
книги / Машины и оборудование нефтяных и газовых промыслов. Буровые машины и механизмы
.pdf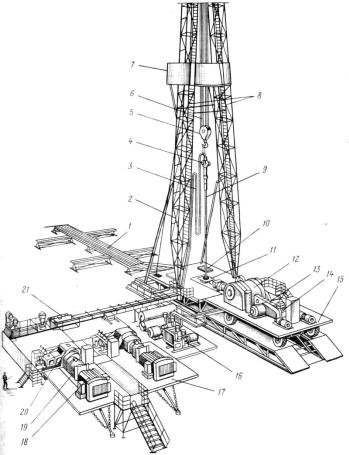
вышечного, лебедочного, насосного, компрессорного блоков, циркуляционной системы и стеллажей для труб 1. Основание вышечного блока служит для установки на нем мачты 2 (со стояком и гибким шлангом 3, вертлюгом 4, крюкоблоком 5, талевым канатом 6, балконом 7 и лестницами 8), ротора 11 и пакетов 10 свечей или обсадных труб. Буровая лебедка 12 с коробкой передач 13, электродвигателем 14 привода и шкафами управления расположены на отдельном основании 15.
На основании насосного блока 17 находятся два насоса НБТ-375 20 с регулируемыми электродвигателями 19 и станциями их управления 18. Компрессорная станция 16 и циркуляционная система 21 с оборудованием для очистки и приготовления бурового раствора представляют собой отдельные блоки.
Рис. 2.4. Буровая установка БУ1600ЭУ:
1 – стеллажи для бурильных труб; 2 – мачта; 3 – буровой шланг; 4 – вертлюг; 5 – крюкоблок; 6 – талевый канат; 7 – балкон; 8 – лестницы; 9 – бурильные трубы;
10 – подсвечники для размещения бурильных труб; 11 – буровой ротор; 12 – буровая лебѐдка; 13 – КПП буровой лебѐдки; 14 – приводной электродвигатель буровой лебѐдки; 15 – основание буровой лебѐдки; 16 – компрессорная станция; 17 – основание насосного блока; 18 – станция управления двигателем бурового насоса; 19 – двигатель бурового насоса; 20 – буровой насос; 21 – циркуляционная система
Все основное и вспомогательное оборудование смонтировано на металлических основаниях, что позволяет перевозить установку с точки на точку в собранном виде на колесных или гусеничных тележках. Это значительно сокращает сроки монтажа и демонтажа установки. Крепления блоков между собой, элементов манифольда, трубопроводов на блоках и в местах стыковки имеют быстроразъемные соединения и
31
компенсаторы длины. В отдельных случаях установка может разбираться и перевозиться универсальным транспортом.
Схема установки обеспечивает простоту конструкции и оперативность управления механизмами. В соответствии с принятой схемой лебедка и ротор приводятся в движение от одного электродвигателя мощностью 300 кВт с частотой вращения 750 об/мин через фрикционную муфту МШ и цепную коробку передач. При отключении электроэнергии бурильные трубы 9 на безопасную высоту можно поднимать при помощи аварийного вспомогательного привода, работающего от электростанции установки.
Лебедка и ротор имеют шесть прямых и обратных скоростей от основного и вспомогательного приводов. Скорости лебедки изменяются путем переключения муфты МШ в коробке перемены передач. Барабан лебедки включается с помощью сдвоенной муфты МШ, расположенной с противоположной стороны от пульта бурильщика. Вспомогательный тормоз включается кулачковой муфтой. Буровые насосы, компрессоры, вибросита, вспомогательная лебедка, шламовые насосы имеют самостоятельные индивидуальные приводы. Масса всей установки 185 т [6].
2.7. Установки для бурения структурно-поисковых скважин
Структурно-поисковые скважины на нефть и газ глубиной 25–3000 м бурят с целью изучения геологической структуры площади, а также для установления расположения пластов-коллекторов на выявленной структуре. Диаметр этих скважин значительно меньше диаметра эксплуатационных. Конечный диаметр поисковой скважины обычно составляет 76–146 мм. В подавляющем большинстве случаев бурят роторным способом с использованием бурильных труб диаметром 50–89 мм. При проводке скважины отбирается большое количество образцов породы – кернов.
