
книги / Technologie des Kali - und Steinsalzbergbaus
..pdf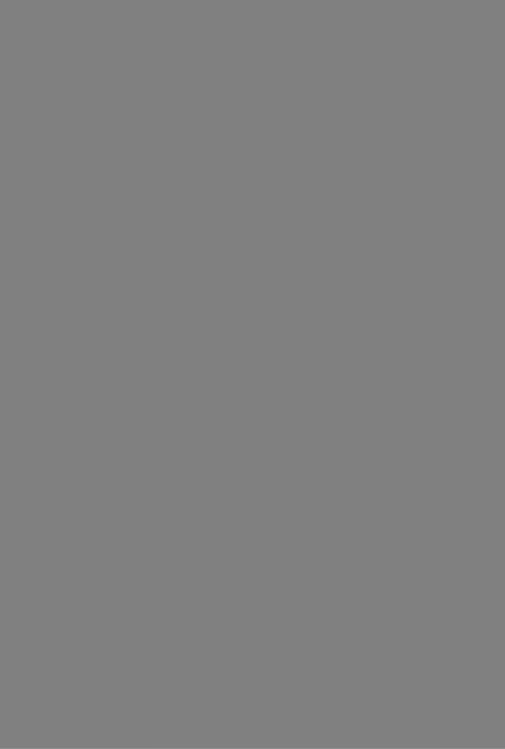
ßen Durchmesser haben, um das Seil zu schonen. Die Befestigung der Rolle im Stoß muß sorgfältig und sicher eingebracht werden, um Störungen und Unfälle zu vermei den. Andererseits muß die Befestigung der Rolle leicht lösbar sein, damit die Um lenkrolle mehrmals in der Schicht umgehängt werden kann. Die in Bild 7/13 darge stellte Befestigung läßt zwei Keile erkennen. Einer davon ist mit einer Schlaufe aus geführt, in die die Umlenkrolle eingehangen werden kann.
Andere Rollen sind notwendig, um das Leerseil unterwegs zu führen. Diese Rollen müssen seitlich beweglich aufgehängt*sein. Sie verhindern ein Einschneiden des Seiles in der Sohle oder im Stoß.
Der Schrapperkasten wird durch das Vollseil vor der direkten Entladung in Förder wagen über eine Schrapper- oder Ladebühne gezogen (Bild 7/14). Die Bühne ist auf einem Eisengerüst verankert und an ihrem höchsten Punkt um etwa 20° nach unten abgeknickt. Der abwärts geneigte Teil der Schurre dient als Führung des abrutschen den Haufwerkes, das direkt in die Förderwagen fällt. Beim Zweistreckensystem mit Rollochverbindung kann die Ladebühne entfallen. Der Schrapperkasten wird dann direkt bis über das Rolloch gezogen, das gleichzeitig zur Magazinierung dienen kann.
Der eigentliche Betrieb in der Schräpperförderung ergibt sich aus der Darstellung im Bild 7/11. Die wichtigste Forderung, die leider in den Kaligruben nur ungenügend er füllt werden kann, ist die möglichst vollständige Ausnutzung der Schrapperkapa zität.
Die theoretische Leistungsfähigkeit einer Schrapperanlage ist hoch. Ihre Ausnutzung ist aber von mehreren Faktoren abhängig, die sich zum Teil gegenseitig beeinflussen und kaum alle vollständig berücksichtigt werden können. Die hauptsächlichsten Ein flußfaktoren sind:
Länge der Abbaukammern,
Lage des Haufwerkes vor Ort,
Einfallen oder Ansteigen des Lagers,
Kastengröße, Stückgröße und Förderwagengröße.
Anordnung des Wagenumlaufes,
Belegung und Organisation des Schrapperbetriebspunktes.
