
книги / Машины и оборудование нефтяных и газовых промыслов. Буровые машины и механизмы
.pdf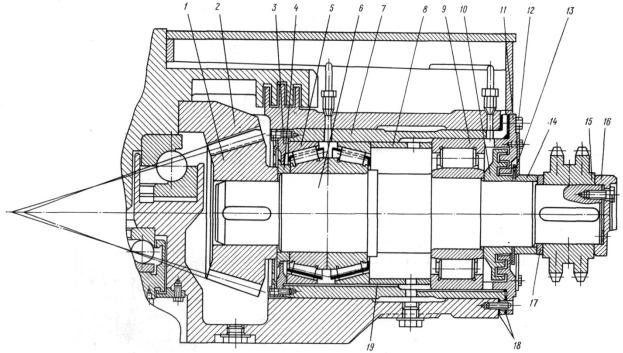
конических подшипников). Поэтому показанная на рис. 11.3 схема установки подшипников 5, когда ролики сходятся в сторону уплотнения и оси их качения скрещиваются вне подшипников (О-образная схема), более предпочтительна. Для предохранения подшипников от перегрева вследствие затруднительной циркуляции масла, находящегося в карманах, образованных подшипниками и уплотнениями крышек, в нижней части стакана имеются продольные каналы 19 для выхода масла в масляную ванну стакана.
Рис. 11.3. Быстроходный вал ротора в сборе
Центральная масляная ванна, образованная между станиной и столом ротора, заправляется жидким маслом через заливное отверстие, которое закрывается пробкой с жезловым указателем уровня масла. Для предохранения центральной масляной ванны от попадания промывочного раствора, разливаемого при спуско-подъемных операциях, между станиной и столом ротора имеются кольцевые лабиринтные уплотнения. Коническая зубчатая пара и подшипники стола смазываются разбрызгиванием масла, захватываемого шестерней при вращении. В связи с этим уровень масла в центральной ванне должен быть выше нижнего контура шестерни.
Смена масла производится после бурения каждой скважины и не реже чем через 2…3 месяца. Для слива отработанного масла в основании корпуса имеются сливные пробки. Перед заливкой свежего масла ванну необходимо промыть керосином. В тех случаях, когда вспомогательный подшипник располагается над зубчатым колесом, смазывать его разбрызгиванием затруднительно. В роторах такой конструкции для смазывания вспомогательного подшипника используют пластичное масло, заправляемое ручным насосом через пружинную масленку.
В роторе, представленном на рис. 11.2, применяется циркуляционная система смазки подшипников и зубчатой пары с помощью плунжерного насоса 16, приводимого от эксцентричной втулки 15 на быстроходном валу 9. Насос забирает масло из маслоотстойника А в станине ротора и по трубкам 5 через кран 17 подает его на верхний подшипник 4. Часть масла стекает на зубчатый венец и смазывает зубчатую пару, а другая часть проходит по каналам и поступает на нижний подшипник 10, с которого стекает в масляную ванну.
191
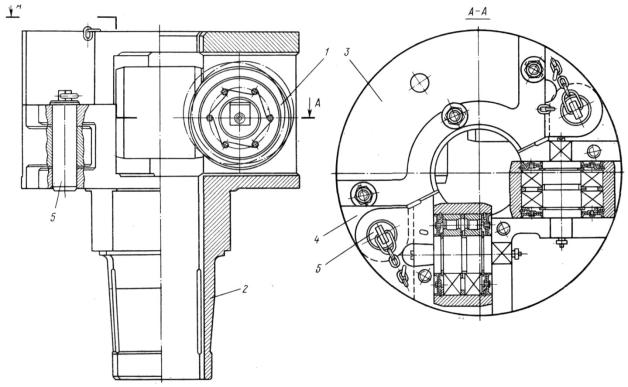
В роторе УР-760 используется стол сборной конструкции, состоящий из полой втулки 1, соединяемой с диском 3 болтами 2 с потайной головкой. Взамен стакана используются переходные гильзы 6 и 8.