К установкам этого типа предъявляют требование значительно большей универсальности, чем к установкам для глубокого эксплуатационного бурения. Допустимая нагрузка на крюке таких установок в зависимости от глубины и конструкции скважины составляет 10…800 кН. Кинематическая схема их мало отличается от схем буровых установок, предназначенных для бурения роторным способом эксплуатационных и глубоких разведочных скважин. Однако конструктивно эти установки значительно различаются.
Структурно-поисковые скважины в большинстве случаев проводят в легкобуримых породах. Условия проходки часто не требуют резервирования оборудования, поэтому в установках для структурно-поискового бурения применяют один двигатель и один буровой насос. Это допустимо, так как вес бурильных колонн обычно такой, что при остановке двигателя колонна может быть приподнята на безопасное расстояние вращением лебедки вручную.
Поскольку время, затрачиваемое на проходку структурно-поисковых скважин, обычно небольшое, а расстояние между скважинами значительное, то установки транспортируют на пневматических шинах или гусеничном ходу. Некоторые установки для бурения скважин до 600 м выполняются самоходными и только с автономным приводом (с двигателями внутреннего сгорания), так как в большинстве случаев бурение ведется в районах, где нет электроэнергии.
В легких установках для неглубокого бурения используют иногда даже двигатель автомашины или трактора, на котором смонтирована установка. В этих установках применяют вышки мачтового типа высотой 6…23 м. В большинстве случаев вышки мачтового типа транспортируют одновременно с установкой. Вышки высотой более 16 м – телескопические.
Для роторного бурения с выносом выбуренной породы промывочной жидкостью или газом существует несколько типов буровых установок. Установки с допустимой нагрузкой на крюке 100 кН для бурения на глубине до 100 м выполняются в различных
32
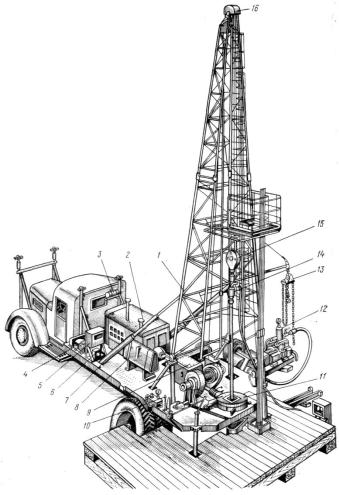
модификациях, при этом выбуренная порода удаляется продувкой или промывкой в труднобуримых породах и механическим способом (при помощи шнеков) в рыхлых легкобуримых породах. Если колонна вращается, выбуренная порода поднимается шнеком. Бурение шнеками не требует применения воды и растворов, дает хороший геологический материал. Недостатки этого способа – трудность и неэффективность бурения в твердых породах. Для бурения с продувкой воздухом или работы с пневматическим инструментом установки снабжаются компрессором.
Установки для бурения скважин глубиной до 600 м снабжаются механизмами подачи для создания дополнительной нагрузки на породоразрушающий инструмент, так как вес труб малых диаметров недостаточен для создания требуемых нагрузок. В этом случае часто применяют гидравлические устройства. Гидравлические домкраты широко используются также для подъема мачт, извлечения шнеков и других устройств. В качестве источника гидравлической энергии применяют масляные насосы, имеющие привод от трансмиссии или электродвигателей.
Рис. 2.5. Буровая установка УРБ-ЗАМ для бурения разведочных скважин:
1 – мачта; 2 – двигатель; 3 – бензобак пускового двигателя; 4 – генератор; 5 – щит; 6 – реостат; 7 – домкрат; 8 – топливный бак; 9 – КПП; 10 – дроссель домкратов; 11 – ротор; 12 – насос; 13 – вспомогательная таль; 14 – вертлюг; 15 – талевый блок; 16 – кронблок
Установки для бурения скважин глубиной свыше 100 и до 1000 м с допустимой нагрузкой на крюке до 200 кН выполняются самоходными на шасси автомашин и тракторов или на прицепных тележках и салазках.
