
книги / Научно-исследовательская работа магистров по технологии машиностроения
..pdfРазновидностью микрометрического метода измерения износа является профилографирование. При этом могут использоваться два варианта этого метода. Первый из них применяется, когда на детали или образце имеются изношенный и неизношенный участки. При снятии профилограммы этих двух участков по высоте «уступа» можно оценить износ, а также изменение шероховатости поверхности. Когда изнашиваются лишь выступы микронеровностей, приме-
няют способ наложения профилограмм, снятых с одного и того же участка до и после изнашивания. Для точного совмещения профилограмм на поверхности наносят контрольную риску. При этом можно судить не только о средней величине износа, но и о росте площади опорной поверхности. Точность измерения зависит от условий касания и погрешности повторной проверки.
Находят применение различные варианты рассматриваемого мето-
да: методотпечатков, метод вырезанныхлуноки методслепков.
Если измерить износ непосредственно на детали трудно, ис-
пользуют метод негативных отпечатков (слепков). С поверхности детали в том месте, где нанесено углубление (обычно отпечаток или специальная риска), снимают слепок из самотвердеющей массы или оттиск на пластичном металле или пластмассе. Высоту отпечатка измеряют обычными способами и сравнивают с размером, снятым при вторичном оттиске изношенной поверхности.
Особенности измерения износа режущих инструментов. Ре-
жущие инструменты изнашиваются более интенсивно по сравнению с изнашиванием большинства деталей машин в процессе их эксплуатации. Независимо от геометрии износа, мерой износа инструмента является линейный и массовый износ. При чистовой обработке в качестве критерия затупления выбирают линейный износ. Об изношенности задней поверхности судят по максимальной ширине площадки износа hз. Для исследования физической природы износа инструментов используют массовый износ – масса изношенной части инструмента, которая пропорциональна работе сил трения, затраченной на превращение инструментального материала в продукты изнашивания. Измерение фаски износа производят при помощи индикаторных устройств или на микроскопе. Износ по передней по-
51
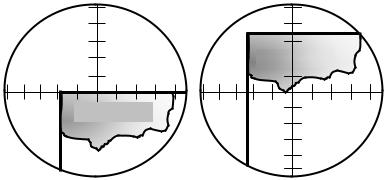
верхности (лунку износа) измеряют с помощью микроскопа, инди-
каторными щупами, а также профилографированием передней
поверхности на профилометре.
Измерение износа с помощью инструментальной лупы
имикроскопа ММИ-2. Для измерения износа резца по главной задней поверхности используется инструментальная лупа и различные микроскопы типа ММИ-2. В поле зрения микроскопа (рис. 6) видны две сплошные взаимно перпендикулярные риски со шкалой.
Многогранная неперетачиваемая пластина (МНП), которой оснащен резец, устанавливается на столе микроскопа с помощью призмы или пластилина таким образом, чтобы боковая (главная задняя) поверхность пластины была обращена к окуляру микроскопа
ирасполагалась перпендикулярно его оптической оси. Вращая микрометрические винты стола микроскопа, совмещаем одну из взаимно перпендикулярных рисок окуляра с главной режущей кромкой (рис. 6, а) и считываем показания на барабане микрометрического винта. Затем, продолжая вращать микрометрический винт, устанавливаем риску окуляра по границе максимального износа (рис. 6, б)
иснова считываем показания барабана. Разница этих показаний даст величину, соответствующую ширине фаски износа по задней поверхности.
фаска износа
фаска износа
|
|
|
|
|
|
|
|
|
|
|
|
|
|
|
|
|
|
|
|
а |
б |
|
Рис. 6. Поле зрения микроскопа
52
Современный микроскоп РСЕ-ММ200 с 200-кратным увеличением позволяет записывать показания микроскопа, делать снимки на персональный компьютер. В работе требуется ознакомиться с устройством и порядком применения согласно инструкции в ПК.
