
книги / Металлургические технологии
..pdfтем самым реакцию окисления углерода [С] + (FeO) = Fe + СО, а за тем на очень короткое время отключают подачу компонентов топли ва. В результате парциальное давление СО в печной атмосфере сни жается, и происходит взрывообразная активизация реакции окисле ния углерода. Шлак вспенивается и вытекает через рабочие окна в шлаковые чаши. При включении подачи компонентов топлива ме таллическая ванна «оседает».
Далее необходимо по возможности быстро провести операцию наведения свежего высокоосновного шлака. Для этого в печь добав ляют известь вместе с плавиковым шпатом в качестве разжижителя шлака. Быстрое формирование высокоосновного шлака (CaO/Si02 = = 3,0) позволяет дополнительно удалить из металла некоторое коли чество фосфора, а также и серы.
Далее проводят кипение ванны. Для этого на шлак подают же лезную руду или продувают ванну кислородом, активизируя реакции окисления углерода. Ванна «кипит». Как только интенсивность «ки пения» падает, в ванну подают новую порцию железной руды, обес печивая тем самым ровное «кипение».
При скрап-кислородном процессе ванну в период доводки про должают продувать кислородом. Поскольку количество плавильного шлака при ведении печи скрап-кислородным процессом довольно велико, активизация процессов окисления углерода поднимает его уровень выше уровня рабочих окон, и плавильный шлак самопроиз вольно вытекает из печи.
Последние 15 мин доводки проводят без каких-либо присадок в ванну. Этот период называют периодом «чистого кипения».
Период доводки завершают проведением предварительного рас кисления - для этого в жидкую сталь вводят ферромарганец и ферро силиций.
Легирование элементами первой группы (Си, Ni, Мо) можно проводить в любой удобный для металлурга период плавки. Легиро вание элементами второй группы возможно только после предвари тельного или окончательного раскисления в ковше.
7. Выпуск. При достижении требуемого состава и температуры проводят выпуск готовой стали из печи в сталеразливочный ковш. Выпускное отверстие (летка) мартеновской печи расположено в нижней части задней стенки по центру печи. Отверстие рассверли вают, и сталь по желобу вытекает в ковш. В ковше проводят оконча тельное раскисление и, при необходимости, легируют сталь элемен тами второй группы.
ГЛАВА 8. Электрометаллургия сталей
Электрометаллургия - способ производства сталей, при котором источником тепла для расплавления шихты и протекания физико химических процессов является электрическая энергия. В отличие от кислородно-конвертерного и мартеновского процессов выделение те пла при электроплавке не связано с потреблением окислителей. Это позволяет вести процесс в любой атмосфере: нейтральной, восстано вительной, окислительной. Кроме того, электрический нагрев металла может быть осуществлен при нормальном (атмосферном) давлении, а также при повышенном и пониженном давлении (в вакууме).
Регулирование состава и давления газовой фазы в широких пре делах дает возможность осуществлять более глубокую дефосфорацию и десульфурацию, удаление газов (дегазацию) и легирование.
По способу превращения электрической энергии в тепловую все электрические печи можно разбить на следующие группы: дуговые печи, печи сопротивления, индукционные, электронно-лучевые, плазменные и комбинированные.
В сталеплавильном производстве наибольшее применение нашли дуговые электропечи, работающие при атмосферном давлении.
8.1. Устройство дуговых электропечей
По типу используемого электрического тока печи делят на трех фазные, питаемые переменным током промышленной частоты (в Рос сии - 50 Гц), и однофазные, питаемые постоянным током, получаемым путем преобразования промышленного переменного тока в постоянный.
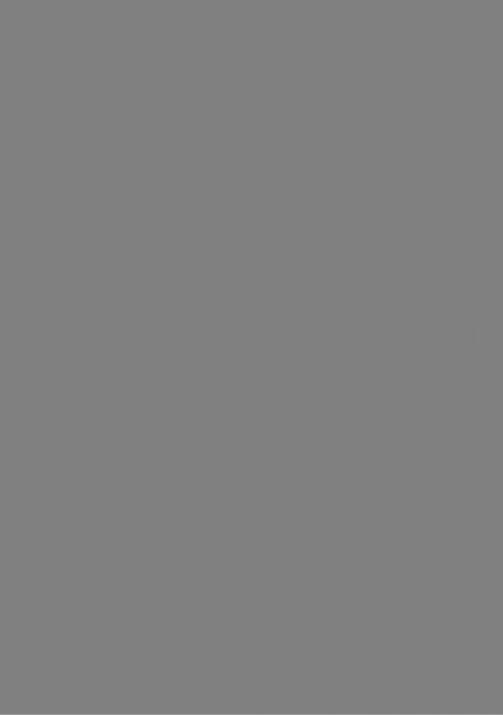
Плавку ведут в рабочем пространстве (рис. 8.2) ограниченном сверху куполообразным сводом 7, снизу - сферическим подом 6, с бо ков - стенками 2. Через отверстия в своде в рабочее пространство вво дят электроды 9, которые с помощью специальных механизмов могут перемещаться вверх-вниз. Нагрев и плавление шихты осуществляется за счет тепла электрических дуг 5, возникающих между электродами и жидким металлом или твердой металлической шихтой.
