
книги / Машины и оборудование нефтяных и газовых промыслов. Буровые машины и механизмы
.pdf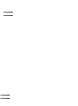
(окружном) u и радиальном. Однако поскольку размер лопастей турбин турбобуров мал по сравнению со средним диаметром турбины, можно пренебречь изменениями в потоке жидкости вдоль радиуса и рассмотреть планы скоростей по двум осям: на направлении переносной скорости и на цилиндрической поверхности со средним диаметром Dср и в осевом направлении cz. На рис. 4.7. показаны планы скоростей в осевой решетке лопастей турбины. Окружная скорость на среднем диаметре Dcp лопаток определяется по формуле:
|
u = πDcpn. |
(4.2) |
Конструктивные углы наклона профиля лопаток на выходе статора обозначим α1, |
||
на входе – α2, на входе ротора – β1 |
и на выходе – β2. В турбинах турбобуров применяют |
|
густые решетки, и угол наклона α1 |
абсолютной скорости с1 |
приблизительно равен углу |
наклона лопастей статора. |
|
|
Направление относительной скорости ω зависит от соотношения скоростей u1 и c1. Построим треугольник скоростей в координатах u2 и c1 в точке истечения из ротора на входе в статор нижележащей ступени (координаты u2 = u1 и cz2 = cz1). Относительная скорость истечения жидкости с лопатки ротора направлена под углом β2 между направлением кромки профиля лопатки ротора и вектором окружной скорости. На рис. 4.7, б показано совмещение этих двух треугольников скоростей, по которым можно судить об изменении циркуляции потока.
При движении поток жидкости направляется в каналы статора, неся с собой определенный запас энергии, представленный в виде давления. По всей высоте канала статора происходит трансформация давления в скоростной напор. При этом весь поток к концу канала статора вследствие поворота лопаток ротора начинает вращаться вокруг оси турбины. Статор вырабатывает в потоке к моменту его истечения винтовой вихрь, осью которого является ось турбины, а напряжение вихря потока зависит от скорости циркуляции его вокруг этой оси. Скорость циркуляции потока, созданная в статоре,
cст |
с1u πDср , |
(4.3) |
скорость циркуляции потока в роторе |
|
|
cрт |
с2u πDср , |
(4.4) |
где с1u и с2u – проекции скоростей потока, с1u = c1 cos α1; с2u = c2 cos α2; с1 и с2 – абсолютные скорости, с1 = cz / sin α1; с2 = cz / sin α2.
Вращающийся ротор турбины, принимая винтовой вихрь, снижает величину его напряжения, создавая некоторый вращающийся момент. Лопатки статора, закручивая поток вокруг оси турбины, воспринимают направленный в противоположную сторону реактивный момент и передают его на неподвижный корпус турбобура. В многоступенчатой аксиальной турбине напряжение вихря потока, отработанного в ступени ротора, равно напряжению вихря потока на входе в статор следующей расположенной ниже ступени и т. д.
Эффективная мощность турбины пропорциональна суммарному возбужденному в ступенях ротора крутящему моменту, умноженному на угловую скорость вращения ротора. Таким образом, чем больше амплитуда изменения давления потока в ступенях статора и ротора, тем больше создаваемый на роторе рабочий момент и тем ниже можно получить угловую скорость вращения вала турбины при одной и той же ее мощности.
При небольшом отношении радиальной ширины каналов турбины к среднему радиусу rср можно считать, что средний момент скорости по сечению равен среднему
51
моменту скорости по окружности радиусом rср. Тогда из уравнений теории турбин Эйлера получим приближенный момент, развиваемый одной ступенью турбины (Н∙м),
M = ρQ (c1u – c2u) rср , |
(4.5) |
где ρ – плотность жидкости, кг/м3; Q – расход жидкости, м3/с; rср – средний радиус ступени, м. Мощность турбины (Вт)
N=Mω, |
(4.6) |
где ω – угловая скорость ротора турбины, ω = πn/30, с-1; n – частота вращения ротора, об/мин.
Мощность, развиваемая одной ступенью турбобура,
N = ∆pстQ, |
(4.7) |
где ∆рст – эффективный используемый перепад давления на ступени турбины, МПа,
∆pст = N/Q. |
(4.8) |
Для турбобуров с числом ступеней k мощность и вращающий момент будут в k раз больше.
Для тихоходных турбин турбобуров с большим вращающимся моментом требуется создание значительной амплитуды колебания циркуляции, а следовательно, большой разности проекций скоростей потока c1u – с2u.
