
книги / Металлургические технологии
..pdfэлектродной промышленности, появление новых шихтовых материа лов (например, прямовосстановленного губчатого железа) привели к созданию новых мощных дуговых печей большой емкости, предна значенных для производства низколегированных и углеродистых сталей массового использования.
Все более широко используются приемы, позволяющие сущест венно сократить длительность плавки: предварительный подогрев шихтового скрапа отходящими газами, использование двухкорпус ных дуговых печей, ведение плавки с так называемым «жидким стар том», когда небольшую часть металла от предыдущей плавки остав ляют в печи. Последний прием оказался особенно перспективным
вслучае использования в качестве основного компонента шихты металлизованных окатышей.
Еще одним весьма перспективным приемом является использо вание модуля «дуговая печь постоянного тока - конвертер», соче тающего преимущества дуговой печи постоянного тока и кислород ного конвертера. Такой модуль позволяет увеличить долю скрапа
вконвертере до 10 0 % при одновременном повышении качества вы плавляемых сталей и без снижения производительности конвертера.
Успешно решается проблема использования смешанного скрапа, содержащего остатки пластмасс, наличие которых в шихте является причиной появления в составе отходящих газов крайне токсичных соединений: диоксинов и фуранов.
Таким образом, в ближайшие годы доля электростали в общей доле ее мирового производства будет увеличиваться.
ГЛАВА 9. Дуплекс-процессы
Дуплекс-процессы - это двухстадийные процессы, при которых выплавка сталей осуществляется последовательно в двух агрегатах. Агрегаты могут быть как одинаковыми, так и различными. Называют дуплекс-процессы следующим образом: сначала указывают агрегат, используемый на второй стадии, а затем агрегат, используемый на первой стадии, например: «кислородный конвертер на кислородный
конвертер» или «дуговая электропечь на кислородный конвертер», т.е. в первом случае процесс на обеих стадиях ведут в кислородных конвертерах, а во втором случае на первой стадии используют ки слородный конвертер, а на второй - дуговую электропечь.
Ниже приведены некоторые примеры использования дуплекспроцессов.
9.1. Дуплекс-процесс «кислая мартеновская печь
на основную мартеновскую печь»
Известно, что удаление фосфора и серы возможно только в агрегатах с основной футеровкой, однако в кислых печах возможно получение проч ных неметаллических включений наиболее благоприятной - сферической формы, которые не деформируются при обработке давлением, сохраняя свою сферическую конфигурацию. Поэтому на первой стадии в основной мартеновской печи получают жидкий полупродукт с минимально возмож ным содержанием фосфора и серы (не более 0,0 1 .. .0,02 %), затем полупро дукт выпускают в ковш и переливают в мартеновский агрегат с кислой фу теровкой, где и проводят выплавку кислой стали с неметаллическими включениями сферической формы. Если необходимо обеспечить еще меньшее содержание фосфора и серы, проводят дуплекс-процесс «кислая мартеновская печь на основную дуговую электропечь».
9.2. Дуплекс-процессы для переработки
природно-легированных чугунов
Довольно часто железные руды содержат оксиды полезных эле ментов, таких как ванадий, хром, марганец и др. В результате домен ной плавки эти примеси восстанавливаются и переходят в чугун. Технологиями, позволяющими выплавить сталь и одновременно от делить эти полезные примеси для последующего производства фер росплавов, являются дуплекс-процессы. Примером такой технологии может служить используемый на ОАО «Нижнетагильский металлур гический комбинат» (НТМК) дуплекс-процесс «основной кислород ный конвертер на основной кислородный конвертер».
В доменных печах ОАО НТМК получают ванадиевый чугун сле дующего среднего состава: 4,4...4,8 % С; 0,40...0,55 % V; 0,15...0,40% Si; 0,20...0,55 % Мл; 0,10...0,35 % Ti; менее 0,045 % S и менее 0,01 % Р. Этот чугун заливают в первый конвертер и ведут продувку кислородом. Главная задача - окислить ванадий и перевести его в шлак:
4[V] + 50!, = 2(V20 5).
