
книги / Технология керамических материалов
..pdf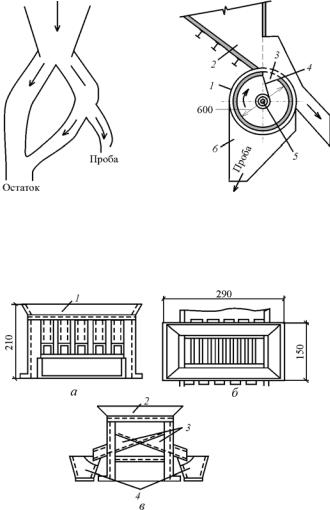
Куски глины измельчают деревянным молотком до 3–5 см и только после этого начинают отбор средней пробы. Пробы сокращают квартованием или с помощью механических де-
лителей (рис. 20, 21, 22).
Рис. 20. Схема продольного |
Рис. 21. Барабанный пробоотби- |
|
рассечения потока сыпучего |
ратель: 1 – стальной цилиндр; |
|
материала |
2 – бункер; 3 – |
щель; 4 – перего- |
|
родка; 5 – |
ось; 6 – желоб |
Рис. 22. Желобчатый сократитель: 1– решетка; 2– приемный бункер; 3– желоб; 4– ящик; а– вид сверху; б– вид спереди; в– вид сбоку
71
Вкачестве механических делителей часто используют желобчатые (струйчатые). В раму сократителя вставлено от 6 до 12 желобков-лотков, причем одна половина их наклонена влево, а другая – вправо (поочередно).
Сокращаемый материал поступает сверху на раму и рас- пределяется примерно поровну между левым и правым ящи- ками. Пробу из одного ящика отбрасывают, а из другого под- вергают повторному делению до получения пробы в необхо- димом количестве.
После сокращения пробу еще раз тщательно перемеши- вают и делят на две равные части: одну направляют на испы- тания, а другую (контрольную) помещают в полиэтиленовый мешок, опечатывают и хранят в лаборатории в течение 2 ме- сяцев на случай проведения арбитражных испытаний.
2.3.Компоненты керамических масс
Впроизводстве керамики в зависимости от вида изго- товляемых изделий и от природных свойств глин используют три вида добавок: отощающие – понижающие пластичность воздушную и огневую усадку глин; выгорающие и пласти- фицирующие – повышающие растяжимость и связующую способность глин. Некоторые добавки оказывают комбини- рованное действие, являясь, например, одновременно ото- щающими и выгорающими.
Выбор добавок и состав формовочной смеси (шихты) необходимо подбирать с таким расчетом, чтобы они облада- ли наилучшими структурно- механическими и сушильными свойствами.
Вкачестве отощающих добавок используют песок, шамот, дегидратированную глину, гранулированный шлак, золу ТЭС.
72
Песок должен быть крупнозернистым с зернами разме- ром 0,5–2 мм, отсеянный от включений более 2 мм. Тонко- зернистые пески ухудшают формовочные и сушильные свой- ства изделий. Лучшим для отощения является кварцевый пе- сок с модулем крупности 2–2,5. Добавляют 10–20 % песка: добавка большего количества песка снижает прочность и мо- розостойкость керамического материала и может явиться причиной «разрыхления» керамического черепка из-за моди- фикационных превращений кварца. Изделие в этом случае лишается звонкости, или на нем появляются тонкие трещи- ны, напоминающие волоски.
Шамотом называют керамический материал, получен- ный обжигом глины при температуре, равной температуре об- жига изделий из этой же глины. На заводах обыкновенного глиняного кирпича в качестве шамота используют порошок, получаемый при помоле отходов обожженного кирпича. Пре- дельная крупность зерен шамота не должна превышать 2 мм. Пылевидная фракция вредна. Допустимое количество шамота при введении в массу составляет 10–15 %, можно довести его до 25 %, но тогда требуется создавать значительный вакуум в прессе, чтобы удалить воздух из пор частичек шамота.
