
книги / Technologie des Kali - und Steinsalzbergbaus
..pdf2 Bohrmaschinen) den Salzanfall je Schicht erhöhen, soweit die Lagerverhältnisse dies zulassen. Grundsätzlich ist aber folgendes zu beachten:
Voraussatzung fiir einen reibungslosen Betrieb in der Gewinnung ist eine ge naue Abstimmung zwischen der Bohrund Schießleistung und der nachgeschal teten Abbauförderung.
Erst in den letzten Jahren ergab sich durch die Entwicklung besonders leistungs fähiger Bohrmaschinen die Möglichkeit, die reine Bohrleistung in den Gewinnungs punkten wesentlich zu erhöhen. Dadurch fällt nun in jeder Abbaukammer mehr Salz in einer Schicht bzw. in einem bestimmten Zeitintervall an. Für die Bergbauma- schinen-Industrie ergibt sich daraus die wichtige Aufgabe, in Zusammenarbeit mit den Kalibergleuten Geräte und Anlagen zur Abförderung größerer Haufwerksmengen aus den Abbaukammern zu schaffen.
Im Laufe der letzten Jahre haben sich für das im Salzbergbau übliche drehende Boh ren besonders drei Bohrmaschinentypen allgemein durchgesetzt:
die alte Siemensmaschine Typ SSW E 158, die Bohrmaschine Typ DIN A 1,
die Schnellfrequenzmaschine Typ SFS 1.
Es handelt sich hierbei um Säulendrehbohrmaschinen, die in allen Gruben eingesetzt werden können und für die wechselnde Härte der Salzgesteine gut geeignet sind. Die Maschinen werden in Normalausführung oder schlagwettergeschützt geliefert. Sie bestehen im wesentlichen aus einem oberflächengekühlten Kurzschlußläufermotor (Drehstrom), einem Getriebe für selbsttätigen Differentialvorschub und mechanischen Spindelrückgang, einem Schalter und dem Anschluß für das Bohrkabel (Bild 6/1).
Die in den letzten Jahren von der Werkzeugmaschinenfabrik VEB WERKÖ König see entwickelten Bohraggregate erreichen unter Berücksichtigung des robusten Gru benbetriebes gute Leistungen. Sie zeichnen sich durch relativ geringe Masse und ein fache Handhabung aus. Die Hauptdaten der DIN A 1 sind lt. Bedienungsanweisung:
Motorleistung |
2,4 kW |
Spannung |
220 V Drehstrom |
nutzbare Bohrspindellänge |
800 mm oder 1500 mm |
Masse |
etwa 82 kg |
Vorschub |
1360 mm/min |
Bohrspindeldrehzahl |
620 U/min |
An der Weiterentwicklung der Maschinen wird ständig gearbeitet, so daß sich Ab weichungen bestimmter Einzelteile im Laufe kurzer Zeit ergeben können. Alle Bohr maschinen sind in verschiedenartiger Ausführung lieferbar. Die Unterschiede beziehen sich auf die Bohrspindeldrehzahl und demzufolge auf den Vorschub.
Bild 0/1. Schoma einer Bohr maschine, Typ DIN A 1
(1) Spindclkopf, .(2) Umschalter.
(3) Anlaßschalter, (4) Kabel-
Steckkontakt, (5) luftgekühlter
Motor
Pflege und Wartung der Bohrmaschinen sind in jeder Grube ausschlaggebend für die Leistungsfähigkeit der Gewinnungsbetriebspunkte.
Eine Steigerung der Bohrleistungen konnte in den Jahren 1961/62 durch Einführung der Schnellfrequenz-Gesteinsdrehbohrmaschine erzielt werden. Diese Maschine mit der Kurzbezeichnung SFS 1 arbeitet nicht mit der üblichen Normalfrequenz von 50 Hz, sondern mit 200 Hz. Sie besitzt zwei umschaltbare Vorschübe und wird mit Frequenz wandler und entsprechendem Spezialkabel geliefert. Diese zusätzlichen Ausrüstungen komplizieren allerdings den Einsatz dieses Bohrmaschinentyps. Bei einem üblichen Bohrlochdurchmesser von 36 bzw. 37 mm wird bei Verwendung normaler Bohrge stänge und Bohrschneiden ein maximaler Vorschub von 2240 mm/min erreicht. Diese Bohrleistung ist vorher von keinem anderen Gerät erzielt worden.
