
книги / Отбелка целлюлозы
..pdfвысокого выхода, чем отбелкой мягкой или среднежесткой целлюлозы.
Расход хлора на хлорирование зависит от способа полу-
чения целлюлозы и от содержания в ней лигнина. Обычно на хлорирование сульфитной целлюлозы средней жесткости расходуется 50–75 % (от общего расхода на отбелку) для хвойной целлюлозы и 40–50 % для лиственной целлюлозы.
При хлорировании сульфитной целлюлозы можно удалить 70–80 % лигнина.
Особенности хлорирования сульфатной целлюлозы:
–процесс протекает медленнее, чем при хлорировании сульфитной целлюлозы;
–лигнин сульфатной целлюлозы удаляется труднее, чем сульфитной;
–при хлорировании сульфатной целлюлозы можно удалить лишь 40–50 % лигнина;
–снижение вязкости целлюлозы;
–трудность растворения хлорированного лигнина в кислой среде, т.е. на ступени хлорирования (растворимость хлорированного лигнина сульфатной целлюлозы 40–65 %, сульфитной целлюлозы 85–90 %). Поэтому для удаления его требуется обязательная горячая щелочная обработка целлюлозы после хлорирования;
–при хлорировании сульфатной целлюлозы поглощается меньше хлора, чем при хлорировании сульфитной целлюлозы, т.е. более низкая естественная поглотительная способность целлюлозы к хлору. Поэтому расход хлора на хлорирование сульфатной целлюлозы составляет не более 50 % от общего расхода хлора на отбелку;
–поскольку при хлорировании сульфатной целлюлозы снижается вязкость и ухудшаются механические показатели,
сцелью уменьшения деструкции целлюлозы применяют различные химические добавки (сульфаминовую кислоту – NH2SO3H, ее натриевую соль – NH2SO3Na и др.) в количест-
21
ве 0,1–0,3 % от массы целлюлозы. Эти добавки снижают ОВП системы и тем способствуют уменьшению деградации углеводов.
Оптимальные условия хлорирования: t = 10–20 °С (по-
вышение температуры усиливает гидролиз хлора с образованием HClO и, соответственно, окислительные реакции и разрушение целлюлозы); См = 3–3,5 % (повышение концентрации затрудняет перемешивание и вызывает неравномерное хлори-
рование); рН = 1,5–3,5; τ = 40–60 мин.
2.2. ЩЕЛОЧНАЯ ОБРАБОТКА ЦЕЛЛЮЛОЗЫ ПОСЛЕ ХЛОРИРОВАНИЯ (Щ)
После завершения хлорирования целлюлоза промывается водой для удаления избытка НСl и перешедших в раствор органических продуктов. Как указано выше, хлорлигнин в кислой среде при хлорировании растворяется не полностью, особенно при хлорировании сульфатной целлюлозы (при хлорировании сульфитной целлюлозы растворяется 85–90 % образовавшегося хлорлигнина, а при хлорировании сульфатной целлюлозы – лишь 40–65 %). Для удаления остаточного хлорлигнина необходима щелочная обработка. При этом в раствор переходят также смола и продукты распада (деструкции) углеводной части, что вызывает понижение медного числа, повышение вязкости и содержания альфа-целлюлозы.
Расход NaOH составляет 1–1,5 % для сульфитной целлюлозы и 2–3 % для сульфатной целлюлозы. Для перевода в раствор остаточного хлорлигнина требуется незначительное количество щелочи (0,3–0,6 % для сульфитной целлюлозы и 0,6–1,2 % для сульфатной целлюлозы). Повышенный расход щелочи в производственных условиях обусловлен неполной отмывкой соляной кислоты от целлюлозы.
22

При щелочной обработке сульфитной целлюлозы повышение температуры необязательно, так как содержание хлорлигнина невелико. Щелочную обработку сульфатной целлюлозы проводят при температуре 60–70 °С, так как хлорлигнин
вэтом случае растворяется с трудом даже в щелочной среде. В обоих случаях скорость растворения хлорлигнина увеличивается с повышением температуры.
Щелочерастворимая часть хлорлигнина представляет собой высокомолекулярную фракцию. Эта же часть лигнина обладает хромофорными (окрашивающими) свойствами. Поэтому после щелочной обработки и промывки цвет целлюлозы делается светлее.
