
книги / Technologie des Kali - und Steinsalzbergbaus
..pdfden. Die unter Punkt 8, 9 und 10 genannten Faktoren sind zum wesentlichen Teil durch die geologischen Verhältnisse bedingt. Das gilt auch für die Wahl des Spreng stoffes (Punkt 19), sie ist abhängig von Härte, Druckfestigkeit und Zähigkeit des Salzgebirges. Es wäre falsch, anzunehmen, daß in Nachbargruben gleiche geologische und abbautechnische Verhältnisse vorliegen und deshalb die Bohrund Schießarbeit in gleicher Weise durchgeführt werden kann. Aber gerade bei der Beurteilung der Arbeitsorganisation in der Gewinnung macht sich die immer etwas konservative Hal tung der Bergleute besonders bemerkbar. Es ist oft schwierig, erfahrene Hauer von alten Bohrschemata abzubringen und sie für neue Arbeitsmethoden zu gewinnen.
Was die beeinflußbaren Faktoren betrifft, so ist die tatsächliche Leistungsfähigkeit im Bolii*- und Schießbetrieb besonders von einem kontinuierlichen Ineinandergreifen der einzelnen Arbeitsvorgänge abhängig. Dabei muß vor allem angestrebt werden, daß eine Ortsbelcgung auch tatsächlich als ein eingespieltes Kollektiv arbeiten kann. Häufiger personeller Wechsel in den Ortsbelegungen führt zu Leistungsrückgängen.
Die Ermittlung der reinen Bohrzeit vor Ort und des Zeitaufwandes für alle anderen Arbeiten wird durch Zeitmessungen erreicht, die von Steigern, in den meisten Fällen aber von den Abteilungsnormierern durchgeführt werden.
Bei diesen Zeitmessungen kommt es darauf an, die wirklichen Einflußfaktoren für die Leistung der Bohrund Schießarbeit vor Ort in ihrer richtigen Höhe zu erfassen und zu beurteilen. Ein zuverlässiger Mittelwert kann dabei nur aus einer Vielzahl von Zeit messungen gewonnen werden. Es ist durchaus möglich, daß sich durch besondere Umstände bei einzelnen Zeitmessungen Extremwerte ergeben, die das wirkliche Leistungsbild des Gewinnungsbetriebspunktes verzerren. Die Arbeit der Normierer ist deshalb verantwortungsreich. Sie sollte nur in enger kollektiver Zusammenarbeit mit der Grubenbetriebsleitung und dem Hauerkollektiv bzw. den einzelnen Brigadeleitern erfolgen. Das Ergebnis der Zeitmessungen muß in der Ermittlung wirklicher Grund lagen für die Berechnung von Normen liegen, die als wissenschaftlich ermittelte tat sächliche Leistungsnormen ein Spiegelbild für die Arbeitsorganisation und Leistungs fähigkeit der Bohrund Schießarbeit darstellen.
Hierzu gehört auch die Ehrlichkeit der Hauer, die u. a. in der richtigen Einschätzung neuer Gezähe, z. B. der Schnellfrequenzbohrmaschine, zu suchen ist und die sich daraus ergebende notwendige Veränderung einer bestehenden, nicht mehr realen Norm.
6.I.4.I. Leistungen uml Kosten beim Bohren und Schießen
Einige Zahlen sollen beweisen, daß der Kostenanteil im Arbeitsabschnitt „Gewin nung“ eines Grubenbetriebes im Kalibergbau das Gesamtbild der Wirtschaftlichkeit einer Grube Wesentlich beeinflußt.
Im Jahre 1961 wurden in den Kaliund Steinsalzgruben der DDR bei der Gewinnung mit Bohrund Schießarbeit insgesamt etwa 8513000 kg Sprengstoff verschossen. Im Durchschnitt aller Kaliwerke war für jede Tonne geförderten Kalirohsalzes ein Spreng stoffverbrauch von 460 g erforderlich.
Die Gesamtkosten in der Gewinnung beliefen sich auf über 25 Mill. DM und ergaben umgerechnet einen spezifischen Anteil des Arbeitsabschnitts „Gewinnung“ von. 1,75 DM/t Rohsalz.