Методика проведения лабораторной работы
Исследование проводится при определенном режиме резания, для чего станок настраивается на заданные частоту вращения шпинделя и подачу So, устанавливается определенная глубина резания и время. Производится один рабочий ход при заданных параметрах режима резания, замеряется время рабочего хода с помощью часов с секундной стрелкой или секундомера. По окончании рабочего хода многогранная режущая пластина снимается с резца и производится измерение износа согласно указанной методике. Износ измеряется в том месте по длине режущей кромки, где он имеет максимальную величину. Полученные результаты заносятся в табл. 1. Резание повторяется, и снова проводится измерение износа. При этом в таблицу записывается суммарное время двух рабочих ходов. Опыты продолжаются до достижения катастрофического износа (полное разрушение режущей кромки) или до заранее заданного преподавателем критерия затупления hЗк. По полученным данным строится график зависимости износа от времени работы инструмента (рис. 7). График позволяет определить стойкость Т при заданном критерии затупления hЗк. Для этого проводится горизонтальная линия из точки hЗк до пересечения с кривой износа.
|
|
Таблица 1 |
|
|
|
|
|
Номер |
Время, мин |
Величина износа по задней |
|
опыта |
поверхности, мм |
||
|
|||
1 |
10 |
|
|
2 |
20 |
|
|
3 |
30 |
|
|
4 |
40 |
|
|
5 |
50 |
|
53
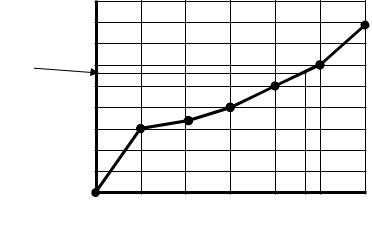
|
h, мм |
|
|
|
|
|
|
|
0,40 |
|
|
|
|
|
|
|
0,35 |
|
|
|
|
|
|
hЗ |
0,30 |
|
|
|
|
|
|
|
0,25 |
|
|
|
|
|
|
|
0,20 |
|
|
|
|
|
|
|
0,15 |
|
|
|
|
|
|
|
0,10 |
|
|
|
|
|
|
|
0,05 |
|
|
|
|
|
|
|
10 |
20 |
30 |
40 |
Т |
50 |
τ, мин |
Рис. 7. График зависимости износа от времени работы резца
Полученную точку пересечения сносят на ось времени τ, а отрезок до полученной точки соответствует стойкости Т в данном опыте. Например, на рис. 7 при hЗк = 0,28 мм стойкость Т = 47 мин
Порядок выполнения работы:
Ознакомиться с содержанием работы и методикой проведения исследований.
Получить 4 различные режущие пластинки с различной величиной износа.
Ознакомиться с устройством и работой измерительных луп различных фирм и с устройством микроскопа РСЕ-ММ200 с применением персонального компьютера.
Провести сравнительные измерения износа по задней поверхности всех пластинок различными инструментами и микроскопом
ирезультаты занести в таблицу.
Настроить токарный станок на заданный режим работы
имикроскоп для измерения износа.
Произвести опыты по точению заготовки с измерением износа через равные промежутки времени и записать результаты в табл. 1.
54
Построить график зависимости hз = f(τ) и определить стойкость при заданном критерии затупления.
Составить отчет по прилагаемой форме.
Содержание и форма отчета
1.Условия проведения опытов:
станок 16К20;
материал заготовки сталь 45
диаметр заготовки 60 мм;
частота вращения шпинделя n = 1000 мин–1;
подача S0 = 0,5 мм/об;
глубина резания t = 1,0 мм;
скорость резания V |
D n |
м/мин; |
|
1000 |
|
материал пластинки Т15К6.
2.Эскиз поля зрения микроскопа (см. рис. 6).
3.Результаты измерения износа.
4.График износа с указанием величины стойкости.
5.Выводы.
Вопросы к зачету
1.Виды износа режущих инструментов.
2.Стойкость режущих инструментов.
3.Зависимость износа и стойкости
–от режимов резания;
–от геометрии инструмента;
–от материала инструмента;
–от материала заготовки;
–от СОЖ.
4.Классическая кривая износа.
