
книги / Научно-исследовательская работа магистров по технологии машиностроения
..pdfцесс стружкообразования, уменьшая относительный сдвиг и удельную работу стружкообразования. При резании материалов, склонных к наростообразованию, влияние скорости резания усложняется.
Только при скоростях резания, при которых температура резания становится больше 600 °С, увеличение скорости резания непрерывно улучшает все показатели стружкообразования.
Влияние механических свойств материала обрабатываемой детали. Непосредственное влияние на процесс стружкообразования механических свойств материала обрабатываемой детали заключается в увеличении угла сдвига с повышением сопротивления сдвигу материала в зоне стружкообразования при постоянных переднем угле и угле действия. Соответственно этому уменьшается степень деформации срезаемого слоя.
Если нарост при резании отсутствует, то косвенное влияние свойств обрабатываемого материала на процесс стружкообразования проявляется в изменении угла действия вследствие изменения среднего коэффициента трения. При постоянной температуре на передней поверхности средний коэффициент трения для различных обрабатываемых материалов изменяется сравнительно мало, так как при увеличении сопротивления материала пластической деформации одновременно возрастают как касательные, так и нормальные контактные напряжения. При постоянной скорости резания с увеличением сопротивления материала пластическим деформациям средний коэффициент трения уменьшается, что уменьшает коэффициент усадки стружки и относительный сдвиг. При наличии нароста косвенное влияние свойств обрабатываемого материала на процесс стружкообразования дополняется их влиянием через изменение фактического переднего угла.
Влияние толщины срезаемого слоя. Толщина срезаемого слоя на процесс стружкообразования влияет только косвенно. Если нарост отсутствует, то влияние толщины срезаемого слоя связано с изменением среднего коэффициента трения, который из-за увеличения средних нормальных контактных напряжений на передней поверхности падает при увеличении толщины срезаемого слоя. Поэтому чем толще срезаемый слой, тем меньше относительный сдвиг
141
и удельная работа стружкообразования. При наличии нароста толщина срезаемого слоя дополнительно влияет через изменение фактического переднего угла инструмента.
Задание на проведение лабораторной работы
1.Изучить предлагаемый теоретический материал о природе деформационных процессов в зоне резания и процессах стружкообразования.
2.Изучить влияние условий обработки на величину и распределение пластической деформации.
3. Изучить методы исследования пластической деформации
взоне резания.
4.Получить от преподавателя образцы с полированными корнями стружки и с помощью микроскопов определить влияние скорости резания и подачи на величину пластической деформации по изменению усадки стружки и по изменению угла сдвига в зависимости от скорости резания и подачи.
5.Занести данные в отчет по работе.
6.Построить графики зависимостей угла сдвига от скорости резания и подачи для двух обрабатываемых материалов.
7.Сделать выводы и ответить на вопросы по теме лабораторной работы.
Вопросы к зачету
1.Что является основным признаком пластической деформации?
2.Почему необходимо знать природу возникновения и методы управления пластической деформацией?
3.Виды деформированного состояния.
4.Дать определение абсолютного и относительного сдвигов.
5.Типы стружек и особенности пластической деформации.
6.Формула расчета угла сдвига.
7.Формула расчета относительного сдвига.
8.Методы изучения пластической деформации.
9.Влияние условий резания – режимы и геометрия на величину пластической деформации.
142
Лабораторная работа № 7 ИССЛЕДОВАНИЕ ФИЗИЧЕСКИХ ЯВЛЕНИЙ
В ПРОЦЕССЕ РЕЗАНИЯ С ИСПОЛЬЗОВАНИЕМ СОВРЕМЕННОГО КОМПЬЮТЕРНОГО ЦЕНТРА ДИАГНОСТИКИ
Цель работы – |
изучить физические явления, |
возникающие |
в процессе резания |
материалов, и их параметры, |
познакомиться |
с работой приборов и методикой проведения экспериментальных исследований одновременного влияния режимов резания при точении на физические параметры процесса резания: шум, вибрацию, силы резания, температуру, мощность резания с помощью центра компьютерной диагностики, научиться проводить зкперименты, делать анализ и обработку результатов.