An Bohrschneiden wurden im Gesamtdurchschnitt der Kaligruben 2,18 Stück für je 10001 Förderung verbraucht. Dabei lag die Grube Roßleben mit 5,09 Stück für 1000 t wegen der dort eingelagerten sehr harten Polyhalitund Langbeinitbänke weit über dem Gesamtdurchschnitt. In den Gruben, in denen Steinsalz bergmännisch mit
sa
Bohrund Schießarbeit gewonnen wird, waren 1961 nur 0,94 Stück für je 1000 t er forderlich. Das ist ein Beweis für die geringere Härte des Steinsalzes gegenüber den Hartsalzlagem.
Schon aus diesen Zahlen ergibt sich, daß die verstärkte Einführung des möglichst vollmechanischen Gewinnungsbetriebes mit der damit verbundenen starken Vermin derung der Bohrund Schießarbeit nicht nur vom technischen, sondern vor allem auch vom ökonomischen Standpunkt aus im Rahmen der Perspektive der Kaliund Steinsalzindustrie der DD R angestrebt werden muß.
6.1.5.Ausbildung des Hauers für den Umgang mit Sprengstoffen und Zündmitteln
Der noch immer bestehende große Verbrauch an Sprengstoffen in der Kaliund Stein salzindustrie zwingt dazu, alle Bergleute, die unter Tage mit Sprengstoffen umgehen müssen, sorgfältig darauf vorzubereiten. Damit muß schon während der Berufsaus bildung begonnen werden. Das Hauptaugenmerk ist dabei auf die richtige Einschät zung der Gefahren zu legen, die eine falsche Handhabung von Sprengstoffen und Zündmitteln mit sich bringen kann. Ein erheblicher Teil der noch auftretenden Un fälle in unseren Grubenbetrieben ist auf Leichtsinn und Unvernunft beim Umgang mit Sprengstoffen zurückzuführen. Leider werden von solchen Unfällen sehr oft ge rade erfahrene Hauer betroffen, die in dem Glauben handeln, es könne ihnen auf Grund ihrer Erfahrungen nichts mehr passieren.
Ein Schießberechtigter im Kaliund Steinsalzbergbau muß das 20. Lebensjahr voll endet haben. Er trägt eine hohe Verantwortung. Deshalb soll auf die wichtigsten R e geln über den Umgang mit Sprengstoffen und Zündmitteln noch einmal zusammen fassend hingewiesen werden:
Bergbau Sprengstoffe dürfen nur von zuverlässigen und der Belegschaft durch Aus hang bekanntgegebenen Personen ausgegeben werden. Nimm keinen Sprengstoff von anderen Kollegen an!
Es ist grundsätzlich verboten, Sprengstoffe unbefugt aus der Grube mitzunehmen und für irgendwelche privaten Zwecke zu benutzen. Dieser Mißbrauch wird streng bestraft!
Liefere gefundene Sprengstoffe und Zündmittel sofort der nächsten Aufsichts person a b !
Unsere Sprengstoffe sind handhabungssicher, d. h., sie können in der Grube gar nicht ohne weiteres explodieren. Lasse dich dadurch nicht zum Leichtsinn verführen! Befördere Sprengkapseln nicht zusammen mit Sprengstoffen! Halte beim Spreng stofftransport in Förderstrecken den richtigen Abstand!
Achte bei der Tätigkeit im Sprengstofflager auf gute Wetterführung und richtige Temperatur (nicht unter + 8 ° C und nicht über + 4 0 °C). Im Sprengstofflager darf nicht geraucht werden. Dulde nicht die Anwesenheit unbefugter Personen!
Sprengstoffe dürfen nur an die Schießberechtigten ausgegeben werden.
Führe als Schießberechtigter das Schießbuch sauber und gewissenhaft! Es wird wöchentlich kontrolliert.
Halte Ordnung in der Schießkiste! Gezähe gehört dort nicht hinein!
Vor Ort darf nur der Schießberechtigte selbst die Bohrlöcher laden und die elek trischen Zünder miteinander kuppeln. Auch in nicht gasgefährdeten Gruben darf bei der Schießarbeit nicht geraucht werden.