Рис. 8.2. Схема рабочего пространства дуговой электропечи: 1 - свод; 2 - стенки; 3 - желоб; 4 - сталевыпускное отверстие; 5 - электриче ские дуги; 6 - под; 7 - рабочее окно; 8 - заслонка рабочего окна; 9 - графитизированные электроды
Выпуск готовой стали и шлака производят через сталевыпускное отверстие 4 по желобу 3 за счет наклона печи или через отверстие в подине печи (см. рис. 8.2). Рабочее окно 7 с заслонкой 8 предназна чено для контроля за ходом плавки, обслуживания подины и стенок, введения в печь различных добавок, в том числе газообразного ки слорода и углеродсодержащих порошков через стальные трубки, вводимые в рабочее окно манипулятором. На самых современных печах в рабочем окне монтируют от 3 до 7 топливно-кислородных горелок для дополнительного подогрева рабочего пространства. Это ускоряет плавление шихты и позволяет экономить электроэнергию.
Шихту в современные печи загружают бадьей с открывающимся днищем за один прием. В зависимости от способа открывания рабо чего пространства различают печи с поворотным сводом, с выкатным корпусом, с откатным сводом. Эти печи отличаются компоновкой и устройством механического оборудования.
На отдельных, ранее построенных печах завалку шихты про изводят мульдами через рабочее окно с помощью завалочной ма шины.
Футеровку пода печей изготавливают из высокоогнеупорного периклазового кирпича. Для кладки стен и свода используют периклазохромитовые огнеупоры (огнеупорность до 2000 °С), изготовляемые из хромита (хромовой руды) и спеченного магнезита. Главной состав ляющей этих материалов является оксид магния MgO (периклаз).
Электрооборудование трехфазных дуговых печей. Дуговые трехфазные электропечи - мощные потребители электроэнергии, по этому для уменьшения потерь электроэнергию подают к печам под высоким напряжением - от 6 до 220 кВ. Рабочее напряжение, пода ваемое на электроды, должно находиться в пределах 110...800 В. Упрощенная схема электрооборудования, обеспечивающего сниже ние напряжения до уровня рабочего и подвод тока к электродам, по казана на рис. 8.3.
Печная подстанция 4 подключена к линии высокого напряжения. В ней размещены печной трансформатор Тр и вспомогательное обо рудование. Печной трансформатор служит для преобразования элек троэнергии высокого напряжения в рабочее напряжение. Трансфор матор имеет устройство для переключения ступеней напряжения под нагрузкой для изменения мощности электрических дуг. В схеме пи тания электропечи устанавливают 2 трехфазных выключателя мощ ности 1В и 2В. Выключатель 1В служит для отключения печи при аварийных ситуациях, выключатель 2В является оперативным и слу жит для дистанционного отключения печи во время проведения раз личных технологических операций (завалке, скачивании шлака, вы пуске, присадке добавок).
Рис. 8.3. Схема электропитания дуговой электропечи: 1 - высоковольтное распределительное устройство; 2 - приборы защиты; 3 - высоковольтный кабель; 4 - печная подстанция; 5 - приборы учета и измерения; 6 - рабочее пространство печи; 7 - устройство для электромагнитного перемешивания; 1Р-ЗР - высоковольтные разъединители (безопасности); 1В - высоковольт ный выключатель защиты печи; 2В - оперативный выключатель; 1РЗ-ЗРЗ - заземляющие разъединители; ТН - трансформатор напряжения; Тр - транс форматор печной; Пр - низковольтные предохранители; 1ТТ-ЗТТ- токовые
трансформаторы
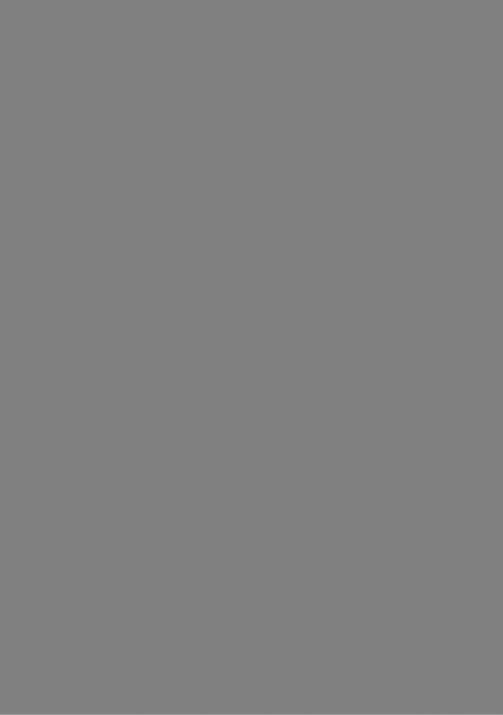
8.2. Электроды дуговых печей
На дуговых электропечах применяют графитизированные элек троды круглого сечения. Длина электродов составляет 2...3 м. Для получения необходимой общей длины их свинчивают в так называе мые свечи, используя для этого цилиндрические или конические ниппели (рис. 8.5).
