
книги / Металлургические технологии
..pdfОксид металла-раскислигеля, образующийся в ходе реакции, будет «выпадать в осадою). Поскольку плотность жидкой стали больше, чем плотность любого соединения, входящего в состав шлака, то для случая сталеплавильного агрегата «выпасть в осадок» означает «всплыть в шлак».
В большинстве случаев раскислители подают в ковш во время выпуска готовых сталей. Непосредственно после выпуска следует операция разливки стали по изложницам. Естественно, что во время выпуска и, тем более, разливки температура стали снижается.
Анализ температурной зависимости AG свидетельствует о том, что по мере снижения температуры вероятность протекания реакции глубинного раскисления в прямом направлении увеличивается. Дру гими словами, в процессе выпуска и, особенно, разливки в жидкой стали появляются все новые порции оксида (МеО). Оксиды, образо вавшиеся в изложнице одновременно с протеканием процесса кри сталлизации, могут по различным причинам не успеть всплыть в при быльную часть, остаются в теле стального слитка и загрязняют сталь.
Таким образом, глубинное раскисление является наиболее про стым и дешевым способом раскисления и поэтому широко использу ется при производстве сталей обыкновенного качества и качествен ных сталей. Однако вследствие загрязненности стали оксидами, об разовавшимися в процессе раскисления, данный способ неприемлем для окончательного раскисления сталей высокого качества.
4.6.2. Диффузионное раскисление
Данный способ раскисления основан на законе Нернста, который гласит: «Отношение активностей (или концентраций) примеси, рас пределенной между двумя фазами, при данных условиях есть вели чина постоянная».
По отношению к кислороду, распределенному между шлаком и жидким железом, данный закон запишется так:
(FeO) = const при Р9Т= const. [О]
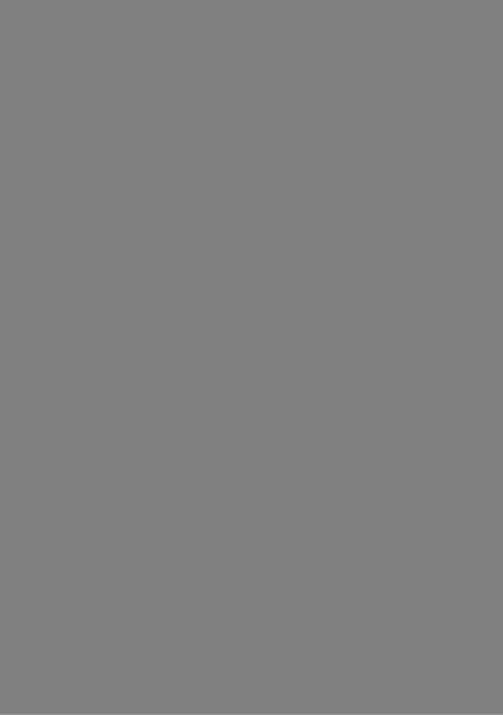
Раскисление синтетическим шлаком (СШ) является разновидно стью диффузионного раскисления. Способ заключается в следую щем: одновременно с выплавкой стали в другом плавильном агрегате готовят СШ, не содержащий оксида железа, т.е. шлак, окисленность которого равна нулю. Готовую жидкую сталь выпускают в один ста леразливочный ковш, а СШ - в другой такой же ковш. Затем сталь постепенно переливают в ковш с СШ.
При ударе о слой СШ жидкая сталь разбивается на капли, кото рые начинают просачиваться сквозь слой шлака. В условиях, когда объем раскисляемого металла уменьшается до капли, а в окружаю щем эту каплю шлаке отсутствует химически активный кислород, процесс диффузии кислорода из жидкой стали в шлак протекает с очень высокой скоростью, и, пока стальная капля просачивается сквозь слой СШ, она успевает «отдать» ему весь свой кислород.
Обладая преимуществом диффузионного раскисления, данный способ является экономичным, поскольку не приводит к снижению удельной производительности сталеплавильного агрегата, и поэтому в настоящее время широко используется предприятиями металлур гической отрасли.
Кроме того, обработка СШ - это универсальный процесс, позво ляющий удалять из жидкой стали не только кислород. Действитель но, если приготовить низкоокисленный шлак с высокой основно стью, то обработка жидких сталей таким СШ при высоких темпера турах позволит удалить серу, а обработка металла СШ с высокой окисленностью и высокой основностью при относительно низких температурах обеспечит удаление фосфора.