Концентрация массы при щелочной обработке 10–14 %. Такая высокая концентрация особенно важна при обработке сульфатной целлюлозы с целью сокращения расхода пара на подогрев массы.
Механизм перехода хлорированного лигнина в щелочной раствор выяснен недостаточно. Считается, что имеют место как коллоидное растворение, так и химические реакции. Основной реакцией считают гидролиз атомов хлора в шестом положении
вбензольных кольцах с образованием гидроксильных групп, нейтрализуемых щелочью.
При щелочной обработке целлюлозы присутствие окислительных реагентов благоприятно влияет на конечную белизну целлюлозы и позволяет лучше сохранить вязкость и механическую прочность целлюлозы, что особенно важно при отбелке сульфатной целлюлозы. Поэтому в последние годы широкое распространение получило окислительное щелочение в присутствии кислорода (ЩО2). Щелочную обработку в этом
23
случае ведут при 60–70 °С, концентрации массы ~10 % и расходе кислорода ~0,5 % к массе волокна, рН = 10–11; расход щелочи такой же, как и при обычном щелочении (для сульфатной целлюлозы 20–25 кг/т). Такое щелочение может проводиться как под давлением, так и при атмосферном давлении. В первом случае давление кислорода в начальный момент от 0,1 до 0,3 МПа, продолжительность контакта массы с кислородом под давлением от 10 до 60 мин.
В промышленности применяют также добавки к щелочи других окислителей – пероксида водорода и гипохлорита. Добавки эти, кроме указанных выше преимуществ, способствуют более глубокой делигнификации целлюлозы и некоторому снижению токсичности сточных вод (БПК и ХПК). Очевидно, окислители участвуют в процессе разрушения лигнина и обесцвечивания его хромофорных групп.
Щелочную обработку лиственных сульфитных и сульфатных целлюлоз следует проводить в более жестких условиях, что связано со «смоляными затруднениями», возникающими при получении лиственных целлюлоз. В этих случаях желательна щелочная обработка с добавками окислителей или поверхностно-активных веществ (Na3PO4, ОП-7, ОП-10 и др.) с целью уменьшения смолистости целлюлозы.
Отработанный щелок после щелочной обработки, как и после хлорирования, имеет темно-коричневый цвет. Целлюлоза после хлорирования, щелочной обработки и промывки имеет серовато-желтоватый оттенок, т.е. низкую степень белизны.
2.3. КИСЛОРОДНО-ЩЕЛОЧНАЯ ОТБЕЛКА (КЩО)
Способ разработан советскими учеными В.М. Никитиным и Г.Л. Акимом в 1956 г., далее усовершенствован зарубежными учеными. В промышленности отбелка производится с 1970 г. и к настоящему времени эксплуатируется несколько
24
десятков установок. КЩО применяется как часть общего процесса отбелки, заменяющая хлорирование и щелочную обработку, т.е. для делигнификации целлюлозы.
Преимущества этого способа перед хлорно-щелочной делигнификацией:
–отработанный щелок после КЩО не содержит вредных соединений хлора и хлорлигнина, что значительно снижает расходы на очистку сточных вод;
–легкое удаление смолы из целлюлозы, т.е. исключение проблемы смоляных загрязнений;
–белизна целлюлозы после КЩО не понижается как при хлорно-щелочной делигнификации, а повышается (до 50–60 % для сульфатной целлюлозы).
Недостатки способа:
–низкая селективность кислорода как отбеливающего реагента, следствием чего является деструкция целлюлозы;
–необходимость проведения процесса под давлением;
–более сложное аппаратурное оформление, чем при традиционной отбелке, что требует больших капитальных затрат.
Делигнификация во время КЩО является результатом совместного действия на остаточный лигнин кислорода и щелочи. Вследствие плохой растворимости кислорода в горячей щелочи (температуpa процесса 90–140 °С), обработку приходится проводить при повышенном давлении (от 0,3 до 1 МПа)
вспециальных реакторах.