Актуальность вопроса применения диагностики процесса резания в современных условиях
Развитие современного машиностроения невозможно без создания нового современного оборудования, новых технологий и инструмента. В настоящее время большинство машиностроительных предприятий активно оснащаются высокопроизводительными станками с ЧПУ и многоосевыми многоцелевыми обрабатывающими центрами с компьютерным управлением отечественного и зарубежного производства. В Пермском крае это такие предприятия, как ОАО «Новомет», ОАО «Протон», ОАО «ПМЗ», ОАО «Инкар», ОАО »Редуктор» и др. Стоимость новых станков достаточно велика – 2–3 млн евро за станок. Значительно выросла, в десятки раз, и стоимость режущих сборных инструментов. Непредвиденный выход из строя этого оборудования и инструмента по различным причинам приводит к большим издержкам производства на машзаводах. Поэтому резко вырос уровень активности исследований в области контроля процессов механической обработки и инструмента в нашей стране и за рубежом. Диаграммы, изображенные на рис. 1, показывают, что основная деятельность разработчиков диагностиче-
143
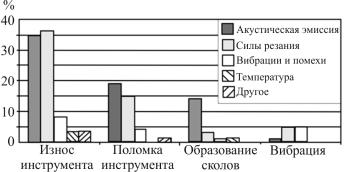
ских систем направлена на контроль износа инструмента или интенсивности его износа в любой текущий момент времени процесса обработки резанием на основе таких косвенных показателей, как вибрация, шум, сила резания, температура резания и др.
Рис. 1. Использование различных диагностических признаков при анализе процессов, происходящих при механической обработке материалов резанием
Интенсивные исследования в области контроля станков и инструмента ведутся во всем мире: в США – национальная лаборатория Лоуренса в Ливерморе, Ок-Риджская национальная лаборатория, Мичиганский университет, Иллинойский университет, Университет шт. Мэриленд, фирмы «Монтроникс», «Ингерсолл миллинг машин» и TPS, в Канаде – Национальный исследовательский совет Канады, Университет Британской Колумбии, Университет Виктории и фирма «Мемекс электроникс». В Европе в области контроля станков и инструмента имеют активные программы: в Германии RWTH Aachen, Университет Пассау, Институт Фраунгофера, фирмы «Роберт Бош», «Прометек», исследовательский институт WZL и Ганноверский лазерный центр; в Испании – фирмы «Текникер», «Соралюче», «Икерлан», «Данобат», «Идеко»; во Франции – фирмы Giat
иObjectif; в Греции – фирмы «Грау» и «Эпсилон»; в Италии – фирмы «Фидия»и ТХТ; в Великобритании – Лидский, Бирмингемский
иНоттингемский университеты; в Швейцарии – фирмы «Кистлер Инструменте» и «Гиндель Гирс»; в Венгрии – Венгерская академия
144
наук. В Японии активные программы имеют следующие организации: Университет Нагойи, Университет Кобе, Университет Кейо, исследовательский центр материалов фирмы «Мицубиси», компания «Хитачи сейки машин тул» и фирма NTN.
ВСША использование систем диагностики данного класса при обработке резанием позволило (в среднем):
– на 30 % повысить производительность обработки;
– на 50 % увеличить срок службы станков (в первую очередь – элементов шпиндельной бабки);
– на 30 % увеличить износостойкость инструмента.
Вчастности, использование таких систем позволило при создании самолета F18 сэкономить 1 млрд долл. за 10 лет.
Ряд машиностроительных компаний успешно применяет вибродиагностические системы в своем производстве. Это – Boeing, Ingersoll, Tool Company, Caterpillar, General Electric, Rolls Royce, Kovosvit A.S. и др.
ВРоссии исследования процесса резания проводятся практически во всех технических вузах страны и в отраслевых НИИ машиностроения. В наибольшей степени это – Станкин, ВНИИТС, завод «Салют» г. Москва. Однако для измерения сил резания, температуры резания, вибрации, мощности применяются различные методы, приборы, датчики часто без преобразования электрического сигнала
вцифровой, т.е. без использования персонального компьютера для анализа, записи и воспроизведения данных на современном уровне.
