
книги / Металлургические технологии
..pdfв которых прщщмает участие газовая фаза, например, реакций окис ления углерода, реакций удаления вредных газов (водорода, азота).
Для разжижения шлаков в сталеплавильный агрегат вводят спе циальные добавхи-разжижители. Для разжижения основных ишаков вводят боксит (Al20 3 +Fe20 3 +Si0 2) или, чаще, плавиковый шпат (CaF2). Для разложения кислых шлаков вводят СаО и MgO. Если не обходимо повысить вязкость основного ишака (что бывает крайне редко), то это достигается введением СаО и MgO; если появляется необходимость повышения вязкости кислого шлака, вводят боксит или кремнезем (Si02).
4.3.Процессы окисления углерода
всталеплавильных агрегатах
Поскольку основную массу сталей получают из чугуна, а содер жание углерода в чугунах значительно выше, чем в сталях, особое значение в практике сталеварения имеют реакции окисления углерода. Другими словами, для того чтобы превратить чугун в сталь, из него необходимо убрать «липший» углерод. Металлурги часто называют эти реакции главными реакциями сталеплавильного производства.
Углерод, растворенный в жидком железе, может быть окислен, во-первых, кислородом газовой фазы:
2[С] + С>2 —» СОг
Температурная зависимость AG данной реакции выглядит сле дующим образом:
A G - - 152570-33,8Г.
Во-вторых, углерод, растворенный в железе, может быть окислен кислородом, растворенным в жидком металле:
[С] + [0 ]—»СОг;
AG = - 35630 - 31 Г.
В-третьих, углерод, растворенный в железе, может быть окислен кислородом, растворенным в шлаке
[С] + (FeO) СОг+ Реж; AG = + 85373 -83,87;
g _ |
Рсо |
Р |
[С] • [FeO] |
Знак минус во всех уравнениях температурной зависимости ДG перед энтропийным слагаемым означает, что повышение температуры в сталеплавильном агрегате благоприятно влияет на протекание реак ций окисления углерода. В связи с этим не следует ожидать активного протекания этих реакций с самых первых моментов работы агрегата: необходимо, чтобы прошло некоторое время, в течение которого тем пература в агрегате повысится и создадутся благоприятные термоди намические условия для протекания реакций окисления углерода.
Анализ константы реакции окисления углерода кислородом шлака свидетельствует о том, что для более полного протекания ре акции необходимо увеличение окисленности шлака и снижение пар циального давления оксида углерода.
Скорость реакций окисления углерода определяется, во-первых, интенсивностью подвода окислителя, роль которого выполняет ки слород, а во-вторых, условиями образования и удаления пузырьков окиси углерода СО.
Пузырек СО образуется в жидкой стали и начинает подниматься вверх в том случае, если выполняется следующее условие:
Рсо — Ратм + Рит Ръл |
Рпов.нат? |
где рсо - парциальное давление СО; /?атм - |
давление газовой атмосфе |
ры в сталеплавильном агрегате; ршл - давление, оказываемое слоем шлака; рм - давление, оказываемое слоем жидкого металла; р ПОъ.тт - силы поверхностного натяжения.
Таким образом, для облегчения образования пузырьков оксида угле рода необходимо каким-то образом уменьшить сумму давлений в правой части неравенства Рассмотрим подробнее возможные мероприятия.
Давления слоя жидкого металла и шлака
7 М — P u m ~ Pnm’g ’^nmj
где рм, ршл - плотность жидкого металла и шлака; /?м, Лщл - высота слоя жидкого металла и шлака; g - ускорение свободного падения.
Отсюда очевидно, чем меньше высота слоя жидкого металла и шлака, тем меньше и давление металла и шлака, и, следовательно, слой металла и шлака должен быть по возможности более тонким. Для этого геометрия ванны сталеплавильного агрегата должна напо минать «блюдце», а не «стакан».
Известно, что сила поверхностного натяжения р п0В.Нат меньше при гетерогенном зарождении новой фазы. Для увеличения вероятности гетерогенного зарождения пузырьков СО необходимо, чтобы пло щадь пода сталеплавильного агрегата была по возможности больше. Таким образом, вновь приходим к тому, что геометрия ванны должна бьггь вполне определенной: «блюдце», а не «стакан».
