
книги / Структура и усталостное разрушение металлов
..pdfполагаясь по границам ячеек, существенно повышают стабильность ячеистой структуры.
Мак Грат и Братина [146] первыми привели данные 0 растворении метастабильных выделений карбидов в стали в процессе усталости. В низкоуглеродистой стали, содержащей после закалки и отпуска при 60° С в течение 1 ч когерентные выделения карбидов, при циклическом нагружении возникают устойчивые полосы скольжения, не содержащие выделений. Вероятность зарождения ус тойчивых полос скольжения в стали зависит от темпера туры и, вероятно, длительности старения. Этот вывод следует из серии экспериментов, выполненных на зака ленно-состаренных низкоуглеродистых сталях [146, 147]. Так как с изменением температуры старения меняется размер и когерентность дисперсных выделений, то логич но допущение об определяющей роли этих факторов на развитие структурной нестабильности в железоуглероди стых сталях.
После закалки от 700° С и старения при 60° С в тече
ние 16 ч углеродистая сталь |
(0,045%) |
имела в структуре |
дисперсные пластинчатые |
выделения |
метастабильных |
|
о |
|
карбидов диаметром 200—300 А [147]. Распределение карбидов было довольно равномерным, за исключением обедненных зон вдоль границ зерен и дислокаций. После нагружения (растяжение — сжатие) в активных полосах скольжения происходит растворение выделений Fe3C. Плотность дислокаций в полосах скольжения относитель но низка. В то же время на границах полос скольжения видна чрезвычайно высокая плотность дислокаций и вы
делений. Сами полосы скольжения узкие, прямые, чаще
о
всего ширина их 50 А. Направление ориентации полос скольжения совпадает с плоскостями типа {110} и {112}. Вильсон и Минц считают, что расширение полос скольжения связано с перерезанием дислокациями час тиц выделений и предполагает участие механизма по перечного скольжения.
С укрупнением частиц дисперсных выделений, что со провождается потерей когерентного сопряжения между выделением и матрицей, дислокации не в состоянии пере резать частицы выделений. После старения при 90° С в течение 16 ч средний диаметр частиц пластинчатой фор-
О
мы составлял 1000—2000 А. Дислокации, которые не в состоянии перерезать частицы выделений, скапливаются
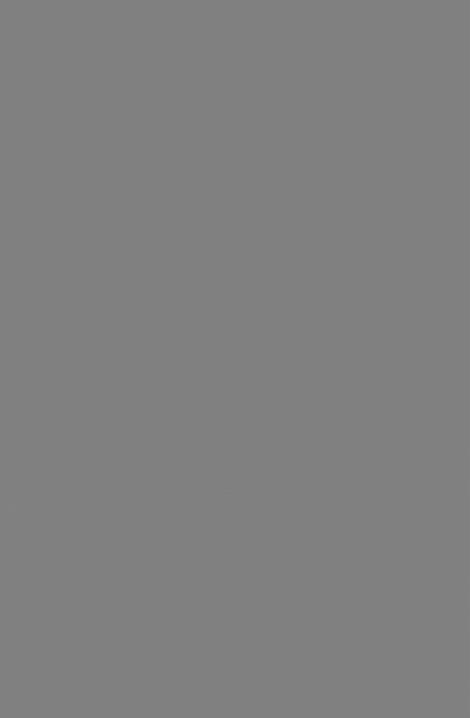
вать его не в состоянии даже интенсивное динамическое деформационное старение. Более того есть все условия для того, чтобы перемещающиеся дислокации выметали атомы углерода к стенкам полос скольжения. По-видимо- му, это способствует росту частиц карбидов вдоль гра ниц полос скольжения. При температуре циклического нагружения 90° С диаметр пластинчатых выделений Fe3C вдоль границ устойчивых полос скольжения достигает ~ 1 мкм. Предпочтительному росту частиц при повышен ных температурах способствует, во-первых, присутствие заблокированных дислокаций в границах полос сколь жения, во-вторых, облегченный перенос атомов углерода через стенку дислокаций, образующих субграницу, пу тем «трубочной» диффузии.
