
книги / Несущая способность сварных соединений
..pdfкачестве присадка Использовали электроды из нержавеющей стали XI8H9T По ГОСТ 10052—62; сварку производили вручную. Во второй^ — ручную дуговую сварку’ выполняли в среде аргона электродом УОНИ-13/55 (ГОСТ 9488—75 й ГОСТ 9467—75).
Как и в предыдущих случаях, наибольшая трещийостойкостьхарактерна для металла шва сварного соединения из стали СтЗсо сталью ЗОХГСА после закалки и отпуска (вариант III). Зна
чения Кс=52,3_МПа-|/М — для присадка из стали XI8H9T к
Кс=67,5 МПаУМ — для присадка УОНЙ-13/55.
Во всех рассмотренных случаях трещиностойкость металла шва ниже трещиностойкости основного металла сварного соединения. Следовательно, несущую способность сварных соединений и конструкдий необходимо определять исходя из данных о трещино стойкости металла шва. Однако для получения наиболее полной информации необходимо располагать данными о трещиностойко сти металла зоны сплавления и зоны термического влияния (ЗТВ), где металл, как правило, претерпевает существенные структурные превращения.
4.7. СТАТИЧЕСКИЕ ИСПЫТАНИЯ ОБРАЗЦОВ СВАРНЫХ СОЕДИНЕНИЙ ИЗ АЛЮМИНИЕВЫХ СПЛАВОВ
Настоящие исследования являются продолжением наших работ [149], выполненных совместно с ИЭС им. Е. О. Патона, и посвя щены изучению статической трещиностойкости новых алюминн-
Т а б л и ц а 4.6
Прочностные характеристики алюминиевых сплавов при одиооеном растяжении
Марка |
Ориентация |
Прочностные свойства |
|
сплава |
прокатки |
СТВ. МПа |
сто.ь МПа |
|
|
||
АМгбНПП |
Продольная |
430 |
310 |
|
Поперечная |
410 |
290 |
1201 |
Продольная |
500 |
320 |
|
Поперечная |
490 |
310 |
1420 |
Продольная |
530 |
360 |
|
Поперечная |
500 |
340 |
евых сплавов (табл. 4.6 и 4.7) и их сварных соединений. Данные сплавы применяются для ответственных узлов и деталей в ави ационной технике и др.
Для изучения трещиностойкости алюминиевых сплавов и их сварных соединений, выполненных встык электронно-лучевой сваркой (ЭЛС) [143], вырезали прямоугольные брусья размером 10ХЮХ80 мм, из которых изготовляли цилиндрические образцы (см. рис. 4.1) с параметрами: D = 8 мм, dK= 6,5 мм, радиус дна
надреза р^0,2 мм, <р=60°, резьба по концам образца М8—6Л. Для определения трещиностойкости металла зоны сплавления и ЗТВ кольцевые надрезы выполняли в данных областях. Для изу чения текстуры прокатки в сплавах заготовки под образцы вы резали вдоль и поперек прокатки. Соответственно в первом слу чае вершина надреза совпадала с направлением прокатки, во втором — была ориентирована поперек ее.