Alle nichtbeteiligten Personen haben beim Laden und Besetzen das Arbeitsort zu verlassen.
Sichere als Schießberechtigter vor dem Zünden alle Zugänge zum Arbeitsort gewissen haft ab!
Lasse nach dem Zünden der Schüsse erst die Sprenggase abziehen!
Warte bei Versagern mindestens 15 min bis zum Wiederbetreten des Abbaus 1
Die meisten Schießunfälle entstehen durch falsche Behandlung von Versagern. Nur der Schießberechtigte darf Versager und steckengebliebene Sprengstoffreste unschäd lich machen. In der Nähe von Versagern darf nicht gearbeitet werden.
Es ist streng verboten, Versager aufzubohren oder Schüsse auszukratzen.
6.1.6.Gewinnung beim Streckenauffahren
Bei der Streckenauffahrung sind neben betriebstechnischen Fragen auch zeitliche und wirtschaftliche Erwägungen zu berücksichtigen. Bisher sind bei normalen Be triebsverhältnissen Streckenbreiten von 4 bis 6 m aufgefähren worden. Im Werrage biet konnte man wegen der günstigeren geologischen Voraussetzungen 10 m breite, in einigen Gruben sogar 20 m breite Strecken ansetzen. Die Ausund Vorrichtungs baue müssen über eine große Lebensdauer verfügen. Sie werden deshalb im Südharz gebiet so schmal wie möglich gehalten, um ungünstige Druckauswirkungen zu ver meiden. Vielfach ist es erforderlich, Ausrichtungsstrecken in das ältere Steinsalz zu verlegen. Da dann das anfallende Haufwerk versetzt werden muß, ist schon aus wirt schaftlichen Gründen die Streckenbreite auf das mögliche Minimum zu beschränken. So haben sich im Südharzbezirk im Laufe der Jahre 5 m breite Strecken für die För derung, aber auch für die geologische Erkundung und für die Wetterführung durch gesetzt.
6.I.6.I. Vortriebsmethoden beim Streckcnauffabrcn mit Bohrund Schießarbeit
Das Auffahren der Strecken innerhalb der Ausund Vorrichtung ist bis in die ersten Jahre des zweiten Weltkrieges hinein ausschließlich im Bohrund Schießbetrieb er folgt. Die Versuche, mit maschinellen Auffahrmethoden eine höhere Vortriebsge schwindigkeit zu erreichen, sind nach kurzer Versuchsdauer ohne befriedigende Er gebnisse abgebrochen worden.
Die bis 1955 fast ausschließlich angewandte Vortriebsmethode war das Fächerschießewr mit einem Abschlag je Schicht. Das Bohrschema ist das gleiche wie beim Gewinnungs betrieb im Abbau. Das Fächerschießen bietet im schmalen Streckenvortrieb einen besonderen Vorteil. Das Haufwerk wird vom Ortsstoß in die Strecke hineingeschleu dert und kann dadurch vom Schrapperkasten gut erfaßt werden.
Die Höhe der Förderstrecken beträgt normalerweise 2,20 m bis 2,50 m. Gruben, die auf Grund großer Entfernungen unter Tage den Mannschaftstransport in speziellen Kraftfahrzeugen durchführen, benötigen Streckenhöhen bis 3 m.
Je nach Höhe der Strecke und nach anstehender Salzart bohrt man beim Fächersatz 3 oder 4, in seltenen Fällen auch 5 Löcher je Gang übereinander. Bei dem bisher in der Streckenauffahrung überwiegend benutzten Sprengstoff Donarit I sind je nach Salzart 60 bis 80 cm Vorgabe üblich.
