
книги / Структура и усталостное разрушение металлов
..pdfравномерно расположенные сплетения дислокаций, а также высокая плотность дислокационных петель и гели коидов.
Исследователи неоднократно обращали внимание на сходство циклической деформации монокристаллов и по ликристаллов в малоцикловой области усталости и пове дение монокристаллов на II и III стадиях статического деформирования. Прежде всего совпадает тип дислока ционной структуры. В условиях циклического и статиче ского нагружения скорость деформационного упрочнения одинаково зависит от температуры и ЭДУ.
В многоцикловой области усталости характер цикли ческого упрочнения для некоторых материалов аналоги чен I стадии статического деформирования монокристал лов. Однако в одних и тех же материалах в зависимости от типа нагружения (растяжение — сжатие, повторное растяжение, изгиб и т. д.) наблюдается различная дис локационная структура.
В работе [74] установлено, что в поликристаллическом железе Ferrovac Е средний размер ячейки dnч тесно связан с амплитудой пластической деформации Дер. На стадии насыщения dn4= 1,25±0,09 мкм при Дер = 0,048 и увеличивается до 2,38±0,26 мкм при ДеР = 0,003. При этом уровень напряжения насыщения (as) связан с dn4
зависимостью типа os=M d7J. Авторы [74] считают, что для каждого уровня насыщения есть равновесный раз мер ячейки, который не изменяется при дальнейшем цик лическом нагружении.
Таким образом, при определенной температуре и скорости пластической деформации уровень насыщения и, следовательно, размер ячейки являются функцией ам плитуды пластической деформации.
Зависимость типа ds= M d 7ч |
обнаружена у железа |
[75], нержавеющей стали [76] |
и в некоторых других ме |
таллах. Исследуя железо в условиях повторного растя жения, авторы работы [75] установили, что ячейки обра зуются при достижении в зернах критической плотности дислокаций (6±1) Ю9 см-2. Образование ячеек проис ходит путем формирования у вытянутых сплетений дис локаций поперечных дислокационных стенок (сплете ний). При этом по данным корреляционно-регрессионно го анализа между средней по образцу плотностью дисло
каций р и dm существует зависимость вида dfl4=Kp~~ll2i
где К — коэффициент пропорциональности. Отсюда сле дует, что для ячеистой структуры с учетом зависимости
типа G = Go+aGb У р получаем сг=ао+ (aGK)/dn4t т. е.
O' Л / | я ч •
По данным работы [77], формирование ячеек в мо либдене, хроме и вольфраме происходит при цикличес ком нагружении (плоский изгиб) с амплитудами нагру жения и временем экспозиции, при которых появляются трещины усталостного происхождения. Ряд исследовате лей [78, 79] отмечают тесную связь развитой субструк туры с процессами деформационного старения. Сегрега ция атомов углерода и азота вдоль дислокаций и части цы дисперсной фазы задерживают формирование суб структуры и развитие усталостной повреждаемости.
Влияние поверхностного слоя
Повышенную плотность дислокаций в поверхностном слое при испытании на усталость в условиях повторного растяжения наблюдали в пластичном железе при темпе ратурах 20 и —196° С [80, 81], молибдене [61, с. 590; 82]
истали 14Х2ГМР со структурой мартенсита отпуска
[83]при комнатной температуре испытания.
Субструктура поверхностного слоя чаще всего похо жа на структуру внутренних слоев, которая образуется при существенно больших амплитудах напряжения (де формации). Например, в поликристаллическом железе при —196° С в поверхностном слое толщиной до 10 мкм формируются плотные сгущения типа мелкоячеистой структуры, характерной для комнатной температуры ис пытания [80]. В остальном объеме образца видны-пря молинейные отрезки дислокаций преимущественно вин товой ориентации, т. е. видна структура, свойственная низкотемпературной деформации. Плотность дислокаций на 1—2 порядка меньше, чем в поверхностном слое.
Не останавливаясь на природе аномального поведе ния поверхностного слоя при деформации, отметим, что это явление приводит к далеко идущим последствиям. Во-первых, большая степень пластической деформации обусловливает в поверхностном слое повышенную плот ность дислокаций, которые при достижении критической плотности стремятся перестроиться с образованием яче истой структуры. В свою очередь наличие в поверхност ном слое развитой ячеистой структуры обусловливает
возможность ее дальнейшего изменения в сторону появ ления устойчивых полос скольжения. Во-вторых, среда испытания заметно влияет на относительно тонкий пла стически деформируемый слой образца [84, 85]. По дан ным Крамера, при одинаковых амплитудах деформации циклическое упрочнение поверхностного слоя меньше в вакууме, чем на воздухе. Усталостная долговечность алюминия и титана сильно зависит от напряжений по верхностного слоя. Увеличение напряжений в нем вызы вает уменьшение усталостной долговечности. Исследуя влияние глубины вакуума до 10-6 мм рт. ст на многоцик ловую усталость технического железа, авторы работы [84] установили, что при улучшении вакуума происхо дит снижение интенсивности следов скольжения на по верхности образцов, их концентрации и соответственно увеличение долговечности образцов.