Быстроходный вал 6 (см. рис. 11.3) монтируется в стакане 7 на спаренных радиально-упорных конических роликоподшипниках 5, расположенных со стороны шестерни 1, и на радиальном роликовом подшипнике 9, установленном на противоположном конце вала. Конические подшипники обладают высокой жесткостью в радиальном и осевом направлениях. Зеркальное расположение конических подшипников обеспечивает точную двустороннюю фиксацию вала, необходимую для надежной и бесшумной работы передачи. Роликовый подшипник – плавающий и обеспечивает осевое перемещение вала при тепловой деформации.
Рис. 11.4. Роликовый зажим |
|
В фиксирующей опоре внутренние кольца подшипников закреплены |
между |
заплечиком вала и маслоразбрызгивающим кольцом 4, которое упирается в торец шестерни. Наружные кольца подшипников 5 и 9 закреплены между внутренним 3 и наружным 11 фланцами стакана при помощи металлических прокладок и дистанционной втулки 8. Внутреннее кольцо роликового подшипника крепится между заплечиком вала и кольцом 10, затянутым торцовым фланцем 16 через промежуточные детали 13, 14, 15 и дистанционное кольцо 17.
Осевые зазоры подшипников регулируются дистанционными втулками 8, 14 и с помощью набора металлических прокладок 18, установленных между стаканом и его фланцами. Осевой зазор подшипников, контролируемый по осевому смещению вала относительно стакана, должен быть в пределах устраняющих защемление и обеспечивающих равномерное распределение нагрузки между роликами [12].
Надежная и бесшумная работа конической пары обеспечивается при правильном контакте зубьев, достигаемом совмещением вершин начальных конусов колеса 2 и шестерни 1. Зацепление регулируется путем изменения осевого положения шестерни с помощью металлических прокладок 18, выполненных в виде полуколец с прорезями для болтов. Благодаря этому прокладки устанавливаются без разборки уплотняемых
192
деталей путем незначительного отвинчивания болтов 12, достаточного для прохода прокладок. Правильность регулировки зацепления обычно контролируется по пятну контакта зубьев. При сборке роторов пользуются менее точным, но более простым способом контроля – по плавности вращения стола ротора при проворачивании быстроходного вала усилием рук рабочего [1, 12].
Роликовый зажим (рис. 11.4) состоит из корпуса 2 и откидной скобы 3. Корпус и нижняя часть откидной скобы закрываются крышками 4 и скрепляются болтами. Откидная скоба соединяется с корпусом шарниром 5. Верхняя часть корпуса имеет квадратное сечение под размеры квадратного углубления вкладышей. Нижняя часть корпуса снабжена центрирующим цилиндрическим пояском. Цапфы оси роликов 1 устанавливаются в пазы квадратного сечения на вертикальных ребрах корпуса и нижней части откидной скобы. Расстояние между роликами по размеру ведущей трубы регулируется поворотом цапфы осей подшипников. На торцах цапф имеются масленки для смазки подшипников. Техническая характеристика роторов приведена ниже.
При спуско-подъемных операциях зажимы ведущей трубы вытаскивают из ротора, а для удержания колонн труб на роторе используют элеватор либо клиновой захват с пневматическим приводом. По сравнению с элеватором пневматический клиновой захват значительно облегчает и ускоряет спуско-подъемные операции. Поэтому на практике преимущественно распространены роторы, оснащенные пневматическим клиновым захватом (ПКР).
Пневматический клиновой захват (рис. 11.5) состоит из втулки 5, двух конических вкладышей 4, клиньев 2 с плашками 9. Втулка и вкладыши неподвижны относительно стола, а клинья с плашками могут перемещаться по наклонным пазам вкладышей. При перемещении вниз клинья скользят по наклонным пазам вкладышей и сближаются в радиальном направлении. Под действием радиального усилия, возникающего в клиньях от собственного веса колонны, плашки зажимают трубу и колонна удерживается в роторе. Для освобождения зажатой трубы клинья перемещаются вверх одновременно с колонной труб, поднимаемой крюком.