Удивительную способность циклических напряжений вызывать структурные изменения демонстрируют иссле дования [129]. В шарикоподшипниковой стали SAE 52100 (0,97% С; 1,43% Сг), термически обработанной на мар тенсит (закалка 860° С+отпуск 160° С) и нижний бейнит (закалка 860° С, изотермическое превращение при 230° С), испытания на контактную усталость при напря жениях 81,5—93,0 кгс/мм2 в течение А7=5,0• 107—109 циклов вызывают распад некогерентных выделений кар бидов и появление зон феррита, свободных от выделений. Довольно протяженные кристаллографические зоны фер рита появляются не только в областях мартенсита, содержащего дисперсные выделения е-карбида, но про
никают |
(в форме |
клинообразных |
полос) |
в довольно |
|
крупные |
(~ 1 мкм) |
сферические |
карбиды |
типа (Fe, |
|
Сг)3С. В ряде случаев ферритные полосы |
пронизывают |
||||
карбид насквозь или даже полностью его |
уничтожают. |
6F, кгс/пп2
Рис. 44. Связь между напряже нием течения стт при пластиче
ской деформации 5% и преде лом усталости стрпизкоуглсро-
днстой стали |
в |
закаленном (/) |
и закаленном |
н |
состаренном со |
стояниях (2). Цифрами у кри вых отмечет»! температуры за калкн и старения [147]
25 30 35 40 45 50
0Т/ кгс/мм2
Аналогичная картина выявляется и в стали со структу рой бейнита. Дисперсные пластинки карбида (Fe, Сг)3С перерезываются ферритными полосами. Это обусловли вает растворение значительной массы указанных выде лений.
По существу в стали SAE 52100 в процессе контакт ной усталости (испытания проводили при 50—55° С) реа лизуются фазовые превращения, которые должны проис ходить после длительного отжига или даже аустенитиза ции. Авторы работы [129] считают, что распад карбидов происходит по диффузионному механизму. Цикличе ские напряжения вызывают значительную пластическую деформацию в феррите, что обусловливает возникнове ние большой плотности дислокаций, а следовательно, и возможность интенсивного протекания трубочной диф фузии атомов углерода. Вполне возможно, что диффузия углерода, вызываемая напряжениями за один цикл, нс получает значительного развития, однако производит значительный эффект за большое число циклов нагру жения.
Образование в процессе малоцикловой усталости (чистый изгиб) каналов пластической деформации, пе ресекающих колонии мартенситных реек, обнаружено в работе [131], выполненной на сталях 15ХНЗМ, 15ХН5МФ и 12ХН4МФ. При этом по границам каналов пластиче ской деформации происходит зарождение и распростра нение усталостных трещин.
На рис. 44 представлено изменение циклической
прочности aF по отношению |
к |
напряжению течения |
егт (еР = 5%) для закаленной |
и |
закаленно-состаренной |
стали с 0,045% С [147]. Видно, что высокий уровень ста тической прочности, достигаемый при упрочнении стали дисперсными когерентными с матрицей выделениями, нс обязательно приводит к высокой циклической прочности. Более высокие значения oF достигаются при крупных карбидах, когерентно не связанных с матрицей, но отно сительно стабильных по отношению к циклическому де формированию. Для закаленных образцов наблюдается линейная связь между oF и сгт. Таким образом, повыше ние температуры закалки, а, следовательно, концентра ции твердого раствора сопровождается ростом oF. Одна ко в целом уровень о> образцов, упрочненных дисперс ными частицами Fe3C, выше aF образцов, термически обработанных на твердый раствор.
ВЛИЯНИЕ ТЕМПЕРАТУРЫ ОТПУСКА НА РАЗВИТИЕ ЦИКЛИЧЕСКОГО РАЗУПРОЧНЕНИЯ ЗАКАЛЕННО-ОТПУЩЕННОЙ СТАЛИ
Поскольку явление циклического разупрочнения яв ляется в высшей степени структурно чувствительной ха рактеристикой, то изменение структуры стали в процес се отпуска (старения) находит выражение в изменении характера циклического разупрочнения закаленно-отпу щенных сталей. Рассмотрим некоторые конкретные при меры циклического поведения дисперсионно-упрочняе- мых сталей в зависимости от температуры отпуска.