Den größten Einfluß hat die Weglänge, die der Schrapperkasten zurückzulegen hat. Bis etwa 40 m Kammerlänge ist ein Schrapperbetrieb unwirtschaftlich, da die Zeit für das Beladen der Förderwagen ungefähr die gleiche ist wie das Vorund Zurück ziehen des Kastens in der Schrapperbahn, d. h., die Leistungsfähigkeit des Schrappers kann nicht ausgenutzt werden, da durch das Einwechseln der Förderwagen Verlust zeiten entstehen. Ab 50 m Kammerlänge arbeitet der Schrapperbetrieb ökonomischer und erreicht zwischen 80 und 110 m Länge seine maximale Leistungsfähigkeit. Bei größeren Abbaulängen wird der Zeitbedarf für Vollund Leerfahrten zu groß. Außer dem kann bei langen Förderwegen ein 100%iger Füllungsgrad des Schrapperkastens kaum erreicht werden, weil immer Unebenheiten in der Sohle vorhanden sind. Vor Ort muß im Interesse einer guten Füllung meist mehrmals bis an die Umlenkrolle zu rückgefahren werden. Auch Einfallen oder Ansteigen des Lagers beeinflussen den Wirkungsgrad des Schrapperbetriebes. Ein schwaches Einfallen verursacht gute Kastenfüllungen. Bei stärker einfallenden Abbaukammern erhöht sich der Seilver brauch. Bei Einfallen über 15° dürfen nur kleine, nicht zu schwere Kästen benutzt werden, da sonst das vor Ort liegende Haufwerk vom Kasten an den Ortsstoß ge schoben wird.
Ein wesentlicher Faktor für die Leistungsfähigkeit eines Schrapperbetriebes ist die Zusammenarbeit des eingesetzten Kollektivs. Hauer und Schrapperfahrer müssen gut
Bild 7/15. Gleisführung an einer Schrnppcrrüiistclle
(1) üaspelstand, (2) Schrappcrscilc, (3) Schrapper-Ladebühne, (4) Seilführungsrollen, (5) Vollseitc der Seilbahn,
(0) Eüllglcis, (7) Lccrscitc der Seilbahn, (8) Auffahrrichtung der Abbaukammer
aufeinander eingespielt sein. Der Hauer muß versuchen, sein Salz so hinzuschießen, daß der Schrapperfahrer ohne Schwierigkeiten seine Rolle hängen kann und gute Kastenfüllungen erreicht.
Die Kastengröße muß so gewählt sein, daß mit einem Schrapperzug mindestens ein, möglichst zwei Förderwagen gefüllt werden können. Während der Leerfahrt des Schrapperkastens kann der Schrapperfahrer einen neuen Leerwagen einwechseln. Aus diesem Grunde sind auch Anlage und Organisation der Gleisführung am Schrap per von Bedeutung. Bei Kettenoder Seilbahnbetrieb in der Hauptförderstrecke ist es zweckmäßig, ein drittes Gleis als Füllgleis zu verlegen (Bild 7/15). Bei Lokomotivbetrieb ist darauf zu achten, daß dieses Füllgleis die notwendige Länge besitzt, um einen ganzen Zug zum Abtransport mit der Lokomotive aufnehmen zu können.
Die Organisation an der Schrapperfüllstelle ist unter Berücksichtigung der jeweiligen Grubenverhältnisse mehrfach verändert worden. Bei langen Abbaukammern kann der Schrapperfahrer allein alle anfallenden Arbeiten bewältigen. Es muß aber be rücksichtigt werden, daß in einem Förderrevier nie der Fall eintreten darf, daß nur lange Schrapperbahnen in Betrieb sind. Die Abbauplanung hat dafür Sorge zu tragen, daß kurze, mittellange und lange Abförderwege für den Schrapper vorhanden sind und in einem günstigen Verhältnis zueinander stehen.