Die hauptsächlichsten technischen Daten sind:
Motorleistung |
4,5 kW |
Spannung |
220 V Drehstrom |
Frequenz |
200 Hz |
Spindeldrehzahl |
820 U/min |
nutzbare Bohrspindellänge |
1050 oder 1400 mm |
Vorschübe (umschaltbar) |
2240 oder 1760 mm/min |
Masse |
etwa 86 kg |
Auf der Grundlage der SFS 1 ist außerdem eine neue Großlochbohrmaschine entwickelt worden, die ebenfalls mit200 Hz arbeitet. Sie erreicht einen Vorschub von 270 mm/min und wiegt 110 kg.
Zur Bohrausrüstung gehören Bohrgestänge, Bohrschneiden und Spannsäulen.
Das Bohrgestänge hat sich gleichzeitig mit der Entwicklung der Bohrmaschinen eben falls weiter verbessert. Seit mehreren Jahren sind überall Schlangenbohrer mit Nasen zapfenverbindung in Anwendung.
Das Material der Bohrgestänge wird beim drehenden Bohren stark beansprucht. Das vom Bohrer übertragene Drehmoment wechselt in seiner Größe ständig entsprechend dem Wechsel in der Härte des abzubohrenden Gesteins. Dabei haben sich Schlangen bohrer mit dem Schwertprofil besonders bewährt.
Von Bedeutung ist die Differenz zwischen dem Durchmesser der Bohrschneide und dem des Gestänges. Um die Reibung des Gestänges an der Bohrlochwand möglichst gering zu halten, muß der Durchmesser des Gestänges kleiner sein als der der Bohr schneide. Bei den heute üblichen Bohrschneiden von 36 oder 37 mm Durchmesser haben die Bohrgestänge 34 mm Durchmesser. Die Ausführung als Schlangenbohrer ermöglicht einen guten Bohrmehltransport.
Die Gestänge werden als Aufsteckgestänge geliefert und durch Nasenzapfen mitein ander verbunden. Wenn ein Gestänge abgebohrt ist,d.h., wenn das Bohrloch die der Gestängelänge entsprechende Tiefe erreicht hat, wird das neue Gestänge hinten auf gesetzt, so daß die Bohrschneide immer im Bohrlochtiefsten verbleibt.
Die Verbindung zwischen Bohrschneide und -gestänge muß möglichst starr sein. Die Schneide wird mit Zapfen in den ausgehöhlten Hals des Gestänges eingeführt und mit einem Splint befestigt.
Die Bohrschneide hat die Aufgabe, das Salz in Spänen herauszufräsen. Sie muß dabei eine Arbeit leisten, die dem Produkt aus Kraft und Weg entspricht. Die Kraft wird durch den Andruck der Bohrschneide gegen das Bohrlochtiefste bestimmt. Der Weg entspricht dem Durchmesser der Schneide und ihrer Tourenzahl. Die größte Arbeit muß demzufolge von den äußeren Kanten der Bohrschneide verrichtet werden, da von die sen der größte Weg zurückzulegen ist. Der Mittelpunkt der Schneide dreht sich prak-
Bild 0/2. Vorschlodono
Bohrschncldonformcn
tisch auf der Stelle, so daß dort keine Arbeit geleistet wird. Deshalb wird die heute allgemein übliche Bohrschneide mit einer Mittelkerbe geliefert.
Die Arbeit der Bohrschneide besteht jedoch nicht nur im Herausfräsen des Salzge steines. Ein Teil des Minerals muß auch gebrochen werden. Aus diesem Grunde hat man eine Elügelschneide entwickelt, deren Ecken mit Hartmetallplättchen besetzt sind. Diese verlängern die Lebensdauer der Schneiden und ermöglichen neben einem großen Anpreßdruck das Erreichen einer hohen Bohrtemperatur. Hartmetalle sind jedoch stoßund schlagempfindlich. Es sind eisenfreie Metallkarbide aus Wolfram, Titan, Tantal, Molybdän, Vanadium, Kobalt und Kohlenstoff. Derartige Hartmetall plättchen wurden 1927 in die Kaliindustrie eingeführt. Sie werden durch Hartlöten auf den Ecken der Schneiden befestigt. Stumpfe Schneiden können nachgeschliffen werden. Diese Arbeit wird in den Kaliwerken von erfahrenen Schleifern durchgeführt. In neuerer Zeit wurden auch mechanisierte Schleifeinrichtungen konstruiert.