Для поддержания в конвертере относительно низких температур, необходимых для успешного протекания процессов окисления ванадия, во время продувки в конвертер присаживают чушковый ванадиевый чугун. Длительность продувки 6 ... 10 мин. Одновременно с ванадием окисляются и другие примеси: кремний, марганец, а также и небольшая часть углерода В результате плавки в первом конвертере получают жидкий полупродукт состава: 2,7 ...3,2 % С; менее 0,04 % V и ванадие вый ш лак18...25 % V2O5; 12...18 % Si0 2 ; 3...5 % Сг20з; FeO - осталь ное. Полупродукт через летку выпускают в ковш и переливают во вто рой конвертер, в котором ведут продувку до получения стали с задан ным содержанием углерода. Слитый в шлаковую чашу ванадиевый шлак отправляют в специальный цех для производства феррованадия.
На ОАО «Чусовской металлургический завод» с этой же целью используют дуплекс-процесс «основная мартеновская печь на бессе меровский конвертер».
9.3. Дуплекс-процесс «кислородный конвертер
на дуговую электропечь»
Этот процесс получил достаточно широкое распространение, по скольку позволяет получать низкоуглеродистую сталь с высоким со держанием хрома (типа 03X18Н9) при использовании дешевого вы сокоуглеродистого феррохрома. Традиционный способ выплавки таких сталей в дуговой электропечи требует применения дорогого низкоуглеродистого феррохрома.
На первой стадии в дуговой электропечи выплавляют легирован ный хромом и никелем углеродистый полупродукт с содержанием углерода 1,3... 2,5 %.
Вторая стадия этого процесса - окончательная выплавка стали в специальном конвертере с нижней аргонокислородной продувкой получила название AOD-процесс (Argon-Oxygen Decarburization).
Полупродукт вместе со шлаком переливают в конвертер, устрой ство которого показано на рис. 9.1. Конвертер продувают аргоно кислородной смесью через сопла, расположенные в стенке у днища. Сопла состоят из центральной трубы для подачи аргонокислородной смеси и наружной трубы, по которой подают аргон для охлаждения сопла. Футеровка конвертера - смолодоломитовая.
Рис. 9.1. Общее устройство аргонокислородного конвертера: 1 - со пло для подачи аргонокислородной смеси; 2 - смолодоломитовый кирпич высокого качества; 3 - обожженный смолодоломитовый кир пич; 4 - обожженный доломитовый кирпич; 5 - смолодоломитовая набивная масса
Продувка делится на два периода. Первый период - окислитель ный. Во время этого периода происходит окисление примесей (леги рующих добавок) и углерода. Перед началом продувки в конвертер загружают охладители: стальной лом и легирующие добавки. Про
дувку ведут аргонокислородной смесью переменного состава: в на чале продувки соотношение расхода кислород/аргон равно 3:1. По мере уменьшения содержания углерода в жидком металле долю ар гона постепенно увеличивают. Заканчивают окислительный период при соотношении кислород/аргон как 1:2. Длительность периода примерно 70 мин.
Когда содержание углерода в металле снизится до 0,03...0,04 %, начинается восстановительный период: отключают подачу кислоро да, продолжая продувку аргоном. Кроме того, в конвертер вводят известь и ферросилиций, который необходим для восстановления хрома, окислившегося и перешедшего в шлак во время окислитель ного периода. Продувка аргоном длится около 5 мин. За это время кремний восстанавливает из шлака до 95 % хрома. Продувку аргоном останавливают. Шлак, содержащий повышенное количество Si02, сливают и наводят свежий шлак, вводя известь и плавиковый шпат. При возобновлении аргоновой продувки в свежий шлак переходит до 95 % содержащейся в жидком металле серы. Длительность повтор ной продувки аргоном длится не более 3...5 мин. Общая длитель ность обработки в AOD-конвертере не превышает 90 мин.
ГЛАВА 10. Технологии получения сталей
высокого и особо высокого качества
Быстрое развитие современной техники предъявляет все более высокие требования к качеству сталей. Для целого ряда изделий авиационной и космической техники, для конструкций и деталей, работающих в условиях Крайнего Севера, для радиоэлектронной и приборостроительной техники требуются стали и сплавы с гаран тированным отсутствием макродефектов, однородные по составу и свойствам, содержащие в своем составе чрезвычайно низкие коли чества нежелательных примесей.
