
книги / Научно-исследовательская работа магистров по технологии машиностроения
..pdf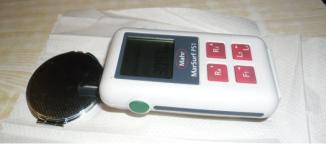
ховатости поверхностей крупногабаритных деталей привод с датчиком снимается со стойки и устанавливается непосредственно на поверхность детали.
Измерение шероховатости с помощью профилометра-профилографа модели MarSurf PS1
Переносной ручной профилометр-профилограф модели MarSurf PS1 (рис. 15) предназначен для измерения шероховатости в цеховых условиях. Прибор позволяет измерять основные параметры шерохова-
тости Ra , Rz , Rmax , S , Sm , tp непосредственно на плоских и цилинд-
рических поверхностях деталей независимо от их габаритных размеров. Основные параметры и порядок проведения измерений изложен в прилагаемой к методическому пособию инструкции изготовителя.
Рис. 15. Профилометр-профилограф модели MarSurf PS1 для измерения шероховатости в цеховых условиях
Порядок выполнения работы
Ознакомиться с устройством прибора MarSurf PS1 и порядком измерения согласно прилагаемой инструкции.
Провести измерение шероховатости представленных преподавателем образцов деталей и результаты занести в общую таблицу.
Записать профилограммы измеренной шероховатости на компьютере и отпечатать на принтере, занести их в отчет
Провести сравнение результатов измерения шероховатости образцов деталей на приборах и образцах сравнения контактным и бесконтактным методами и записать в отчет.
81
Содержание отчета
Отчет о работе должен включать в себя:
1)кратко сформулированную цель работы;
2)таблицу с основными метрологическими характеристиками прибора МИС-11, образцов шероховатости и прибора MarSurf PS1;
3)схему измерения прибора МИС-11;
4)сравнительную таблицу с результатами измерений, расчетов
ипрофилограмм всех образцов на всех приборах;
5)общее заключение по работе.
Вопросы к зачету
1.Каковы причины появления шероховатости?
2.Какими показателями характеризуется шероховатость поверхности?
3.Что такое Ra, Rz, Sm, tp?
4.Как обозначается шероховатость поверхности на чертежах?
5.Как влияют режимы резания – скорость резания, подача, глубина резания – на шероховатость? Четвертый закон резания.
6.Как влияет геометрия инструмента на шероховатость?
7.Какие приборы используются для определения шероховатости поверхности в цеховых и стационарных условиях?
8.Принцип работы прибора МИС 11.
9.Принцип работы прибора MarSurf PS1, анализ параметров профилограмм.
8.Устройство образцов сравнения шероховатости, применение.
82
|
|
|
Приложение 1 |
|
Параметры шероховатости |
|
|
|
|
|
|
Класс |
Наибольшие значения |
Базовая |
|
Шероховатости |
параметров шероховатости, мкм |
длина, мм |
|
(cтарый ГОСТ) |
Ra |
Rz |
l |
1 |
80 |
320 |
8 |
2 |
40 |
160 |
8 |
3 |
20 |
80 |
8 |
4 |
10 |
40 |
2,5 |
5 |
5 |
20 |
2,5 |
6 |
2,5 |
10 |
0,8 |
7 |
1,25 |
6,3 |
0,8 |
8 |
0,63 |
3,2 |
0,8 |
9 |
0,32 |
1,6 |
0,25 |
