
книги / Расчёт потребного количества технологического и транспортного обрудования в курсовом и дипломном проектах
..pdf^£2- = |
m. Г"-' + R ■Tcu • С,(m - 1)Tm~- + |
ЭГ |
^ |
+p C i{m-\)Tm-2 =0,
~m + R-TCM(m-])T-' +М(т-\)Т~' = 0. A.
Откуда
( 12.22)
(12.23)
|
T {\-m){R-TCM+ p ) ^ |
(12.24) |
|
|
m-R |
|
|
|
|
|
|
После подстановки (12.24) в выражение (12.20) получим |
|||
L-h |
j f a - R - p ) |
L-h |
R Г 1 ^ (12.25) |
n-S-t |
|
n-S-t |
l i - w j |
12.5. Экономическое сравнение вариантов технологических процессов
Сопоставление экономичности вариантов технологических процессов осуществляется путем сравнения себестоимости об работки заготовок, отражающей затраты живого и овеществлен ного труда.
Расчет экономичности вариантов технологических про цессов производится двумя методами: бухгалтерским и эле ментным.
Бухгалтерский метод расчета. Себестоимость обработки партии заготовок определяется по формуле
С = Л-п + В , |
(12.26) |
где С - себестоимость обработки партии заготовок; п - коли чество обработанных заготовок в партии; А - текущие затраты, которые повторяются при изготовлении каждой заготовки; В - единовременные затраты, которые производятся один раз на все количество заготовок или периодически на определенную их партию.
Себестоимость обработки одной заготовки в этом случае определяется по формуле
С заг - А + -п. |
(12.27) |
В состав единовременных затрат В, входящих в формулы (12.27) и (12.26), включаются затраты на приобретение специ альных станков и инструментов, а также затраты на наладку этих станков.
Текущие затраты А включают в себя: себестоимость исход ной заготовки Сзаг, затраты на заработную плату основных рабо
чих С3 и все цеховые расходы, связанные с амортизацией и ре монтом оборудования, содержанием зданий, затраты на силовую электроэнергию, затраты на нормальный режущий и меритель ный инструменты, затраты на заработную плату инженернотехнических работников и вспомогательных рабочих цеха.
Цеховые расходы определяются в процентах от заработной
платы основных рабочих цеха: |
|
|
^ ~ Сзаг + С3 |
1+ - |
(12.28) |
|
100 |
|
где Сзаг - себестоимость исходной заготовки, |
включая стои |
мость материала и ее изготовления, за вычетом стоимости отхо дов (стружки); р - сумма всех цеховых расходов, выраженная
в процентах от заработной платы основных рабочих. |
|
|
|
|||||||
|
|
Технологическая |
себестои |
|||||||
|
мость |
обработки |
одной |
детали |
||||||
|
Сзаг |
согласно формуле (12.27), по |
||||||||
|
мере |
увеличения |
количества |
об |
||||||
|
рабатываемых |
заготовок п |
сни |
|||||||
|
жается |
по |
гиперболическому за |
|||||||
|
кону, асимптотически |
приближа |
||||||||
|
ясь к предельному минимальному |
|||||||||
Рис. 12.1. Зависимость техно |
значению |
кр |
(рис. |
12.1). |
Пре- |
|||||
дельное |
значение |
технологиче |
||||||||
логической себестоимости из |
||||||||||
готовления одной детали от |
ской |
себестоимости |
изменяется |
|||||||
числа обрабатываемых заго |
в зависимости от величины еди |
|||||||||
товок |
новременных затрат В. |
|
|
|
Технологический процесс, включающий в себя постоянные единовременные затраты Вх, при количестве заготовок в пар
тии, превышающем предельное значение и,, не может быть
реализован. Для его реализации необходимо произвести допол нительные единовременные затраты, например, путем введения в строй дополнительного станка или применения нового режу щего инструмента и т.д.