Качество сталей, выплавленных в обычных сталеплавильных аг регатах - конвертерах, дуговых электропечах, мартеновских печах, этим требованиям не соответствует. Поэтому во второй половине
XX века получили развитие приемы и технологии, способные обес печить особо высокое металлургическое качество сталей и сплавов.
Эти способы можно разбить на две группы: специальная элек трометаллургия (переплавные процессы) и ковшовая металлургия (или внепечная обработка жидких сталей). Теоретические основы этих способов изложены в главе 4.
10.1. Ковшовая металлургия
Все разработанные на сегодняшний день методы ковшовой ме таллургии по их функциональной направленности можно разделить на 4 основные группы:
1 ) методы перемешивания жидкого металла с целью усреднения температуры и химического состава;
2 ) методы введения порошковых реагентов, раскислителей и ле гирующих микродобавок;
3)вакуумная обработка жидких сталей и сплавов;
4)методы комплексной обработки на установках «ковш-печь».
10.1.1. Методы перемешивания
Перемешивание жидких сталей при продувке аргоном или азо том является простым, дешевым и поэтому самым распространен ным способом внепечной обработки (рис. 10.1). Они позволяют про водить гомогенизацию жидких сталей, удалять до 10... 15 % водоро да и неметаллических включений, а также активизировать обменные процессы между металлом и шлаком.
Продувку металла в ковше инертным газом проводят с помощью фурмы, опускаемой сверху (рис. 1 0 .1 , а), либо через фурмы, распо ложенные тангенциально в днище ковша, либо через пористые проб ки, швы и вставки, устанавливаемые в днище ковша (рис. 1 0 .1 , б). В последние годы метод продувки металла инертным газом получил дальнейшее развитие на заводах японской фирмы Nippon Steel Corpo ration. Для защиты металла от окисления, повышения усвояемости раскислителей и легирующих добавок и точной корректировки хи мического состава сталь покрывают слоем синтетического шлака.
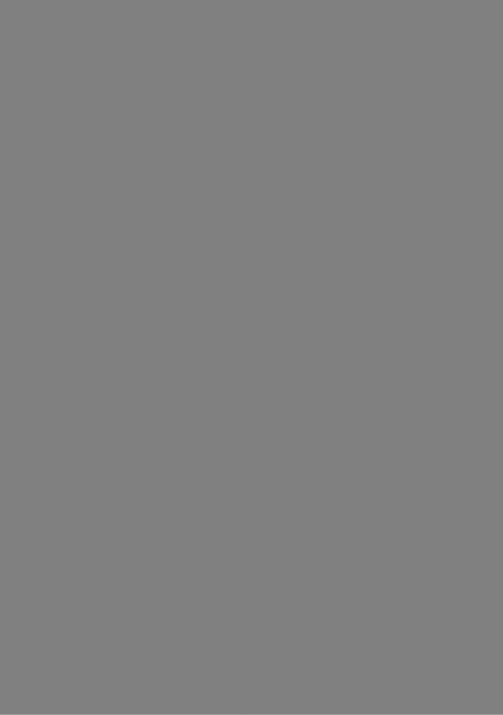
Вдувание смеси порошкообразных материалов (фракция до 2 мм) CaO-FeO-CaF2 в струе инертного газа позволяет проводить глубокую дефосфорацию. Для эффективной десульфурации жидкую сталь под слоем низкоокисленного шлака продувают смесью СаОAl20 3 -CaF2 в струе аргона (рис. 10.2, а).
