
книги / Металлургические технологии
..pdfнепрерывно двигаясь по конвейеру, форма охлаждается до необхо димой температуры и в конце попадает к распаровщику 4. Далее цикл повторяется. Производительность линии 270...280 форм в час.
ГЛАВА 14. Получение отливок
специальными способами литья
Качество отливок, получаемых в песчано-глинистых формах, по многим параметрам не удовлетворяет требованиям современного машиностроения. Поэтому в последние десятилетия получили разви тие специальные высокопроизводительные способы литья, позво ляющие получать плотные высокоточные отливки с высоким уров нем характеристик механических свойств, низкой шероховатостью поверхности и т.д. Основными видами специального литья являются: литье в кокиль, центробежное литье, литье в оболочковые формы, литье под давлением, литье по выплавляемым моделям.
14.1. Литье в кокиль
Кокилем называют разъемную многократно используемую ме таллическую форму, заполняемую жидким металлом под действием гравитационных сил. Материалами для изготовления кокилей служат чугун, сталь, сплавы на основе алюминия. В зависимости от мате риала получаемых отливок, их массы и габаритов, кратность исполь зования кокилей колеблется от 300 до 6000 отливок.
Основные технологические операции литья в кокили:
1)подготовка кокиля, которая включает в себя: очистку от за грязнений, проверку центровки полуформ; нанесение теплозащитно го покрытия (ТЗП);
2)предварительный подогрев кокиля;
3)сборка кокиля: установка стержней, соединение и закрепление полуформ;
4)окончательный нагрев кокиля;
5)заливка жидкого металла;
6)разборка (раскрытие) кокиля и извлечение отливки.
Разновидностью кокильного литья является литье в облицован ные кокили. Облицовка кокиля заключается в следующем. Половин ку модели закрепляют на подмодельной плите и нагревают до 200...220 °С. Затем на половинку модели с зазором 3...5 мм уста навливают кокиль, предварительно нагретый до такой же температу ры. В зазор с помощью пескодувной головки вдувают формовочную смесь с термореактивным связующим. В результате на поверхности кокиля формируется облицовочный слой толщиной З...5мм, кото рый упрочняется под действием температуры разогретого кокиля
имодели. Нанесение облицовочного слоя позволяет существенно увеличить срок службы кокилей.
Преимуществами литья в кокиль, по сравнению с традиционны ми способами литья, являются: снижение трудоемкости (в 2...3 раза)
исебестоимости отливок (на 25...30 %), повышение производитель ности и широкие возможности механизации, автоматизации и робо тизации процесса получения отливок, более высокая точность гео метрических размеров и низкая шероховатость поверхности отливок.
Недостатками кокильного литья являются:
1)высокая стоимость кокиля - в связи с этим кокильное литье эффективно только при массовом производстве;
2)высокие скорости охлаждения получаемых отливок вследствие более высокой теплопроводности металлической формы - это создает трудности при получении тонкостенных отливок сложной формы;
3)кокиль в отличие от земляной формы неподатлив - сопротив ляется усадке, что затрудняет извлечение отливки из формы и спо собствует возникновению трещин в отливке.
14.2. Центробежное литье
При центробежном литье жидкий металл заливают во вращающуюся форму. В результате формирование отливки происходит под действием центробежных сил, что обеспечивает повышение плотности отливки.
Металлические формы (изложницы) для центробежного литья изготавливают из чугуна или стали, толщина стенки формы должна быть в 1,5...2 раза больше толщины стенки отливки. В процессе ли
тья форму снаружи охлаждают водой или сжатым воздухом. Перед заливкой жидкого металла на внутреннюю поверхность формы нано сят ТЗП и подогревают форму до 200 °С.
Машины центробежного литья бывают двух типов: с горизон тальной и вертикальной осью вращения (рис. 14.1). На машинах с горизонтальной осью вращения получают отливки без днища: втул ки, трубы, кольца. Машины с вертикальной осью вращения предна значены для получения отливок типа «стакан» - с днищем.