В этих условиях зависимость себестоимости обработки от количества изготавливаемых заготовок будет иметь ступенча
тый вид (рис. 12.2). |
|
Угол наклона прямых (С = |
|||||
|
|
||||||
|
= А-п + В) относительно оси п |
||||||
|
обратно |
пропорционален |
про |
||||
|
изводительности обработки. |
||||||
|
|
При различных вариантах |
|||||
|
технологических |
процессов, |
|||||
|
имеющих различную произво |
||||||
|
дительность обработки, крити |
||||||
|
ческие значения |
обрабатывае |
|||||
|
мых заготовок неодинаковы. |
||||||
|
|
При сравнении эффектив |
|||||
|
ности проектируемых техноло |
||||||
Рис. 12.2. Зависимость техноло |
гических |
процессов |
наилуч |
||||
шим |
считается |
тот |
вариант, |
||||
гической себестоимости обработ |
который при заданном количе |
||||||
ки от числа обрабатываемых де |
стве |
заготовок |
имеет |
наи |
|||
талей |
|||||||
меньшую технологическую се |
|||||||
|
|||||||
|
бестоимость. Например, |
на |
рис. 12.3 представлены три варианта технологических процес сов обработки отверстия (06О+0,02, Ra = 1,25 мм) протягивани ем (кр. /), растачиванием резцовой головкой (кр. 2) и растачива нием проходным резцом (кр. 3).
Периодически повторяющиеся затраты: В1- стоимость про
тяжки; В2- стоимость резцовой головки; В3- стоимость резца.
При обработке партии заготовок от п - 1 до |
п = п] наи |
более экономично производить расточку отверстия |
проходным |
о л, |
п2 |
п |
Рис. 12.3. Зависимость технологической се бестоимости обработки отверстия от числа обрабатываемых деталей: 1 - при протяги вании; 2 - при растачивании резцовой голов кой; 3 - растачивание резцом
резцом, при обработке партии заготовок от л, до п2 наиболее
экономичным считается второй вариант обработки (расточка отверстия резцовой головкой). При размере партии заготовок п >п 2 наиболее экономичным считается первый вариант (про тягивание отверстия). На рис. 12.3 зона наименьших затрат за штрихована.
Элементный метод расчета. Наиболее точным методом расчета себестоимости вариантов технологических процессов при их сопоставлении считается элементный метод. Технологи ческая себестоимость в этом случае рассчитывается по формуле
Ст = Сст,ч-Гшт..к. |
(12.29) |
Технологическая себестоимость операции Ст |
равна произ |
ведению себестоимости станко-часа Сст.ч на общую Трудоем кость операции 7'шт ,к.
Отдельные слагаемые себестоимости находят не прямым расчетом по точным формулам, а по соответствующим норма тивным таблицам.
В качестве примера в табл. 12.1 приведены некоторые дан ные по элементам затрат на 1 час работы станка из нормативов.
Таблица 12.1
Составляющие технологической себестоимости операций обработки деталей
Тип станка |
Сз.с Сэн Св Срем Са Спр Сг С„н Сст.-ч |
1.Токарно-вин торезный 1К62
|
(тах0 400 мм) |
92,7 |
7,1 |
1,2 |
11,2 |
3,9 |
9,3 |
4,1 |
5,2 |
134,7 |
2. |
Токарный |
|
|
|
26,5 |
19,3 21,2 |
5,8 |
5,0 |
118,6 |
|
|
с ЧПУ 16К20 |
35,3 |
3,8 |
1,7 |
||||||
3. |
Алмазно-рас |
119,5 |
|
|
18,5 |
13,0 |
8,5 |
0,3 |
2,4 |
164,4 |
|
точной 2706 |
1,0 |
1,2 |
4.Круглошли
фовальный 312М 108,5 2,6 1,3 8,8 6,5 5,1 5,4 3,1 141,3
5.Горизонталь но-протяжной 93,8 5,3 2,3 28,9 5,1 7,6 1,2 3,4 147,6
Погрешность расчета технологической себестоимости по нормативам достигает 15-20 % по сравнению с результатами расчета по точным формулам. Однако для большинства случа ев точность такого расчета является достаточной, поэтому он может быть рекомендован для широкого практического при менения.