Trotz aller Bemühungen in der Organisation innerhalb der Abbauförderung ist es nicht gelungen, die Nachteile des Schrapperbetriebes zu überwinden. Hauptnachteil bleibt die Tatsache, daß auch bei mehrschichtigem Betrieb nur eine Auslastung der Schrapperkapazität von höchstens 50 % erreicht werden kann. Man hat deshalb ver: sucht, im Zuge der sogenannten Kleinmechanisierung in einzelnen Grubenbetrieben auch am Schrapper technische Verbesserungen anzubringen.
Die tatsächliche Leistungsfähigkeit der Schrapper im praktischen Betrieb läßt sich nur schwer in absoluten Zahlen ausdrücken. Bei normalen Einsatzbedingungen wird
Uild 7/1C. Scheitln eines Ivnrusscllbctricbes mit 2 Sclirappcrklisten In (1er Sammclsclirai)- pcrbnhn
(1) Zubringerschrapper,
(2) Schrapperkästen des Sammclschrnppcrs, (3) Haufwerk,
(4) Haspelraum der Zubringer,
(5) Ladebühne, (0) Sammelschrapperstand, (7) Förderwagen an der Füllstclle
z. B. im Südharzbezirk so verfahren, daß beim Zwillingsbau in der lin ken Kammer gebohrt und geschossen und in der rechten Kammer in der gleichen Schicht ge schrappt wird. In der nächsten Schicht wird gewechselt. Dadurch kommt eine bessere Aus lastung der Schrapper kapazität zustande, da eine gegenseitige Beein flussung von Schrapper und Hauerarbeit nicht auftritt.
Dennoch liegen die durchschnittlichen Schrapperleistungen im Südharz kaum über 100 t/Schicht. Die brei terenAbbaukammern im Werragebiet haben ört liche Spitzenleistungen von über 150 t/Schicht ermöglicht.Der Gesamt leistungsdurchschnitt al
ler Kaligruben im Jahre 1961 lag aber in der Schrapperförderung nur bei 114 t/Schicht. Mit dieser Leistung kann eine wirkungsvolle Betriebskonzentration mit dem Ziele einer Steigerung der Fördermenge aus einzelnen Betriebspunkten nicht ermöglicht werden. Hinzu kommt, daß die Scbrapperförderung durch ihren sehr hoher Seilver schleiß die Selbstkosten des Grubenbetriebes erheblich beeinflußt. Im Jahre 1961 sind im Durchschnitt aller Kaligruben für je 1000 t Rohsalzförderung 71,88 m Schrapperseil verbraucht worden. Dadurch wurden die Betriebskosten im Arbeits abschnitt „Abbauförderung“ allein durch den Seilverbrauch mit 0,14 DM/t belastet. Dabei ist berücksichtigt, daß im Normalfall die Schrapperseile mit Durchmessern von 20 bis 22 mm für die Leerseile und von 22 bis 24 mm, in Sonderfällen bis 28 mm für die Vollseile geliefert werden.
In fast allen Gruben sind Versuche unternommen worden, unter Ausnutzung der ge
gebenen örtlichen Verhältnisse die Schrapperleistungen zu verbessern. Bei den gün stigen Betriebsbedingungen an der Werra hat sich vorübergehend der Karussellbetrieb nach Bild 7/16 eingeführt. Mehrere Zubringerschrapper arbeiten auf eine Sammel schrapperbahn, in der ein starker Haspel zur Vermeidung des Leerzuges mit zwei Schrapperkästen fährt. An jedem Seil ist also ein Kasten befestigt, und jeder Schrap perzug bringt einen vollen Kasten zur Füllstelle. Die Schrapperseile haben 28 mm Durchmesser. Diese Methode ermöglicht beim Einsatz von Großraumförderwagen eine gute Betriebskonzentration. Die Karussellbetriebe haben Schichtleistungen bis zu 500 t je Füllstelle erzielt. Die Ermittlung der tatsächlichen Wirtschaftlichkeit er gab aber ein negatives Ergebnis. Man kann die Schrapperleistung nicht um jeden Preis steigern.
