
книги / Стандартизация
..pdf5.7.2 Допуски калибров
Взаимозаменяемость гладких изделий зависит от единства размеров, допусков и отклонений калибров и применяемых типов калибров. Стандарты на допуски гладких калибров (ГОСТ 24853 и ГОСТ 24852), разработанные в соответствии с рекомендациями ИСО и СЭВ, распространяются на предельные гладкие калибры (пробки и скобы), служащие для контроля отверстий (внутренних размеров) и валов (наружных размеров) с номинальными размерами до 3150 мы и допусками I T 6 - I T H (ГОСТ 25346), а также на контрольные калибры, предназначенные для контроля калибрскоб. Допуски калибров для контроля деталей, допуски которых отличаются от стандартных, но лежат в диапазоне IT6 -1Т\ 7, следует определять по квалитету, допуск которого является ближайшим к нестандартному допуску изделия.
На гладкие калибры установлены следующие допуски на изготовление (рис.5.7.1,5.7.2): я новых калибр-пробок для отверстий (Из тех же калибров, но со сферическими измерительными поверхностями); Я, - новых калибр-скоб для валов; Н р - контрольных калибров для скоб. Допуски на
изготовление калибров зависят от величины допусков на изготовление контролируемых изделий.
При измерении предельными калибрами из-за погрешности их изготовления необходимо сместить настройку (установить приемочные границы) вне поля допуска контролируемой детали. В этом случае производственный (технологический) допуск 1Тг расширяется до гарантированного значения 1Тар
Для всех проходных калибров поля допусков на изготовление Я (Я ,) и Я, смещены внутрь поля допуска IT контролируемого изделия. Положение середины поля допуска калибра определяется величиной отклонения Z (для
калибр-пробок) |
относительно |
наименьшего предельного |
размера |
||
контролируемого |
отверстия |
D min |
и d ^ , (для калибр-скоб) |
относительно |
|
наибольшего предельного размера контролируемого вала d^ . |
|
|
|||
По отклонениям Z и |
Z,, и допускам калибров H ( H S ) |
и Я, |
находят |
границы их полей допусков.
Износ проходных калибров ограничивается допустимым выходом размера изношенного проходного калибра за границу поля допуска контролируемого изделия ( D min и d ^ y При размерах до 180 мм для проходных калибров, контролирующих отверстия и валы квалитетов 6-8, допускается выход размера изношенного калибра за границу поля допуска изделия на величину У и К, соответственно. Для изделий квалитетов 9-17 граница износа проходных калибров совпадает с проходным пределом изделия (у = у, =о). При размерах свыше 180 мм поле допуска непроходного калибра и границы износа проходного калибра смещены внутрь поля
допуска изделия на величины а (для пробок) и а, (для скоб), называемые
безопасными зонами, которые установлены для компенсации погрешностей контроля.
Поля допусков непроходных калибров для размеров до 180 мм симметричны относительно границы поля допуска изделия ( о для пробок и dmn для скоб), т.е., а = а, =0.
Смещение полей допусков калибров и границ износа их проходных сторон внутрь поля допуска детали устраняет возможность искажения характера посадок и гарантирует получение размеров годных деталей в пределах установленных полей допусков.
5.7.3 Расчет исполнительных размеров калибров
Исполнительными называют предельные размеры калибра, по которым изготовляют новый калибр. Они должны иметь допуск в виде одного отклонения, направленного в тело калибра, т.е. как для основного отверстия Я и основного вала h . Поэтому исполнительный размер на чертеже скобы проставляют как наименьший предельный размер с положительным отклонением, на чертеже пробки и контрольного калибра - как наибольший предельный размер с отрицательным отклонением. Исполнительные размеры калибров определяют по формулам (ГОСТ 24853), приведенным в табл. 5.7.4.
Прежде чем рассчитать исполнительные размеры калибров, нужно найти предельные размеры контролируемой детали.
При подсчете исполнительных размеров калибров необходимо пользоваться следующим правилом: размеры рабочих калибров для контроля изделий квалитетов 15-17 следует округлять до целого микрометра; квалитетов 6-14 и всех контрольных калибров - до величин, кратных 0.5 мкм, при этом допуск на калибры сохраняется; размеры, оканчивающиеся на 0.25 и 0.75 мкм, следует округлять до величин, кратных 0.5 мкм, в сторону сокращения производственного допуска изделия.
