
книги / Структура и усталостное разрушение металлов
..pdfщин, а также некоторые аспекты влияния структуры на пороговый коэффициент интенсивности напряжения. В целом эти вопросы нам представляются малоизучен ными. Решение их невозможно без применения современ ной техники анализа напряженного состояния и тонкого строения металла у вершины трещины, по размеру сопо ставимой с величиной зерна поликристалла.
Анализируя имеющиеся литературные данные по строению дислокационной структуры у вершины трещи ны, можно сделать следующие выводы. Качественно тип дислокационной структуры у вершины распространяю щихся и нераспространяющихся трещин одинаков. Одна ко у нераспространяющихся трещин, например в сплаве Al-f-0,5% Mg, размер пластической зоны у вершины трещины значительно меньше [203]. В стали с 0,03% С впереди ^распространяющейся трещины образуются субзерна размером более 2,7 мкм [204]. Избыточная плотность дислокаций, определяемая по углу разориентации соседних субзерен, у вершины трещины составля ет 5,5-1010 см~2. На образцах сплава Al+0,5% Mg с ра диусом у основания надреза 0,013 мм длина нераспрост раняющихся трещин зависит от амплитуды напряжения. Максимальный размер трещины, проросшей от основания, надреза и затем остановившейся в объеме сплава при дальнейшем циклическом нагружении, достигал 0,42 мм [203].
Частично на основе экспериментальных данных, а большей частью На основе общих рассуждений в литера туре высказаны несколько гипотез относительно причин
существования |
нераспространяю- |
ЛК, Kc/HH3fc>d,2 |
|
|||
щихсл трещин. |
Предполагается, |
|
|
|
||
что задержка роста |
усталостных |
|
|
|
||
трещин обусловлена |
следующи |
|
|
|
||
ми факторами: 1) деформацион |
|
|
|
|||
ным упрочнением металла у вер |
|
|
|
|||
шины трещины; 2) |
границами зе |
|
|
|
||
рен и субзерен; 3) частицами дис |
|
|
|
|||
персной фазы; |
4) |
деформацион |
|
|
|
|
ным старением; |
5) |
образованием |
|
|
|
|
плотной окисной пленки на по |
|
|
|
|||
верхности трещины, |
препятству |
|
|
|
||
ющей выходу дислокаций на по |
Рис. 71. Скорости роста тре |
|||||
верхность металла; |
6) переходом |
щин в |
сталях при |
/?= 0,33 |
||
трещины в объемы |
металла со |
/- 4 М Р ; |
[205]: |
3 — 2Р |
||
2 —- 5МР; |
||||||
|
|
|
|
и |
ЗР; 4 — 1FP |
|
сжимающими напряжениями, образующимися при на гружении или при различных режимах поверхностного упрочнения.
По данным [205], микроструктура стали также су щественно влияет на уровень ДДт (принято, что Д/Ст со ответствует da/dN= КН мм/цикл). На рис. 71 приведе ны данные по влиянию микроструктуры среднеуглероди стых сталей на da/dN в образцах типа SEN при У? = 0,33. При da/dN^1 0 ~ 5 мм/цикл скорость изменения da/dN от ДК определяется структурой материала. Химический со став, механические свойства и параметры структуры ис следованных сталей представлены в табл. 16.
Т А Б Л И Ц А 16. СВОЙСТВА СРЕДНЕУГЛЕРОДИСТЫХ СТАЛЕЙ [205]
|
Содержание, % (по массе) |
Объемная доля, % |
°0,2 |
1 °В |
||||
Сталь |
С |
Мп |
S |
феррит |
перлит |
мар |
кгс/мм* |
|
|
тенсит |
|||||||
IFP |
0,55 |
0,66 |
0,024 |
16,5 |
83,5 |
0 |
43,4 |
77,8 |
2Р |
0,54 |
1,44 |
0,028 |
2.5 |
97,5 |
0 |
44,5 |
85,7 |
ЗР |
0,55 |
1,84 |
0,024 |
1,0 |
99,0 |
0 |
49,8 |
92,6 |
4МР |
0,57 |
1,86 |
0,026 |
1,0 |
92,8 |
6,2 |
62,5 |
112,0 |
5МР |
0,55 |
2,23 |
0,024 |
0 |
95,1 |
4,9 |
59,0 |
105,4 |
Видно, что уровень ДКтдля сталей с различной мик роструктурой и механическими свойствами неодинако вый (табл. 17). Наибольшие значения Д/Ст наблюдаются у сталей со смешанной перлито-мартенситной структу рой. Величина Д/Ст существенно снижается с ростом R.