б |
в |
Рис. 14.1. Схемы центробежного литья на машинах с вертикальной (/) и горизонтальной (II) осью вращения: а - вращение формы до затвер девания отливки; б - остановка формы; в - удаление отливки из формы; 1 - форма; 2 - металл; 3 - желоб; 4 - разливочный ковш; 5 - отливка
Этот способ позволяет получать достаточно плотные отливки без применения формовочных смесей.
Формирование внутренних полостей при центробежном литье происходит без использования стержней. Отсутствие литниковой системы позволяет упростить технологию, кроме того, существенно экономит металл.
Уникальным преимуществом данного способа литья является возможность получения многослойных отливок. В этом случае необ ходимо во вращающуюся форму последовательно залить сталь и чу гун или чугун и бронзу (или латунь).
14.3. Литье под давлением (жидкая штамповка)
Принципиальное отличие литья под давлением от литья в кокиль заключается в том, что заливку жидкого сплава в металлическую форму и кристаллизацию отливки осуществляют под давлением мно го больше атмосферного - от 0,1 до 50 МПа (10...500 атм).
Машины литья под давлением делят на два типа:
1)машины с холодной камерой прессования;
2)машины с горячей камерой прессования.
Вмашинах первого типа камера прессования находится в нор мальных условиях - на воздухе, в машинах второго типа камера прессования находится внутри подогреваемого тигля с расплавлен ным металлом для будущих отливок.
На рис. 14.2 представлена схема машины литья под давлением
схолодной камерой прессования. Порцию расплавленного металла заливают в камеру прессования (рис. 14.2, а). Затем под действием прессующего поршня жидкий металл через литниковые каналы за полняет полость пресс-формы, быстро затвердевает при избыточном давлении и образует отливку (рис. 14.2, б).
После окончания кристаллизации подвижная часть пресс-формы 3 отходит в сторону и отливка специальными толкателями 5 вытал кивается из неподвижной части пресс-формы 1 (рис. 14.2, в). Прессформу осматривают, очищают продувкой сжатым воздухом, наносят защитное покрытие и закрывают. Одновременно с подготовкой пресс-формы готовят камеру прессования: поднимают прессующий поршень, извлекают пресс-остаток 4, осматривают камеру, наносят защитное покрытие. Далее цикл повторяют.
Литье под давлением позволяет получать плотные отливки с бла гоприятной структурой, обеспечивающей высокий комплекс харак теристик механических свойств. Точность геометрических размеров и чистота поверхности такова, что последующая механическая обра
ботка не требуется. Данный способ позволяет получать отливки с толщиной стенки менее 1 мм, а также готовые резьбы.
Рис. 14.2. Схема получения отливок способом литья под давлением: а - заливка металла в камеру прессования; б - запрессовка металла; в - открывание пресс-формы и удаление отливки; 1 - толкатель; 2 - неподвижная часть пресс-формы; 3 - отливка; 4 -подвижная часть пресс-формы; 5 - пресс-остаток
Недостатки данного способа такие же, как и при литье в кокиль. Кроме того, литье под давлением не позволяет получать крупные отливки.
Литье под давлением применяют в крупносерийном и массовом производствах точных малогабаритных отливок из сплавов на основе алюминия, магния, меди.
14.4. Литье в оболочковые формы
Этим методом получают тонкие, толщиной не более 15...20 мм, но довольно прочные разъемные формы. Формовочная смесь, из ко торой изготавливают оболочковые формы состоит из 90 % мелкозер нистого кварцевого песка и 10 % связующего. Связующим в данном случае является термореактивная смола с добавкой уротропина - пульвербакелит. При нагреве до 120... 140 °С смола плавится, и смесь приобретает свойство текучести, а при последующем нагреве выше 250 °С смола необратимо затвердевает и смесь упрочняется.