Таблица 5.7.4 |
Формулы для определения размеров калибров в диапазоне |
||||
|
________ диаметров 180-3150 м |
м __________________ |
|||
Тип калибра |
Рабочий калибр |
|
Контркалибр |
||
Номинальный |
Предельные |
Номинальный |
Предельные |
||
|
размер |
отклонения |
|
размер |
отклонения |
|
Для контроля отверстий D |
|
|
||
Проходной |
|
±" |
|
|
|
|
2 |
|
|
|
новый
< **•
Проходной |
Dmin - Y + а |
|
изношенный |
||
|
Непроходной
Проходной
новый
Проходной
изношенный
проходной
2
А п а х ~ а
<*т>
|
Для контроля валов d |
|
|
|
^ m a x |
+ *L |
^ п и х |
^ 1 |
+ — Е |
2 |
н в |
|||
|
|
|
2 |
|
d ^ + y - C h |
|
|
+ ” Л 1 |
Н в |
|
^ ш а х |
± ---- |
||
|
|
|
|
2 |
d ^ + a |
|
|
|
Н в |
|
2 |
|
|
± — |
|
|
|
2 |
П р и м е ч а н и е Формулы справедливы и в диапазоне размеров до 180 мм, если принять а = а , =0.
Приведем примеры расчета исполнительных размеров калибров, используя формулы табл. 5.7.4.
Пример 5.7.1. Определить размеры калибр-пробок для контроля отверстия 30Я7
По ГОСТ 25347-82 находим предельные отклонения отверстия ES = + 21 мкм; EI = О,
тогда D ш =30.021 |
мм; D = 30 По ГОСТ 24853 для отверстия размером 30 мм, 7 |
квалитета определим допуски и отклонения рабочих калибров, мкм: |
|
Я = 4,Z = 3,У = 3. |
Схема расположения полей допусков соответствует приведенной на |
рис. 5.7.1.
Используя формулы табл. 5.7.4, найдем наибольший размер проходной новой калибр-
пробки: П Р ^ = |
+ Z + -у = 30 +0.003 +у у = 30.005 мм. |
Исполнительный размер калибр-пробки, проставляемый на чертеже, |
|
= (^^шах )-// = 30.005^004 ММ' |
|
Наименьший размер изношенной проходной калибр-пробки |
|
П Р ШН = Dmin - У = 30 - 0.003 = 29.997 мм, |
при достижении которого его нужно изъять из эксплуатации. Наибольший размер непроходной калибр-пробки
пил |
= D Пи л + —^ = 30.021 + ^ |
= 30.023 мм. |
Исполнительный размер калибр-пробки, проставляемый на чертеже |
||
НЕт |
=(Я£га1).„ =30.023^ |
мм |
Пример 5.7.2. Определить размеры калибр-скоб для контроля вала 30кб .
По ГОСТ 25347 находим предельные отклонения вала es = +15 мкм; ei = +2 мкм, тогда ^пих =30.015 мм; d min = 30.002 мм. По ГОСТ 24853 определим допуски и отклонения рабочих калибр-скоб и контрольных калибров, мкм: Я, =4,Z, =3,Яр = 1.5,У =3 мкм.
Схема расположения полей допусков соответствует приведенной на рис. 5.7.2. Наименьший размер проходной новой калибр-скобы
ПРтta = - Z, - у = 30.015-0.003 - у у = 30.01 мм.
Исполнительный размер проходной калибр-скобы, проставляемый на чертеже, П Р " =(ЯРт4п)+// = 30.01*°004 мм.
Наибольший размер изношенной проходной калибр-скобы
ПРm |
=dnax+У, =30.015+0.003 = 30.018 мм, |
|
при достижении которого его нужно изъять из эксплуатации. |
0.004 = 30 мм. |
|
|
j-j |
|
Наименьшийразмер непроходной калибр-скобы H E min = </mjn- —L= 30.002- |
||
|
|
2 |
Исполнительный размер непроходной калибр-скобы, проставляемый на чертеже |
||
НЕисп |
=(НЕтпУ"= ЗО^мм. |
|
Далее |
определяем наибольшие и исполнительные размеры контрольных калибров |
(К-ПР уК-НЕуК-И):
K - n P mu = d m a - Z l + ^ - |
= 30.015 - 0.003 + |
= 30.01275 мм. |
|
К - П Р „„ |
= ( К - П Р ^ ) _ И' |
=30.01275^,, мм. |
|
К - Н Е ^ |
= rf™ + у - = 30.002 + ^ у ^ = 30.00275 мм. |
||
К - Н Е иа, = ( К - Н Е „ |
= 30.003^,00,5 мм. |
|
|
K - H max= d max + Y , + - ^ - = 30.015 +0.003 + |
= 30.01875 мм. |
||
К - К о . |
= ( К - И ^ )_,,г = 30.01875^,5 мм. |
|
При маркировке на калибр наносят номинальный размер с буквенным обозначением поля допуска контролируемой детали, цифровые величины предельных отклонений детали в миллиметрах, тип калибра (например, ПРуНЕуК-И) и товарный знак завода-изготовителя.
