
книги / Technologie des Kali - und Steinsalzbergbaus
..pdf14.Was versteht man unter Kanonenund unter Schlitzeinbruchsverfahren? Zeich nen Sie einige charakteristische Bohrschemata der Streckenauffahrung! Nennen Sie die Namen von verdienten Hauern der Kaliindustrie, deren Vortriebsmethoden allgemein eingeführt worden sind!
15.In welcher Höhe liegen die durchschnittlichen Sprengstoffverbrauch bei 5 m breiten Strecken/m Vortrieb?
16.Nach welchem Prinzip arbeiten unsere Streckenvortriebsmaschinen?
17.Nennen Sie die Hauptteile und die Einsatzbedingungen der V 3Ö01!
18.Erarbeiten Sie einen Zeitplan und einen Belegungsplan für eine V 3001, die in 6 Monaten 1200 m Erkundungsstrecke auffahren soll! Berücksichtigen Sie vor beugende Reparaturen! Stellen Sie zur besseren Übersicht eine graphische Dar stellung auf!
19.Welche Möglichkeiten der Abförderung des geschnittenen Salzes hinter Vortriebs maschinen gibt es ?
20.Berichten Sie von den Hindernissen, die einer vollmechanischen, maschinellen Gewinnung im Abbaubetrieb der Kaligruben noch im Wege stehen!
21.Welche maschinellen Gewinnungsmethoden würden Sie in der Ihnen bekannten Kaligrube anwenden? Begründen Sie Ihren Vorschlag!
22.Eine Säulendrehbohrmaschine DIN A 1, Ausführung a, erreicht einen Vorschub von 1360 mm/min.
Wie lange dauert es, bis ein Bohrloch von 4 m, 4,80 m und 6,25 m Länge herge stellt ist, wenn für Anhacken und Bohrgestängeaufsetzen je 12 % Zeitbedarf hin zugerechnet werden?
23.Eine Bohrschneide erreicht im Durchschnitt eine Lebensdauer von 1500 Bohr metern.
Wieviel Schneiden sind für 22000 Bohrmeter erforderlich?
24.1 m Zündschnur brennt 2 min.
Wie lange brennen Zündschnurstücken, die 4,50 m, 2,00 m und 3,70 m lang sind?
25.Der spezifische Sprengstoffverbrauch einer Steinsalzgrube beträgt 405 g/t eff. Wie hoch ist der Gesamtverbrauch im Monat bei 90000 t monatlicher Förderung?
26.Von einer Förderstrecke aus ist ein 70 m langer Querschlag zu einer Wetterstrecke herzustellen.
Wie lange dauert diese Auffahrung im zweischichtigen Betrieb, wenn in jeder Schicht 1,75 m Vortrieb erreicht werden?
27.Die gewinnbare Bauhöhe des Kalilagers ist mit entscheidend für die Wirtschaftlichkeit der Grube.
Errechnen Sie den Salzanfall pro Abbau beim Kammerbau mit folgenden Ab messungen (Dichte 2,2):
a)10 m Abbaubreite, 200 m Abbaulänge, 3 m bauwürdige Höhe,
b)8 m Abbaubreite, 230 m Abbaulänge, 7 m bauwürdige Höhe.
Täglich werden aus dem Abbau b 3801 Salz abgefördert. Welche Lebensdauer er reicht diese Abbaukammer?
28.Durch Einführung eines VerbesserungsVorschlages werden bei der Gewinnung pro t Salz 7 g Sprengstoff eingespart.
Welche Ersparnis ergibt sich bei einer Monatsförderung von 23049 t, wenn 1 kg Sprengstoff 1,23 DM kostet?
7. Die Abbauförderung
Früher war in der Abförderung die Handarbeit noch weit verbreitet. Heute ist im Kalibergbau nur noch in Sonderfällen Schaufelarbeit notwendig.
7.1.Ladegeräte und ihr möglicher Einsatz bei den verschiedenen Abbauverfahren
Reine Ladegeräte haben sich in Salzgruben trotz verstärkter Mechanisierungsbestre bungen bisher kaum durchsetzen können. Die ideale Fördermethode im Abbau kann nur mit einem Gerät erreicht werden, das den eigentlichen Ladevorgang und den nachfolgenden Abfördervorgang kombiniert.
Die Ladegeräte sind aber auch in den Kaligruben der DDR unter verschiedenen Ein satzbedingungen erprobt worden und sollen deshalb unter Erläuterung ihrer Vorund Nachteile kurz beschrieben werden.