Т а б л и ц а 4.7
Роет усталостных трещин ■ различных зонах сварных соединений из алюминиевых сплавов
В р е м я о б р а з о в а н и я т р е щ и н ы
Н а и м е н о в а н и е з о н ы |
|
|
|
|||
с и н и ц и и р о в а н н о й т р е щ и н о й |
А М г б Н П П |
1201 |
1420 |
|||
|
в о б р а з ц е |
|
||||
Граница сплавления |
2,6 |
2,4 |
2,2 |
|||
Шов |
|
|
|
3,1 |
2,9 |
3,3 |
Зона термического влия-» |
3,3 |
3,2 |
3,0 |
|||
ния |
|
|
|
|
|
5,7 |
Основной |
металл |
(попе |
4,6 |
6,5 |
||
речная |
ориентация) |
|
|
5,5 |
||
Основной |
металл |
(про |
4,5 |
6,3 |
||
дольная |
ориентация) |
|
|
|
Исходные кольцевые трещины в образцах получали на токар ном станке путем кругового изгиба при жестко-фиксированной стреле прогиба [80] (частота вращения образца о —7 с-1, стрела
|
Трещиностойкость Кс различных зон |
Т а б л и ц а |
4.8 |
|||||
|
|
|
|
|||||
|
сварных соединений из алюминиевых сплавов |
|
|
|||||
|
З о н а с и н и ц и и р о в а н н о й |
|
|
К с , М П а /М |
|
|
||
|
|
|
|
|
|
|||
|
т р е щ и н о й в о б р а з ц а х |
А М г б Н П П |
1201 |
1420 |
||||
|
|
|
|
|||||
|
Линия сплавления |
|
12,8 |
12,5 |
ИД |
|||
|
Шов |
|
|
13,8 |
11,3 |
10,9 |
||
|
Зона термического |
влия |
15,6 |
14,4 |
13,6 |
|||
|
ния |
|
|
|
|
|
|
|
|
Основной металл |
(попе |
15,9 |
22,6 |
17,7 |
|||
|
речная ориентация про |
|
|
|
|
|
||
|
катки) |
|
|
|
|
|
|
|
|
Основной металл |
(про |
15,1 |
19,9 |
16,3 |
|||
|
дольная ориентация про |
|
|
|
|
|
||
|
катки) |
|
|
|
|
|
|
|
прогиба /*=1,0 мм). Диаметр нетто-сечения при |
этом |
d = ( 6,0± |
||||||
±0,15) |
мм. |
усилия прогиба |
за |
счет снижения |
жесткости |
|||
По |
изменению |
|||||||
образца в связи |
с зародившейся |
трещиной установлено время, |
необходимое для образования кольцевой трещины заданной глу бины в исследуемых партиях образцов из алюминиевых сплавов трех марок (см. табл. 4.7).
Бремя образования трещины t и трещиностойкоеть Кс ■а различных зонах сварного соединения из сплава 1420
Тип сварки п режим |
термообработки |
Зона |
инициирования |
t. |
Кс. |
|||
|
трещины |
мин |
МПа/М |
|||||
|
1 |
|
1 |
|
4 |
|
3 |
* |
Электронно-лучевая сварка (ЭЛС) |
' |
|
|
|
|
|
||
|
|
|
|
|
|
|||
С термообработкой после сварки: за Шов |
после термооб |
4,2 |
12,3 |
|||||
калка + искусственное старение-}-свар- работки |
(393 |
К, 8 ч) |
||||||
ка+искусственное старение |
|
|
|
|
|
|
||
Без термообработки: закалка+ искус Шов |
без термообра |
4,3 |
12,4 |
|||||
ственное старение+сварка |
ботки |
|
|
|
||||
С термообработкой после сварки: заЛиния сплавления пос |
|
|
||||||
'чалка+ искусственное старение+свар ле |
термообработки |
5,3 |
14,3 |
|||||
ка-(-искусственное старение |
(393 К. 8 ч) |
|
||||||
Без |
термообработки: закалка+искус Линия сплава |
без тер |
3,3 |
12,7 |
||||
ственное старение+сварка |
мообработки |
|
||||||
С термообработкой после сварки: за Зона |
|
термического |
|
|
||||
калка + искусственное старение+свар влияния, после термо |
|
|
||||||
ка + искусственное старение |
обработки (393 К, 8 ч) |
5,5 |
14,7 |
|||||
Без |
термообработки: закалка+ искус Зона |
|
термического |
|
|
|||
ственное старение+сварка |
влияния |
без термооб |
|
|
||||
|
|
|
работки |
|
|
3,0 |
10,3 |
|
Аргоно-дуговая сварка (АДС) |
|
|
|
|
|
|
||
С термообработкой после сварки: за Шов |
после термооб |
2.8 |
8,8 |
|||||
калка + искусственное старение+ свар работки |
(393 |
К, 8 ч) |
||||||
ка + искусственное старение |
|
|
|
|
|
|
||
Без термообработки: закалка+ искус Шов |
без термообра |
3,0 |
9,1 |
|||||
ственное старение+сварка |
ботки |
|
|
|
||||
С термообработкой после сварки: за Линия сплавления пос |
|
|
||||||
калка + искусственное старение+свар ле |
термообработки |
3,5 |
10,1 |
|||||
ка + искусственное старение |
(393 К, 8 ч) |
|
||||||
С |
термообработкой: |
закалка+сварЛиния сплавления пос |
|
|
||||
ка+искусственное старение |
ле |
термообработки |
3,2 |
9,3 |
||||
|
|
|
(393 К, |
8 ч) |
|
|||
.Без термообработки: закалка+ искус Линия |
сплавления без |
3,7 |
10,9 |
|||||
ственное старение+сварка |
термообработки |
|||||||
Без термообработки: закалка+ искус Зона |
|
термического |
|
|
||||
ственное старение+сварка |
влияния |
без термооб |
4,0 |
15,3 |
||||
Основной металл |
|
работки |
|
ориента |
||||
|
Поперечная |
5,9 |
19,8 |
|||||
|
|
|
ция прокатки |
ориента |
||||
|
|
|
Продольная |
5,8 |
19,4 |
|||
|
|
|
ция прокатки |
Как видим, минимальную сопротивляемость усталостному разрушению имеют образцы с трещиной на границе сплавления для трех марок сплавов, максимальную — основной металл с поперечной и продольной ориентацией прокатки. Металл шва и ЗТВ занимают промежуточное положение по сопротивляемости усталостному разрушению.