Die Lebensdauer einer Bohrschneide ist wegen des teuren Hartmetallbesatzes wichtig für die wirtschaftliche Entwicklung des Gewinnungsbetriebes. Je nach Härte des ab zubohrenden Salzes können mit einer Schneide 1200 bis 1800 Bohrmeter erreicht werden, wobei bis zu 30 neue Anschliffe möglich sind. Beim Bohren im Anhydrit oder im harten Polyhalit bzw. Langbeinitsinkt die Lebensdauer einer Bohrschneide erheb lich, in äußersten Fällen bis auf unter 100 Bohrmeter herab.
Bild 6/2 zeigt die wichtigsten Bohrschneidenformen mit den dazugehörigen Schnitt winkeln.
Zum Zubehör des Bohrbetriebes gehört außerdem die Spannsäule (Bild 6/3). Sie be steht in der Hauptsache aus zwei ineinander verschiebbaren Rohren. Diese können auf die erforderliche Länge ausgezogen werden. Die Mindestlänge bzw. -höhe der Spannsäule beträgt 1,50 m. Die Normalausführung ist bis 2,25 m ausziehbar. Um die Masse niedrig zu halten und so die Handhabung zu erleichtern, stellt man die Spann säulen aus Leichtmetallverbindungen her.
Die Spannsäulen sind grundsätzlich besonders in der Firste gut festzuziehen. Vor heriges einwandfreies Berauben ist Voraussetzung für eine unfallfreie Bohrarbeit.v
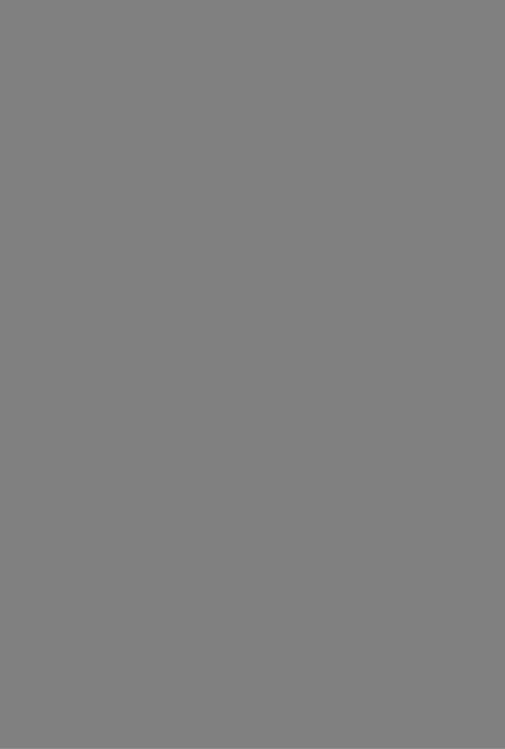
1)11(1 0/5. Drücken der steilen Firste hinter dem Vortrieb (nach Spackelcr)
(1)Vortrieb (Einbruch), (2) steile Firste im Kalilagcr, (3) angebautc Bank,
(4)Decksteinsalz oder grauer Salzton
Bei beiden Bohrmethoden wird zunächst mit dem Fächerschießen der sogenannte Vortrieb von 2,5 bis 3 m Höhe hereingewonnen. Danach werden hinter dem Vortrieb Bohrlöcher zum Abschießen der Firste angesetzt. Beim Drücken der steilen Firste, das in Bild 6/5 nach dem Beispiel einer Südharzgrube dargestellt ist, wird in einer be stimmten Entfernung hinter dem Vortriebsort das noch anstehende bauwürdige Salz durch schräg nach oben gerichtete, d. h. steile Bohrlöcher abgebohrt und abgeschos sen. Je nach Bauhöhe und Abbaubreite ist dabei auf den richtigen Rhythmus im Ab schießen zwischen den Einbruchslöchern im Fächerschießen und den Firstlöchern zu achten.