33
Установки для бурения поисковых скважин глубиной 1200…3000 м с допустимой нагрузкой на крюке 320…800 кН обычно предназначены для роторного способа. Их монтируют на рамах-салазках, они состоят из нескольких блоков. Эти установки не только по схеме, но и по конструкции и характеристикам приближаются к установкам, предназначенным для бурения неглубоких эксплуатационных скважин.
Состав оборудования и схема установки для структурно-поискового бурения мало отличаются от установок для глубокого эксплуатационного бурения. Все оборудование монтируется на платформе колесного, гусеничного прицепа, автомашины или трактора.
На рис. 2.5 показана буровая установка УРБ-ЗМА для бурения структурнопоисковых скважин глубиной до 500 м с максимальной нагрузкой на крюк до 80 кН. Все узлы установки смонтированы на платформе автомобиля. Буровой насос, глиномешалку и бак устанавливают на отдельной платформе.
Мощность от ДВС через карданный вал и клиноременнуго трансмиссию передается на контрпривод насоса или на КПП. От КПП мощность и движение через цепную трансмиссию передаются на лебедку, а от нее на талевую систему. Неподвижный конец каната закреплен в приспособлении с индикатором веса. К талевому блоку подвешен вертлюг с ведущей трубой. Привод бурильной колонны осуществляется ротором, приводимым во вращение карданным валом от КПП.
Для бурения геофизических скважин глубиной до 60 м используют установку УШ-2Т, предназначенную для шнекового бурения. Эта установка смонтирована на тракторе Т-130БГ-1 и приводится в действие от его двигателя. Мачта установки телескопическая с гидравлическим подъемом на высоту до 9 м. Вдоль мачты расположены два вертикальных вала. Один вал передает вращение от блока привода через зубчатую муфту к верхнему редуктору, приводящему во вращение через второй ведущий вал вращатель бурового шнека или другого породоразрушающего инструмента [6].
3. ПОРОДОРАЗРУШАЮЩИЙ ИНСТРУМЕНТ
3.1. Общие сведения
При бурении нефтяных и газовых скважин используются следующие виды породоразрушающего инструмента:
–буровые долота для бурения скважины сплошным забоем;
–бурильные головки для бурения скважин кольцевым забоем;
–расширители для расширения ствола скважины;
–калибраторы, стабилизаторы, центраторы для выравнивания стенок скважины и центрирования бурильной колонны.
По характеру разрушающего действия на породу буровые долота и бурильные головки разделяются на дробяще-скалывающие (шарошечные), режуще-скалывающие (лопастные) и истирающе-режущие (алмазные).
Стойкость долота определяется временем, в течение которого долото изнашивается до предельного состояния, когда его дальнейшее применение недопустимо или нецелесообразно. Стойкость долота измеряется в часах и зависит от таких же факторов, как износ. На износ и, следовательно, на стойкость долота наибольшее влияние оказывают частота вращения долота, осевая нагрузка, подача и качество промывочного раствора, определяющие режим бурения в заданных геологотехнических условиях.
Стойкость долота также значительно зависит от физико-механических свойств и качества используемых материалов, вооружения и промывочных устройств долота, точности изготовления и других конструктивных и технологических факторов. По уровню циклических нагрузок, сочетанию различных видов износа (абразивного, ударно-абразивного, коррозионного, усталостного) буровые долота находятся в
34
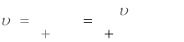
наиболее неблагоприятных условиях по сравнению с другим оборудованием, применяемым в бурении. Вместе с тем никакое другое оборудование в бурении так существенно не влияет на сроки и себестоимость строительства скважин, как долота.