Для оценки этих качеств турбобуров введены понятия:
– коэффициент циркулятивности турбин
c u=(c1u – c2u) / u, |
(4.9) |
где u – окружная скорость потока;
– коэффициент расхода ступени
c z = cz/u, |
(4.10) |
где cz – осевая скорость потока.
С увеличением разности проекций скоростей потока возрастает вращающий момент, развиваемый каждой ступенью; с уменьшением окружных скоростей снижается частота вращения.
Высокий коэффициент циркулятивности c u имеют тихоходные турбины с большим вращающим моментом. Быстроходные турбины имеют низкий коэффициент циркулятивности и небольшой вращающий момент. В современных турбобурах применяют высокоциркулятивные турбины с небольшим расходом, но при высоком напоре.
В реальных условиях поток жидкости в каналах турбин турбобуров неодинаков и неоднороден. При работе турбобура скорость и давление жидкости в любой точке потока изменяются без определенной закономерности, что вызвано неравномерностью нагрузки на валу при бурении и колебаниями подачи насосов. Форма же лопаток статора и ротора турбины постоянна, и она должна быть такой, чтобы обеспечивать достаточно высокий КПД при различных режимах работы.
При изменении скоростей потока у входа в каналы ротора и выхода из него изменяются стороны треугольников скоростей. В зависимости от конструкции турбины
52
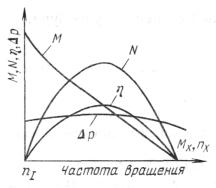
все стороны треугольника скоростей, т.е. векторов абсолютных, относительных и
окружных |
скоростей, |
могут |
изменяться |
либо |
пропорционально, |
либо |
непропорционально. В последнем случае нет подобия между геометрическими |
и |
|||||
динамическими требугольниками |
скоростей. |
Турбина будет работать в режиме с |
низким КПД вследствие ударного течения вихревого потока жидкости. Наиболее благоприятен безударный режим без интенсивного вихреобразования на лопатках.
При замедлении вращения происходит вихреобразование с тыльной стороны профиля (зона на рис. 4.7.), а при увеличении скорости u вихреобразование происходит на лицевой стороне лопатки (зона S'). Наиболее благоприятные условия для уменьшения гидравлических потерь обеспечиваются при плавном и безотрывном обтекании лопатки потоком с обеих сторон.
Характеристика турбин при постоянном расходе жидкости показана на рис. 4.8. кривыми зависимости момента М, перепада давления ∆р, мощности N и КПД η от частоты вращения n при постоянном значении расхода жидкости Q с определенными свойствами (плотность ρ и вязкость μ). Для построения кривых используются формулы (4.5) – (4.6). По этим формулам могут быть определены характеристики каждой ступени, а характеристики всего турбобура пропорциональны числу ступеней k.
Рис. 4.8. Характеристика турбины турбобура при постоянном расходе жидкости
Гидравлический КПД пропорционален мощности:
η=Nk / Q∆p. (4.11)
Режим работы турбобура при максимальном КПД ηmax называется оптимальным. Наиболее устойчивая и эффективная работа турбобура при экстремальном режиме, т.е. при наибольшей мощности. В многоступенчатых турбинах экстремальный и оптимальный режимы почти совпадают. Гидравлический КПД турбины определяется потерей мощности при прохождении жидкости в каналах турбины. Эти потери зависят от шероховатости поверхности лопаток, их формы, утечек в зазорах между дисками турбины.
Характеристики турбин различных конструкций неодинаковы, поэтому существует много модификаций и конструкций турбобуров. Для снижения частоты вращения и перепада давления при режиме холостого хода в турбобурах с высокоциркулятивными турбинами устанавливаются клапанные устройства для отвода части потока от турбины и сохранения заданного перепада давления. Для регулирования экстремальной частоты вращения используются решетки гидроторможения и др. [6].
4.6. Эксплуатация турбобуров
Для эффективного использования турбобура его диаметр и тип следует выбирать в зависимости от конкретных условий бурения. Наружный диаметр турбобура должен быть на 25…30 мм меньше диаметра долота. Требования к характеристике турбобура и
53
числу его секций определяются условиями обеспечения необходимого режима работы долота.