Привод клинового захвата осуществляется при помощи пневматического цилиндра 11, закрепленного на кронштейне станины 12 ротора. Шток пневматического цилиндра соединяется с коротким плечом рычага 10. Длинное плечо рычага на конце имеет вилкообразную форму и надевается на ролики 8 кольцевой рамы 7, с которой соединяются стойки 6, перемещающиеся в вертикальных направляющих пазах втулки 5. Верхние концы стоек укреплены в траверсе 1, которая рычагами 3 соединяется с клиньями 2.
Под действием сжатого воздуха, подаваемого в поршневую полость пневмоцилиндра, шток поршня поворачивает рычаг 10 против часовой стрелки. При этом кольцевая рама 7 вместе со стойками 6, траверсой 1 и рычагами 3 перемещается вверх и поднимает клинья 2. Обратное перемещение клиньев осуществляется при подаче сжатого воздуха в штоковую полость пневмоцилиндра и повороте рычага 10 по часовой стрелке. Рычаги 3 обеспечивают перемещение клиньев в радиальном направлении при подъеме и опускании клиньев. Соотношение плеч рычага 10 выбирается в зависимости от хода поршня пневмоцилиндра и необходимой высоты подъема клиньев.
Вес бурильной колонны, удерживаемой клиновым захватом, ограничивается допускаемым контактным давлением между плашками и телом трубы. Для снижения контактных давлений пользуются удлиненными клиньями и специальными плашками, охватывающими трубу с минимальным зазором между их продольными торцами. В некоторых конструкциях вместо трех используются шесть клиньев, что способствует более равномерному распределению контактных давлений.
193
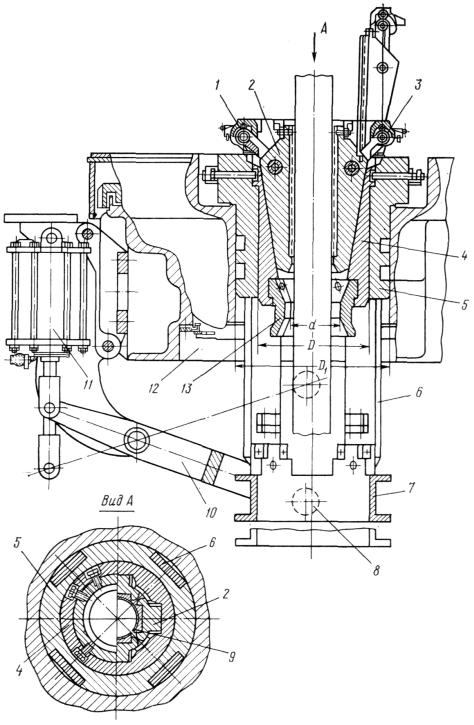
Рис. 11.5. Пневматический клиновой захват ПКР-560
При недостаточной удерживающей способности клиновые захваты заменяются подкладным кольцом (рис. 11.6, а) для установки элеватора либо подкладными клиньями, удерживающими трубу за торец муфты.
