
книги / Основы металловедения и термообработки
..pdfДиффузионная подвижность атомов углерода в этом интер вале температур делает возможным существование в аустените микрообъемов с пониженной концентрацией углерода. Именно в этих участках становится возможным образование мартенсита, так как с понижением содержания углерода в аустените темпе ратура его мартенситного превращения повышается. В микро объемах аустенита, обогащенных углеродом, происходит обра зование карбидов в виде коротких пластинок кристаллов цемен тита. Вследствие этого уменьшается локальное содержание углерода и развивается мартенситное превращение. К моменту полиморфного превращения аустенит не полностью освобожда ется от растворенного углерода, поэтому образующиеся кри сталлы Fea несколько пересыщены углеродом и имеют форму тонких пластин, на границах которых оказываются тонкие пла стинки цементита.
Образовавшийся при температурах 400-550 °С бейнит на зывают верхним, он имеет перистое строение.
Образующийся при температурах < 400 °С...М и нижний бейнит имеет пластинчатое (игольчатое) строение. Его а-фаза значительно пересыщена углеродом, и поэтому сразу после (у -» а) превращения в a -фазе выделяются дисперсные карбиды.
После закалки на мартенсит или бейнит стали имеют высо кую прочность (твердость) и низкую пластичность. Для повы шения пластичности и снижения твердости закаленные стали подвергают отпуску (нагрев до температур < А а ) для получения требуемого сочетания прочности и пластичности.
После отпуска стали, закаленные на мартенсит или на ниж ний бейнит, образовавшийся при температурах на 50-100 °С выше точки М„, имеют высокую прочность и достаточно высо кую пластичность и вязкость, в то время как для сталей, зака ленных на верхний бейнит, после отпуска характерно сочетание относительно низкой прочности с недостаточной пластичностью и вязкостью.
Вследствие повышенной устойчивости аустенита высоко углеродистых и легированных сталей температура окончания мартенситного превращения (Мк) этих сталей может быть ниже комнатной. В структуре таких сталей после закалки кроме мар тенсита есть остаточный аустенит. Для его превращения в мартенсит детали после закалки подвергают обработке холо дом - охлаждению до температуры - 40.. .-196 °С.
Отпуск закаленных сталей включает нагрев до температур, не превышающих Аи выдержку при этой температуре и после дующее охлаждение. При отпуске происходят изменения струк туры, связанные с протеканием нескольких процессов. Основ ной - распад мартенсита, состоящий в выделении углерода из пересыщенной им a -фазы и образовании карбидов, кроме того, распадается остаточный аустенит (в сталях с точкой Мк ниже комнатной температуры), происходит коагуляция (укрупнение
и«округление») карбидов, уменьшение плотности несовершенств кристаллического строения a -фазы и остаточных напряжений.
Отпуск стали снижает ее прочность (твердость, ав, аод)
иповышает пластичность (Ô, \р) - рис. 60.
Обычно выделяют три вида отпуска, соответствующие оп ределенным интервалам температур нагрева.
Низкий отпуск (до 200 °С) не приводит к заметным струк турным изменениям, так как при малой подвижности атомов углерода они по-прежнему остаются в состоянии пересыщенно го твердого раствора a -фазы, и лишь их смещение к несовер шенствам кристаллического строения (границы зерен и субзе рен, дислокации, вакансии) способствует некоторому снижению остаточных напряжений и делает возможным распад остаточно го аустенита. Отпущенный мартенсит сохраняет высокую твер дость, но менее хрупок. Низкий отпуск применяется для режу щего инструмента и деталей, термообрабатываемых на высокую твердость и износостойкость.
Рис. 60. Влияние температуры отпуска
на механические свойства конструкционной углеродистой стали (0,45 % С)
Средний отпуск (350-500 °С) формирует структуру троостита отпуска, представляющего собой феррито-цеменшгаую смесь. При температуре среднего отпуска подвижность атомов углерода достаточна для выхода из пересыщенного твердого раствора а-фазы и образования карбидов. Однако a -фаза (феррит) сохраняет фазо вый наклеп и фрагментацию мартенситных пластин, а карбидные частицы весьма дисперсны и имеют форму тонких пластин. Сред ний отпуск снижает прочность и повышает пластичность стали. Структура троостита отпуска обеспечивает достаточно высокую упругость и твердость стали. Средний отпуск применяют для пру жин, рессор, штампов, ударного инструмента и т.п.
