
книги / Разрушение твердых тел
..pdf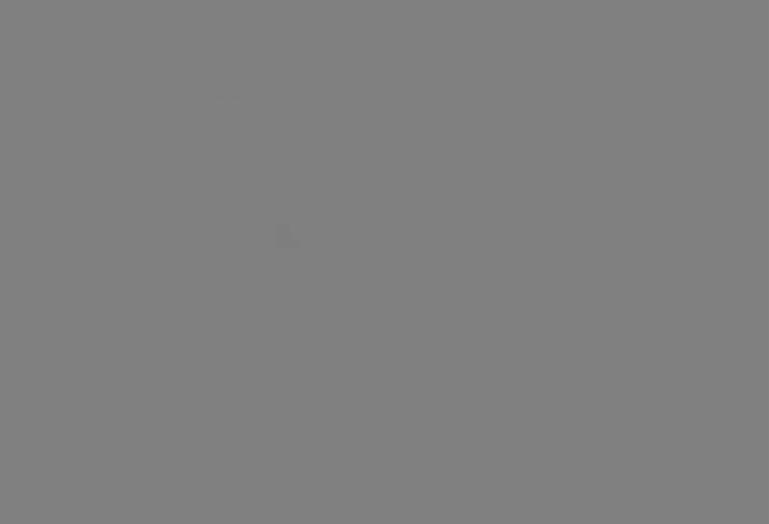
При исследовании многих трещин не было обнаружено ни одно го случая предварительного образования обособленных микро трещин; пример показан на рис. 22,6.
На основании результатов описанных опытов можно сделать два вывода:
1.Образование субзерен само по себе не является достаточ ным условием для развития усталостных трещин в алюминии; для зарождения трещин по субграиицам необходимо наличие свободной поверхности, хотя специфическая роль поверхности здесь менее ясна, чем в более четко выраженном случае разви тия трещин по плоскостям скольжения.
2.Развитие трещин под поверхностью происходит в резуль тате раскрытия границ субзерен или границ зерен, непосредст венно прилегающих ж вершине трещины, а не в результате само стоятельного дискретного зарождения и последующего слияния трещин, «ак это предполагал Холден [24].
Довольно трудно сделать какое-либо заключение относитель
но возможности применения критерия критического напряжения, рассмотренного Холденом [24], для случая развития трещин по субграницам.
Другая возможность, рассмотренная в статье Холдена [24], заключается в том, что субструктура является причиной образо вания непродвигающихся усталостных трещин. В частности, предполагалось, что образование трещин вызывается напряже ниями, развивающимися в результате удовлетворения условий совместимости при переходе пластической деформации через сильно искаженные субграницы. Так, трещина не будет продви гаться, если пластически деформированный объем в области ее вершины находится целиком в пределах одного субзерна. Исхо дя из того, что даже при самых тщательно контролируемых опы тах на монокристаллах наблюдается большое число зарождаю щихся, но не развивающихся далее трещин, можно считать изложенную идею вполне удовлетворительной. Большая роль субграниц в развитии трещин дает еще одно подтверждение существования корреляции между энергией дефектов упаковки и скоростью роста трещин, установленной в работах Фроста [26]; результаты исследования на усталость при пульсирующем рас тяжении надрезанных образцов различных материалов, в кото рых энергия дефектов упаковки изменяется от высокого значе ния для алюминия до низкого значения для аустенитной нержа веющей стали, показывают, что образование субструктуры при понижении энергии дефектов упаковки затрудняется параллель но с уменьшением скорости развития трещин.
Накопление данных относительно образования субструктур при усталости подсказывает еще одну интересную теорию. Впол не возможно, что тенденция к образованию субструктур влияет на величину изменений рельефа поверхности образца, которые
181
необходимы для образования зародышей трещин и должны про изойти до того, как может быть рост трещин. Описанные экспе рименты Чина [78] показывают, что при хорошо развитой суб структуре большие изменения рельефа совершенно не обяза тельны для развития трещин. Железо также склонно к развитию субструктур [24, 30] и деформируется карандашным скольжени ем. В то же время случаи появления мощных экструзий и интру зий в железе, испытанном на усталость, весьма редки [63]. Воз можно, что в данном случае этот эффект (возникновение суб структуры) ведет к тому, что образование зародышей трещин может происходить лишь при умеренных искажениях поверхно сти, например в области внутренних несплошностей (поверхно стей раздела матрица — включение), или у других мало стеснен ных поверхностей. Вероятно, результаты многих наблюдений подповерхностных трещин, часто используемые как аргумент против необходимости наличия свободной поверхности для обра зования трещины, могут быть объяснены на этой основе.