Для спуска обсадных труб, диаметр которых больше диаметра конусной втулки, используется подкладное кольцо, заменяющее клинья и конусную втулку (рис. 11.6, б). Пневматический клиновой захват сблокирован с приводом ротора так, что при поднятом клиновом захвате исключается возможность вращения стола ротора. Во время бурения клинья с траверсой убираются и заменяются зажимом под ведущую трубу, а стойки с кольцевой рамой опускаются в крайнее нижнее положение. Управление
194
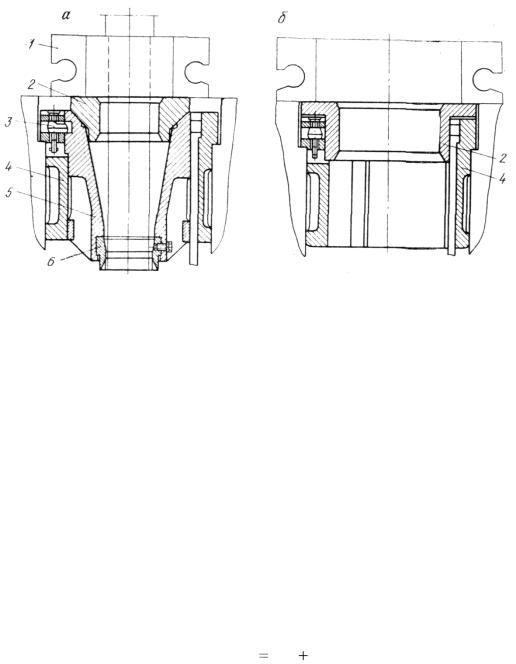
пневматическим клиновым захватом осуществляется педальным краном, установленным у пульта бурильщика.
Рис. 11.6. Оснастка для спуска обсадной колонны:
1 – элеватор; 2 – подкладное кольцо; 3 – защелка; 4 – втулка; 5 – корпусная втулка; 6 – центратор
Роторы имеют групповой либо индивидуальный привод. При групповом приводе ротор соединяется с двигателями буровой лебедки посредством цепных передач, карданных валов и зубчатых редукторов. Индивидуальный привод применяется в электрических буровых установках, предназначенных для бурения скважин глубиной 6000 м и более. Величина крутящего момента, передаваемого ротором, контролируется датчиками, установленными на приводном валу либо в силовых передачах ротора [1].
11.3. Расчет и выбор основных параметров
Параметры ротора определяют, исходя из конструкции скважины, компоновки бурильной колонны и требований, предъявляемых технологиями бурения и крепления скважин.
Диаметр проходного отверстия в столе ротора должен быть достаточным для спуска долот и обсадных труб, используемых при бурении и креплении скважины. Для этого необходимо, чтобы отверстие в столе ротора было больше диаметра долота при бурении под направление:
D Dдн δ , |
(11.1) |
где D – диаметр проходного отверстия в столе ротора, мм; Dдн – диаметр долота при бурении под направление скважины, мм; δ – диаметральный зазор, необходимый для свободного прохода долота, δ = 30…50 мм.
Диаметр долот зависит от конструкции скважин. В глубоких скважинах диаметр направления обычно возрастает вследствие увеличения числа промежуточных колонн. Ниже приведены наиболее распространенные диаметры направлений и долот для бурения скважины под направление.
Глубина скважины, м |
<3000 |
3000–5000 |
5000–8000 |
Диаметр направления, мм |
325–426 |
426–525 |
525–580 |
Диаметр долота, мм |
394–540 |
490–640 |
590–705 |
195
Из приведенных данных следует, что диаметры направлений и соответствующих им долот для рассматриваемых глубин скважин ограничиваются определенными пределами. Благодаря этому можно использовать в буровых установках смежных по глубине бурения классов роторы, имеющие одинаковый диаметр проходного отверстия, и сократить соответственно их номенклатуру.
Проходное отверстие вкладышей стола ротора должно быть достаточным для прохода бурильной колонны при спуско-подъемных операциях. Исходя из наибольших диаметров (203 мм) бурильных замков (ЗШ-203) и утяжеленных бурильных труб, отверстие вкладышей стола роторов всех типоразмеров принято равным 225 мм.
Допускаемая статическая нагрузка на стол ротора должна быть достаточной для удержания в неподвижном состоянии наиболее тяжелой обсадной колонны, применяемой в заданном диапазоне глубин бурения. В большинстве случаев более тяжелыми оказываются промежуточные колонны обсадных труб, вес которых для некоторых конструкций скважины приближается к значению допускаемой нагрузки на крюке буровой установки. Поэтому паспортное значение допускаемой статической нагрузки на стол ротора обычно совпадает с величиной допускаемой нагрузки на крюке, принятой для буровых установок соответствующего класса.
