
книги / Основы металловедения и термообработки
..pdfру, состоящую из перлита и ледебурита. Режим отжига на структуру ферритного ковкого чугуна (рис. 55, а) обеспечивает распад при длительных выдержках (~ 25 ч) как ледебуритных карбидов (при 950-1000 °С: Fe3C„w -» Fe,,(C)ayc + Г), так и пер литных карбидов (при 720-740 °С: РезСперл -> Реа(С)ферр+ Г).
Перлитный ковкий чугун получают отжигом белого чугуна при температуре ~ 1000 °С (рис. 55, б) с последующим непре рывным охлаждением, исключающим графитизацию перлитных карбидов.
Рис. 55. Схема отжига белого чугуна на ковкий: а - ферритный КЧ; б - перлитный КЧ
Отметим, что в этой главе пособия рассмотрены структуры и свойства сплавов в равновесном состоянии, т.е. формирую щиеся при очень медленном охлаждении. В реальных условиях (в деталях, конструкциях, инструменте) сплавы подвергают термообработке по заданным температурно-временным режи мам нагрева и охлаждения, что формирует специфические структуры сплавов с требуемым комплексом физико-механи ческих свойств.
5.ТЕРМООБРАБОТКА МЕТАЛЛОВ
ИСПЛАВОВ
Термическая обработка - самый распространенный способ изменения свойств металлов и сплавов.
Термической обработкой называют технологические про цессы, при которых путем нагрева металлов и сплавов до опре деленной температуры, выдержки при этой температуре и по следующего охлаждения с определенной скоростью добиваются получения структуры, обеспечивающей требуемый комплекс свойств металлов.
Термической обработке подвергают слитки, отливки, по луфабрикаты, сварные соединения, узлы и конструкции, детали машин, инструменты.
Термическая обработка металлов и сплавов проводится в тех случаях, когда имеются полиморфные превращения, огра ниченная или переменная растворимость одного компонента в другом в твердом состоянии, изменение строения металла по сле холодной деформации.
Основные виды термической обработки - отжиг, нормали зация, закалка, отпуск, старение. Каждый из этих видов имеет несколько разновидностей.
Отжиг - термическая обработка, в результате которой ме таллы и сплавы приобретают структуру, близкую к равновесной. Исходная неравновесность состояния сплава перед отжигом может быть связана с химической неоднородностью, возникшей при кристаллизации, со структурной неоднородностью, обу словленной незавершенностью фазовых превращений при ох лаждении или последствиями пластической деформации, с на личием остаточных напряжений I или П рода. В связи с этим
отжиг проводится соответственно как гомогенизационный, перекристаллизационный или рекристаллизационный, как релак сационный, для снятия напряжений. Скорость охлаждения
с температур отжига невелика (50-200 °/ч). Отжиг разупрочняет металлы и сплавы, повышает их пластичность.
Закалка - термообработка, в результате которой в сплавах образуется неравновесная структура. Неравновесная структура при закалке может быть получена только в том случае, когда в сплавах имеются превращения в твердом состоянии: умень шение растворимости одного компонента в другом при пониже нии температуры, полиморфные превращения твердых раство ров, эвтектоидный распад твердых растворов при охлаждении и др. Неравновесную структуру сплава получают нагревом вы ше температуры фазового превращения в твердом состоянии и последующим быстрым охлаждением, предотвращающим рав новесное превращение.
Отпуск и старение - термообработка, в результате которой в предварительно закаленных сплавах происходят фазовые пре вращения, приближающие их структуру к равновесной.
Сочетание закалки с отпуском или старением всегда пред полагает получение более высоких характеристик прочности сплава по сравнению с отожженным состоянием. В большинстве сплавов после закалки получают пересыщенный твердый рас твор, а при последующем отпуске или старении - распад пере сыщенного твердого раствора.
Термин «отпуск» используют обычно применительно к сталям, твердость которых в результате отпуска уменьшается по сравнению с закаленным состоянием, а пластичность - воз растает. Термин «старение» чаще всего связан с повышением характеристик прочности сплавов по сравнению с закаленным состоянием вследствие образования при старении упрочняю щих фаз (дуралюмин, безуглеродистые мартенситостареющие стали и т.п.).
5.1. Структурообразование
при нагреве углеродистой стали
Теорш термической обработки стали призвана дать объ яснение процессов структурообразования при нагреве и охлаж дении и указать температурно-временные условия, обеспечи вающие получение требуемого комплекса свойств стали.
