
книги / Технологические процессы и технические средства для глубинно-насосной эксплуатации нефтяных скважин
..pdf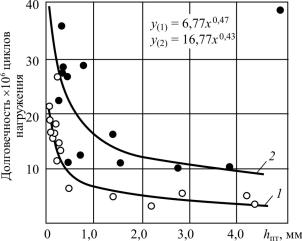
ме аппроксимации минимизировалась величина максимальной абсолютной погрешности, при этом максимальные относительные погрешности составили 72 и 102 %, а средние относительные погрешности 21 и 28 % для уравнений (1.2) и (1.3) соответственно. В графическом виде полученные зависимости представлены на рис. 1.17.
Рис. 1.17. Зависимость долговечности насосных штангот величины слояспониженнойтвердостью(hпт): 1 – насоснаяштанга, изготовитель Очёрский машзавод, г. Очёр, сталь20Н2М, режимтермообработки нормализация; 2 – насосная штанга, изготовительмашзавод
им. В.И. Ленина(г. Пермь), сталь15Х2НМФ, режимтермообработки закалка ивысокий отпуск
Из анализа графического материала, представленного на рис. 1.17, следует:
–долговечность штанг, прошедших нормализацию из стали 20Н2М, и термоулучшенных штанг из стали 15Х2НМФ, уменьшается по закону, близкому к гиперболическому, при увеличении толщины слоя с пониженной твердостью;
–вид полученных зависимостей для штанг из различных сталей практически одинаковый, следовательно, аналогичны и физические причины, вызывающие усталостное разрушение штанг;
41
–взаимное расположение кривых, изображенных на рис. 1.17, свидетельствует о влиянии на усталостную прочность материала штанг комплекса стандартных механических свойств (см. табл. 1.2), которые
утермоупроченной стали 15Х2НМФ в целом выше, чем у нормализованной стали 20Н2М;
–существенный разброс экспериментальных результатов относительно аппроксимирующих зависимостей является следствием многофакторности усталостного разрушения каждой отдельной штанги. Различные факторы, как из числа рассмотренных, так и неучтенные, действуя в самых разнообразных сочетаниях, могут ускорять или, наоборот, замедлять процесс усталостного разрушения. И тем не менее на фоне этого многообразия два фактора являются доминирующими – это местная пластическая деформация и поверхностный слой с пониженной микротвердостью, достигающий 1 мм и более у образцов (фрагментов) насосных штанг со скважин №№ 427, 975, 507, 647, 1057, 513, 2276, 399, 339, 858, 505, 694. Механические характеристики образцов (фрагментов) с данных скважин представлены в табл. 1.5.
Введенное понятие «слой с пониженной микротвердостью» не дает представление о физической природе этой аномалии материала штанг. Исходя из объема выполненных исследований, можно перечислить ряд предположений относительно появления протяженного слоя с пониженной твердостью по длине и радиусу штанги:
–первопричина появления данного слоя – внутренняя неоднородность материала штанг, связанная, например, с различной скоростью охлаждения наружной криволинейной поверхности и ее сердцевины после термической обработки;
–вторая причина появления протяженного слоя с пониженной твердостью – продольная деформация изделия, например насосной штанги, имеющей неоднородную структуру как по длине, так и в пределах поперечного сечения под воздействием растягивающей нагрузки; механизм образования протяженного слоя с пониженной твердо-
стью (hпт) под воздействием продольной растягивающей нагрузки представлен на рис. 1.18;
42
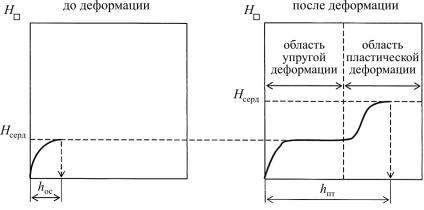
Рис. 1.18. Механизм образования протяженного слоя с пониженной твердостью: hос – глубина обезуглероженного слоя; hпт – толщина слоя с пониженной твердостью
–любая внутренняя неоднородность по длине и в пределах поперечного сечения штанг и при восстановлении ее прямолинейности может вызвать неоднородную упругопластическую деформацию ее тела, следствием чего должно стать появление поля внутренних напряжений. Например, если поверхность деформируется упруго, а центр пластически, то это должно вызвать наклеп в сердцевине и, как следствие, увеличение протяженности слоя с пониженной микротвердостью. При этом в поверхностном слое должны появиться неблагоприятные растягивающие напряжения, резко снижающие усталостную долговечность деталей [22].