Эффективность бурения во многих случаях зависит от соотношения величины гидравлической мощности, подводимой к долоту и турбобуру. Количество прокачиваемой жидкости определяется типом и размером долота, а не характеристикой турбобура, который является средством для привода долота во вращение. Опора турбобура должна допускать любую осевую нагрузку, которая требуется для работы долота. Полезная мощность насосной установки:
Nнп = Nд+Nбк+Nт+Nзп, |
(4.12) |
где Nд – мощность, подводимая к долоту (50–60 % полезной мощности насосов); Nбк – мощность, затрачиваемая на прокачку жидкости через бурильную колонну; Nт – мощность, затрачиваемая на вращение вала турбобура; Nзп – мощность, затрачиваемая на прокачку жидкости в затрубном пространстве и на подъем выбуренной породы (5–10 % полезной мощности).
Таким образом, Nбк и Nт должны составлять 30…45 %. Гидравлическая мощность, расходуемая в турбобуре,
Nт= (0,5…0,6)Nнп – Nбк. |
(4.13) |
При постоянном давлении на выходе насосов рн = const наибольшая мощность будет подведена к долоту, когда перепад давления на турбобуре
∆рт=1/3(рн – ∆рбк – ∆рзп), |
(4.14) |
где ∆рбк – потери давления в бурильной колонне и манифольде; ∆рзп – потери давления в затрубном пространстве. Мощность на валу турбобура
Nт = ∆pтQη, |
(4.15) |
где η – общий КПД турбобура; Q – расход жидкости.
Для выбора турбобура и определения необходимых параметров и режима работы буровых насосов делают расчеты или определяют их параметры по номограммам, чтобы обеспечить оптимальные параметры прокачивания раствора через долото с учетом необходимых мощности и давления на турбобуре и количества раствора в остальных элементах циркуляционной системы.
Надо иметь в виду, что высокая эффективность использования турбобура обеспечивается его надежностью, что закладывается в процессе его конструирования, обеспечивается качественным изготовлением и техническим обслуживанием.
При транспортировке турбобура на буровую должна быть обеспечена его сохранность. Во избежание засорения турбины и повреждения резьб турбобур необходимо транспортировать с предохранительными пробками и колпаками. Транспортировка турбобуров волоком и сбрасывание их при разгрузке недопустимы.
Перед соединением секций турбобура на буровой их проверяют. Элементы турбобура с видимыми дефектами и повреждениями к сборке не допускаются.
Поступивший из турбинного цеха турбобур допускается к эксплуатации при следующих условиях:
–осевой люфт 2 мм для турбобуров с резинометаллической осевой опорой и не более 0,4 мм с шаровой осевой опорой;
–величина подъема вала в верхних секциях находится в соответствии с указанной
винструкции;
54
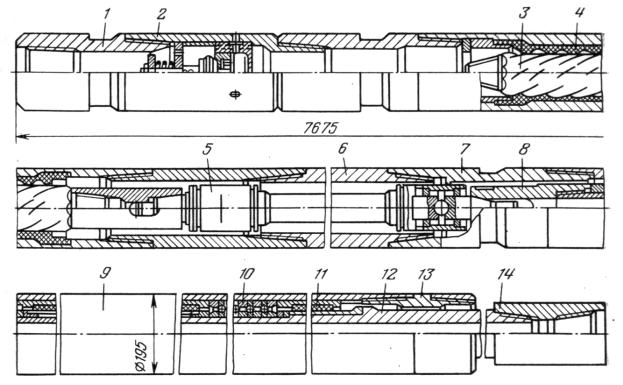
–перепад давления в турбобуре соответствует паспортному;
–все резьбовые соединения герметичны при прокачке раствора, расход которого соответствует паспортному.
Перед спуском в скважину вал турбобура проверяют на легкость вращения, проворота его ключом при моменте не более 200 Н∙м. Целесообразно перед спуском турбобур опробовать над столом ротора. Запускаться он должен при давлении 1…1,5 МПа. Перепад давления необходимо фиксировать в его паспорте и буровом журнале. При опробовании турбобур должен работать без рывков и плавно останавливаться при прекращении подачи раствора.
В процессе работы необходимо следить за изменением люфта вала. В процессе бурения турбобур может остановиться вследствие перегрузки, снижения подачи насосов или неисправности. В первых двух случаях необходимо попытаться турбобур запустить, разгрузив опору, приподняв его над забоем, и довести подачу до установленной паспортом. Если запустить не удалось, турбобур поднимают на поверхность и устраняют неисправность или направляют на ремонт.
Отработанный турбобур укладывают на мостки, и на корпусе делают пометку «на ремонт». К нему прикладывают заполненный паспорт, в котором указывают номер буровой, даты начала и конца его работы, время работы в часах, интервал бурения, параметры бурового раствора и причины отказа [6].
