
книги / Металлургические технологии
..pdfПри агломерации происходит частичное удаление серы и мышь яка. Сера в шихте находится в виде пирита FeS2, гипса CaS04-2H20 и барита BaS04. Пирит окисляется кислородом воздуха:
3FeS2 + 802 = Рез04 + 6S02.
Гипс и барит разлагаются под действием высоких температур: CaS04 = СаО + SO3, BaS04 = ВаО + SO3.
В настоящее время производят только офлюсованный агломерат, имеющий основность (CaO)/(Si02) = 1,1...2,0. Такой уровень основ ности агломерата отвечает условию полного выведения флюсов из
доменной плавки. |
|
|
|
|
||
На |
производство 1 |
т |
агломерата |
расходуется |
в среднем |
|
1230.. . 1270 |
кг шихты, |
|
в том числе |
руды и концентрата - |
||
800.. |
.950 кг, |
топлива - |
59...63 кг, электроэнергии - |
37...39 кВт-ч, |
||
воды - |
0,3...0,8 м3, флюса - |
60... 180 кг. |
|
|
В настоящее время на металлургических заводах работает более 1000 агломашин. Наиболее производительные имеют площадь спе кания до 600 м2. В России самые мощные машины АКМ-312 имеют площадь спекания 312 м2.
Производство окатышей. Окатыши - твердые тела размером 2 .. .30 мм, имеющие форму, близкую к сферической. Окатыши полу чают путем окатывания (окомкования) тонкоизмельченных рудных материалов с добавками связующих веществ и флюсов с последую щим термическим упрочнением (обжигом). Окатыши получают на окомковательных фабриках, расположенных на территории горнообогатительных комбинатов (ГОКов). Широкое использование ока тышей в качестве шихты доменного процесса (начиная с середины 50-х годов прошлого века) обусловлено следующим:
во-первых, значительно увеличивается производство тонкоиз мельченных богатых концентратов, окускование которых методом агломерации снижает технико-экономические показатели процесса;
во-вторых, окатыши, вследствие их высокой механической прочности, удобно транспортировать на большие расстояния с мно гократными перегрузками;
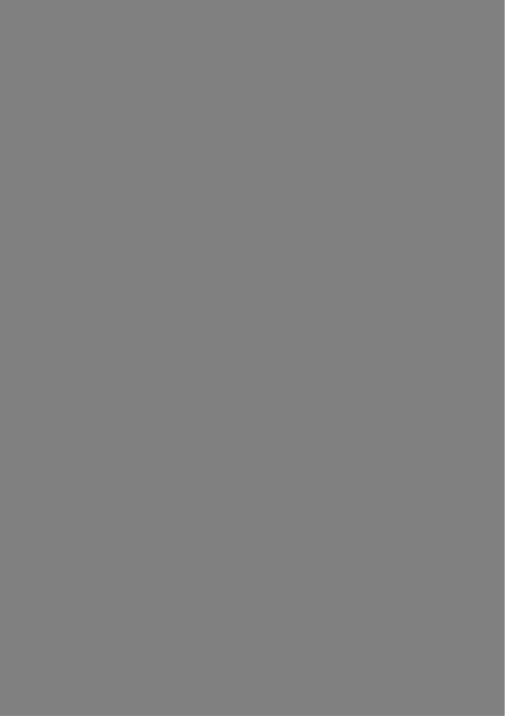
ванные мелкие фракции шихты достигали верхней кромки борта и отрывались с помощью скребка. Кроме того, установка скребка пре дотвращает круговое движение шихты и вынуждает шихту двигаться по траектории, показанной на рис. 1.7, а.
Далее сырые окатыши подвергают сушке при температуре 300...600 °С и упрочняющему обжигу при 1150... 1350 °С. Для обжи га используют конвейерные колосниковые машины (подобные агло машинам), шахтные печи, кольцевые колосниковые машины и др.
Процесс упрочнения окатышей при высокотемпературном обжи ге основан на спекании частиц концентратата за счет протекания фи зико-химических реакций в твердой и жидкой фазах. Наиболее эф фективное упрочнение окатышей достигается при наличии 1 2 ...2 0 % жидкой фазы, которая после остывания служит цементирующей связкой. В настоящее время обжиг проводят в окислительной атмо сфере с окислением магнетита до гематита. В результате между зер нами магнетита появляются перемычки из гематита, которые пре вращают материал окатыша в прочный монолит.
