 1 - коэффициент многостаночности.
Рсл - число рабочих слесарей, Рсл = 0,02 353 = 7,06 = 8 чел.
8.2. Определение количества основных рабочих, заня тых в 1-ю и во 2-ю смены.
В 1-ю смену: Рпр , см = 0,55 Рпр = 0,55 -361 = 198,5 = = 199 чел.
Во 2 -ю смену: Рпр2см = 361 - 199 = 162 чел.
8.3.Определение количества вспомогательных рабочих:
Рвсп = 0,2 361 = 72,2 = 73 чел.
8.4.Определение количества ИТР:
Ритр = 0,11 ■(361 + 73) = 47,74 = 48 чел.