
книги / Машины и оборудование нефтяных и газовых промыслов. Буровые машины и механизмы
.pdf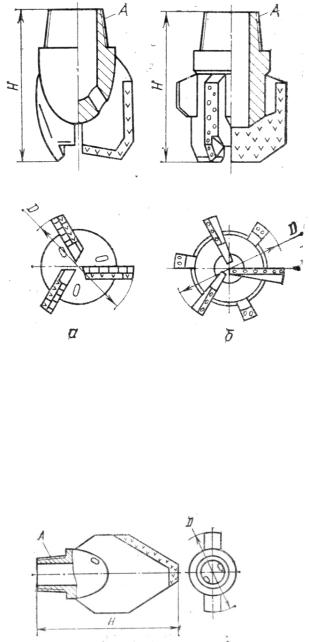
Рис. 3.6. Долота истирающе-режущие: а – трехлопастное; б – шестилопастное
Однолопастные пикообразные долота (рис. 3.7) используются для разбуривания цементных пробок в обсадной колонне (тип Ц) или для расширения стенок скважины (тип Р). Оба указанных типа однолопастных долот имеют сварную либо цельнокованую конструкцию. Рабочие кромки лопасти скошены под углом 45° и армированы с набегающей стороны релитом и твердосплавными пластинами, защищенными чугунным покрытием.
Рис. 3.7. Долото лопастное пикообразное
Алмазное долото (рис. 3.8), подобно лопастному, не имеет подвижных деталей и состоит из корпуса 1 с присоединительной резьбой 2 и фасонной алмазонесущей головкой (матрица) 3, выполненной из порошкообразного твердосплавного материала. Промывочные отверстия 4 сообщаются с промывочными каналами 5, которые делят поверхность матрицы на секторы 6. Для предотвращения отклонений ствола скважины при бурении рабочие поверхности секторов имеют выпукло-вогнутую, двоякоконусную и ступенчато-конусную формы. На рабочей 7 и калибрующей 8 поверхностях секторов матрицы крепятся алмазы 9. В зависимости от крепления алмазов в матрице различают долота с однослойной укладкой относительно крупных алмазов и с многослойной укладкой сравнительно мелких алмазов (импрегнированное алмазное долото). В долотах используют наименее ценные разновидности природных алмазов либо синтетические алмазы.
41
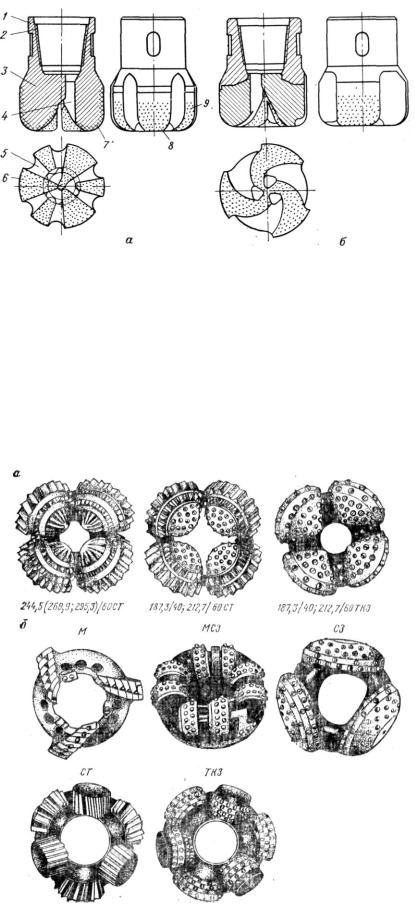
Рис. 3.8. Алмазные долота: а – радиальное; б – радиально-спиральное
Институтом сверхтвердых материалов (ИСМ) разработан на основе недефицитных мелких фракций природных и синтетических алмазов новый сверхтвердый материал славутич, не уступающий по эксплуатационным качествам природным алмазам [1].
