
книги / Статистическое управление качеством технологических процессов
..pdfВероятность обнаружить не более х дефектных деталей в выборке
G(x) = G(x;p) = £ g (/). |
(5.4) |
1=0
Пример. Решим приведенный в п. 5.2.1 пример с использованием таблиц распределения Пуассона.
Определяем среднее число дефектных деталей в партии: р = п р = 100-0,02 = 2.
Последовательно вычисляем вероятности обнаружения в выборке ровно 0; 1; 2; 3; 4 дефектных деталей:
g(0) = ^ e ~2 =0,1353, g(l) = j e ~2 =0,2706,
2 2
g (2) = ■— е - 2 = 0,2706, g(3) = =^е~2 = 0,1804,
24
g(4) =- e - 2 =0,0902.
4!
Определяем суммарную вероятность обнаружения в выборке не бо лее 4 дефектных деталей:
G(4) = g(0) + g(l) + g( 2 ) + g(3) + g(4) =
= 0,1353 + 0,2706 + 0,2706 + 0,1804 + 0,0902 = 0,9471.
Отдельные и суммарные вероятности распределения Пуассона для часто встречающихся значений р приведены в табл. 7, 8 приложения.
5.2.4.Использование номограммы Торндайка
В случаях, когда не требуется высокая точность расчета, можно ис пользовать номограмму Торндайка, которая представляет собой графиче ский способ решения задачи на основе суммарной функции распределения Пуассона (рис. 5.3). С помощью номограммы Торндайка можно опреде лить значение вероятности распределения для заданных р их.
Порядок определения вероятности распределения с использованием номограммы Торндайка:
1) определяют значение р (среднее число дефектов) и отмечают это значение точкой на горизонтальной шкале номограммы;
2) проводят вертикальную линию из этой точки до пересечения с кривой, отвечающей допускаемому числу дефектов или дефектных деталей; 3) из точки пересечения проводят горизонталь до пересечения с ле
вой вертикальной шкалой G(x);
Рис. 5.3. Определение вероятности обнаружения в выборке дефектных деталей по номограмме Торндайка
4)снимают значение суммарной вероятности G(x) по вертикальной шкале в месте пересечения ее с горизонталью;
5)значение вероятности g(x) определяют как разность значений
G(*HT(X-1).
Пример. Решим приведенный в п. 5.2.1 пример с использованием номограммы Торндайка.
Среднее число дефектных деталей в партии
\i = n- /7 = 100-0,02 = 2.
Прямая вертикальная линия на рис. 5.3 проведена от точки со сред ним числом дефектных деталей р = 2. Горизонтальные линии проведены через точки пересечения вертикали с кривыми для х = 0; 1; 2; 3; 4 к шкале суммарной вероятности G. Суммарную вероятность можно определить не посредственно по оси G. Вероятность обнаружения в выборке ровно 0; 1; 2; 3; 4 дефектных деталей равна соответствующим отрезкам шкалы G.
5.3./7-Карты для доли несоответствующих единиц
/7-Карты используются для регулирования доли несоответствующих (дефектных) изделий в контролируемой группе. Это может быть выборка из 75 изделий, берущаяся дважды в день, некоторый процент продукции, группируемой на почасовой или ежедневной основе, доля с выдержанны ми сроками поставки и т.д. При этом можно опираться на оценку одной характеристики или многих характеристик. Важно то, что каждая компо нента, часть или изделие, будучи проверены, записываются как соответст вующее или несоответствующее (даже если изделие имело несколько кон кретных несоответствий). Результаты контроля группируются, и несоот ветствующие изделия выражаются в виде долей от объема подгруппы.
5.3.1. Сбор данных
Выбор объема, частоты отбора и числа подгрупп. Объем под групп. Для ведения карты по альтернативному признаку требуются по под группе большие объемы (например, от 50 до 200 или больше), чтобы иметь возможность своевременно обнаружить умеренные сдвиги в процессе. Для того чтобы карта показывала неслучайное поведение процесса, поддаю щееся анализу, объем подгрупп должен быть таким, чтобы имелось не сколько несоответствующих единиц на подгруппу (например, пр > 5). Од нако большой объем подгруппы может быть недостатком, если каждая подгруппа отбирается в течение длительного периода работы процесса. Наиболее удобно, если объемы подгрупп постоянны или меняются не бо лее чем на ±25 %, но это требуется не всегда. Также полезно выбирать объем подгрупп достаточно большим, согласовывая с /?, чтобы при расчете
обеспечить нижнюю контрольную границу, позволяющую фиксировать запланированные причины усовершенствования процесса.