5.Критический и катастрофический износ.
6.Пути повышения износостойкости режущих инструментов.
55
Лабораторная работа № 4 ОПРЕДЕЛЕНИЕ ШЕРОХОВАТОСТИ ПОВЕРХНОСТИ ДЕТАЛИ
Цель работы – практическое ознакомление с параметрами, характеризующими шероховатость поверхности детали, методами оценки и средствами измерения (оценки) шероховатости контактным и бесконтактным способами.
Приборы и оборудование
Приборы MarSurf PS1, МИС 11, образцы сравнения, образцы деталей разной шероховатости (4 наименования).
Общая часть
Основные понятия и определения. Шероховатостью поверхно-
сти, согласно ГОСТ 25142-82, называется совокупность микронеровностей поверхности с относительно малыми шагами, выделенную с помощью базовой длины.
Базовая длина l – длина базовой линии, используемая для выделения неровностей, характеризующих шероховатость поверхности. Числовые значения базовой длины выбираются из ряда (0,01); (0,03); 0,08; 0,25; 0,80; 2,5; 8; (25) мм (значения, указанные в скобках применяются в особых случаях).
Базовая линия (поверхность) – линия (поверхность) заданной геометрической формы, определенным образом проведенная относительно профиля (поверхности) и служащая для оценки геометрических параметров поверхности.
Шероховатость поверхности является следствием поверхностного пластического деформирования поверхностного слоя детали при образовании стружки, копирования неровностей режущих кромок инструмента и трения его о деталь и т.д.
Числовые значения шероховатости поверхности определяются от единой базы, за которую принимается средняя длина профиля m, т.е. базовая линия, имеющая форму номинального профиля и проведенная так, что в пределах базовой длины среднее квадратичное
56
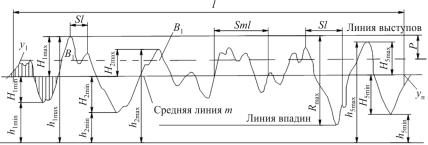
отклонение профиля до этой линии минимально. Система отсчета шероховатости от средней линии профиля называется системой средней линии (рис. 1).
Рис. 1. Профилограмма шероховатости поверхности по ГОСТ 2789-74
Согласно ГОСТ 2789-74, шероховатость поверхности изделий независимо от материала и способа изготовления (получения) поверхности можно оценить количественно одним или несколькими параметрами: средним арифметическим отклонением профиля Ra ,
высотой неровностей профиля по десяти точкам Rz , наибольшей высотой неровностей профиля Rmax , средним шагом неровностей Sm , средним шагом местных выступов профиля S, относительной опорной длиной профиля tp .
Параметры поверхности, связанные с высотными свойства-
ми неровностей. Ra – среднее арифметическое отклонение профи-
ля из абсолютных значений отклонений профиля в пределах базовой линии:
l |
|
|
|
n |
|
|
|
|
|
Ra 1l 0 |
|
y x |
|
dx , или Ra 1n i 1 |
|
Yi |
|
, |
(1) |
|
|
|
|
||||||
|
|
|
|
|
|
|
|||
где l – базовая длина; n |
|
– число выбранных точек профиля на ба- |
зовой длине; y – отклонение профиля, т.е. расстояние между лю-
бой точкой профиля и средней линией, измеренное по нормали, проведенной к средней линии через эту точку профиля (см. рис. 1).
57
Высота неровностей профиля по десяти точкам Rz – сумма
средних абсолютных значений высот пяти наибольших выступов профиля и глубин пяти наибольших впадин профиля в пределах базовой длины:
Rz |
1 |
S |
Hi max |
S |
Hi min |
|
, |
(2) |
5 |
|
|
|
|||||
|
i 1 |
|
i 1 |
|
|
|
|
|
где Hi max – высота i-го наибольшего выступа профиля; Hi min |
– глу- |
бина i-й наибольшей впадины профиля. Для случая, когда отклонения профиля определяются относительно произвольной прямой, параллельной средней линии и не пересекающей профиль,
Rz |
1 |
S |
S |
|
, |
(3) |
5 |
hi max hi min |
|||||
|
i 1 |
i 1 |
|
|
|
где hi max – расстояние от высшей точки i-го наибольшего выступа до линии отсчета; hi min – расстояние от низшей точки i-й наибольшей впадины до линии отсчета.