3.4. Головки бурильные
Бурильные головки (рис. 3.9) применяют для создания кольцевого забоя и отбора керна, который формируется в центральной части забоя скважины и, по мере углубления скважины, поступает через бурильную головку в компоновку кернорвателя и керноприѐмное устройство.
Рис. 3.9. Головки бурильные:
а – керноприемник съемный; б – керноприемник несъемный
42
Наличие отверстия диаметром 40…100 мм в центральной части рабочего торца бурильной головки обеспечивает формирование керна соответствующего диаметра при бурении.
Типы выпускаемых бурильных головок: М, МСЗ, СЗ, СТ, ТЗ, ТКЗ. Обозначение бурильных головок: К – для керноприѐмных устройств без съемного керноприѐмника, КС – для керноприѐмных устройств со съемным керноприѐмником.
Резьба у бурильных головок типа К – муфта, КС – ниппель.
Основные геометрические размеры и типы присоединительных резьб отечественных бурильных головок приведены в табл. 3.2 [2, 7].
|
Головки бурильные (рис. 3.9). ГОСТ 21210-75; ОСТ 39-079-79 |
Таблица 3.2 |
|||||
|
|
||||||
|
|
|
|
|
|
|
|
Диаметр, мм |
|
Высота долота, |
Присоединительная |
|
Конусность |
||
долота |
|
керна |
|
мм |
резьба |
|
резьбы |
|
|
|
Керноприѐмник несъѐмный |
|
|||
76,0 |
|
36 |
|
110 |
66 |
|
– |
93,0 |
|
40 |
|
120 |
81 |
|
– |
112,0 |
|
44 |
|
140 |
101,5 |
|
– |
132,0 |
|
60 |
|
150 |
118 |
|
– |
139,7 |
|
52 |
|
260 |
З-110 |
|
1:8 |
142,9 |
|
52 |
|
260 |
З-110 |
|
1:8 |
149,2 |
|
52 |
|
260 |
З-110 |
|
1:8 |
158,7 |
|
67 |
|
280 |
З-133 |
|
1:6 |
165,1 |
|
67 |
|
280 |
З-133 |
|
1:6 |
171,4 |
|
67 |
|
280 |
З-133 |
|
1:6 |
183,7 |
|
80 |
|
300 |
З-150 |
|
1:8 |
196,0 |
|
80 |
|
300 |
З-150 |
|
1:8 |
212,7 |
|
80 |
|
320 |
З-150 |
|
1:8 |
222,3 |
|
80 |
|
320 |
З-150 |
|
1:8 |
244,5 |
|
100 |
|
360 |
З-189 |
|
1:6 |
269,9 |
|
100 |
|
380 |
З-189 |
|
1:6 |
295,3 |
|
100 |
|
400 |
З-189 |
|
1:6 |
311,1 |
|
100 |
|
420 |
З-189 |
|
1:6 |
320,0 |
|
100 |
|
420 |
З-189 |
|
1:6 |
349,2 |
|
100 |
|
440 |
З-189 |
|
1:6 |
|
|
|
|
Керноприѐмник съѐмный |
|
||
187,3 |
|
40 |
|
300 |
З-147 |
|
1:6 |
212,7 |
|
60 |
|
320 |
З-161 |
|
1:6 |
244,5 |
|
60 |
|
360 |
З-171 |
|
1:6 |
269,9 |
|
60 |
|
380 |
З-171 |
|
1:6 |
295,3 |
|
60 |
|
400 |
З-171 |
|
1:6 |
4. ЗАБОЙНЫЕ ДВИГАТЕЛИ
В процессе бурения скважины долото приводится во вращение либо ротором, либо забойными двигателями, расположенными непосредственно в нижней части бурильной колонны над долотом. Для этих целей применяют гидравлические и электрические двигатели.