Частота отбора подгрупп должна быть сопоставимой с периодами производства, что поможет при анализе и коррекции проблем качества. Короткие интервалы времени между выборками позволяют ускорить полу чение информации о течении процесса, но это требование вступает в кон фликт с требованием больших объемов подгрупп.
Число подгрупп должно быть достаточным, чтобы обеспечить дли тельный период сбора данных, позволяющий выявить все вероятные ис точники изменчивости, воздействующие на процесс. Обычно он должен включать 25 или более подгрупп, чтобы провести хорошую проверку на стабильность и, если она есть, дать надежную оценку пригодности процес са.
Вычисление доли несоответствующих единиц для каждой подгруппы (р). Для каждой подгруппы на бланке должны быть записаны число проверенных единиц п и число найденных несоответствующих единиц пр как основа для начального анализа. С учетом этого вычисляем долю несоответствующих единиц:
(5.5)
п
Если известны недавние данные, то они также могут использоваться для ускорения анализа.
Выбор шкалы для контрольной карты (рис. 5.4). Карта, на кото рую наносятся данные, должна иметь вертикальную шкалу для долей (или процентов) несоответствующих единиц и горизонтальную шкалу для обо значения подгрупп (час, день и т.п.). Вертикальная шкала должна пере крывать значения от нуля до 1,5- 2-кратного наибольшего значения доли несоответствующих единиц, отмеченного в исходных данных.
• Нанесите значения р для каждой подгруппы. Соедините точки ли ниями, выделив неслучайное поведение и тренды. Если некоторые точки существенно выше или ниже других, убедитесь, что вычисления правиль ны.
• Запишите в карты изменения процесса или необычные события, способные повлиять на процесс, и время, когда они наблюдались.
5.3.2. Вычисление контрольных границ
Вычисление средней доли несоответствующих единиц для про-
цесса (р). Среднюю долю несоответствующих единиц для периода изуче ния т подгрупп определяем по формуле
|
Контрольная карта регулирования |
Деталь |
Завод/мастерская/цех |
|
|
качества для качественных признаков |
Процесс |
|
|
|
|
Оборудование |
Стр. № |
|
Вид дефекта |
1 2 3 4 5 6 7 8 9 10 11 |
12 14 14 15 16 17 13 |
19 20 21 22 23 24 25 |
Сумма |
Выборка. Объем (л) |
|
|
Количество дефектов |
|
|
Кол-во дефектных |
|
|
единиц |
|
|
Мероприятия |
Объем л |
|
дефектов |
выборки |
|
Контрольный |
||
Количество |
интервал |
|
OEG: |
||
|
||
|
Среднее |
|
|
UEG: |
|
1 |
Оцен. возврат |
|
Дата |
Разработал |
|
Время |
_TTrVMlAIЗИЛ |
|
Фамилия |
||
|
||
|
Рис. 5.4. Пример бланка контрольной карты по качественному признаку |
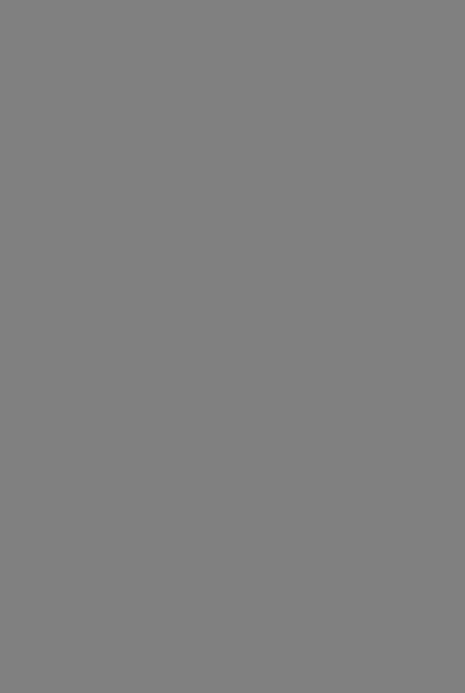
Когда объемы подгрупп изменяются более чем на 25 %, требуется определить отдельные контрольные границы для периодов с особенно ма лыми или большими выборками. Для этого:
•определите размах объемов выборки, который даёт изменение объ ема от среднего на ±25 %, и отметьте все подгруппы с объемами вне этого размаха;
•пересчитайте точные границы для этих подгрупп по формуле
OEGp,UEGp = р ± и д = р ± ^ ' Р > . |
(5.9) |
где щ- объем выборки отдельной подгруппы. От точки к точке меняется только значение п\
• нанесите новые верхнюю и нижнюю границы на карту для изме няющихся подгрупп и используйте их как основу для идентификации осо бых причин воздействия на процесс.