В работе [148] показано влияние 1-ч отпуска в ин тервале температур от комнатной до 650° С на поведение кривых циклического деформирования о—г вакуумированной закаленной (1000° С, 1 ч, масло) стали AISI 4140, испытанной на малоцикловую усталость. Образцы в за каленном состоянии обнаруживают исключительно цик лическое деформационное упрочнение, а после отпуска выше 200° С — циклическое разупрочнение, которое до стигает максимума при 400° С (табл. 9).
ТЛБЛИЦЛ 9. ОЦЕНКА ВКЛАДА СУБСТРУКТУРНОГО Д(7С
ИМЕХАНИЧЕСКОГО Ао м РАЗУПРОЧНЕНИЯ
ВОБЩЕЕ ЦИКЛИЧЕСКОЕ РАЗУПРОЧНЕНИЕ А<Т£ СТАЛИ 4140
Температура отпуска, |
Ла2 |
Д(ТС |
дам |
°С |
|
кгс/мм2 |
|
|
|
|
|
400 |
50 |
31 |
20/19 |
550 |
38 |
14 |
20/24 |
650 |
28 |
9 |
13/19 |
П р и м е ч а в и е. В числителе — значения Асгм после испытания на деформационное старение; в знаменателе — подсчитанное по фор муле Аам = А а2 —Аос.
Циклическое деформирование закаленно-отпущенной стали (Дв;э = 2%) сопровождается заметным изменени ем типа дислокационной структуры: квазиоднородное распределение дислокаций внутри мартенситных реек сменяется ячеистой структурой. Подобный характер из менения дислокационной структуры в условиях цикличе ского нагружения предполагает действие субструктуриого механизма разупрочнения. По данным [148], цикличе
ское упрочнение стали обусловлено деформационным старением, а циклическое разупрочнение — механическим и субструктурным разупрочнением. Вклад в циклическое разупрочнение каждого из механизмов зависит от темпе ратуры отпуска (см. табл. 9). Вклад субструктурного разупрочнения доминирует в образцах, отпущенных при 400 и 550° С. По аналогичному механизму разупрочияет- с.я и среднеуглеродистая сталь системы Fe—Ni—А1—Си, подвергнутая отпуску при 350 и 550° С (предварительный отпуск при 650° С) [149].
Файн с сотрудниками [148] пришли к выводу о боль шей информативности для циклически нестабильных ма териалов сравнения уровня aw с уровнем циклического предела текучести а'. До настоящего времени сравнение
проводили между ow и ав. Такое сравнение, вероятно, показательно для циклически стабильных материалов. На рис. 45 в виде полосы рассеяния показано влияние температуры отпуска на отношение ow!aT для сталей ти
па 4140. Это отношение растет с повышением темпера туры отпуска почти до 400° 2. В интервале температур от 400 до 650° С отношение а. ,/сг' практически постоянно. Не исключено, что подоб ный характер изменения
ow/a'T с температурой отпус ка обусловлен действием не
Рис. 45. Зависимость отношении пре |
Рис. 46. Кривые усталости стали! |
|||
дела усталости ош к циклическому |
Ге+16% Ni + 0,05% |
С |
(/) |
н Fe+13 |
напряжению текучести (0,2% деформа |
Ni—0,3% С стали |
(2) |
в свсжезак. |
|
ции) ат от температуры отпуска за |
ленном состоянии (Л) и после о |
|||
каленной средиеуглероднстой стали |
пуска при 350° С |
(В) |
[150] |
|
H48] |
|
|
|
|
скольких механизмов циклического разупрочнения. Ве роятно, изменение типа связи между aw и а ' при 400°С
не случайно.
