
книги / Основы металловедения и термообработки
..pdfа - по Бринеллю; б - по Роквеллу; в - по Виккерсу
Определение твердости по Бринеллю проводят на прессе вдавливанием в испытуемый материал стального закаленного шарика с последующим измерением диаметра отпечатка. Твер дость по Бринеллю обозначается НВ (размерность кг/мм2, МПа) и определяется по формуле;
HB = 2pjnD^D-^D2- d 2Y
где D - диаметр вдавливаемого индентора (шарика); d - диаметр отпечатка; Р - нагрузка.
Практически величину НВ определяют по диаметру отпечат ка, пользуясь таблицами, составленными для постоянных величин
P H D. При испытании стали, чугуна устанавливают D = |
10 мм |
и Р= 3000 кГс (Р = 30 D2), для меди и ее сплавов - D - |
10 мм |
иР = 1000 кГс (Р = 10 D1), для очень мягких металлов (алюминий
иего сплавы, боббиты и др.) - D = 10 мм и Р = 250 (Р = 2,5 D2). Недостатки метода: невозможность испытания материалов,
имеющих твердость свыше 450 НВ (возможна деформация ша рика) и непригодность метода для испытаний тонкого листа и тонкого упрочненного поверхностного слоя вследствие продавливания.
Подготовка поверхности для измерения твердости по Бринеллю может быть ограничена грубой шлифовкой. Метод наи более часто применяется для измерения твердости заготовок (поковки, прокат, литье и т.п.).
Существуют эмпирические формулы перевода значений твердости по Бринеллю (НВ, кг/мм2) в значения прочности
(ав, кг/мм2):
Сталь с твердостью НВ = 125-175 кг/мм2 |
а в = 0,343 НВ |
Сталь с твердостью НВ > 175 кг/мм2 |
ств = 0,362 НВ |
Алюминиевое литье |
о в = 0,260 НВ |
Бронза и латунь отожженные |
а в = 0,550 НВ |
Бронза и латунь наклепанные |
ств = (HB-4Ô) • 1/6 |
Серый чугун |
а в = 0,343 НВ |
Цинковые сплавы |
а в = 0,09 НВ |
Метод измерения твердости по Роквеллу основан на опре делении глубины вдавливания в испытуемый материал алмазно го конуса с углом при вершине 120° (для материалов с высокой твердостью) или стального шарика диаметром 1,59 мм (для ма териалов с относительно малой твердостью). Индентор вдавли вают последовательно нагрузками 10 кГс (предварительная) и основной 90 кГс (для шарика) или 140 кГс (для конуса), сум марная нагрузка 100 и 150 кГс соответственно.
Твердость по Роквеллу определяется в условных единицах, соответствующих перемещению наконечника на глубину 0,002 мм, и фиксируется на шкале прибора остановкой вра щающейся стрелки после снятия нагрузки. На приборе имеются две шкалы: черная - для измерений твердости конусом (обозна чение твердости HRC) и красная - для измерений шариком (HRB). Твердость сверхтвердых материалов (HRA) определяют вдавливанием конуса при суммарной нагрузке 60 кГс с отсчетом по черной шкале.
Сводные таблицы значений твердости по Бринеллю (НВ) и по Роквеллу (HRC, ЙКВ, HRA) позволяют переводить твер дость по Роквеллу с условных единиц в кг/мм2 (МПа).
Для определения твердости деталей малой толщины и тон ких поверхностных слоев используют метод Виккерса. На ис пытуемой поверхности приготавливают шлиф (полировка). В поверхность вдавливают алмазную четырехгранную пирамиду с углом между гранями 136°. Соразмерно толщине материала выбирают нагрузку (1, 2, 5, 10, 20, 30, 50 или 100 кГс). После снятия нагрузки с помощью микроскопа определяют среднее (из двух) значение диагонали отпечатка. Нагружающее устрой ство и микроскоп находятся на одной оси вращения. Твердость по Виккерсу (HV) каждой нагрузки определяют по таблицам в которых значениям HV (кг/мм2, МПа) соответствуют опреде ленные размеры диагоналей отпечатка.
