
книги / Технология керамических материалов
..pdf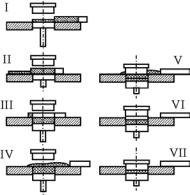
штампы, коленорычажные прессы) и плавное прессование (гидравлические прессы, гидростатическое прессование).
Формование плиток из пресс-порошков производится на гидравлических и коленорыжачных прессах и осуществ- ляется двукратным приложением нагрузки:
–1- е прессование производится при удельном давле- нии 4–6 МПа;
–2- е прессование при удельном давлении 22–30 МПа. Сброс давления между первым и вторым прессованием
обеспечивает удаление воздуха из прессуемого порошка. Все процессы формования плиток автоматизированы. Схема прес- сования двухслойных плиток показана на рис. 30.
На I позиции изобра- жен стол пресса после вы- талкивания отформованной плитки. Справа на столе имеется каретка с емкостью для двух порошков (основ- ного и лицевого). На схеме показано, что оба отсека ка- ретки (большой и малень- кий) заполнены. На II пози- ции показано, что каретка при движении сталкивает от- формованную плитку со сто- ла. После перемещения ниж-
него штампа основная масса порошка из большой емкости каретки засыпается в пресс-форму (III позиция), а маленький отсек с массой лицевого слоя находится на другой половине стола. На IV позиции, при возврате каретки в исходное по- ложение, подсыпается лицевой слой из маленькой емкости.
Прессование происходит в обычной последовательно- сти: первичное прессование (V позиция), затем подъем штем- пелей для освобождения запрессованного воздуха (VI пози-
91
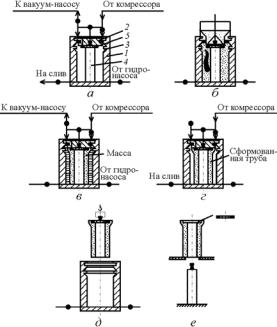
ция) и окончательное прессование (VII позиция). Во время прессования излишняя масса лицевого слоя сдувается и воз- вращается в бункер.
Формование канализационных труб крупного диамет-
ра из полусухих масс осуществляют гидростатическим прессованием в резиновых оболочках. Трубы формуют из масс с W = 7–11 %. Пред сжатием массу вакуумируют при разряжении не менее 600 мм рт. ст. при гидростатическом давлении прессования не ниже 15 МПа. Трубы изготовляют с внутренним диаметром ствола от 150 до 600 мм при толщине стенки от 18 до 42 мм и общей длиной от 800 до 1200 мм.
Последовательность операций показана на схеме (рис. 31):
Рис. 31. Схема прессования керамических труб гидростати- ческим способом: а – подготовка пресс-формы к засыпке;
б– засыпка массы; в – вакуумирование и прессование трубы;
г– отделение резиновой трубы; д – извлечение трубы
скерном; е – освобождение трубы от керна
92
Рассмотрим рис. 31. Металлический корпус пресс- формы 1 снабжен съемной крышкой 2. На дне корпуса и внут- ренних стенках закреплена резиновая оболочка 3. По центру пресс-формы установлен съемный керн 4 – толстостенный ме- таллический цилиндр диаметром равным внутреннему диа- метру трубы. В крышке пресс-формы установлен штуцер для подвода сжатого воздуха и удаления воздуха после вакууми- рования. В нижней части корпуса пресс-формы имеются два отверстия для подачи воды от гидронасоса высокого давления
ипоследующего отвода воды. Цикл прессования состоит из следующих операций:
–после погружения керна и закрытия крышки в про- странство между резиновой оболочкой и керном подают сжатый воздух. Резиновая оболочка при этом растягивается
иприжимается к внутренней поверхности формы, образуя пространство для засыпки массы с учетом Ксж;
–после снятия крышки в пресс-камеру засыпают массу
икрышку герметично закрывают;
–далее камеру подключают к вакуум-насосу и вакуу- мируют массу;
–затем между корпусом и резиновой оболочкой пода- ется вода под давлением до 15 МПа, и производится прессо- вание массы;
–после достижения давления 15 МПа снимают давле- ние воды и открывают крышку пресс-формы;
–далее трубу с керном извлекают из пресс-формы, ус- танавливают над приямком;
–после освобождения от креплений, керн под собст- венной массой опускается в приямок.
93
3.2.1.3. Особенности формования керамических масс полусухим прессованием
Кдостоинствам этого способа формования относят следующие:
– влажность формовочной массы при полусухом прес- совании составляет 6–8 %, что сокращает длительность суш- ки по сравнению с пластическим и шликерным способом формования;
– усадка изделий, сформованных полусухим прессова- нием при сушке и обжиге меньшая, чем при остальных спо- собах формования;
– при таком способе формования обеспечиваются точ- ные размеры и четкие формы изделий;
– повышенная прочность сырцовых изделий после прессования обеспечивает уменьшение возможного раскалы- вания их при транспортировке;
– при прессовании из порошков можно использовать малопластичные глины, вводить больше добавок (золы, шлак).
