
книги / Разрушение твердых тел
..pdf58. |
H e a r m o n |
R. F. S. Rev. Mod. Phys., 1946, v. 18, p. 409. |
|
|
|
||||||||||||||||||
59. |
(L i p s i 11 H. |
A. a. W a n g |
D. Y. Trans. AIME, |
1961, v. 221, p. 918. |
|||||||||||||||||||
60. |
W o l f |
H!. Z. |
Naturforsch., |
1960, |
Bd. |
15, |
S. |
180. |
|
|
|
|
|
|
|
||||||||
61. |
К e m s 1e у D. S. J. Inst. Metals, |
1956, |
v. 85, p. 420. |
|
189. |
|
|
|
|||||||||||||||
62. |
S m i t h |
G. C. Proc. !Roy. Soc., |
<L., A, |
1957, |
v. 242, p. |
|
M. P; |
||||||||||||||||
63. |
H e m p e l |
M. -R. Fracture, |
Wiley, |
N. Y., 1959, |
p. 376. |
[ Х е м п е л |
|||||||||||||||||
В сб. «Атомный механизм разрушения». Металлургиздат, 1963, с. 376]. |
|
||||||||||||||||||||||
64. |
H u l l 'D. J. |
Inst. Metals, |
1957, v. 86, |
p. |
425. |
|
|
|
|
|
|
|
|
||||||||||
65. |
S t u b b i n g t о n |
C. A., |
F o r s y t h |
P. J. |
E. |
J. |
Inst. |
Metals, |
|
1957* |
|||||||||||||
v. 86, |
p. 90. |
|
|
|
|
|
|
|
|
|
|
|
|
|
|
|
|
|
|
|
|
|
|
66. |
P a r k e r |
E. |
a. |
o. |
Internal |
Stresses |
and |
Fatigue |
in |
|
Metals, |
Elsevier* |
|||||||||||
N. Y., |
1958, p. 263. |
|
|
|
|
|
|
|
|
|
|
|
|
|
|
|
|
|
|
|
|
||
67. |
C 1a r e b г о u g h L. M. a. o. Proc. !Roy. Soc. L., A,1957, v. 242, |
p. 160. |
|||||||||||||||||||||
68. H a m iR. K., |
B r o o m |
T. Proc. Roy. |
Soc., |
L. |
1957, |
v. 242, p. |
|
166. |
|||||||||||||||
69. |
S e g a 11 |
R. 'L. a. |
o. Phil. Mag., |
1961, |
v. |
6, |
p. |
1493. |
1960, v. 8, |
p. |
453. |
||||||||||||
70. |
K e rn s le y D. S. |
a. P a t e r s o n |
M. S. Acta |
Met., |
|||||||||||||||||||
71. |
H i r s c h |
P. |
B. |
a. |
o. |
Phil. Mag., |
1959, |
v. |
4, p. 721. |
|
|
v. 4, p. |
912. |
||||||||||
72. |
S e g a 11 |
R. |
L. |
a. |
P a r t r i d g e |
P. G. |
Phil. Mag., |
1959, |
|||||||||||||||
73. |
W i l s o n |
R. |
N. |
a. |
F o r s y t h |
P. J. E. |
J. |
Inst. |
Metals, |
1959, |
|
v. |
87* |
p.336.
74.G г о s s к r e u t z J. C. Proc. Intern. Congr. Electron Microscopy, 5th* Acad. Press, N. Y., 1962.