Добавка в доменную шихту окатышей существенно повышает производительность доменных печей. Доля окатышей в общем объ еме железорудного сырья в настоящее время превышает 30 %. Тем не менее, исходя из особенностей работы доменных печей, агломерат не может быть полностью заменен на окатыши.
1.3. Флюсы
Флюсами называют материалы, вводимые в металлургический агрегат для формирования шлака определенного состава с опреде ленными физико-химическими свойствами, способного растворять в себе пустую породу руд, золу топлива и вредные примеси.
Дело в том, что температура плавления оксидов, входящих в со став пустой породы железных руд и золы топлива (кокса, угля) зна чительно выше температуры плавления шлаков не только доменного, но и сталеплавильного производства: Si02 - 1728 °С, А120з - 2040 °С, СаО - 2570 °С, MgO - 2800 °С.
Однако при определенном количественном соотношении кислых и основных оксидов, входящих в состав шлака, формируются легко плавкие составы, температура плавления которых не превышает 1300 °С. Известно, что для обеспечения формирования легкоплавких составов соотношение кислых и основных оксидов должно быть рав
но примерно 1, т.е. (CaO )/(Si02) « l . Поскольку в пустой породе железных руд преобладают кислые оксиды, становится ясно, что в качестве флюсов необходимо вводить оксиды основные. Вот поче му в качестве флюса чаще всего используют известь СаО. Кроме то го, в качестве флюсов можно использовать известняк СаСОз, доломитизированный известняк (известняк, содержащий небольшое ко личество карбонатов магния), доломит CaCCb-MgCCb, боксит (Al20 3 +Si0 2 +Fe20 3 ), плавиковый шпат CaF2 и др.
1.4. Металлургический кокс
Кокс в металлургических процессах, в первую очередь в домен ном производстве, исполняет роль топлива, восстановителя и науглероживателя.
Кокс - это твердый пористый углеродистый остаток, получае
мый |
в результате нагрева (коксования) специальных углей до |
900.. |
.1200 °С без доступа воздуха. |
Перед коксованием уголь различных марок дробят, обогащают для снижения зольности и усредняют. Затем угли смешивают в опре деленной пропорции и подвергают измельчению. Необходимо, что бы доля фракции до 3 мм составляла не менее 92...94 %, поскольку это позволяет обеспечить меньшую трещиноватость и, как следствие, более высокую прочность кокса.
Коксование ведут в герметизированных камерах, которые для увеличения производительности и уменьшения расхода топливных газов собраны в батареи по 40...80 камер. Общий вид коксовой бата реи показан на рис. 1.8. Камеры коксования расположены в ряд в верхней части батареи. Между камерами находятся обогреватель ные простенки, в которых движутся продукты сгорания топливных
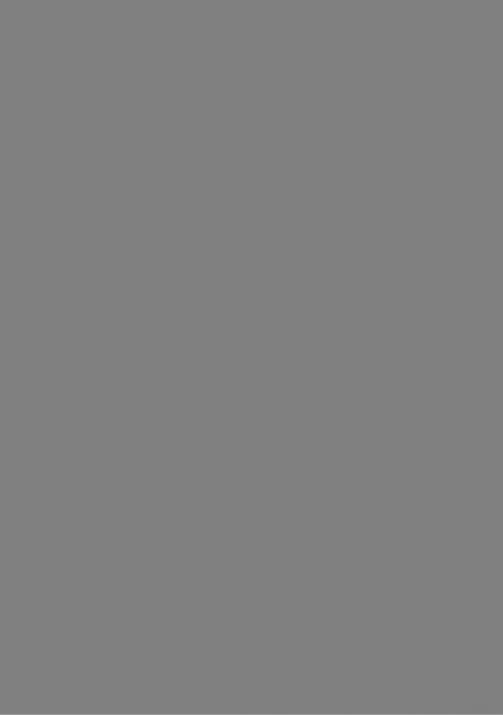
•до 250 °С - испарение свободной (гигроскопической) влаги, выделение адсорбированных газов;
•250...300 °С - выделение паров смолы и связанной (гидратной)
влаги, пропитка частиц угля смолой;
• 350.. .400 °С - переход угля в пластичное состояние;
•400...550 °С - разложение пластической массы с выделением газа и смол и последующее ее отверждение с получением полу кокса;
•550...700 °С - разложение полукокса с выделением газообраз
ных продуктов и упрочнение;
• выше 700 °С - превращение полукокса в кокс.