Важные показатели работы долота – проходка на долото и механическая скорость бурения. Проходка измеряется в метрах ствола скважины, пробуренных долотом от его спуска до подъема вследствие износа, поломок и других отказов. Механическая скорость бурения
υм = h / t, |
(3.1) |
где h – проходка на долото, м; t – продолжительность работы долота на забое, ч. Одновременное увеличение проходки на долото и механической скорости
способствует повышению темпов углубления скважины, характеризуемых рейсовой скоростью бурения:
р |
h |
|
м |
, |
(3.2) |
|
|
||||
|
t tСПО |
|
1 tСПО / t |
|
|
где tСПО – продолжительность спуско-подъемных операций, выполняемых при смене долота и наращивании бурильной колонны, ч.
Важно отметить влияние проходки и механической скорости долота на работу наземного бурового оборудования. Увеличение проходки на долото способствует уменьшению объема спуско-подъемных операций за период бурения скважины. При повышении механической скорости бурения сокращается занятость буровых насосов, вертлюга и ротора в строительстве скважины. В результате этого снижаются энергетические затраты и расход быстроизнашиваемых узлов и деталей подъемного механизма и оборудования циркуляционной системы буровых комплексов.
Независимо от назначения, конструкции и типа диаметры буровых долот должны быть согласованы с диаметрами бурильных и обсадных труб, а также забойных двигателей [1].
3.2. Шарошечные долота
Шарошечные долота наиболее распространены. На их долю приходится 90…95 % всего объема проходки скважин. Шарошечные долота для сплошного бурения скважин изготовляются трех видов: одношарошечные, двухшарошечные и трехшарошечные.
Шарошки долот имеют три вида вооружения (рис. 4.1):
– с фрезерованными зубьями, составляющими одно целое с телом шарошки (для долот типов М, МС, С, СТ, Т, ТК);
– со вставными (твердосплавными) зубьями (для долот типов МЗ, СЗ, ТЗ, ТКЗ, К, ОК);
– со вставными зубками и фрезерованными зубьями (для долот типа МСЗ).
По расположению и конструкции промывочных или продувочных каналов долота изготовляются:
–с центральной промывкой – Ц;
–с боковой гидромониторной промывкой – Г;
–с центральной продувкой – П;
–с боковой продувкой – ПГ. Опоры шарошек изготовляются:
–на подшипниках с телами качения – В;
–на двух и более подшипниках скольжения – А;
–на одном подшипнике скольжения (остальные подшипники качения) – Н;
–с герметизацией уплотнительными кольцами и резервуаром для смазки – У.
35
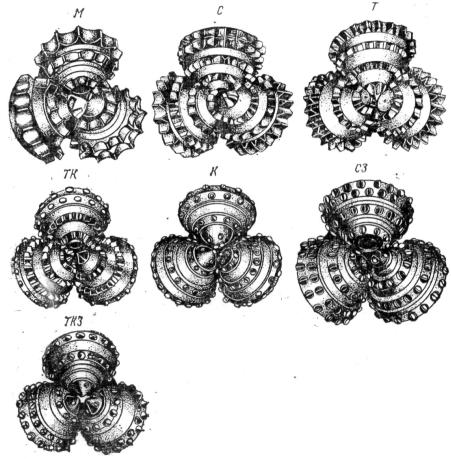
Рис. 3.1. Долота шарошечные
Всего предусмотрено 39 размеров шарошечных долот диаметром от 46 до 508 мм. В наиболее широком ассортименте и количестве изготовляются долота диаметрами 190 (190,5) мм и особенно 214 (215,9) мм. Это объясняется сравнительно большим объемом проходки и многообразием физико-механических свойств горных пород.
Диаметр и основные конструктивные признаки буровых долот указываются в условном обозначении. Например, обозначение долота Ш-215,9СЗ-ГНУ-2 расшифровывается следующим образом: трехшарошечное (Ш), диаметром 215,9 мм, для бурения абразивных пород средней твердости (СЗ), с боковой гидромониторной промывкой (Г), с герметизированной, маслонаполненной опорой на одном подшипнике скольжения, остальные подшипники с телами качения (ГНУ), 2 – номер заводской модели.
То же долото, изготовленное по лицензии США, имеет условное обозначение Ш-215,9СЗ-ГНУ-Р16, в котором буква Р означает, что долото изготовлено по импортной технологии, 16 – порядковый номер сборки.