Das Drücken der hohen Firste bleibt, von Sonderfällen abgesehen, auf sehr mächtige Lagerstätten (bis zu 15 m) beschränkt. Bei derartigen Mächtigkeiten kann die end gültige Kammerfirste durch schräg nach oben gerichtete Bohrlöcher nach dem Ab schießen nicht mehr beherrscht werden. Da die mächtigen Lagerstättenteile meistens carnallitisch ausgebildet sind und in Carnallitkammern die Steinfallgefahr besonders groß ist, wird die hohe Firste flach, d. h. mit horizontal angesetzten Bohrlöchern ge drückt. Dabei ist im Carnallit noch auf ein sorgfältiges Wölben der gesamten Decke zu achten. Die im Prinzip in Bild 6/6 dargestellte Arbeitsweise des Drückens der hohen Firste ist deshalb umständlich und zeitraubend, weil für die Bohrarbeit ein besonderes Gestell oder Gebrück gebaut werden muß. Voraussetzung für das Drücken der hohen Firste ist ein Magazinieren des Haufwerkes. Auf dem Haufwerk wird das Gestell für die Bohrmaschine aufgebaut.
Bild G/G. Drücken der hohen Firste
Bild 6/7. Fttclicrsntz in einem 10 m breiten Abbau (12 GAngc)
Von den außerordentlich zahl reichen Bohrmethoden, die der Gewinnung in den Abbaukam mern dienen, sollen zwei Sche mata des Fächerschießens aus den 10 m breiten Abbaukam mern des Kaliwerkes „Glück auf“ ausgewählt und beschrie ben werden.
Die Ortsbelegung imVEB Kali werk „Glückauf“ , Sondershau
5 m
sen, arbeitet nach einem Orts- paß. Im Ortspaß findet der Hauer schriftliche Angaben über die für seinen Betriebspunkt und seine Arbeit maß
gebenden Bedingungen vor. Hierzu gehören die geologischen Verhältnisse, die Techno logie der Gewinnung und Abförderung, die Aufzählung der zum Einsatz kommen den Arbeitsaggregate, vor allem aber die Aufzählung der Kennziffern des Arbeits ortes, wie Förderplan, d. h. Fördersoll je Schicht und Monat, Sprengstoffverbrauch, Bohrschneidenverbrauch usw.
Ein normaler Fächersatz in einem 10 m breiten Abbau ist in Bild 6/7 dargestellt. Fol gende Kennziffern und Einsatzbedingungen sind gegeben:
Aus den 12 Gängen ergeben sich 120 bis 140 Bohrmeter/Tag; anfallendes Haufwerk aus dem Vortrieb 110 t/Tag.
Vortrieb |
2m |
Sprengstoffverbrauch |
500 bis 560 g/t |
Belegung |
1 Hauer, 1 Lehrhauer, 1 Schrapperfahrer |
Einsatzbedingungen |
einfallender Abbau, läpger Anmarschweg, ver |
|
worfene Lagerstätte |
Maschineneinsatz |
1 oder 2 DIN A l |
Bohrund Schießschema |
|
1. und 2. Gang |
4 Loch übereinander |
3. bis 12. Gang |
3 Loch übereinander |
Für Gang 1 |
7 Patronen Donarit I und |
|
5 Patronen Donarit II |
Für Gang 2 |
8 Patronen Donarit I und |
|
6 Patronen Donarit II |
Für Gang 3 |
9 Patronen Donarit I und |
|
6 Patronen Donarit II |
Für Gang 4 |
10 Patronen Donarit I und |
|
6 Patronen Donarit II |
Für Gang 5 |
11 Patronen Donarit I und |
|
7 Patronen Donarit II |
Für Gang 6 bis 12 |
11 Patronen Donarit I und |
|
8 Petronen Donarit II |
Die Schlagpatrone, d. h. die Patrone mit eingeführter Sprengkapsel, ist die vorletzte Patrone.