Любая процедура обработки меняющихся контрольных границ явля ется сложной и может вызвать затруднения у людей, пытающихся анали зировать карты. Лучше подготовить план сбора данных так, чтобы исполь зовались постоянные объемы выборок.
Пример построения /7-карты. Из процесса литья были взяты 20 вы борок. Результаты контроля этих выборок занесены в карту (рис. 5.5). Рас считать контрольные границы по нормам Форда и построить /?-карту.
Средняя доля дефектов
Р= I А = 0,674 = 0,0337,
т20
средний объем выборки
_ 5> / 9985 |
499,25. |
|
т20
Контрольные границы по нормам Форда
OEGp = р + З^ -1^ - = 0,<>,0337 + 0,0337(1-0,0337) = 0,058, 499,25
та, - р-JSES ,0,0337_ J O.0337Q-O.O337) ,
р |
у |
V |
П |
V |
499,25 |
По полученным данным строим контрольную карту (см. рис. 5.5). |
|||||
5.3.3. |
Анализ управления процессом |
|
|||
Цель анализа - |
найти свидетельство того, что процесс больше не ра |
ботает на прежнем уровне, т.е. вышел из-под контроля, и принять надлежа щие действия. Точки за контрольными границами, очевидные тренды или
|
Контрольная карта регулирования качества |
+ |
1 р |
Деталь К о р п у с в о д я н о г о |
н а с о с а |
Завод/мастерская/цех |
||||||||||||||
|
|
|
для качественных признаков |
|
|
|
1п р |
Процесс Л и т ь е |
|
|
|
Лит ейное производство |
||||||||
|
|
|
|
|
|
|
|
|
|
|
гг |
Оборудование |
|
|
|
|
Стр. № |
|||
Вид дефекта |
1 |
2 |
3 |
4 |
5 |
6 |
7 |
8 |
9 |
10 |
и |
12 |
13 |
14 |
15 |
16 |
17 |
18 |
19 |
20 21 :22 23 :24 25 Сумма |
У с а д о ч н а я р а к о в и н а |
1 0 |
1 4 |
1 9 |
1 2 |
1 0 |
2 9 |
1 8 |
1 2 |
1 6 |
1 8 |
1 6 |
2 8 |
1 2 |
2 6 |
1 7 |
1 0 |
1 7 |
1 8 |
1 9 |
1 5 |
Выборка. Объем (п ) |
4 2 0 |
4 6 7 |
5 0 4 |
4 7 0 |
5 4 9 |
5 6 2 |
5 0 7 |
4 3 6 |
4 6 6 |
4 9 8 |
5 0 0 15 8 8 ' |
5 3 4 |
( 4 2 2 |
• 5 2 4 |
[ |
4 8 8 |
' 5 3 9 |
»5241 4 8 1 |
5 0 6 |
||
Количество дефектов |
1 0 |
1 4 |
1 9 |
1 2 |
1 0 |
2 9 |
1 8 |
1 2 |
1 6 |
1 8 |
1 6 |
2 8 |
1 2 |
2 6 |
1 7 |
’ |
1 0 |
1 7 |
75 |
1 9 |
1 5 |
| |
0 2 4 |
ОЗС |
0 3 8 |
0 2 6 |
0 1 8 |
0 52 |
0 36 |
0 28 |
0 3 4 |
0 3 6 |
0 3 2 ! |
048; |
0 22 |
>0 6 2 |
10 3 2 |
0 2 0 |
>0 3 2 |
’ 0 3 4 f |
0 4 0 ) |
ОЗС1 |
|
Доля дефектных единиц |
|
|
|
|
|
|
|
|
|
|
|
|
|
|
|
|
|
|
|
|
|
Мероприятия |
|
|
|
|
|
|
|
|
|
|
|
|
|
|
|
|
|
|
|
|
Объем |
|
|
|
|
|
|
|
|
|
|
|
|
|
|
|
|
|
|
|
|
|
выборки |
Количество дефектов
1 2
1 1
1 0
0 9
0 8
0 7 О б
0 5
0 4
0 3
0 2
0 1
|
|
|
|
4 9 9 ,2 5 |
|
|
|
|
|
Конт |
|
|
|
|
|
рольный |
|
|
|
|
|
интервал |
|
|
• |
|
|
O E G : |
|
Г |
\ |
/ |
) \ |
0 ,0 5 8 |
|
Среднее |
|||||
|
|
|
|
||
1 . |
|
|
\ . / _ |
0 ,0 3 3 7 |
|
S , Г |
’ |
|
\ Г “ |
U E G : |
|
|
|
|
|
0 ,0 0 9 |
|
|
Оцен. |
|
1 |
возврат |
Дата |
Разработал |
|
Время |
] |
Проверил |
Фамилия |
|
|
|
Рис. 5.5. Пример построенияр-карты |
|
неслучайное расположение точек указывают на наличие особых причин изменчивости.
