
книги / Структура и усталостное разрушение металлов
..pdfпозволяет прогнозировать резкое увеличение da/dN на третьем участке зависимости da/dN =f(AK ). В этой об ласти амплитуда локальных напряжений сравнима с разрушающими напряжениями при статическом рас тяжении. При этом пластически деформируются до вольно большие объемы металла, по размеру сравни мые с величиной зерна. В этом случае для оценки п и OFF оправдано использовать характеристики, получен ные на гладких образцах.
Остановимся на вопросах, связанных с условиями появления усталостных микрополос. Плумбридж и Рай дер [62], а также В. С. Иванова с сотрудниками [63] предположили, что образование усталостных микропо лос свидетельствует о реализации в вершине трещины плоско-деформированного состояния. В. С. Иванова связывает образование усталостных микрополос со ста дией стабильного роста трещины, считая, что ширина микрополосы равна приращению трещины за один цикл. Появление микрополос отождествляется с образо ванием впереди магистральной трещины дислокацион ной трещины скола по механизму двойного плоского скопления. Силовые и энергетические условия распрост ранения трещины в рамках этого механизма подробно рассмотрены в работах [6, 64].
В работе [65] показано, что для стали А533, стали системы Ni — Мо — V и стали НР9-4-25, а также алю миниевых сплавов 7079-Т6 и 5456-Н321 и сплава Ti+ +6% Al+4% V изменение ширины А усталостных мик рополос в зависимости от АК/Е подчиняется зависи мости:
(17)
Усталостные испытания проводили на образцах с од ним боковым надрезом. Вне зависимости от конкретно го состава все сплавы располагались в пределах одной полосы разброса. Сопоставление данных по изменению расстояния между микрополосами А и макроскопичес кой скоростью роста трещины от Д/С показывает, что в интервале значений АК— 112-=-245 кгс/мм’/» наблюдается хорошее совпадение (рис. 21). Полоса рассеяния А шире полосы рассеяния da/dN, что, по-видимому, обусловле но большей экспериментальной ошибкой при измерении А. Макроскопическая скорость роста трещины при Д/С
менее 112 кгс/мм3/2 меньше, чем величина А. Не исклю
чено, что при малых Д/С трещина иногда останавлива ется.
При больших Д/С реализуются две возможности [65]. Так, макроскопическая скорость роста в стали А533 уменьшается относительно Д из-за нестабильного роста трещины, когда рост трещины в течение многих
циклов тормозится |
(см. рис. |
21). Однако в сталях сис |
темы Ni — Мо — V и стали |
НР9-4-25 при больших Д/С |
|
макроскопическая |
скорость |
роста значительно больше |
расстояния между микрополосами. В этом случае в зна чительной части излома микрополос не наблюдается, видны участки чашечного разрушения и относительно бесструктурные области. Предполагается, что при этих Д/С трещина распространяется большими скачками. Таким образом, нестабильный рост трещины при боль ших Д/С сопровождается образованием микрополос с меньшими Д и «вступлением» в действие другого мик ромеханизма разрушения.