So bleibt bei Berücksichtigung der heute für einen modernen Grubenbetrieb notwen digen Aufgaben in der Abbauförderung die Feststellung, daß der Schrapperbetrieb trotz seiner auch z. Z. noch vorhandenen Vorteile in zukünftigen Jahren seine beherr schende Rolle verlieren wird. Die starke Abhängigkeit der Schrapperleistung von der Abbaulänge führt zu unbefriedigenden Ergebnissen bei langen Abbaukammern. Wei terhin ist der große Seilverbrauch als besonderer Nachteil zu nennen.
Wieviel Betriebsschrapper müssen in einer Schicht im Einsatz sein, wenn eine Grube 48001 eff in 2 Schichten )ordert und eine durchschnittliche Schrapperschichtleistung von 801 eff erreicht wird ?
Die Schrapperleistung errechnet sich nach
T |
_ |
3600 • v •J • |
(t/Schicht) |
— |
2- Z- H V - t F |
Es bedeuten:
L Schrapperschichtleistung [t eff] v Schrappergeschwindigkeit [m/s] J Kasteninhalt [t]
ts Stunden Schrappzeit [je Schicht] tFFüllzeit [s]
l Streckenlänge [m]
Errechnen Sie die Schrapperschichtleistung bei folgenden Annahmen:
v 1,4 l 100
J 2
h 4 tF 90
7.3.2.Arbeitsorganisation in der Abbauförderung beim Einsatz moderner Ladeund Fördergeräte
Die Perspektivplanung der Kaliindustrie muß die Aufgabe lösen, in zukünftigen mo dernen Grubenbetrieben neue Wege in der Abbauförderung mit gutem wirtschaft lichem Erfolg zu finden. Da diese Aufgabe nur im Zusammenhang mit einer Teilöder Vollmechanisierung gelöst werden kann, wird der Einsatz von Ladegeräten in un mittelbarer Verbindung mit modernen Abfördergeräten notwendig werden.
Hierbei kommt es auf eine sinnvolle und gut durchdachte Kombination der Geräte-
Bild 7/17. Schema eines konzentrierten Gewinnung»-Abbaufördorbotriebspunktos mltspozlollom Gerüteolnsatz
(1) Doppelfrässcheibenlader, (2) Bunkerpendchvagcn, (3) Kratzförderer, (4) Durchlaufbrecher, (5) Quer-Kratzförderer,
(0) Förderband
typen und auf einen Arbeitseinsatz an, der ihre hohe Leistungsfähigkeit besser aus nutzt, als es im Schrapperbetrieb möglich ist.
Die beschriebenen Joy-Lader oder die Doppelscheiben-Fräslader erreichen Stunden leistungen von etwa 2001. Ihr hoher Anschaffungspreis verlangt zwangsläufig ihren Einsatz an mehreren Betriebspunkten im Verlaufe einer Schicht. Die auf Raupen fahrbaren Ladegeräte lassen sich relativ schnell bewegen und können bei Benutzung der Durchhiebe zwischen den Abbaukammern von einem Ortsbetrieb zum anderen gefahren werden. Sie beladen Bunkerpendelwagen, die im ständigen Vorund Zurück fahren zwischen Ortsbetrieb und Hauptförderstrecke eine hohe Schichtleistung er reichen. Um Leerfahrten zu vermeiden, muß ein Ladegerät mindestens zwei Pendel wagen bedienen, bei langen Abbaukammern ist ein dritter Pendelwagen erforderlich. Die Entladung der Bunkerpendelwagen kann direkt in Förderwagen oder auf Kratz förderer erfolgen, die das Haufwerk dann über einen Durchlaufbrecher der Bandför derung in der Hauptstrecke zuleiten. Der Durchlaufbrecher ist im VEB Bergwerks maschinenwerk Dietlas entwickelt worden. Er hat die Aufgabe, das grobstückige Haufwerk auf Kantenlänge von max. 200 mm zu zerkleinern und damit einen zu schnellen Verschleiß der nachgeschalteten Gummitransportbänder zu verhindern.