83
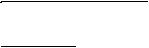
Приложение 2
Шероховатость поверхности и квалитеты при обработке деталей резанием (образцы сравнения шероховатости)
|
|
|
Значения |
|
|
|
|
|
|||
Вид обработки |
параметрамкм |
Rа, |
|
|
|
Квалитеты |
|||||
|
экономичные |
|
|
|
|
|
|
|
|
|
достижимые |
|
1 |
|
|
2 |
|
|
|
|
3 |
4 |
|
Отрезка |
пилой |
|
25... |
50(12,5) |
15 |
...17 |
– |
||||
|
резцом |
|
25…10 |
14... |
17 |
– |
|||||
|
фрезой |
|
25…50 |
14... |
17 |
– |
|||||
|
абразивом |
|
3,2…6,3 |
12... |
15 |
– |
|||||
|
черновое |
|
6,3... |
12,5 |
|
|
|
|
|
||
Фрезерование |
чистовое |
|
3,2…6,3(1,6) |
12 |
...14 (11) |
|
|||||
торцовой фрезой |
тонкое |
|
(0,8)... |
1,6 |
|
|
11 8,9 |
10 6,7 |
|||
Фрезерование |
черновое |
|
25... |
50 |
12... |
14 (11) |
– |
||||
цилиндрической |
чистовое |
|
3,3... |
6,3 |
|
|
11(10) |
– |
|||
фрезой |
тонкое |
|
|
|
|
|
|
|
8,9 |
6,7 |
|
Фрезерование |
черновое |
|
|
3,2 |
|
12... |
14 |
11 |
|||
скоростное |
чистовое |
|
0,8... |
1,6 |
11... |
13 |
8,9 |
||||
Сверление |
до 15 мм |
|
6,3…12,5 |
12... |
14 |
10,11 |
|||||
|
свыше 15 мм |
|
12,5... |
25 |
12... |
14 |
10,11 |
||||
Рассверливание |
12,5...25(63) |
|
12... |
14 |
|
|
|
10,11 |
|||
Зенкерование |
черновое (по кор- |
|
12,5... |
25 |
|
12…15 |
– |
||||
|
ме) чистовое |
|
3,2... |
6,3 |
|
|
10,11 |
8,9 |
|||
Растачивание |
черновое |
|
50... |
100 |
|
15…17 |
– |
||||
|
получистовое |
|
12,5... |
25 |
12... |
14 |
– |
||||
|
чистовое тонкое |
|
1,0... |
3,2(0,8) |
|
|
8,9 |
7 |
|||
|
(алмазное) |
|
0,4... |
0,8(0, 2) |
|
|
|
7 |
6 |
||
Развертывание |
получистовое |
|
6,3... |
12,5 |
|
|
9,10 |
8 |
|||
|
чистовое |
|
1,6... |
3,2 |
|
|
7,8(8) |
– |
|||
|
тонкое |
|
(0,4)... |
0,8 |
|
|
|
7 |
6 |
||
Протягивание |
получистовое |
|
|
0,3 |
|
|
|
8,9 |
– |
||
|
чистовое |
|
0,8... |
3,2 |
|
|
7,8 |
– |
|||
|
отделочное |
|
0,2... |
0,4 |
|
|
|
7 |
6 |
||
Зенкерование |
угловое плоское |
|
3,2... |
6,3 |
|
|
|
– |
– |
||
|
с направлением |
|
6,3... |
12,5 |
|
|
|
– |
– |
||
Слесарная опиловка |
|
(1,6)... |
25 |
|
|
8…11 |
6,7 |
||||
Шлифование |
получистовое |
|
3,2... |
6,3 |
|
|
8…11 |
– |
|||
круглое |
чистовое |
|
0,8... |
1,6 |
|
|
6... |
8 |
– |
||
|
тонкое |
|
0,2... |
0,4 (0,1) |
|
|
|
5 |
выше 5-го |
84
Окончание таблицы
|
1 |
2 |
3 |
4 |
Шлифование |
получистовое |
3,2 |
8…11 |
– |
плоское |
чистовое |
0,8…1,6 |
6…8 |
– |
|
тонкое |
0,2...0,4 (0,1) |
6,7 |
6 |
Прошивание |
чистовое тонкое |
0,4...1,6 |
7...9 |
– |
|
|
0,05...1,6 |
6,7 |
– |
Калибрование |
после сверления |
0,4…1,6 |
8,9 |
7, 6 |
отверстийшари- |
растачивания |
0,4...1,6 |
7 |
|
комилиоправкой |
развёртывания |
0,05...1,6 |
7 |
|
Притирка |
чистовая |
0,4...3,2 |
6,7 |
– |
|
тонкая |
0,1...1,6 |
5 |
– |
Полирование |
обычное |
0,2...1,6 |
6 |
– |
|
тонкое |
0,05...0,1 |
5 |
– |
Доводка |
грубая |