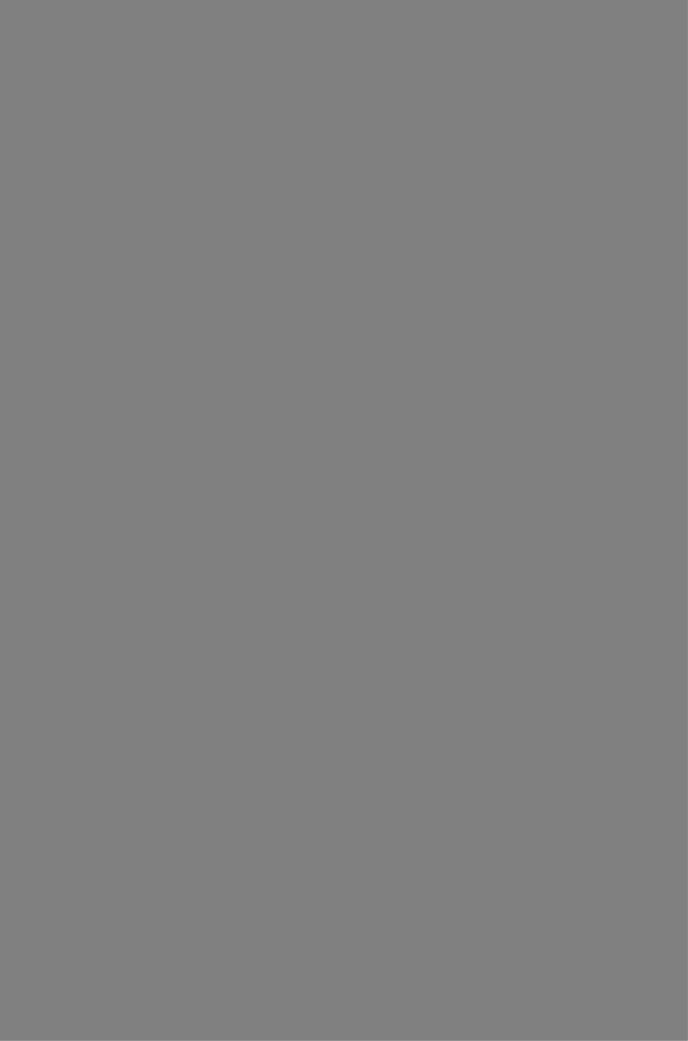
Т а б л и ц а 4.10
Изменение твердости сталей 60С2А и 65Г после закалки и температурного отпуска
Марка стали и режим |
|
Температура |
Диаметр за |
Твердость, |
|
термообработки |
|
отпуска, К |
готовки |
HRC |
|
|
|
|
|
D ,мм |
|
Сталь |
60С2А закалка |
в |
473 |
16,0 |
51 |
<(1073 |
К), охлаждение |
573 |
|
45 |
|
масле |
|
|
623 |
|
41 |
То же |
|
523 |
12,0 |
48 |
|
|
|
|
623 |
|
42 |
Сталь |
65 Г: закалка |
|
673 |
|
36 |
в |
523 |
16,0 |
46 |
||
(1093 |
К), охлаждение |
573 |
|
42 |
|
масле |
|
|
623 |
|
38 |
|
|
|
673 |
|
35 |
|
|
|
723 |
|
32 |
|
|
|
773 |
|
28 |
То же |
|
523 |
12,0 |
46 |
|
|
|
|
573 |
|
42 |
|
|
|
623 |
|
38 |
|
|
|
673 |
|
35 |
|
|
|
723 |
|
32 |
|
|
|
773 |
|
28 |
Опыты на ударный изгиб проводили на маятниковом копре МК-75 с развиваемой энергией молота при ударе 110 Дж. Работу разрушения KCV определяли по формуле (4.11). Полученные результаты приведены в табл. 4.11.