In die Gruppe der Schaufellader gehört der Überkopflader, der besonders im Streckenvor trieb Verwendung findet. Eine als Schaufel ausgebildete Gefäßform wird in das Hauf werk hineingefahren und bewegt sich auf einer Kurvenbahn über das Gerät hinweg. Die Entleerung erfolgt in die hinter dem Lader stehenden Förderwagen (Bild 7/1).
In Tabelle 6 sind die hauptsächlichsten technischen Kenngrößen der bei uns im Ein satz befindlichen Überkopflader angegeben. Aus diesen Daten kann man auch einige Nachteile des Gerätes ableiten.
Die Überkopflader waren zunächst bevorzugt in der Steinkohle und im Erzbergbau im Einsatz. Sie wurden dort mit Preßluft betrieben. Die Umstellung auf den im Kaliberg bau üblichen elektrischen Antrieb bereitete Schwierigkeiten, da in vielen Südharz gruben schlagwettergeschützte elektrische Einrichtungen gefordert werden mußten.
So vorteilhaft Überkopf lader im Streckenvor trieb bei guter Arbeits organisation sein kön nen, so wenig wirtschaft lich hat sich ihr Einsatz bisher im Abbau gezeigt. Hauptnachteil ist die Notwendigkeit der Mit führung einer Gleisan lage für den Abtransport des Salzes in Förderwa gen. Im Streckenvor trieb kann dieser Nach teil in Kauf genommen
Bild 7/1. Scliomatlsclio Dar stellung eines Üborkopfladors
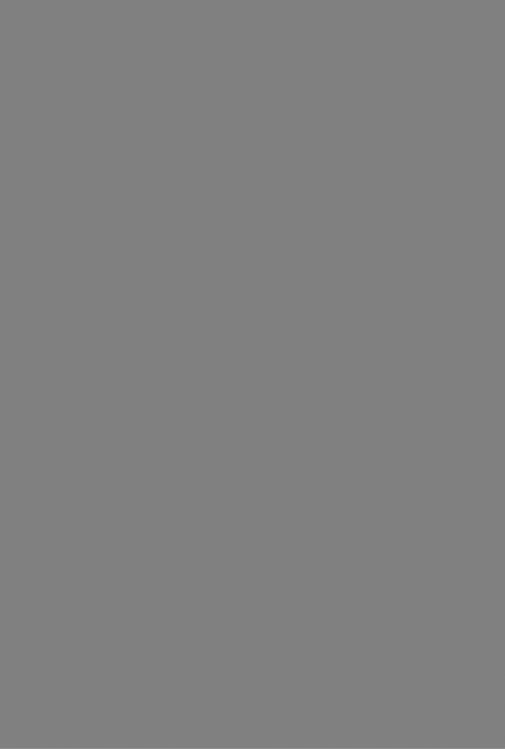
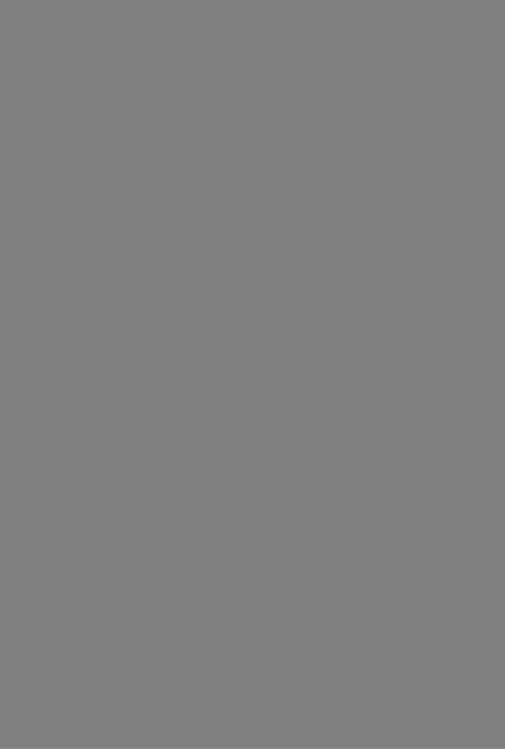
Haufwerk fällt unter Ausnutzung der halbsteilen Lagerung von allein in den Vorratsbunker jeder Abbaufirste.