В. А. Степаненко, А. Я. Красовский [66], исследуя железо (0,05% С) (круговой изгиб, диаметр рабочей
части образца |
15 мм), |
обнаружили, |
что среднее |
рас |
||||||||
стояние между микрополосами, измеренное |
на |
поверх |
||||||||||
|
|
|
|
|
|
ности излома, почти на порядок |
||||||
|
|
|
|
|
|
больше ожидаемого в результа |
||||||
|
|
|
|
|
те измерения |
макроскопической |
||||||
|
|
|
|
|
|
скорости роста. Подобная ситуа |
||||||
|
|
|
|
|
|
ция возникает в том случае, когда |
||||||
|
|
|
|
|
действует |
несколько |
микромеха |
|||||
|
|
|
|
|
низмов разрушения. В локальных |
|||||||
|
|
|
|
|
|
зонах (например, в благоприятно |
||||||
|
|
|
|
|
|
ориентированных зернах) |
возни |
|||||
|
|
|
|
|
|
кают транскристаллические |
вяз |
|||||
|
|
|
|
|
|
кие или хрупкие трещины. При не |
||||||
|
|
АК, matin 3/2 |
|
прерывном циклическом нагруже |
||||||||
|
|
|
нии в перемычках между трещи |
|||||||||
Рис. |
21. Изменение |
расстоя |
нами происходит разупрочнение |
|||||||||
границ и накопление |
поврежде |
|||||||||||
ния |
между |
усталостными |
||||||||||
микрополосами |
Л (/) и |
за |
ний в неразрушенных |
зернах. В |
||||||||
висимость |
макроскопической |
|||||||||||
скорости |
роста |
трещины |
результате |
возникают |
условия |
|||||||
daJdN (2) от размаха коэф |
для быстрого и плавного, с обра |
|||||||||||
фициента |
интенсивности |
на |
||||||||||
пряжений |
в |
образцах |
из |
зованием |
зернограничных |
уста |
||||||
стали |
Л533, испытанных |
при |
||||||||||
24° С |
(приведены |
полосы |
лостных микрополос, разрушения |
|||||||||
рассеяния |
соответствующих |
перемычек железа. |
|
|
|
|||||||
характеристик) |
[65] |
|
|
|
|
В поликрпсталлйческом сплаве Fe+2,9% Si, испы танном на усталость в вакууме в условиях растяже ния— сжатия в интервале температур 100—250° С, об наружено действие двух микромеханизмов разрушения [67]. В образцах, циклически нагружаемых при 100 и 150° С, наблюдается медленный рост трещины с образо ванием в некоторых зернах участков хрупкого разруше
ния сколом. При |
понижении температуры |
растет доля |
|
площади излома, |
занимаемая участками |
скола. При |
|
100° С хрупкое разрушение сколом |
занимает всю по |
||
верхность излома. На фоне фасеток |
скола с «ручьистым |
узором» видны усталостные микрополосы. Расстояние Д между микрополосами изменяется пропорционально АК в степени ~ 3 /2 .
Скорость роста трещины, рассчитанная по податли вости образца, меньше, чем величина Д, измеренная по данным фрактографического анализа изломов. Это ука зывает на возможность задержки трещины. Интересно, что величина da/dN зависит от Д/С и не зависит от /Стах. Последнее согласуется с выводами [57] о незави симости da/dN от /Стах в случае разрушения по меха низму усталостных микрополос. Если же при росте усталостной трещины наблюдаются значительные уча стки хрупкого скола, то величина da/dN в значительной степени зависит от средних напряжений цикла (или R).
На рис. 22, а, б представлено изменение величины т в выражении (9) для среднеуглеродистых сталей Р (0,55% С; 0,66% Мп) и МР (0,55% С; Мп 2,33%) при разных R [57]. Механические свойства сталей Р и МР соответственно: сто,2=43,4 и 75,3 кгс/мм2, ав= 77,8 и
112,4 кгс/мм2; 6=24,7 и 21,7%, /С|с=160 и 134 кгс/мм3/2- Видно, что по сравнению со сталью МР величина т для стали Р при всех значениях R имеет общий мини мум. Увеличение скорости роста трещины в стали МР зависит от R. Несмотря на то, что значения К\с обеих
сталей |
близки, характер разрушения их |
различен. |
Сталь |
Р разрушается полностью хрупко за |
последний |
цикл нагружения. Это происходит при значениях /Стах приблизительно на 30% больших К\с. Для стали МР с ростом /Стах свойственно увеличение доли разрушения
по механизму хрупкого скола, |
при этом |
разрушение |
сколом при R от 0,10 до 0,72 |
начинается |
при /С т а х = |
=48 кгс/мм3/2 и выше этого значения существенно за висит от Д/С.