An das fachliche Können eines Streckenhauers werden hohe Anforderungen gestellt. Dabei kommt es weniger auf körperliche Kräfte als vielmehr auf Überlegung und möglichst wirtschaftlichen Einsatz des Sprengstoffes an. Da früher die monatlichen Vortriebsleistungen im Fächerschießen bei einschichtigem Betrieb kaum über 40 m hinausgingen, wurden in fast allen Grubenbetrieben zahlreiche Versuche unternom
men, durch Verbesserungen der üblichen Methode einen schnelleren Streckenvortrieb zu erreichen. Bis vor wenigen Jahren ergaben sich für einen Abschlag in einer 5 m breiten Strecke einer Südharzgrube folgende durchschnittliche Kennziffern:
Ortsquerschnitt |
5 X 2,5 m |
Bohrmeter je Satz |
75 m |
Länge der längsten Bohrlöcher |
4 m |
Länge der kürzesten Bohrlöcher |
1,40 m |
durchschnittliche Vorgabe |
0,65 m |
Sprengstoffverbrauch je Satz |
etwa 42 kg |
Vortrieb je Satz |
etwa 1,90 m |
Haufwerk je Satz |
etwa 45 t |
Ein zweischichtiger oder gar dreischichtiger Bohrund Schießbetrieb in schmalen Strecken läßt sich wegen der Schwierigkeiten bei der Abförderung und bei der Wetter führung nur in wenigen Fällen verwirklichen. Man hat früher hohe Streckenauffahrleistungen erreicht, indem man je Schicht zwei Sätze abbohrte und abschoß. Beim Fächerschießen mußte dabei der erste Satz links und der zweite rechts herum gebohrt werden. Während der Frühstückspause wurde das Arbeitsort soweit wie möglich freigeschrappt und mit der Sonderbewetterung die Sprenggase abgesaugt.
Für die Hauer war diese Methode mit großen körperlichen Anstrengungen verbunden und schädigte in vielen Fällen auch ihre Gesundheit. Obwohl man auf diese Art Vor triebsleistungen bis zu 100 m im Monat erreichte, wurde in den Jahren nach 1945 dieses Verfahren grundsätzlich eingestellt. Einschneidende Maßnahmen im Rahmen der Grubensicherheit im Hinblick auf die Schlagwettergefährdung ließen zunächst die Vortriebsleistungen erheblich zurückgehen. Man begann deshalb sofort, neue Me thoden zu entwickeln und zu erproben, um die wichtigen Ausund Vorrichtungsar beiten zu beschleunigen. So kam es in den letzten Jahren zu einer Vielzahl neuer Schnellvortriebsmethoden beim Auffahren von Strecken. Entweder wurde der Ein satz von 2 Hauern mit je einer Bohrmaschine erprobt oder man versuchte, vom über lieferten Fächersatz abzukommen.
Nachfolgend sind einige Vortriebsmethoden aufgezählt, die in mehreren Gruben der Kaliindustrie mit Erfolg angewendet wurden und die zunächst das Fächerschießen in seinen Grundzügen beibe
hielten.
Die Methode des Hauers Riemert vom VEB Kaliwerk „Glückauf“ Sondershausen ist in Bild 6/11 skizziert. Riemert bohrte bei den ersten Gängen 5, anschließend jeweils 4 Löcher je Gang ab. Der als dritter Gang abgeschossene Stoßgang am linken Stoß wurde jeweils am Vortage als letzter Gang weit überbohrt und diente damit am neuen Arbeitstag zur Vereinfa chung der Einbruchsarbeit.
Bild 6/11. Vortrlobsmcthodo Riemort
In 6 m breiter Strecke
Illld 6/12. Vortrlcbsmcthodo Nordhcim mit Gegciiclnbruch
Mit dieser Methode •wurde ein Vortrieb von etwa 2,20 m je Satz erreicht, was bei einschichtiger Belegung einer Monatsleistling von etwa 55 m Strecke entsprach. Je Meter Vortrieb wurden etwa 23 kg Sprengstoff verschossen. Das ist eine günstige Verbrauchszahl.
Bei der Methode Nordheim vom Werrawerk ,,Marx-Engels“ arbeitet man mit dem soge nannten Gegeneinbruch nach Bild 6/12. Die ersten 3 oder 4 Gänge jedes Satzes werden am linken Stoß links herum gebohrt und auf diese dann ein normaler Eächersatz abgeschossen.
Diese Methode erleichtert die nachfolgende Schrapperarbeit und ermöglicht Vor triebsleistungen von 2,40 m/Schicht. Das Verfahren wurde auch von mehreren Süd harzgruben übernommen und wird heute noch teilweise augewendet.