4.7. Винтовые гидравлические двигатели
Винтовой двигатель представляет собой забойный агрегат (рис. 4.9) с гидравлическим объемным двигателем, приводимый в действие потоком бурового раствора, который закачивается в бурильную колонну с поверхности насосами.
Рис. 4.9. Винтовой забойный двигатель Д1-195:
1, 6, 7 – верхний, средний и нижний переводники; 2 – переливной клапан; 3 – ротор; 4 – статор; 5 – двухшарнирное соединение; 8 – соединительная муфта; 9 – корпус шпинделя; 10 – многорядная упорная шаровая опора; 11 – радиальный подшипник; 12 – вал шпинделя; 13 – ниппель; 14 – наддолотный переводник
55
Винтовой двигатель состоит из статора и эксцентрично расположенного винтового ротора, представляющего собой как бы зубчатую пару с внутренним зацеплением с винтовыми зубьями. Число зубьев статора на один больше зубьев ротора, что позволяет ему совершать планетарное движение, обкатываясь по зубьям статора: ось ротора при этом движется по окружности диаметром, равным двойному эксцентриситету е. Для соединения ротора с валом шпинделя, соосно расположенного с корпусом, служит шаровая двухшарнирная муфта, компенсирующая эксцентриситет.
Шпиндель винтового двигателя сходен по конструкции со шпинделем турбобура. Он укреплен на радиальных резинометаллических подшипниках и снабжен шаровой пятой для восприятия осевой нагрузки. Вал шпинделя – пустотелый, в верхней части снабжен каналами для прохода жидкости к долоту, присоединяемому через переводник к нижней части вала двигателя. Корпус последнего через переводник прикрепляется к нижней части бурильной колонны.
По принципу действия винтовые двигатели относятся к объемным роторным машинам. Основными элементами рабочих органов таких машин являются:
–статор – корпус с полостями, примыкающими по концам и камерам высокого и низкого давления;
–ведущий ротор – винт, вращающий момент которого передается валу шпинделя; Винтовые поверхности статора и ротора делят рабочий объем двигателя на ряд
полостей. Полости, связанные с областями высокого и низкого давления, называются камерами, а замкнутые полости – шлюзами. В поперечном сечении имеются камеры, разделенные между собой контактной линией. Каждая камера по мере вращения периодически связывается с полостями высокого и низкого давления и в каждый заданный момент времени становится шлюзом. Теоретически на длине одного шага происходит разобщение полостей, находящихся выше и ниже рабочих органов.
Поверхности винтовых зубьев ротора и статора, взаимно пересекаясь, отсекают область высокого давления жидкости от области низкого давления и препятствуют ее свободному перетоку. Под действием перепада давления жидкости на ведущем винте образуется вращающий момент, передаваемый на вал шпинделя. Чем больше перепад давления на двигателе, тем больше вращающий момент. По принципу действия винтовой двигатель можно сравнить с поршневым гидравлическим двигателем, снабженным поршнем, который перемещается вдоль оси ротора по винтовой линии. Роль поршня выполняют отсекающие поверхности винтового ротора.
Винтовые двигатели и насосы имеют ряд преимуществ, что позволило использовать их как гидравлические забойные двигатели:
–отсутствие клапанных и золотниковых распределителей потока жидкости;
–отсутствие относительного перемещения трущихся деталей пары «ротор – статор»;
–непрерывное изменение положения линии контакта рабочих органов при вращении ротора позволяет потоку бурового раствора удалять абразивные частицы из камер и шлюзов.
Условия создания шлюзов в паре «ротор – статор» объемных винтовых двигателей следующие:
–число зубьев или заходов статора z1 должно быть на единицу больше зубьев
ротора z2;
– отношение шага зубьев статора Т к шагу зубьев ротора должно быть пропорционально отношению их числа, т.е.
T / t = z1/z2. |
(4.16) |
Отношение чисел зубьев статора и ротора называется передаточным числом:
56
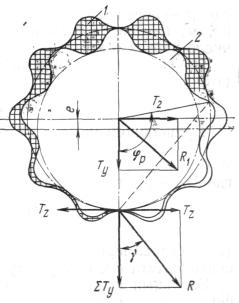
uп = z1 / z2. |
(4.17) |
Теоретически винтовой двигатель может иметь любое передаточное число.