Наибольшее влияние на da/dN отмечено при /Сшах^
^ 9 6 кгс/мм3/2, |
когда отдельные |
фасетки |
скола слива |
||
ются в один сплошной массив. С ростом R от 0,33 до |
|||||
0,70 значения т выросли от 6 до |
17 (см. рис. 22, а). |
||||
Больших |
значений достигает |
т и при разрушении |
|||
с участием микромеханизма |
квазискола. |
Углеродистые |
|||
стали с 0,38—0,39% С и 0,44—0,45% С |
(см. табл. 4) |
||||
в закаленном |
и |
отпущенном |
ниже 400° С состояниях |
разрушаются с образованием перемежающихся облас тей чашечного разрушения и квазискола [55].
Поверхность разрушения образцов, отпущенных вы ше 400° С, показывает совершенно другие особенности разрушения. Основную долю излома занимают участки вязкого разрушения. Усталостные микрополосы видны только в отдельных, изолированных участках излома. Чаще всего они характеризуются нерегулярным рассто янием между микрополосами. При температурах отпус ка выше 400° С влияние состава и чистоты стали отно сительно слабое.
Таким образом, из изложенного можно сделать сле дующие выводы: 1) наименьшей скорости распростра нения усталостных трещин соответствует разрушение по микромеханизму образования пластичных микрополос; 2) при этом микромеханизме разрушения средние на пряжения слабо или совсем не влияют на величину
Рис. 22. Зависимость величины т |
от |
da/clN |
для сталей Р (а) и МР (б) [57] |
при |
R, |
равных: |
|
/ — 0,10; |
2 — 0,33; |
3 — 0,70 |
da/dN\ влияние их наблюдается при переходе к третье му участку зависимости da/dN=f(kK) и связано с вступлением в действие других микромеханизмов раз рушения; хрупкого транскристаллитного скола, квазискола или чашечного; 3) при разрушении с образовани ем пластичных микрополос влияние структуры металла на da/dN очень слабое или практически отсутствует.
Подобный характер влияния структуры на скорость распространения трещины на стадии II предполагает действие какого-то универсального фактора, устраня ющего влияние структуры. По-видимому, таким факто ром является интенсивная пластическая деформация у вершины трещины. Многочисленными исследованиями показано, что у вершины трещины, в том числе в усло виях плоской деформации, происходит развитие ячеи стой или субзеренной структуры. Образование подобной структуры у вершины распространяющейся усталост ной трещины — процесс в достаточной степени общий для многих материалов особенно с высокой энергией де фектов упаковки. Изменение субструктуры у вершины трещины подробно рассмотрено в монографии [6]. Яче истую структуру у вершины трещины наблюдали в ма териалах с о.ц.к., г.ц.к. и г.п.у. решетками, в том числе в тех случаях, когда матрица упрочнялась частицами второй фазы. В работе [68], выполненной на железе с использованием электронного микроскопа с ускоря ющим напряжением 500 кВ, обнаружено, что у вершины трещины образуется пластическая зона, в которой раз меры ячеек составляют 0,5 мкм. Наблюдаемый нами и В. С. Ивановой в поликристаллическом железе (0,02% С) на расстоянии 7—20 мкм от вершины трещины размер ячеек 0,35—0,45 мкм практически совпадает с данным в работе [68]. Размер субзерен у вершины трещины увеличивается с понижением энергии дефектов упаковки, составляя 2,6; 1,4; 2,8 и 7,6 мкм для алюминия, меди, а-латуни и алюминиевой бронзы соответственно [69]. Отсюда вывод, что именно дополнительной пластической деформацией у вершины трещины объясняется слабое влияние исходной структуры материала иа скорость ро
ста усталостных трещин.