При этой температуре концентрация углерода в твер дом растворе приближается к равновесной. С понижени ем температуры отпуска в твердом растворе растет кон центрация углерода и соответственно увеличивается вклад механизма механического разупрочнения. В Fe—Ni—А1—Си — стали после 1,5-ч отпуска при 350° С разупрочнение вследствие механической разблокировки дислокаций завершается за первые несколько циклов нагружения (ДеР = 0,04) [149]. С понижением темпера туры отпуска уменьшается также размер карбидных вы делений. Это способствует включению в процесс еще од ного механизма разупрочнения — структурного. Как по казано ранее, его вклад существен при температурах несколько выше комнатной. Кстати, при реализации структурного механизма разупрочнения растворение час тиц дисперсной фазы в пределах устойчивой полосы скольжения предполагает локальное повышение концент рации атомов углерода в твердом растворе. Можно пред положить, что атомы углерода в состоянии (по механиз му динамического деформационного старения) в какойто степени ограничивать подвижность дислокаций. В ре зультате следует ожидать снижения скорости цикличе ского разупрочнения.
Таким образом, стабильность углеродистой стали в значительной степени зависит от содержания углерода в твердом растворе. Это особенно относится к сталям с развитой субструктурой, образующейся при закалке на мартенсит. На рис. 46 представлены кривые усталости стали Fe+16% Ni+0,05% С и повышенной чистоты ста ли Fe+13% Ni+0,3% С, подвергнутых закалке на па кетный мартенсит (Р. Beardmore [61, с. 1898]). Видно заметное различие сталей в долговечности в мало- и мпогоцикловой областях усталости. При этом в зависимости от содержания углерода в стали системы Fe—Ni—С они могут упрочняться или разупрочняться. Сталь с содер жанием углерода от 0,05 до 0,1% разупрочняется. По оценкам [61, с. 1898], это соответствует 5—10 атомам уг лерода на атомную плоскость дислокаций. При содержа нии углерода выше 0,1% сталь обнаруживает существен ное циклическое упрочнение. Следовательно, закрепление развитой дислокационной субструктуры возможно только
при определенной концентрации углерода; ниже ее за крепления субструктуры не происходит. В процессе цик лического деформирования такая субструктура (квазиоднородное распределение дислокаций) начинает транс формироваться с образованием дислокационных ячеек. В этом отношении указанная сталь ведет себя аналогич но материалам в холоднодеформированном состоянии (например, железу и низкоуглеродистой стали после про катки).
Отпуск сталей Fe+16% Ni+0,05% С и Fe+13% N i+ +0,3% С при 350° С устраняет различие в усталостной долговечности (см. рис. 46). В этих сталях с одинаковым типом субструктуры содержание карбидов различное. Обе стали обнаруживают заметное циклическое разу прочнение. Беадмоо считает, что подобное поведение ста лей указанной системы обусловлено относительно низкой концентрацией углерода в твердом растворе. Атомы уг лерода, покидая места закрепления дислокаций, .образу ют массивные карбиды.
Режим отпуска по-разному влияет на сопротивление стали системы Fe—Ni—А1—Си малоцикловой и много цикловой усталости [149]. Старение при 350° С, 1,5 ч по сравнению со старением при 650° С, 1 ч+550° С, 8 ч обеспечивает наибольшее сопротивление усталости в ма лоцикловой области. Однако в многоцикловой области усталости более высокими усталостными свойствами об ладает сталь, состаренная по второму режиму. Пересе чение кривых усталости происходит при 104 циклов. Та ким образом, сталь после старения при 350° С в состоя нии аккумулировать большое количество пластической деформации, но вследствие интенсивного развития цикли ческого разупрочнения характеризуется относительно не большим сопротивлением многоцикловой усталости.
