
книги / Основы металловедения и термообработки
..pdfПри проведении закалки существует опасность коробления или даже растрескивания деталей вследствие возникновения значительных остаточных напряжений. Основной источник на
пряжений - увеличение объема при превращении аустенита в мартенсит. Опасные макроскопические напряжения возникают из-за неодновременности превращения по сечению детали, а также в закаливаемых деталях сложной формы.
Для осуществления закалки, т.е. для получения мартенсита, высокая скорость охлаждения необходима только в интервале температур минимальной устойчивости аустенита. Снижение скорости охлаждения в интервале температур мартенситного превращения Ми-М куменьшает напряжения закалки. В практике термической обработки стали широкое использование нашли способы закалки в двух средах, ступенчатой закалки и изотер мической закалки (рис. 66), когда деталь погружают в воду только на время охлаждения в интервале температур минималь ной устойчивости аустенита.
Рис. 66. Схема режимов при разных способах закалки:
1 - закалка в одном охладителе; 2 - закалка в двух средах;
3 - ступенчатая закалка; 4 - изотермическая закалка;
5 - идеальный режим охлаждения
При закалке в двух средах деталь после определенной вы держки в воде переносят в охлаждающую среду с меньшей ско ростью охлаждения, например в масло. При ступенчатой закал ке деталь из воды переносят в жидкую среду с температурой на 50-100 °С выше мартенситной точки М„, дают непродолжитель ную выдержку для выравнивания температуры по сечению и окончательно охлаждают на спокойном воздухе. Изотермиче ская закалка осуществляется переносом закаливаемой детали из воды в ванну с расплавленными солями, имеющими температуру на 50-100 °С выше температуры М„. После выдержки детали в ванне до полного распада аустенита на структуру нижнего бейнита ее окончательно охлаждают на воздухе. Закалка на нижний бейнит дает сочетание высокой прочности и вязкости стали.
В качестве охлаждающей среды при ступенчатой и изотер мической закалке применяют расплавленные соли (55 % KN03 и 45 % NaN02) и щелочи (20 % NaOH и 80 % КОН) в интервале температур 150-500 °С. Чем ниже температура расплава, тем выше скорость охлаждения в нем. Скорость охлаждения возрас тает при перемешивании. Если нагрев деталей под закалку про водится в не вызывающих окисления жидких слоях (NaCL, КС1, ВаС12), то после закалки в расплавах щелочи детали имеют чис тую поверхность светло-серого цвета. Закалку по этому способу называют светлой.
5.3. Термообработка легированной стали.
Влияние легирования на структурообразование
при термообработке стали
Стали, содержащие специально вводимые элементы, назы ваются легированными. Легирование стали имеет целью полу чение более высоких по сравнению с углеродистыми сталями механических свойств, а также придание стали специальных
свойств - коррозионной стойкости, жаростойкости, жаропроч ности и др. Следует отметить, что роль легирующих элементов в повышении свойств стали обусловлена их влиянием на про цессы структурообразования при термообработке стали (устой чивость аустенита при охлаждении, отпускоустойчивость мар тенсита, сдерживание роста зерна аустенита и т.п., рассмотрены ниже). В связи с этим применение более дорогих легированных сталей целесообразно только для деталей, подвергаемых термо обработке.
Принятая в России буквенно-цифровая система маркировки легированных сталей позволяет указать в марке стали содержа щиеся в ней легирующие элементы и их количество.
Основные легирующие элементы и их обозначение в марке стали: Сг - обозначается буквой X, Ni - Н, Мп (если > 0,8 %) - Г, Si (если > 0,4 %) - С, W - В, Mo - М, V - Ф, Al - Ю, Ti - T, Nb - Б, Со - К, Си - Д, В - Р. Концентрация Nb, Ti обычно » 0,1 %,
аВ < 0,005 % (микролегирование).
Вконструкционных легированных сталях обозначение ма рок сталей означает: первые две цифры показывают содержание углерода в сотых долях процента; после буквы, обозначающей
легированный элемент, указывается его среднее содержание
вцелых процентах, если оно больше 1 % (если меньше, или около
1% - цифра не ставится). Например, сталь 38ХНЗМФА содер жит - 0,38 % С, 1,2-1,5 % Сг, 3 % Ni, 0,3-0,4 % Mo, 0,1-0,2 % V.