Принципиальным моментом в понимании механизма распространения усталостной трещины является вопрос о соотношении скачка трещины и параметра субструкту ры у вершины трещины. Интенсивная пластическая де
формация у вершины трещины происходит как в усло виях плоской деформации, когда образуются микропо лосы, так и в условиях плосконапряженного состояния, когда возникают чашки. Авторы работ [6, 70] при сопо ставлении параметров дислокационной структуры у вер шины трещины и рельефа излома в зоне роста трещины в условиях плоской деформации пришли к выводу, что стабильный рост трещины с минимальной скоростью сохраняется до тех пор, пока величина микроскачка тре щины не станет близкой или равной размеру субзерна (ячейки) вторичной структуры, образующейся в пла стической зоне у вершины трещины.
Поскольку во многих, особенно пластичных металлах, минимальные размеры субзерен близки, нет ничего уди вительного в совпадении величин скачков трещин на стадии стабильного роста усталостной трещины. Не яс ным остается вопрос о траектории распространения ус талостной трещины на стадии стабильного роста. Воз можны, вероятно, два пути распространения трещины: по границам субзерен (ячеек) или по телу субзерен. Совпадение траектории трещины с границами субзерен отмечалось в работах [69, 70]. К такому же выводу при шли В. И. Трефилов с сотрудниками [71] при исследо вании распространения вязкой трещины в армко-железе в условиях статического растяжения.
Пример разрушения по границам ячеек с образова нием «пилообразного» профиля трещины при статиче ском растяжении фольги железа, приготовленной из об разца, испытанного на усталость выше предела устало сти, представлен на рис. 23. Траектория трещины про ходит по границам ячеек, границы которых в данном случае ориентируются под углом 45° к направлению рас пространения трещины; шагу между «зубцами» соответ ствует диагональ куба. Шаг излома в среднем состав ляет 0,34 мкм при величине ячейки (вдоль) стороны ку ба 0,48 мкм. Эти размеры субзерен в окрестности трещины существенно меньше субзерен вне зоны влияния трещины. Можно предположить, что при распростране нии трещины у ее вершины произошла дополнительная пластическая деформация. Зарождение микротрещин на рис. 23 видно в месте пересечения полос скольжения с границей зерна (маленькие стрелки); плоскости раз рушения субмикротрещин ^располагаются вдоль нап
равлений, близких [ПО] и [ПО].
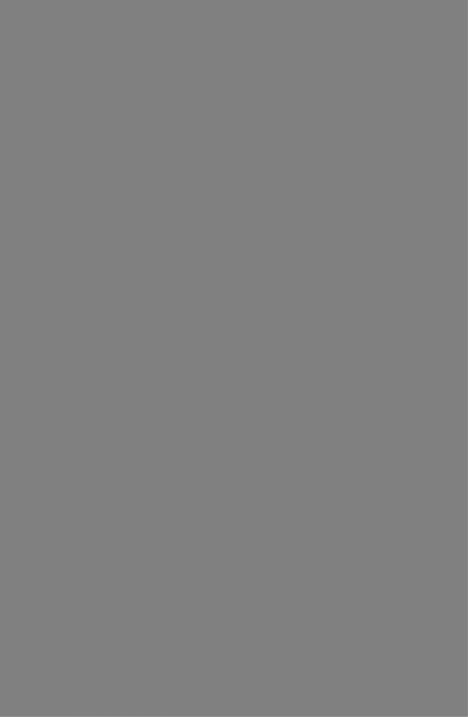
минимальному размеру ячейки (субзерну) вторичной субструктуры у вершины трещины. В случае меньшей интенсивности напряжения при распространении тре щины границы ячеек не повреждаются. В результате смены микромеханизма распространения трещины про исходит изменение скорости роста трещины.