Следует заметить, что если затраты на технологическую оснастку и специальное оборудование невелики, то оценка эко номической эффективности вариантов по технологической се бестоимости и производительности обработки будет достаточно объективной. Но если в одном из рассматриваемых вариантов предусматривается приобретение дорогостоящего специального оборудования или специализированной оснастки, то сопостав ление экономичности вариантов только по технологической се бестоимости и трудоемкости обработки оказывается недоста точным. Высокопроизводительная оснастка и специальное обо
рудование, как правило, обеспечивают меньшие затраты на об работку заготовки, поэтому сопоставление вариантов по себе стоимости и трудоемкости может оказаться в пользу варианта с большим капитальным вложением.
Для объективной оценки экономичности сравниваемых технологических процессов следует принимать за основу целе сообразность дополнительных капитальных затрат, которые оп ределяются с помощью коэффициента экономической эффек
тивности капитальных вложений |
|
£ = (С ,-С 2).(К2- К ,), |
(12.30) |
где С,,С2 - себестоимость годового выпуска заготовок по пер вому и второму вариантам, руб/год; К,,К2 - капитальные за траты, связанные с осуществлением первого и второго вариан тов технологического процесса, руб.
Для определения экономической целесообразности введе ния новой техники в различных отраслях промышленности ус тановлен нормативный коэффициент экономической эффектив ности £ н , который определяет минимальную величину годовой экономии на себестоимости продукции на 1 руб. дополнитель ных капитальных затрат. Для машиностроительной промыш ленности Ен = 0,2 руб. в год на 1 руб. капитальных вложений.
Экономическая целесообразность дополнительных капи тальных вложений определяется путем сравнения расчетного Е с нормативным Ен коэффициентом экономической эффектив ности:
£ = (С ,-С 2)-(К2- К 1) ^ £ н . |
(12.31) |
При сравнении экономичности различных вариантов сле |
|
дует подсчитывать приведенные затраты: |
|
Зпр = Смг • <7+ £ н • К , |
(12.32) |
где Зпр - приведенные затраты на осуществление годового вы пуска заготовок, руб.; С1агстоимость изготовления одной за готовки, руб./шт.; q - годовой выпуск заготовок, шт,- К - ка
питальные вложения на осуществление данного варианта техно логического процесса, руб.
Из формулы (12.32) следует, что приведенные затраты складываются из себестоимости годового выпуска (С = C^r -q)
и нормативной годовой экономии для соответствующей отрасли промышленности при рациональном использовании капиталь ных вложений ( Ен • К ).
Приведенные затраты Зпр определяются для каждого срав
ниваемого варианта. Лучшим признается вариант с минималь ными приведенными затратами. Годовой экономический эффект от внедрения разработки определяется разностью приведенных затрат сравниваемых вариантов:
ЭГОд = Зпр6- З пр, |
(12.33) |
где Зпр б , Зпр - приведенные затраты базового и нового варианта соответственно.
13. ОПТИМИЗАЦИЯ ТЕХНОЛОГИЧЕСКИХ ПРОЦЕССОВ [27, ГЛ. 7]
13.1. Общие положения
Основной целью технологического процесса является обеспечение заданных характеристик качества изделий наибо лее производительным путем при минимальных затратах. От сюда возникает необходимость в определении двух главных критериев оптимальности: максимальной производительности и минимальной себестоимости.
При решении оптимизационных задач технолог должен, вопервых, определить систему ограничений, отражающих условия протекания технологического процесса и требования, предъяв ляемые к нему, а во-вторых, обеспечить экстремум критерия оп тимальности. Однако следует иметь в виду, что оптимальный технологический процесс - это не идеальный процесс, который удовлетворяет условиям оптимальности всех искомых парамет
ров, а наилучший только по одному или по двум критериям оп тимальности. Например, требуется обеспечить максимальную производительность или минимальный расход материала, или наивысшую точность обработки и т.д. Поэтому при проектиро вании новой технологии необходимо четко определиться с вы бором критерия оптимальности. Критерий оптимальности дол жен учитывать специфику предприятия, условия производства и задачи, стоящие перед ним. Например, если завод испытывает трудности с изготовлением режущего и измерительного инст румента, то в качестве критерия оптимальности на первый план выступает минимум затрат на инструменты. Критерий опти мальности представляется в виде функции, которую называют функцией цели или целевой функцией.