Для уменьшения давления газовой атмосферы /?атм возможна от качка газов после предварительной герметизации агрегата (вакууми рования).
Таким образом, реакции окисления углерода протекают полнее при повышении температуры в сталеплавильном агрегате под шла ками с высокой окисленностью, а также в агрегатах с плоскими и неглубокими ваннами. Кроме того, мощным фактором, существен но облегчающим протекание процессов окисления углерода, хотя и весьма дорогим, является вакуумирование.
Пробулькивание большого количества пузырьков СО на поверх ности ванны создает иллюзию кипения, вот почему отрезок времени, в течение которого активно происходят реакции окисления углерода, металлурги называют периодом «кипения» (или периодом «кипа»).
Кроме уменьшения содержания углерода в жидком металле, без которого невозможно превращение чугуна в сталь, кипение способ ствует выравниванию температуры и химического состава металла за счет интенсивного его перемешивания, снижению содержания ато мов газов (водорода, азота), а также мелких неметаллических вклю чений.
4.4. Процессы окисления и восстановления примесей
Рассмотрим эти процессы на примере поведения марганца, кремния и фосфора.
Окисление и восстановление марганца. Марганец по свойствам близок к железу и поэтому растворяется в нем в любых соотношени ях. Марганец - элемент, легко окисляющийся при относительно не высоких температурах до высших оксидов: М п02, Мп20з, МП3О4. При высоких температурах устойчив только оксид МпО.
Основная доля марганца поступает в сталеплавильный агрегат вместе с чугуном. Довольно часто марганец присутствует в железной руде и стальном ломе (скрапе).
Марганец, растворенный в жидком металле, может быть окислен: 1 ) кислородом газовой фазы:
[Мл] + 1/2 0 2 = (МпО), AG = - 361380 - 106Г;
2 ) кислородом, растворенным в металле:
[Мп] + [О] = (МпО), AG = - 245000 + 1097;
3) кислородом, содержащимся в окислах железа шлака:
[Мп] + (FeO) = (МпО) + Fe*, AG = - 124000 + 56,47;
к _ |
(МпО) |
р |
[Mn]-(FeO) |
Следует обратить внимание на то, что в двух первых реакциях перед энтропийным слагаемым стоит знак плюс. Это означает, что с повышением температуры в сталеплавильном агрегате возможно протекание реакций восстановления марганца. Действительно, мар ганец может восстанавливаться железом, углеродом, кремнием и другими элементами, растворенными в железе, сродство которых к кислороду в данных условиях выше, чем у марганца:
(МпО) + Fe = [Мп] + (FeO);
(МпО) + [С] = [Мп] + СОг;
(МпО) + [Si] = [Мп] + (Si02).
На процессы окисления и восстановления марганца большое влияние оказывает окисленность шлака (FeO) —чем выше окисленцость ишака, тем полнее протекают реакции окисления марганца и тем выше температура термодинамического равновесия, т.е. темпе ратура, начиная с которой возможно протекание реакций восстанов ления марганца.
Окисление и восстановление кремния. Кремний, как и марга нец, растворяется в жидком железе в любых соотношениях. Основ ная масса кремния поступает в сталеплавильный агрегат вместе с чугуном. Так же как и другие элементы, кремний может быть окис лен кислородом газовой фазы (реакция 1), кислородом, растворен ным в жидком железе (реакция 2), и кислородом, содержащимся
воксидах железа шлака (реакция 3):
1)[Si] + 0 2 = (Si02), AG = -775678 + 1987;
2)[Si] + [О] = (Si02), AG = -300000 + 987;
3) [Si] + 2(FeO) = (Si02) + 2Реж, AG = -541840 + 2037;
(S iP2)
p [Si]-(FeO)2'
Реакция окисления кремния кислородом газовой фазы (реакция 1) сопровождается очень значительным экзотермическим эффектом, ко торый, по сути, является «топливом» бессемеровского процесса.
Знак плюс перед энтропийным слагаемым свидетельствует о возможности протекания обратных реакций - реакций восстановле ния кремния при повышении температуры. Действительно, процессы восстановления кремния протекают под кислыми шлаками, когда ак тивность двуокиси кремния высока, а окисленность шлака мала. По вышение окисленности шлака, как следует из записи константы реак ции 3, способствует протеканию реакций окисления кремния и пре пятствует протеканию процессов восстановления кремния.