Измерение микротвердости отдельных структурных со ставляющих проводится в микротвердомерах (тип ПМТ-3) ана логично измерению твердости по Виккерсу. Однако нагружаю щее устройство и микроскоп прибора рассчитан на небольшие нагрузки (5-500 г) и измерение диагоналей очень мелких отпе чатков (мкм). Перед измерением микротвердости на поверхно сти приготавливают микрошлиф.
3.4. Ударная вязкость металла
Кроме прочности и пластичности одной их важнейших ха рактеристик механических свойств металла является ударная вязкость, характеризующая его способность к поглощению энергии при динамическом (ударном) нагружении вплоть до разрушения. Ударная вязкость является характеристикой на дежности металла, так как позволяет оценить его способность выдерживать (релаксировать) локальные перегрузки в местах концентрации напряжений.
Ударной вязкостью называется работа, затраченная при разрушении ударным изгибом надрезанного образца, отнесенная к площади поперечного сечения образца в месте надреза (F0).
Ударную вязкость металлов определяют испытаниями раз рушением образцов на маятниковом копре, схема испытаний приведена на рис. 34. Образец устанавливают на двух опорах, затем наносят удар по его середине со стороны, противополож ной надрезу. Работа, затраченная на разрушение образца,
A =P ( H - h ) ,
где Р - масса маятника, кг; Я и h - высота подъема маятника до и после удара, м.
Рис. 34. Схема маятникового копра (а) и образца при испытании (б):
1 - маятник; 2 - образец; 3 - шкала; 4 - стрела; 5 - тормоз
В зависимости от вида надреза-концентратора ударную вязкость обозначают KCU, KCV и КСТ, КС - символ ударной вязкости, a U, V или Т означают вид концентратора: радиус над реза 1 мм, 0,25 мм или усталостная трещина соответственно.
Величина работы разрушения позволяет судить о том, как оно происходило: хрупко, т.е. без значительной пластической деформации (поверхность излома с блестками скола), или вязко- с затратой работы на пластическую деформацию металла, предшествующему разрыву его сплошности при образовании новой поверхности (неблестящий, матовый вид поверхности излома).
Принято считать, что работа разрушения складывается из работы пластической деформации металла, приводящей к обра зованию трещины критического размера, и работы распростра нения трещины (работы образования поверхности разрушения). Вторая составляющая работы разрушения наиболее показатель но характеризует степень склонности металла к хрупкому раз рушению. Именно в связи с этим испытания образцов с концен траторами в виде трещины наиболее эффективны для сравни тельной оценки склонности металлов к хрупкому разрушению.
Оценка механических свойств металлов и сплавов не огра ничивается характеристиками прочности, пластичности и удар ной вязкости. Часто эти характеристики недостаточны для пред ставительной оценки работоспособности применяемых в изде лиях материалов.
Критерии надежности, долговечности, жаропрочности рас смотрены в подразделах, посвященных высокопрочным и спе циальным сталям.
3.5. Возврат и рекристаллизация
деформированного металла
Как уже отмечалось, пластическая деформация металла из меняет его структуру и свойства, в частности вызывает наклеп - повышение прочности и снижение пластичности.
Для большинства металлов структура, образовавшаяся в ре зультате пластической деформации, и свойства устойчивы при температурах до « 25 °С. Повышение температуры делает возмож ным перемещение точечных дефектов и дислокаций, их взаимо действие и уменьшение их количества.
Изменение структуры деформированного металла при на греве происходит в две стадии, возврата (температуры ниже 0,3 Гпл) и рекристаллизации (при более высоких температурах). Возвратом называют изменения тонкой структуры и свойств без
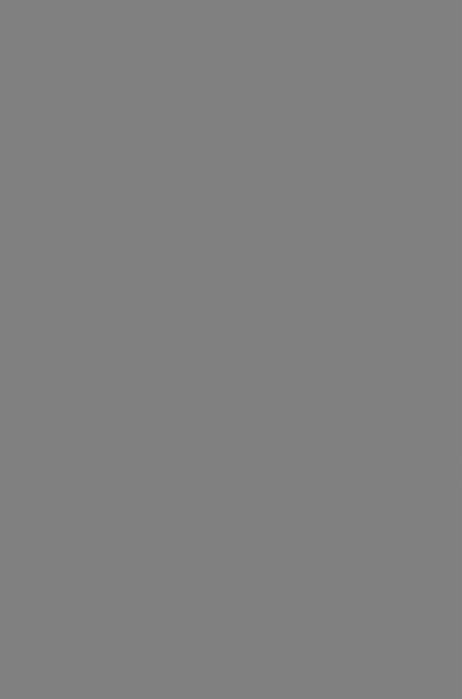
Для технически чистых А1, Си и Fe |
составляет 100, 270 |
и450 °С соответственно.