Наряду с этим допускаемая статическая нагрузка не должна превышать статической грузоподъемности подшипника основной опоры стола ротора. Исходя из рассмотренных условий, можно записать:
Gmax ≤ Р ≤ С0, (11.2)
где Gmax – вес наиболее тяжелой колонны обсадных труб, применяемой в заданном диапазоне глубин бурения, кН; Р – допускаемая статическая нагрузка на стол ротора, кН; С0 – статическая грузоподъемность подшипника основной опоры стола ротора, кН.
Подшипники опор стола ротора, как указывалось ранее, подбираются по диаметру проходного отверстия. Основные размеры и ориентировочные расчетные параметры упорно-радиальных шарикоподшипников, применяемых в основной опоре стола буровых роторов, приведены в табл. 11.1.
Таблица 11.1 Основные параметры радиально-упорных шарикоподшипников
буровых роторов
|
Допускаемая статическая нагрузка на стол ротора Р, кН |
|
Размеры подшипника, |
Шарики |
Грузоподъем- |
Запас грузоподъемности, CJP |
||||
|
|
|
мм |
|
ность, т |
|||||
|
|
|
|
|
|
|||||
Тип |
Условное |
|
|
|
|
|
|
|
||
Внутренний диаметр, d |
Наружный диаметр, D |
|
ш |
|
|
Динамическая, С |
||||
обозначение |
|
|
|
|||||||
Высота, H |
Диаметр, D |
|
|
|||||||
ротора |
|
|
||||||||
подшипника |
|
0 |
||||||||
|
|
|||||||||
|
|
Числоz, |
статическая С |
|||||||
УР-560 |
3 200 |
91682/750X |
750 |
1 000 |
150 |
76,2 |
29 |
8 420 |
1 030 |
2,63 |
УР-760 |
4 000 |
1687/770Х |
770 |
1 000 |
150 |
76,2 |
31 |
9 000 |
1 060 |
2,25 |
УР-950 |
6 300 |
1687/1060 |
1 060 |
1 280 |
150 |
63,5 |
48 |
9 670 |
980 |
1,53 |
УР-1260 |
8 000 |
1687/1400 |
1 400 |
1 630 |
150 |
63,5 |
62 |
12 500 |
1 090 |
1,56 |
Из приведенных в табл. 11.1 данных следует, что упорно-радиальные шариковые подшипники, выбранные по диаметру проходного отверстия стола ротора, обеспечивают более чем 1,5-кратный запас по отношению к допускаемой статической нагрузке на стол ротора.
Частоту вращения стола ротора выбирают в соответствии с требованиями, предъявляемыми технологией бурения скважин. Наибольшая частота вращения стола ротора ограничивается критической частотой вращения буровых долот nmax ≤ 250 об/мин. Опыт бурения скважин роторным способом показывает, что при дальнейшем увеличении частоты вращении ухудшаются показатели работы долот.
196
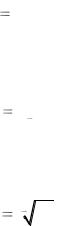
Наряду с этим следует учитывать, что с ростом частоты вращения увеличиваются центробежные силы, вызывающие продольный изгиб бурильной колонны, вследствие которого происходят усталостные разрушения в ее резьбовых соединениях и искривление ствола скважины.
Бурение глубокозалегающих абразивных и весьма твердых пород, забуривание и калибровка ствола скважин проводятся при частоте вращения до 50 об/мин. Для периодического проворачивания бурильной колонны с целью устранения прихватов при бурении забойными двигателями, а также для вращения ловильного инструмента при авариях в скважине требуется дальнейшее снижение частоты вращения стола ротора до 15 об/мин. С учетом этих требований наименьшая частота вращения стола ротора
nmin = 15…50 об/мин.
Отношение предельных значений частоты вращения определяет диапазон ее
регулирования Rn = nmax / nmin.