Считается, что в щелочном водном растворе окислителем является не кислород, окислительный потенциал которого невысок, а возникающие по цепному механизму органические радикалы и пероксиды. Молекула кислорода О2 в щелочной среде легко превращается в бирадикал •О–О•, который может реагировать с фенилпропановыми единицами лигнина с образованием феноксильных радикалов.
25
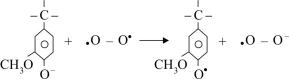
Образование феноксильных радикалов является 1-й стадией окисления лигнина кислородом, которая дает начало ряду цепных превращений, в ходе которых возникают органические пероксидные ионы типа НОО– и RОО–, обладающие мягким окислительным действием, и оксидные и пероксидные радикалы типа RО• и RОО•, обладающие высокой окислительной активностью. Пероксидные группы разрушают хромофорные группировки лигнина, что способствует повышению степени белизны целлюлозы. Разрушение лигнина и переход его в раствор при КЩО происходит под действием горячей щелочи, как и при сульфатной варке. Лигнин переходит в раствор главным образом в виде низкомолекулярных фрагментов вплоть до мономеров, содержащих карбонильные и карбоксильные группы, и в виде молекулярных продуктов его разрушения ароматических
иалифатических карбоновых кислот вплоть до щавелевой
имуравьиной. Пероксидные радикалы оказывают деструктирующее действие не только на лигнин, но и на гемицеллюлозы и целлюлозу.
Предполагается, что окисление целлюлозы в щелочной среде происходит через образование активных центров, способных взаимодействовать с бирадикалами кислорода.
Схемы превращений углеводов при КЩО: таутомерные превращения с образованием альфа-
дикетона
26
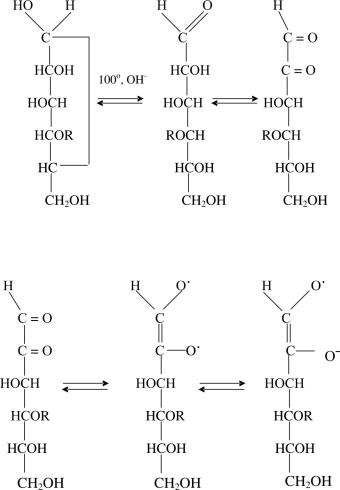
образование свободных радикалов
Кислородно-щелочная отбелка, по сравнению с хлор- но-щелочной делигнификацией, обладает значительно худшей избирательностью (т.е. заметно разрушает целлюлозу). В этом основной недостаток способа. Во избежание значительных потерь углеводов делигнификацию сульфатной целлюлозы при кислородно-щелочной отбелке проводят
27
только наполовину (50–60 %), и оставшийся лигнин удаляют хлорно-щелочной обработкой или диоксидом хлора.
Для уменьшения деструкции целлюлозы при кислород- но-щелочной отбелке добавляют стабилизаторы (ингибиторы). Наилучшим ингибитором щелочной деструкции целлюлозы оказались соли магния – MgCO3, MgSO4, MgSiO3 и в особенности комплексные магниевые соли. Расход ионов магния всего от 0,05 до 0,4 % от массы абсолютно сухой целлюлозы. Ингибирующее действие оказывает также смесь солей магния с триэтаноламином.
Технологические факторы кислородно-щелочной отбелки.
Концентрация массы. В настоящее время в технике ки- слородно-щелочной отбелки сложились две тенденции: отбелка при высокой концентрации (25–30 %) и при средней концентрации (10–12 %). Второй вариант дает возможность осуществить в отбельном цехе очень удобную технологию средней концентрации (МС-medium consistency).
Высокая концентрация позволяет снизить расход щелочи и пара, но требует мощных обезвоживающих устройств и более дорогого оборудования; средняя упрощает работу, но увеличивает количество стоков.
При равном расходе щелочи высокая концентрация массы означает высокую концентрацию щелочи в растворе, а это,
всвою очередь, ускоряет делигнификацию, т.е. сокращает продолжительность процесса, но усиливает деструкцию целлюлозы (снижает вязкость и механические показатели). Однако отбелка при высокой концентрации массы применяется на большинстве установок еще с 1970-х годов. При такой отбелке
вмассу, кроме раствора NaOH, необходимo вводить значительное количество газообразного кислорода. Поэтому процесс проводится в газовой фазе, и масса в реакторе представляет
28
собой распушенную на мелкие кусочки влажную целлюлозу, окруженную газом.