На рис. 5.7.3 приведен пример маркировки двухстороннего двухпредельного калибра-пробки 60Я7 и калибра-скобы .
Рис. 5.7.3 Калибр-пробка 60Н 1 (а) и калибр-скоба 25кв (б)
Требования к шероховатости поверхностей гладких калибров (ГОСТ 2015) регламентируются параметры шероховатости Ra (не более указанных значений в микрометрах) в зависимости от наименования поверхности: измерительные поверхности - 10% допуска (соответственно Я ,# ,,# ,,# р), но
не более 0.2 мкм при допусках /ГУ6 - /Г12 и не более 0.4 мкм - свыше /Г12; поверхность заходных и выходных фасок калибров - 1.6; поверхность конуса
60° центровых отверстий и наружных вставок -0.8 мкм; поверхность конуса 1:50 хвостовиков вставок -3.2 мкм и отверстий ручек - 2.5 мкм; остальные обработанные поверхности -3.2 мкм.
5.8. Нормирование отклонений формы, расположения, волнистости и шероховатости деталей.
5.8.1 Отклонения и допуски формы поверхностей. Основные понятия.
Форма большинства деталей, применяемых в машиностроении, представляет собой простейшую геометрическую форму. В основном это цилиндрические детали (70%), плоские (12%), зубчатые колеса (3%) и корпусные детали (4%)[17]. Получить идеальную форму деталей в процессе изготовления невозможно из-за погрешностей станка, инструмента, приспособления, обрабатываемой детали, неоднородности материала и т.п.
Искажение идеальной формы детали приводит к снижению ее эксплуатационных свойств. В неподвижных соединениях, например, искажение формы приводит к неравномерности натягов в соединении, что является причиной снижения передаваемого момента, прочности соединения, точности центрирования, ресурса соединения и т.п. При увеличении нагрузок, что характерно для горных машин, воздействие отклонений формы и расположения усиливается. Отклонения формы и расположения поверхностей могут существенно затруднить сборку изделия (потребовать дополнительные технологические операции, такие, например, как пригонка, что ведет к увеличению трудоемкости сборки, увеличению стоимости изделия), влияют на точность базирования детали при изготовлении и контроле. В подвижных соединениях отклонения формы и расположения приводят к повышению удельного давления на выступах неровностей (площадь контакта уменьшается), увеличения износа сопрягаемых поверхностей, снижают точность центрирования.
Основные термины и определения, относящиеся к отклонениям и допускам формы и расположения поверхностей деталей машин и приборов, устанавливаются ГОСТ 24642.
В ГОСТ 24642 отклонения и допуски формы и расположения поверхностей классифицируются следующим образом:
отклонения и допуски формы поверхностей; отклонения и допуски расположения поверхностей; суммарные отклонения и допуски формы и расположения поверхностей.
Отклонение формы - отклонение формы реальной поверхности или реального профиля от формы номинальной поверхности или профиля.
Под номинальной поверхностью понимается идеальная поверхность, номинальная форма которой задана чертежом или другой технической документацией.
Под реальной поверхностью понимается поверхность, ограничивающая деталь и отделяющая ее от окружающей среды. Как следует из определения, отклонения формы могут рассматриваться и применительно к профилю.
Профиль это линия пересечения поверхности с плоскостью или заданной поверхностью. Если в технической документации не указано подругому, то направление секущей плоскости определяется по перпендикуляру к поверхности. Различают номинальный профиль и реальный профиль.
Номинальный профиль - профиль номинальной поверхности. Реальный профиль - профиль реальной поверхности.
Для наглядности в табл. 5.8.1 приведены отклонения, относящиеся к группе
отклонения и допуски формы поверхностей.