Существуют гидравлические двигатели двух типов: гидравлические многоступенчатые турбины, называемые турбобурами, и гидравлические двигатели объемного действия. Электрические забойные двигатели – электробуры – состоят из
43
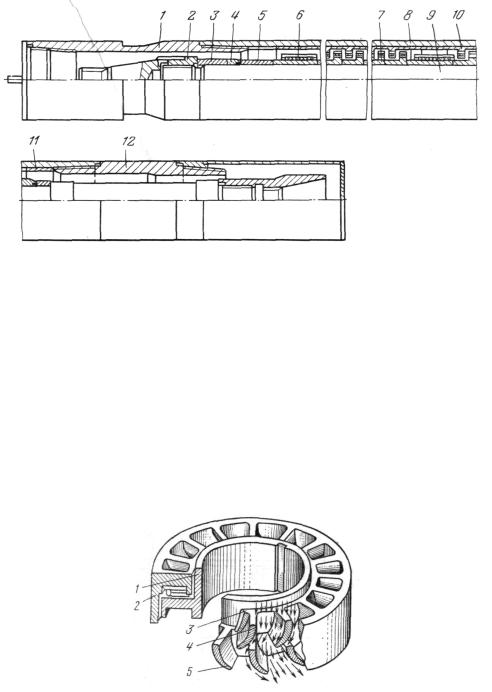
маслонаполненного электрического двигателя трехфазного переменного тока, соединенного со шпинделем, на котором укреплено долото.
4.1. Турбобуры
Турбобур представляет собой забойный гидравлический двигатель с многоступенчатой турбиной. Гидравлическая энергия потока бурового раствора приводит во вращение вал, соединенный с валом шпинделя и долотом. Для различных условий бурения отечественная промышленность выпускает турбобуры, различающиеся по диаметру, числу секций, расположению и конструкции опор и устройству турбинных аппаратов. Унифицированная секция турбобура, применяемая для одно- и многосекционных турбобуров, не имеет осевой опоры, а осевые нагрузки воспринимаются опорой, расположенной в шпиндельной секции.
Рис. 4.1. Унифицированная турбинная секция турбобура ЗТСШ-195
Унифицированная турбинная секция турбобура ЗТСШ-195 (рис. 4.1.) состоит из переводника 1, свинченного на конусной резьбе с корпусом 8, в котором находятся пакеты статоров гидротормоза 7 и турбины 10, сжимаемые регулировочными кольцами 11 и фиксируемые нижним переводником 12. Этот переводник снабжен ниппелем с конусной замковой резьбой, к которой присоединяется вторая секция турбобура или шпиндельная секция, а при транспортировке навинчивается колпак.
Вращающаяся группа деталей: регулировочное кольцо 3, втулки уплотнения 4 и распорная 5, радиальные опоры средняя и верхняя 6 и пакеты роторов гидротормоза 7 и турбины 10, закрепленные на валу секции 9 стяжной полумуфтой 2.
В многосекционных турбобурах валы секций соединяются с помощью конусных или шлицевых муфт на резьбах с небольшим углом конусности.
Рис. 4.2. Ступень турбины турбобура
44
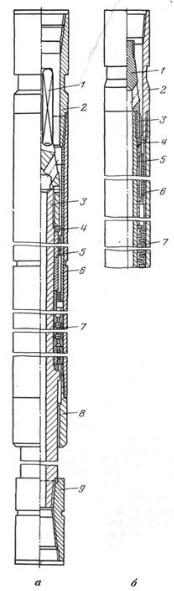
Турбина состоит из большого числа ступеней (до 370). Каждая ступень (рис. 4.2.) состоит из статора с наружным 2 и внутренним 3 ободами, между которыми размещены лопатки 4 и ротор, обод 1 которого снабжен лопатками 5. Лопатки статора и ротора расположены под углом друг к другу, вследствие чего поток жидкости, поступающий под углом из каналов статора на лопатки ротора, меняет свое направление и давит на них. В результате этого создаются силы, стремящиеся повернуть закрепленный на валу ротор в одну сторону, а закрепленный в корпусе статор – в другую.