Опыты на системе Си—А1
Из рис. 17 ясно вытекает четкая зависимость скорости роста трещин от энергии дефектов упаковки в поликристаллических сплавах, изучавшихся в данной работе. Для подтверждения той мысли, что уменьшение долговечности связано с повышени ем энергии дефектов упаковки, но никоим образом не с умень шением напряжения течения в сплавах с пониженным содержа нием алюминия, дальнейшие эксперименты были проведены на сплаве С и + 8% Ni, имеющем зерно того же размера. Энергия дефектов упаковки в этом сплаве будет несколько выше, чем у меди, в то время как напряжение течения было близко к напря жению течения сплавов с высоким содержанием алюминия. Дол говечность этого сплава была ниже, чем у меди, откуда следует, что энергия дефектов упаковки действительно является основ ным определяющим параметром.
Доказательства существования субструктур в поликристал лах Си — А1 ограничивались наблюдением дебаевских колец на рентгенограммах, получаемых с поверхностей образцов из спла вов меди с содержанием алюминия 2% или менее, доведенных до усталостного разрушения. Некоторые результаты измерений колец приведены на рис. 15. У монокристаллов дебаевские коль ца были получены лишь на чистой меди; в этом случае связь их с субструктурой была очевидной и непосредственной, так как субзерна хорошо выявляются в области расположения трещин,
видимых |
на |
металлографических шлифах, |
как например на |
||
рис. 25, а. Исходя из схемы, представленной |
на |
рис. 21, |
можно |
||
считать, |
что |
материал непосредственно вблизи |
трещины |
может |
|
перейти |
в следующую область — В ; вероятно, другие трещины, |
182
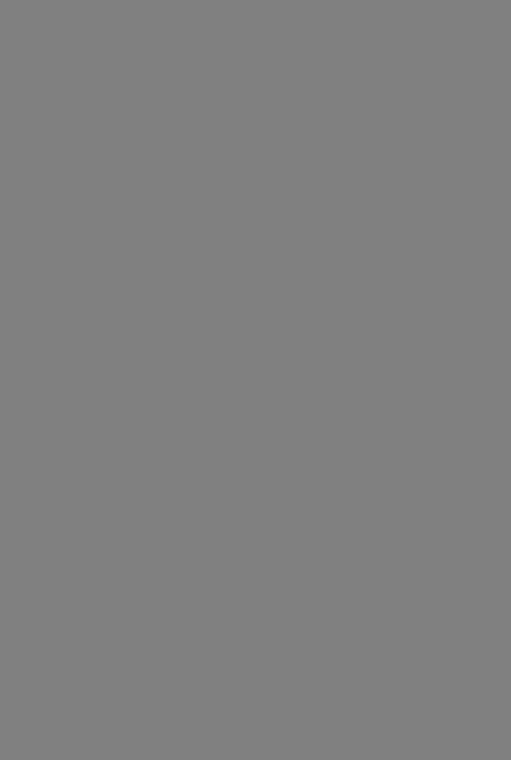
шения монокристаллов чистой меди. Трещина развивается в глу бину в областях, где активные плоскости скольжения являются плоскостями первичного и поперечного скольжения, а период от зарождения трещины до разрушения образца увеличивается примерно в 2,5 раза, по сравнению с долговечностью чистой меди. Травление выявляет лишь прямолинейные кристаллогра фические следы скольжения. Пятна Лауэ для кристалла S8 после 8* 105 циклов нагружения не выявляют признаков суб структуры.