Таблица 5.8.1 Классификация отклонений и допусков формы поверхностей
Наименование отклонения |
Наименование допуска |
Условный знак |
|
|
допуска |
Отклонение от прямолинейности Отклонение от плоскостности Отклонение от круглости Отклонение от цилиндричности
Допуск прямолинейности |
|
Допуск плоскостности |
C J |
Допуск круглости |
Q |
Допуск цилиндричности |
Ч |
|
Отклонение профиля продольного Допуск профиля сечения цилиндрической поверхности продольного сечения
В основу нормирования и количественной оценки отклонений формы и расположения поверхностей положен принцип прилегающих прямых,
плоскостей, поверхностей и профилей. |
|
Прилегающая поверхность |
поверхность, имеющая форму |
номинальной поверхности, соприкасающаяся с реальной поверхностью и расположенная вне материала детали так, чтобы отклонение от нее наиболее удаленной точки реальной поверхности в пределах нормируемого участка было минимальным.
Прилегающий профиль- профиль, имеющий форму номинального профиля, соприкасающийся с реальным профилем и расположенный вне материала детали так, чтобы отклонение от него наиболее удаленной точки реального профиля в пределах нормируемого участка было минимальным.
Прилегающий цилиндр - цилиндр минимального диаметра, описанного вокруг реальной наружной поверхности, или максимального диаметра, вписанного в реальную поверхность.
Допуск отклонения формы и расположения относятся ко всей поверхности (профилю) или длине рассматриваемого элемента, если нормируемый участок не задан.
Нормируемый участок - участок поверхности или линии, к которому относится допуск или отклонение формы или расположения элемента.
Отсчет отклонений формы поверхности производится от прилегающих поверхностей и профилей.
Параметром для количественной оценки отклонения формы является наибольшее расстояние Д от точек реальной поверхности (профиля) до прилегающей поверхности по нормали к последней (рис. 5.8.1) в пределах участка L .
Допуск формы это наибольшее допускаемое значение отклонения формы. Требования, определяемые допуском формы, геометрически поясняются понятием о поле допуска формы.
Реальный профиль
Прилагающий профиль
Рис. 5.8.1 В табл. 5.8.2 приводятся определения отдельных видов прилегающих
поверхностей и профилей и их графическое представление.
Наименование |
|
Таблица |
5.8.2 |
|
Определение |
|
|
прилегающего |
|
|
|
элемента____ |
|
|
|
Прилегающая |
Прямая, |
соприкасающаяся с |
реальным |
прямая |
профилем и расположенная вне материала |
||
|
детали так, чтобы отклонение от нее |
||
|
наиболее |
удаленной точки |
реального |
|
профиля в пределах нормируемого участка |
||
|
имело минимальное значение (Д) |
Прилегающая Плоскость, соприкасающаяся с реальной плоскость поверхностью и расположенная вне материала детали так чтобы отклонение от нее наиболее удаленной точки реальной поверхности в пределах нормируемого участка было минимальным_____________
Прилегающая Окружность минимального диаметра, окружность: описанная вокруг реального профиля
наружной поверхности вращения
для вала
Эскиз
Прилегающая прямая
А< А| А< А3
для отверстия |
Окружность |
максимального |
диаметра, |
r<rt Г<Г2 |
|
вписанная в реальный профиль внутренней поверхности вращения
Прилегающий |
|
|
|
|
|
|
цилиндр: |
Цилиндр |
|
минимального |
диаметра, |
||
для вала |
|
|||||
|
описанный |
вокруг |
реальной |
наружной |
||
для отверстия |
поверхности |
|
|
|
|
|
|
Цилиндр |
|
максимального |
диаметра, |
||
|
вписанный |
в реальную |
внутреннюю |
|||
Прилегающий |
поверхность__________________________ |
|||||
Две |
|
параллельные |
|
прямые, |
||
профиль |
соприкасающиеся с реальным профилем и |
|||||
продольного |
расположенные вне материала деталей так, |
|||||
сечения |
чтобы |
наибольшее |
отклонение |
точек |
||
цилиндрическо |
образующих |
профиля от соответствующей |
||||
й поверхности |
стороны |
прилегающего профиля |
имело |
|||
|
минимальное значение (А) |
|
|
Прилегающий профиль
Реальный профиль Л < Л,
В зависимости от вида допуска формы поле допуска может представлять собой:
1)область в пространстве, ограниченную двумя поверхностями, эквидистандными номинальной поверхности и отстоящими друг от друга по нормали к ним на расстоянии, равном допуску формы поверхности.
2)область в пространстве, ограниченную цилиндром, диаметр которого равен допуску формы оси (линии) в пространстве.
3)область в пространстве, ограниченную прямоугольным параллелепипедом, стороны которого равны допускам формы оси (линии) в двух взаимно перпендикулярных направлениях.