Grundsätzlich muß festgestellt werden, daß bei Beibehaltung des Fächersatzes die Vortriebsleistungen beschränkt bleiben und das in der Kaliindustrie angestrebte Ziel einer Auffahrung von 200 m im Monat nicht erreicht werden kann. Deshalb ist in den letzten 10 Jahren mit vielen Versuchsvariationen das Kanoneneinbruchschießen wie der eingeführt worden.
Schon um 1925 wurde es im Kaliwerk „Glückauf“ , Sondershausen, erstmalig er probt. Es ist aucli unter dem Namen Brennereinbruch, Röhrenschießen oder Parallel bohrverfahren bekannt geworden. Der Hauer bohrt dabei lange Löcher rechtwinklig zum Ortsstoß und parallel zur Vortriebsrichtung. Dabei werden mehrere Löcher durch besondere Gestänge und Bohrschneiden mit einem großen Durchmesser gebohrt, aber nicht mit Sprengstoff geladen. Diese sogenannte Kanone ersetzt die zusätzliche freie Fläche des Fächerschießens. Die übrigen im normalen Bohrbetrieb hergestellten Gän ge werden etwas auf die Kanonenlöcher zulaufend gebohrt.
Obwohl mit dieser Vortriebsärt große Abschlagtiefen in einer Schicht erzielt werden können, ergeben sich dabei besondere Schwierigkeiten für das Abfördern mit dem Schrapper. Das losgeschossene Haufwerk bleibt direkt am Ortsstoß liegen. Für den Einsatz in mehrschichtigem Betrieb ist deshalb eine besondere Arbeitsorganisation mit einer einwandfreien Sonderbewetterung erforderlich.
Der Hauer Gebauer entwickelte im VEB Kaliwerk „Einheit“ eine Vortriebsmethode mit Kanoneneinbruch (Bild 6/13). Bei 5 oder 6 m Streckenbreite arbeiteten vor Ort 2 Hauer mit je einer Maschine. Ein
Hauer bohrte die Kanone, die in diesem Fall aus einem einzigen Loch bestand, und die Erweiterungsgänge. Der andere Hauer bohrte auf die Kanone zu den restlichen Strecken stoß ab. Das erforderliche Großbohr loch hatte einen Durchmesser von 160 mm und wurde mit einer Ma-
nild 6/13. Vortrlobsmctliodo Gebauer mit Knnoncnloch
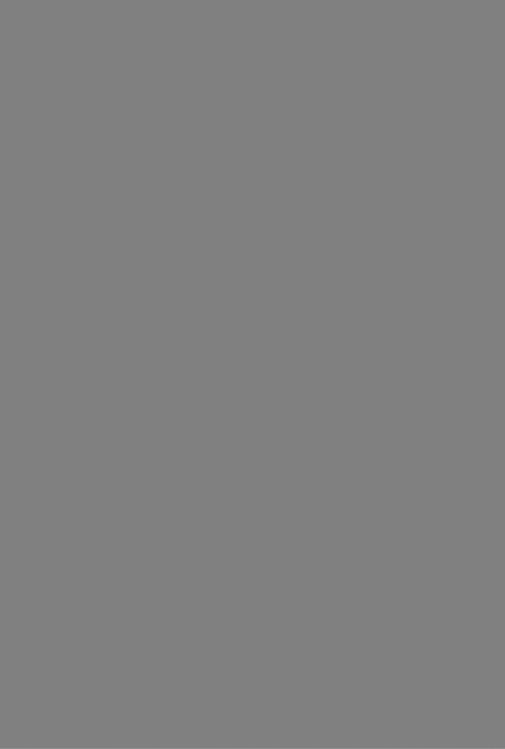
Bild 6/10. Streckenvortrieb |
|
mit Schlitz einer SFG |
|
Gang 4 |
22 Patronen |
|
Donarit und |
|
4 Patronen |
|
Gelatine- |
|
Donarit |
Gang 5 |
20 Patronen |
|
Donarit und |
|
4 Patronen |
|
Gelatine- |
Gang 6 bis 10 |
Donarit |
18 Patronen |
|
|
Donarit und |
|
4 Patronen |
|
Gelatine- |
|
Donarit |
In anderen Grubenbetrieben sind ähnliche Methoden er probt und angewandt worden.