Шарошечные долота изготовляются с цельнолитым либо сварным корпусом. Долота с цельнолитым корпусом, называемые корпусными, состоят из литого
корпуса с приваренными к нему лапами, на цапфах которых смонтированы свободно вращающиеся шарошки. В корпусе имеются отверстия для насадок, через которые промывочная жидкость поступает на забой скважины. Для соединения с бурильной колонной корпус долота снабжается муфтовой замковой резьбой.
Корпусные конструкции используются для долот диаметром более 394 мм. Долота со сварным корпусом, называемые секционными, имеют
преимущественное распространение в мировой практике. Корпус секционных долот (рис. 3.3.) сваривается из предварительно собранных секций, число которых равно
36
числу шарошек долота. Каждая секция состоит из лапы 1 с косой цапфой 2 и конусообразной шарошки 4, вращающейся на подшипниках 3.
Шарошки различаются по числу образующих конусов, геометрии и типу вооружения. Двух- и трехшарошечные долота комплектуются многоконусными шарошками, на поверхности которых концентрическими рядами (венцами) располагается вооружение (зубья, зубки). Венец, расположенный у основания шарошки, называется периферийным. Нумерация венцов на шарошке начинается с ее вершины. Шарошки нумеруются от наиболее высокой с минимальным числом зубьев на первом венце до низкой с наибольшим числом зубьев на первом венце.
В плане шарошки размещаются со смещением осей относительно оси долота в направлении вращения долота. В вертикальной плоскости угол между осью долота и осями вращения шарошек изменяется в пределах 52…57°. Для повышения износостойкости зубья наплавляются твердым сплавом. Вставные зубья имеют сферическую либо клиновидную форму рабочего торца. В зависимости от типоразмера долота вставные зубья имеют диаметр 3,2…14,3 мм. Одношарошечные долота комплектуются сферическими шарошками, оснащенными вставными твердосплавными зубьями.
Для бурения твердых малоабразивных, хрупких и хрупкопластичных пород используются долота типа Т, оснащенные двух- и трехконусными самоочищающимися шарошками, оси которых пересекаются в одной точке на оси долота. Шарошки снабжены мелкими зубьями с большим углом заострения (рис. 3.2, а).
Долота типа К, применяемые для бурения самых твердых и крепких абразивных пород, оснащаются одноконусными самоочищающимися шарошками с твердосплавными зубками (рис. 3.2, б).
Долота типа М для бурения мягких пород имеют двухили трехконусные самоочищающиеся шарошки с осями цапф секций, смещенными относительно оси долота в сторону его вращения (рис. 3.2, в). Зубья шарошек отличаются большой высотой и длиной и небольшим углом заострения. Увеличение угла наклона оси шарошек к оси долота (55…57°30') позволяет вписать в долото шарошки большого диаметра.
Долота типа С для бурения пород средней твердости имеют двух- и трехконусные самоочищающиеся шарошки с короткими острыми зубьями (рис. 3.2, г).
На основании обобщения данных эксплуатации установлены следующие средние показатели проходки на долото в зависимости от его типа:
Тип долота |
М |
С |
Т |
К |
Проходка, м |
50 |
30 |
20 |
15 |
Общая особенность долот всех типов – снижение проходки на долота с уменьшением его диаметра [1].
У самоочищающихся долот зубья одной шарошки заходят во впадины смежной шарошки. Двух- и трехконусные конструкции шарошек позволяют усилить опоры долот. Смещение осей цапф относительно оси долота вызывает скольжение зубьев шарошек по поверхности забоя. Поэтому долота со смещенными осями наряду с дробящим действием скалывают породу. Шарошки буровых долот устанавливаются на многорядных подшипниках качения и скольжения. Вследствие ограниченных размеров шарошек в долотах используются безобойменные бессепараторные подшипники качения.