а б е г
Рис. 10.2. Методы введения порошкообразных реагентов, раскислителей и микролегирующих добавок: а - вдувание порошков; б - введение полой проволоки; в - выстреливание пуль; г - погружение в жидкую сталь в кон тейнере; 1 - контейнер; 2 - трайб-аппарат; 3 - пневматическая пушка;
4 - штанга; 5 - закрытый контейнер
Перспективным способом введения порошкообразных материа лов является введение их в жидкую сталь внутри тонкостенной труб ки с помощью трайб-аппарата (рис. 10.2, б). Этот метод, называемый CW (Cored Wire), обладает следующими преимуществами по сравне нию с вдуванием порошков в струе инертного газа: стальная оболоч ка защищает реагенты от окисления во время хранения и транспор тировки, предохраняет их от окисления при прохождении через слой шлака, позволяет точно дозировать количество добавок и вводить их на определенную глубину. Одновременно с введением добавок сталь продувают аргоном снизу.
В качестве наполнителей для десульфурации используют не только кальцийсодержашие соединения, но и микролегирующие до бавки, позволяющие с высокой точностью регулировать содержание в сталях алюминия, титана, бора, углерода и других элементов. Про
волоку с добавками можно вводить не только во время внепечной обработки, но и в процессе непрерывной или сифонной разливки.
Несколько меньшее распространение в практике внепечной об работки сталей получил способ введения компонентов путем вы стреливания капсул пневматической пушкой в глубь жидкого метал ла (рис. 10.2, в). Подобный способ, разработанный в Японии, полу чил название ABS (Aluminium Bullet Shooting).
Еще одним способом введения активных реагентов в жидкую сталь является погружение их в ковш в закрытом контейнере на фу терованной штанге (рис. 1 0 .2 , г).
10.1.3. Вакуумная обработка
Вакуумная обработка жидких сталей получает все большее рас пространение: только за последние 10 лет на металлургических заво дах мира введено в действие более 80 новых установок для вакуум ной обработки общей производительностью 62 млн т/год. По прогно зам в 2010 году до 30 % всех выплавляемых сталей в мире сталей будет подвергаться вакуумной обработке.
Вакуумная обработка при снижении давления в камере до 0,1... 1,0 кПа обеспечивает глубокое обезуглероживание (до 0,01 %) и раскисление, снижение содержания водорода до 1 ppm (ppm - part per million - число атомов примеси на миллион атомов железа), уменьшение доли неметаллических включений, гомогенизацию по температуре и химическому составу, точное легирование при высо кой степени усвоения вводимых компонентов.
Все методы вакуумирования можно разделить на три группы:
1 ) струйное вакуумирование при выпуске металла из сталепла вильного агрегата в ковш, при переливе из ковша в ковш, при раз ливке в изложницы или при непрерывной разливке;
2) вакуумирование в ковше с одновременным электромагнитным перемешиванием или продувкой инертным газом;
3) вакуумирование порций металла вне ковша в вакуум-камере. Струйное вакуумирование (рис. 10.3) применяют при разливке в из
ложницы слитков большой массы (до 500 т и более) для поковок ответст-
венного назначения (коленчатых и гребных валов океанских судов, рото ров турбин, прокатных валков большого диаметра). Перспективным яв ляется разработанный в России метод поточного вакуумирования сталей при непрерывной разливке (рис. 10.4). Метод позволяет снижать содер жание водорода, кислорода и долю неметаллических включений в струе металла в вакуумной камере, расположенной над промежуточным ков шом установки непрерывной разливки сталей.
Рис. 10.3. Схема струйного вакуу |
Рис. 10.4. Поточное вакуумирова |
мирования: 1 - вакуумная камера |
ние стали при непрерывной разлив |
|
ке: 1 - сталеразливочный ковш; 2 - |
|
вакуум-камера; 3 - промежуточный |
|
ковш; 4 - кристаллизатор |
Вакуумирование сталей при выпуске из печи и при переливе из ковша в ковш не получило широкого распространения вследствие значительного охлаждения металла (на 40...90 °С).
Вакуумирование в ковше, помещенном в специальную вакуумную ка меру или закрытом герметичной крышкой, является наиболее простым способом вакуумной обработки жидкого металла (рис. 10.5). Такой обра ботке чаще подвергают нераскисленную сталь, в которой в результате ин тенсивного кипения, содержание водорода и кислорода может быть сни жено до 3 ppm. Для повышения эффективности вакуумирования применя