Рис. 4.3. Унифицированная шпиндельная секция турбобура 3ТСШ-195:
а – на резинометаллической опоре; б – на упорно-радиальных шарикоподшипниках
Далее поток раствора из каналов ротора вновь поступает на лопатки статора второй ниже расположенной ступени, на лопатки ее ротора, где вновь изменяется направление потока раствоpa. На роторе второй ступени также возникает крутящий момент. В результате раствор под действием энергии давления, создаваемой буровым насосом, расположенным на поверхности, проходит все ступени турбобура. В многоступенчатой турбине раствор движется вдоль ее оси. Активный крутящий момент, создаваемый каждым ротором, суммируется на валу, а реактивный (равный по
45
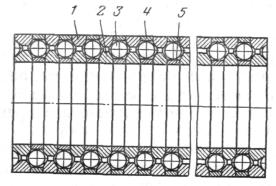
величине и противоположный по направлению), создаваемый на лопатках статора, суммируется на корпусе турбобура. Реактивный момент через корпус турбобура передается соединенной с ним бурильной колонне, а активный – долоту. На создание крутящего момента перепад давления, срабатываемый в турбобуре, составляет от 3 до 7 МПа, а иногда и более. Это является большим недостатком турбобура, поглощающего значительную часть энергии, создаваемой насосом, и затрачивающего ее на вращение долота, а не на очистку и эффективное разрушение забоя скважины, что практически исключает возможность применения гидромониторных долот.
По устройству турбин, требующих различного расхода жидкости, турбобуры подразделяются:
–на низколитражные, высоконапорные, имеющие максимальную мощность, большую частоту вращения и значительный вращающий момент;
–среднелитражные, развивающие максимальный вращающий момент, среднюю частоту вращения при высоком расходе жидкости;
–высоколитражные, имеющие максимальное отношение вращающего момента к частоте вращения, относительно низкую частоту вращения и повышенный расход жидкости.
По числу секций турбобуры подразделяются на односекционные, в которых турбина и опорная пята расположены в одном корпусе, и многосекционные, состоящие из нескольких турбинных секций и шпинделя с осевой опорой.
Унифицированная шпиндельная секция (см. рис. 4.3) представляет собой самостоятельную сборку, которую можно использовать с одно- и многосекционным турбобуром. Шпиндельная секция выполняется в двух модификациях: на упорном подшипнике качения (см. рис. 4.3, а) и на резинометаллической опоре скольжения (см.
рис. 4.3, б).
Все основные детали шпиндельных секций – взаимозаменяемые, что упрощает ремонт и обслуживание. Вал 3 шпинделя в нижней части имеет ниппельную часть с резьбой для присоединения переводника 9 долота. Верхний конец вала 3 снабжен конической резьбой, на которую навинчивается полумуфта 1, стягивающая регулировочные кольца 4, втулку радиальной нижней опоры 5 и внутренние кольца
упорно-радиального подшипника 7 (см. рис. 4.3, а) или диски резинометаллической пяты 7 (см. рис. 4.3, б). Корпус шпинделя 6 представляет собой трубку с внутренней конической резьбой по концам, к которым сверху привинчен переводник 2, а снизу ниппель 8, являющийся радиальной опорой вала шпинделя. Пята 7 воспринимает осевые нагрузки от долота и гидравлического давления и передает их через корпус бурильной колонне.
Многорядный осевой подшипник качения (рис. 4.4) имеет несколько параллельно работающих упорных бессепараторных шариковых подшипников (до 10), каждый из которых состоит из наружного 1 и внутреннего 2 колец, между которыми размещены шары 3, наружные 4 и внутренние 5 распорные кольца. Многорядные осевые подшипники качения опор турбобуров работают в пределах 20–100 ч.
Рис. 4.4. Осевая опора качения турбобура
46
Резинометаллический подшипник состоит из нескольких ступеней. Каждая ступень имеет подпятник, который представляет собой металлический обод с резиновой облицовкой, укрепляемый в корпусе, и стальной диск, расположенный на валу турбобура. Резиновая облицовка одного из элементов радиального или осевого подшипника обеспечивает его работу со смазкой буровым раствором. Резинометаллические опоры турбобуров в зависимости от условий эксплуатации имеют работоспособность в пределах 50…150 ч.