|
|
Т а б л и ц а 4.11 |
|
K C V для пружинных сталей 60С2А |
|
|
|
и 65Г после испытаний на ударный изгиб |
|
||
Сталь 60С2А |
Сталь 65Г |
||
Температура |
KCV, |
Температура |
KCV, |
отпуска, К |
Дж/см2 |
отпуска* К |
Дж/см2 |
Пруток 0 |
.16 мм |
Пруток 0 |
16 мм |
473 |
69,0 |
523 |
64,0 |
573 |
61,0 |
573 |
77,0 |
623 |
67,0 |
623 |
191,0 |
|
- |
673 |
264,0 |
___ |
|
723 |
436,0 |
— |
---- |
773 |
430,0 |
Пруток 0 |
12 мм |
Пруток 0 |
12 мм |
523 |
69,0 |
523 |
46,0 |
623_ |
63,0 |
573 |
43,0 |
723 |
99,0 |
623 |
72,0 |
|
|
673 |
187,0 |
|
___ |
723 |
278,0. |
— |
— |
773 |
507,0 |
1S/
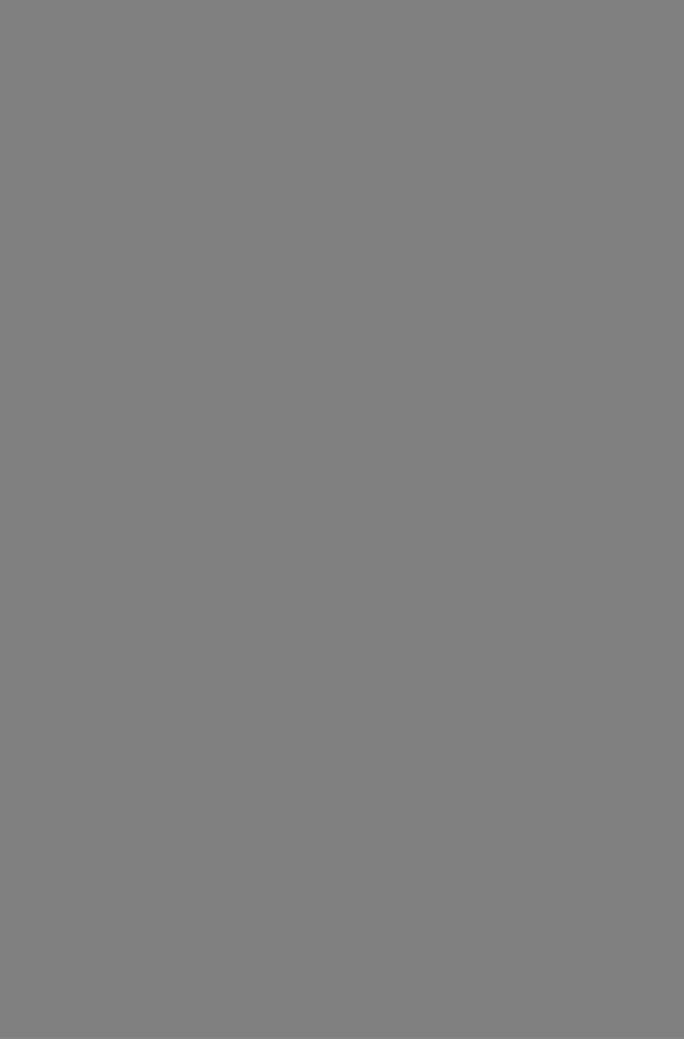
минимальное сопротивление зарождению трещины для стали 40Х в нормализованном виде несколько ниже, чем у стали ЗОХГСА после нормализации. Более высокую сопротивляемость зарож дению усталостных трещин имеет сталь 40Х после закалки и от пуска 773 К (табл. 4.12).