Высокий отпуск (500-650 °С) полностью устраняет внут ренние напряжения и формирует структуру сорбита отпуска, представляющего собой феррито-цементитную смесь. Достаточ-
83
но высокая подвижность атомов углерода и железа при темпера туре высокого отпуска приводит к коагуляции карбидов и рекри сталлизации a -фазы, имевшей до этого фазовый наклеп и повы шенную плотность дефектов кристаллического строения. После высокого отпуска сталь приобретает наилучший комплекс меха нических свойств: повышенную пластичность и вязкость при достаточной прочности. Высокий отпуск применяют для деталей машин и конструкций, работающих в сложных условиях статиче ского, динамического и знакопеременного нагружения. Термиче скую обработку конструкционных сталей, включающую полную закалку и высокий отпуск, называютулучшением.
5.2. Основные виды термообработки
углеродистой стали
Термическую обработку сталей можно разделить на пред варительную (отжиг, нормализация) и упрочняющую (закалка с последующим отпуском). Схема проведения этих видов тер мообработки представлена на рис. 61.
Отжиг и нормализация могут быть и окончательной термо обработкой заготовок, деталей, конструкций, если не ставится задача получения высокой прочности металла.
Время
Рис. 61. Схематические графики основных операций термической обработки:
1 - отжиг; 2 - нормализация; 3 - закалка;
4 - отпуск на различные температуры
Отжиг проводят для устранения химической или физиче ской неоднородности металла заготовок, созданной предшест вующими обработками (литье, обработка металла давлением, сварка, правка).
Цели отжига:
-устранение химической и структурной неоднородности
стали;
-уменьшение внутренних напряжений;
-снижение твердости стали для облегчения механической обработки;
-получение мелкозернистой однородной структуры стали перед проведением упрочняющей термообработки.
Существуют различные виды отжига: полный, неполный (ускоренный), диффузионный (гомогенизация), рекристаллизационный, изотермический, отжиг для снятия остаточных на пряжений. Температурно-временные параметры режимов от жига различны, но для них характерны длительная выдержка при температурах нагрева и последующее медленное охлажде ние. На рис. 62 представлена схема, указывающая температур ные интервалы нагрева для различных видов отжига углероди стой стали.
Полный отжиг проводится для доэвтектоидных сталей с нагревом на 30-50 °С выше критической температуры Аз (од нородный аустенит), выдержкой при этой температуре и по следующим медленным охлаждением (рис. 63). Перекристал лизация стали при Fea -> Fey превращении обеспечивает полу чение однородной структуры, а распад аустенита на перлитную структуру - низкую твердость и высокую пластич ность, что весьма важно для механической обработки и холод ной деформации.
0,2 0,40,60,81,01,2 1,4 1,61,8 С,%
Рис. 62. Температура нагрева при отжиге и нормализации: отжиг I рода
(1 - диффузионный отжиг; 2 - рекристаллизационный отжиг; 3 - отжиг для снятия напряжений;
отжиг Прода (4 - полный отжиг; 5 - неполный отжиг; 6 - нормализация)
Рис. 63. Кривые охлаждения при полном и изотермическом отжиге
Изотермический отжиг включает нагрев заготовки на 30-50 °С выше температуры точки А3, выдержку при этой тем пературе и быстрый перенос в среду с постоянной температурой несколько ниже температуры точки А\ (обычно 630-700 °С). За готовку выдерживают при этой температуре до полного распада аустенита, после чего охлаждают на воздухе (рис. 63). Распад аустенита при постоянной температуре дает более равномерную структуру феррито-цементитной смеси, чем получаемую при полном отжиге. Это дает лучшую обрабатываемость стали реза нием (выше качество поверхности) и уменьшает деформации деталей при последующих нагревах.
При неполном отжиге нагревают заготовки до температур незначительно превышающих точку Аси вследствие чего пере кристаллизация доэвтектоидных сталей происходит лишь час тично: в аустенит превращается только перлит и незначительная доля феррита. Неполный отжиг доэвтектоидных сталей прово дится в тех случаях, когда не требуется исправление крупноили разнозернистости структуры стали заготовок, но необходи мо улучшение их обрабатываемости резанием.
Для заэвтектоидных сталей применяют только неполный отжиг (нагрев выше температуры Ai), который позволяет полу чить зернистую структуру перлита вместо пластинчатой (рис. 64, б). Такой отжиг называют сферодизацией. Сталь с зер нистым перлитом имеет более высокую пластичность и вязкость и меньшую твердость. Полный отжиг заэвтектоидной стали с нагревом выше температуры Аст до аустенитного состояния нецелесообразен, так как при медленном охлаждении стали в интервале Аст... Ас\ будет выделяться цементит в виде сетки по гарницам аустенитных зерен (рис. 64, а). Пластичность стали с цементитной сеткой очень низка, разрушение обычно хрупкое по границам зерен.