Окисление и восстановление фосфора. Фосфор растворяется в железе в значительных количествах, при этом выделяется некото рое количество тепла. Фосфор в железоуглеродистых сплавах счита ют вредной примесью и поэтому его удалению из стали металлурги
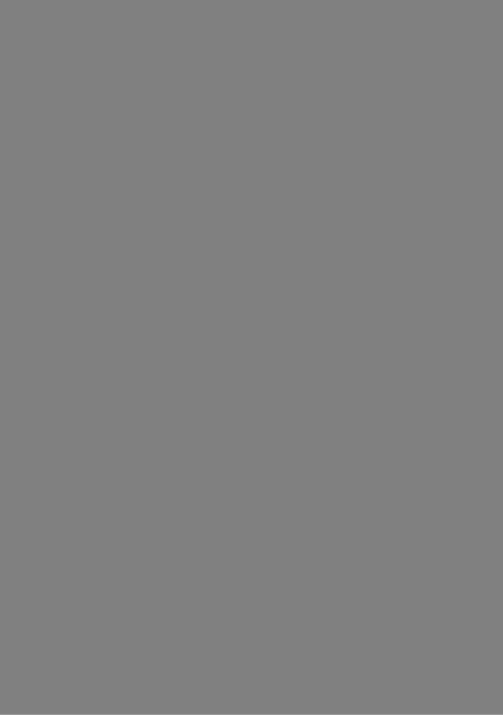
в прочные соединения, например, трифосфат кальция (СаО)з(Р20 5) или тетрафосфат кальция (СаО)4(Р2С>5). Для этого наводят шлак с высокой основностью. В таких условиях реакция окисления фосфора кислоро дом шлака с образованием тетрафосфата кальция запишется так:
2[Р] + 4(СаО) + 5(FeO) = (СаО)4 (Р20 5) + 5Реж, а ее константа
(СаО)4-(Р205)
р [Р]2 • (СаО)4 • (FeO)5
Совместный анализ температурных зависимостей AG реакций окисления фосфора и константы последней реакции позволяет окон чательно сформулировать условия успешной дефосфорации:
1) температура в сталеплавильном агрегате должна быть относи тельно низкой; другими словами, дефосфорацию необходимо прово дить в начале сталеплавильного процесса;
2)окисленность шлака (FeO) должна быть высокой;
3)основность шлака (СаО) должна быть высокой;
4) активность фосфорсодержащего продукта реакции
(Са0)4(Р20 5) должна быть низкой.
Мероприятием, гарантирующим отсутствие процесса рефосфорации, является проведение операции замены высокофосфористого шлака на новый шлак, не содержащий фосфора. Операцию удаления шлака металлурги называют «скачивание шлака», а создание нового шлака - «наведение шлака».
В заключение важно отметить, что в агрегатах с кислой (динасо вой) футеровкой проведение дефосфорации принципиально невоз можно, поскольку в подобных агрегатах невозможно создание шлака
свысокой основностью.
4.5.Сера и ее удаление из жидкой стали
Сера в железоуглеродистых сплавах является вредной примесью. С железом и другими элементами сера образует легкоплавкую эвтек тику, которая плавится при температуре 988 °С, поэтому при нагреве
слитков или заготовок под горячую обработку давлением (ковку, прокатку) происходит оплавление границ зерен, и, как следствие, резко уменьшается межзеренная когезия. Это, в свою очередь, при водит к разрушению слитка в процессе горячей пластической дефор мации. Данное явление получило название красноломкость.
Источниками поступления серы в сталеплавильный агрегат яв ляются чугун, скрап, особенно промасленная стальная стружка, а также атмосфера агрегата, работающего на газе или мазуте.
Для удаления серы из жидкого железа (десульфурации) вводят элементы-десульфураторы. Элемент-десульфуратор (Э) - это хими ческий элемент, энергия образования сульфида которого меньше энергии образования сульфида железа:
AG(3S)< AG(FeS) или AG(3S)- AG(pes)< 0.
Такими элементами являются марганец, магний, натрий, кальций и др. Необходимо отметить, что вероятность протекания реакций об разования сульфидов элементов-десульфураторов увеличивается по мере повышения температуры в сталеплавильном агрегате.
