
книги / Несущая способность сварных соединений
..pdfматериала усталостному разрушению. В итоге такие испытания можно перенести на конструкцию и судить о ее работоспособности.
Таким образом, испытания по определению характеристик сопротивления развитию трещин (трещиностойкости) материалов при усталостном нагружении состоят в последовательном изме рении при заданных параметрах цикла нагрузки, размера t (дли ны, глубины) растущей трещины и числа циклов нагружении iV. На основе полученных данных строят графики роста трещины, представляющие собой зависимость изменения длины трещины от числа циклов нагружения; вычисляют скорость роста трещины
/Л / |
dl |
\ |
v ( — , — |
) как средний прирост ее длины за один цикл при |
|
\Д N |
an J |
заданных условиях испытания; устанавливают зависимость изме нения скорости роста трещины от величины напряженно-дефор мированного состояния около ее вершины и определяют пара метры этой зависимости — характеристики сопротивления раз витию трещины (трещиностойкости) материала при усталостном нагружении.
Различают основные и специальные испытания. Основные служат для получения исходных данных о сопротивлении разви тию трещины в металле при усталостном нагружении. Их про водят при полном диапазоне нагрузок (от пороговой, ниже которой трещина не развивается, до*критической, при которой наступает долом или состояние полной текучести образца). Специальные испытания проводят, как правило, в ограниченном диапазоне нагрузок для выяснения влияния отдельных факторов (асим метрии и формы цикла, частоты и др.) на скорость роста трещины. Кроме того, они имитируют эксплуатационные условия работы материала и служат справочными данными к техническим требованиям. Специальные испытания выбирают в соответствии с их назначением и реализуют на образцах с исходной трещиной, расположенной в плоскости, перпендикулярной наибольшим рас тягивающим напряжениям. Их проводят при непрерывно изменя ющемся или постоянном коэффициенте интенсивности напряжений. При этом устанавливают влияние различных факторов на скорость роста усталостной трещины. Такого постоянства можно достичь при соответствующем способе нагружения образца, напри мер, применении жесткого нагружения (с заданными переме щениями), а также программном изменении нагрузки по мере роста трещины.
Зависимость скорости роста трещины от максимального коэффициента интенсивности напряжений цикла Кшах пли ве личины размаха при постоянной ассиметрии цикла ДКшах изо
бражают диаграммой усталостного разрушения (диаграммой циклической трещиностойкости). Диаграмма, построенная в ло гарифмических координатах (рис. 4.8), состоит из двух криво линейных участков: 1 — низкой (обычно 1»<СКН м/цикл) и 3 — высокой (и > 10 _б м/цикл) скоростей роста трещины, а также
ш
среднего участка 2, аппроксимируемого прямой. Для знакопере менного цикла нагружения ее, как правило, строят по Ктах-
Диаграмма усталостного разрушения дает наиболее полную информацию о трещиностойкости материала.
По ней устанавливают:
минимальное пороговое значение коэффициента интенсивности напряжений цикла К*л, при котором трещина не развивается в течение заданного числа циклов;
Рис. 4.8. Общий вид кине тической диаграммы уста лостного,*! разрушения:
/, 2> 3 — .участки изменения скорости распррстранения трещи ны.
максимальное (критическое) значение коэффициента интенсив
ности напряжений цикла |
К /с , при |
котором наступает |
долом |
образца (циклическая вязкость разрушения). |
из фор |
||
Скорость роста трещины |
(м/цикл) |
можна определить |
|
мулы Париса [202]: |
= cK*mtl, |
|
(4.13) |
v |
|
где с и п — параметры, аппроксимирующие средний участок диаг раммы.