0,4 |
6,7 |
5 |
|
средняя |
0,1...0,2 |
5,6 |
5 |
|
тонкая |
0,05 |
5 |
выше 5-го |
|
отделочная (зер- |
0,012...0,025 |
– |
– |
|
кальная) |
|
|
|
Хонингование |
плоскостей |
0,1...0,4 |
7,8 |
6 |
|
цилиндров |
0,05...0,1 |
6,7 |
– |
Суперфиниши- |
плоскостей |
0,2...0,4(0,05) |
5 и точнее |
– |
рование |
цилиндров |
0,1...0,4 |
6 и точнее |
|
|
|
(0,05) |
|
|
Обработка зубь- |
строгание |
3,2...6,3 (1,6) |
7…10 |
– |
ев зубчатых ко- |
фрезерование шли- |
(1,6)...3,2 |
7...10 |
– |
лес |
фование |
0,4...0,6 |
5,6 |
– |
|
шевингование |
0,8...1,6 (0,4) |
5,6 |
– |
Анодно- |
черновое чистовое |
1,6...3,2 |
6...9 |
– |
механическое |
притирочное отде- |
0,2...0,8 |
6,7 |
– |
шлифование |
лочное |
0, 4...0,1 |
5...7 |
– |
|
|
0,05...0,2 |
5.6 |
– |
Электроискровое |
шлифование |
3,2…2,5 |
8...10 |
– |
Электроконтактное сверление |
2,5...100 |
12...14 |
– |
|
Электрополиро- |
декоративное |
0,4...3,2 |
6…9 |
– |
вание(взнамена- |
никелевых покры- |
1,6...12,5 |
|
– |
телезначениеRа |
тий |
0,4…0,8 |
|
|
исх. поверхности) |
|
1,6...3,2 |
|
|
Нарезание резьбы |
фрезой |
3,2...6,3 (1,6) |
8 |
– |
Шлифование резьбы |
1,6...3,2(0,4) |
4...6 |
– |
|
Накатывание, резьбы роликами |
0,4...0,8 |
6...8 |
– |
|
Ультразвуковая обработка твердых |
0,2...0,8 |
– |
– |
|
сплавов |
|
|
|
|
85
Лабораторная работа № 5 ВЫБОР ШЛИФОВАЛЬНЫХ КРУГОВ И РАСЧЕТ РЕЖИМА РЕЗАНИЯ
ПРИ КРУГЛОМ ШЛИФОВАНИИ
Цель работы – изучить конструктивные особенности, назначение и применение шлифовальных кругов, изучить новую маркировку шлифовальных кругов по ИСО, методику выбора шлифовальных кругов и расчета режима резания при шлифовании аналитическим способом. Приобрести навыки работы со справочной литературой.
Общие сведения
Шлифование – процесс резания материалов с помощью абразивного инструмента, режущими элементами которого являются абразивные зерна. Движение резания при шлифовании – вращение шлифовального круга, движение подачи – возвратно-поступательное движение стола станка с заготовкой и (или) поступательное движение шлифовальной бабки со шлифовальнымкругом.
Понятие об абразивном инструменте. Характеристики абразивного инструмента. Назначение. Применение
Шлифование представляет собой операцию обработки поверхности заготовки абразивным инструментом. Абразивный инструмент чаще всего включает в себя три элемента: абразивный материал, связку и поры.
Под абразивными понимаются материалы естественного или искусственного происхождения, зерна которых обладают высокой твердостью и способностью резания. Абразивные инструменты могут быть изготовлены со связанными зернами (шлифовальные круги, головки, сегменты, бруски, шкурки) (рис. 1) и в виде несвязанных, свободных зерен (пасты, суспензии, порошки). Абразивные инструменты характеризуются материалом зерен и их величиной, видом связки, твердостью, структурой, формой и размерами.