Наибольшая высота неровностей профиля Rmax – расстояние
между линией выступов профиля и линией впадин профиля в пределах базовой длины:
Rmax Hmax Hmin .
При возможности осуществления выбора предпочтение должно отдаваться параметру Ra .
Параметры шероховатости, связанные со свойствами неровностей в направлении длины профиля. Средний шаг неровностей профиля Sm – среднее значение шага неровностей профиля в пре-
делах базовой длины,
|
1 |
n |
|
Sm |
Smi , |
(4) |
|
|
n i 1 |
|
где n – число шагов в пределах базовой длины l ; Smi – шаг неровностей профиля, равный длине отрезка средней линии, пересекаю-
58
щей профиль в трех соседних точках и ограниченный двумя крайними точками (см. рис. 1).
Средний шаг местных выступов профиля S – среднее значение шага местных выступов профиля в пределах базовой длины,
|
1 |
n |
|
S |
Si , |
(5) |
|
|
n i 1 |
|
где n – число шагов неровностей по вершинам в пределах базовой длины l ; Si – шаг неровностей профиля по вершинам, равный дли-
не отрезка средней линии между проекциями на нее двух наивысших точек соседних выступов профиля (см. рис. 1).
Параметры шероховатости, связанные с формой неровностей профиля. Опорная длина профиля p – сумма длин отрезков bi , отсе-
каемых на заданном уровне p в материале профиля линией, эквидистантной средней линии m в пределах базовой длины (см. рис. 1),
|
n |
|
|
p bi . |
(6) |
||
i 1 |
|
||
Относительная опорная длина профиля tp |
– отношение опор- |
||
ной длины профиля к базовой длине, |
|
||
tp |
p |
. |
(7) |
|
|||
|
l |
|
Опорная длина профиля p определяется на уровне сечения профиля p , т.е. на заданном расстоянии между линией выступов
профиля и линией, пересекающей профиль эквидистантно линии выступов профиля.
Линия выступов профиля – линия, эквидистантная средней линии, проходящая через высшую точку профиля впределах базовой длины.
Значение уровня сечения профиля p отсчитывается от линии выступов и выбирается из ряда: 5; 10; 15; 20; 25; 30; 40; 50; 60; 70; 80; 90 % от Rmax .
59
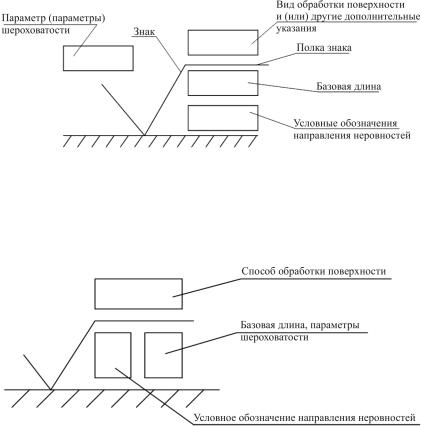
Обозначения шероховатости поверхностей. Ранее, согласно ГОСТ 2309-73, шероховатость поверхностей обозначалась на чертеже для всех выполняемых по заданному чертежу поверхностей детали, независимо от методов их образования, кроме поверхностей, шероховатость которых не обусловлена требованиями конструкции (прил. 1). Структура обозначения шероховатости приведена на рис. 2.
Рис. 2. Структура обозначения шероховатости поверхности по прежнему ГОСТ 2309-73
В 2003 году структура обозначения шероховатости изменилась согласно ГОСТ 2.309–2003 (рис. 3).
Рис. 3. Структура обозначения шероховатости поверхности по новому ГОСТ 2.309–2003
В обозначении шероховатости поверхности, вид обработки, которой конструктор не устанавливает, применяют знак, показанный
60