Осевые подшипники турбобуров располагают в верхней или нижней части турбобура. При верхнем расположении опора снабжается каналами для протока раствора, а при расположении в нижней части вала – не имеет каналов и служит лабиринтным уплотнением, препятствующим утечкам раствора в зазор между валом и нижним радиальным резинометаллическим подшипником, расположенном в ниппеле. При такой конструкции можно работать с некоторым перепадом давления на долоте без значительных утечек раствора через нижнюю опору. Валы верхних секций имеют только радиальные опоры.
Ниппель, свинченный с корпусом турбобура, служит также для зажатия статоров турбины. В турбинных секциях осевые деформации элементов ротора и статора турбины должны быть одинаковыми. Деформация определяется соотношением натягов конусных резьб муфты и соединительного переводника. Детали шпиндельной секции крепятся за счет деформации вращающихся и неподвижных элементов подшипника, обеспечивающих равномерное распределение нагрузки.
В зависимости от требований бурения применяют турбобуры диаметром от 127 до 240 мм с числом ступеней от 52 до 369, длиной от 8,8 до 26 м. Для удобства монтажа и перевозки турбобуры выполняются из отдельных секций (до четырех) длиной 6…10 м каждая, соединяемых между собой на буровой перед спуском в скважину.
Односекционные турбобуры типа Т12М3 изготовляют диаметрами 240, 195 и 172 мм с числом ступеней 98…106, собранных в одном корпусе. Они снабжены резинометаллической осевой опорой, расположенной в верхней части корпуса.
Многосекционные унифицированные турбобуры типа ЗТСШ1, А9Ш и А7ГТШ изготовляют диаметрами 240 и 195 мм. Турбобуры ЗТСШ1 имеют три секции, а А9Ш и А7Ш – две секции.
Турбобуры с буквой А в шифре отличаются тем, что их турбины имеют изменяющуюся характеристику при постоянном расходе жидкости. Эти турбины сконструированы так, что перепад давления на них уменьшается в зависимости от снижения нагрузки на долото и вращающего момента. В этих турбобурах использованы высокоциркулятивные турбины, постоянство перепада давления на которых поддерживается с помощью перепускного клапана. Через этот клапан часть жидкости сбрасывается в затрубное пространство, минуя турбобур. Буква Ш в шифре обозначает, что турбобур шпиндельный. Редукционные клапаны для сброса жидкости могут устанавливаться над турбобуром или на некотором расстоянии от него.
Многообразие конструкций турбобуров объясняется тем, что около 90 % объема бурения на нефть и газ осуществляется трехшарошечными долотами, для которых частота вращения должна регулироваться в пределах от 30 до 250 об/мин независимо от нагрузки. Во многих породах при бурении с частотой более 250 об/мин шарошечные долота дают проходку, иногда во много раз меньшую, чем ее можно получить при современном роторном бурении.
К недостаткам забойных гидравлических двигателей относится также потребление значительно большего количества жидкости, чем требуется для работы долота. На привод долота и на гидравлические потери при транспортировке жидкости к забою должно расходоваться не более 1/3 мощности, развиваемой насосами на поверхности. Условия бурения скважин многообразны, и единых рекомендаций быть не может, но
47
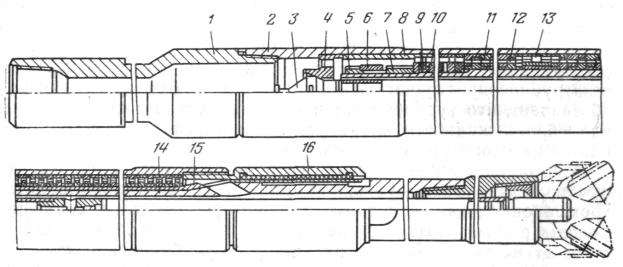
совершенно ясно, что в каждом случае должно быть дано экономическое обоснование выбора того или иного оборудования для бурения [6].
