
книги / Материалы на основе ненасыщенных полиэфиров
..pdf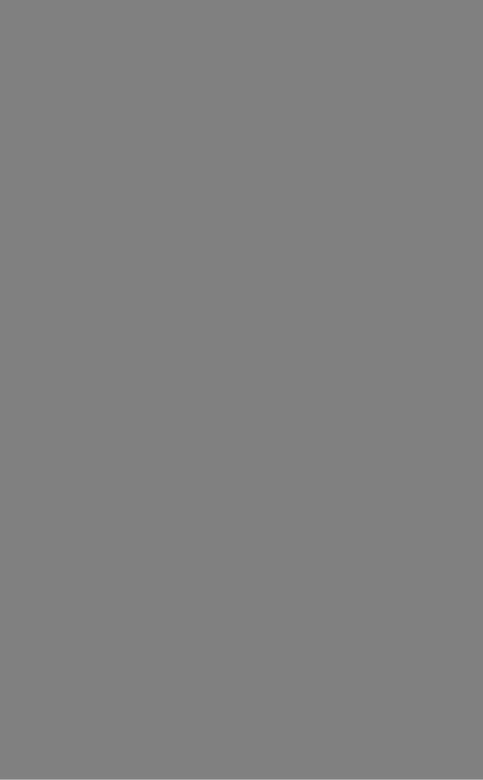
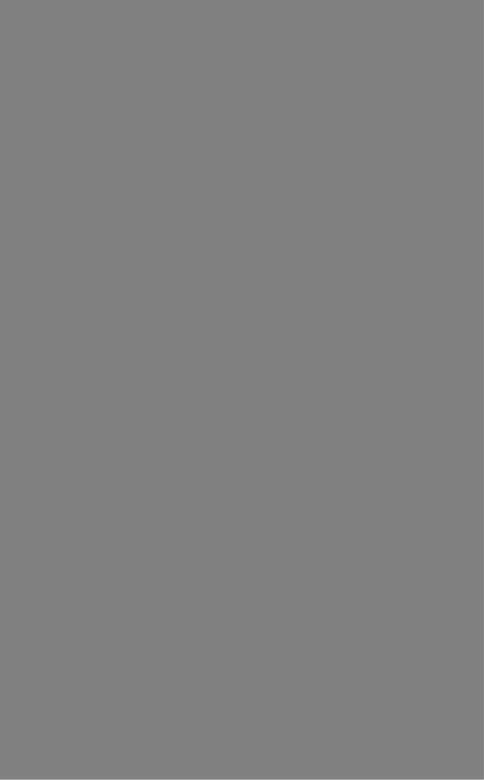
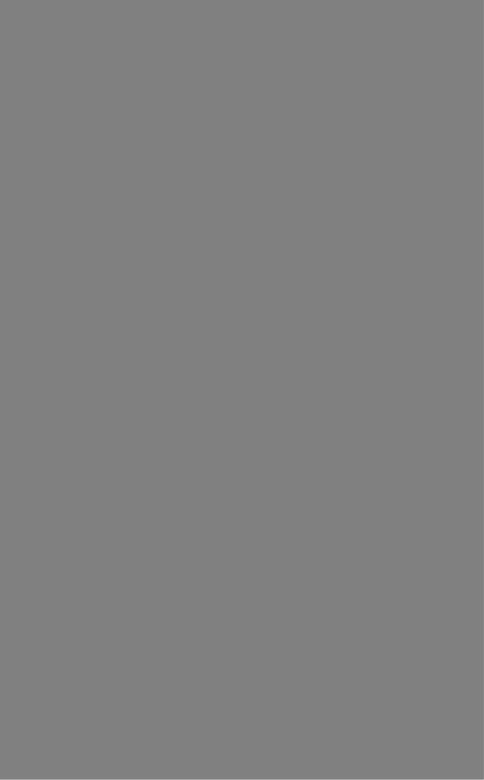
Т а б л и ц а 2.13. Составы пресс-композиций и их свойства на |
ос |
|||||
нове отходов НПЭС, |
измельченных на стадии |
РС |
|
|||
Состав композиций |
Содержание |
Твердость по |
Предел проч |
|||
компонентов, |
Бринеллю, |
ности при на |
||||
|
|
мае. ч. |
МПа |
гибе» МПа |
||
Отходы |
|
100,0 |
|
|
59—60 |
|
Смола ПН -12 |
|
2 0 ,0 |
65— 67 |
|
|
|
Перекись бензоила |
|
0 ,2 |
|
|
|
|
Отходы |
|
100,0 |
58—60 |
|
5 5 - 5 7 |
|
Стирол |
|
10,0 |
|
|
||
Дибут илфталат |
|
2 ,0 |
|
|
|
|
Перекись бензоила |
|
0 ,2 |
|
|
|
|
Отходы |
|
100,0 |
|
|
|
|
Фенолформальдегидная |
смо |
2 0 ,0 |
67— 69 |
|
63—65 |
|
ла СФ-010 |
|
|
|
|||
Отходы |
смо |
100,0 |
|
|
|
|
Фенолформальдегидная |
3 0 ,0 |
72—75 |
|
70—71 |
|
|
ла СФ-342 |
|
|
|
|||
П р и м е ч а н и е . |
Отходы получены при двукратном |
пропуске |
||||
через вальцы при зазоре 0, 15 |
мм, прессование через 6 |
ч |
после |
из |
||
мельчения. |
|
|
|
|
|
|
2 раза. При дополнительном диспергировании необходи мо интенсивно охлаждать валки, что позволяет увели чить количество пропусков через вальцы до 3—4 раз.
Эффективное измельчение и максимальная реакци онная способность отходов достигаются при зазоре меж ду валками 0,1—0,5 мм. При увеличении зазора частицы композиции за счет упругих свойств проходят его без разрушения. Хотя реакционная способность отходов, измельченных на стадии РС, достаточно высока, целе сообразнее их использовать в составе композиций с до бавкой структурно-активных компонентов, способных к сополимеризации с золь-фракцией отходов.
Активность отходов после измельчения с течением времени снижается. Характер изменения свойств анало гичен изменению их свойств при увеличении кратности пропусков через вальцы, что объясняется структуриро ванием, потерями стирола за счет развитой поверхности отходов и соответственно снижением содержания зольфракции. Вследствие этого технологическая жизнеспо собность измельченных отходов в значительной степени зависит от кратности пропуска через вальцы, темпера туры валков, температуры и условий хранения, твердо