На скоростную характеристику ротора существенно влияет тип используемого привода. Предпочтительным является электропривод постоянного тока, обеспечивающий бесступенчатое изменение частоты вращения стола ротора в необходимом диапазоне регулирования. При дизельном приводе и электроприводе переменного тока используются механические передачи, осуществляющие ступенчатое регулирование частоты вращения стола ротора. Число скоростей ротора должно быть достаточным для удовлетворения требований бурения. Однако при групповом приводе с буровой лебедкой ротор обычно имеет три-четыре скорости. В этом случае пользуются сменными цепными звездочками, с помощью которых число скоростей ротора может увеличиваться согласно следующей зависимости:
z zкm , |
(11.3) |
где z – число скоростей ротора; zк – число скоростей, передаваемых от буровой лебедки; m – число сменных цепных звездочек на приводном валу ротора.
Промежуточные значения частоты вращения целесообразно выбирать по закону геометрической прогрессии:
ni ni 1φ , |
(11.4) |
где ni и ni-1 – частота вращения стола ротора соответственно на i-й и i–1-й ступени; θ – знаменатель геометрического ряда чисел.
Зная диапазон регулирования Rn и задаваясь числом скоростей ротора z, можно определить знаменатель геометрического ряда:
φ |
z 1 R . |
(11.5) |
|
n |
|
С целью более полного удовлетворения требования бурения диапазон регулирования частоты вращения стола ротора делят на средний и крайние интервалы. В среднем сравнительно узком интервале частота вращения ротора изменяется согласно геометрическому ряду чисел, знаменатель которого меньше, чем у крайних интервалов диапазона регулирования. Благодаря этому в среднем интервале уменьшается разница между смежными частотами вращения стола ротора, что позволяет точнее согласовывать частоту вращения долота с требованиями бурения.
Для обратного вращения (реверса) достаточно одной или двух передач, обеспечивающих вращение стола ротора с частотой 15…50 об/мин, необходимой для работы с трубами и ловильным инструментом, имеющими левую резьбу. При электрическом приводе вследствие реверсирования двигателей ротор имеет одинаковые частоты при прямом и обратном вращении.
В процессе проектирования привода ротора и особенно группового привода буровой лебедки и ротора возможны отклонения окончательно принятых значений частоты вращения стола ротора от расчетных, обусловленные конструктивными соображениями. Следует также отметить, что при дизель-гидравлическом приводе
197
благодаря турботрансформатору частота вращения ротора изменяется по непрерывноступенчатой кривой.
Мощность ротора должна быть достаточной для вращения бурильной колонны, долота и разрушения забоя скважины:
N = (Nx.в + Nд) / η, |
(11.6) |
где Nx.в – мощность на холостое вращение бурильной колонны, кВт; Nд – мощность на вращение долота и разрушение забоя, кВт; η – КПД, учитывающий потери в трущихся деталях ротора.
Мощность на холостое вращение бурильной колонны (момент, передаваемый долоту, равен нулю) расходуется на преодоление сопротивлений вращению, возникающих в системе «бурильная колонна–скважина». Сопротивление вращению зависит от длины и диаметра бурильной колонны, плотности промывочной жидкости в скважине, трения труб о стенки скважины. Сопротивление вращению изменяется в зависимости от кривизны и состояния стенок скважины, пространственной формы бурильной колонны, вибраций, вызванных трением и центробежными силами.
Экспериментально установлено, что с увеличением частоты вращения мощность на холостое вращение бурильной колонны возрастает в степенной зависимости. Наряду с этим на мощность холостого вращения бурильной колонны влияет ряд случайных и трудно учитываемых факторов, возникающих при бурении скважины (крутильные колебания, обвал стенок скважины, образование каверн, искривление ствола скважины, изменение пространственной формы бурильной колонны и др.).