Диаметр электродов зависит от емкости печи. Для трехфазных пе чей емкостью 100... 130 т использу ют электроды диаметром 610 мм;
Шдиаметр электрода для однофазных печей емкостью 130... 170 т равен
710 или 800 мм.
Сырьем для изготовления элек тродов служат графит, кокс и уголь.
|
|
Исходные материалы дробят, |
прока |
||||||
а |
б |
ливают, |
добавляют |
связующее |
- |
ка |
|||
менноугольный электродный |
пек |
и |
|||||||
Рис. 8.5. Соединение электродов |
|||||||||
подвергают |
прессованию. |
Спрессо |
|||||||
при помощи цилиндрического |
ванные заготовки обжигают в газовых |
||||||||
(а) и конического (б) ниппеля |
печах |
при |
1300 |
°С в |
течение |
||||
|
|
15...30 сут, а затем подвергают графитизации при температуре 2600...2800 °С прямым пропусканием тока. После графитизации и охлаждения готовые электроды подвергают механической обработке.
Преобразование электрической энергии в тепловую в дуговых электропечах происходит в электрической дуге, которая горит между торцом электрода и поверхностью твердой шихты или жидкого ме талла. Дуга представляет собой поток электронов, ионов, паров ме талла и шлака. Температура дуги выше 3000 °С.
Для получения дуги концы электродов вначале приводят в со прикосновение друг с другом, а затем электроды разводят. При раз ведении электродов между ними возникает электрический разряд -
дуга. Электроны, эмитированные катодом (отрицательно заряженный электрод), непрерывно ускоряясь в электрическом поле, движутся к положительно заряженному электроду - аноду. На пути к аноду элек троны сталкиваются с электронейтральными молекулами или атома ми. При столкновении движущихся электронов с молекулами или атомами происходит ионизация последних, что приводит к возник новению ионов и вторичных электронов.
На дуговых электропечах постоянного тока горение дуги после ее возбуждения (возникновения) быстро стабилизируется. При горении дуг на трехфазных печах переменного тока графигизированный электрод в течение одного периода является попеременно то катодом, то анодом. Поэтому в начале периода плавления, когда дуга горит на поверхности твердой холодной шихты, ее поведение отличается высокой нестабиль ностью. Такая дуга является источником мощного шума 120... 130 дБ. По мере разогрева шихты и постепенного плавления горение становится более устойчивым, после полного расплавления горение стабилизирует ся. В месте контакта дуги с жидким металлом (пятне дуги) создаются чрезвычайно высокие температуры (примерно 3300 °С). От пятна дуги тепло передается в глубь металла теплопроводностью и вынужденной конвекцией вследствие перемешивания жидкого металла. Кроме того, тепло передается излучением станкам и своду печи.
Впятне дуги под действием высоких температур происходят ре акции диссоциации молекул водорода и азота и растворения атомов этих газов в жидком металле. В связи с этим сталь, выплавленная
вдуговых печах, обычно содержит азота и водорода больше, чем мартеновская и кислородно-конвертерная сталь. Поэтому необходи мо проведение специальных мероприятий с целью уменьшения со держания атомов этих вредных элементов в электросталях.
8.3.Технологии выплавки сталей
вдуговых электропечах
Вдуговых электропечах можно выплавлять любые виды сталей - от высокоуглеродистых низколегированных до безуглеродистых вы соколегированных, а также различные специальные сплавы.
По типу используемой технологии выплавки дуговые электропе чи условно разбивают на 3 группы:
1 ) печи большой емкости (80... 180 т), предназначены для вы плавки нелегированных (углеродистых) и низколегированных сталей
массового назначения; 2) печи средней емкости (25...60 т), предназначены для выплав
ки конструкционных легированных и коррозионно-стойких сталей;
3 ) |
печи малой емкости |
(3...25 т), предназначены для выплавки |
быстрорежущих сталей, а также |
жаропрочных и жаростойких сталей |
и сплавов.
Для всех типов печей общими являются операции заправки, за валки и плавления. Далее технология выплавки сталей в печах раз ной емкости может существенно отличаться.
8.3.1. Технология выплавки сталей сложного состава в печах средней емкости
Данная технология, часто называемая технологией выплавки «на свежей шихте», применяется в течение многих лет на печах средней и малой вместимости для выплавки сталей сложного состава и в на стоящее время является традиционной для дуговых электропечей. Плавка состоит из следующих периодов:
1 ) заправка печи;
2 ) завалка шихты;
3)плавление;
4)окислительный период;
5) восстановительный период;
6) выпуск готовой стали.
Заправку печи проводят аналогично тому, как это делают на мар теновских печах. Длительность периода 10... 15 мин.
Завалку шихты проводят с помощью бадьи за один прием. Ших та на 90 %, как минимум, состоит из стального лома. Для повышения содержания углерода в шихту могут вводить до 7 ...8 % чугуна, боя графитизированных электродов или кокса. В качестве добавки вво дят 2...3 % извести. Укладку шихты в бадью проводят в определен
н о