Влияние температуры испытания на субструктуру и характеристики усталости
Образование развитой субструктуры предполагает поперечное скольжение дислокаций, которое в большой степени зависит от температуры испытания. В поликристаллическом молибдене в условиях консольного изгиба (/= 50 Гц) и числе циклов нагружения N =103-T- 104 об разование ячеек происходит в широком диапазоне темпе ратур: от 200 до 800° С [77]. Средний размер ячеек со ставляет 1,5—5 мкм, а разориентация между ячейками до 3—5 град. Наиболее четкие субграницы возникали при циклическом нагружении в интервале 400—500° С; выше этих температур четкая ячеистая структура обна руживалась не всегда. При данной амплитуде деформа ции образования ячеек вследствие интенсивного разуп рочнения молибдена не происходит.
Ячейки образуются также в рекристаллизованных хроме и вольфраме, испытанных при температурах 400 и 600° С соответственно [77]. Упрочнение, достигаемое при циклическом нагружении молибдена, сравнимо с упроч нением, которое может быть получено при пластической деформации прокаткой на 90%. Предел текучести цик
лически |
нагруженных |
образцов |
составлял ПО— |
120 кгс/мм2 по сравнению |
с 50—60 кгс/мм2 в исходном |
||
состоянии |
[77]. |
|
|
Испытания на усталость поликристаллических об |
|||
разцов меди и рплава Cu-p7,5% А1 |
(Дер= 0,05 и 0,005) в |
интервале 78—300 К показали, что размер ячейки с по вышением температуры и уменьшением амплитуды де формации увеличивается [86]. При этом размер ячейки практически одинаков как для отожженного, так и де формированного (сужение диаметра образца на 5%) со стояний. В аустенитной нержавеющей стали типа AISI 316 при Дер= 0,5ч-2% характер дислокационной струк туры также существенно зависит от температуры испы тания [76]. Наблюдается отчетливый переход от квазподнородного распределения дислокаций при 430° С до ячеистой структуры при 650° С и субзеренной при 816° С. Авторы [76] обнаружили, что размер ячейки dn4 оказы вает влияние как на показатель деформационного упроч нения стали п (рис. 26,а), так и на коэффициент прочно сти К в уравнении Холломона (в условиях статического и циклического видов испытания):
при усталости
ДСу/2 = Kf |
* |
(18) |
при статике |
|
|
ot = Kt*n* |
|
(19) |
При этом значения щ и Kj зависят от размера ячей ки dn4:
п |
d, мкм |
Рис. 26. Изменение показателя деформационного упрочнения |
п |
(а) и раз |
||
мера |
(диаметра) субзерна d (б) при статическом (Л 2) и |
циклическом |
||
(3, 4) |
нагружениях |
сталей AISI 304 и 316 при испытаниях |
на |
усталость |
|
в |
интервале температур 430—816° С [761 |
|
|
(21)
В выражении (21) величина Сг=0,0002 практически одинакова как при статическом, так и при циклическом нагружениях. Из выражения (18) следует, что уровень насыщения определяется размером ячейки или субзерна. Измельчение элементов субструктуры d приводит к рос ту циклической долговечности материала Nf, которая связана с пластической деформацией за цикл Дер степен ной зависимостью Мэнсона — Коффина:
Щ Дер = С, |
(22) |
где С и z — постоянные материала.
В нержавеющей стали типа 316 при повышении тем пературы испытания с 650 до 816° С обнаружено измене ние типа связи между величиной d и амплитудой насы щения о3 [76] (рис. 26, б). Как отмечено выше, при тем пературе испытания 650° С образуются ячейки; в этом
случае as« d _1/2. Однако при 816°С, когда формируется отчетливо выраженная субзеренная структура, наблюда ется зависимость типа as« c H . По-видимому, в интерва ле исследуемых температур происходит смена механиз ма деформации.
УСЛОВИЯ ПОЯВЛЕНИЯ И ОСОБЕННОСТИ СТРОЕНИЯ
УСТОЙЧИВЫХ п о л о с с к о л ь ж е н и я
Еще в начале XX в. Эвинг и Хэмфри, исследуя разру шение шведского железа в условиях усталости, обнару жили, что усталостные трещины образуются в результа те скольжения. Первоначально возникают линии сколь жения, которые с увеличением числа циклов расширяют ся в полосы. Плотность полос скольжения повышается с ростом приложенных напряжений. Полировка и трав ление образцов после усталости, устраняя следы сколь жения, выявляют трещины. Типичные усталостные поло сы скольжения в поликристаллическом ардоко-железе представлены на рис. 27.