Основоположником теории термообработки стали считают Д.К. Чернова, открывшего в 1868 г. наличие критических точек (температур нагрева) стали. Он показал, что термообработка стволов повышает их прочность и изменяет характер разруше ния только в тех случаях, когда при термообработке достигается определенная, критическая температура нагрева. Впоследствии было установлено, что нагрев стволов до температур выше кри тических качественно изменяет структуру стали в термообрабо танном состоянии, что и делает возможным повышение экс плуатационной прочности стволов.
Теория термообработки стали рассматривает, в первую очередь, процессы образования аустенита при нагреве и распа де его при охлаждении, а также структурообразование при от пуске закаленной стали.
Ранее рассмотренная диаграмма состояния сплавов систе мы Fe - С (см. рис. 48) указывает значения критических темпе ратур и описывает структуру сталей, формирующуюся при рав новесном нагреве и охлаждении. При термообработке реальные температурно-временные условия фазовых превращений фор мируют совершенно иные структуры и, следовательно, придают стали соответствующий этим структурам комплекс свойств.
Образование аустенита при нагреве эвтектоидной стали (сталь У8, содержание углерода 0,8 %), имеющей исходную структуру перлита, происходит при достижении температуры
выше критической точки Aj (727 °С) на границах феррита и це ментита образуются зародыши аустенита:
_________________ Перлит_________________ |
727 °С |
|
||
Fe0(C); 0,02 % С |
+ |
Fe3C; 6,67% С |
->• |
Fc/C); 0,8 % С |
феррит |
|
цементит |
|
аустенит |
С повышением температуры и увеличением выдержки эти зародыши вырастают в зерна аустенита, поглощая ферритные участки и растворяя цементитные частицы.
В доэвтектоидных и заэвтектоидных сталях образование аустенита также начинается при температуре нагрева > 727 °С (Ai), но завершается при температурах выше критических А3 (линия GS) и Ас,п (SE) с исчезновением последних количеств из быточных фаз, соответственно феррита и цементита.
Завершение аустенизации при нагреве до температур на 30-50° выше температур А3и Астдает относительно мелкое аусте нитное зерно. При повышении температуры нагрева увеличение размера аустенитного зерна происходит более интенсивно у при родно-крупнозернистых сталей (раскислены при выплавке ферро силицием и ферромарганцем). Для природно-мелкозернистых ста лей (раскислены ферроалюминием или содержащие до 0,15 % V, Nb, Ti) рост аустенитного зерна при нагреве сдерживается трудно растворимыми в аустените мелкими нитридами и карбидами.
Крупнозернистая структура стали (результат перегрева) может быть исправлена повторной аустенизацией с нагревом до относительно низких температур.
Превращение аустенита при охлаждении ниже температу ры А\ может происходить изотермически (при постоянной тем пературе). Диаграммы изотермического распада аустенита мо гут быть построены экспериментально, если фиксировать время начала распада аустенита и количество распавшегося аустенита во времени при всех температурах ниже A h От степени переох лаждения аустенита ниже температуры А х зависит механизм и кинетика его распада и, следовательно, структура образую щихся продуктов превращения.
Возможны три типа процессов распада аустенита при ох лаждении: диффузионное (перлитное), промежуточное (бейнитное) и бездиффузионное (мартенситное). Рассмотрим эти пре вращения на примере стали У8.
Диаграмма распада аустенита стали У8 (рис. 56) представляет собой две С-образные кривые и две горизонтальные линии, соот ветствующие температурам Мни Мх. Линии 1 и 2 указывают время начала (1) и завершения (2) изотермического превращения аусте нита при соответствующей температуре с образованием ферритоцементагных структур. Левее линии 1 находится переохлажден ный аустенит, между линиями 1 и 2 - переохлажденный аустенит и продукты распада аустенита. Температура Ми - температура на чала бездиффузионного (мартенситного) превращения аустенита, развивающегося при понижении температуры и завершающегося при достижении температуры Мк(конец превращения).
Рис. 56. Диаграмма изотермического превращения переохлажденного аустенита эвтектоидной стали У8 (схема):
I - перлитное превращение; II - промежуточное превращение; Ш - мартенситное превращение; П - перлит; С - сорбит; Т - троостит; Б - бейнит
Переохлажденный ниже температуры А, аустенит стали У8 наименее устойчив при температуре » 550 °С (время устойчиво сти ~ 1 с). Превращение аустенита при температурах в интерва ле А' - 550 °С называют перлитным, а превращение в интервале температур 550 °С - М н- бейнитным (промежуточным).