Es hat sich gezeigt, daß Vortriebsverfahren mit reinem Fächersatz dem kombinierten Großloch-Fächerverfahren unterlegen sind. Im Streckenvortrieb mit Bohrund Schießbetrieb hat sich das Zünden der Schüsse mit ms-Zündern immer mehr durch gesetzt.
6.2.Maschinelle Gewinnung
6.2.1.Maschinelle Streckenauffahrung
Trotz guter Leistung im Streckenvortrieb mit Bohrund Schießarbeit ist die Schnel ligkeit beim Streckenauffahren immer hinter den Erwartungen zurückgeblieben. Dies trifft besonders für Erkundungsstrecken zu, die im Interesse des Neuaufschlusses von Lagerstättenteilen in von den Abbaubetriebspunkten weit entfernte, noch unverritzte Teile des Gebirges führen.
Es ist deshalb schon vor vielen Jahrzehnten versucht worden, durch maschinelle Streckenauffahrung den Vortrieb zu beschleunigen. Aber alle Versuche scheiterten früher an den physikalischen Eigenschaften der Salzgesteine. Im Gegensatz zur Kohle ist besonders im Hartsalz durch die im Salzgestein vorhandenen Anhydritbzw. Kieseritkomponenten eine rein schrämende oder fräsende Gewinnungsart bisher nicht möglich gewesen.
Erst nach 1945 hat die damalige Maschinenbaufirma SCHMIDT, CRANZ & Co., heute VEB „NOBAS“ , in Nordhausen Streckenvortriebsmaschinen konstruiert und zum Einsatz gebracht, die brauchbare Leistungen erzielten. Die Maschinen arbeiteten nach dem Prinzip des Fräsens und Brechens.
Diese ersten leistungsfähigen Vortriebsmaschinen schnitten einen kreisrunden Quer schnitt von 3 m Durchmesser und frästen gleichzeitig die Fahrbahnen für die Ma schine aus. Im Südharzkaliwerk Bleicherode wurden in den Jahren 1947 bis 1950
Bild 0/17. Prinzip des Frilscns und Brechens bei der Strcckcnvortricbsninschino
Durchschnittsleistungen bis zu 170 m und Spit zenleistungen bis zu 250 m im Monat in zwei schichtigem Betrieb erreicht. Allerdings konnten diese Leistungen nicht über einen längeren Zeit raum hinweg gehalten werden, weil Reparatur arbeiten, Schwierigkeiten bei ungünstigen geolo gischen Bedingungen (starkes Einfallen,Anfahren von Salzton) die Auffahrung beeinträchtigten.
Der Hauptnachteil dieser Maschine war ihre Unbeweglichkeit. Sie wog 40 t und er reichte mit Verladeband eine Länge von 27 m. Sie konnte deshalb nur einen weiten Kurvenradius durchfahren und war bei einem Einfallen bzw. Ansteigen über 6° nicht mehr betriebsfähig.
Im Laufe der letzten Jahre hat der gleiche Betrieb auf der Grundlage der alten Ma schine ein neues, wesentlich leistungsfähigeres Aggregat entwickelt. Diese neue Ma schine Typ V 3001 ist seit 1958 in verschiedenen Kaligruben zum Einsatz gekommen. Selbstverständlich waren zunächst viele Anfangsschwierigkeiten zu überwinden, die zum Teil in Bedienungsfehlern, zum Teil auch in Konstruktionsmängeln zu suchen waren.
Durch ausgezeichneten Einsatz der mit den Vortriebsmaschinen arbeitenden Maschi nisten, der entsprechenden Lenkungskräfte unter Tage unter Anleitung eines für diese spezielle Aufgabe gebildeten Arbeitskreises sind bis 1961 die eingesetzten Maschinen zunächst in maschinentechnischer, später in organisatorischer Hinsicht in bezug auf Belegung, Reparatureinsatz usw. zu sehr leistungsfähigen Aggregaten entwickelt worden. Die Maschinen haben zum Zweck der geologischen Erkundung viele Kilo meter von Strecken weit ins Feld vorgetrieben und damit den Aufschluß neuer Rohsalzvorräte ermöglicht.