Формулу (4.13) можно представить также в виде
V— 10~7(К т а х /К * ) п- |
(4.14) |
где К #==К т а х При v — \0~7 м/цикл. |
|
Между параметрами с и л существует взаимосвязь: |
|
с= 1 0 -7(К*)-я. |
(4.15) |
В полном диапазоне скоростей развития трещины диаграмму усталостного разрушения опишем формулой [4]
1 |
К / . - К ц А» - - |
(4.16) |
V = — |
|
А К„„ - К ,Л '‘ • *
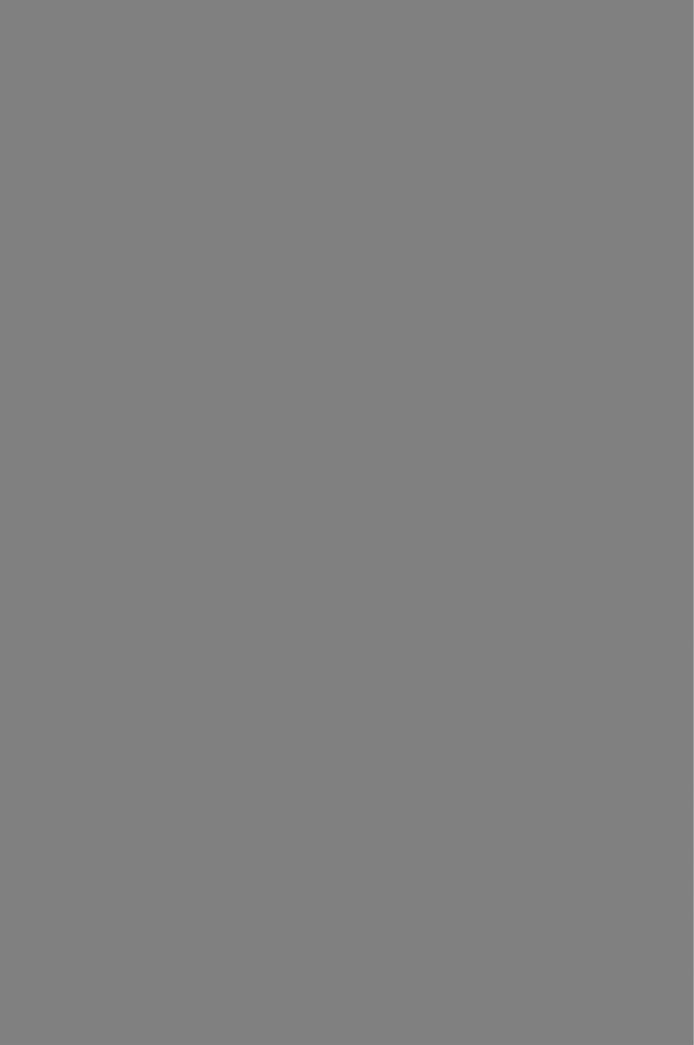
_ |
Ы |
J i - h - x |
(4.19) |
|
Vl |
Щ |
ДАТ, * |
||
|
где U-u h — соответственно начальная и конечная длина трещины на f-м продвижении при количестве циклов ANи
Для усталостных испытаний используют, например, машину ЦДМПу-10, (см. рис. 4.9) оснащенную устройством 5 для нагру жения балочного образца трехточечным изгибом, которое связано
А . а -л
Рис. 4.10. Балочный образец с боковым над резом для сосредоточенного изгиба.
с верхним захватом 4. Образец устанавливают на опоры 3 и 7, жестко прикрепленные к основанию 1, расположенном на нижнем захвате 2. Правую часть образца закрепляют в неподвижной установочной вилке б, а левую — кладут на ролик. Нагружающее
усилие |
образцу передается через |
каток |
прижимного |
устройства |
|
5. Для |
контроля |
действующего |
усилия |
устройство |
снабжено |
тензометрическим |
динамометром, |
сигнал |
от которого |
передают |
|
на осциллограф. |
|
|
|
|
Рост трещины, след которой выходит на боковую поверхность образца, фиксируют катетометром КМ-8 с точностью до 0,01 мм.
Испытание образца проводят в два этапа: до зарождения усталостной трещины и на стадии циклического нагружения образца с наведенной усталостной трещиной.
На первом этапе для построения полной диаграммы уста лостного разрушения необходимо навести острую усталостную трещину, по которой определяют пороговый коэффициент интен сивности напряжений К*л- Практически это достигается пульси рующим нагружением надрезанного образца, равным 0,5 К$ (КQ — параметр трещиностойкости материала образца при стати ческом нагружении).