Результаты усталостных испытаний согласуются с результа тами статических испытаний, что подтверждает корректность про веденных опытов.
|
|
|
|
Та б л и ц а 4.12 |
Циклическая трещиностойкость конструкционных сталей |
||||
Марка |
стали и режим |
К1Л, МПау'М |
Kfc. М П ауМ |
|
|
термообработки |
|||
Сталь |
40Х после нормали |
20,8 |
83,6 |
|
зации |
(1113 К) |
|
|
|
Сталь ЗОХГСА после норма |
21,5 |
98,7 |
||
лизации |
(1133 К) |
|
|
|
Сталь 40Х после закалки и |
23,0 |
103,8 |
||
отпуска |
(773 К) |
|
|
4.10. ТР ЕЩ И Н О С ТО Й К О С ТЬ М ЕТА Л Л А СВА РН Ы Х СО ЕД И Н ЕН И Й ПРИ НАЛИЧИИ Д ЕФ ЕК Т О В
Практика эксплуатации сварных конструкций и анализ причин их разрушения показывают, что хрупкие и квазихрупкие разруше ния происходят, как правило, из-за технологических дефектов: непроваров и несплавлений, обусловливающих неоднородность свойств отдельных участков соединения и появление в них зон с пониженной деформационной способностью. Поэтому при выборе методики оценки способности сварных соединений к хрупким раз рушениям следует учитывать результаты испытаний образцов, в которых воспроизведены условия сварки. Последние в процессе
зарождения хрупкого разрушения |
могут |
оказаться решающими. |
С другой стороны, для дефектов |
сварки |
(непровары, несплавле- |
ния) острота в вершине, как правило, больше остроты усталост ной трещины. Так, радиус в вершине непровара изменяется в до вольно широких пределах р = 0,001... 1 мм.
В связи с этим использование критериев разрушения, напри мер, Kic и 5с, может привести к существенным погрешностям, поскольку они справедливы, строго говоря, для концентраторов напряжений типа трещин.
Для оценки сопротивляемости металла сварных соединений квазихрупкому разрушению предложен деформационный крите рий Vic — критический коэффициент интенсивности деформаций, учитывающий изменение механических свойств в зоне концен-
ш
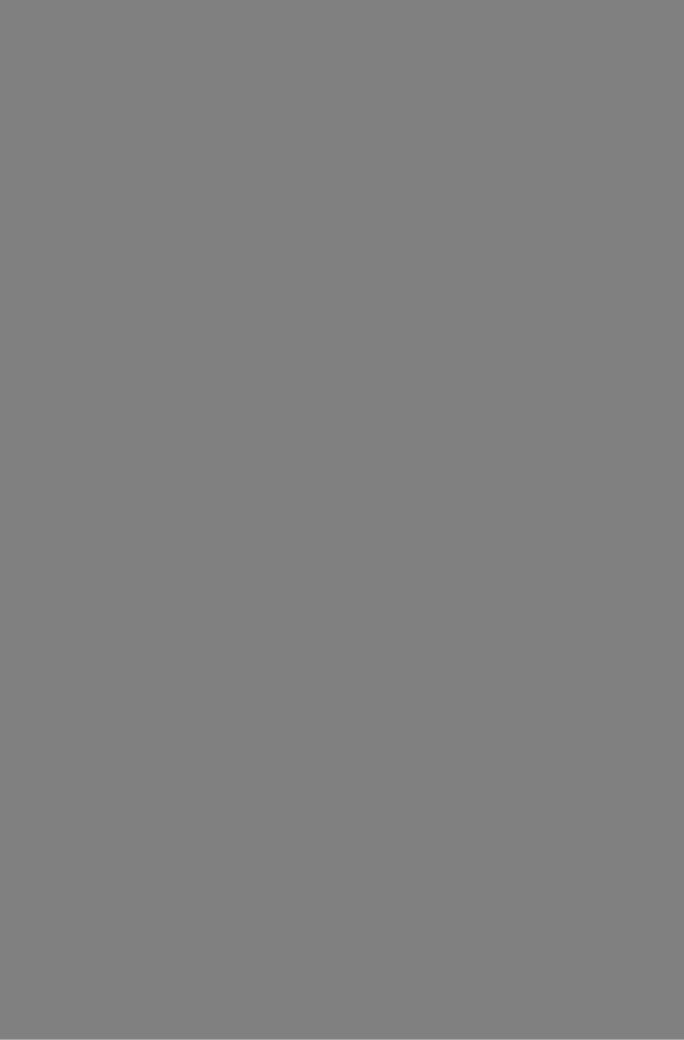
шины трещиноподобного концентратора, которая определяется формой и размерами образца, конфигурацией и местом располо жения дефекта, а также схемой нагружения.