Расчеты показывают, что на каждые 1000 м бурильной колонны расход мощности на холостое вращение (частота вращения 100 об/мин, плотность раствора 1,2 г/см3, угол искривления 3…5°) составляет:
Диаметр труб, мм |
114 |
127 |
141 |
168 |
Мощность Nx.в , кВт |
8,8 |
10,9 |
13,6 |
19,1 |
Мощность, расходуемая на вращение долота и разрушение забоя скважины, рассчитывается по следующей формуле, учитывающей влияние типа долота:
где μ0 – |
|
Nд=μ0PnRср , |
|
|
(11.7) |
|||
коэффициент сопротивления долота; Р – осевая нагрузка |
на долото, кН; |
|||||||
n – частота вращения долота, с-1; Rср – средний радиус долота, м. |
|
|
||||||
|
Коэффициент сопротивления долота имеет следующие значения: |
|||||||
|
|
|
|
|
|
|
|
|
|
Долото |
|
Алмазное |
|
Твердосплавное и |
|
Шарошечное |
|
|
|
|
|
|
режущего типа |
|
|
|
|
μ0 |
|
0,2…0,4 |
|
0,4…0,8 |
|
0,2…0,4 |
|
Средний радиус долота Rср=Dд/3.
В процессе бурения скважины происходит непрерывно-ступенчатое изменение потребляемой ротором мощности. Это обусловлено последовательным увеличением длины бурильной колонны, ступенчатым уменьшением диаметра используемых долот, а также изменением режимов бурения по мере углубления скважины. В теоретических расчетах, выполняемых при выборе мощности ротора, так же, как и при расчете бурильной колонны на прочность, осевая нагрузка на долото, частота его вращения и плотность промывочной жидкости, характеризующие режим бурения, принимаются неизменными для каждого размера долот, используемых при бурении скважин заданной конструкции. Расчетные значения указанных параметров бурения выбирают на основе
198

эмпирических зависимостей и опытных данных, полученных при бурении скважин аналогичных конструкций.
В предварительных расчетах частоту вращения стола ротора в зависимости от текущей и конечной глубины бурения вычисляют по эмпирической зависимости:
n 200 150 |
L |
, |
(11.8) |
|
L |
||||
|
|
|
||
|
к |
|
|
где L и Lк – соответственно текущая и конечная глубина скважины.
Плотность промывочной жидкости, учитываемая при расчете мощности, которая расходуется на холостое вращение бурильной колонны, определяется по формуле:
ρ = 0,21 lg L+ l,25, |
(11.9) |
где L – глубина скважины, м.
На основе указанных зависимостей определяют мощности, необходимые для бурения скважины под направление, кондуктор, промежуточные и эксплуатационную
колонны. По наибольшей полученной величине выбирают |
расчетную мощность |
ротора. |
|
Максимальный вращающий момент (кН∙м) определяют по мощности и |
|
минимальной частоте вращения стола ротора: |
|
Mmax = Nη/nmin, |
(11.10) |
где N – мощность ротора, кВт; η – КПД ротора; nmin – минимальная частота вращения, об/мин.
Максимальный вращающий момент ограничивается прочностью бурильной колонны и деталей, передающих вращение столу ротора.
Базовое расстояние, измеряемое от оси ротора до первого ряда зубьев цепной звездочки на быстроходном валу ротора, используется при проектировании цепной передачи, передающей вращение от лебедки ротору [1].
11.4. Монтаж и эксплуатация роторов
Надежная работа ротора во многом зависит от правильности его монтажа и эксплуатации. Обычно ротор устанавливают в пазах вышечного основания. Горизонтальность стола следует выверять по уровню. Центр проходного отверстия должен строго совпадать с геометрической осью скважины.
При монтаже ротора с приводом от лебедки цепной передачей необходимо обращать внимание на то, чтобы ведущее колесо на валу лебедки и ведомое цепное колесо на ведущем валу ротора находились в одной плоскости без перекоса. Параллельное смещение допустимо не более чем 0,5 мм на 1 м длины межцентрового расстояния.