С момента появления усталостной трещины и по мере ее про движения постоянно снижают максимальную нагрузку цикла
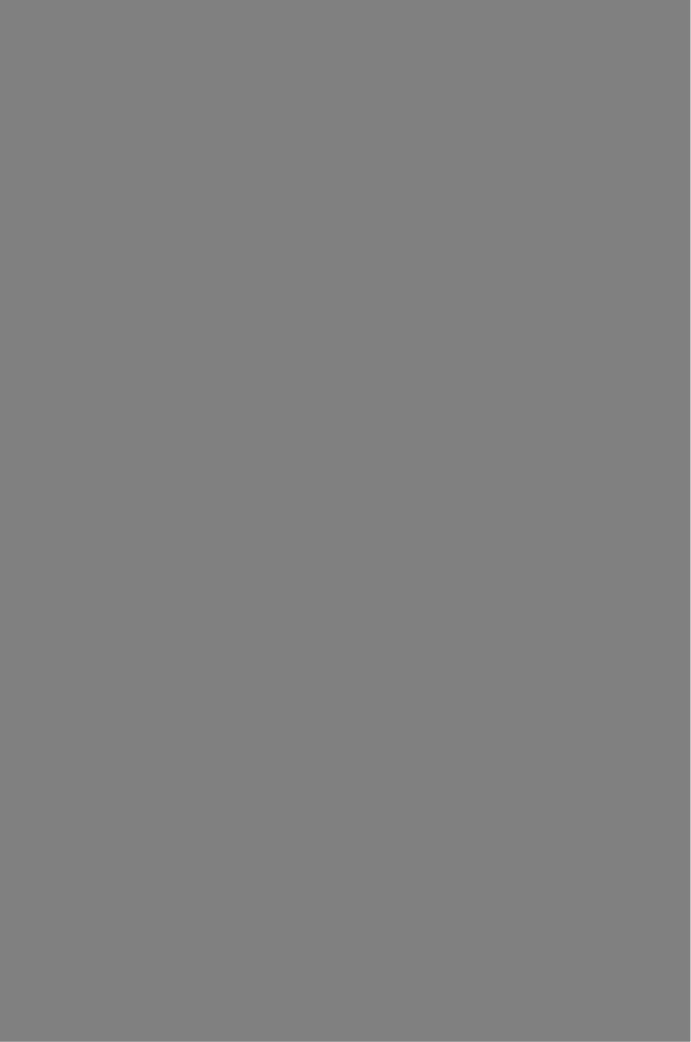
•или квазихрупким разрушениям, в силу условий их эксплуатации должны проектироваться с учетом повышенной вязкости разру шения. Для выбора оптимального варианта термической обработ ки или марки стали служат статические испытания образцов с наведенной усталостной трещиной.
Испытания проводили на цилиндрических образцах из сталей двух марок (см. рис. 4.1 и табл. 4.2). По методике [80] в образ цах создавали усталостные трещины путем кругового изгиба при
Т а б л и ц а 4,2
Режимы |
образования |
усталостных трещин |
для конструкционных |
сталей |
|||||||
|
|
|
|
|
|
|
|
Частота |
Время |
об |
Глубина |
Марка |
стали и режим |
D, |
|
L, |
Прогиб |
разования |
|||||
ММ |
вращения |
трещины |
трещины |
||||||||
термообработки |
мм |
мм |
f, мм |
(а, с - 1 |
t, мин |
/, мм |
|||||
Сталь |
40Х |
(закалка при |
|
|
|
|
|
|
|
||
1133 |
К, |
охлаждение |
в |
12,0 |
200 |
2,0 |
5 |
16—17 |
1,0—1,5 |
||
масле, отпуск при 773 К) 15,0 |
|||||||||||
Сталь ЗОХГСА (нормали |
|
|
|
|
|
|
|
||||
зация |
при 1153 К, охлаж |
12,0 |
200 |
2,0 |
5 |
9—11 |
1,0—1,5 |
||||
дение |
на |
воздухе) |
15,0 |
||||||||
Сталь |
40Х |
(нормализа |
|
|
|
|
|
|
|
||
ция при 1143 К, охлаж |
12,0 |
200 |
2,0 |
5 |
8—10 |
1,0—1,5 |
|||||
дение |
на |
воздухе) |
15,0 |
фиксированном прогибе. При этом использовали токарный станок 1К-62.
Как показали данные усталостных испытаний согласно выбран ных режимов (см. табл. 4.2), наибольшая сопротивляемость усталостному разрушению характерна для стали 40Х после за калки и отпуска при 773 К. Стали ЗОХГСА и 40Х после норма лизации имеют меньшую усталостную прочность, а по времени зарождения и распространения усталостной трещины близки между собой, причем сталь ЗОХГСА незначительно превосходит по указанным параметрам 40Х с аналогичной термообработкой.