Впроцессе рекристаллизации выделяют две стадии, отли чающиеся образующейся структурой: рекристаллизации обра ботки (первичная) и рекристаллизации собирательной (вторич ная) (рис. 36). Зарождение новых зерен при первичной рекри сталлизации происходит в объемах металла с наибольшей плотностью дислокаций и на границах деформированных зерен. На стадии собирательной рекристаллизации происходит рост образовавшихся зерен по механизму миграции границ, т.е. с ук рупнения больших зерен, поглощающих мелкие зерна. Собира тельная рекристаллизация развивается при увеличении выдерж
ки или при повышении температуры и формирует крупно- и разнозернистую структуру металла.
а |
б |
в |
гд
Рис. 36. Схема изменения микроструктуры
наклепанного металла при нагреве:
а - наклепанный металл; б - начало первичной
рекристаллизации; в - завершение первичной
рекристаллизации; г, д - стадии собирательной
рекристаллизации
Разупрочнение деформированного металла в результате рекристаллизации (снятие наклепа - снижение значений НВ и Ов) сопровождается повышением пластичности (рис. 37).
Рис. 37. Схемы изменения твердости (а) и пластичности (б) наклепанного металла при нагреве: I - возврат; П - первичная рекристаллизация; Ш - рост зерна
Обработку металла давлением подразделяют на холодную (ниже температуры рекристаллизации), когда металл наклепы вается и сохраняет наклеп, и горячую (выше температуры рек ристаллизации), когда получаемый наклеп снимается одновре менно проходящей рекристаллизацией.
Размер зерен, образующихся после рекристаллизации, за висит в основном от степени деформации и температуры, при которой происходит рекристаллизация. Эту зависимость отра жают диаграммы рекристаллизации (рис. 38), обнаруживающие критические степени деформации, рекристаллизация после ко торых дает аномально крупнозернистую структуру металла. При проведении рекристаллизационных отжигов и при горячей обработке металла давлением назначают такие температурные, деформационные и временные параметры технологии, которые не допускают образование крупнозернистой структуры металла, так как для крупнозернистого металла характерна низкая пла
стичность, вязкость и прочность. Температура рекристаллизационного отжига металла после холодной пластической дефор
мации превышает на 100-150 °С.
Рис. 38. Зависимость размера зерна D рекристаллизованыого металла отдеформации (а) и диаграмма рекристаллизации технически чистого
железа (б); D0 - размер исходного зерна
Рассмотренные представления о формировании структуры металла при кристаллизации, пластической деформации и рек ристаллизации, о механических свойствах металлов и методах определения их характеристик важны для понимания процессов формирования фазового состава и структуры сплавов.
Кристаллизация металла обычно дает грубую крупнозерни стую структуру с выраженной дендритностью и химической не однородностью, что объясняет низкие значения прочности и пластичности металла - слитков, отливок, литых деталей, сварных соединений. Пластическая деформация литого металла в заготовительном производстве (прокатка, ковка, штамповка ит.п.), последующая его рекристаллизация, а также перекри сталлизация при термообработке, позволяют получить в металле реальных деталей относительно однородную мелкозернистую структуру.
Мелкозернистость структуры металла является важнейшим фактором, определяющим комплекс его механических свойств. Так, для сопротивления деформации металла (ат) установлена зависимость
стт =о, +k d 'Y *,
где d - размер зерна; а,- и к - const для данного металла. Атомный механизм пластической деформации металлов
позволяет представить напряжение макродеформации ат как сумму напряжения преодоления дислокациями сопротивления <сгрения» кристаллической решетки, дефектов ее строения, при месных атомов и вакансий (<тО и напряжения передачи дислока ционной деформации от зерна к зерну с выходом дислокаций на поверхность ( kd~&).
Понятно, что для реальных сплавов, в том числе сталей, за висимость сопротивления деформации от структуры, легирова ния и фазового состава значительно более сложная.