Дегидратированной глиной называют глину, обожжен-
ную до температуры 700–750 º С. При обжиге удаляется хи- мически связанная вода, глина теряет свойство пластичности. Добавляют ее в количестве 30–50 %.
Рекомендуемый зерновой состав добавки из дегидра- тированной глины:
–фракция 2–1 мм до 20–30 %;
–фракция 1–0,63 мм до 15–60 %;
–фракция 0,63–0,35 мм до 15–20 %;
–фракция 0,315–0,14 мм до 25 %;
–фракция < 0,14 мм до 30 %.
73
В качестве отощающих и выгорающих добавок исполь- зуют древесные опилки, антрацит, коксик, тощие каменные угли, бурые угли, отходы углеобогатительных фабрик, лиг- нин, золы ТЭС.
Древесные опилки вводят для улучшения сушильных свойств полуфабриката-сырца. Опилки должны использо- ваться только от поперечного реза древесины, так как тогда образуются короткие, мелкие частицы, хорошо перемеши- вающиеся с вязкой глиняной массой. Вводят древесные опилки при производстве кирпича в количестве 8–28 об. %.
Антрацит, коксовая мелочь (коксик) и тощие камен-
ные угли добавляют в глину в количестве 60–80 % расхода топлива на обжиг, что составляет 2–2,5 % объема глины. Ос- новное назначение добавки каменного угля – создать восста- новительную среду в толще обжигаемого материала, что ин- тенсифицирует процесс спекания и упрочнения керамическо- го черепка.
Бурые угли добавляют в глину с той же целью. Выделе- ние тепла и газов происходит при добавлении бурых углей более равномерно и в более широком температурном интер- вале, чем при антраците, благодаря чему почти не возникает опасности пережога кирпича.
Отходы углеобогатительных фабрик. От обогати-
тельных фабрик в отвалы отходы поступают в виде шлама, влажность которого снижается в отвале до 10–12 %. Зольная часть этих отходов является глинистой с содержанием гли- нозема до 16 %. Использование этих отходов вместо углей экономически целесообразно, поскольку обеспечивает бо- лее равномерное распределение горючей массы в обжигае- мых изделиях.
Золы ТЭС также используют в качестве добавок в глину при производстве кирпича в количестве 10–15 % от массы глины. Они действуют как отощители, а из – за наличия в них
74
невыгоревшего коксового остатка – так же, как и выгорающие добавки. Удельная поверхность золы колеблется в преде-
лах 2000–3000 см2/г.
Лигнин – порошковый тонкодисперсный отход произ- водства древесного спирта. Он действует не только как выго- рающая, но и как пластифицирующая добавка, улучшающая сушильные и формовочные свойства глиняной массы. Лиг- нин вводят в количестве 4–15 %, комбинируя с другими вы- горающими порошками (опилки, уголь).
Торф поглощает влагу из воздуха и с трудом отдает ее при сушке. Он замедляет сушку, так как у торфа высокая влагоемкость и гигроскопичность.
Топочные шлаки – хорошая отощающая добавка, если в остеклованной части шлака содержится несгоревший уголь, то шлаки используются и как выгорающие добавки (сни- жается Кч).
Пластифицирующими добавками являются высокопла-
стичные глина, бентониты и лигносульфонаты.
Высокопластичные глины и бентониты улучшают ке-
рамические свойства суглинков. Бентониты – высокодис- персные глинистые породы с преобладающим содержанием монтмориллонита. Он действует аналогично высокопластич- ным глинам. Бентонит добавляют до 3 % по массе. Высоко- пластичные глины и бентониты вводят в виде шликера с влажностью 40–50 %.