Кнедостаткам способа полусухого прессования отно- сят следующее:
– водопоглощение изделий после обжига выше, чем водопоглащение изделий, сформованных другими способа- ми. Объясняется это тем, что при обжиге частицы спекают- ся только в местах контакта. Ввиду низкой влажности (W = 6–8 %) происходит незначительное растворение солей, присутствующих в глине, недостаточно жидкой фазы при спекании и не происходит понижения температуры спека- ния и расплавления;
– температура обжига сырца назначается на 50 ° С вы- ше, чем при пластическом формовании, что необходимо для увеличения количества жидкой фазы на поверхностях кон- такта частиц.
94
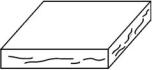
– морозостойкость изделий полусухого прессования по- нижена из-за обилия микротрещин. Микротрещины возника- ют при усадке каждой глиняной частицы при сушке, то есть идет усадка не всего объема изделия, а каждой отдельной час- тицы. При этом происходит отделение одной частицы от дру- гой в местах контакта с образованием трещин, разрывов и, как следствие, понижение морозостойкости изделий.
3.2.1.4. Дефекты изделий при прессовании
Трещины расслаивания возникают на боковых поверх- ностях изделий перпендикулярно направлению прессования. Это явление называют «перепрессовкой» изделий (рис. 32) .
Причинами возникновения трещин могут служить: упругое сжатие формы, где прессуются из- делия; запрессованный воздух; уп- ругие деформации плоских глини- стых частиц по типу консольной балки или балки на 2 опорах; воз- никновение «барического рельефа»
(различное давление на отдельные участки изделия во время прессования, возможно из-за неровности поверхности формы).
Мерами по предотвращению появления данного дефек- та могут являться: отощение порошка грубозернистыми час- тицами; повышение однородности порошка по грансоставу; достижение однородности массы по влажности; применение пониженной влажности массы при более высоких давлениях прессования; использование более медленного прессования или двустороннего прессования; вакуумирование порошка; поддерживание поверхности пресс-формы в хорошем со- стоянии (исключить неравномерный износ).
Выбор того или иного способа устранения трещин про- водят с учетом его влияния на конечные физико-технические свойства изделий.
95
Заусеницы по краям сырца. Причина появления заусе-
ниц состоит в износе боковых стенок пресс-формы и штампа. Для ликвидации этого вида дефекта проводят замену пресс- формы, наваривание пластин на боковые грани штампа, шлифование поверхности формы.
Вырывы на поверхности сырца после формования обра-
зуются из-за налипания массы к штампу или дну формы. Этот дефект может быть обусловлен повышенной влажностью мас- сы, а также использованием холодной формы или штампа. Для предотвращения появления подобных дефектов необходимо проводить регулировку влажности порошка и подогрев формы и штампа перед формованием.
Разнотолщинность изделия. Дефект возникает из-за не-
правильной дозировки при подаче массы. Требуется отрегули- ровать количество массы, подаваемой на прессование.
Низкая прочность получаемого изделия-сырца обуслов-
лена образованием рыхлой структуры отпрессованного изде- лия вследствие отсутствия выхода воздуха из массы за счет плотно подогнанного к форме штампа. Для ликвидации де- фекта необходимо обеспечить минимальный зазор между штампом и формой.
3.2.2. Пластическое формование керамических изделий
3.2.2.1. Свойства пластических масс
Способ переработки сырья для пластического формо- вания заключается в подготовке пластичной глиняной массы влажностью 20–22 %. При пластическом формовании ис- пользуют достаточно вязкие глиняные массы, которые не прилипают к формовочному оборудованию, и применяют добавки, выполняющие различные функции.
Структурно-механические свойства пластических ке-
рамических масс, кроме числа пластичности, отражаются ря- дом других показателей.
96
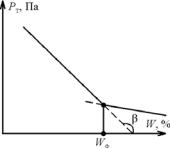
Пластичность глинистых структур, исходя из анализа классического уравнения Бингама – Шведова для вязкой жидкости, предложено характеризовать показателем пла- стичности ϕ :
|
ϕ = |
Рт |
, |
(15) |
|
|
|||
|
|
η |
|
|
где Рm – |
напряжение сдвига (предел прочности при сдвиге); |
|||
η – |
структурная (пластическая) вязкость. |
|
Масса не будет пластичной, когда φ = 0. Это может быть в двух случаях: либо когда Pm стремиться к 0 (тогда система будет текучей), либо когда η → ∞ , тогда масса будет хрупкой.
Показатель пластичности с большей четкостью отра- жает физический смысл пластического состояния.