Вид трещин аналогичен получаемому при коррозионном рас трескивании под напряжением и, следовательно, может быть
Рис. 26. Схема возможных механизмов прерыви стого скольжения, связанных с образованием окислов на ступеньках скольжения:
а — в первую четверть цикла действует плоскость а — а \ тогда как скольжение по плоскости б — б' требует затя гивания частиц оксидов на плоскость скольжения; б — при обратном знаке напряжения действует плоскость б — б', так как частицы окислов, только что образовав шиеся по а — а', препятствуют скольжению в обратном
направлении
связан с воздействием среды. Сванн и Наттинг [85] недавно вы сказали предположение о том, что чувствительность к образова нию трещин в результате коррозии под напряжением должна возрастать с понижением энергии дефектов упаковки. Сходные данные вытекают из результатов опытов Водсворта и Хатчингса [86], проводивших испытание на усталость при постоянном на
пряжении; они нашли |
увеличение долговечности |
примерно в |
20 раз при испытании |
меди в вакууме ~ 1 0 -2 мм |
рт. сг., в то |
же время на долговечность химически инертного золота вакуу мирование не оказало влияния. Уже высказывалось предположе ние о том, что образование окислов на только что возникших ступеньках скольжения способствует образованию трещин по плоскостям скольжения, так как частицы окислов под действи ем циклической деформации затягиваются внутрь кристалла [87]. Как схематично показано на рис. 26, прерывистое скольжение может, по-видимому, также зависеть от окисления. Можно ожи дать, что в сплаве с низкой энергией дефектов упаковки и интен-
184
сивным латентным упрочнением, ограничивающим скольжение преимущественно единственной системой плоскостей, трещины должны распространяться на большие расстояния, прежде чем концентрация напряжений вызовет их переход в другую плос кость.
Рассмотрим теперь общую картину продвижения трещин, ис ходя из данных различных наблюдений. Если энергия дефектов упаковки возрастает, плоскость развития трещин изменяется чаще (так как снижается скрытое упрочнение), трещина теряет свой кристаллографический характер и образует ряд сложных разветвлений (в результате усиления развития субструктур); путь трещины в основном определяется уже направлением глав ных растягивающих напряжений. Аналогичное изменение харак тера развития трещины наблюдал Вуд [14] в меди и латуни в результате возрастания амплитуды деформации. Схемы обоих изменений показаны на рис. 21.
Представления о континууме
Хотя это и не входит в задачи настоящей работы, необходимо
рассмотреть тот вклад в рассматриваемую проблему, который |
||
вносят представления о континууме, |
особенно — для роста тре |
|
щин. На поверхностях |
усталостного |
разрушения многократно |
наблюдались регулярно |
расположенные бороздки — следы про |
движения трещин [27, 88—90], причем эти следы образуются в фазе с циклом нагружения. Это дает веское подтверждение воз можности описания развития трещины с точки зрения механики континуума. И действительно, наблюдение за процессом уста лости на образцах из пластилина четко показывает, что микроструктурный и кристаллографический аспекты усталости не всег да адэкватны. В действительности можно найти много общего между поведением металла и пластилина. В кристаллическом материале, даже если зарождение трещин и происходит в ре зультате скольжения, трещины могут развиваться на достаточную глубину, так что вполне допустимо представление о континууме, хорошо оправдывающееся для пластилина; такой способ интер претации допустим вплоть до момента разрушения образца. В настоящее время на основе представлений о континууме раз работан ряд механизмов прерывистого скольжения развития трещин; их экспериментальная проверка была вполне успешной.
Замечательное подтверждение плодотворности идей континуума дал в своих опытах Коффин [82]. Показано, что для мно гих поликристаллических металлов, подвергаемых нагружению по схеме растяжение — сжатие с постоянной амплитудой пласти ческой деформации, справедлива зависимость;
N = KAep- v*,
где N — число циклов полностью обратимей деформации до раз рушения;
К — постоянная; Дер — постоянная величина пластической деформации за цикл.
Типичные результаты представлены ца рцс. 27 Я логарифми ческих координатах [82]; здесь разрушающая деформация при «статическом растяжении отнесена к N *= lU. Весьма замечатель но практически полное совпадение результатов длЯ материалов со столь сильно различными энергиями дефектов упаковки, та ких, как алюминий и нержавеющая сталь. Было предложено
Рис. 27. Диаграммы усталости согласно представлениям Коффина [821.
1 — алюминиевый сплав (24S-T); 2 — алюминий (2S); 3 — нержавеющая сталь типа 347
-большое число теоретических обоснований этого факта [24, 35, 1]. Однако рациональное объяснение, вероятно, должно быть осно вано на том что уже на ранних стадиях развития пластической деформации ее распределение столь грубо по сравнению с атом ными процессами скольжения, что частные усталостные харак теристики отдельных кристаллов не играют роли и выводы, по лученные на пластилине, оказываются вполне приемлемыми для определения величины развития трещины за каждый цикл за данной макроскопической деформации.