Das in Bild 7/17 dargestellte Schema zeigt, wie unter der Voraussetzung einer guten Arbeitsorganisation eine Dauerleistung von 600 t/Schicht aus einem Gesamtbetriebs punkt erreicht werden kann. Zu diesem Betriebspunkt zählen 6 Abbaukammern ver schiedener Länge bei Beibehaltung der jetzigen Abbaumethode und der üblichen Bohrund Schießarbeit. Es werden Südharzverhältnisse mit einer durchschnittlichen Lager mächtigkeit von 6 m angenommen.
Geräteeinsatz: 1 Doppelfrässcheibenlader |
|
|
2 oder 3 Bunkerpendelwagen |
I für jeweils 6 Abbaukammern |
|
1 |
Kratzförderer |
|
1 |
Durchlaufbrecher |
|
Die tatsächliche Leistung des Laders im Dauerbetrieb wird mit 170 t/h angesetzt. Diese Kapazität muß voll ausgelastet werden, wenn das Gerät wirtschaftlich arbeiten soll. Voraussetzung für den angegebenen Geräteeinsatz ist ein Rohsalzanfall von min destens 2001 täglich je Abhau. Das kann erreicht werden, wenn im zweischichtigen Betrieb von den 6 Kammern eines Abbaublocks jeweils 3 zum Bohren und Schießen und 3 zum Abfördern belegt sind. In der Gewinnung werden 2 Abbaue mit Einbruch schießen (Vortrieb) belegt. Das ergibt einen Salzanfall von 2 mal 1401. In der dritten Kammer wird die Firste gedrückt mit einem Salzanfall von etwa 330 t.
Daraus ergibt sich ein Gesamtsalzanfall von 2(330 + 280) = etwa 1220 t/Tag. Diese Salzmenge muß von den zum Einsatz bestimmten Geräten bewältigt werden. Das Fassungsvermögen der Pendelwagen wird im Dauerbetrieb mit je 12 t angesetzt. Der beladene Wagen erreicht eine Geschwindigkeit von 5,3 km/h, bei Leerfahrt be trägt sie 8 km/h. Der Kratzförderer am Boden des Wagens läuft bei der Entleerung mit etwa 0,2 m/s, so daß der 7,3 m lange Wagen theoretisch in der sehr kurzen Zeit von etwa 30 Sekunden entladen werden kann. In der Praxis ist die Entladezeit von den Bedingungen des nachgeschalteten Streckenfördermittels abhängig.
Das Beladen eines Pendelwagens dauert nach Erfahrungswerten einschließlich Ran gierarbeiten etwa 5,3 min.
Die Gesamtfahrzeit des Bunkerpendelwagens ist von der Abbaulänge abhängig. Be triebsversuche ergaben folgende Erfahrungswerte:
Abbaulänge |
Fahrzeit |
Fahr-, Beladeund |
|
|
Entladezeit |
[m] |
[min] |
[min] |
60 |
0,5 |
7,4 |
100 |
0,9 |
7,9 |
160 |
1,4 |
8,3 |
200 |
1,9 |
8,8 |
300 |
2,8 |
9,7 |
400 |
3,0 |
10,7 |
Aus dieser Tabelle ist zu ersehen, daß bei kurzen Abbaulängen 2 Pendelwagen völlig ausreichen, von denen einer am Ladegerät steht, der andere unterwegs ist. Erst bei längeren Abbaukammern (über 200 m) muß ein dritter Pendelwagen eingesetzt wer den, wenn am Frässcheibenlader keine Wartezeiten auftreten sollen. Entscheidend für die tatsächliche Leistungsfähigkeit eines „Gerätegespannes“ bleibt die Beladezeit der Pendelwagen am Lader, da dort der längste Zeitbedarf - unabhängig von der Kammer länge - vorhanden ist. Diese Beladezeit beträgt 5,3 min. Danach ergibt sich:
-n,.. j |
Pendelwageninhalt •Minuten |
, |
Fordermenge = |
--------------Beladezeit-------------- |
° der |
Q = i- ^ ~ = i35tjh .