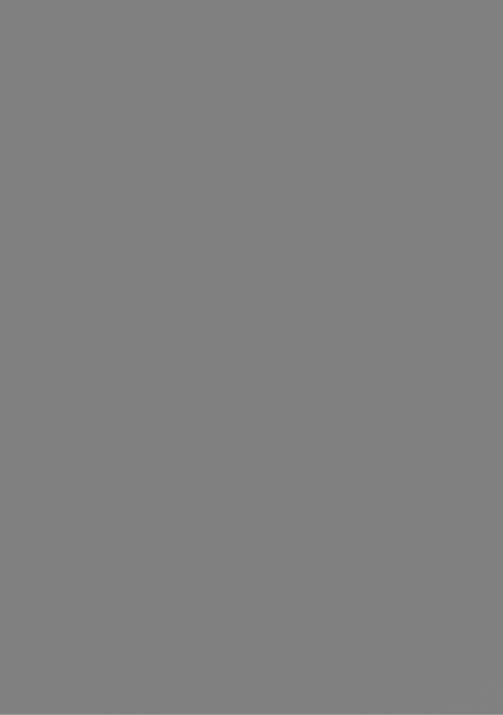
4) подмодельную плиту вместе с половинкой модели и оболоч кой снимают с бункера и помещают в печь с температурой 300 °С, где происходит окончательное (необратимое) упрочнение оболочки.
Аналогичным образом готовят вторую половину литейной формы и оболочки литниковой системы. Готовые оболочковые полуформы склеивают быстротвердеющим клеем или соединяют с помощью струб цин. При необходимости предварительно в форму устанавливают стержни. Форму помещают в контейнер. Оставшийся объем засыпают песком для придания дополнительной механической прочности и предохранения оболочковой формы от преждевременного разрушения (рис. 14.3, г). Подогревают готовую форму и заливают жидкий металл.
Этим способом получают тонкостенные отливки сложной формы массой от 0,5 до 200 кг из чугунов, сталей и цветных сплавов. Способ литья в оболочковые формы широко применяется в автотракторной промышленности.
14.5. Литье по выплавляемым моделям
Особенность данного способа в том, что модели изготавливают из легкоплавких материалов и после изготовления формы модели из формы не извлекают, а выплавляют.
Модели изготавливают методом прессования из парафиностеа риновой смеси (50 % парафина и 50 % стеарина). После прессования готовая модель выталкивается в чан с холодной водой. Поскольку детали, получаемые этим методом, достаточно мелкие, готовые мо дели при помощи паяльника объединяют в блоки моделью литнико вой системы, которую готовят так же, как и модели отливок. В одном блоке может быть от 2 до 100 моделей отливок (рис. 14.4, а).
Технология изготовления отливок этим способом состоит из сле дующих основных операций:
1) формирование корки на поверхности блока моделей (облицов ка) - блок окунают в керамическую суспензию (рис. 14.4, б), после окунания посыпают циркониевым песком или электрокорундом (рис. 14.4, в), затем просушивают (рис. 14.4, г). Длительность сушки на воздухе составляет 2 ч, в среде аммиака - 40 мин. Эти операции по
вторяют несколько раз (от 3 до 20 раз, чаще всего - от 3 до 6 раз). Ке рамическая суспензия частично растворяет песок, и на поверхности блока моделей формируется и с каждым окунанием нарастает плотная корочка. Окончательная толщина корочки составляет от 2 до 4 мм;
д е ж з
Рис. 14.4. Схема процесса изготовления отливок по выплавляемым моделям: 1 - литниково-питающая система; 2 - паяльник; 3 - модели
2)облицованный блок моделей помещают в контейнер, который засыпают кварцевым песком (рис. 14.4, <));
3)выплавление моделей: контейнер переворачивают и в таком по
ложении помещают в печь с температурой примерно 200 °С или в бак
сгорячей водой; модельный состав плавится и вытекает из формы;
4)прокаливание форм - контейнер с формой помещают в печь с температурой 900...950 °С (рис. 14.4, е). Под действием высокой температуры происходит спекание смеси и упрочнение формы, уда ление влаги, выгорание остатков модельного состава;
5) сразу же после прокаливания в готовые формы заливают жид кий металл (рис. 14.4, ж).