Коэффициент наклона кривой усталости—7г с уменьшением энергии-дефектов упаковки и при наличии соответствующих по верхностных пленок может приблизиться к нулю в монокристал лах и, возможно, даже в крупнозернистых поликристаллах. Од нако это имеет меньшее значение для практики, чем данные, при веденные на рис. 27. Основным и очевидным способом увеличе ния долговечности является уменьшение амплитуды пластиче ской деформации, которое может быть осуществлено различны ми способами, включая повышение резкого предела текучести,
186
«если это может быть достигнуто [59, 45]. Контроль, среды и состоя ния поверхности — другой возможный путь снижения скорости роста трещин, который иногда может получить практическое зна чение. Определенные возможности могут быть также найдены в области управления такими важными для зарождения и роста трещин характеристиками материала, как энергия дефектов упа ковки; в условиях малых амплитуд деформации и весьма боль ших долговечностей, где приложимость закона Коффина неясна, можно рассчитывать на этот путь. Как было отмечено выше, ар гументы для всей области усталости (область В на рис. 21) одинаковы. Конечно, возможности управления процессом уста лости на основе выбора и изменения материалов и микрострук туры еще не исчерпаны, однако новые пути не вполне ясны и нет уверенности, что они дадут столь же эффективные результа ты, что и направления, введенные недавно на основе теоретиче ских представлений [11].
Выводы
Различие между процессами зарождения и роста трещин можно считать подтвержденным, хотя оно выявляется и не всег да четко. Зарождение трещин с физической точки зрения являет ся в основном поверхностным процессом и требует наличия свободной или незначительно стесненной для деформации по верхности и приводит к развитию изменений рельефа поверхно сти, создающего более или менее притупленные бороздки, из которых затем развиваются трещины. Зарождение трещин мо жет происходить либо медленно — под действием беспорядочно го скольжения, либо быстро — по механизму прерывистого (од ностороннего) скольжения с участием поперечного скольжения. В экспериментах, проведенных на твердых растворах алюминия в меди, показано, что снижение энергии дефектов упаковки в монокристаллах способствует развитию скольжения по одной системе, без образования барьеров и, таким образом, приводит к медленному образованию статистически распределенных заро дышей трещин. Энергия дефектов упаковки не оказывает влияния на зарождение трещин в крупнозернистых поликристаллических образцах, так как у барьеров наблюдается развитие попе речного скольжения (обеспечивающего функционирование ме ханизма прерывистого скольжения) под действием напряжения, вероятно, без участия термической активации; инкубационный период в поликристаллических сплавах меньше, чем в монокри сталлах, примерно на порядок величины.
Рост трещин зависит от энергии дефектов упаковки. В поли кристаллах сплавов Си — А1 интервал между обычно наблюда емым зарождением трещины и окончательным разрушением об разца возрастает примерно в 40 раз при переходе от чистой меди (у « 40 мдж/м2) к сплаву Си + 7% А1 (у « 2 мдж/м2). Такое
187
различие, видимо, связано с тенденцией к развитию субструктур. При наличии субструктур трещины развиваются по границам субзерен. Если понижается энергия дефектов упаковки и подав ляется развитие субструктур, то пути развития трещин прини мают более заметную кристаллографическую ориентацию, а дей ствие среды становится более сильным. Области, прилегающие к границам зерен и двойников, в поликристаллическом сплаве меди с алюминием являются преимущественными путями про движения трещин, а с повышением энергии дефектов упаковки трещины приближаются к границам зерен.
Вообще говоря, наблюдаемые результаты можно связать с взаимодействием параметров, оказывающих наиболее сильное влияние на процесс усталости: амплитуды деформации, энергии дефектов упаковки и, вероятно, температуры.
В условиях описанных экспериментов обнаружено сходство усталостного упрочнения моно- и поликристаллов. Для объяс нения этого факта было высказано предположение о том, что структурные изменения и в процессе циклического деформирова ния со сравнительно низкими амплитудами оказывают то же действие, что и напряжения трения в решетке, которые опреде ляют упрочнение, но не характер скольжения и изменения рель ефа поверхности, вызывающего образование трещин. Корреля ция между характеристиками упрочнения и механизмами уста лости весьма слабая.
Наконец, универсальность закона Коффина подчеркивает трудности и необходимость дальнейших теоретических разрабо ток для практического приложения. Очевидна важная роль ана лиза процесса усталости с позиций механики континуума.