7.2.Fördermittel im Abbau
Wie bei den reinen Ladegeräten gibt es auch bei den Fördermitteln Aggregate, die nur einem Arbeitsprozeß dienen. Zu diesen reinen Fördermitteln, die im Abbau bisher er probt wurden, gehören Schüttelrutschen, Bänder, Kratzoder Panzerförderer, För derwagen und Bunkerpendelwagen.
Die Schüttelrutsche ist in früheren Jahren in mehreren Kaliund Steinsalzgruben als Fördermittel im Abbau und vor allem in der Zwischenförderung als Zuführung zu Großrollöchern benutzt worden. Heute ist ihr Einsatz auf Sonderfälle beschränkt. Auch in Zukunft wird die Schüttelrutsche weder im Abbau noch im Streckenvortrieb kaum wieder an Bedeutung gewinnen.
Die Rutsche besteht aus mehreren ineinandergcsteckten Blechen, die Gesamtlängen bis zu 200 m erreichen können. Die Breite der Rutschenbleche liegt zwischen 400 und 1100 mm (die großen Breiten sind Sonderanfertigungen). Der Rutschenstrang ist auf Rollen in der Sohle verlagert oder an Ketten frei aufgehängt. Das Fördergut erhält seine Bewegung durch ruckartigen Betrieb, d.h., der Hingang der Rutsche in Förder richtung erfolgt langsam, und der plötzlich einsetzende ruckartige Rückzug der Rut sche läßt das Haufwerk in Förderrichtung nach vorn gleiten. Bei dem letztgenannten Bewegungsvorgang muß die Reibung des Fördergutes auf dem Rutschenblech über wunden werden. Im Salzbergbau ist der Reibungskoeffizient maßgeblich von der jeweiligen Beschaffenheit des Salzes abhängig. Feuchter Carnallit z. B. rutscht nicht. Für zu flaches Einfallen eignet sich die Schüttelrutsche wenig, da der ungleichförmige Bewegungsablauf nur bei Einhaltung eines Mindesteinfallwinkels voll wirksam werden kann.
Die Benutzung von Förderbändern wird sich im Abbau ebenfalls auf Ausnahmen be schränken. Dagegen werden Gummitransportbänder in den kommenden Jahren in der Hauptstreckenförderung unserer Kaliund Steinsalzgruben zum beherrschenden Fördermittel werden. Eine eingehende Beschreibung dieses Fördermittels erfolgt des halb im Abschnitt „Streckenförderung“ .
Transportbänder aus anderem Material, wie z. B. Stahlgliederbänder, sind als A b fördermittel kaum einsatzfähig und in unseren Gruben auch in Zukunft nicht zu er warten.
Die für den Steinkohlenbergbau entwickelten Kratzförderer sind auch in Kaligruben mit Erfolg erprobt worden. Sie können im Abbau eingesetzt werden, sollen aber bei der Projektierung zukünftiger Grubenausrüstungen bevorzugt als Zwischenförder mittel anstelle der jetzt noch weit verbreiteten Sammelschrapper Verwendung finden. Die Kratzförderer sind wegen ihrer robusten Bauart für den rauhen Grubenbetrieb geeignet. Im Gegensatz zu Gummitransportbändern können auf ihnen größere Salz brocken ohne weiteres befördert werden.