4.6.4. Вакуумно-углеродное раскисление
Данный способ основан на раскисляющем действии углерода, растворенного в жидком металле. Запишем реакцию окисления угле рода, растворенного в жидком металле кислородом, растворенным в жидком металле, а также - константу данной реакции:
[С] + [0] |
cor, fr — Pco |
|
p [C]-[0]’ |
Очевидно, что уменьшение парциального давления угарного газа приведет к смещению реакции вправо - к уменьшению концентра ции исходных веществ, в том числе кислорода в жидком металле.
Для того чтобы реализовать этот способ раскисления, необходи мо герметизировать агрегат или ковш со сталью, а затем начать от качку газов из объема над ванной. Однако технически реализовать этот технологический прием достаточно сложно и дорого. В связи с этим в предыдущие десятилетия данный способ раскисления исполь зовался редко и только при выплавке сталей особо высокого качест ва. В настоящее время доля сталей, подвергаемых вакуумно углеродному раскислению, существенно увеличилась, и к 2010 году доля сталей, обрабатываемых этим способом, достигла 30 % (в эко номически развитых странах).
4.7. Легирование сталей
Легирование - это технологическая операция введения в жидкую сталь легирующих элементов.
Легирующие элементы - это химические элементы, чаще - ме таллы, специально вводимые в сталь для направленного изменения ее структуры и свойств.
По химическому составу принято делить все стали на нелегиро ванные (углеродистые) и легированные. Легированные стали - это стали, содержащие в своем составе легирующие элементы; соответ ственно, нелегированные стали - это те, которые не содержат в со ставе легирующих элементов.
Металлургу-сталеплавильщику важно знать поведение леги рующих элементов при выплавке сталей для того, чтобы выплавить сталь нужного состава с минимальными потерями легирующих эле ментов. Вот почему главная проблема легирования - избежать взаи модействия легирующих элементов с кислородом и свести процессы их окисления к минимуму. Процесс окисления легирующих элемен
тов и их переход в виде оксидов в шлак металлурги называют «угар», поэтому кратко можно сказать, что главная проблема легирования - минимизация угара легирующих добавок.
В зависимости от степени химического сродства к кислороду все легирующие элементы металлурги делят на две группы. В первую группу входят легирующие элементы, сродство к кислороду которых меньше, чем у железа. К ним относятся никель (Ni), кобальт (Со), медь (Си), молибден (Мо). В условиях выплавки и разливки сталей легирую щие элементы первой группы не окисляются и, следовательно, могут быть введены в сталь в любой удобный для металлурга момент плавки.
Ко второй группе относятся легирующие элементы, химическое сродство которых к кислороду больше, чем у железа. Сюда можно отнести такие элементы, как марганец (Мл), хром (Сг), вольфрам (W), ванадий (V), ниобий (Nb), титан (Ti), кремний (Si), алюминий (А1). Исходя из принципа минимизации угара, легирование элемен тами второй группы проводят либо после раскисления, либо одно временно с раскислением. Общий принцип введения легирующих элементов второй группы таков: чем выше сродство данного элемен та к кислороду, тем позднее он вводится в жидкую сталь.
Легирующие добавки могут вводить в сталь в чистом виде, на пример, так вводят медь, алюминий, никель. Чаще всего легирующие элементы вводят в жидкую сталь в виде сплавов с железом - ферро сплавов. Так вводят марганец, хром, ванадий, титан, кремний и многие другие элементы. Некоторые элементы вводят в виде соединений, ча ще - окислов: ванадий в виде пятиокиси ванадия V2O5, марганец в ви де марганцевой руды, молибден в виде молибдата кальция и др.
Иногда для легирования (и раскисления) используют экзотерми ческие брикеты, которые помещают в сталеразливочный ковш перед выпуском в него жидкой стали. В состав таких брикетов входят по рошкообразные раскислители и восстановители (алюминий или маг ний), окислители (селитра), шлакообразователи, а также соединения, в состав которых входят легирующие добавки (оксиды хрома, окси ды марганца)-
Под действием высоких температур окислители и восстановите ли реагируют между собой, при этом выделяется определенное коли чество тепла. Шлакообразующие добавки обеспечивают получение неметаллических включений, обладающих свойством несмачиваемости и поэтому быстро всплывающих в шлак. Одновременно проис ходит восстановление легирующих элементов и растворение их в жидкой стали. Правильный подбор состава брикетов позволяет эко номить достаточно дорогие легирующие добавки.