Температура процесса от 90 до 140 °С. Повышение температуры до 130–140 °С ускоряет делигнификацию, но уменьшает растворимость кислорода и требует повышения давления кислорода до 0,8–1,0 МПа и более, а также снижает выход целлюлозы.
Расход NaOH на практике колеблется от 2 до 6 % (от волокна) в зависимости от содержания лигнина в целлюлозе. На 1 % остаточного лигнина для делигнификации необходимо расходовать всего 0,5–0,6 % NaOH. Избыток щелочи нужен для нейтрализации кислых продуктов деградации углеводов.
Расход кислорода также зависит от содержания лигнина в целлюлозе и колеблется от 1,5 до 3 % от массы целлюлозы. Увеличение расхода кислорода улучшает белизну целлюлозы после кислородно-щелочной отбелки, но требует повышения давления в реакторе.
Продолжительность – 30–90 мин, на практике около часа. Увеличение ее не усиливает делигнификацию и не улучшает белизну, а лишь усиливает деструкцию целлюлозы.
Таким образом, условия кислородно-щелочной отбелки при высокой концентрации массы (25–30 %): 90–140 °С; 1 час; расход NаОH 2–6 %, концентрация NaOH в растворе 1–2 %; расход кислорода 1,5–3 % от массы целлюлозы; давление кислорода 0,8–1,0 МПа; добавка Мg2+ 0,05–0,4 % от массы волокна.
При получении целлюлозы для химической переработки отбелку проводят при 130–140 °С, целлюлозы для бумаги – при
90–100 °С.
Установки, работающие под давлением, используются при необходимости понижения числа Каппа примерно на 50 %. Для снижения числа Каппа на 30–35 % достаточна установка КЩО, работающая без давления (разработка фирмы Раума – Репола).
29

Кислородная ступень без давления с продленной варкой обеспечивает достижение того же числа Каппа, что и нормальная варка с КЩО под давлением.
Потери волокна при отбелке зависят от содержания лигнина в исходной целлюлозе. Так, при содержании 5 % лигнина потери волокна составляют ~ 1 %.
На рис. 1 приведены варианты схем КЩО, а в табл. 1 – режимы основных видов КЩО.
Таблица 1
Типовые технологические режимы основных видов кислородно-щелочной обработки целлюлозы
|
Видкислородно-щелочнойобработки |
Щело- |
||||
Параметр |
|
|
облаго- |
двухступенчатая |
чение |
|
делигни- |
отбелка |
ражива- |
обработка |
скисло- |
||
|
фикация |
|
ние |
1-я |
2-я |
родом |
|
|
|
|
ступень |
ступень |
|
Концентрация |
|
|
|
|
|
|
массы, % |
8–12 |
8–12 |
8–12 |
8–12 |
8–12 |
8–12 |
Расходщелочи*, |
|
|
|
|
|
|
кгNaOH/т |
25–40 |
20–30 |
70–90 |
20–30 |
0–10 |
10–20 |
Расходкислорода, |
|
|
|
|
|
|
кг/т |
25–35 |
15–25 |
20–25 |
15–25 |
0–10 |
3–10 |
Избыточноедавле- |
|
|
|
|
|
|
ниекислорода, МПа |
0,5–1,0 |
0,5–1,0 |
0,4–0,6 |
0,7–1,0 |
0,3–0,5 |
0–0,5 |
Температура, оС |
110–120 |
100–115 |
95–100 |
80–85 |
95–105 |
60–80 |
Продолжителность |
|
|
|
|
|
|
обработкищелочью |
|
|
|
|
|
|
доконтактаски- |
|
|
|
|
|
|
слородом, мин |
– |
– |
40–50 |
– |
– |
– |
Продолжительность |
|
|
|
|
|
|
обработкикислоро- |
|
|
|
|
|
|
дом, мин |
60–120 |
40–90 |
90–120 |
20–30 |
60–70 |
5–30 |
* В качестве щелочи при кислородно-щелочной обработке кроме едкого натрия могут применяться окисленный белый щелок, карбонат натрия, гидроксиды магния и кальция и другие щелочные реагенты.
30