Die Hauptteile eines Kratzförderers sind in Bild 7/5 dargestellt. Auf einer aus ineinandergesteckten Stahlblechrinnen bestehenden Unterlage wird das Fördergut von quergestellten Stegen bewegt. Die Stege sind seitlich an zwei endlosen Ketten be festigt, die auf der Rinne entlang gezogen werden. Kratzförderer können bei guter Arbeitsorganisation hohe Leistungen erreichen. Bei entsprechender Betriebskonzen tration, die eine volle Auslastung der für die Abförderung eingesetzten Gerätetypen ermöglicht, kann ein Kratzförderer 200 bis 250 t/h Rohsalz transportieren. Dazu ist
2 |
3 |
4 |
**1500
Bild 7/6. Bunkcrpcndelvrngon lm Grundriß und Aufriß
(1) Kratzbandantrieb, (2) Fahrantrieb, (3) Kabeltrommel, (4) Kratzband, (5) Gleich |
5 |
6 |
stromgenerator, (6) Motor |
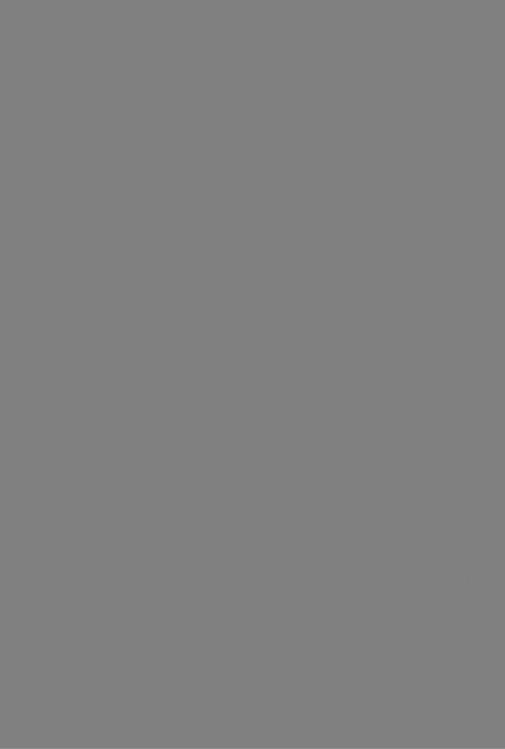
Der Pendelwagen ist als Großraumwagen ausgebildet und kann 6 bis 14 t Rohsalz aufnehmen; es sind je nach den LagerVerhältnissen Typen verschiedener Größe ent wickelt worden. Die Wagen werden einzeln durch Dieselmotor angetrieben oder sind mit einem Elektromotor ausgerüstet, wobei die Stromzuführung durch ein bis zu 250 m langes Schleppkabel erfolgt. Die Wagen arbeiten als Selbstentlader. Der Bo den besteht aus einem Stahlgliederband, das den Wageninhalt nach hinten entleert.
Die Hauptteile und die Hauptabmessungen des Bunkerpendelwagens sind aus den Bildern 7/6 bis 7/8 zu entnehmen. Die wichtigsten technischen Daten:
Fahrzeuglänge |
etwa 7,30 m |
|
|
Fahrzeugbreite |
etwa 2,30 m |
|
|
Fahrzeughöhe |
1,70 m |
|
|
Bunkerbreite |
1,00 m |
|
|
Fassungsvermögen |
etwa 8 m3 |
|
|
Nutzlast |
14 t |
|
|
Eigenmasse |
etwa 161 |
|
|
Energiequelle |
Gleichstromnetz und |
Zuführungskabel 3X |
|
|
25 mm2, etwa 250 m |
lang, oder Dieselmotor |
|
Fahrantrieb |
120 PS mit Gleichstromgenerator |
||
2 X |
18 kW |
|
|
Antrieb Stahlgliederband |
12,5 |
kW |
|
7.3.Kombination von Ladeund Fördermitteln, ökonomischer Einsatz der Geräte
S te in k o h le n b e rg b a u (S tre b b a u )
S a lz b e r g b a u (kam m erbau)
G ew in n u ng |
A bbauförderung |
|
(Bohren und Schießen) |
||
|
||
1i |
|
|
z. T.Zwischenförderung \i |
H auptstrecken - |
|
mit Vorzerkleinerung j1 |
fö rd e ru n g |
|
1 |
|
|
_________________________________________11 |
|
Der Einsatz einzelner Gerätetypen allein wird in der Praxis kaum mehr Vorkommen. Ge rade im Salzbergbau muß im Interesse eines wirtschaftlichen Be triebsablaufs eine sinn volle Kombination von Ladeund Förderarbeit im Abbau gefunden werden. Solange die Gewinnung noch mit Bohrund Schießarbeit betrieben wird, kann der Arbeitsabschnitt „Gewinnung“ nur zum Teil in diese Kombina tion mit einbezogen werden. Es ist Haupt-
ßlld 7/0
Arbeltsabschnltte im Stein kohlenund Salzbergbau