В работе [87] введено понятие устойчивых полос скольжения. Испытания на усталость проводили на отожженных образцах чистых меди и никеля в условиях
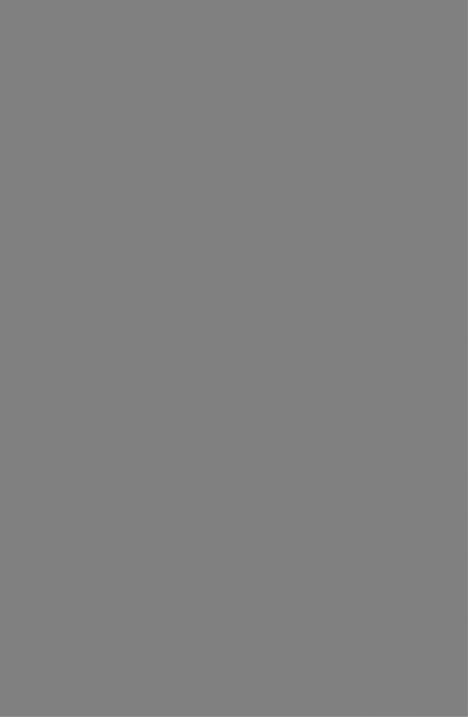
зии достигали ~ 1 0 мкм в высоту и имели ширину от 1 до нескольких десятков микрон, ограничиваясь в ряде случаев размером зерна. Толщина их была менее 0,1 мкм. После электрополировки и травления в образце стано вились видимыми трещины.
Форсайт и Стабингтон [89] установили, что не все материалы показывают наличие экструзий на поверхно сти циклически нагружаемых сплавов. Характерные осо бенности экструзий в значительной степени зависят от режима термической обработки и температуры испыта ния металлов. Например, экструзии образуются в поло сах скольжения при перестаривании алюминиевых спла вов. Концентрация деформации в разупрочненных поло сах вызывает образование в них экструзий. С понижением температуры испытания полосы скольжения стано вятся уже и, как следствие этого, зоны перестаривания также оказываются более узкими. В результате толщи на экструзий соответственно уменьшается и, по мнению авторов работы [89], при пониженных температурах вследствие торможения процесса перестаривания воз можно полное прекращение развития экструзий. Разви тие экструзий при усталости происходит в зонах разуп рочнения материала. Рекристаллизация ряда сильно холоднодеформированных образцов подтверждает идею о разупрочнении металлов при усталости. Однако в целом попытка связать проблему зарождения усталостных тре щин с экструзиями не увенчалась успехом. В ряде слу чаев в металле при усталости развиваются трещины, не связанные с экструзиями, хотя они образуются при тех же условиях нагружения. Эти факты послужили основой для вывода авторов работы [90] о том, что экструзии в большей степени являются следствием, чем причиной ус талости металлов. В дальнейшем при изучении рельефа поверхности металла после усталости нашли также ин трузии (провалы). На рис. 28 схематически приведены основные типы экструзий и интрузий, возникающих в процессе усталости в пределах устойчивых полос сколь жения.
Так же как и при образовании ячеистой структуры, развитие устойчивых полос скольжения происходит при достижении в некоторых зернах определенной плотности дислокаций и интенсивном протекании процессов попе речного скольжения дислокаций. По данным [91], пони жение ЭДУ металлов препятствует формированию раз
витой субструктуры, одновременно задерживая образо вание устойчивых полос скольжения. Эвери и Бэкофен [92, с. 76] показали, что снижение Э.ДУ в монокристал лах сплавов Си—А1 ниже 20 эрг/см2 полностью подавля ет зарождение устойчивых полос скольжения на поверх ности образцов и почти в 10 раз увеличивает число циклов, необходимых для возникновения усталостных тре щин. В поликристаллах влияние ЭДУ менее заметно. Сравнивая монокристаллы меди и сплавов системы Си—Zn с 15 и 31% Zn, авторы работы [93] установили, что интенсивность развития устойчивых полос скольже ния уменьшается с увеличением содержания Zn, т. е. с ростом сопротивления поперечному скольжению дисло каций.