Die Arbeitsweise ist in den Hauptzügen folgende:
Ein mit Schneidstählen besetzter zweioder dreiflügeliger Schneidarm fräst Rillen von 32 mm Breite in das Salzgestein. Nach etwa 90 mm brechen die über die Schneid stähle aufgesetzten Brecher die zwischen den Rillen stehengebliebenen Salzrippen ab (Bild 6/17). Das anfallende Haufwerk wird über eine Schurre einem unter der Vor triebsmaschine laufenden Gummitransportband zugeführt. Von dort wird das Salz hinter der Maschine an das Abfördermittel übergeben. Hinter dem Schneidarm wer den links und rechts durch die vorhandenen Fahrbahnfräser die Laufflächen ge schnitten, auf denen die gesamte Maschine fährt. Diese Fahrbahnfräser sind höhen verstellbar, um je nach den Lagerverhältnissen ein ansteigendes oder einfallendes Fahren zu ermöglichen.
Ein Drehstrommotor mit 70 kW Leistung treibt über ein Getriebe den Schneidarm an. Die Vorderachse mit 2 Laufrädern ist starr mit dem Getriebe verbunden. Die Hinterachse ist verschiebbar.
Es ist möglich, Linksoder Rechtskurven mit einem kleinsten Radius von 25 m zu fahren. Die Maschine wird seitlich am Stoß verspannt. Abspannung und Vorschub erfolgen hydraulisch. Der Vorschubzylinder hat einen Hub von 900 mm. Um diese Länge fährt der Zylinder aus, dann muß die gesamte Maschine nachgenommen und neu verspreizt werden. Hinter dem Hauptmotor ist die Fahrerkabine angebracht, die mit dem Kabelwagen verbunden ist. In der Kabine sind alle Steuerschieber, Druck-
Bild (5/18. llaupttellc der V 3001 (Wcrkszoichnung)
(1) Sclmcidnrm, (2) Getriebe, (3) Motorcnkonsol, (4) Vorderachse, (5) Hinterachse, (0) Kugel, (7) Lenker, (8) Vorschubund Spanngcrut, (9) Fahrerkabine, (10) Fahrbahnfrsiscr, (11) Unterband, (12) Kabclwagen, (13) Abförderband, (14) ülpumpc, (15) Hauptmotor
messer uncl Kontrollgeräte angeordnet. Der Kabelwagen kann bis 250 m Zuleitungs kabel aufnehmen.
Im Bild 6/18 ist die Maschine im Schnitt schematisch gezeigt. Die Hauptteile sind aufgezählt.
Die wichtigsten technischen Daten der Streckenvortriebsmaschine V 3001 sind in der Tabelle 5 zusammengestellt. Die Tabelle zeigt, daß die neue Maschine hinsichtlich Länge, Masse und Kurvenradius gegenüber früheren Ausführungen wesentliche Ver besserungen aufweist.