p. |
75. |
F o r s y t h |
P. |
J. |
|
E., |
a. |
S t u b b i n g t o n |
C. |
A. |
Acta Met., |
1960. |
v. 8* |
|||||||||||
811. |
F o r s y t h |
P. J. |
|
E. Proc. Intern. Conf. Fatigue |
Metals. |
IME, |
L., |
1956* |
||||||||||||||||
p. |
76. |
|
||||||||||||||||||||||
535. |
|
|
|
|
|
|
|
|
|
|
|
|
|
|
|
|
|
|
|
|
|
|
|
|
|
77. |
G r o s s k r e u t z |
|
J. C. J. Appl. Phys., 1962, |
v. |
33, |
p. |
1787. |
p. |
13. |
||||||||||||||
|
78. |
C h i n G. Y., а. В а с к о f e n W. A. J. |
Inst. Metals, |
1961, |
v. 90, |
|||||||||||||||||||
p. |
79. |
W о о d |
W. A. |
a. |
S e g a 11 R. L. Proc. iRoy. |
Soc., |
L., A, |
1957, v. |
242. |
|||||||||||||||
180. |
G o u g h |
H. J. |
a. W o o d |
W. A. J. |
Roy. Aeronaut. |
Soc., |
1936, |
v. |
40* |
|||||||||||||||
p. |
80. |
|||||||||||||||||||||||
586. |
|
|
|
|
|
|
|
|
|
|
|
|
|
|
|
|
|
|
|
|
|
|
|
|
|
81. |
B a r r e t t |
C. |
S. |
|
Metallurgia, |
1937, |
v. |
15, p. |
165. |
|
Elsevier, |
N. Y.. |
|||||||||||
|
82. |
С о f f i n E. F. Internal Stresses and |
Fatigue |
in Metals, |
||||||||||||||||||||
1959, p. |
363. |
|
|
|
F. A., |
Proc. |
Intern. |
Conf. Fatigue |
Metals, |
Inct. Mech. |
||||||||||||||
|
83. |
M c C l i n t o c k |
||||||||||||||||||||||
Engrs., |
L., |
1956, |
p. |
538. |
|
|
|
|
|
Univ. Chicago, |
Press, |
Chicago, |
ITT., |
1960. |
||||||||||
p. |
84. |
A |
History |
of Metallography, |
||||||||||||||||||||
125. |
S w a n n |
P. iR. |
a. N u t t i n g |
J. J. |
Inst. |
Metals, |
1961, |
v. |
90, |
p. |
133. |
|||||||||||||
|
85. |
|||||||||||||||||||||||
|
86. W a d s w o r t h |
|
N., |
a. |
H u t c h i n g s |
J. Phil. Mag., |
1958, |
v. 3, |
p. |
1154. |
||||||||||||||
|
87. |
S h a n l e y |
F. |
R. |
Colloquium |
on Fatigue, |
Springer-Verlag, |
Berlin* |
||||||||||||||||
1956, S. |
251. |
C. |
a. S m i t h |
G. |
C. Phil. Mag., |
1962, v. 7, p. |
847. |
|
|
|
|
|||||||||||||
|
88. |
L a i r d |
|
p. |
117. |
|||||||||||||||||||
|
89. |
F o r s y t h |
P. J. |
E., a. o. -Ryder D. A. Metallurgia, |
1961, |
v. 63, |
||||||||||||||||||
p. |
90. |
F o r s y t h |
P. J. E. a. o. J. 'Inst. Metals, |
Techn. |
Note 47, 1962, |
v. |
90- |
|||||||||||||||||
238. |
|
|
|
|
|
|
|
|
|
|
|
|
|
|
|
|
|
|
|
|
|
|
|
СВЯЗЬ УСТАЛОСТИ С МИКРОСТРУКТУРОЙ
ВВЕДЕНИЕ
Большая часть наших сведений о механизме процесса уста лости получена при изучении сравнительно простых структур, таких как монокристаллы. Технические материалы, конечно, зна чительно более сложны по своему строению и содержат дисперс ные частицы включений, вторые фазы, границы; поэтому весьма важен вопрос о влиянии всех этих осложняющих факторов на процесс усталости. В данном обзоре рассматриваются различ ные случаи, когда микроструктура в действительности оказыва ет сильное влияние на ту стадию процесса усталости, на которой происходит зарождение трещин у границ двойников в дисперси онно твердеющих сплавах алюминия.
ДИСПЕРСИОННО ТВЕРДЕЮЩИЕ АЛЮМИНИЕВЫЕ СПЛАВЫ
Известно, что сопротивление усталости дисперсионно твер деющих алюминиевых сплавов сравнительно низко. Например, отношение ограниченного предела усталости на базе 107 циклов- к пределу прочности у высокопрочных алюминиевых сплавов составляет всего около 0,3, тогда как у сталей оно близко к 0,5. Такое поведение определяется тремя основными структурными факторами: 1) присутствием включений интерметаллических соединений; 2) существованием обедненных зон, 3) нестабиль ностью выделений. Ниже будет рассмотрен каждый из этих фак торов.
Включения интерметаллических соединений
Промышленные высокопрочные сплавы алюминия содержат большое количество частиц твердых интерметаллических фаз. Состав этих частиц весьма сложен, но их число и размеры силь но зависят от содержания в сплаве железа и кремния. Эти ча стицы могут ухудшать свойства сплава, так как для образова ния трещин достаточна весьма небольшая пластическая дефор мация12. Частицы способствуют образованию пустот при одноос ной деформации и поэтому снижают пластичность сплавов. Однако с точки зрения усталостных свойств более важно, что в этих частицах могут возникать трещины на стадии механиче ской обработки в процессе придания материалу окончательной
1 A. J. Me Evily, R С. Boettner.
2 По данным Глассмана.