В отличие от критерия Кю описывающего разрушение в усло виях максимального стеснения пластических деформаций, крите рий 6Сучитывает вид напряженного состояния в окрестности вер шины концентратора, местоположение дефекта, форму образца и схему нагружения и является наиболее приемлемым для анализа
XJC Ш, мла i/м
Рис. 4.14. Изменение вязкости разру
шения Kic(p) Км(р) от |
радиуса |
в вершине концентратора |
р [140, |
208] |
|
</ — феррнтоперлнтиая сталь; 2 — сталь типа 40XH2M).
Рис. 4.15. Образец для оцен ки трещиностойкостн металла сварных соединений (штрихо вые линии — поле линий скольжения в нетто-сеченнн
образца).
локального разрушения сварных соединений с трещиноподобны ми дефектами.
Для установления связи между критическим раскрытием тре щиноподобного концентратора и радиусом в его вершине [179] использована зависимость (4.21) между критерием Винокурова [36] Vic и вязкостью разрушения Kic» а также между силовым и деформационными критериями Kic и 6С [104]:
где а* — коэффициент, зависящий от коррекции на зону пластич ности.
С учетом этого получено выражение
5С= a* J — е£„ р. |
(4.24) |
4 от |
|
В литературе известны различные значения а*, зависящие от места, в котором определяется КРТ. В результате упругопласти ческих расчетов получены значения а*= 1—4/л [28]. Экспери ментально установлено, что а*«1 [192, 201, 203, 205].
Выражение (4.24) позволяет связать критическое раскрытие трещиноподобного концентратора б /= 6 с(р) с ресурсом пластич
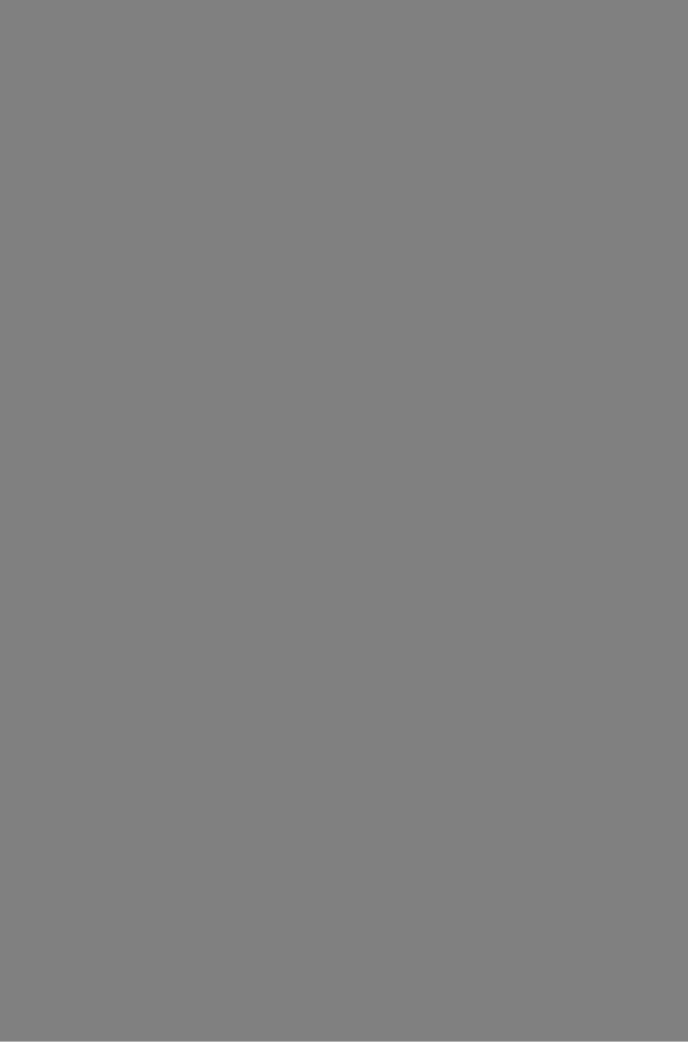