Достижение порогового состояния сталей лучше все го связано с /Стах и максимальным размером пластиче ской зоны (табл. 17).
Интересно, что влияние R и Ктах на da/dN начинает ся при достижении максимальным размером пластичес кой зоны величины, близкой к размеру зерна феррита и перлита (rf3=5,0-10~2 мм). Размер обратимой пластиче ской зоны определенно зависит от R. Он существенно
меньше размера зерна и по порядку близок к размере субзерен.
При этом, как отмечают авторы [205], в области зна чений ДК, близких к Д/Ст, в изломе преобладают кри сталлографические фасетки разрушения. Траектория
ТАБЛИЦА |
/7. ВЛИЯНИЕ СТРУКТУРЫ СТАЛЕЙ НА ДКТ. # raaI |
И РАЗМЕР |
МАКСИМАЛЬНОЙ И ОБРАТИМОЙ (« ''„ а х и ^ обр) |
ПЛАСТИЧЕСКОЙ ЗОНЫ У ВЕРШ ИНЫ ТРЕЩИНЫ [205] |
|
|
дкт |
*тах = «т |
|
*2 |
Сталь |
R |
|
кгс/мм^/2 |
w o6p * |
W шах ’ |
|
|
|
мм-10"-3 |
мм-10"-2 |
|
IFP |
0,26 |
21,2 |
28,6 |
6,11 |
4,49 |
|
0,27 |
21,1 |
28,9 |
6,20 |
4,59 |
|
0,34 |
17,4 |
26,4 |
4,17 |
3,84 |
|
0,51 |
14,1 |
28,8 |
2,74 |
4,55 |
2Р |
0,34 |
18,0 |
27,3 |
4,18 |
3,91 |
ЗР |
0,26 |
23,2 |
31,4 |
5,65 |
4,12 |
|
0,34 |
19,5 |
29,6 |
3,96 |
3,65 |
4Р |
0,34 |
26,1 |
39,6 |
4,36 |
3,65 |
|
0,50 |
19,6 |
40,4 |
2,70 |
4,31 |
5МР |
0,27 |
27,2 |
37,2 |
6,00 |
4,16 |
|
0,36 |
24,5 |
38,4 |
4,46 |
4,37 |
|
0,37 |
24,2 |
38,5 |
4,38 |
4,39 |
|
0,37 |
24,3 |
38,6 |
4,40 |
4,44 |
|
0,50 |
19,2 |
38,4 |
2,73 |
4,35 |
* К,тах = 1/Зя(К тах/ам )2.
движения трещины довольно сложная. Подобный тип из ломов обычно связывают с ограниченным числом систем скольжения, действующих у вершины усталостной тре щины [206].
По Лукашу и Клеснилу, между Д/Ст и Д с о о т в е т
ствующим пороговому коэффициенту интенсивности на пряжения при R = 0, наблюдается простое соотношение
ДКт=Д/(1о(1—tf)v где у — параметр, отражающий
свойства материала.
В литературе известны данные о том, что величина у изменяется от 0,7—1,0 для феррито-перлитных и полно стью перлитных сталей до ~0,5 —для мартенситных сталей. Подобный тип связи легко может быть выведен из известных соотношений. По определению Д/С=/Стах—
—/Сщщ и R=Km\n/Kmax. Если эти соотношения |
справед |
ливы И Д Л Я пороговых условий, Т О Д ^ т = / ( т т а х |
— Д ’т ш . п |
и tf= tfTmIn//fTmax • Отсюда следует, что при R = 0 Д/Ст= =/Сттах= ^т„- Следовательно, Д/Ст=КХо (1—R)-
Лал и Вейс, обобщив имеющиеся в литературе дан ные по величине ДКГо для углеродистых и нержавеющих
сталей различного состава, пришли к выводу, что Д/СТо =
= 20,1 ±2,9 кгс/мм3/2. Существенно более высокие значе ния ДКТо получены Мазонейв и Бейлон [61, с. 639] для
крупнозернистых феррито-перлитных сталей (табл. 18).