После завершения процесса коксования готовый кокс выталки вают в вагон и транспортируют к башне тушения. Здесь кокс подвер гают тушению и охлаждению водой (мокрое тушение) или инертны ми газами (сухое тушение). После тушения и охлаждения кокс сор тируют по классам крупности.
Из 1 т сухой шихты получают в среднем 750...800 кг кокса, 320...330 м3 коксового газа. Коксовый газ, после очистки содержа щий примерно 6 % СО, 25 % СЕЦ, до 60 % Н2 и 6 ...7 % С 0 2 и N2 и имеющий теплоту сгорания 18 МДж/м3, используют как топливо. В частности, зажигательные горны агломерационных машин отапли вают смесью коксового и доменного газов.
Кокс хорошего качества имеет серебристый оттенок, не пачкает ся и немного звенит при ударе куска о другой кусок.
Кроме кокса и коксового газа в результате коксования получают много других продуктов: бензол, фенолы, нафталин, сульфат аммо ния, каменноугольную смолу и др.
ГЛАВА 2. Технология получения железа
Под металлургией железа понимают такие химические, химико термические или электрохимические процессы, которые позволяют без участия доменной печи получать железо в виде губки, металлизованных окатышей или жидкого металла.
Внастоящее время такие продукты называют прямовосстановленным железом (ПВЖ). В случае, если губчатое железо или металлизованные окатьппи подвергают последующему горячему брикети рованию, то такие продукты называют горячебрикетированным же лезом (ГБЖ).
Методы прямого получения железа из руд известны давно, но в последние десятилетия интерес к ним сильно возрос. Причины этого заключаются в том, что, во-первых, при реализации этих процессов отпадает необходимость в использовании кокса, во-вторых, совер шенствование способов обогащения привело к возможности полу чения железорудных концентратов, очень богатых по железу и одно временно очень чистых по сере и фосфору. Например, железорудный концентрат, производимый на ОАО «Лебединский ГОК», содержит менее 0,01 % серы и менее 0,003 % фосфора. Преимущество высокой чистоты исходной шихты в доменном процессе не может быть ис пользовано, поскольку большое количество фосфора и особенно се ры в доменную печь попадает с коксом.
Внастоящее время до 90 % всего ПВЖ и ГБЖ получают при восстановлении газообразными восстановителями (СО и Н2), полу чаемыми в результате конверсии природного газа. Поэтому наи большую долю ПВЖ и ГБЖ производят страны, имеющие большие запасы природного газа (Мексика, Венесуэлла и др.).
Кнедостаткам методов производства ПВЖ можно отнести склонность ПВЖ к самовозгоранию, низкую абсолютную производи тельность, присутствие в ПВЖ золы и серы угля.
Среди методов твердофазного восстановления оксидов железа с использованием природного газа наиболее распространен процесс Мидрекс. Вторым по распространенности является процесс ХИЛ.
2.1. Процесс Мидрекс
Процесс разработан в 1966 году. Главными агрегатами для реа лизации процесса являются (рис. 2 .1 ): шахтная восстановительная печь для металлизации 6 и риформер (реактор) 9 для получения га зов-восстановителей из природного газа.
Рис. 2.1. Схема процесса Мидрекс:
I - труба для отвода дымовых газов; 2 - подача природного газа для подогре ва рекуператора; 3 - компрессор колошникового газа; 4 - скруббер для очист ки колошникового газа; 5 - загрузочный бункер шихтовых окатышей: 6 - шахтная печь: 6а - зона восстановления, 66 - зона охлаждения; 7 - реку ператор; 8 - подача смеси природного и колошникового газов в риформер:
9 |
- |
риформер; 10 - подача восстановительных газов в шахтную печь: |
II |
- |
добавка природного газа и кислорода к восстановительным газам: |
12 - |
подача природного газа для отопления риформера и науглероживания |
ПВЖ; 13 - компрессор холодного воздуха; 14 - подача нагретого в рекупера торе воздуха в риформер для сжигания природного газа; 15 - дымовые газы; 16- брикетировочный пресс
В риформере осуществляют конверсию природного газа. При этом природный газ вначале разлагают на водород и углерод, а затем дожигают углерод до СО кислородом (кислородная конверсия), уг лекислым газом (углекислотная конверсия) или водяными парами (водяная или паровая конверсия). Процесс проводят в риформере на никелевом катализаторе. Суммарные реакции для различных видов конверсии выглядят следующим образом:
кислородная конверсия: 2СКЦ + 02 = 4Н2 + 2С0; углекислотная конверсия: СН4 + С 02 = 2Н2 + 2С0; паровая (водяная) конверсия: СН4 + Н20 = ЗН2 + СО.