Для оценки исследуемых сталей по трещиностойкости Кс проводили статические испытания образцов на осевое растяжение. Для проведения опытов использовали разрывную машину РМ-50. Скорость перемещения активного захвата составляла v = ^=2,0 мм/мин. В процессе эксперимента фиксировали нагрузку F— F*, при которой происходило разрушение образца с трещиной и замеряли его диаметры D, d. Характеристики трещиностойкости Кс для исследуемых образцов из указанных сталей рассчиты вали по формулам (4.1) и (4.2). Полученные данные для тем пературы 293 К приведены в табл. 4.3. Как видим, наибольшую трещиностойкость имеет сталь 40Х после закалки и отпуска при 773 К.
При растяжении цилиндрических образцов из сталей 40Х и ЗОХГСА после нормализации (за исключением стали 40Х после закалки и отпуска при 773 К) на диаграмме растяжения наблю-
и л
дался участок текучести. В связи с этим проводили дополни-* тельные исследования по выявлению изменения Кс в зависи мости от увеличения наружного диаметра D (см. рис. 4.1), т. е. по выявлению масштабного эффекта.
Из исследуемых марок сталей изготовляли цилиндрические
образцы трех партий различного диаметра D, равного |
20, 30 |
й |
||||||||
40 мм и десятикратной длины L— 1 0 D. Как и ранее, В образцах |
||||||||||
|
|
|
|
|
|
|
|
Т а б л и ц а |
4.3 |
|
Трещиноетойкость Кс конструкционных сталей |
|
|
|
|
||||||
Марка |
стали |
н режим |
о, мм |
d K, мм |
d, мм |
|
F*, кН |
к^, |
|
|
термообработки |
|
|
|
МПа КМ |
||||||
Сталь |
40Х |
после |
за |
15,0 |
12,0 |
10,80 |
0,745 |
143,5 |
90 |
|
калки при 1133 К и |
15,0 |
12,0 |
10,67 |
0,739 |
149,5 |
95 |
|
|||
отпуска (773 К) |
|
15,0 |
12,0 |
10,10 |
0,697 |
135,0 |
97 |
|
||
|
|
|
|
|
|
|
Средшге |
|
94,2 |
|
Сталь |
ЗОХГСА |
пос |
15,0 |
12,0 |
10,90 |
0,752 |
84,5 |
66 |
|
|
ле |
нормализации |
15,0 |
12,0 |
10,65 |
0,735 |
76,0 |
63 |
|
||
(1153 |
К) |
|
|
15,0 |
12,0 |
10,00 |
0,692 |
65,0 |
59 |
|
|
|
|
|
|
|
|
Средне‘е |
|
62,3 |
|
СталЬ 40Х после нор |
15,0 |
13,0 |
12,20 |
0,813 |
93,5 |
52 |
|
|||
мализации |
(1143 |
К) |
15,0 |
13,0 |
11,80 |
0,789 |
85,0 |
55 |
|
|
|
|
|
|
15,0 |
13,0 |
12,05 |
0,803 |
91,0 |
57 |
|
|
|
|
|
|
|
|
Среди'ее |
|
56,1 |
создавали усталостные трещины, а затем испытывали их на статическое растяжение для определения трещиностойкости ( K ic ) .
Как видим из рис. 4.12, изменение кривых в направлении к горизонтальному участку тем значительнее, чем ниже прочность
Рис. 4.12. .Изменение Кс в |
|
|||
зависимости |
|
от |
диаметра |
|
образца Д |
для |
конструк |
|
|
ционных |
сталей: |
|
||
/ — 4ОХ после |
нормализации; |
|
||
2 — ЗОХГСА после нормали |
|
|||
зации; 3 — 40Х |
после закалки |
|
||
и отпуска (/отп«773 К). |
|
|||
стали. Постоянство |
значений К с |
для стали 40Х после закалки |
||
и отпуска 773 К |
начинается с |
15 мм и составляет независимо |
от диаметра Kc=Ki<‘=94 МПаУм, Для нормализованных сталей
40Х и |
ЗОХГСА |
это |
явление |
наблюдается начиная |
с |
диаметра |
D —30 |
мм. При |
этом |
K c = K i c |
равно соответственно |
72 |
МПаУМ |
и 76 МПа]/М, т. е. в последнем случае для корректного опре деления K ic можно ограничиться диаметром 30 мм, поскольку дальнейшее его увеличение не ведет к повышению К с .