Основные параметры винтовых двигателей
Винтовые двигатели имеют разные передаточные числа, зависящие от
соотношения числа зубьев ротора и статора. Двигатели, |
имеющие uп = 1:2, развивают |
||
максимальные |
частоты |
вращения и минимальные |
вращающие моменты. Их |
применяют, когда требуется |
высокая частота вращения. |
|
Рис. 4.10. Поперечный разрез винтового двигателя Д2-172М:
1 – статор; 2 – ротор (заштрихованные полости заполнены жидкостью высокого давления, незаштрихованные – жидкостью низкого давления)
По мере увеличения числа заходов ротора (т.е. передаточного отношения) уменьшается частота вращения и увеличивается вращающий момент. Это объясняется тем, что многозаходный роторный механизм, каким является винтовой двигатель, в отличие от других механизмов представляет собой соединение гидравлического двигателя и понижающего планетарного редуктора, причем передаточное число редуктора пропорционально заходности ротора.
Многозаходные рабочие органы имеют большую протяженность контактных линий по сравнению с рабочими органами, имеющими отношение uп = 1 : 2. Это предопределяет снижение механического и общего КПД винтовых двигателей с многозаходными рабочими органами. В то же время двигатели с многозаходными рабочими органами обладают большой нагрузочной способностью и более жесткой характеристикой, что обусловило выбор для забойного винтобура Д2-172М передаточного числа uп = 9 : 10.
Вращающий момент – основная характеристика винтового двигателя. При анализе его рабочего процесса рассматривается действие перепада давления жидкости в камерах пары «ротор – статор», так как на этой длине происходит разобщение камер с полостями высокого и низкого давления, расположенных выше и ниже рабочих органов. В каждом поперечном сечении на длине шага ротора возникает неуравновешенная гидравлическая сила R1, действующая на центр вращения ротора
(рис. 4.10).
57
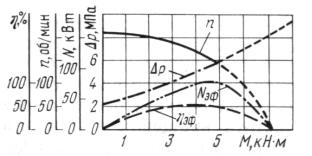
Характеристика забойного винтового двигателя
Энергетические параметры винтового гидравлического двигателя определяются его передаточным числом, перепадом давления и расходом рабочей жидкости. При постоянном расходе Q двигатель характеризуется изменением вращающего момента М от перепада давления Ар, частоты вращения n вала шпинделя, мощности N и КПД η.
На рис. 4.11. приведена рабочая характеристика винтового забойного двигателя Д2-172М.
Наибольшая частота вращения соответствует режиму холостого хода, а максимальный вращающий момент – режиму торможения при n = 0. Двигатель запускается при перепаде давления ∆p = l–2 МПа. Это давление расходуется на механические и гидравлические потери. При увеличении момента торможения перепад давления возрастает, одновременно повышаются мощность и КПД.
Режим максимальной мощности называется эффективным, а наивысшего КПД – оптимальным. Обычно в этих двигателях они не совпадают. Зона устойчивой работы двигателя находится между этими режимами. В рабочем режиме гидромеханический КПД составляет 0,4…0,5, объемный – 0,8…0,9, а общий достигает 0,5…0,55. При достижении предельного момента торможения вал двигателя останавливается, а величина давления определяется герметичностью пары «ротор – статор». При нарушении герметичности раствор протекает через двигатель.
Рис. 4.11. Рабочая характеристика винтового двигателя Д2-172М при постоянном расходе раствора
В рабочей области от режима холостого хода до оптимального частота вращения n прямо пропорциональна расходу Q, поэтому при изменении расхода Q1 на Q2 частота вращения определяется по формуле:
n2 = n1Q2 / Q1. |
(4.18) |
С увеличением расхода раствора диапазон устойчивой работы двигателя расширяется. В винтовых двигателях частота вращения существенно зависит от величины вращающего момента. В этих двигателях по мере их износа характеристики ухудшаются. Это объясняется повышением утечек жидкости через зазоры по мере их увеличения при износе. Износ ротора и статора по выступам и профилю зубьев приводит к нарушению герметичности рабочей пары, увеличению объемных потерь и снижению нагрузочной характеристики. Износ рабочей пары определяет межремонтный срок службы двигателя, составляющий 50…200 ч в зависимости от качества двигателя и свойств бурового раствора [6].