Основой диагностики и алгоритма выбора оптимальных режимов резания может служить известная в мире диаграмма вибрационной стабильности процесса резания (рис. 2). Анализ этой диаграммы позволяет выявить зоны в пространстве параметров обработки (скорость шпинделя – глубина резания), работа в которых обеспечит наибольшую производительность, виброустойчивость процесса и как следствие требуемое качество обработки.
Для выбора виброустойчивых режимов резания на станках с ЧПУ применяются различные системы вибродиагностики. На рис. 3 представлена схема тарировки аппаратуры вибродиагностики на фрезерном станке при ударном воздействии импульсного молоточка
145
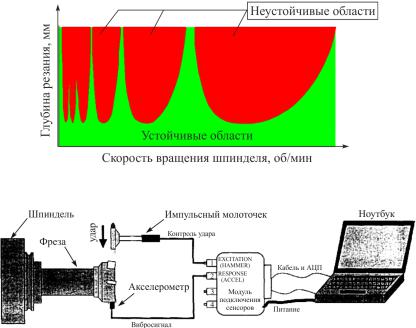
по корпусу фрезы. Вибросигнал фиксируется на экране подключенного компьютера. В дальнейшем вибрация фрезы фиксируется в процессе фрезерования деталей машин.
Рис. 2. Типичная диаграмма стабильности
Рис. 3. Схема тарировки для получения частотных характеристик вибрации фрезы (установлена в шпиндель)
Очевидно, что эффективность диагностики в основном определяется информативностью используемых диагностических признаков, их зависимостью от условий обработки. Традиционно для диагностики процесса резания применялись его статические температур- но-силовые параметры, в большинстве случаев недостаточно информативные. Последнее время и у нас в стране, и за рубежом все большее внимание специалистов привлекает диагностика механической обработки на основе анализа высокочастотных динамических явлений различной физической природы: акустической эмиссии (АЭ) [2]; электромагнитного излучения (ЭМИ) [2]; экзоэлектронной эмиссии
146
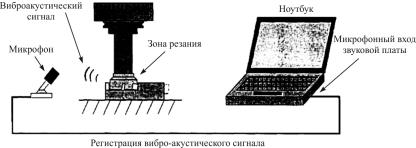
(ЭЭЭ) [2]. На этапе поиска информативных признаков ограничивают число измеряемых параметров вибрации, шума и ударов. При этом из множества параметров, характеризующих вибрационный процесс, выделяют только те, которые прямо или косвенно характеризуют состояние объекта. По этим параметрам формируют информативную систему признаков, используемых при диагностировании. В настоящее время метод АЭ получил наибольшее развитие и применение (рис. 4). По сравнению с ним диагностические возможности других эмиссионных процессов применительно к решению технологических задач раскрыты существенно меньше.
Рис. 4. Компьютерный анализ сигнала виброакустической эмиссии (шум резания) в зоне резания при торцевом фрезеровании
Метод АЭ основан на явлении генерации в твердом теле волн упругой деформации частотой 50–100 кГц [39] при локальном динамическом изменении полей механических напряжений, обусловленном развитием дефектов, например зарождением и ростом трещин, фазовыми превращениями и другими быстропротекающими процессами. С помощью установленного в зоне резания микрофона можно зафиксировать возникающий шум в зоне резания от увеличения износа фрезы, усиления вибрации, появления различных дефектов. Сигнал от микрофона регистрируется на персональном компьютере с помощью проводов или радиосигнала.
Простота установки датчика на станке и возможность метода АЭ регистрировать одновременно все энергоемкие физические процессы, происходящие в зоне резания, в том числе износ инструмен-
147
та, постоянно привлекала исследователей как в нашей стране, так и за рубежом. Однако трудности, связанные с защитой принимаемого сигнала от случайных помех, с выделением параметров АЭ, генерируемых износом инструмента по задней грани и т.д., до недавнего времени сдерживали развитие метода АЭ.
Интерес к колебаниям при резании в более высоком частотном диапазоне появился в 80-е годы прошлого века в связи с проблемами автоматического контроля процесса резания на станках с ЧПУ, встраиваемых в ГПС.
