
книги / Основы металловедения и термообработки
..pdf5.4. Основы технологии термообработки стали
Технологические процессы термоупрочнения стальных де талей включают объемную термообработку, обеспечивающую заданную структуру и свойства металла во всем объеме детали, и термоупрочнение поверхностных слоев деталей.
Оборудование для проведения объемной термической об работки деталей и заготовок включает средства нагрева (камер ные, проходные и шахтные печи с пламенным и элекгронагревом, электродные соляные печи - ванны) и средства охлаждения (универсальные и специализированные закалочные баки, зака лочные прессы, спреерные устройства), часто объединенные взакалочно-отпускные агрегаты. Современное нагревательное оборудование обеспечивает безокислительный нагрев в защит ных атмосферах и в вакууме. Некоторые типы электропечей представлены на схемах рис. 71,72,73,74,75.
Рис. 71. Камерная электропечь типа СНЗ:
1 - нагревательные элементы; 2 - газопровод; 3 - футеровка;
4 - дверца для загрузки; 5 - механизм подъема дверцы;
б - кожух; 7 - газопровод
Рис. 72. Механизированная камерная электропечь (тип СНЗА):
1 - закалочный бак; 2 - закалочная камера; 3 - стол для загрузки
ивыгрузки деталей; 4 - вентилятор; 5 - нагревательная камера;
б - цепной механизм для передвижения поддона с деталями
Вкрупносерийном и массовом производствах этапы термо обработки совмещают в одном агрегате. Схема закалочно отпускного агрегата представлена на рис. 75. Агрегат включает конвейер 1 загрузки деталей в проходную печь 2 для нагрева под закалку, механизированный закалочный бак 3, из которого они конвейером подаются в отпускную ванну 4 и далее - в мо ечную машину 5 и в тару 6.
Продолжительность нагрева деталей при аустенизации стали (нагрев под закалку, нормализацию, полный отжиг) должна обес печить прогрев деталей по сечению и завершение фазовых пре вращений, но не должна быть слишком большой, чтобы не вы звать роста зерна и обезуглероживания стали в поверхностных слоях детали. Для определения общего времени нагрева детали (время сквозного прогрева и время выдержки) пользуются опыт ными данными, например продолжительностью нагрева 1 мм се
чения: в электропечи 1,5-2 мин, в пламенной печи - 1,0 мин, в соляной ванне - 0,5 мин, в свинцовой ванне - 0,15 мин.
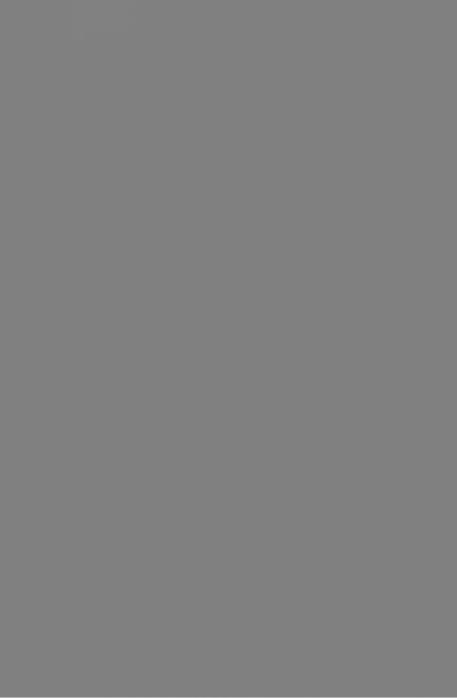
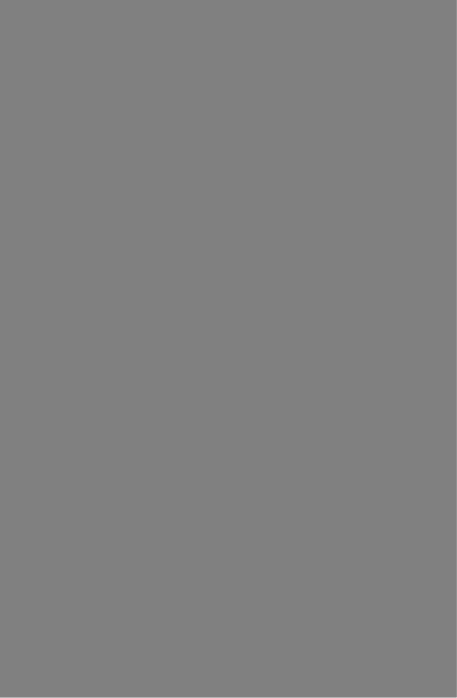
ката, синтетических веществ, например полиакрилнитрель, ак вапласт (концентрация 0,5-0,7 %).