4.2. Турбодолото
Турбодолото (рис. 4.5) – турбинный забойный двигатель, служащий для вращения колонковой головки для бурения скважин с отбором образцов породы (кернов). Оно представляет собой одноили двухсекционный турбобур с резинометаллической осевой опорой и пустотелым валом.
Рис. 4.5. Турбодолото КТД:
1 – переводник; 2 – корпус; 3 – керноприемная труба; 4 – опора грунтоноски; 5 – контргайка; 6 – колпак; 7 – гайка; 8 – втулка; 9, 10 – кольцо и диск пяты;
11, 12 – диски статора и ротора; 13 – опоры; 14 – вал; 15 – переводник; 16 – ниппель
Вал турбодолота имеет полость, внутри которой расположена колонковая труба – грунтоноска для приема выбуренного керна. В верхней части корпуса турбодолота помещена опора грунтоноски, имеющая конусное посадочное гнездо. Грунтоноска снабжена головкой с конусной поверхностью, на которую она садится. Благодаря этому при вращении вала турбодолота с бурильной головкой керноприемная труба не вращается.
Грунтоноска закрывает отверстие в валу, благодаря чему жидкость не проходит через него, а поступает в турбину турбодолота. Поскольку давление раствора в верхней части турбины больше, чем в нижней, то под действием этого перепада колонковая труба прижимается к опоре, что препятствует утечке жидкости через зазор между колонковой трубой и отверстием вала. Это могло бы приводить к разрушению выбуренного керна. В остальном конструкция турбодолота аналогична конструкции турбобура.
В турбодолотах типа КТДС-4 (см. рис. 4.5.) осевая опора расположена в нижней части. Эти турбодолота выпускают с наружным диаметром корпуса 172 и 195 мм, первый – для бурильных головок диаметром 190, а второй – для 214-мм головок.
Все турбины турбодолот имеют номинальный расход бурового раствора 0,028 м3/с при плотности ρ = 1200 кг/м3 [6].
4.3. Турбобуры для забуривания наклонных скважин
Для забуривания наклонных стволов скважин турбобур с долотом должен быть поставлен в скважине под углом к вертикали. Чтобы этот угол был большим, турбобур должен быть возможно меньшей длины. Для этих целей применяют укороченные турбобуры-отклонители с числом ступеней 52…109. По конструкции они аналогичны
48
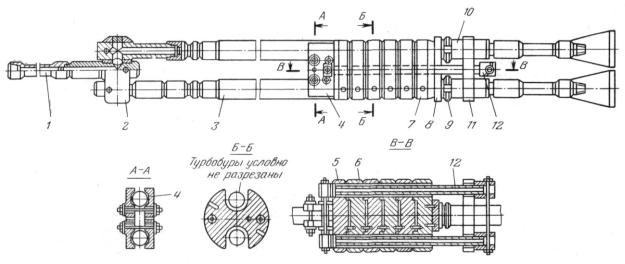
унифицированным турбобурам и состоят из турбинной и шпиндельной секций с той разницей, что шпиндельная секция соединяется с турбиной переводником, имеющим перекос осей 1°30'. Это позволяет набирать кривизну ствола скважины. Вал турбины соединяется с валом шпинделя шарнирной муфтой, компенсирующей эксцентриситет. Корпус турбины через переводник соединяется с бурильной колонной [6].
4.4. Реактивно-турбинные агрегаты
Для бурения верхних интервалов скважин диаметром 0,394…1,02 м применяют реактивно-турбинные агрегаты, у которых два турбобура смонтированы параллельно и жестко соединены между собой. Для бурения скважин в горнорудной промышленности используют реактивно-турбинные агрегаты с тремя и четырьмя турбобурами, соединенными параллельно. Такими агрегатами бурят скважины диаметром от 1,26 до
5 м.