Таким образом, с учетом полученных результатов для существенного повышения долговечности насосных штанг необходимо следующее:
–разработка организационных мероприятий и совершенствование технических решений, исключающих или сводящих к минимуму местную пластическую деформацию штанг, обезуглероживаение поверхности штанг и обеспечивающих формирование протяженного слоя по длине с требуемой микротвердостью;
43
–разработка и совершенствование методов упрочнения поверхности штанги, комплексно повышающих поверхностную твердость и сопротивление пластической деформации, создающих благоприятные напряжения сжатия;
–разработка и совершенствование методов, технических средств разрушающего и неразрушающего контроля при изготовлении насосных штанг и эксплуатации;
–разработка и совершенствование методов, технических средств, снижающих величину силового воздействия на колонну штанг.
Перечисленные предложения – основа для проведения исследований, выработки технических решений и совершенствования нефтепромыслового оборудования, технологических процессов для осуществления эффективной работы глубинного плунжерного насоса.
Технические и технологические методы обеспечения новых качественных показателей работы нефтепромыслового оборудования и устройств
Процесс добычи нефти осложнен условиями эксплуатации нефтепромыслового оборудования в добываемых жидкостях, содержащих:
–асфальтосмолопарафинистые отложения (АСПО);
–высоковязкие нефтяные эмульсии (ВВЭ);
–неорганические соли;
–гидратные и парафиновые образования;
–механические примеси;
–коррозионно-активные компоненты в составе добываемой жидкости.
С учетом физико-химических особенностей добываемых жидкостей установлены следующие определяющие технические предложения, направленные на повышение надежности нефтепромыслового оборудования, эффективности при его использовании и расширение его функциональных возможностей.
Термическое воздействие на материал насосной штанги:
–низкотемпературная термическая обработка насосной штанги из горячедеформированной заготовки;
44
–химико-термическое упрочнение концевых участков насосной штанги, обеспечивающее ее восстанавливаемость;
–упругопластическая деформация тела насосной штанги при нормальных условиях среды;
–холодная правка и контроль насосных штанг продольным нагружением;
–упрочнение длинномерных цилиндрических изделий, например насосных штанг, действием продольной растягивающей нагрузки и кручения;
Неразрушающий контроль и исследование технических показателей насосных штанг при изготовлении и эксплуатации:
–неразрушающий магнитолюминесцентный контроль концевых участков насосных штанг;
–неразрушающий контроль состояния поверхности и подповерхностного слоя концевого участка насосной штанги методом измерения шумов Баркгаузена при коррозионно-усталостном ее испытании;
–неразрушающий магнитоиндукционный контроль насосной штанги при напряжении в ее теле, превосходящем эксплуатационное;
–неразрушающий контроль растяжением технических показателей насосной штанги;
–неразрушающий контроль структуры металла протяженного изделия (насосной штанги) растяжением и кручением;
–неразрушающий контроль растяжением и кручением технических характеристик насосной штанги;
–неразрушающее определение предела выносливости длинномерного изделия, например насосной штанги из стали 20Н2М;
–неразрушающее определение предела пропорциональности материала насосных штанг (предела микротекучести) по кривым магнитоупругого размагничивания под действием продольной растягивающей нагрузки.
Разрушающий контроль и исследование технических показателей фрагментов насосных штанг при изготовлении и эксплуатации:
–усталостные испытания натурных фрагментов насосных штанг
вкоррозионной среде (изгиб с вращением, плоский изгиб, вибродинамическое воздействие на фрагмент);
45
–усталостные испытания фрагментов насосных штанг на пульсаторе при асимметричном режиме их нагружения.
Снижение величины силового воздействия на колонну штанг достигается:
–изменением реологических свойств добываемой жидкости (тепловое, магнитное воздействие на жидкость);
–механической очисткой насосных штанг и насосно-компрессор- ных труб от асфальтосмолопарафинистых отложений (АСПО);
–тепловым воздействием на внутрискважинное пространство для предупреждения и ликвидации гидратных и парафиновых образований в подземных трубах нефтяных и газовых скважин;
–через упругое деформирование колонны насосных штанг;
–конструированием головки, тела насосной штанги, колонны штанг, специального оборудования с учетом осложненных условий нефтедобычи;
–на основе результатов текущих исследований и моделирования работы наземного и погружного нефтепромыслового оборудования с учетом данных его эксплуатации в промысловых условиях;
–путем установки демпферов для уменьшения амплитуды или исключения вынужденных колебаний в колонне штанг.