ЛИТЕРАТУРА
1. G i 1ш a n J. J. Fracture, Wiley, N. Y., and !L., 1959, p. 374 [Гилман Дж. Дж. В сб. «Атомный механизм разрушения», Металлургнздат, 1963, с. 220].
2 . |
S o d e r b e r g C . |
R. Met. |
Rev., |
1956, v. 1, p. |
31. |
|
|
|
||
3. |
The Failure of Metals by |
Fatigue, Melbourne Univ. Press, |
Melbourne. |
|||||||
Australia, 1947. |
|
|
|
|
|
|
|
|
|
|
4. |
Fatigue and Fracture of Metals, Wiley, N. Y., 1952. |
|
|
|
||||||
5. |
Colloquium of Fatigue, Springer—Verlag, Berlin, 1956. |
|
|
|
||||||
6. |
Proc. intern. Conf. Fatigue Metals, IME, L., 1956. |
|
|
|
||||||
7. |
Deformation Flow of Solids |
(Colloquium |
Madrid). |
Springer-Verlag, |
||||||
Berlin, |
1956. |
|
|
|
|
|
|
|
|
|
8. Fatigue in Aircraft Structures, |
Acad. Press, N. Y., 1956. |
|
|
|
||||||
9. Discussion on Work Hardening and Fatigue in Metals, Proc. Roy Soc.. |
||||||||||
1957, v. A242, p. 4 5. |
|
|
|
|
|
|
|
|
||
10. |
Internal |
Stresses and Fatigue |
in Metals, Elsevier, N. Y., 1959. |
|
||||||
11. Fracture, Wiley* N. Y., 1959. [Атомный механизм разрушения Метал- |
||||||||||
лургиздат, 1963, |
с. 438]. |
|
|
|
|
|
|
|
|
|
12. |
T h o m p s o n N. a. W a d s w o r t h |
N. J. Adran. Phys., |
1958, v. |
7 , p. 72. |
||||||
13. |
E w i n g |
J. A. |
a. H ' u m f r e y |
J. W. |
Phil. |
Trans. 1903, v. |
200, |
i). 241. |
|
14. |
W o o d |
W'. A. Fracture, |
Wiley, |
N. Y.t 1959, p. 412. |
[В. А. Ву д . |
В сб. |
||||||||||||||||||||||||||||
«Атомный механизм разрушения». Металлургиздат, 1963, 438]. |
2, |
p. |
149. |
|
|||||||||||||||||||||||||||||||
|
15. |
E w e n |
|
D. |
|
a. R o s e n h a i n |
W. J. |
Inst. (Metals, |
1912, |
v. |
Wi |
||||||||||||||||||||||||
|
16. |
M o t t |
N. |
|
F. Dislocations |
and |
Mechanical |
Properties |
of |
Crystals, |
|||||||||||||||||||||||||
ley, N. |
Y., 1957, |
p. |
472. |
|
|
|
|
|
|
|
|
|
|
|
|
|
|
|
|
|
|
|
|
|
|
|
|
|
|
|
|||||
|
17. |
S e i t z |
|
F. |
Advan. |
Phys., |
1952, |
v. |
1, |
|
p. |
43. |
|
|
|
|
|
|
|
|
|
|
|
|
|
||||||||||
|
18. M a s o n |
W. P. Deformation |
and Flow |
of |
Solids (Colloquium |
Madrid), |
|||||||||||||||||||||||||||||
Spri-nger-Verlag, Berlin, 1956, p. |
314. |
|
|
|
|
|
|
|
|
|
|
|
|
|
|
|
|
|
|
|
|
||||||||||||||
v. |
19. |
F o r s y t h , |
|
P. |
|
J. |
-E. |
a. |
|
S t u b b i n g t o n |
C. |
A. |
Inst. |
|
Metals, |
|
1957, |
||||||||||||||||||
85, p. 339. |
|
|
|
|
|
|
|
|
|
|
|
|
|
|
|
|
|
|
|
|
|
|
|
|
|
|
|
|
|
|
|
|
|
||
|
20. |
F e 11 h a m |
P. Phil. Mag., |
1961, v. |
6, p. |
1479. |
|
p. |
79. |
|
|
|
|
|
|
|
|
||||||||||||||||||
|
21. |
O r o w a n |
|