4.8. Неметаллические включения в сталях
Неметаллические включения (НВ) - это содержащиеся в сталях соединения металлов с неметаллами. Неметаллические включения в большинстве случаев оказывают отрицательное влияние как на ме ханические (прочность, пластичность, ударная вязкость), так и на физико-химические свойства сталей (электропроводность, магнитная проницаемость, сопротивление коррозии и т.д.). В связи с этим уменьшение объемной доли НВ и управление характером распреде ления, формой и размерами НВ - важная задача, стоящая перед ме таллургами.
Согласно классификации, предложенной А.А. Байковым, все НВ по их происхождению можно разделить на два вида:
1)НВ, возникающие в результате химических реакций, проте кающих при производстве сталей. Такие НВ называют эндогенными. Типичным примером эндогенных НВ являются оксиды, возникаю щие в результате глубинного раскисления;
2)НВ, попадающие в сталь в готовом виде. Такие НВ называют экзогенными. Типичный пример экзогенных НВ - это частицы непереработанной шихты, кусочки попавшей в сталь футеровки.
Указанные виды НВ могут взаимодействовать между собой, об разуя комплексные соединения.
Неметаллические включения в зависимости от их химического состава принято делить на сульфиды (FeS, MnS и др.), оксиды (FeO, MnO, Si02, А120 3 и др.) и нитриды (TiN, ZrN и др.).
Очень часто НВ представляют собой сложные соединения типа си ликатов (wFeO-/wMn07?Si02), алюмосиликатов (лМп0*т8Ю2-рА120 3), шпинелей (FeOAl20 3).
Эндогенные НВ образуются в результате взаимодействия рас творенных в жидком металле компонентов или уменьшения их рас творимости при кристаллизации. Плотность всех НВ меньше плотно сти стали, и поэтому они стремятся всплыть в шлак. Скорость всплывания зависит от многих факторов: размеров НВ, вязкости жидкого металла, смачиваемости НВ металлом и шлаком, интенсив ности движения металла и шлака. Количественно скорость всплыва ния можно оценить по формуле Стокса
v = 0,22gr2 -(pMe~ pHB),
Л
где v - скорость всплывания НВ; g - ускорение свободного падения; г - радиус НВ; рМе - плотность жидкого металла, рнв - плотность НВ; г| - вязкость жидкого металла.
Таким образом, быстрее будут всплывать крупные и легкие включения в металле с низкой вязкостью.
На скорость всплывания большое влияние оказывают процессы укрупнения НВ: коагуляция (слипание) и коалесценция (слияние с исчезновением поверхности раздела), так как в соответствии с при веденной формулой скорость всплывания пропорциональна квадрату радиуса частицы НВ.
В случае если дисперсность НВ велика (очень мелкие НВ), силы смачивания на границе «включение - жидкий металл» заставляют их эти включения двигаться вместе с металлом. Иногда включение, дос тигшее шлака, им не смачивается и остается в металле.
Наименее благоприятные условия для удаления НВ создаются в тех случаях, когда эти включения образуются в процессе кристалли зации сталей - по мере снижения температуры вязкость расплава возрастает, а, кроме того, растущие кристаллы препятствуют всплы ванию НВ. В результате часть НВ неизбежно остается в металле. Ти пичным примером являются оксиды, возникающие в процессе глу
бинного раскисления. В данном случае главная задача металлурга - обеспечить такую форму и распределение включений в готовом из делии, которые бы снижали качество металлопродукции в мини мальной степени.
Количество НВ и особенно их размер в различных сталях и даже отдельных плавках могут сильно различаться. Обычно объемная до ля НВ находится в пределах 0,01...0,1 %, а размер - от 10'5 до 10 мм и более. Основная масса НВ имеет размер более 10"3 мм. Экзогенные НВ практически всегда значительно крупнее эндогенных.
Влитых сталях НВ присутствуют либо в виде кристаллов (пра вильная геометрическая форма), либо в виде глобулей (форма, близ кая к сферической).