Bei guten Einsatzbedingungen (söhliger Abbau, gute Wetterführung, nicht zu langer Anmarschweg) kann die kombinierte Fächer-Großlochschlitzmethode angewandt wer den (Bild 6/8). Bei 10 m Abbaubreite ergeben sich folgende Kennziffern:
Anfallendes Haufwerk |
220 t/Tag |
Abbaufortschritt |
4 m/Tag |
Bohrmeter im Vortrieb |
220 bis 250 m, |
|
dazu 30 bis 40 Großlochbohrmeter |
Sprengstoffverbrauch |
450 bis 550 g/t |
Belegung |
2 Hauer, 1 Lehrhauer, 1 oder 2 Schrapper |
|
fahrer (je nach Abbauhöhe, die durch Drücken |
Geräteeinsatz |
der flachen Firste hereingewonnen wird) |
2 SFS |
|
|
(Schneilfrequenzmaschinen normal) |
|
1 SFG |
Bohrund Schießschema |
(Großloch-Schnellfrequenzmaschine) |
|
|
1. Gang |
5 Löcher übereinander |
2. bis 5. Gang |
4 Löcher übereinander |
6. bis 15. Gang |
3 Löcher übereinander |
Großlochschlitz |
9 oder 10 Löcher übereinander |
Für Gang 1 |
Durchmesser je 165 mm |
20 Patronen Donarit I |
|
Für Gang 2 bis 5 |
2 bis 4 Patronen Gelatine-Donarit und |
Für Gang 6 bis 15 |
5 bis 7 Patronen Donarit I |
kombiniert Donarit I und II mit Gelatine- |
|
|
Donarit je nach Salzart |
Bei beiden Beispielen bezieht sich die Menge des anfallenden Haufwerkes nur auf den im Fächersatz abgebohrten Vortrieb, wie folgende Rechnung für die zuletzt beschrie bene Gewinnungsmethode (s. Bild 6/8) beweist^
Vortrieb X |
Breite X |
Höhe |
X |
Dichte = |
anfallende Salzmenge in t |
4 X |
10 X |
2,5 X |
2,2 |
= |
2201 |
Zu dieser Menge kommt das vom Firstedrücken stammende Salz hinzu. Wenn über dem Vortrieb noch 5m bauwürdiges Lager anstehen (vgl. Bild 6/5) und davon im täglichen Abbau fortschritt 2m hereingewonnen werden, ergibt sich einGesamt anfall von 220 t aus dem Vor trieb + 2 X 5 X 10 X 2,2 aus der Firste = 440 t/Tag
Bild 0/8. Komblnlorto
FüchorGroOlochBChlltzmothodo
Im 10 m breiton Abbau (15 GAngo)
aus einem Gewinnungsbetriebspunkt im Abbau. Diese Menge muß das nachgeschal tete Abbaufördermittel bewältigen!
Ein 200 m langer Abbau mit 7,5 m gewinnbarer Bauhöhe enthält demnach insgesamt 200 X 10 X 7,5 X 2,2 = 33000 t förderfähiges Rohsalz.
6.1.3.Schießund Zündmittcl
Auf eine allgemeine Beschreibung der Sprengstoffe und Zündmittel, ihre Handhabung, ihren Transport und die Lagerung kann hier unter Hinweis auf das Kapitel IX der „Allgemeinen Bergbaukunde“ verzichtet werden. Das dort vermittelte Wissen wird für das Verständnis der folgenden Ausführungen vorausgesetzt.
Allein die Tatsache, daß im Kaliund Steinsalzbergbau der DDR jährlich mehrere Millionen Kilogramm Sprengstoff in der Gewinnung und Streckenauffahrung ver braucht werden, beweist die besondere Bedeutung der Bohrund Schießarbeit als beherrschendes Gewinnungsverfahren. In der Gegenwart und in der nahen Zukunft wird sich an dieser Tatsache kaum etwas ändern. Da die Sprengstoffund Zündmittel kosten bei der Gewinnung einen ganz wesentlichen Anteil an den entstehenden Selbst kosten einer Grube ausmachen, ist ein ökonomischer Einsatz der im Kali -und Stein salzbergbau benutzten Sprengstoffe wichtigste Voraussetzung für eine wirtschaftliche Betriebsführung unter Tage.
Im Gegensatz zu anderen Bergbauzweigen muß im Kaliund Steinsalzbergbau jeder Hauer auch als Schießhauer tätig sein. Seine Ausbildung, die auf die Gewinnung der Kalirohsalze ausgerichtet ist, wird also zu einem wesentlichen Teil von der richtigen und in sicherheitlicher Hinsicht einwandfreien Handhabung der Sprengstoffe und Zündmittel bestimmt.