4)область на плоскости заданного направления, ограниченную двумя линиями, эквидистандными номинальному профилю и отстоящими друг от друга по нормали к ним на расстоянии, равном допуску формы профиля.
5.8.2 Отклонения и допуски расположения поверхностей.
Отклонением расположения называется отклонение реального расположения рассматриваемого элемента от его номинального расположения. Под номинальным понимается расположение, определяемое номинальными линейными и угловыми размерами между рассматриваемым элементом и базами.Номинальное расположение определяется непосредственно изображением детали на чертеже без числового значения номинального размера между элементами, когда:
номинальный линейный размер равен нулю (требования соосности, симметричности, совмещения элементов в одной плоскости);
номинальный угловой размер равен 0° или 180° (требование параллельности);
номинальный угловой размер равен 90° (требование перпендикулярности).
Втабл. 5.8.3 приведены отклонения, относящиеся к группе отклонения
идопуски расположения поверхностей.
При определении номинального расположения плоских поверхностей координирующие размеры задают непосредственно от баз. Для поверхностей тел вращения и других симметричных групп поверхностей координирующие размеры обычно задают от их осей или плоскостей симметрии.
|
Таблица 5.8.3 |
Наименование отклонения |
Наименование допуска |
Отклонение от параллельности |
Допуск параллельности |
Отклонение от |
Допуск перпендикулярности |
перпендикулярности |
|
Отклонение от наклона |
Допуск наклона |
Отклонение от соосности |
Допуск соосности |
Отклонение от симметричности |
Допуск симметричности |
Позиционное отклонение |
Позиционный допуск |
Отклонение от пересечения осей |
Допуск пересечения осей |
Условный знак допуска
/ /
_1_
©
—
-Ф- X
Для оценки точности расположения поверхностей, как правило назначают базы.
База - элемент детали (или выполняющие ту же функцию сочетание элементов), определяющий одну из плоскостей или осей координат, по отношению к которой задается допуск расположения или определяется отклонение расположения рассматриваемого элемента.
Базами могут быть, например, базовая плоскость,базовая ось, базовая плоскость симметрии. В качестве базовой оси в зависимости от требований может быть задана ось базовой поверхности вращения или общая ось двух или нескольких поверхностей вращения. В качестве базовой плоскости симметрии может быть задана плоскость симметрии базового элемента или общая плоскость симметрии двух или нескольких элементов. Примеры общей оси и общей плоскости симметрии нескольких элементов приведены в табл. 5.8.4
Иногда для однозначной оценки точности расположения отдельных элементов деталь должна быть ориентирована одновременно по двум или трем базам, образующих систему координат, по отношению к которой задается допуск расположения или определяется отклонение расположения, рассматриваемого элемента. Такая совокупность баз называется комплектом баз.
Базы, образующие комплект баз, различают в порядке убывания числа степеней свободы, лишаемых ими (рис. 5.8.2):
база А лишает деталь трех степеней свободы (называется установочной базой), база В - двух (называется направляющей базой), а база С - одной степени свободы (называется опорной базой).
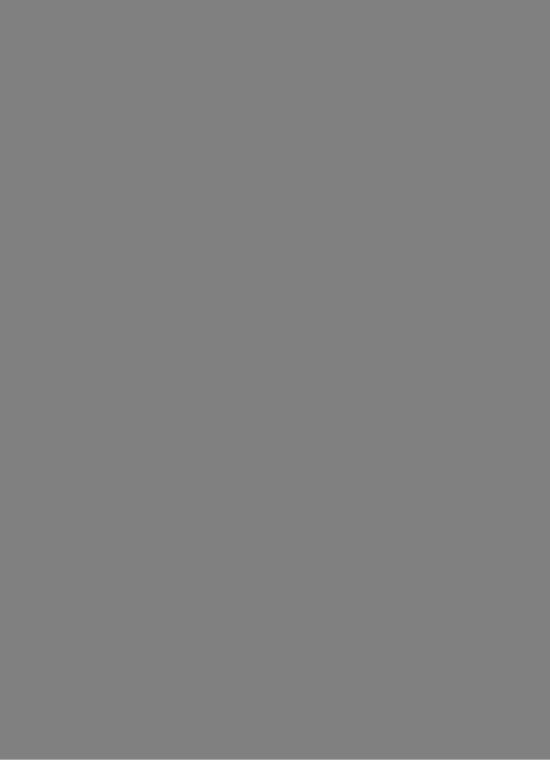