Основные технические характеристики диагностической аппаратуры, входящей
вкомпьютерный центр диагностики ПНИПУ
Компьютерный анализатор «Камертон»
Внастоящей лабораторной работе в качестве основного прибора в диагностической аппаратуре используется многоканальный компьютерный анализатор «Камертон» (рис. 5). Прибор позволяет проводить следующие исследования:
вибродиагностика физических процессов, происходящих в зоне резания на токарных, фрезерных и шлифовальных станках, динамического оборудования (металлорежущих станков, насосов, компрессоров, вентиляторов, турбин и др.);
диагностика методом ваттметрграфирования мощности процессов резания, мощности редукторов, электродвигателей, насосов, компрессоров, вентиляторов, турбин, глубинных штанговых насосов, станков-качалок и др.
В лабораторной работе прибор «Камертон» позволяет принимать, измерять, записывать, преобразовывать и анализировать любые сигналы по 8 каналам с датчиков силы, вибрации, температуры, мощности, оборотов, шума. Диапазон рабочих частот и диапазоны измерения виброускорения и виброскорости достаточно широк – от 5 до 5000 Гц. Диапазоны измерения виброускорения (пик), 0,5–80 м/с2. Диапазоны измерения виброскорости (СКЗ) 0,8–100 мм/с.
148
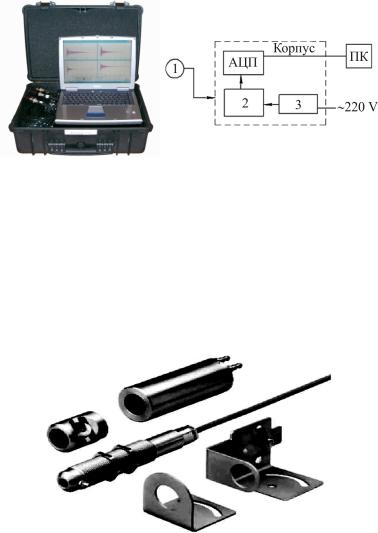
а б
Рис. 5. Многоканаль ый прибор для измерения и анализа вибрации «Камертон»: а – общий вид; б – принципиальная схема: 1 – датчик; 2 – платафильтров; 3 – одуль подзарядки; ПК– персональныйкомпьютер
Пирометр
Для бесконтактного измерения те пературы резания в диапазоне от 0 до 500 ºС «IN 3000» применяе ся стационарный инфракрасный п рометр (рис. 6).
Рис. 6. Инфракрасный бесконтактный пирометр IN 3000 для измерения температуры резания
Данный пирометр имеет фиксированную установку коэффициента излучения 95 % оптическое со тношение (соотношение расстояния до объекта к нтроля и диаметра области измерения) 5:1.
149
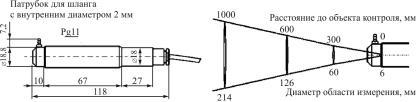
Эти характеристики в сочетании с временем отклика 300 м/с позволяют решать различные задачи измерения (рис. 7).
Рис. 7. Размеры инфракрасного пирометра
Принцип действия: оптическая система пирометра, наведенная на выбранный для измерения объект, фокусирует излучаемую им инфракрасную энергию на один или несколько фоточувствительных детекторов. Детектор конвертирует инфракрасную энергию в электрический сигнал.
Пирометр IN3000 удовлетворяет требованиям исследования температуры в процессе резания с подключением и анализом на приборе «Камертон». Недостатком является узкий диапазон измеряемой температуры: от 0 до 500 ºС, в то время как температура в зоне резания может достигать при скоростной обработке 800 °С, а на поверхности трения по передней грани даже 1200 °С и выше.
Датчик шума
Для измерения уровня шума в процессе резания применяется датчик шума МКУ-1, который представляет собой электретный микрофон с активным усилителем (рис. 8). Полоса частот воспринимаемого звука находится в диапазоне от 150 до 10000 Гц. Максимальное расстояние передачи сигнала по проводу диаметром 0,5 мм (не менее) 1000 м. Габариты датчика 28×7×7 мм. Диапазон громкости звука 65…105 Дб.
Микрофон – электроакустический преобразователь, с помощью которого акустические колебания в воздушной среде преобразуются в электрический сигнал.
150