Лигносульфонаты (ЛСТ) – это поверхностно-активные вещества, являющиеся отходами целлюлозного производст- ва. Их добавляют к тощим суглинкам в виде слабоконцен- трированных растворов в количестве 0,3–0,5 % в расчете на сухое вещество. Лигносульфонаты способствуют более равномерному распределению влаги и твердых добавок в сырце и снижению «жесткости» керамической массы.
75
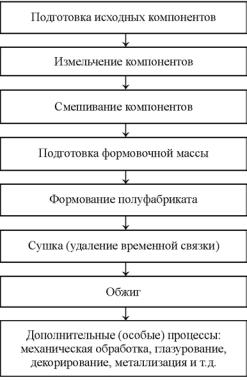
3. ПРОЦЕССЫ И МЕТОДЫ КЕРАМИЧЕСКОЙ ТЕХНОЛОГИИ
3.1. Основные стадии керамического производства
Под керамическим производством понимают изготов- ление тех или иных изделий (грубая строительная керамика, кислотоупорная керамика, огнеупоры, фарфор, фаянс, кера- мика из оксидов металлов и так далее) по керамической тех- нологии.
В разнообразных керамических производствах можно выделить ряд основных общих стадий, или периодов (рис. 23).
Рис. 23. Основные стадии керамического производства
76
Подготовка исходных компонентов должна обеспечи-
вать для каждого компонента керамической массы заданный химико-минералогический состав, необходимую степень чис- тоты, а также определенное физическое состояние и влаж- ность, требуемые для последующей переработки.
Эта стадия может включать:
–процессы обогащения минерального сырья, т.е. про- мывку водой, сортировку, магнитную или ситовую сепара- цию, химическую очистку или другие способы удаления вредных примесей (выделение КЗВ, промывку песка);
–предварительное дробление;
–сушку сырья до влажности, при которой возможно проводить измельчение;
–предварительный обжиг, обеспечивающий необхо- димое уплотнение и удаление летучих веществ. Для высоко- пластичных глин и каолинов – это «обжиг на шамот», чтобы уменьшить их пластичность, так как излишняя пластичность глин приводит к деформации изделий при сушке и обжиге.
Перечисленные процессы применяют при подготовке различных видов природного сырья, а если используют про- дукты химической промышленности, то сначала получают их
ввиде «спеков», то есть после предварительного их спекания. Следует отметить, что для приготовления шамота или спеков также возможно использовать несколько технологических пе- ределов: измельчение и смешивание компонентов, формова- ние брикетов, их сушку и обжиг. А затем эти же процессы мо- гут повторяться при получении готовых изделий.
Измельчение компонентов обеспечивает получение раз- меров их зерен в соответствии с последующей технологией изготовления и требованиями к свойствам изделий. Так, для керамических плиток, изготовляемых прессованием, нужен определенный зерновой состав пресс-порошков.
Для измельчения используют разнообразные помоль- ные агрегаты: мельницы шаровые периодического и непре-
77
рывного действия, дезинтеграторы, распылительные сушил- ки и т.д. Для глин и каолинов иногда процесс измельчения заменяют так называемым распусканием, то есть дисперга- цией до первичных частиц глинистых минералов при замачи- вании водой кусков породы.
Смешивание компонентов должно обеспечивать полу- чение однородной шихты, или массы определенного химико- минералогического и зернового состава. Компоненты дози- руют по массе или по объему и смешивают в смесителях пе- риодического и непрерывного действия. Иногда процесс смешивания совмещают с измельчением в мельницах тонко- го помола.
Подготовка формовочной массы заключается в том,
чтобы придать массе определенные физические свойства: пла- стичность, вязкость, плотность, необходимые для последую- щих процессов формования. Эти свойства можно обеспечить только в присутствие технологической (временной) связки. Последняя представляет собой жидкость, хорошо смачиваю- щую глинистые и другие минеральные частицы и которую легко удалить из полуфабриката при обжиге. Роль такой жид- кости может выполнять вода, водные растворы минеральных
иорганических веществ, органические вещества и их смеси. Для каждой массы необходимо определенное количество связки, например воды, чтобы получить нормальную формо- вочную влажность и изготовить изделие правильной формы. Иногда в порошок вводят связку уже при перемешивании компонентов. При подготовке масс следят и за плотностью массы, так как наличие пор в массе связано с содержанием воздуха в них, а воздух при нагревании расширяется и может вызвать растрескивание изделий. Поэтому на стадии подго- товки формовочных масс иногда проводят их вакуумирование.