Анализ данных на наличие нестабильности процесса.
При анализе выявляются следующие случаи:
1. Точки за контрольными границами. Наличие одной или несколь ких точек за любой из контрольных границ - свидетельство нестабильно сти процесса в этой точке. Если процесс стабилен и присутствуют только обычные причины изменчивости, то точки за' контрольными границами крайне редки и поэтому мы предполагаем, что на выпавшее значение по влияла особая причина. Она может быть вредной или полезной, а это зна чит, что каждая ситуация требует немедленного исследования. Это - осно вание для начала действий по любой контрольной карте. Каждая точка за контрольными границами должна быть помечена.
Точка выше верхней контрольной границы - обычно признак одной или более из следующих причин:
-контрольная граница или точка ошибочны;
-пригодность процесса ухудшилась или непосредственно в этой точке, или в этой точке как части тренда;
-изменилась система оценки (например, контролер, прибор). Точка ниже нижней контрольной границы - обычно признак одной
или более из следующих причин:
-контрольная граница или точка ошибочны;
-пригодность процесса улучшилась (это следует изучить, чтобы в дальнейшем внедрить необходимые усовершенствования);
-измерительная система изменилась.
2.Неслучайное поведение процесса или тренды внутри контрольных границ. Наличие необычного хода процесса или тренда, даже когда все точки внутри контрольных границ, может быть свидетельством неуправ ляемости процесса или изменения уровня его пригодности на протяжении такого периода или тренда. Это может быть упреждающим признаком ус ловий, которые, будучи не исправленными, могут в будущем дать точки за контрольными границами.
ЗАМЕЧАНИЕ. Когда среднее число несоответствующих единиц на подгруппу {пр) достаточно велико (9 или больше), то распределение зна чений р для подгрупп близко к нормальному и может использоваться ана лиз трендов, подобный используемому для Jc-карт. Когда пр становится малым (5 и меньше), анализ неслучайного поведения затруднен и указан ные правила впрямую не применимы.
Неслучайное поведение внутри контрольных границ проявляется в виде сдвига точек или очевидного неслучайного их расположения.
Серии точек. Для управляемого процесса при достаточно большом пр примерно одинаковое число точек должно находиться по обе стороны
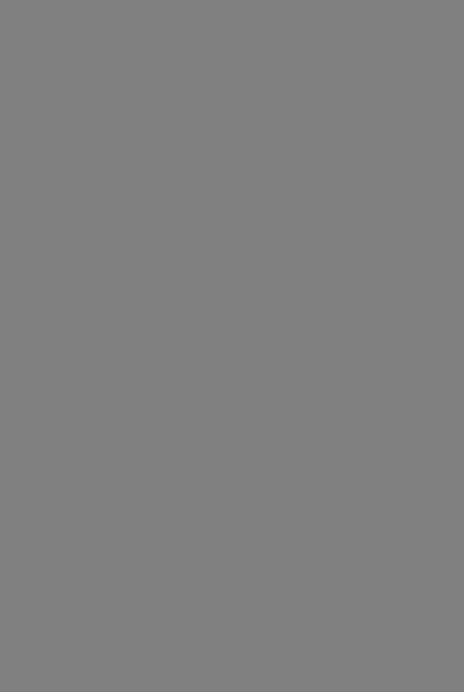