Отверстие для центральной промывки выполняется в виде круглого сквозного канала, просверленного по оси долота. Поток промывочной жидкости из бурильной колонны по каналу долота направляется к центру забоя. Распыляясь на мелкие струи, жидкость очищает забой и поднимает кусочки разрушенной породы по зазорам между
37
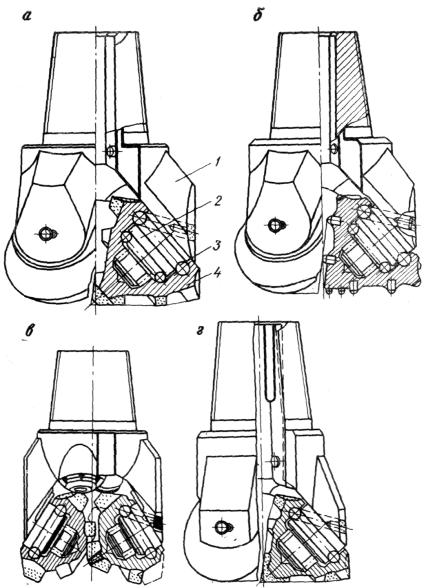
стенками лап и скважины в затрубное пространство и далее на поверхность. При центральной промывке хорошо очищаются от шлама центр забоя и вершины шарошек.
Рис. 3.2. Шарошечные секционные долота
Отверстия для боковой промывки просверливаются в специальных приливах (бобышках) лап. Струи промывочной жидкости направляются на забой между зубьями шарошек. Эффективность боковой промывки возрастает с увеличением скорости истечения жидкости. Для этой цели промывочные каналы оснащаются профилированными насадками, преобразующими потенциальную энергию жидкости (давление) в кинетическую (скоростной напор) струи. Высокоскоростное истечение жидкости (120 м/с и более) улучшает очистку забоя и создает эффект динамического воздействия струй на забой (гидромониторный эффект).
Эффективность гидромониторного воздействия зависит не только от скорости истечения, но и от направления струи. Напор пропорционален квадрату скорости истечения жидкости, поэтому при использовании гидромониторных насадок значительно возрастает давление буровых насосов. В связи с этим для бурения гидромониторными долотами требуются более мощные и надежные буровые насосы. Насадки гидромониторных долот изготовляют из износостойкого керамического
38
алюмооксидного материала 2ХС. Каноидальная форма проходного сечения насадки обеспечивает компактную струю и сравнительно небольшие потери напора.
Таблица 3.1
Причины аномального износа шарошечных долот
Состояние отработанного |
Возможные причины аномального износа |
|
долота |
||
|
||
|
Неправильный выбор долота. |
|
Большое число |
Неправильная приработка долота. |
|
Чрезмерно высокая частота вращения. |
||
сломанных зубьев |
||
Чрезмерно большая нагрузка на долото. |
||
|
||
|
Работа по металлу. |
|
Большое число |
Эрозия тела шарошки. |
|
Чрезмерно большая нагрузка на долото. |
||
потерянных зубьев |
||
Слишком продолжительное время механического бурения. |
||
|
||
|
Чрезмерно высокая частота вращения. |
|
Сильный износ по |
Слишком продолжительное время механического бурения. |
|
диаметру |
Сдавливание шарошек в результате спуска в ствол |
|
|
уменьшенного диаметра. |
|
|
Большое содержание твердой фазы в промывочной |
|
Эрозия тела шарошки |
жидкости. |
|
Чрезмерный расход промывочной жидкости. |
||
|
||
|
Долото предназначено для более твердых пород. |
|
|
Чрезмерно высокая частота вращения. |
|
|
Чрезмерно большая нагрузка на долото. |
|
Чрезмерный износ опор |
Слишком продолжительное время механического бурения. |
|
Чрезмерно большое содержание песка в промывочной |
||
|
жидкости. |
|
|
Отсутствие стабилизаторов над долотом и (или) между УБТ. |
|
|
Чрезмерно большая нагрузка на долото. |
|
Закупорка межвенцовых |
Недостаточный расход промывочной жидкости. |
|
промежутков в шарошках |
Большое содержание твердой фазы в промывочной |
|
разбуренной породой и |
жидкости. |
|
твердой фазой |
Долото предназначено для более твердых пород. |
|
|
Спуск долота в заполненную шламом призабойную зону. |
В секционных шарошечных долотах в отличие от корпусных используется ниппельная присоединительная резьба. Шарошечные долота диаметрами 46 и 59 мм имеют правую цилиндрическую резьбу. Долота диаметром 76 мм и более имеют правую коническую резьбу, профиль и размеры которой совпадают с замковой резьбой бурильных труб. Некоторые причины аварийного выхода из строя шарошечных долот представлены в табл. 3.1 [2, 7].