Формование полуфабриката. Задача формования – при-
дать изделию требуемые размеры с учетом усадки при сушке
иобжиге, обеспечить определенную плотность, однородность
78
строения, получить изделие-полуфабрикат с некоторой меха- нической прочностью, чтобы можно было перевозить сформо- ванное изделие на сушку.
Варианты процесса формования, используемые в кера- мической технологии, могут быть сведены к трем главным группам:
1.Прессование из порошкообразных масс, осуществ- ляемое с приложением высоких удельных давлений.
2.Формование из пластичных масс: выдавливание (про- тяжка), штемпельное формование и раскатка заготовок в тела вращения. Выдавливанием на ленточном прессе формуют кирпич, черепицу и так далее. Штемпельное формование – это допрессовка изделий, полученных выдавливанием, для удале- ния воздуха. Давление прессования небольшое (до 2–3 МПа). Излишняя масса выделяется через зазоры между штампом
иформой. Кирпич, черепица могут иметь стадию допрессовки.
3.Отливка из текучих суспензий, так называемых ке- рамических шликеров. Прочная отливка получается при по-
степенном удалении (отсасывании) жидкости из отливки
впористую форму или при затвердевании связки. Можно обеспечить дополнительную прочность отливки прессовани- ем при давлении до 0,2 МПа.
Сушка керамического полуфабриката должна закреп-
лять его форму и снижать содержание связующей жидкости
втакой степени, чтобы исключить ее отрицательное влияние на последующий процесс обжига. Если используют органи- ческую связку (лигносульфонаты), то проводят предвари- тельное выжигание связки при Т = 200–220 ° С.
Обжиг – важнейший и завершающий передел керами- ческой технологии. Во время обжига в керамической массе протекают физико-химические процессы. В результате обжи- га происходит уплотнение, упрочнение массы, при этом она приобретает требуемые физико-механические свойства (во- достойкость, огнеупорность, морозостойкость). На степень
79
спекания и уровень этих свойств оказывает влияние приня- тый режим обжига: температура, продолжительность, ско- рость подъема температуры, газовая среда и так далее.
Дополнительные процессы обработки. Обожженные изделия не всегда являются готовой продукцией. После обжига для многих видов изделий проводят шлифование, резку, оправку, обточку и, далее, глазурование, нанесение рисунков. Подробнее все эти прцессы будут рассмотрены при рассмотрении конкретных видов изделий.
3.2.Методы формования керамических изделий
3.2.1.Формование изделий из порошковых масс
3.2.1.1.Способы получения и свойства пресс-порошков
Для полусухого прессования керамических изделий (с удельным давлением прессования до 40 МПа) использу- ют керамические порошки. Пресс-порошки состоят из соб- ственно глинистых частиц, также они могут содержать тон- коизмельченные непластичные материалы, не обладающие связностью (шамот, кварцевый песок и так далее). В кера- мические порошки (пресс-порошки) вводят технологиче- скую связку – воду, потому что без воды глинистые части- цы не проявляют своих пластических свойств.
Цель прессования – получить полуфабрикат высокой плотности, значительной прочности, точных размеров, тре- буемой конфигурации.
Количество связки в подготовленных для формования порошках не превышает 14 %, поэтому такой полуфабрикат будет обладать маленькой усадкой при сушке и обжиге. В процессе обжига появляется небольшое количество рас- плава, спекание происходит по точкам контакта между час- тицами (рис. 24).
80