Врезультате горячей обработки давлением (ковка, штамповка, прокатка) включения изменяют форму и расположение в зависимости от их свойств. Если НВ пластичны при температуре горячей деформа ции, то, независимо от их исходной формы в литом металле, они вытя гиваются в направлении главной деформации и приобретают нитевид ную форму. Так себя ведут сульфиды и силикаты марганца.
Иначе ведут себя включения, которые сохраняют высокую проч ность при температуре горячей деформации - НВ сферической фор мы не деформируются и сохраняют форму сферы после горячей об работки металлов давлением (ОМД). Так, например, ведут себя включения диоксида кремния SiC^. Прочные включения геометриче ской формы в результате ОМД могут разрушаться на осколки непра вильной формы и присутствовать в металле в виде скоплений, стро чек, цепочек, вытянутых в направлении главной деформации. Так себя ведут, например, оксид алюминия и нитрид титана.
Размеры НВ и их объемная доля в сталях должны соответство вать требованиям ГОСТ 1778-70 и другой нормативной документа ции. Загрязненность сталей НВ в соответствии с ГОСТ 1778-70 оп ределяют путем сравнения с эталонными шкалами или подсчетом числа и объемной доли НВ в деформированном и литом металле.
4.9.Газы в сталях
Всталях всегда содержатся элементы, которые в обычных услови ях являются газами: кислород, водород, азот. Газы могут содержаться
вметаллах в виде газовых пузырей, соединений - оксидов, гидридов, нитридов, а также в виде атомов или ионов, распределенных между атомами или ионами жидкого металла или внедренных в кристалличе скую решетку твердого металла. Газы, даже при содержании в не сколько тысячных долей процента, оказывают существенное, в боль шинстве случаев неблагоприятное влияние на свойства металлов.
4.9.1.Кислород в сталях
Атмосфера большинства сталеплавильных агрегатов является окислительной. При окислительном характере атмосферы некоторое количество кислорода всегда переходит из газовой фазы через шлак
вметалл. Дополнительными источниками кислорода служат шихто вые материалы, содержащие оксиды железа, например, ржавчина или окалина на поверхности стального лома. Если в шлаке имеется ка кое-то количество оксидов железа, то по закону Нернста в результате перехода кислорода из шлака в металл между суммарным содержа нием оксидов железа в шлаке (FeO) и кислородом, растворенным
вметалле [О], устанавливается определенное соотношение (FeO)/[0]. Растворимость кислорода в жидком железе с повышением тем
пературы возрастает (рис. 4.1). Если сталь содержит примеси, срод ство которых к кислороду больше, чем у железа, то происходит окисление этих примесей и концентрация кислорода в жидкой стали падает. Если в жидкую сталь специально вводят примеси с химиче ским сродством к кислороду, большим, чем у железа, то такую опе рацию называют раскислением, а вводимые примеси (марганец, кремний, алюминий и др.) - раскислителями. Раскислителем может являться и углерод, который в период кипения активно реагирует с растворенным в металле кислородом с образованием газа СО. По этому в период кипения содержание кислорода определяется не со отношением (FeO)/[0], а содержанием углерода в стали (рис. 4.2).
1520 1600 1680 1760
Температура металла, °С
Рис. 4.1. Влияние температуры на растворимость кислорода в жидком железе
0,1 |
0,3 |
0,5 |
0,7 |
Содержание углерода [С], % (по массе)
Рис. 4.2. Влияние углерода на окисленность стали в период кипения: 1 - кривая равно весных концентраций [С] и [О]; 2 - кон центрации [С] и [О], фактически наблюдае мые в сталеплавильном агрегате в период
кипения
Таким образом, если металл не содержит примесей, то содержание кислорода в нем зависит от окисленности шлака и температуры. Если в металле имеются примеси, то окисленность металла (содержание кисло рода в жидком металле) определяется активностью этих примесей. В пе риод кипения окисленность металла определяется содержанием углерода.
4.9.2. Водород в сталях
Атмосфера любого сталеплавильного агрегата содержит некото рое количество водорода или водяных паров. Из атмосферы агрегата
водород может переходить в жидкий металл по реакции Н \ —>2[Н].
Константа данной реакции запишется следующим образом:
к, ж ,
’р н ;
аконцентрация растворенного в жидком металле водорода при дан ной температуре
[Н]= (* р.рНг2)1/2.
по