Таким образом, максимальную трещиностойкость имеет сталь 40Х после закалки и отпуска 773 К-
4.6. СТАТИЧЕСКИЕ ИСПЫТАНИЯ ОБРАЗЦОВ ОДНОРОДНЫХ И НЕОДНОРОДНЫХ СВАРНЫХ СОЕДИНЕНИИ
Проведение таких испытаний позволяет получать не только характеристики трещиностойкости металла шв-а сварных соеди нений, но и сравнивать различные способы и режимы сварки, марки присадочных проволок и т. п. для достижения максималь ной трещиностойкости металла шва сварного соединения. Ис следования выполняли на сборных трубчатых образцах с внутренней кольцевой трещиной.
Сварка однородных материалов. На образцах (см. рис. 4.4), изготовленных ручной дуговой сваркой из нормализованных сталей 40Х и 30X1 СА и стали 40Х после закалки и отпуска 773 К ,
изучали статическую трещиностойкость металла наплавки. В качестве присадочного металла использовали сварочную прово локу Св-08Г2С диаметром 1,6 мм, в качестве защитного газа — аргон.
Опыты на растяжение образцов проводили на разрывной
машине |
FP-100/1 (ГДР) со |
скоростью .перемещения подвижного |
|
захвата |
v =2,0 мм/мин. Трещиностойкость наплавляемого |
метал |
|
ла определяли по формулам |
(4.3) и (4.4). |
* |
Установлено, что для трех марок сталей металл шва при аргоно-дуговой сварке имеет практически одинаковую трещино стойкость (табл. 4.4). Однако детальный анализ диаграмм ста тического растяжения в координатах нагрузка — деформация показал различие процессов разрушения. Так, разрушение об разцов из стали 40Х после нормализации сопровождалось за метным течением в верхней части диаграммы, подрастанием трещины, образовыванием шейки по наружному диаметру образца. Поверхность разрушения — крупнозернистая, светло-серого цвета.
Для этой же стали после закалки и отпуска 773 К на диаграм
мах разрушения уменьшается площадка текучести и замедляется подрастание трещины без явно выраженной утяжки наружной поверхности образца. Излом серого цвета с темным оттенком и мелкозернистым рельефом.
Для нормализованной стали ЗОХГСА диаграмма разрушения имеет минимальую текучесть, характерную для хрупкого раз рушения. Изломы образцов крупнозернистные, светло-серые.
Достаточно высокая вязкость разрушения наплавляемого ме талла для всех трех вариантов аргонодуговой сварки позволяет рекомендовать данную технологию для изготовления сварных конструкций.
Сварка неоднородных металлов. Рассмотрим изменение трещиностойкости наплавляемого металла при соединении двух разных металлов.
Т а б л и ц а 4.4
Трещиностойкость Кс однородных саарнык соединений
Марка стали и режим |
D. |
da, |
d. |
d |
F“. |
Kc |
термообработки |
мм |
мм |
мм |
R= D ~ |
xH |
МПа, ГМ |
Сталь |
40Х |
после |
нормали |
14 |
7.0 |
7,80 |
0,557 |
81,0 |
|
73,4 |
||
зации |
(1143 |
К) |
|
|
14 |
7,0 |
7,60 |
0,542 |
83,25 |
75,7 |
||
|
|
|
|
|
|
14 |
7,0 |
7,85 |
0,561 |
81,0 |
73,3 |
|
|
|
|
|
|
II |
|
|
Среднее |
|
|
1 |
74,2 |
Сталь |
40Х |
|
после |
|
1 |
14 |
7,0 |
8,05 |
0,575 |
82,0 |
|
78,5 |
и |
закалки |
|
||||||||||
(1133 |
К) |
отпуска |
(773 ' |
14 |
7.0 |
8,00 |
0,572 |
76.0 |
70,9 |
|||
К) |
|
|
|
|
| |
14 |
7,0 |
7,85 |
0,561 |
81,5 |
1 |
77,1 |
|
|
|
|
|
|
|
|
Среднее |
|
|
|
75,5 |
Сталь |
ЗОХГСА после |
нор |
14 |
7,0 |
8,35 |
0,596 |
73,5 |
|
72,4 |
|||
мализации |
(1153 К) |
|
14 |
7,0 |
8,20 |
0,586 |
80,0 |
|
76,3 |
|||
|
|
|
|
|
|
|
7,0 |
7,80 |
0,557 |
82,25 |
|
74,2 |
Средне*3 |
74,5 |
Исследования проводили на модернизированном сварочном
автомате типа А-825 М, |
переоборудованном |
в автоматичес |
||
кую установку (см. |
рис. |
4.6). |
Изготовляли |
12 вариантов |
трубчатых образцов |
(см. рис. 4.4) |
из конструкционных сталей |
в различных сочетаниях, включая стали 40Х, ЗОХГСА после нор мализации и закалки, сталь СтЗ после нормализации и сталь 35 после закалки.