Tabelle 5. Zusammenstellung der wichtigsten technischen Daten der Streckenvortriebs maschine V 3001
Höhe |
|
2350 mm |
Breite |
|
2650 mm |
Länge ohne bzw. mit Bändern |
|
8,7 m bzw. 47 m |
Masse der Maschine |
|
13,5 t |
Masse der Bandanlage |
|
8,0 t |
Kurvenradius min. |
|
25 m |
Schneidarm |
|
|
2 Flügel 19 Scheidstähle |
|
3 Flügel 25 Schneidstähle |
2 Außenstähle |
|
3 Außenstähle |
1 Zentrierbohrer |
|
1 Zentrierbohrer |
Schneidarmdrehzahl |
|
6.8 U/min |
Rillenbreite |
|
32 mm |
Rillentiefe |
bi |
130 •••150 mm |
Rippendicke |
85 mm |
|
Schnittgeschwindigkeit außen |
max. |
1,06 m/s |
Öldruck der Hydraulikanlage |
200 atü |
|
Betriebsdruck |
max. |
60 atü |
Antriebsdrehzahl |
|
1450 U/min |
Abspannbzw. Vorschubdruck |
|
18850 kg/max. |
Vorschubgeschwindigkeit regelbar |
|
0 •••0,955 m/min |
Hub Vorschubzylinder |
|
900 mm |
Hub Abspannzylinder |
|
154 mm |
Geschwindigkeit der Förderbänder |
|
1.9 m/s |
Antriebsleistungen |
|
|
Getriebe |
|
70 kW |
Fahrbahnfräser |
je |
10 kW |
Hydraulik |
|
5 kW |
Bänder |
je |
1,9 kW |
Ventilator |
|
0,25 kW/220 V |
Spannung |
|
500 V |
Entscheidend für die Leistungsfähigkeit ist neben der einwandfreien Wartung die Organisation der Belegung und die der Abförderung des anfallenden Haufwerkes hin ter der Streckenvortriebsmaschine. Erst wenn diese Fragen gelöst sind, kann die tat sächliche Schneidkapazität der Maschine weitgehend ausgenutzt werden. Die Abför derung kann erfolgen in
a)direktem Abwurf des Salzes vom Zubringerband in Förderwagen und anschlie ßendem Abtransport mit Lokomotiven oder
b)durch Abwurf des Salzes vom Band in die Strecke und anschließende Abförderung durch Schrapper in Förderwagen.
Voraussetzung für eine leistungsfähige Abförderung mit Lokomotiven ist eine gün stige Gestaltung der Rangierarbeit mit den Förderwagen hinter der Streckenvor triebsmaschine. Hierfür kommen Wagenwechsel durch Verwendung von Verteilerweichen oder durch Verwendung eines Patentgleises mit Auflegeweiche in Frage.
Bei der Schrapperabförderung sollte man sich auf Ausnahmefälle beschränken, die nur dann vorliegen, wenn stark ansteigende oder einfallende Maschinenstrecken (über 3 %) die Benutzung von elektrischen Lokomotiven nicht mehr zulassen. Der Einsatz von Schrappern setzt die Auffahrleistung herab, da umfangreiche Nebenar beiten wertvolle Zeit in Anspruch nehmen.
Die Belegung sollte in jeder Schicht wie folgt angestrebt werden:
2 Maschinisten für das Fahren der Maschine, Einhaltung der Stunden, Auswechseln der Schneidstähle, laufende Überprüfungsund Instandhaltungsarbeiten,
1 Füller für die Abförderung,
1 Lokfahrer für die Rangierarbeiten der Leerund Vollwagen, Abfahren des geschnit tenen Salzes zur Hauptstreckenförderung und Heranführung der leeren Wagen.
Dazu kommen in der Reparaturschicht 3 Handwerker für Gleisarbeiten, Kabelnachziehen, Vorbringen der Sonderbewetterung und Durchführung evtl. Reparaturen. Die Maschinenbrigaden sind sorgfältig zusammenzustellen. Die Maschinisten müssen eine hohe Qualifikation besitzen, da neben rein maschinentechnischen'Kenntnissen das sichere Beherrschen und Befolgen aller Vorschriften der technischen Sicherheit und des Arbeitsschutzes verlangt werden müssen. Betriebspunkte der Streckenvor triebsmaschine sind oft viele Kilometer vom sonstigen Grubenbetrieb entfernt. Das dort eingesetzte Kollektiv muß auf sich allein gestellt leistungsfähig sein und verant wortungsbewußt arbeiten.
Mit der neuen Vortriebsmaschine V 3001 sind seit 1961 beachtliche Leistungen voll bracht worden. Die aufgefahrenen Streckenmeter können zwar noch nicht in allen Fällen voll befriedigen, man darf aber erwarten, daß noch bestehende Schwierigkeiten auf maschinentechnischem Gebiet und noch vorhandene Organisationsfehler bald überwunden sind.
Laut Arbeitsmittelpaß kann die V 3001 Leistungen von 2 bis 4 m/h beim Auffahren