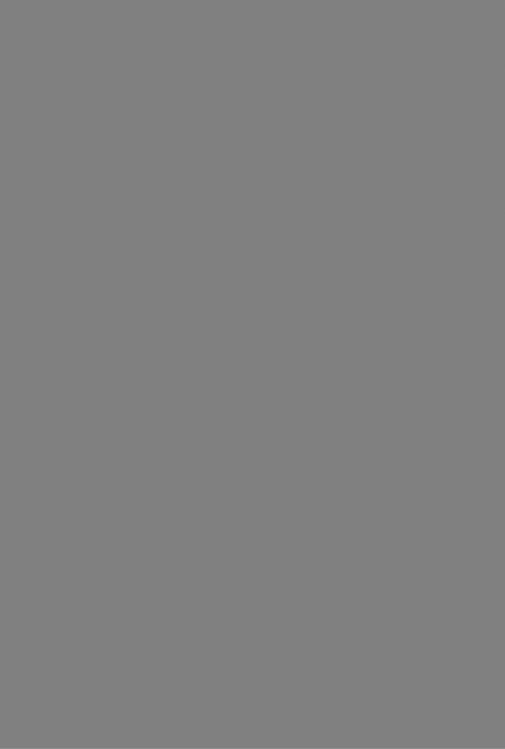
|
|
|
S 10001) |
S 63002) |
S 25003) |
S 40004) |
Zugkraft |
P |
Lkp] |
900 |
6300 |
2500 |
4000 |
mittlere Seilgeschwin- |
|
|
|
|
|
|
digkeit |
|
[m/s] |
1,25 |
1,75 |
1,6 |
1,8 |
Seilaufnahme |
|
[m] |
50 |
250 |
150 |
250 |
Motorleistung |
N |
[kW] |
14 |
125 |
42 |
72 |
Motordrehzahl |
n |
[U/min] |
1000 |
750 |
1000 |
1000 |
Masse ohne Motor |
|
[kg] |
650 |
7600 |
2800 |
3800 |
größte |
|
|
|
|
|
|
Abmessungen |
|
[mm] |
1620 x 720 |
2380 X 950 |
2300 x 1235 |
2300 X 1295 |
|
|
|
X 700 |
X 960 |
X 1300 |
X 1220 |
*) Klcinhaspel mit Zahnradvorgelege
:) Große Sonderausführung mit Zahnradvorgelege
3)Streckenschrapper mit Keilriemenantricb
4)Kali 4, verbreitetster Typ mit Flachricmcnantrieb; wird in Zukunft nur noch mit Direktantrieb geliefert
Die andere Trommel sitzt lose auf der Welle und läßt das Seil ablaufen. Das ablau fende Seil muß ständig straff gehalten werden, was durch eine besondere, gewichts belastete Nachlaufbremse erreicht wird. Der wichtigste Teil des Haspels sind die Kupplungen, die den Lauf der beiden Trommeln in gegenläufiger Richtung ermög lichen. Von der früher entwickelten Außenbandkupplung ist man abgekommen. Die heute generell benutzte Kupplung ist das Planetengetriebe (Bild 7/12). Das soge nannte Sonnenrad S sitzt fest auf der ständig umlaufenden Antriebswelle und ist mit den beiden Planetenrädern P verzahnt. Diese sitzen mit Achsstummeln auf der Trommel und greifen mit ihren Zähnen in das lose auf der Welle sitzende innenver zahnte Hohlrad J. Auf diesem Hohlrad liegt außen ein Bremsband B auf. Wenn das Bremsband gelöst ist, drehen sich die Planetenräder auf der Welle und nehmen das Hohlrad in der gleichen Drehrichtung mit. Wird die Bremse angezogen und dadurch das Hohlrad festgehalten, so wälzen sich die Planetenräder auf dem Hohlrad ab und erzeugen dabei die Drehung der Trommel. Da jede Trommel innen ihr eigenes Pla netengetriebe besitzt, ist die Bedienung des Haspels einfach. Sie besteht lediglich im Lösen oder Anziehen des jeweils notwendigen Bremsbandes.
Der Schrapperhaspel mit seinem Antriebsmotor ist der wichtigste, zugleich aber auch teuerste Teil einer Schrapperanlage. Die Antriebsmotoren hatten früher Leistungen zwischen 30 und 50 kW, waren dann lange Zeit auf 70 kW standardisiert und errei chen heute bei großen Anlagen 125 kW. Dementsprechend sind auch die Schrapper kästen größer geworden und damit die möglichen Abförderleistungen im Abbau ge wachsen. Die zwangsläufig mit der Schrapperförderung verbundene Salzstaubent-
Dlld 7/12. Skizze des Plnnctcngctriebes(nnch Spnckclcr)
(5) Sonnenrad, (P)Planctenriidcr, («/) innenverzahnte Trommel.
( B) Bremsband, (F) Trommel für Vollseil, ( Z f ) Trommel für Leerseil, ( N) Nnchlaufbremscn