Jeder, der mit Sprengstoff umgeht, muß neben güten fachlichen Voraussetzungen langjährige Erfahrungen besitzen. Er muß mindestens das 18. Lebensjahr vollen det haben.
In den Kaliund Steinsalzgruben werden Gesteinssprengstoffe und in geringem Um fang Pulversprengstoffe verwendet. Die in der Hauptsache zum Einsatz kommenden Gesteinssprengstoffe sind Donarit I und II und Gelatine-Donarit. Der Patronendurch messer beträgt generell 28 und 30 mm, in Sonderfällen 25 mm.
Der Gelatine-Donarit enthält neben Sprengöl zusätzlich etwa 10% Nitrokörper und einen entsprechenden Anteil an Ammonsalpeter. Diesen brisanten Gesteinsspreng stoffbenutzt man seit einigen Jahren besonders in der Ausund Vorrichtung, um die Vorgaben zwischen den einzelnen Gängen erhöhen zu können.
Bei Donarit I ist der Anteil an Hitrokörpern geringer als bei Gelatine-Donarit. Bei Donarit II wird die Brisanz durch einen Zusatz von Sägemehl weiter herabgesetzt. Bei den einzelnen Schießmethoden hat sich unter Berücksichtigung der jeweiligen SalzVerhältnisse eine Kombination in der Verwendung von Donarit I und II in viel gestaltigen Variationen durchgesetzt.
Die Pulversprengstoffe haben in den letzten 20 Jahren im Salzbergbau an Bedeutung verloren. Sie sind nicht sehr handhabungssicher und werden nur in besonderen Fällen nach Genehmigung durch die Bergbehörde zum schonenden Wölben von Carnallitfirsten benutzt.
Das Zünden der Schüsse erfolgt bei allen Gesteinssprengstoffen über eine Initialzün dung mit Zündschnur oder durch elektrische Fernzündung.
Die Initialzündung ist erforderlich, um den handhabungssicheren Sprengstoff tat sächlich zur Detonation zu bringen. Die im Kalibergbau allein übliche Spreng-
Bild 0/0. Aufbau dcB Brückonzündors A
(1) Zünderdraht, (2) Metallstreifen mit Durchboh rungen, (3) Ccllonmasse, (4) Mctallstreifen,
(5) Glühdraht. (6) Zündsatz
kapsel Nr. 8 besteht aus Knallqueck silber oder häufiger aus Bleiazid ir Aluminiumkapseln.
Achtung: Vorsicht beim Anklemmen der empfindlichen Sprengkapseln auf die Zünd schnur; nur die vorgeschriebene Zange benutzen !
Die geteerte Zündschnur mit der aus Schwarzpulver bestehenden Pulverseele brennt mit einer Geschwindigkeit von einem Meter in 2 Minuten.
Achtung: Die kürzeste Schnur muß mindestens 1,50 m lang sein!
Zum Zünden der Zündschnur von Hand darf nur das Zündlicht verwandt werden. Mit ihm wird die freigelegte Pulverseele entzündet. Das Zündlicht brennt eine Minute. Alle Schüsse müssen mit einem einzigen Zündlicht angebrannt werden.
Achtung: Die Verwendung eines zweiten Zündlichtes an einem Arbeitsort ist grund sätzlich verboten !
Während der letzten 10 Jahre hat sich nach folgenschweren Gasausbrüchen in meh reren Bergbaurevieren der Kaliindustrie die elektrische Fernzündung durchgesetzt. In den kohlensäure-gefährdeten Gruben des Werragebietes werden die Schüsse nach Ausfahrt der Belegschaft elektrisch von über Tage aus ferngezündet. Ebenso verfährt man in den schlagwettergefährdeten Gruben des Südharzbezirkes. In einzelnen Be trieben wird die elektrische Fernzündung noch revierweise aus Schießkammern unter Tage vorgenommen.
Der Zündimpuls wird dem Stromnetz der Grube entnommen und in einer gesonderten Schießleitung über Schießverteilungen den Abbauorten zugeführt.
Im Salzbergbau verwendet man allgemein den Brückenzünder A, der auch als Kalizünder bezeichnet wird (Bild 6/9). Beim Zünden glüht der Verbindungsdraht auf; durch die dabei freiwerdende Wärme entzündet sich der leicht brennbare Zündsatz, der wiederum die Pulverseele der Zündschnur in Brand setzt. Für das richtige Arbeiten mit elektrischen Zündern ist eine bestimmte Stromstärke erforderlich, die ungefähr 1 A beträgt (vgl. „Allgemeine Bergbaukunde“ , S. 282).