Т А Б Л И Ц А 18. ХАРАКТЕРИСТИКИ СТРУКТУРЫ, МЕХАНИЧЕСКИЕ
с в о й с т в а и з н а ч е н и я ДКт0 ф е р р и т о -п е р л и т н ы х с т а л е й
[61, с. 639]
|
|
|
|
СЧ |
|
|
|
|
|
а |
|
СО |
|
|
ат> кгс/мм* |
d, мкм fa |
АЛ мкм |
а |
- |
а |
d, мкм |
fa |
|
- о |
н |
* |
АЛ мкм |
||||
|
|
Ь * |
< |
* |
|
|
|
сч
‘ С| V *
* g
<1 2
19,0 |
0,954 |
Не'опр. |
21,8 |
25,6 |
7,5, |
0,20 |
0,19 |
47,7 |
34,9 |
|
40,0 |
0,945 |
» |
» |
19,2 |
33,0 |
8 ,3 , |
0,29 |
0,17 |
43,0 |
25,3 |
152,0 |
0,950 |
» |
» |
16,8 |
58,6 |
6 - 9 |
0,45 |
0,19 |
49,3 |
22,4 |
64,0 |
0,85 |
» |
» |
24,5 |
35,8 |
— |
0 |
0,26 |
53,2 |
36,5 |
87,0 |
0,86 |
» |
» |
20,6 |
48,0 |
— |
0 |
0,22 |
48,0 |
32,6 |
134,0 |
0,73 |
» |
» |
17.2 |
53.8 |
|
0 |
0,21 |
48,8 |
32,6 |
9,9 |
0,32 |
0,19 |
40.2 |
28.8 |
|
|
|
|
|
* Межчастичное расстояние.
Величина АКТп зависит от величины зерна феррита:
A K ^ A K o + K f d 1' 2.
Отсюда следует, что в противоположность влиянию величины зерна на предел текучести измельчение зерна снижает сопротивление феррита распространению ранее возникших усталостных трещин.
Подобным образом влияет величина зерна феррита и в феррито-перлитных сталях. В табл. 18 приведены па раметры микроструктуры и механические свойства фер рито-перлитных сталей, содержащих от 0,07 до 0,8% С. Предложено уравнение вида:
АДГт. = Га [АКо + К ,d1/2) + (l - /£) АКр.
где fa — объемная доля феррита; АКр — вклад перлита.
Множественный регрессионный анализ данных табл. 18 обнаружил, что АКо=0, /0= 1,58 -102 кгс/мм2, АКР= =33,0 кгс/мм3/2 и и » 1.
Следовательно, межпластинчатое расстояние в пер лите оказывает незначительное влияние на ДК .
184 |
То |
Г Л А В А VIII
ПУТИ И С П О С О Б Ы П О В Ы Ш Е Н И Я
Ц И К Л И Ч Е С К О Й П Р О Ч Н О С Т И С Т А Л Е Й И С П Л А В О В
Рассмотренные выше закономерности развития уста лостной повреждаемости и разрушения в сталях и спла вах с различной структурой и субструктурой позволяют сделать некоторые общие выводы по повышению цикли ческой прочности.
1. Предотвращение появления в структуре трещин, образующихся в процессе закалки, послезакалочного вы леживания и отпуска, а также зон концентрации дефор мации. Исключительно большое значение имеет ограни чение неблагоприятного влияния крупных неметалли ческих включений и обедненных зон. Уменьшение числа трещин в термически обрабатываемых сплавах достига ется соответствующим выбором режимов термической обработки и отпуска (старения); ширина обедненных зон также контролируется режимом термической обра ботки.
2. Повышение однородности (по объему) пластиче ской деформации, осуществляемое с помощью стабиль ных некогерентных выделений дисперсной фазы (опти мального размера и распределения), стабилизации раз витой субструктуры, снижения склонности дислокаций к поперечному скольжению (при снижении ЭДУ сплава).
3. Повышение напряжения циклической микротеку чести.
Повысить уровень этого напряжения можно легиро ванием элементами внедрения и замещения; интенсив ным деформационным старением; формированием устой чивой субструктуры и созданием с помощью различных обработок в поверхностном слое остаточных напряжений сжатия.
Для обоснованного выбора способа повышения цик лической прочности сталей и сплавов необходимо преж де всего учитывать схему и режим нагружения, а также условия (температуру, среду и т. д.) эксплуатации. Це лесообразно также принять во внимание свойственный данному материалу в данном структурном состоянии ме ханизм усталрстцой повреждаемости и разрушения.
В настоящее время становится актуальным вопрос об оптимизации параметров структуры (размера и распре деления частиц дисперсной фазы, размера зерна и т. л.) сталей и сплавов, предназначенных для использования в условиях переменных нагрузок прежде всего с точки зре ния максимального сопротивления усталости. Широко практикуемая оптимизация параметров структуры по ре зультатам статических испытаний часто не обеспечивает достаточно высокого комплекса эксплуатационных ха рактеристик сплавов.