Für einen Abbau mit 200 t Haufwerk benötigen die eingesetzten Geräte also etwa 1,5 Stunden. Für das Umsetzen des Frässcheibenladers durch einen Durchhieb in den nächsten Abbau wird ein Zeitbedarf von einer halben Stunde gerechnet. Bei 3 Um setzungen je Schicht steht also eine produktive Arbeitszeit von 6 — 1,5 = 4,5 Stun den zur Verfügung. Danach ergibt sich eine Schichtleistung von
Q = 4,5 X |
135 = |
605 t/Schicht oder |
605 X |
2 = |
1210 t/Tag bei zweischichtigem Betrieb. |
Diese Menge würde einer sehr günstigen Betriebskonzentration entsprechen, da beim zweischichtigen Schrappereinsatz mindestens 7 komplette Schrapperbetriebspunkte vorhanden sein müßten, um die gleiche Salzmenge zu fördern.
Allerdings ist der vorgeschlagene Geräteeinsatz von mehreren Bedingungen abhängig. In den Abbaukammern darf kein zu starkes Einfallen vorhanden sein. Die Sonder bewetterung muß gut arbeiten, da ein ziemlich starker Staubanfall hervorgerufen wird. Die eingesetzten Geräte erfordern eine hohe Qualifikation des Bedienungsper sonals. Für die ständige Wartung und Durchführung von Reparaturen in der dritten Schicht muß ein geschulter Stamm von Handwerkern herangebildet werden. Dadurch steigen die Lohnkosten an.
Dennoch scheinen die Vorteile der nach Bild 7/17 durchgeführten, in großzügiger Form angesetzten Betriebsversuche zu überwiegen. Abschließende genaue Ergebnisse sind noch nicht bekannt. Es steht aber fest, daß der Einsatz der beschriebenen Geräte kombinationen in den dafür geeigneten Grubenfeldern nicht nur eine Senkung der Grubenselbstkosten, sondern vor allem eine Steigerung der Arbeitsproduktivität er warten läßt.
7.3.3.Besonderheiten des Arbeitsschutzes
und der technischen Sicherheit in der Abbauförderung
Die Vorschriften für die technische Sicherheit in der Abbauförderung sind bei dem in allen Gruben fast ausschließlich eingesetzten Schrapperbetrieb besonders umfang reich. Obwohl die Schrapperförderung in technischer Hinsicht als eine einfache und gut übersehbare Fördermethode bezeichnet werden kann, birgt das Arbeiten mit den langen Schrapperseilen viele Gefahrenmomente.
Ein Schrapperseilriß kommt häufig vor und kann zu schweren Unfällen führen, wenn die abgerissenen Seilenden in der Schrapperbahn auf dort unbefugt arbeitende Berg leute treffen.
Die wichtigste Schutzbestimmung ist deshalb:
Schrapperbahnen dürfen während der Förderung nicht betreten werden. Auf das Verbot ist durch Verbotstafeln an allen Zugangsstellen hinzuweisen. - Der Stand des Schrapperfahrers und die an der Füllstelle vorbeiführenden Fahrwege und Durchgänge müssen durch Schutzvorrichtungen gegen Seilschlag gesichert sein.
Es ist verboten, auf dem Schrapperkasten mitzufahren. Durch eine derartige Hand lungsweise ist es in der Vergangenheit zu vielen schweren Unfällen gekommen. Eine der wesentlichsten Voraussetzungen für einen störungsfreien Betrieb innerhalb der Schrapperförderung ist das Vorhandensein einer Signalanlage zur Verständigung
zwischen dem Schrapperfahrer und dem Hauer. Es ist nur bei ganz kurzen Abbau längen und auch dann nur unter günstigen Bedingungen möglich, daß zwischen beiden eine Sichtverbindung besteht. Bei längeren Abbaukammern, bei wechselhaftem Ein-
fallen und bei unübersichtlichen Betriebsverhältnissen ist die SignalVorrichtung obligatorisch. Ausnahmen kann die Bergbehörde im Einvernehmen mit der Arbeitsschutzinspektion dann bewilligen, wenn Gewin nung und Förderung getrennt voneinander erfolgen, d. h. wenn Schrapperfahrer und Hauer nicht in der gleichen Schicht im gleichen Abbau arbeiten.