Консервация погружного и наземного нефтепромыслового оборудования осуществляется на основе консервационного состава, обеспечивающего защиту поверхности оборудования от преждевременного разрушения.
Перечисленные предложения послужили основой для проведения исследований и разработки технических решений, обеспечивших
вдальнейшем эффективную работу глубинного плунжерного насоса.
1.5.Изготовлениенасосной штанги изгорячедеформированной заготовкинизкотемпературной термической обработкой
Техническая и экономическая целесообразность способа – повышение предела выносливости штанг как единого целого, повышение его стабильности и снижение обрывности насосных штанг [23, 24, 25, 26].
46
Способ раскрывается в ходе рассмотрения существующего технологического процесса изготовления насосных штанг на Очёрском машзаводе. Первой операцией при изготовлении является высадка концов штангового проката, в процессе которой происходит формирование головки с ниппелем, буртиком, квадратом и галтелью. Нагрев проката осуществляют в индукторе до температуры 1250 ° С. Высокотемпературный нагрев приводит к тому, что в районе головки штанги формируется крупнозернистая структура с характерным видманштеттовым строением. Для устранения этой структуры, повышения вязкости, снижения твердости и улучшения обрабатываемости резанием после высадки головок штанги проводят ее термическую обработку. В соответствии с данным техническим решением такой термической обработкой является нормализация с нагревом до 870 ° С в течение 0,5 ч.
На нормализацию поступают горячедеформированные заготовки штанг со структурой оскольчатого видманшеттова феррита, кристаллографически ориентированного относительно исходно деформированного и текстурированного аустенита. В результате при нагреве заготовок в процессе нормализации вновь образующимся аустенитом наследуется кристаллографическая ориентировка аустенитных зерен
впрокате. В процессе охлаждения заготовок штанг формируется полосчатая ферритно-сорбитная структура, которая в сравнении с однородной ферритно-сорбитной структурой проката снижает предел выносливости штанг в среднем на 20 %. Полосчатость ферритно-сорбит- ной структуры обусловлена преимущественной диффузией углерода к границам деформированного и текстурированного аустенита при охлаждении в межкритическом интервале температур.
Вданном способе после высадки головок заготовки штанг подвергают низкотемпературному отжигу 1-го рода при температуре 500–700 ° С с охлаждением на воздухе. Использование низкотемпературного отжига взамен нормализации позволяет повысить предел выносливости тела и штанг в целом, снизить вероятность обрыва насосных штанг. При этом некоторое снижение предела выносливости
ввысаженных концах штанг в достаточной степени компенсируется
47
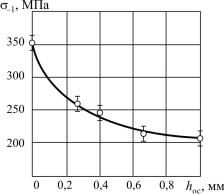
их массивностью (площадь сечения головки примерно в два раза больше площади сечения тела).
К числу факторов, оказывающих существенное влияние на величину предела выносливости штанг и их обрывность при эксплуатации, как показали исследования, представленные в [27], относятся обезуглероживание поверхности, структурная полосчатость тела штанг, а также неблагоприятные напряжения и пластическая деформация до критической величины, возникающие при правке.
Исследуемый низкотемпературный отжиг с нагревом до 500– 700 ° С практически не создает дополнительного обезуглероживания, глубина слоя остается такой, какая сформировалась в ходе проката заготовок, и составляет 0,086±0,033 мм. Влияние глубины обезуглероженного слоя (hос) на величину предела выносливости стали 20Н2М изображено на рис. 1.19. Глубина обезуглероженного слоя в штангах определялась методами М и МТ согласно ГОСТ 1783–68.
Как следует из рис. 1.19, обезуглероживание на глубину 0,23 мм, создаваемое прокатным нагревом и нормализацией при 870 ° С, влечет снижение предела выносливости до 270 МПа. Обезуглероженный слой глубиной 0,086 мм, полученный в результате только прокатного нагрева, поскольку низкотемпе-
|
ратурный отжиг при 500–700 ° С |
|
невносил дополнительного обез- |
|
углероживания, снижает предел |
|
выносливостилишьдо325 МПа. |
|
Уменьшение глубины обез- |
|
углероженного слоя при замене |
|
нормализации на низкотемпе- |
|
ратурный отжиг позволяет по- |
|
высить предел выносливости |
|
в среднем на 17 %. При низко- |
Рис. 1.19. Зависимость предела |
температурном отжиге с нагре- |
вом до температур, не превы- |
|
выносливости (σ–1 ) насосной штанги |
шающих Ас1, не происходит фа- |
от глубины обезуглероженного слоя |
зовой перекристаллизацииисох- |
|
48
раняется сравнительно однородная ферритно-сорбитная структура проката.