Achtung: Behandle alle Zünder sorgfältig. Überprüfe die Zündkreise täglich mit demOhm meter !
In den letzten Jahren sind wiederholt Versuche mit Millisekundenzündern (Bild 6/10) angestellt worden. Sie haben Verzögerungen von weniger als 50 ms und ermöglichen die Ausnutzung der gesamten Sprengstoffenergie. Bei Verwendung normaler Zünder detonieren die einzelnen Schüsse in zum Teil erheblichen Zeitintervallen hinterein ander. Das Haufwerk wird je nach dem angewandten Bohrschema in die freie Strecke geschleudert, wobei infolge des gro
ßen zeitlichen Abstands der Schüsse voneinander ein gewisser Teil der
Bild 0/10. Aufbau eines Mlllisckundonzünders
(1) Zünderdrähte,' (2) Zündpillc, (3) Verzögerungs satz, (4) Aufladung, (5) Unterladung, (0) Zeitstufe
Sprengenergie nutzlos verpufft. Die sehr kurzen Verzögerungszeiten der Millisekunden zünder verhindern das. Die gesamte Vorgabe wird nicht nur mehrere Meter vom Stoß weggeschleudert, sondern auch kleinstückiger zertrümmert. Besonders das Wegschleu dern vom Ortsstoß kann bei engen Strecken für den nachfolgenden Schrapperbetrieb von wesentlicher Bedeutung sein.
6.1.4.Zusammenwirken von Bohrund Schießarbeit, Zeitmessungen, Normierung in der Gewinnung
Das reibungslose Zusammenwirken von Bohrund Schießarbeit in der Gewinnung und die sich daraus ergebende optimale Leistung in den einzelnen Abbaukammern ist entscheidend von der Arbeitsorganisation der Gewinnungsbetriebspunkte abhängig.
Die Leistungen im Bohrund Schießbetrieb ergeben sich aus zahlreichen ineinandergreifenden und sich sehr oft wiederholenden Arbeitsgängen. Die wichtigsten sind: Berauben, Freischaufeln des Arbeitsplatzes, Aufund Umstellen der Bohrmaschinen, reine Bohrarbeit, Gestängeund Schneidenwechsel, Sprengstofftransport, Laden und Abtun der Schüsse.
Bei der Beurteilung der tatsächlichen Leistungsfähigkeit eines Gewinnungsbetriebes muß unterschieden werden zwischen den Arbeitsvorgängen, die von den Hauern be einflußt werden können, und den Tatsachen, die auf Grund der geologischen oder mineralogischen Situation als gegeben hinzunehmen sind. Letztere können in jeder Grube nach Art und Bedeutung sehr unterschiedlich sein und müssen im einzelnen untersucht werden.
Die nachstehend aufgeführten Faktoren sind für die Leistung in der Gewinnung ent scheidend :
1. Härte |
I |
|
2. |
Festigkeit und Zähigkeit |
J- des Salzgesteins |
3. |
Dichte |
J |
4.Mächtigkeit
5.Einfallen oder Ansteigen
6. Tektonik |
des Kalilagers |
7.Gasoder Laugeneinschlüsse
8.Abbauverfahren
9.Abbauquerschnitt
10.Einfluß der unmittelbaren Liegendbzw. Hangendschichten
11.Bohrschema mit Bohrlochlänge und -neigung
12.Absetzen 1 der Bohrlöcher
13.Vorgabe J
14.Art und Leistungsfähigkeit (Vorschub) der Bohrmaschine
15.Art und Anschliff der Schneiden
16.Länge der Anund Ausfahrwege
17.Wetterführung und Temperatur vor Ort
18.Ortsbelegung
19.Sprengstoffart
20.Art der Zündung
21.Schießmethode (kombiniertes Schießen, Hohlraumschießen)
Die genannten Faktoren müssen je nach den gegebenen örtlichen Verhältnissen er gänzt werden.
Die geologischen Verhältnisse (Punkt 1 bis 7) müssen als gegeben hingenommen wer-