E. Proc. Roy. Soc., |
L., |
1939, |
v. |
171, |
|
|
|
|
|
|
|
|
|||||||||||||||||||
|
22. H e a d |
|
A. K. J. Mech. Phys. |
Soluds, |
|
1953, |
v. |
1, |
p. |
|
134. |
|
6, |
p. |
565. |
||||||||||||||||||||
|
23. |
F u j i t a |
F. |
E. |
Sci. Rep. |
Inst., |
Tohuku Univ., A, 1954, v. |
|
|||||||||||||||||||||||||||
|
24. |
H o l d e n |
|
J. Phil. Mag., |
1961, |
v. 6, p. 547. |
|
|
|
|
|
|
|
|
|
|
|
|
|
||||||||||||||||
p. |
25. |
M a ch i in |
|
E. |
|
S. |
Fracturing |
of Metals, |
ASM, |
Cleveland, |
Ohio, |
1948, |
|||||||||||||||||||||||
282. |
|
|
|
|
|
|
|
|
|
|
|
|
|
|
|
|
|
|
|
|
|
|
|
|
|
|
|
|
|
|
|
|
|
|
|
|
26. |
F r o s t |
-N. E. Proc. ЧМЕ, |
1959, |
v. 1, p. 151. |
1959, |
p. |
524. |
[III. Крюссар |
||||||||||||||||||||||||||
|
27. |
C ' r u s s a r d |
C. a. o. Fracture, |
Wiley, |
-N1. Y., |
||||||||||||||||||||||||||||||
и др. В сб. «Атомный механизм разрушения». Металлургиздат, |
1963, с. |
535]. |
|||||||||||||||||||||||||||||||||
|
28. |
T h o m p s o n |
N. а. о. Phil. Mag., |
1956, |
v. |
1, |
р. ИЗ. |
|
|
|
|
|
|
|
|
||||||||||||||||||||
|
29. |
F o r s y t h |
Р. J. iE. Nature, 1953, |
v. |
171, р. |
172. |
|
181. |
|
|
|
|
|
|
|
||||||||||||||||||||
|
30. |
F o r s y t h |
Р. |
J1. IE. J. Inst. Metals, |
1951, |
v. 80, |
p. |
|
|
|
p. 352. |
|
|||||||||||||||||||||||
|
31. |
A l d e n |
T. H. |
a. B a c k o f e n |
W. |
A. ActaMet., 1961, |
v. 9, |
510. |
|||||||||||||||||||||||||||
|
32. |
iE b n e г M. 1. |
а. В a |
с k о f e n W. A. Trans.AIME,1959, |
|
v. |
215, |
p. |
|||||||||||||||||||||||||||
|
33. |
B a c k o f e n |
W7. A. |
Fracture, N. Y., |
|
1959, |
v. |
435. |
[В. А. |
Б э к о ф е н. |
|||||||||||||||||||||||||
В сб. «Атомный механизм разрушения». Металлургиздат, 1963, с. 438]. |
|
|
|||||||||||||||||||||||||||||||||
|
34. |
M a y |
А. |
N. Nature, |
|
1960, |
v. |
185, р. |
|
303. |
|
|
|
|
|
|
|
|
|
|
|
|
|
|
|||||||||||
|
35. |
M a y |
А. |
N. Nature, |
|
1960, |
v. |
188, р. |
|
573. |
|
|
Inst. Metals, |
|
1958, v. 87, |
||||||||||||||||||||
p. |
36. |
F a g r e d o D . |
|
М. |
a. G r e e n о u g h |
|
G. В. J. |
|
|||||||||||||||||||||||||||
1. |
A l d e n |
T. H. Acta |
Met., |
1962, |
v. |
10, |
p. |
653. |
|
|
|
|
|
|
|
|
|
|
|
|
|||||||||||||||
|
37. |
|
|
|
N. Y., |
1959, |
p. |
450. |
|||||||||||||||||||||||||||
|
38. |
M e E v i l |
у A. J. a. |
Machlin |
E. S. Fracture, |
Wiley, |
|||||||||||||||||||||||||||||
[А. Дж. М а к |
И в л и |
|
мл. и |
Е. С. Мэ ч л и н . |
В |
сб. «Атомный |
механизм |
раз |
|||||||||||||||||||||||||||
рушения». Металлургиздат, 1963, с. 455]. |
|
|
|
|
|
С. A. |