На рис. 4.6 показан реактивно-турбинный агрегат для бурения скважин диаметром 1,02 м. Этот агрегат имеет: переводник 1, соединяющий его с бурильной колонной, траверсу 2, скрепляющую верхние части агрегата и подводящую жидкость к двум турбобурам, турбобуры 3, соединенные в средней части полухомутами 4, грузы 5, 6 и 7, плиту 8, две разрезные втулки 9, кольца 10, нижнюю плиту 11 и стяжки 12. К валам турбобуров присоединены долота.
При бурении агрегат вращается бурильной колонной вокруг ее оси, а долота совершают планетарное вращение вокруг осей турбобуров и оси скважины, разрушая ее забой. Нагрузка на забой создается грузами 5, 6 и 7. Разбуренная порода выносится циркулирующим потоком бурового раствора, подаваемого в скважину насосами.
Для бурения скважин с помощью РТБ используются обычные буровые установки [6].
Рис. 4.6. Реактивно-турбинный агрегат РТБ-1020
4.5. Характеристика турбобура
Рабочая характеристика турбины турбобура определяется частотой вращения вала n, крутящим моментом М на его валу, развиваемой мощностью N, перепадом давления ∆р и гидравлическим коэффициентом полезного действия η количеством бурового раствора Q, прокачиваемого через турбину. В процессе бурения вследствие изменения момента сопротивления на долоте и количества прокачиваемого раствора все параметры турбобура меняются.
Крутящий момент на валу турбины возникает в результате взаимодействия потока жидкости с лопатками статора и ротора. В расчетах принимают, что в каналах ротора и статора турбины жидкость движется цилиндрическими слоями и не влияет на другие
49
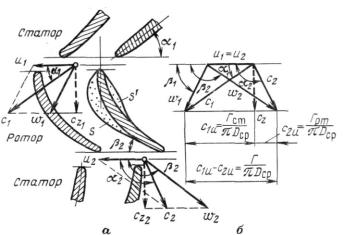
слои в радиальном направлении. Течение жидкости в цилиндрическом слое рассматривается в теории турбин. Согласно этой теории в проточной части турбины протекает бесчисленное число цилиндрических слоев жидкости, а в каждом слое имеется множество струек или линий тока жидкости. Скорости движения струек в каждом цилиндрическом слое различны как в радиальном, так и в окружном направлении.
Для упрощения расчетов принимают, что эквивалентная струйка имеет некоторую среднюю скорость, соответствующую усредненным параметрам жидкости на расчетном диаметре Dср лопаток турбобура.
Осевая скорость потока cz жидкости (в м/с) в любом поперечном сечении турбины вычисляется по уравнению расхода:
cz = Q / F=Q / πDcpl, |
(4.1) |
где Q – расход жидкости, м3/с; F – площадь поперечного сечения решетки турбины, м2; l – радиальная длина лопаток, м.
Для обеспечения протекания жидкости через турбину с определенной скоростью надо на входе в турбину иметь напор, который расходуется как на полезную работу, так
ина преодоление вредных сопротивлений.
Втурбобурах применяются многоступенчатые аксиальные турбины с густой решеткой специфичной конструкции, и в теории турбин общего назначения эти
турбины не рассмотрены. На основе анализа степени циркулятивности (Cn) турбины была предложена методика выбора наиболее важного параметра турбобура – соотношения вращающего момента М и частоты вращения n при работе на оптимальном режиме, т.е. отношение М/n.
Построение специальной циркулятивной теории аксиальных турбин потребовало введения некоторых понятий и обозначений к ранее существовавшим в теории турбин. Для всех величин, относящихся к месту входа потока жидкости в каналы ротора, принимаются индексы «1», а к месту выхода – индексы «2». Абсолютные скорости потока жидкости обозначаются буквой «с», относительные – «ω» и переносные (окружные) – «u».
Рис. 4.7. Планы скоростей в турбине:
а – осевая решетка лопастей турбины; б – совмещенный график треугольников скоростей
Рассмотрим изменение скоростей потока жидкости в лопастной системе многоступенчатой осевой турбины турбобура. Абсолютная скорость потока с может быть разложена на скорости в трех направлениях: осевом cz, тангенциальном
50