Характерные дефекты закалки:
- коробление, поводка деталей вследствие неравномерно сти изменения объема при быстром охлаждении в связи с тер мической усадкой и структурными изменениями (предотвраща ется закалкой в заневоленном состоянии, например - в прессах); - закалочные трещины возникают в том случае, если мест
ные внутренние напряжения превысят предел прочности стали; - неудовлетворительная структура закалки - это крупно
игольчатый мартенсит при перегреве под закалку, ферритные участки при неполной закалке, троостит при недостаточной ско рости охлаждения.
Неудовлетворительная структура металла деталей может быть исправлена повторной термообработкой по откорректиро ванному режиму.
Термические цехи заводов кроме нагревательного и закалоч ного оборудования могут быть оснащены оборудованием для правки деталей (прессы, вальцы), для очистки поверхности деталей от окалины (дробеструйные и гидропескоструйные установки, ванны травления, нейтрализации и промывки), приборами контро лятвердости металла и контроля геометрии деталей.
6. ПОВЕРХНОСТНОЕ ТЕРМОУПРОЧНЕНИЕ
СТАЛЬНЫХ ДЕТАЛЕЙ
Многие детали, работающие в сложных условиях нагруже ния, подвергаются воздействию динамических и знакоперемен ных нагрузок, некоторые участки их поверхности работают в условиях трения (валы, оси, шестерни и т.д.). Материал таких деталей должен обладать высокой прочностью и вязкостью и одновременно иметь твердую износостойкую поверхность. Та кие детали после общей термообработки подвергают поверхно стному термоупрочнению, основными методами которого явля ются поверхностная закалка и поверхностный наклеп, а также химико-термическая обработка поверхности.
6.1. Поверхностная закалка и деформационное
упрочнение поверхности деталей
Поверхностная закалка включает нагрев поверхностного слоя до температуры аустенитного состояния (выше температу ры А3) и быстрое охлаждение с получением мартенсита в по верхностном слое.
Индукционная закалка с нагревом поверхностных слоев де тали токами высокой частоты (ТВЧ) - наиболее распространен ный и технологичный способ поверхностной закалки. Индукци онный нагрев поверхности детали ТВЧ заключается в том, что в поверхностном слое детали, помещенной в индуктор, индуциру ется ток, разогревающий этот слой. Толщина поверхностного слоя Ô, в котором выделяется 90 % теплоты, зависит от частоты тока/ магнитной проницаемости ц и удельного элекгросопротив-
ления р нагреваемого металла (ô = 500p/p/‘). Через индуктор,
представляющий собой соленоид из нескольких витков водоохла ждаемой медной трубки или шины (рис. 76), пропускают ТВЧ большой силы (f = 50 Гц - 10 МГц). Охлаждающую жидкость (воду, водные растворы полимеров) для закалки обычно подают через душевое устройство (спреер). Регулируя частоту тока / и продолжительность нагрева, можно получить требуемую глу бину закаленного слоя, которая обычно колеблется в преде лах 1 - 1 0 мм.
Рис. 76. Схема установки для высокочастотной закалки
Поверхностную закалку с газопламенным нагревом приме няют для крупных деталей (валы, прокатные валки и т.п.). Тол щина закаленного слоя обычно 2-4 мм с мартенсито-троостит- ной структурой. В этом случае не достигается равномерности нагрева поверхности и возникает структурная неоднородность закаленного слоя.
Поверхностная закалка с контактным нагревом заключа ется в пропускании тока в несколько тысяч ампер (частота 50 Гц, напряжение 2-8 В) через перемещающийся по поверхно сти ролик-электрод и интенсивном охлаждении водой нагревае мой под роликом полосы поверхности вращающейся детали. Глубина закаленного слоя зависит от силы тока, ширины ролика и скорости его перемещения.