J. |
|
Inst. |
|
Metals, |
|
1954, |
||||||||||||||||||||||
|
30. |
F o r s y t h |
|
Р. |
J. |
Е. |
a. |
S t u b b i n g t o n |
|
|
|
||||||||||||||||||||||||
v. |
83, р. 395. |
|
D. Н. а. о. Acta |
Met., |
1961, v. 9, р. 892. |
|
|
|
|
|
|
|
|
|
|
||||||||||||||||||||
|
40. |
A v e r y |
|
|
|
|
|
|
|
|
|
|
|||||||||||||||||||||||
|
41. |
M o t t |
|
N. |
|
F. |
Acta Met., |
1958, |
v. 6, p. 195. |
|
|
|
|
|
|
|
|
|
|
|
|
|
|||||||||||||
|
42. |
K e n n e d y |
A. J. |
Phil. Mag., |
1961, v. 6, p. 49. |
|
A., |
|
1957, |
v. |
242, |
||||||||||||||||||||||||
|
43. |
C o t t r e l l |
|
A. |
|
H. |
a. |
H u l l |
D. |
Proc. |
|
Roy. Soc., L., |
|
||||||||||||||||||||||
p. |
2 1 1 . |
T h o m p s o n |
N. Fracture, Wiley, |
N. Y., |
1959, |
p. |
354. [H. Т о м п с о н . |
||||||||||||||||||||||||||||
|
44. |
||||||||||||||||||||||||||||||||||
В сб. «Атомный механизм разрушения». Металлургиздат, 1963, с. 354]. |
|
||||||||||||||||||||||||||||||||||
|
45. |
S h i h |
С. |
|
Н. а. о. Trans. ASM, Quart., |
1956, |
v. 48, |
p. 86. |
|
|
|
|
|
||||||||||||||||||||||
|
46. |
N a g a i |
R. J. |
Phys. |
Soc., |
Japan, |
1959, |
v. |
114, |
p. |
1252. |
p. |
447. |
|
|
||||||||||||||||||||
|
4 7 . A r g o n |
A. |
S., |
a. |
E. O r o w a n , |
Nature, |
1961, |
v. |
|
192, |
|
|
|||||||||||||||||||||||
|
48. |
S’ e e g e r |
|
A. |
Dislocations |
and |
Mechanical |
|
Properties |
|
of |
|
Crystals, |
||||||||||||||||||||||
Wiley, |
N. Y., 1956, p. 243. |
|
|
|
|
S. M. Mass. Inst. Technol., |
Cambridge, |
Mass., |
|||||||||||||||||||||||||||
|
49. M i 11 |
e г G. A., |
T h e s i s |
||||||||||||||||||||||||||||||||
1961. |
D i e h l |
J. |
u. a. Z. Metallkunde, 1955, |
Bd. 46, _S. 650. |
|
|
|
|
|
|
|
||||||||||||||||||||||||
|
50. |
|
|
|
|
|
|
|
|||||||||||||||||||||||||||
|
51. |
K e l l y |
A. Phil. Mag., |
1956, |
v. |
1, |
p. |
|
835. |
|
|
A., |
1959, |
v.251, |
|
p. |
186. |
||||||||||||||||||
|
52. |
H a m R.K. a. B r o o m T . |
Proc. IRoy. Soc., L., |
|
|||||||||||||||||||||||||||||||
|
5 3 . |
H a m |
R. |
|
K. a. B r o o m |
T. Phil. Mag., |
1962, |
v. 7, p. |
95. |
|
|
|
|
|
|
|
|||||||||||||||||||
|
54. |
S u z u k i |
|
|
H., |
Sci |
'Rep. |
Res. |
Inst., |
|
Tohoku |
Univ., 1952, |
|
v.4, |
p. |
455. |
|||||||||||||||||||
|
55. |
W h e l a n |
|
M. J. Proc. Roy. Soc. L., |
|
1959, |
v. 249, |
p. |
114. |
|
|
|
|
|
|||||||||||||||||||||
|
56. |
S w a n n |
P. R. |
Thesis |
|
Ph. D. |
Univ. |
|
Cambridge, |
1960. |
|
|
|
|
|
|
|
||||||||||||||||||
|
57 |
A v e r y |
D. H. |
a. o. Trans. AIME, |
1958, |
v. 212, |
p. |
256. |
|
|
|
|
|
|
|