В результате перлитного превращения аустенита образуют ся пластинчатые структуры, представляющие собой смесь чере дующихся кристаллов феррита и цементита. Для образования смеси фаз, значительно различающихся по содержанию углеро да (0,02 % С в феррите и 6,67 % в цементите) из аустенита (0,8 % С) необходимо диффузионное перемещение атомов угле рода на расстояния, значительно превышающие межатомные. Относительно высокая температура перлитного превращения обеспечивает достаточную диффузионную подвижность атомов
углерода. Полиморфное превращение Fey -> Fea при этих темпе ратурах также происходит по диффузионному механизму - не упорядоченным перестроением атомов железа из кристалличе ской решетки ГЦК в ОЦК.
С увеличением степени переохлаждения аустенита ниже температуры А\ диффузионная подвижность атомов железа и углерода уменьшается, вследствие чего уменьшаются размеры образующихся кристаллов феррита и цементита и межпластин чатые расстояния, т.е. возрастает дисперсность ферритоцементитной смеси (рис. 57). Условно можно выделить перлит
(образуется при 650-670 °С) с межпластинчатым расстоянием ~ 6 10"7 мм), сорбит (640-590 °С, ~ 3 10-7 мм) и троостит
(580-550 °С, ~ 1 10~7 мм). Чем дисперснее структура перлитно го типа, тем выше твердость и прочность стали; лучшее сочета ние прочности и пластичности имеет структура сорбита.*
* Принято отмечать температуры критических точек превращения аустенита при охлаждении как Агхи Аг3, а при нагреве - как Ас\ и Ас3.
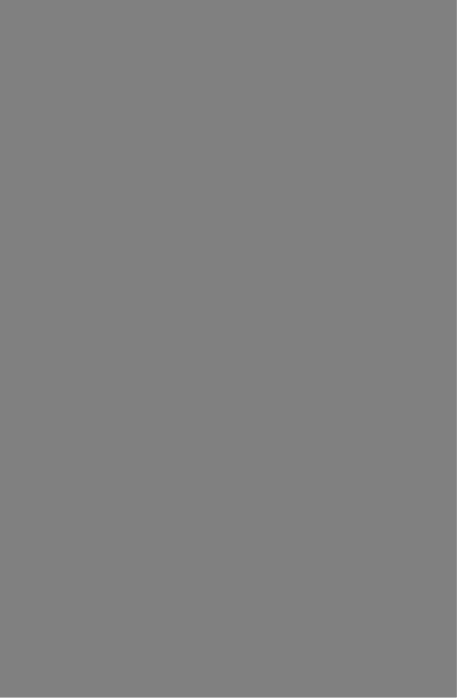
сыщенный твердый раствор углерода в a -железе, полученном бсздиффузионным механизмом превращения аустенита при вы сокой скорости охлаждения (> Р^). Именно с целью получения структуры мартенсита проводят закалку сталей. Мартенситное превращение не бывает полным - всегда остается от 2 до 10 % аустенита остаточного.
Мартенсит имеет высокую плотность дефектов кристалли ческого строения (дислокаций), что является одним из факторов его упрочнения (фазовый наклеп). Однако основная причина высокой твердости мартенсита - это содержание в нем углеро да. С увеличением содержания углерода резко возрастает твер дость мартенсита сталей (рис. 58), но снижается пластичность.
Содержание углерода
Рис. 58. Твердость мартенсита в зависимости от содержания в нем
углерода: / - углеродистая сталь; 2 - легированная сталь
Механизм образования кристаллов мартенсита обусловли вает очень высокую скорость их роста в пределах исходного аустенитного зерна, а форма кристаллов мартенсита проявляет ся в специфике его микроструктуры (рис. 59).
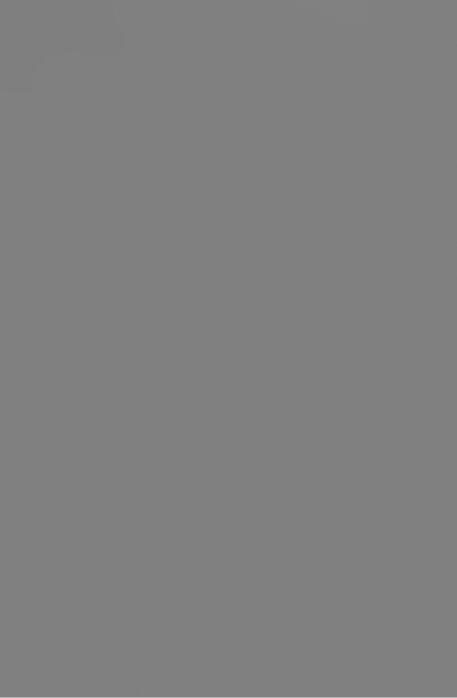