Поверхностная закалка с кратковременного нагрева детали погружением в расплав солей или металлов применяется при термоупрочнении поверхности малонагруженных деталей не сложной формы и малых размеров.
Поверхностная закалка с нагревом детали в водном элек тролите (СаСОз и К2С03) происходит в металлической ванне при пропускании через электролит тока высокого напряжения - до 300 В (рис. 77). Образующаяся на поверхности детали оболоч ка из Н2 обладает высоким электросопротивлением, что обеспе чивает нагрев поверхности детали. Закалка поверхности происхо дит с охлаждением непосредственно при отключении тока после определенного времени нагрева.
Рис. 77. Схема поверхностной закалки в электролите:
1 - закаливаемая деталь (катод); 2 - ванна (анод);
3 - электролит; 4 - водородная оболочка; 5 - источник питания
Поверхностное упрочнение деталей пластической дефор мацией (наклеп) после упрочняющей термообработки (закалка и отпуск) может осуществляться дробеструйной обработкой, накаткой роликами и чеканкой. Кроме повышения твердости поверхности в поверхностных слоях возникают большие напря жения сжатия, что повышает усталостную прочность a_i и, сле довательно, долговечность и выносливость деталей, работаю щих в условиях знакопеременного нагружения (пружины, рес соры, коленчатые валы).
6.2. Химико-термическая обработка стали
Химико-термической обработкой (ХТО) называют процесс диффузионного насыщения поверхностного слоя детали различ ными элементами, изменяющий его химический и фазовый со став, микроструктуру и свойства.
ХТО применяют для повышения твердости, износостойко сти, сопротивления усталости и контактной выносливости,
атакже для защиты поверхности деталей от электрохимической
игазовой коррозии.
Процесс ХТО осуществляется при повышенной температу ре и включает стадию образования диффундирующих элементов в активном (скорее всего, в ионизированном) состоянии, стадию адсорбции (или хемосорбции) их тончайшим слоем поверхности и стадию диффузионного проникновения элемента вглубь на сыщаемого металла.
ХТО включает цементацию, азотирование, нитроцемента цию, цианирование, алитирование, силицирование и т.д. Диф фузия элементов, образующих твердые растворы внедрения (С, N), протекает легче, чем диффузия элементов, образующих твердые растворы замещения (Al, Si, Сг). Поэтому диффузион ную металлизацию ведут при более высокой температуре.
Поверхностный слой металла детали, отличающийся от ис ходного металла по химическому составу, называется диффузи онным слоем, в отличие от находящегося под ним металла серд цевины.
Цементацией называется процесс диффузионного насыще ния поверхностного слоя стальных деталей углеродом. Цель це ментации - получение на поверхности детали высокой твердо сти и износостойкости в сочетании с вязкой сердцевиной. На цементацию поступают детали после механической обработ ки с припуском на последующее шлифование до 0,1 мм. Участ ки поверхности детали, не подлежащие цементации, защищают огнеупорной обмазкой или электролитическим меднением.
Цементацию проводят при температурах выш е критиче ской точки Аз (910-950 °С), при которых аустенит обеспечивает значительную растворимость углерода.
Цементации подвергают стали с низким содерж анием угле рода (0,1-4),2 %). После цементации концентрация углерода на поверхности достигает 1,0 %. Глубина цементованного слоя оп ределяется длительностью выдержки при температуре цемента ции и обычно составляет 0,7-2,5 мм (до содержания углерода порядка 0,4 %). Структура цементованного слоя после медлен ного охлаждения с температуры цементации (рис. 78) изменяет ся по глубине слоя в соответствии с изменением содержания углерода. После цементации всегда проводится термообработка деталей, включающая закалку и низкий отпуск, для получения высокой твердости поверхности и вязкой сердцевины.
Рис. 78. Микроструктура диффузионного слоя после цементации низкоуглеродистой стали:
1 - заэвтектоидная зона; 2 - эвтектоидная зона;
3 - доэвтектоидная зона