Поскольку сопротивление усталости в значительной степени связано с состоянием поверхностных слоев ме талла, большинство традиционных методов повышения циклической прочности основано на активном воздейст вии на поверхность детали или элемента конструкции. К таким воздействиям относятся поверхностный наклеп (обкатка роликами, дробеструйная обработка и т. п.), поверхностная закалка ТВЧ, поверхностная термомеха ническая обработка, цементация, покрытия и т. д. Повы шение циклической прочности при различного рода по верхностных упрочняющих обработках обеспечивается как путем создания структуры и субструктуры, облада ющих повышенным сопротивлением усталости, так и в результате появления в поверхностных слоях материала сжимающих остаточных напряжений.
В тех случаях, когда необходимо обеспечить не толь ко высокое сопротивление зарождению трещины, но и затормозить ее распространение — целесообразно ис пользовать методы объемного упрочнения. В этом отно шении благоприятные возможности открывает термоме ханическая обработка (ТМО) сталей и сплавов.
Авторы не ставили себе целью рассмотреть все из вестные способы повышения циклической прочности и тем более приводить результаты (за некоторым исклю чением) многочисленных примеров успешного примене ния этих методов к реальным элементам конструкций и деталям машин. Рассмотрены в основном методы упроч нения, в которых с целью получения высокого уровня циклической прочности используется в той или иной сте пени принцип оптимизации или создания структуры и субструктуры с повышенным сопротивлением процессу зарождения и развития усталостной повреждаемости и разрушения,
Повышение циклической прочности Материалов с по мощью поверхностного наклепа — традиционный и эф фективный способ упрочнения. Развитая дислокационная субструктура и появление в поверхностных слоях оста точных напряжений сжатия — основные факторы, обу словливающие заметное повышение усталостных свойств сталей и сплавов.
В работе [207], выполненной на сталях 18Х2Н4ВА и 45ХНМФА, повышение усталостной прочности при по верхностном пластическом деформировании происходит более интенсивно в стали с мартенситной структурой и менее интенсивно — при сорбитной (рис. 72, кривые 1— 4) и трооститной (рис. 72, кривые 2, 5) структурах. Ис пытания на изгиб с вращением и кручение влияют на усталостную прочность практически одинаково. Рост предела усталости стали с сорбитной и трооститной структурами при сравнительно небольших усилиях об катки затухает, а стали с мартенситной структурой ста билизируются только при очень больших усилиях об катки.
Остаточные напряжения сжатия, появляющиеся в по верхностном слое после обкатки образцов сталей 18Х2Н4ВА и 45ХНМФА, имеют максимальный уровень
Рис. 72. Зависимость предела усталости стали с различной исходной структу рой от усилия обкатки [207]:
а — сталь 18Х2Н4ВА; б — сталь 45ХНМФА; 1—3 — изгиб с вращением; 4—6 — кручение; 1 , 4 — сорбит; 2, 5 — троостит; 3, 6 — мартенсит
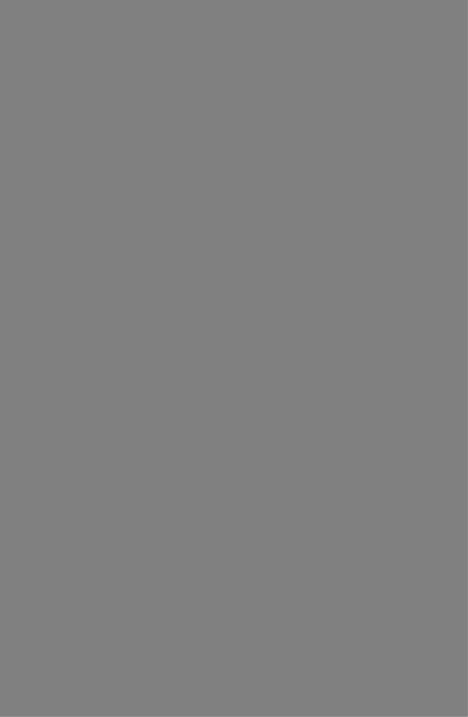
Необходимо иметь в виду, что эффективность обкат ки, увеличивающаяся с повышением уровня статической прочности, наблюдается не во всех случаях. В качестве основной причины снижения интенсивности повышения уровня предела усталости М. А. Балтер называет малое сопротивление хрупкому разрушению и повышение чув ствительности к концентрации напряжений стали с мар тенситной структурой (табл. 19). Этим же объясняется различный характер изменения предела усталости ста лей с разной структурой в зависимости от величины сжи мающих напряжений.