Формуемостью керамической массы называют способ-
ность массы деформироваться без разрушения структуры. Ко- личественной мерой формуемости является величина сtg β
на диаграмме РТ – W, который должен быть не менее 2. При сtg β менее 2 глины формуются плохо (рис. 33).
Реология как наука о де- формации и текучести реальных масс под действием различных механических напряжений раз- работана академиком П.А. Ре- биндером и его школой.
Пластичные керамические массы являются дисперсными системами, которые состоят из твердой и жидкой фазы. Они способны образовывать связан-
Рис.33. Схема определения величины сtg β
97
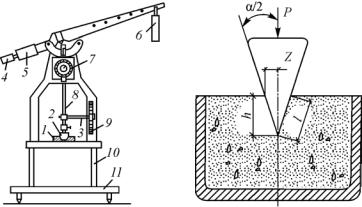
ные пространственные структуры. По свойствам пластиче- ские массы занимают промежуточное положение между твердым и жидким состоянием. Чисто пластические массы начинают деформироваться только под влиянием некоторого усилия, называемого пределом текучести Рm. Считается, что такая пластическая структура при пределе текучести мгно- венно разрушается, и тело превращается в жидкость.
Пластическая прочность, или механическая прочность, структуры представляет собой предельное напряжение сдвига, которое может выдержать масса при статическом нагружении.
Определяют пластическую прочность с помощью ко- нического пластометра П.А. Ребиндера (рис. 34, 35).
Рис.34. Схема лабораторного |
Рис. 35.Схема к расчету пласти- |
конического пластометра |
ческой прочности массы |
П.А. Ребиндера |
|
При вдавливании конуса прибора в испытуемую массу под действием груза растет сопротивление массы его погру- жению. Прекращение погружения конуса означает, что на- грузка уравновешивается пластической прочностью массы.
В керамических пластических массах процесс разру- шения и деформации структуры идет постепенно. Такое по-
98
ведение пластических керамических масс описывается урав- нением Шведова – Бингама, имеющим вид:
Р = Рк + |
dε |
ηпл ; |
(16) |
||||
dτ |
|||||||
ηпл = |
Р−Рк |
, |
(17) |
||||
|
|
dε |
|
|
|||
|
|
|
dτ |
|
|
|
где Р |
– |
напряжение сдвига; |
||
|
Рк |
– |
статический предел текучести, при котором реально |
|
начинается деформация; |
||||
|
dε |
|
– |
скорость деформации; |
|
dτ |
|||
|
|
|
||
ηпл |
– |
пластическая вязкость. |
В дисперсных пластичных керамических массах под действием сдвиговых напряжений могут возникнуть три типа деформаций:
– быстрая упругая деформация εб происходит в первые
мгновения после приложения нагрузки. Она связана с упру- гой деформацией частиц глины. При снятии нагрузки она полностью исчезает;
– медленная эластичная деформация εм развивается
с момента приложения внешней нагрузки в течение не- скольких (3–5) мин с постепенно уменьшающейся скоро- стью. Она связана со скольжением частиц относительно друг друга без разрушения структуры. После снятия нагруз- ки она постепенно полностью исчезает;
– пластическая деформация εпл возникает только тогда,
когда напряжение сдвига достигает определенной величины, называемой предельным напряжением сдвига или пределом текучести. При этой деформации происходит частичное раз- рушение структуры, которая самопроизвольно восстанавлива- ется со временем за счет тиксотропного упрочнения. Дефор- мации этого вида происходят с постоянной скоростью и явля- ются необратимыми.
99
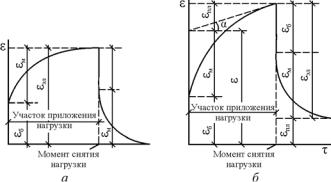
Таким образом, если приложенная внешняя нагрузка вызывает напряжение, лежащее ниже предела текучести Рк, то в системе возникают только первые два вида деформа- ции – εб и εм . Если напряжения превышают Рк, то имеют ме-
сто деформации всех видов, которые складываются по закону аддитивности:
ε = εб + εм + εпл .
Для изучения деформационных свойств керамических масс задают два вида сдвиговых нагрузок:
1.Р < Рк и определяют эластичные деформации εб и εм ;
2.Р > Рк определяют все виды деформаций (рис. 36).
Рис. 36. Зависимость деформации от времени действия напряжения сдвига: а – Р < Рк; б – Р > Рк
В первом случае после снятия нагрузки достигнутая деформация полностью исчезает. Во втором – остаточная де- формация характеризует пластическую деформацию. По из- меренным величинам деформаций и нагрузке определяют ряд характеристик упруговязко пластических масс:
– модуль быстрой упругой деформации (модуль уп- ругости)
Еупр = |
Ра |
; |
(18) |
εб |
100