ВЛИЯНИЕ ТЕМПЕРАТУРЫ ОТПУСКА НА РАСПРОСТРАНЕНИЕ УСТАЛОСТНОЙ ТРЕЩИНЫ
Систематическое изучение влияния температуры от пуска на механические свойства и скорость распростра нения усталостной трещины dalcLN проведено в работе [25], выполненной на вакуумированной низколегиро ванной стали AISI 4140 (0,38% С). С повышением тем пературы отпуска ат вначале растет, а затем уменына-
ется, тогда как ав непрерывно снижается во всем иссле дованном интервале температур отпуска (табл. 10). Из табл. 10 следует, что все образцы после отпуска подвер жены циклическому разупрочнению. Интересно, что Кс для образцов толщиной 3,2 мм монотонно увеличивается с повышением температуры отпуска. С уменьшением толщины образца до 1,3 мм резко увеличивается Кс закаленных и отпущенных при 200° С образцов. После отпуска при 550 и 650° С влияние толщины образца практически не сказывается.
На рис. 47 показано изменение da/dN (образцы типа БНР и ВР [60]) в зависимости от температуры отпуска. Величина da/dN для образцов толщиной 3,2 и 1,3 мм до стигает максимальных значений в закаленном состоянии и после закалки и отпуска при 200° С. Начиная с АК =
= 125 кгс/мм3/2 и ниже, da/dN |
обнаруживает мини |
мум при температуре ^-'400° С. |
При этом величина |
da/dN заметно изменяется с толщиной образца. da/dN (мкм/цикл)
слева — 3,2; справа — 2,3
ТАБЛИЦА 10. ИЗМЕНЕНИЕ МЕХАНИЧЕСКИХ СВОЙСТВ И ВЯЗКОСТИ РАЗРУШЕНИЯ Kc( K i c) СТАЛИ 4140 В ЗАВИСИМОСТИ
ОТ ТЕМПЕРАТУРЫ ОТПУСКА И ТОЛЩИНЫ ОБРАЗЦА [25]
|
|
§ |
ав |
|
б |
|
|
К с, кгс/мм"/-1' |
|
Температура |
стт |
° т |
°f |
4> |
7 |
для толщин |
|||
отпуска, °С |
|
кгс/мм2 |
|
|
|
образца, мм |
|||
|
|
|
|
% |
|
1,3 |
3,2 |
||
25 ( закалка) |
122 |
138 |
190 |
227 |
8 |
21 |
0,230 |
381 |
131* |
200 |
146 |
128 |
179 |
259 |
7 |
34 |
0,410 |
496 |
150* |
400 |
128 |
78 |
140 |
169 |
8 |
39 |
0,500 |
406 |
230 |
550 |
99 |
62 |
ПО |
150 |
10 |
42 |
0,540 |
365 |
333 |
650 |
81 |
54 |
92 |
\ 134 |
14 |
46 |
0,610 |
339 |
349 |
П р и м е ч а н и е , — циклический предел текучести; а/ и е/ —
напряжение и деформация при разрушении.
*Кс =
Внешний вид поверхности разрушения в значитель ной степени зависит от толщины образца. В образцах толщиной 3,2 мм распространение трещины происходит преимущественно по межзеренному механизму. Доля разрушения этого типа растет с увеличением Д/G После
отпуска |
400° С при Д/С вплоть до |
~128 кгс/мм3/2 по |
|
верхность разрушения |
образована |
главным образом |
|
грубым |
бороздчатым |
рельефом, с ориентацией борозд |
вдоль направления распространения трещины (по типу
квазискола); при Д/(>128 кгс/мм3/2 возрастает доля разрушения по типу чашечного и в меньшей степени по типу хрупкого транскристаллитного скола и межзеренного разрушения [25].
Разрушение образцов толщиной 3,2 мм, отпущенных при 550 и 650° С, внешне похоже на характер разруше ния образцов, отпущенных при 400° С, при более низком уровне Д/С. Однако с ростом Д / С чашечный механизм разрушения после отпуска 550° С наблюдается только в
отдельных участках излома и полностью |
отсутствует |
после отпуска при 650° С. Кроме того, на |
поверхности |
разрушения довольно часто видны вторичные трещины, располагающиеся перпендикулярно основному направ лению распространения трещины. Эти трещины похожи на трещины полос скольжения, наблюдаемые Томкинсом. Расстояние между этими трещинами и ширина их возрастает с ростом ДК- Авторы работы [25] высказали предположение, что слияние микротрещин при /Стах,