Режимы и условия сварки выдерживали постоянными (ско рость вращения образца ©=0,14 с-1, количество проходов л = 2 , сварочная проволока Св-08Г2С диаметром 1,6 мм). Трещино стойкость наплавляемого металла (табл. 4.5) в порядке умень шения можно представить в такой последовательности (по вари антам): III, VII, IX, II, XI, XII, V, X, VIII, I, IV. Таким образом, наибольшую трещиностойкость имеет металл шва при сочетании стали СтЗ со сталью ЗОХГСА после закалки и отпуска, а наи меньшую —• при сочетании стали СтЗ со сталью 40Х после нор мализации.
Аналогичные опыты выполнены на двух партиях сборных об разцов (см. рис. 4.4) для двенадцати вариантов сочетаний иссле дуемых сталей с целью определения трещиностойкости металла шва в зависимости от марки присадка. В одной из партий в
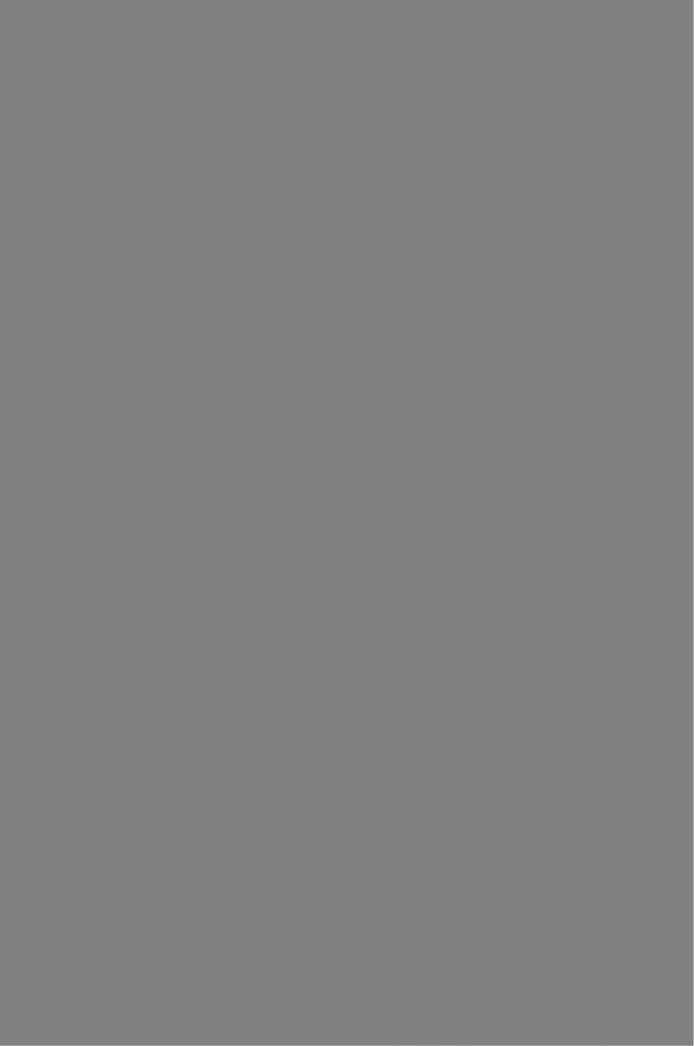