3.3. Лопастные и алмазные долота
Лопастные долота делятся на следующие типы: двухлопастные 2Л; трехлопастные истирающе-режущие ЗИР; шестилопастные истирающе-режущие 6ИР; пикообразные (однолопастные) П.
Лопастные долота отличаются от шарошечных более простой конструкцией и успешно их заменяют при бурении рыхлых, мягких и несцементированных пород. При бурении абразивных пород средней твердости лопастные долота менее эффективны, а для бурения твердых и крепких пород непригодны. Они применяются в основном при
39
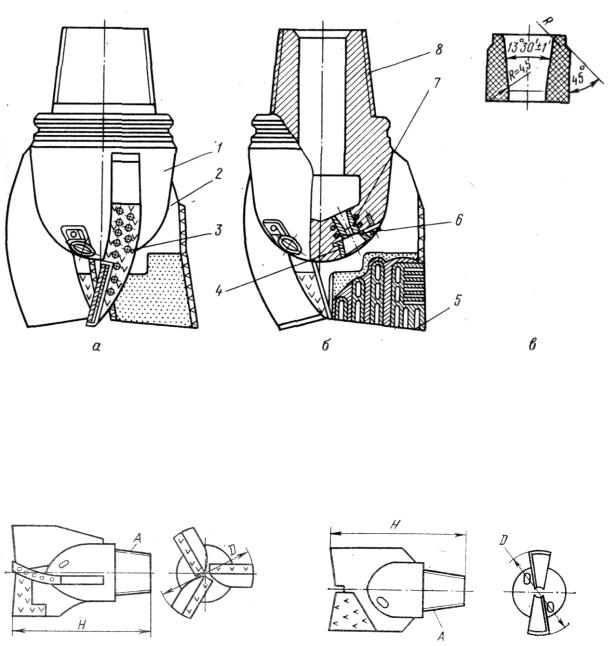
роторном бурении, при бурении забойными двигателями используются реже, так как для их работы необходимы большие крутящие моменты.
На рис. 3.3. показана конструкция трехлопастного долота ЗЛ, состоящего из корпуса 1 и приваренных к нему лопастей 2, изготовляемых из стальных поковок. Промывочное устройство состоит из сопла 7, уплотнительных колец 6, байонетной шайбы 4 для удержания сопла. Рабочие и калибрующие поверхности лопастей упрочняются твердосплавными штырями 3 и пластинами 5. Для соединения с бурильной колонной на головке корпуса имеется замковая резьба 8.
Рис. 3.3. Трехлопастное долото: а – общий вид; б – разрез; в – сопло
Трехлопастные долота (рис. 3.4) выпускаются диаметрами 118…445 мм. Двухлопастные долота 2Л (рис. 3.6) изготавливают цельноковаными, и они не имеют сопел в промывочных отверстиях. Выпускаются двухлопастные долота диаметрами от
76 до 165,1 мм.
Рис. 3.4. Долото трехлопастное |
Рис. 3.5. Долото двухлопастное |
Долота истирающе-режущего типа (рис. 3.6) используются для бурения мягких, среднемягких и средних абразивных пород. В отличие от долот 2Л и ЗЛ их лопасти имеют ступенчатую форму. Калибрующая поверхность и режущие кромки лопастей армируются твердосплавными штырями и покрываются релитом. Предусматривается изготовление долот ЗИР диаметрами 190,5…269,9 мм. Долота диаметром более 140 мм выпускаются с гидромониторной и обычной промывкой.
40