Винструментальных сталях начальная цифра показывает содержание углерода в десятых долях процента. Если содержание углерода в стали около 1 % и более, начальную цифру не ставят.
По легированию стали могут называть хромистыми, мар ганцевыми, кремнистыми, хромоникелевыми, хромомарганце выми, хромоникельмолибденовыми и др.
По назначению легированные стали разделяют на конст рукционные, инструментальные и стали с особыми свойствами.
Влияние легирования на комплекс свойств стали эффек тивно проявляется только в термоупрочненном состоянии.
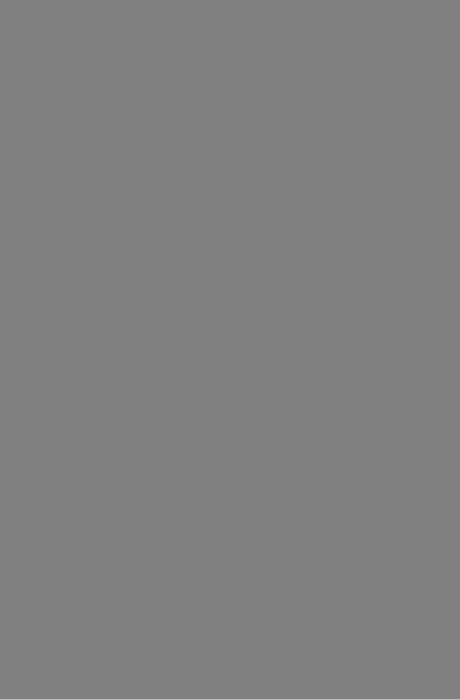
стойких дисперсных карбидов VC, TiC, NbC, ZrC сдерживает рост аустенитного зерна при повышении температуры нагрева легированных сталей при проведении закалки.
При высоком содержании карбидообразующих легирую щих элементов сталь становится заэвтектоидной при содержа нии углерода менее 0,8 % (сталь 40X13), а при высоком содер жании углерода (« 1 %) в структуре стали могут быть первич ные (ледебуритные) карбиды (инструментальные стали типа Х12МФ и быстрорежущие).
Легированный аустенит более устойчив при охлаждении ниже критической температуры А и чем аустенит углеродистой стали, что иллюстрируют кривые изотермического распада (рис. 67). Увеличение продолжительности минимального инку бационного периода уменьшает критическую скорость охлаж дения стали (Г,*), необходимую для обеспечения мартенситного превращения аустенита.
Рис. 67. Диаграммы изотермического превращения аустенита
углеродистых и легированных сталей: а - легирующие элементы
не образуют карбидов; б - легирующие элементы образуют карбиды
Повышение устойчивости аустенита при температурах ниже А\ имеет исключительно важное значение для практики термооб
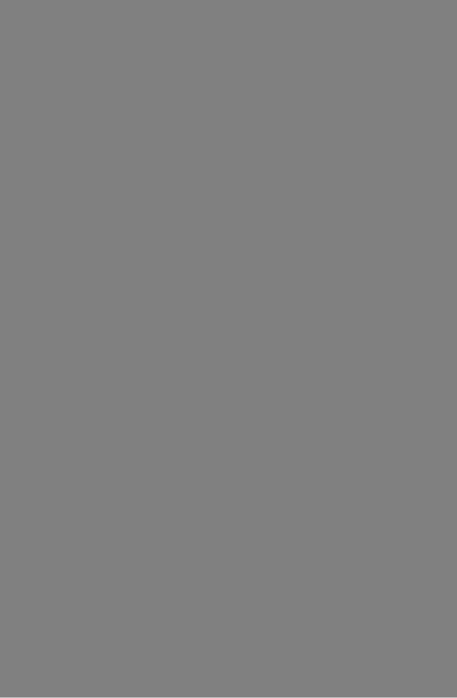
Скорость охлаждения при 700 °С
HRC |
105 |
23 |
13,5 |
7,5 °С/с |
|
|
|
|
|
50 |
|
|
|
|
40 |
|
|
|
|
30 |
|
|
|
|
20 |
|
|
|
|
10 |
|
I |
|
|
|
|
|
|
|
0 |
6 |
10 |
19 |
24мм |
Расстояние от закаливаем ого торца
а
Рис. 68. Определение прокаливаемости по торцовой пробе:
а - изменение твердости по длине образца после торцовой закалки: I - твердость полумартенситной зоны; 1 - сталь с низкой прокапиваемостью; 2 - сталь с высокой прокаливаемостью;
б - схема закалки образца
Легирующие элементы, вводимые в сталь и повышающие устойчивость аустенита при охлаждении, не только сдвигают вправо кривые изотермического превращения аустенита и изме няют их вид (см. рис. 67), но и изменяют температуру начала и завершения мартенситного превращения аустенита (темпера туры Мв и Мк). Стали, температура Мк которых ниже комнатной, после закалки содержат в структуре наряду с мартенситом зна чительное количество остаточного аустенита. Только А1 и Со повышают температуру мартенситного превращения, уменьшая количество остаточного аустенита.