После полного затвердевания отливок форму разрушают и из влекают отливки (рис. 14.4, з).
Этот метод позволяет практически из любых сплавов получать тон костенные отливки сложной формы с высоким качеством поверхности, массой от нескольких граммов до нескольких десятков килограммов.
Литье по выплавляемым моделям широко используют в авиа строительной промышленности для изготовления турбинных и ком прессорных лопаток из жаропрочных сталей и сплавов, сплавов на основе титана. Этим способом получают также насосные колеса сложной конфигурации из коррозионно-стойких сталей.
ГЛАВА 15. Литейные сплавы
В отечественном машиностроении около 70 % всех отливок из готовляется из чугуна, около 17 % - из стали, остальное - из цветных сплавов.
15.1. Производство отливок из чугуна
Плавку чугунных чушек на машиностроительных заводах ведут в вагранках или электропечах. Вагранка - это печь шахтного типа, по принципу работы похожая на доменную печь. Стальной кожух из нутри футеруют шамотным кирпичом. Загрузка шихты сверху осу ществляется порциями (колошами) с помощью подъемника. Шихта состоит из металлической и топливной частей, кроме того, в шихту входит флюс. В состав металлической части шихты могут входить доменный чушковый чугун, чугунный и стальной лом, возврат (лит ники и брак), брикетированная стружка, природно-легированные чугуны и ферросплавы. Вагранка обычно работает на коксе, а в качест ве флюса используют известняк. Топливо (кокс) сгорает в струе воз духа, вдуваемого через фурмы в нижней части вагранки. Шихта расплавляется, и происходят химические реакции, необходимые, прежде всего, для удаления вредных примесей. Переплавленный
жидкий чугун вытекает в копильник, установленный перед вагран кой, откуда раздаточными ковшами подается на участок заливки форм. Плавильные электропечи - дуговые и индукционные, широко использующиеся в современных литейных цехах, позволяют повы сить технико-экономические и экологические показатели плавки по сравнению с вагранками.
Чугун, в котором основная часть углерода находится в виде гра фита, называют серым. Если же углерод в чугуне связан в химиче ское соединение - карбид железа (цементит - Fe3C), то такой чугун называют белым. Цементит обладает очень высокой твердостью, но при этом весьма хрупок, поэтому его стараются получать в виде тон кого поверхностного слоя только в тех случаях, когда требуется обеспечить отливке высокую износостойкость.
В качестве конструкционного сплава используют серый чугун, причем в зависимости от формы графита серые чугуны делят на соб ственно серые - чугуны с графитом в виде пластинок, ковкие чугу ны - с графитом в форме хлопьев, и высокопрочные чугуны - в них графит имеет форму, близкую к сферической.
Серый чугун является самым дешевым и наиболее распростра ненным материалом для изготовления разного рода отливок. Он об ладает хорошими литейными свойствами - высокой жидкотекучестью и низкой (около 1 %) усадкой, что позволяет получать из него отливки самой сложной конфигурации. Механические свойства серо го чугуна повышаются путем модифицирования. При модифициро вании в жидкий чугун за 5... 10 мин до разливки вводят в измельчен ном виде небольшое количество (до 1 %) модификатора - ферроси лиция, силикокальция и др. Мелкие частицы модификатора увеличивают число центров кристаллизации (зародышей) и тем са мым приводят к измельчению зерен в структуре отливки, а следова тельно, и к увеличению ее прочности.
В высокопрочном чугуне графит имеет наиболее компактную шаровидную форму. Для получения графита шаровидной формы чу гун модифицируют магнием, церием, иттрием. Чугун, подвергаемый модифицированию, должен быть низкосернистым, так как повышен