Правка штанг – операция, в обязательном порядке проводимая после нормализации в существующем способе на Очёрском машзаводе, не является необходимой непосредственно после низкотемпературного отжига при температуре 500–700 ° С, поскольку такой нагрев с охлаждением на воздухе, как показали эксперименты, не вызывает нарушение пространственной геометрии тела штанг. Правка штанг в предложенном способе имеет цель облегчить требуемую соосность тела и головки штанг и может быть проведена как после отжига либо после охлаждения на воздухе, так и до отжига, непосредственно после высадки головки. В последнем случае нагрев деформированной штанги до температур 500–700 ° С полностью устраняет самые незначительные остаточные напряжения и наклеп, полученный при правке. Пластическая деформация при 500–700 ° С (теплая деформация) сопровождается не только повышением плотности дислокаций, но и одновременным их перераспределением с образованием малоподвижных устойчивых конфигураций среднеугловых субграниц. Такие дислокационные конфигурации неблагоприятны для образования зародышевых усталостных трещин.
Нагрев до температуры 500–700 ° С позволяет устранить остаточный наклеп в высаженных частях штанги, понизить твердость, улучшить обрабатываемость материала штанги резанием, повысить характеристики пластичности, выводя механические свойства на уровень требуемых ГОСТ 13877–80, а также устраняет самые незначительные остаточные напряжения. Более низкая температура нагрева (ниже 500 ° С) не обеспечивает требуемого снижения твердости материала штанг, поскольку в этом случае не будет достигнута температура рекристаллизации стали. Более высокая температура (свыше 700 ° С) лежит выше температуры фазовой перекристаллизации, и нагрев выше этой температуры сопровождается как дополнительным обезуглероживанием поверхности, так и повышением напряжений за счет образования новой фазы и, как следствие, увеличением коробления штанги. Перегрев головки штанги в процессе ее высадки, не устраняемый отжигом при температуре 500–700 ° С, не приводит
49
к снижению предела выносливости штанги как целого, о чем свидетельствуют результаты усталостных испытаний: 100 % испытанных штанг с перегревом в головке (номер зерна 5 и менее) разрушились по телу, имеющему меньшее сечение по сравнению с головкой.
Способ изготовления насосной штанги из горячедеформированной заготовки, низкотемпературной термической обработкой был опробован в производственных условиях Очёрского машзавода при изготовлении насосных штанг из стали 20Н2М.
Материалом для исследования служил штанговый прокат диаметром 19 мм и длиной 8000 мм.
Оборудование, используемое для осуществления предложенного способа:
– высокочастотная установка ВПЧ-100/8000 с индуктором 0774-6074 для нагрева концов штанг под высадку головок до температуры 1250 ° С за 16–26 с;
–ковочный 4-ручьевой пресс для высадки головок;
–газопламенный проходной агрегат для низкотемпературного отжига штанг конструкции ВНИИ «Теплопроект» с 12 температурными зонами; время выдержки 28 мин;
–установка для растяжения штанг с усилием до 18 тс, скоростью деформации до 1,5 м/мин, ходом подвижной части до 780 мм (Г8337.022.00.00.00.00СБ; разработчик – ПКТБхиммаш, г. Пермь);
–автоматическая линия для механической обработки головок штанги и нарезки резьбы (ЛМ0768).
Концы заготовки насосных штанг нагревали в индукторе высокочастотной установки до температуры 1250±30 ° С в течение 16–26 с, после чего высаживали концы штангового проката, формируя головку штанги с ниппелем, буртиком, квадратом и галтелью. Следующим этапом проводили низкотемпературный отжиг в газопламенном проходном агрегате. Температура нагрева по зонам изменялась в диапазоне от 550 до 590 ° С, время выдержки 28 мин. Штанги охлаждали на воздухе до температуры цеха. После этого заготовки правили на установке для растяжения штанг с усилием до 18 тс и удлинением не более 120 мм на длине 8000 м. Завершающие операции – механи-
50