сти отходов в момент измельчения, длительности резино подобного состояния связующего и составляет 8— 15 ч.
Проведенные исследования подтвердили целесооб разность переработки отходов НПЭС путем их измельчения на стадии РС. Введение в состав пресскомпозиций на основе отходов исходных связующих (не насыщенных полиэфирных и формальдегидных смол) позволяет существенно повысить физико-механические характеристики и улучшить внешний вид изделий [185].
Определены оптимальные технологические режимы грессования таких композиций: давление 20—25 МПа, температура 403—413 К и выдержка под давлением из расчета 0,5— 1 мин на 1 мм толщины. В табл. 2.13 при ведены оптимальные составы пресс-композиций. Таким образом, композиционные материалы, содержащие в ка честве активного наполнителя отходы НПЭС, можно использовать для изготовления деталей различного тех нического назначения.
Г л а в а 3
МЕТОДЫ ПЕРЕРАБОТКИ КОМПОЗИЦИОННЫ Х МАТЕРИАЛОВ НА ОСНОВЕ
НЕНАСЫЩЕННЫХ ПОЛИЭФИРОВ И ОБЛАСТЬ ИХ ПРИМЕНЕНИЯ
Ненасыщенные полиэфирные смолы обладают низ кой вязкостью, которую можно изменять в широких пре делах, используя загустители, способностью отверждаться без выделения летучих продуктов в диапазоне темпера тур от —2 0 0 до + 140 °С. Это предопределяет возмож ность их переработки практически всеми известными методами.
Композиционные материалы на основе НПЭС, содер жащие волокнистые наполнители, перерабатываются в основном контактным формованием, прессованием и литьем под давлением, методом пропитки волокнистого наполнителя в замкнутой форме, намоткой пропитанно го стекловолокна на оправку, напылением стекловолок на и смолы на форму с последующим уплотнением мате риала прикаткой, непрерывным формованием плоских и профильных материалов, а также центробежным мето дом.