Bei Sammelschrapperanlagen müssen an demZubringerschrappern und an den in die Sammelschrapperbahn einmündenden Abbaustrecken solche Signalvorrich tungen vorhanden sein, die eine einwandfreie gegen seitige Verständigung ermöglichen.
Bei Befahrungen der Schrapperbahn durch Steiger oder andere Aufsichtspersonen können bis zu einer Länge von 50 m Signale mit der Lampe gegeben wer den. Dabei haben entsprechend der Zeichnung im Bild 7/18 die einzelnen Zeichen mit dör Lampe folgende Be deutung :
Kreisende Bewegung |
Halt |
Senkrechte Bewegung |
Auf (vorwärts) |
Waagerechte Bewegung |
Hängen |
Diese Zeichengebung entspricht bei der offiziellen Si gnalvorrichtung folgenden Unterscheidungen, wobei die Zeichengebung optisch oder akustisch erfolgen kann:
1 Zeichen |
Halt |
2 Zeichen |
Auf (vorwärts) |
3 Zeichen |
Hängen |
Sämtliche Schrapperanlagen müssen vor ihrer Inbetriebnahme vom Sicherheitsin spektor des Werkes und vom Leiter der betrieblichen Arbeitsschutzkommission einer Abnahmeprüfung unterzogen werden. Der Abnahmebefund ist mit der Freigabe schriftlich zu formulieren.
7.4.Zwischcnfördcrung
Es ist nicht immer möglich, das gewonnene Haufwerk aus der Abbauförderung direkt der Hauptstreckenförderung zu übergeben. Wenn auf Grund geologischer Besonder heiten oder sonstiger örtlicher Verhältnisse ein zusätzliches Fördermittel eingeschal tet werden muß, wird auch im Salzbergbau die Zivisclienförderung angewendet.
Die Zwischenförderung besaß früher eine größere Bedeutung als heute, weil besonders in den Staßfurter Kaligruben bei halbsteiler Lagerung Abförderprobleme durch Bremsberge oder Aufhauen gelöst werden mußten. Nach Einführung des Steilfirsten baues war diese Zwischenförderung nicht mehr erforderlich.
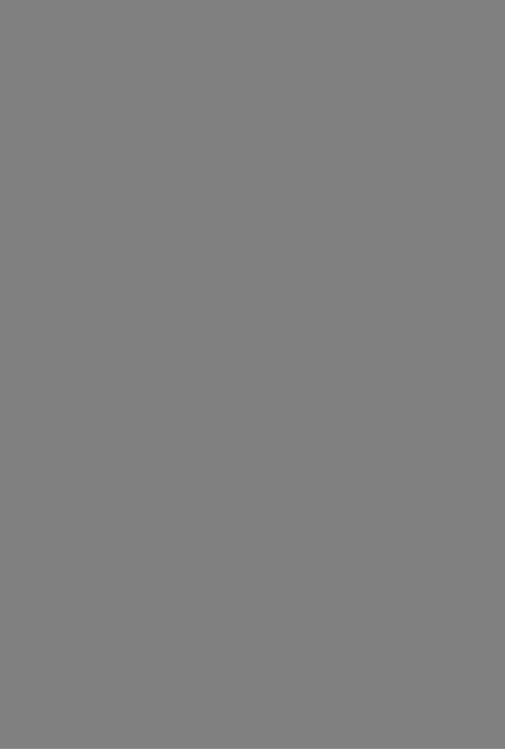