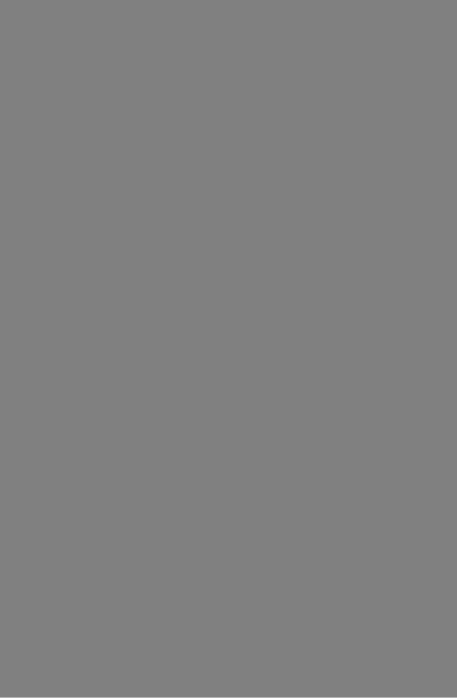
Отжиг для снятия остаточных напряжений применяют для отливок, сварных узлов и конструкций, деталей после обра ботки резанием, после правки и др., когда технологические опе рации дают неравномерность охлаждения, неоднородность де формации. Остаточные напряжения за время хранения детали могут вызвать коробление и даже разрушение (шлифовочные трещины, трещины в сварных соединениях и др.). Отжиг сталь ных изделий для снятия статочных напряжений проводится при температуре от 160 до 700 °С с последующим медленным охла ждением. Так, прецизионные длинномерные детали (трубы, хо довые винты, червяки, зубчатые колеса и др.) после основной механической обработки часто проходят отжиг при 570-600 °С (2-3 ч), а после окончательной - при 160-180 °С (2,5-2 ч) для снятия шлифовочных напряжений. Отжиг сварных соединений проводят при 650-700 °С.
Так называемому противофокенному отжигу подвергают крупные (сечение > 100 мм) поковки и отливки из легированных сталей. Этот отжиг имеет целью исключить опасность образова ния в металле заготовок флокенов - трещин-надрывов. Причину их образования объясняют наличием водорода в твердом рас творе и внутренних напряжений в металле после обработки дав лением, кристаллизации и ускоренного охлаждения заготовок. Поскольку растворимость водорода в Fea значительно меньше, чем Fey, отжиг ведут при температуре ниже Ас\ (650-680 °С), добиваясь длительными выдержками (до « 50 ч) снижения со держания водорода в твердом растворе до неопасных для флокенообразования концентраций (< 2 см2/100 г).
Нормализация заключается в нагреве стали в аустенитное состояние (на 50 °С выше температуры доэвтектоидных и Аст заэвтектоидных сталей), выдержке при этой температуре и ох лаждении на воздухе. Полная фазовая перекристаллизация при нагреве устраняет крупнозернистую структуру стали, получае мую в крупных отливках, поковках, прокате. Ускоренное охла ждение на воздухе предотвращает образование феррита в интер-
89
вале температур А3-А, и приводит к распаду аустенита на дис персную феррито-цементитную структуру типа сорбита. Норма лизация применяется для исправления структуры перегретой стали, устранения цементитной сетки заэвтектоидных сталей, выравнивания структуры металла сварного соединения, снятия внутренних напряжений.
Закалка применяется с целью повышения твердости стали за счет получения структуры мартенсита. Закалка заключается в нагреве стали до температуры выше критической (рис. 65), выдержке и последующем охлаждении со скоростью, превы шающей критическую. Высокая твердость и хрупкость мартен сита и напряжения, вызванные закалкой, делают обязательным проведение отпуска закаленной стали.
0,8 |
С,% |
Рис. 65. Оптимальные температуры нагрева под закалку углеродистых сталей
Для того чтобы переохладить аустенит углеродистых ста лей до температуры мартенситного превращения, необходима высокая скорость охлаждения (К^ = 400-1400 град/с). Такая скорость охлаждения достигается погружением закаливаемых деталей в холодную воду и в воду с добавками соли-NaCl или едкого натра (NaOH).