Полиэфирные смолы и композиции на их основе, не содержащие волокнистых наполнителей, можно перера батывать свободной заливкой и центробежным литьем; распылением и поливом (лаки), пропиткой и экструзи ей, прессованием и литьем под давлением, кроме того, различными методами, принятыми при переработке кле ев и мастик.
Основные области применения и методы переработки полиэфирных смол и композиционных материалов на их основе достаточно полно описаны в работах [12, 15, 124, 126, 127, 129, 189, 190]. Рассмотрим методы переработки,
не требующие применения сложного технологического оборудования.
3.1. ИЗГОТОВЛЕНИЕ ИЗДЕЛИЙ МЕТОДОМ КОНТАКТНОГО ФОРМОВАНИЯ
Метод контактного формования не требует сложно го оборудования, и поэтому он широко применяется при изготовлении объемных и плоских деталей из стекло пластиков в строительстве, машино-, приборо-, автомо биле- и судостроении. При контактном формовании от верждение материала происходит, как правило, при комнатной температуре, однако для ускорения процесса можно применять обогреваемые формы или проводить
отверждение |
при повышенных температурах |
(60— |
|
100 °С) [12]. |
|
|
|
Контактное |
формование |
изделий из |
стекло |
пластика осуществляют в |
формах, изготавливаемых |
из дерева, гипса, стеклопластика, металла и т. д. Рабо чую поверхность шаблона или формы обезжиривают обычно бензином Б-70 или ацетоном, контролируя чис тоту, гладкость, отсутствие задиров и других дефектов поверхности.
На подготовленную оснастку (форму, шаблон) на носится плоской кистью, тампоном или распылителем разделительный слой — антиадгезионная смазка, кото рую необходимо просушить при температуре 18—20 °С до исчезновения липкости.
К антиадгезионному средству предъявляется ряд спе цифических требований: обеспечение легкого съема от вержденного изделия с формы, быстрое высыхание, нетоксичность, неприлипание к изделию, а также возмож ность получения изделий с глянцевой или матовой по верхностью.
В качестве антиадгезионных средств используют поли мерные пленкообразующие материалы, в том числе вод ные и водно-спиртовые растворы поливинилового спирта, раствор ацетата целлюлозы в ацетоне, каучука (не со держащего двойных ненасыщенных связей). Их наносят на поверхность форм плоскими кистями или распылени ем.
Наиболее широко применяют водно-спиртовые раст воры поливинилового спирта, скорость высыхания кото
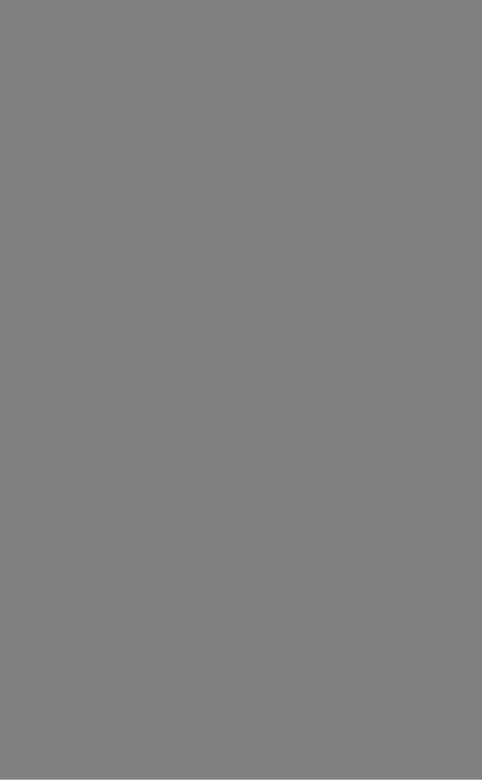
представляет собой пасту, состоящую из 2— 15 мае. ч. различных рафинированных горных восков, 1— 10 мае. ч. твердого воска, 0,5—4 мае. ч. полиэтилена низкого дав ления, 1— 5 мае. ч. стеаратов металлов, 56—94,5 мае. ч. углеводородов бензиновой фракции с температурой ки пения 80—200 °С [191].