В процессе Мидрекс (см. рис. 2.1) используют углекислотную конверсию, при этом источником С 02 является колошниковый газ шахтной восстановительной печи, который после очистки и охлаж дения в скруббере 4 добавляют к природному газу 2, нагнетая ком прессором 3. Смесь природного и углекислого газов подогревают в рекуператоре 7 и подают в риформер 9, где и происходит образова ние восстановительных газов СО (30...35 %) и Н2 (70...65 %). Обра зовавшиеся восстановительные газы, имеющие температуру 850... 1050 °С, подают в шахтную восстановительную печь. Шахтная печь 6 разделена на две зоны: зону нагрева и восстановления (6а\ в которой протекают процессы восстановления оксидов железа (про цессы металлизации) и зону охлаждения и науглероживания (66) по лученного ПВЖ. Реакции металлизации, протекающие в зоне 6а шахтной печи, аналогичны реакциям косвенного восстановления, протекающим в шахте доменной печи (см. подразд. 3.3.3).
Подогрев рекуператора обеспечивается газами 75, выходящими из риформера. Подогрев риформера осуществляют смесью природного газа 72 и подогретого в рекуператоре воздуха, нагнетаемого воздухо дувной машиной 73. Кроме того, природный газ 72 подают в зону 66 шахтной печи для науглероживания полученного в зоне 6а ПВЖ.
На одной из последних установок Мидрекс на заводе Ispat Mexi can (Мексика) достигнута производительность 1,2 млн т ПВЖ в год.
В России процесс Мидрекс реализован на ОАО «Оскольский электрометаллургический комбинат». Четыре установки Мидрекс имеют суммарную годовую производительность 2 млн т ПВЖ в год.
2.2. Процесс ХИЛ
Процесс разработан в 1957 году. Процесс ХИЛ ведут в четырех ретортах. В определенный момент времени на одной из реторт осу ществляют разгрузку готового ПВЖ и загрузку железорудного сы рья. На второй реторте в это время производят подогрев шихты
и восстановление ее газами, выходящими из третьей и четвертой ре торт, причем предварительно эти газы очищают от паров воды и по догревают. В третьей реторте происходят процессы довосстановления шихты свежим горячим газом-восстановителем, поступающим из риформера, а на четвертой реторте проводят науглероживание по лученного ПВЖ.
В процессе ХИЛ используют паровую (водяную) конверсию природного газа
СН4 + Н20 = ЗН2 + СО.
После осушки восстановительный газ содержит 70...75 % Н2 и 15.. .20 % СО. Степень металлизации ПВЖ - 84...88 %.
Современный вариант процесса ХИЛ, получивший название ХИЛ-Ш, реализуют в противоточном шахтном агрегате, подобном восстановительной печи, используемой в процессе Мидрекс. Техно логия процесса ХИЛ-Ш предусматривает использование восстанови тельного газа с повышенным содержанием водорода (до 87 %), по вышенного давления в реакторе и высокой температуры в зоне вос становления (выше 920 °С). Шихтой для процесса ХИЛ-Ш является смесь окатышей (70 %) и богатой кусковой железной руды (30 %).
В России первая установка ХИЛ-Ш с производительностью 1 млн т ГБЖ в год запущена в строй на ОАО «Лебединский ГОК».
Перспективы развития процессов получения |
ПВЖ связывают |
с подачей подогретой смеси колошникового и |
природного газов |
в зону восстановления шахтной печи. Туда же подают конвертиро ванный восстановительный газ с добавкой кислорода. Для улучше ния газопроницаемости столба шихты газы подают на двух уровнях. Природный газ, попадая в шахту, подвергается авториформингу. Ав ториформинг означает превращение (конверсию) природного газа в смесь газов-восстановителей за счет использования каталитических свойств свежеполученного металлического железа:
СН4 + FeO = F e ^ + 2Н2 + СО.