Различают два вида оптимизации технологических процес сов: структурную и параметрическую. Структурная оптимиза ция характеризует выбор оптимальной структуры технологиче ского процесса, например, выбор оптимального маршрута обра ботки или выбор оптимальной конфигурации заготовки, типа оборудования и т.д. Параметрическая оптимизация обеспечива ет получение оптимальных технологических параметров, на пример, определение режимов резания, стойкости инструмента, допусков на межоперационные размеры и т.д.
Любой технологический процесс представляет структуру, состоящую из отдельных блоков и связей между ними. Под структурой понимается не любое сочетание блоков и связей, а только та часть из них, которая обеспечивает выполнение тре буемой функции. Процесс создания структуры и определения параметров объекта в общем случае является процессом управ ления. В свою очередь, оптимизация как метод управления тех нологическим процессом может быть количественной и качест венной. Качественная оптимизация основана на субъективном опыте, здравом смысле, логическом анализе типовых решений и справочных данных. Понятие качественной оптимизации яв ляется условным, так как любое решение можно представить количественно (например, путем определения себестоимости сравниваемых вариантов).
При проектировании технологии в ряде случаев возникает необходимость решения целого ряда задач, которые не подда
ются аналитическому расчету, например, выбор схемы базиро вания, выбор оборудования, назначение последовательности удаления припуска и т.д. Причем эти задачи имеют также мно жество вариантов решения. Оптимальное содержание операции зависит от числа переходов, методов настройки станков, числа подналадок, технологической возможности оборудования и ос настки и т.д.
При формировании структуры операции необходимо:
-упорядочить общую совокупность переходов;
-определить место термической обработки;
-минимизировать количество установок и холостых дви жений инструмента;
-на каждый переход назначить припуски и допуски на размеры обрабатываемых поверхностей и фактические глубины
резания; - для каждого перехода установить частоту вращения
шпинделя и величину подачи, обеспечивающие требуемую точ ность и шероховатость поверхности.
Оптимизация технологических параметров может выпол няться в детерминированной (статической) постановке, т.е. при постоянных значениях всех входящих в модель параметров и в стохастической (динамической) постановке с учетом вероят ности изменения целевой функции. Например, известно, что при разработке операции шлифования в детерминированной (стати ческой) постановке при постоянных значениях всех входящих в математическую модель параметров надежность целевой функции достигает уровня доверительной вероятности не более 0,5-0,6. При этом наблюдается значительная вероятность отка зов, т.е. невыполнения ограничений по стойкости, режущей спо собности инструментов, точности шероховатости обработанных поверхностей и т.Д. Для повышения надежности протекания операции шлифования требуется диагностика и применение до полнительной (внутренней) оптимизации на этапе осуществле ния операции, т.е. при обработке.
Величина тепловой деформации ходового винта при шли фовании резьбы определяется по детерминированной модели. Она должна быть сопоставлена с величиной, замеренной датчи ком в конце прохода. Обнаруженное при этом различие должно
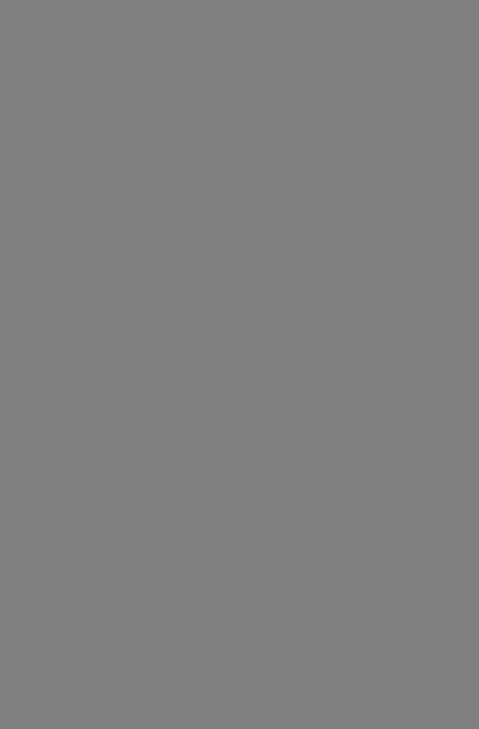