При изготовлении малогабаритных изделий можно использовать смазки на основе пчелиного воска или це резина в виде 15—20%-ных растворов в бензине или в смеси бензина с уайт-спиритом или скипидаром, взятых в
соотношении 1 |
3 или 1 :5 . Хорошими антиадгезионны- |
ми свойствами |
и полируемостыо обладают смазки на |
основе воска и силикона, применяемые в быту для нати рания паркета или линолеума. В промышленности при переработке полиэфирных стеклопластиков с использо ванием деревянных шаблонов и форм применяют смазку следующего состава, мае. ч.:
Уайт-спирит |
|
100,0 |
Церезин М-80 |
|
17.1 |
Воск буроугольный |
|
17.1 |
Полиэтиленовый воск.П В-300 |
4 .2 9 |
|
Полиэтиленовый воск |
окисленный |
4 .2 9 |
Смазка обеспечивает до 15—20 съемов изделий. Ее |
||
готовят путем растзорения |
смеси сухих |
компонентов в |
уайт-спирите в течение 3—4 ч при 80—90 °С на водяной бане. Для повышения эффективности смазки рекоменду ется в состав ее вводить ускорители отверждения, напри мер 10 мае. ч. диметиланилина и 10 мае. ч. нафтената кобальта на 100 мае. ч. воска [192].
Для изделий, отверждение и термообработку кото рых проводят при высоких температурах, хорошие ре зультаты дают смазки на основе силиконовых каучуков и полидиметилсилоксановых жидкостей в виде 5— 10 %- ных растворов в бензине, ксилоле и других растворите лях [193].
После высыхания разделительного слоя рабочую по верхность оснастки покрывают равномерным слоем фор мовочного состава, включающего полиэфирную смолу, инициирующую систему и функциональные ингредиен ты (красители, загустители, добавки, снижающие инги бирующее действие кислорода воздуха, и т. д.). Затем укладывают стеклоткань по длине (ширине) стола, шаб
лона. Стыки полотнищ стеклоткани шириной не менее 20 мм необходимо равномерно смещать по длине (шири не) формовочной оснастки во избежание утолщений го товых изделий.
Выклейку заготовки из слоев стеклоткани можно производить различными способами, при этом ткань иногда пропитывают заранее (до раскроя) в пропиточ ных машинах или кистью вручную на специальных рам-
Т а б л и ц а 3.2. Расчетное количество слоев в стеклоткани для выбора необходимой толщины деталей
Толщина детали, |
Количество слоев стеклоткани |
|||
|
мм |
Т Р -0, 7-ГВС-9 |
ЭЗ-200 |
| Т -11-ГВС-9 |
1 ,5 ;1-0,5 |
1— 2 |
1—2 |
1—2 |
|
2,0п 1-0,5 |
2— 3 |
1— 2 |
1— 2 |
|
3,0Н1-0,5 |
2— 3 |
2— 3 |
1—2 |
|
4 ,0 ] Ь0,5 |
4—5 |
2— 3 |
1— 2 |
|
5 |
,ОНЬ0,5 |
5—6 |
1— 2 |
1—2 |
6 |
,ОН;0 ,5 |
7— 8 |
1— 2 |
1— 2 |
7 |
,ОН-0 ,5 |
8— 9 |
2— 3 |
1— 2 |
8 , ОННО ,5 |
8— 10 |
2—3 |
1— 2 |
ках, которые могут быть смонтированы в установке кас сетного типа.
При изготовлении деталей со сложными контурами применять заранее пропитанную стеклоткань неудобно. Поэтому сухую стеклоткань прикрепляют к столу (шаб лону), первый слой пропитывают формовочным соста вом, после чего покрывают стеклоткань следующим сло ем сухой стеклоткани и приглаживают кистью без связу ющего до его появления на поверхности ткани. Уплотне ние слоев производят рифлеными, стальными, тефлоно выми, полиэтиленовыми или полипропиленовыми вали ками. Затем на стеклоткань дополнительно наносят связующее до полной ее пропитки, после чего укладыва ют последующий слой ткани. Процесс повторяют до по лучения нужной толщины изделия. Как правило, при изготовлении изделий из стеклопластиков используют несколько видов стеклоткани для повышения прочност ных характеристик. Количество слоев стеклоткани для набора необходимой толщины деталей можно ориентиро вочно определить по данным, приведенным в табл. 3.2.
Для получения определенного количества связующе