Расстояние от выходного фланца превентора или обсадной колонны до нижнего торца втулки стола ротора должно быть не менее 600 мм. При монтаже ротора необходимо проверить наличие и качество смазки в его корпусе. Затем следует вручную провернуть стол ротора на несколько оборотов. Стол должен проворачиваться усилием одного рабочего: если стол свободно вращается (без заеданий), то его надо проверить на холостое вращение от силового привода в течение 15…20 мин, наблюдая за плавностью работы и температурой.
Первые 2–3 дня эксплуатации нового ротора необходимо особенно тщательно следить за температурой и уровнем смазки. Качество смазки надо проверять в течение всего времени эксплуатации ротора. Повышение температуры корпуса ротора выше 80 °С недопустимо.
Менять масло и промывать ротор следует в соответствии с заводской инструкцией. Если в масляной ванне будет обнаружен раствор или грязь, то корпус ротора должен быть опорожнен и промыт, после чего может быть восстановлена работа.
199
Если в процессе работы ротора наблюдаются рывки, чрезмерный нагрев, стук или другие неполадки, то работа ротора должна быть прекращена. Ротор надо заменить другим или его следует отремонтировать, устранить дефекты, после чего повторить его опробование.
Уход за ротором в процессе эксплуатации заключается в следующем:
–систематическая обмывка ротора снаружи и удаление раствора и грязи;
–проверка состояния стопорного механизма;
–осмотр вкладышей и зажимов ведущей трубы (защелки должны свободно перемещаться от усилия руки);
–проверка легкости вращения стола;
–крепление болтов и подтяжка гаек;
–смазка цепи трансмиссии и проверка состояния ограждения;
–проверка уровня и качества масла в картере.
При монтаже и демонтаже ротора необходимо соблюдать предосторожности: поднимать и перемещать ротор надо в горизонтальном положении, захватывая его в трех точках за рамы корпуса, во избежание переворачивания, что может привести к травмированию рабочих.
Карта смазки ротора приведена в табл. 11.2. Зубчатая передача и опоры ротора смазываются из общей ванны или масляным насосом под давлением. Масло в картер заливают через отверстие, закрываемое пробкой. В пробку вставляют щуп, с помощью которого определяют уровень масла в ванне. В некоторых конструкциях роторов подшипники ведущего вала смазывают из другой ванны или консистентной смазкой. Менять масло и пополнять ванну необходимо в соответствии с заводской инструкцией
[6, 12].
|
|
Карта смазки ротора |
Таблица 11.2 |
|
|
|
|
||
|
|
|
|
|
|
|
Период смазки |
|
|
Место смазки |
лето |
зима |
Указание по смазке |
|
|
|
|||
|
|
|
|
|
Зубчатая коническая |
Масло |
индуст- |
Масло индуст- |
В ванну заливают масло в |
передача, главная и |
риальное И-50А |
риальное И-12А |
соответствии с инструк- |
|
вспомогательная |
(ГОСТ 20799–75) |
(ГОСТ 20799–75) |
цией. Пополнение ванны |
|
опоры |
|
|
|
по мере надобности. Кон- |
|
|
|
|
троль уровня щупом еже- |
|
|
|
|
дневно. Смена масла не |
|
|
|
|
реже одного раза в 2 мес. |
Картер приводного |
То же |
То же |
|
|
вала |
|
|||
|
|
|
|
|
Вспомогательная |
Смазка |
универсальная средне- |
Пополнение по 0,5 л 1 раз |
|
опора и подшипни- |
плавкая УС-3 (ГОСТ 1033–79) |
в неделю |
||
ки приводного вала |
|
|
|
|
12. ВЕРТЛЮГИ И БУРОВЫЕ РУКАВА
12.1. Назначение и схемы
Вертлюг предназначен для подвода бурового раствора во вращающуюся бурильную колонну. В процессе бурения вертлюг подвешивается к автоматическому элеватору либо к крюку талевого механизма и посредством гибкого шланга соединяется со стояком напорного трубопровода буровых насосов. При этом ведущая труба бурильной колонны соединяется с помощью резьбы с вращающимся стволом вертлюга, снабженным проходным отверстием для бурового раствора. Во время спуско-
200