ТАБЛИЦА 19. СТРУКТУРА И МЕХАНИЧЕСКИЕ СВОЙСТВА СТАЛЕЙ 18Х2Н4ВА и 45ХНМФА [207]
Структура |
° В |
1 СТ- 1 |
|
А . |
|
|
K B = a - l / ° B |
“ п* |
|
|
кгс/мм2 |
кгссм |
||
|
|
|
||
|
Сталь |
18Х2Н4ВА |
|
|
Сорбит . |
98,5 |
45/53 |
0,46/0,54 |
723 |
Троостит |
120 |
52/67 |
0,43/0,56 |
321 |
Мартенсит |
146 |
56/84 |
0,38/0,57 |
228 |
|
Сталь 45ХНМФА |
|
|
|
Сорбит . |
134 |
57/76 |
0,42/0,56 |
302 |
Троостит |
153 |
62/78 |
0,40/0,51 |
114 |
Мартенсит |
208 |
67/86 |
0,32/0,41 |
24 |
П р и м е ч а н и е . В числителе — данные до обкатки, в знамена теле— после обкатки. А п — полная работа разрушения при статиче ском изгибе образцов с трещиной.
Благоприятное влияние поверхностного наклепа за висит от того, в какой степени созданная в результате наклепа субструктура устойчива к механическому воз действию. Высокая степень устойчивости субструктуры поверхностного наклепа (дробью) достигнута в стали 40ПП, содержащей 0,6% V [199]. Сравнение усталост ной прочности образцов из сталей 40ПП и 40ПП + + 0,6%V в поверхностно-наклепанном состоянии (с уче том получения одинаковой прочности перед наклепом) показало, что даже при одинаковой прочности сталь с 0,6% V обладает более высокими усталостными характе
ристиками. Величина or_i стали 40ПП+0,6% V (отпуск 600° С) достигает 122 кгс/мм2, а у стали 40ПП (отпуск 450° С) 68 кгс/мм2.
Авторы работы [199] считают, что в дисперсионноупрочняемой углеродистой стали, легированной ванади ем, перемещение дислокаций ограничивается размерами субзерен. В результате затруднена релаксация напряже ния поверхностного слоя и отдаляется процесс образо вания усталостных трещин. В углеродистой стали суб структура не стабилизирована и дислокации относитель но легко проникают через субграницы, способствуя быстрой релаксации напряжений в поверхностном слое. Данные рентгенографического анализа (по физическому уширению линии Р221) указывают на более интенсивное снижение остаточных напряжений сжатия у стали 40ПП без ванадия.
Положительное влияние поверхностного наклепа на усталостные свойства стали 40ПП с ванадием и без вана дия сохраняется в широком интервале температур от пуска (вплоть до 600° С). В целом упрочнение стали 40ПП частицами дисперсной фазы в комбинации с поверхно стной дробеструйной обработкой обеспечивает рекорд ный уровень циклической прочности (симметричный кон сольный изгиб) (рис. 73).
Интенсивность поверхностного наклепа сплавов за висит от величины ЭДУ. По данным Боггса Брайяна и
б, кгс/ммг |
Бирна, |
|
устойчивость |
(ста |
|||||
бильность) |
остаточных на |
||||||||
|
|||||||||
|
пряжений |
(после упрочняю |
|||||||
|
щей |
дробеструйной обработ |
|||||||
|
ки) |
при |
усталости |
заметно |
|||||
|
выше у |
никелькобальтового |
|||||||
|
сплава |
с пониженной |
ЭДУ. |
||||||
|
Более |
легкая подвижность |
|||||||
|
дислокаций в сплаве на ос |
||||||||
|
нове |
|
никеля |
(величина |
|||||
|
ЭДУ«185 |
эрг/см2) |
способ |
||||||
|
ствовала |
большей |
по |
срав |
|||||
|
нению со сплавом на основе |
||||||||
|
кобальта (ЭДУ |
39 эрг/см2) |
|||||||
Рис. 73. Циклическая прочность по |
интенсивности |
релаксации |
|||||||
остаточных напряжений. |
|||||||||
верхностно упрочненных сталей |
|||||||||
ле отпуска при 450 (/), 550 (2) и |
В общем случае сущест |
||||||||
40ПП с 0,6% V и без ванадия пос |
венное |
|
влияние |
структуры |
|||||
600° С (3) [199] |
|