86
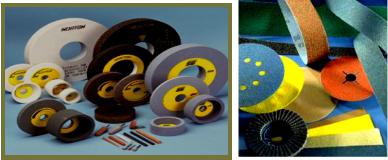
Рис. 1. Общий вид абразивных инструментов со связанн м абразивом: круги, бруски и ленты
А мазные круги и бруски дополн тельно характе изуются конструкцией и маркой алмазов.
Абразивные материалы делятся на искусственные (синтетические) и естественные (природные).
И кусственные бразивные материалы. К н м относятся электрокорунд, карбид кремния (карб рунд), карбид бора, синтети-
ческие алмазы, кубический нитрид |
ора (эльбор). |
Более широко |
применяются в промышленности, чем естественные. |
|
|
Электрокорунд (А 12О3). Большая |
часть (≈80 %) абразивного |
инструмента изготавли вается из электрокорунда, который получают путем плавки глинозема в электрических печах. Существует несколько разновидностей электрокорунда:
Э – электрокорунд нормальный (91…99 % А12О3) (марки: 16А, 15А, 14А, 13А, 1 2А); применяется при черново м, получистовом и чистовом шлиф вании сталей и чугунов, а такж для обдирки литья и при заточке режущих инструментов из инструментальной стали.
ЭБ – электрокорунд белый (9 …99 % А12О3) (марки: 25А, 24А, 2 3А, 22А); превосходит по своим режущим св йствам электрокорунд нормальный, так как содержит меньше пр месей. Находит наиболее широкое применение. Применяется при шлифовании прочн ых и вязких сталей (незакаленны х и закаленных), ковкого чугуна, заточки инструментов из быстро ежущих сталей.
87
ЭХ – электрокорунд хромистый (97 % А12О3+2 %CrO) (марки: 34А, 33А, 32А); получают в электропечах при плавке глинозема
сдобавлением хромистой руды. Зерна имеют розовую окраску. ЭХ применяют при повышенных режимах шлифования углеродистых и конструкционных сталей и при чистовой обработке. ЭТ – элек-
трокорунд титанистый марки 37А (содержит ≈97 % А12О3 и 2 % ТiO2); при плавке глинозема добавляют соединения титана. Титанистый электрокорунд (ЭТ) представляет собой соединения 98,5 %
А12О3 + 1,5 % ТiO2, отличается от нормального электрокорунда большей вязкостью и стабильностью свойств, что хорошо для дово- дочно-притирочных работ.
М – монокорунд (97 % А12О3), его зерна представляют собой отдельные кристаллы и имеют большое число режущих граней (марки: 45А, 44А). Он получается из боксита оксисульфидным способом в виде зерен, состоящих из изометрических кристаллов корунда различной величины. Сущность способа получения монокорунда состоит в сплавлении боксита с сернистым железом и восстановителем – антрацитом или коксом – в электропечах. Применяется для обработки весьма прочных сталей, ковкого чугуна, быстрорежущей стали.
Хромтитанистый электрокорунд (ЭХ+ЭТ) марки 91А, 92А имеет более высокие режущие свойства, чем Э и ЭБ. Применяют при повышенных режимах шлифования углеродистых и конструкционных сталей и при чистовой обработке.
Карбид кремния (SiС) – химическое соединение кремния с углеродом, получается при спекании кварцевого песка и кокса. Зерна SiС имеют более высокую твердость, чем электрокорунд. Применяются две разновидности карбида кремния: черный КЧ (95…97 % SiС) марок 55С, 54С, 53С, 52С и карбид кремния зеленый КЗ (98…99 % SiС) марок 64С, 63С, 62С. Карбид кремния зеленый более твердый, но менее прочный, чем карбид кремния черный. Недостаток карбида кремния – высокая хрупкость, малая прочность адгезионная активность к сталям. Поэтому при обработке сталей он почти не используется. Карбид кремния применяется при заточке
88
твердосплавного инструмента, шлифовании титана, абразивной обработке цветных и хрупких материалов: чугунов, бронзы; тугоплавких сплавов, металло- и минералокерамики, а также неметаллических материалов – резины, кожи, стекла, мрамора и т.д.