4.8. Электробуры
Электробур служит для привода во вращение долота. Он представляет собой забойный агрегат с электрическим двигателем трехфазного переменного тока. Электроэнергия к нему передается с поверхности по кабелю, расположенному внутри колонны бурильных труб. Оборудование на установке при бурении электробуром
58
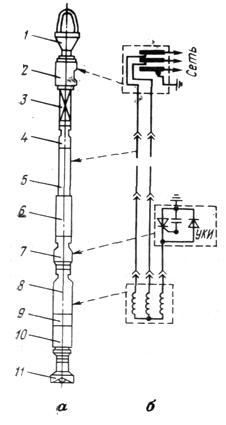
применяется в основном такое же, как и при бурении роторным или турбинным способом. Электробурами бурят скважины глубиной до 5000 м.
Несколько отличной является схема электроснабжения электробуровой установки. Силовой трансформатор мощностью 630 кВ∙А с номинальным током 155 А имеет две вторичных обмотки. Одна из них служит для питания электробура и имеет 25 ступеней регулирования напряжения в пределах 1100…2300 В. Другая вторичная обмотка напряжением 525 В предназначена для питания электродвигателей привода лебедки и ротора.
На установке применяется дополнительно комплектное устройство для включения и защиты электробура, измерения электрических параметров и сигнализации о состоянии электробура. Это устройство состоит из станции управления, навесных шкафов, вольтметра и трех амперметров, блока измерения сопротивления изоляции системы «токопровод – электробур» и кнопки для включения и выключения электробура.
На рис. 4.12, а показана компоновка бурильной колонны с электробуром, состоящая из асинхронного трехфазного электродвигателя 8 переменного тока с короткозамкнутым ротором, редуктора-вставки 9 для снижения частоты вращения, шпинделя 10 для восприятия осевых нагрузок, к которому присоединяется долото 11. Двигатель электробура соединен с устройством 7 для контроля его изоляции (УКИ).
Рис. 4.12. Схема питания электробура по системе два провода – труба
В бурильную колонну также входят УБТ 6 и бурильные трубы 5, обратный клапан 4, ведущая труба 3, внутри которых расположен кабель, подводящий электроэнергию к электробуру. Ток к электровертлюгу 2 поступает от силового трансформа тора. Бурильная колонна соединена с обычным вертлюгом 1, подвешенным на крюке к талевой системе буровой установки.
На рис. 4.12, б показана схема подвода тока к электробуру по системе «два провода – труба» (ДПТ), третий провод электродвигателя соединен через УКИ с колонной труб.
59
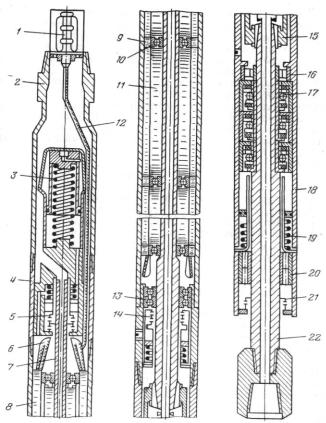
Давление на долото для разрушения породы так же, как и при роторном бурении, создается нижней частью бурильной колонны, которая воспринимает реактивный момент. Разбуренная порода выносится на поверхность буровым раствором по кольцевому пространству между стенками скважины и бурильной колонной. Буровой раствор, нагнетаемый насосами через вертлюг внутрь колонны бурильных труб с кабелем, подводится к электродвигателю и по его пустотелому валу через отверстия в валах редукторной вставки и шпинделя поступает к долоту. Двигатель, редуктор и подшипники шпинделя наполнены маслом и имеют систему защиты от проникновения внутрь бурового раствора.
Преимуществами электрического двигателя по сравнению с гидравлическим являются: независимость частоты вращения от нагрузки на долото, момента и других параметров от количества подаваемой жидкости, ее плотности и физических свойств и глубины скважины; постоянство частоты вращения, большая перегрузочная способность электродвигателя; возможность контроля кривизны, отклонения ствола скважины и процесса работы с поверхности земли. К недостаткам электродвигателя относятся необходимость одновременной подачи к забою двух видов энергии – электрической и гидравлической и сложность конструкции.
Электробур (рис. 4.13) представляет собой цилиндрический значительной длины герметичный маслонаполненный трехфазный асинхронный электродвигатель с короткозамкнутым ротором 11 из нескольких секций.
Рис. 4.13. Электробур Э215-8М без редуктора-вставки
Корпус статора 4 электродвигателя представляет собой трубу с соединительными резьбами на концах, в которую запрессованы пакеты магнитной стали 8, чередующиеся с пакетами немагнитной стали 9. Последние служат для уменьшения электрических потерь в статоре в местах установки подшипников 10 вала 7 ротора. В пакетах ротора имеются пазы, в которых заложена обмотка 6. Концы ее соединены с кабелем 12,
60