Остаточный аустенит понижает твердость закаленной стали и, будучи нестабильной фазой, способен к распаду в процессе работы детали во времени, что может значительно изменить размеры детали и свойства стали. В связи с этим детали из ста
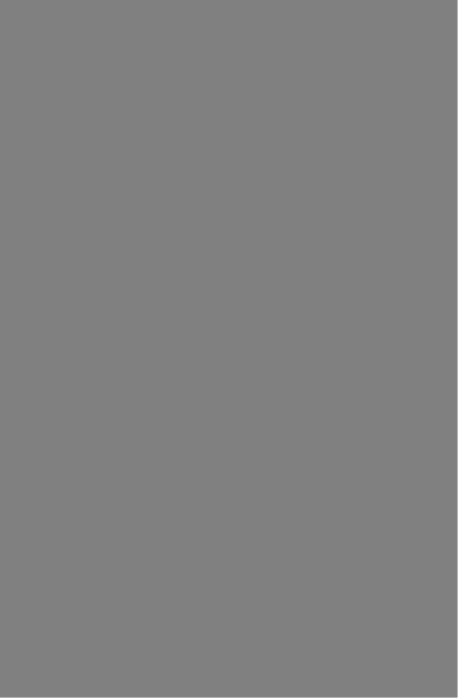
Рис. 69. Изменение твердости закаленных сталей при отпуске: У 12 - углеродистые стали; высоколегированные стали Х12
(2 % С, 12 % Сг), закалка от 950 °С; Р18 (0,75 % С, 18 % W, 4 % Сг, 1,2 % V), закалка от 1260 °С
Многие легирующие элементы повышают температурный интервал распада остаточного аустенита при отпуске до темпе ратур 400-580 °С. Наличие в твердом растворе легирующих элементов сдерживает выделение из остаточного аустенита спе циальных карбидов и повышает температуру отпуска, необхо димую для уменьшения легированное™ аустенита и превраще ния его в мартенсит при последующем охлаждении.
Как уже отмечалось, в результате отпуска мартенсита ха рактеристики прочное™ стали монотонно снижаются, а харак теристики пластичности - возрастают. По мере повышения температуры отпуска увеличивается и ударная вязкость стали. Однако есть два интервала температур отпуска, при которых ударная вязкость сталей заметно снижается: 250-350 и 500-600 °С (рис. 70) - температуры отпуска, вызывающие отпускную
хрупкость 1-го и 2-города соответственно. Природа охрупчивания сталей после отпуска при указанных температурах недостаточ но ясна, несмотря на многочисленные ее исследования.
Рис. 70. Влияние температуры отпуска и скорости охлаждения от температуры отпуска на ударную вязкость конструкционных легированных сталей (схема):
I - отпускная хрупкость 1-го рода; П - отпускная хрупкость 2-го рода
Отпускная хрупкость 1-го рода, называемая необратимой, наблюдается у всех сталей, независимо от степени легирования. Отпускная хрупкость 2-го рода наблюдается только у легиро ванных сталей - хромистых, марганцевых, хромоникелевых, хромомарганцевых и др. и проявляется только при медленном охлаждении деталей с температур отпуска. Быстрое охлаждение с температур отпуска (в воде или масле) предотвращает охруп чивание. Повторный нагрев на температуру отпуска с после дующим ускоренным охлаждением также ликвидирует охруп чивание стали (отпускная хрупкость 2 -го рода называется обра тимой). При невозможности ускоренного охлаждения с температуры отпуска (детали большого сечения) сталь допол нительно легируют Mo (0,3-0,4 %) или W (1-1,2 %), подавляю щих развитие отпускной хрупкости 2-го рода.