По данным [91], образование устойчивых полос скольжения происходит при условии
Т > т0 + 4 (1 — v/2) тс,
где то— напряжение трения решетки, а тс — критическое
Рис. 28. Схематическое представление основных типов экструзий и ин трузий, образующих устойчивые полосы скольжения (УПС) [112]:
/ — экструзии, |
возникшие |
вдоль отдельных узких участков полосы |
|||||||||||
скольжения; 2 — экструзии |
нерегулярной формы; |
3 — рельеф поверхно |
|||||||||||
сти вблизи |
экструзий; |
4 — микрополосы, на |
поверхности экструзий; |
5 — |
|||||||||
следы скольжения |
на |
экструзиях; |
6 — «усы» |
экструзий; |
7 — двойные |
||||||||
экструзии; |
8 — устойчивые |
полосы |
скольжения |
(УПС); |
9 — экструзии, |
||||||||
когерентные с |
матрицей: |
ниже экструзий |
пор |
не |
обнаружено; |
10 — |
|||||||
интрузии |
вблизи |
экструзий; // — изогнутые |
экструзии; |
/2 — высокая |
|||||||||
плотность |
дислокаций; |
13 — УПС; |
14 — интрузии |
(I |
стадия |
роста |
тре |
||||||
щины); /5 — стрелками указано направление роста |
трещины; 16 — мик |
||||||||||||
рополосы, наблюдаемые на поверхности пор; |
17 — слияние |
нескольких |
|||||||||||
пор; 18 — поры |
различной |
глубины |
в пределах |
УПС; 19 — следы |
гру |
||||||||
|
|
|
|
|
бого скольжения |
|
<■ |
|
|
|
|
напряжение, способное вызвать движение дислокаций в направлении нормальном своей плоскости скольжения. Поскольку т0 включает напряжение Пайерлса — Набарро, то отсюда следует, что усталостная прочность о. ц. к. металлов выше, чем г. ц. к. металлов. Существование критического уровня напряжения, необходимого для за рождения устойчивых полос скольжения, согласуется с данными эксперимента, в частности на монокристаллах меди различной ориентации [91].
Робертс [94] предположил, что уровень критическо го напряжения, если в материале предварительно созда на развитая субструктура, снижается. Другими словами, напряжение, необходимое для зарождения устойчивых полос скольжения, определяется прежде всего условия ми появления развитой субструктуры. Многочисленными экспериментами, например Вудса с сотр. [95, с. 402] и других [75, 96], выполненными на материалах с г. ц. к., г. п.у. и о. ц. к. решетками, установлено, что устойчивым полосам скольжения на поверхности образцов соответст вует специфическая дислокационная структура в объеме материала. Это прежде всего относительно регулярное чередование областей с высокой и низкой плотностью дислокаций (рис. 29). Устойчивые полосы скольжения располагаются в плоскостях скольжения и, как правило, их ориентация совпадает с направлением поперечного скольжения [95*, с. 402, 96]. Одной из особенностей раз
вития устойчивых полос |
скольжения является способ |
|
ность их к образованию |
на поверхности |
материала |
(в пределах устойчивых полос скольжения) |
экструзий и |
|
интрузий [97]. |
|
|
Вранних работах по усталости (см. например, Микин
иПетч [34], с. 218) возникновение подобного рельефа связывали с обязательностью знакопеременного характе ра внешнего нагружения. В модели Коттрелла и Халла
[98]образование экструзий и интрузий ожидается на пе ресекающихся плоскостях скольжения. Перемена пло скости скольжения происходит при перемене знака на гружения. Однако появление интрузий и экструзий на поверхности образца отмечали при усталостных испыта ниях в условиях знакопостоянного нагружения. В част ности, в поликристаллическом отожженном железе нами
* Atkinson J. D., Brown L. М., Kwadio R., Stobbs W. M., Win ter A. T., Woods P. J.
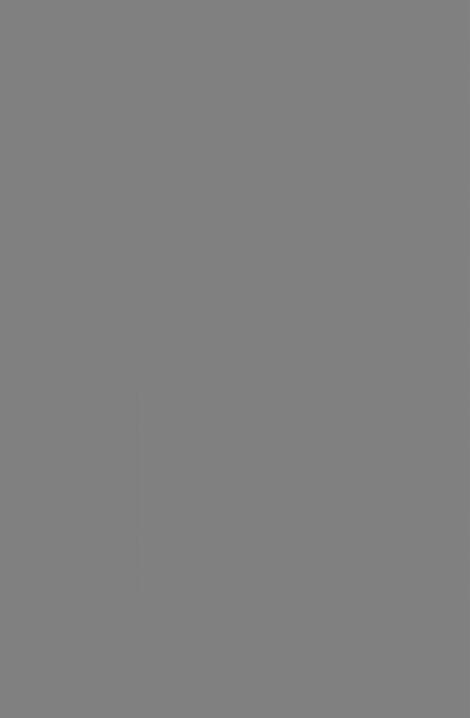