Чаще всего для проведения десульфурации используют известь СаО. Тогда реакция десульфурации выглядит следующим образом:
[FeS] + (СаО) = (FeO) + (CaS),
аее константа запишется как
к_ (FeO) ♦(CaS)
р[FeS] • (СаО)
Серосодержащие продукты реакций десульфурации (CaS) и (MnS) не только не растворяются в жидком железе, но даже не сма чиваются им и поэтому полностью переходят в шлак.
Таким образом, можно сформулировать условия успешной де сульфурации:
1)высокая температура в сталеплавильном агрегате;
2)высокая основность шлака;
3)низкая окисленность шлака;
4)низкая активность серосодержащего продукта реакции (CaS).
Кроме того, необходимо учитывать, что сера является поверхно стно-активным элементом, и поэтому ее содержание на границе раз дела двух фаз, например, жидкий металл-шлак всегда выше, чем
втолще жидкого железа. В связи с этим наибольший эффект дают такие методы ведения плавки, которые обеспечивают увеличение поверхности контакта десульфуратора с жидким металлом. К таким приемам можно отнести перемешивание жидкого металла со ишаком и л и вдувание порошкообразных реагентов.
Взаключение сравним условия успешного проведения дефосфорации и десульфурации. Очевидно, что фосфор успешно удаляется
вначале процесса сталеварения при относительно низких температу
рах в агрегате, тогда как сера удаляется при высоких температурах - в конце процесса. Окисленность шлака для дефосфорации должна быть высокой, а для десульфурации - низкой. Таким образом, следу ет признать, что в традиционных сталеплавильных агрегатах одно временное удаление фосфора и серы из жидкой стали невозможно.
4.6. Раскисление сталей
Для успешного протекания реакций окисления углерода - «ки пения» - в сталеплавильный агрегат в том или ином виде подают ки слород, поэтому после завершения периода «кипения» содержание кислорода в жидком металле весьма велико. Кислород, так же как фосфор и сера, является вредной примесью и поэтому его необходи мо удалять.
Технологическую операцию удаления кислорода из жидкой ста ли или связывания его в химически прочные и нерастворимые в ста ли соединения называют раскислением.
В настоящее время при выплавке сталей используют четыре ос новных способа раскисления:
1)глубинное (осаждающее) раскисление;
2)диффузионное раскисление;
3)раскисление синтетическим шлаком;
4)вакуумно-углеродное раскисление. Рассмотрим подробнее эти способы раскисления.
Глубинное раскисление заключается в том, что в толщу (глуби ну) жидкого металла вводят элементы-раскислители, т.е. такие хи мические элементы или их соединения, химическое сродство кото рых к кислороду больше, чем у железа.
Если элемент-раскислитель, растворенный в жидком железе обо значить, например, как [Me], то реакция глубинного раскисления бу дет выглядеть так же, как и реакция окисления примеси, растворен ной в жидком железе, кислородом, растворенным в жидком железе:
[Me] + [О] = (MeO), AG = ±AH+AST;
_ а (МеО)
а [Ме] * ° [ 0 ]
Исходя из экономических соображений, наиболее часто в качестве раскислителей используют марганец, кремний и алюминий. Марганец
икремний используют в виде сплавов с железом (ферросплавов - фер ромарганца и ферросилиция), а алюминий - в чистом виде.
Применяют и комплексные раскислители: силикомарганец (SiMn), силикокальций (SiCa), а также сплавы типа АМС (Al+Mn+Si)
иКМК (Si+Mn+Ca).
Анализ записи константы реакции глубинного раскисления гово рит о том, что для более полного протекания реакции в прямом на правлении активность продукта реакции Я(МеО) должна быть мини мальной. Другими словами, чем более химически прочным является получаемый оксид, тем более полно протекает глубинное раскисление.
Поскольку среди перечисленных элементов минимальным срод ством к кислороду обладает марганец, то сталь, раскисленная одним ферромарганцем, содержит в своем составе повышенное количество кислорода. Иначе говоря, сталь, раскисленная ферромарганцем, - кипящая. Сталь, раскисленная ферромарганцем и ферросилицием, содержит значительно меньшее количество кислорода, и ее относят к полуспокойным сталям. Сталь, раскисленная последовательно фер ромарганцем, ферросилицием и алюминием, содержит минимальное количество кислорода и является спокойной.