Карбид бора (В4С) – химическое соединение бора с углеродом – получают плавлением борной кислоты В2О2 с нефтяным коксом при температуре 2000...2350 °С. Карбид бора имеет высокую твердость, большую хрупкость и применяется в виде порошков для доводочных процессов и при ультразвуковой обработке хрупких материалов
ивесьма твердых – рубина, корунда, кварца. При доводке твердосплавных режущих инструментов обеспечивает минимальный радиус округления режущей кромки до 6…10 мкм, тогда как электрокорунд обеспечивает только до 15 мкм.
Борсиликарбид в отличие от карбида бора не содержит вредной примеси графита, отличается большей стабильностью свойств, более прочный и дешевый. На операциях доводки показал на 30…40 % более высокую производительность, чем карбид бора.
Окись хрома – порошок темно-зеленого цвета для доводки. Получается из бихромата калия с примесью серы.
Окись железа (крокус) – тонкий полировальный порошок, состоящий в основном из кристаллической окиси железа. Получается переработкой железного купороса и щавелевой кислоты.
Синтетические алмазы (АС) получают в виде мелких кристаллов,
размером обычно не более 1 мм. Синтез алмазов происходит в результате воздействия на графит высоких давлений (до 1,7·105 кгс/см2)
ивысоких температур (до 2500 °С). В присутствии металлического катализатора происходит перекристаллизация углерода из гексагональной структуры графита в кубическую структуру алмаза. Синтетические алмазы в зависимости от прочности делятся на пять марок: низкой прочности (АСО), повышенной прочности (АСР), высокой прочности (АСВ), монокристальные (АСК и АСС).
Марка АС2 обычной прочности, предназначена для изготовления инструментов на органической связке, а также паст и порошков.
Марка АС4 повышенной прочности, применяется для инструментов на керамической и металлической связках.
89
Марка АС6 высокой прочности, применяется для инструментов на металлической связке, для чернового шлифования.
Марка АС15 по прочности близка к прочности природных алмазов.
Наряду с монокристаллическими алмазными зернами выпускаются поликристаллические, которые обозначаются АР.
Алмазные микропорошки марок АСМ, АМ, АСН, АН предназначены для притирочных и доводочных работ при доводке твердых сплавов и сталей, а также алмазов и рубинов.
Основное применение – шлифование твердых керамических
ититановых сплавов, заточка и переточка инструментов. В последнее время применяется для обработки композитов.
Отрицательное свойство алмазов заключается в том, что при обработке стальных заготовок при температуре 850…900 °С наблюдается активная диффузия углерода из алмаза в железо, что резко повышает износ алмаза. В таких случаях лучше применять кубический нитрид бора.
Кубический нитрид бора (КНБ, боразон или эльбор) состоит из 44 % бора и 56 % азота. Твердость его ненамного уступает алмазу, а теплостойкость в 2 раза выше алмаза (до 1500…1900 °С). Процесс изготовления достаточно сложен (рис. 2). Требуется обеспечить высокое давление, до 90 000 бар, и высокую температуру, до 2200 °С. В результате гексогональная структура решетки исходного материала BN переходит в высокопрочную кубическую структуру решетки CBN. Круги из эльбора наиболее эффективны при чистовом шлифовании, заточке и доводке инструментов из быстрорежущих сталей повышенной производительности (кобальтовых и высокованадиевых). Эльбор в России выпускается двух марок: ЛО – обычной механической прочности с обычным содержанием основной фракции
иЛП – повышенной механической прочности, с повышенным содержанием основной фракции.
Всводной табл. 1 приведены основные механические свойства рассмотренных искусственных абразивных материалов.
90