Г Л А В А III
УС Т А Л О С Т Н А Я
ПО В Р Е Ж Д А Е М О С Т Ь
О Д Н О Ф А З Н Ы Х М А Т Е Р И А Л О В
ФОРМИРОВАНИЕ РАЗВИТОЙ СУБСТРУКТУРЫ
В ПРОЦЕССЕ УСТАЛОСТНОГО НАГРУЖЕНИЯ
Для широкого круга металлов и сплавов, как одно фазных, так и многофазных, усталостная повреждае мость обусловлена эволюцией дислокационной структу ры в пластичной матрице. К настоящему времени систе матические исследования изменения дислокационной структуры в процессе усталости выполнены практически для всех пластичных однофазных материалов (железо, медь, алюминий, никель, нержавеющая сталь и некото рые другие). В зависимости от материала, вида нагруже ния, температуры испытания и амплитуды напряжения (деформации) наблюдается широкий спектр дислокаци онных структур: по мере увеличения числа циклов на гружения растет плотность дислокаций и вначале обра зуются сплетения, сгущения дислокаций, а затем ячеи стая и субзеренная структуры (рис. 24). Эволюция дислокационной структуры протекает в различных мате риалах с разной степенью интенсивности, охватывая все сечение образца или сосредоточиваясь только в некото рых объемах, например в поверхностном слое.
Влияние различных факторов, структуры металла и режима циклического нагружения на дислокационную структуру циклически деформируемых материалов об стоятельно рассмотрено в монографиях [6, 16]. В этой работе остановимся более подробно на особенностях формирования субструктуры (ячеек, субзерен) в процес
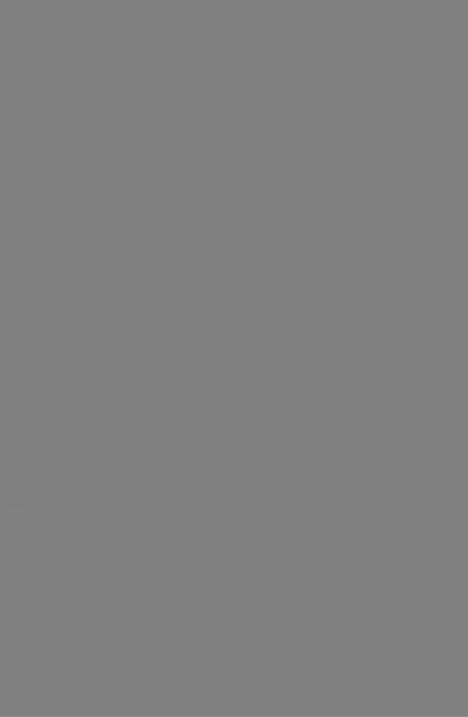
Область существования развитой субструктуры
Вероятность появления развитой субструктуры зави сит от материала, вида нагружения, температуры испы тания, амплитуды и числа циклов нагружения. На рис. 25 схематически показано изменение типа дислокацион ной структуры в отожженных поликристаллическом же лезе (0,02% С) и молибдене, испытанных на усталость при комнатной температуре в условиях повторного рас тяжения. Для пластичного железа, у которого предел усталости ow выше предела текучести сгт, ячейки образу ются при амплитудах напряжения сга ниже ow• У более хрупкого молибдена, для которого а ^ < а т, область су ществования развитой дислокационной структуры суще ственно выше Ow- Момент появления ячеистой структуры зависит от сга и числа циклов нагружения. Использова ние для испытания на усталость более жестких схем на гружения смещает область существования развитой суб структуры в область более низких амплитуд напряжения (деформации). Еще в ранних исследованиях [73] обна ружено, что на структуру существенно влияет амплиту да напряжения. После деформации алюминия при на пряжениях, обеспечивающих долговечность ~ 105 цик лов, возникала ячеистая структура, при этом размер ячеек и плотность дислокаций в стенках ячеек были за метно больше, чем в образцах после деформации растя жением до одинаковой средней плотности дислокации. При более низких аа (ожидаемая долговечность ~10° циклов) ячейки не возникали. Наблюдались достаточно
оа, кгс/пп2 |
6а, пгс/пм2 |
Рис. 25. Область существования ячеистой |
(/) и полосовой (2) структу |
|
ры в поликристаллическом железе |
(а) и молибдене (б), испытанных на |
|
многоцикловую усталость в |
условиях |
повторного растяжения |