19L
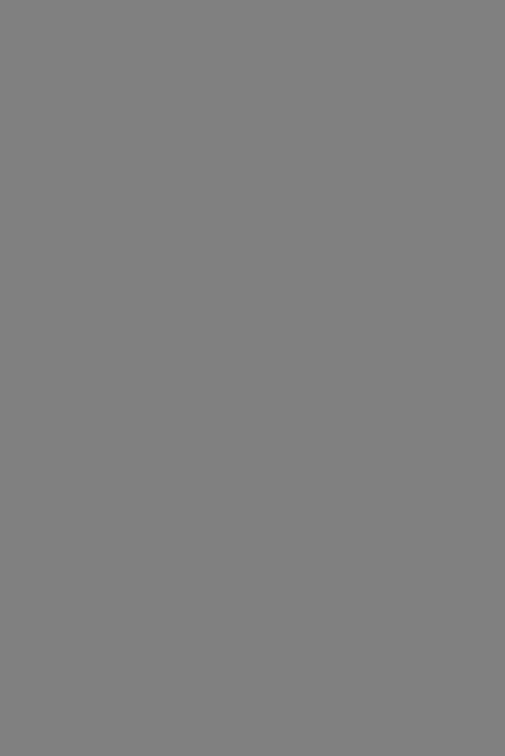
ний. Эти напряжения в свою очередь вызывают зарождение интеркристаллитных трещин при циклическом нагружении '. При мер влияния циклического нагружения на сплав, в структуре которого имеются обедненные зоны, показан на рис. 2. Образец был изготовлен из сплава А1 + 10% (по массе) Mg, подвергнуто го старению после закалки на твердый раствор при 200° С, 20 ч. Темные области вдоль границы зерен, показанные стрелками,— трещины. Такие трещины могут привести в конце концов к раз рушению, так как установлено, что его источник находится в интеркристаллитных областях.
Было показано, что после деформации с обжатием 50% до старения природа усталостного разрушения значительно меня ется. Как показано на рис. 2, б, присутствуют классические экс трузии и полосы скольжения, которые оказываются местами за рождения транскристаллитного разрушения. Холодная дефор мация уменьшает влияние обедненных зон из-за возникновения Других участков для зарождения трещин и из-за образования крупных порогов по границам зерен, которые препятствуют ре лаксации напряжений.
Нестабильность дисперсных выделений
Даже если в сплавах алюминия и нет частиц интерметаллидных включений, имеющих трещины, или обедненных зон, их ус талостная прочность сравнительно низка. Было высказано пред положение [1], что это связано с нестабильностью дисперсных выделений при циклическом нагружении в результате перестаривания или возврата. Были получены дополнительные данные, которые подтверждают мысль о том, что возврат может действи тельно иметь место. В данной работе образцы из промышленно го сплава А1 — Си — Mg — Mn (2024-Т4) подвергали цикличе скому нагружению длительностью 10% (от полной долговечно сти) при напряжении 171,5 Мн/м2 (17,5 кГ/мм2), затем выдер живали 16 ч при 150° С и снова подвергали циклическому на гружению до разрушения.
Средняя долговечность образцов этой группы примерно вдвое выше, чем образцов, не подвергавшихся указанной проме жуточной обработке. Это означает, что термическая обработка не только залечивает повреждения, но также и повышает меха нические свойства сплава. Указанные результаты показывают, что возврат происходит на ранних стадиях циклического нагру жения, так как если перестаривание приводит к снижению со противления усталости, то указанная обработка при повышен ных температурах (выдержка 16 ч при 150° С) должна была бы повлечь за собой дальнейшее перестаривание материала и пото-
1 По данным А. Дж. Мак-Эвили и др.
13 Зак. 351
му должна была бы привести к снижению, а не к повышению долговечности, которое в действительности наблюдалось.
В развитие идей Келли и Файна [2] было высказано предпо ложение о том, что механизм возврата связан с движением ди слокаций через когерентные зоны или полукогерентные частицы выделений. Возвратно-поступательное движение дислокаций че рез эти зоны при циклическом нагружении приводит к их раз дроблению до блоков субкритических размеров, и тогда выделе ния вновь -переходят в твердый раствор, либо распределяются по сетке дислокаций. При этом полосы скольжения будут разупроч-
няться, |
что определяет |
возможность развития сдвигов. |
Это |
||
в свою |
очередь приводит к возникновению |
бороздок |
и в ряде |
||
случаев — к зарождению |
трещин. Процесс |
возврата |
может |
за |
нимать значительную долю долговечности образца, в результате чего в сплавах зарождение трещин происходит позже, чем в чи стых монокристаллах.
Выводы
Из трех рассмотренных эффектов самым главным является нестабильность дисперсных выделений, определяющая низкую усталостную прочность высокопрочных алюминиевых сплавов. Повышение усталостной прочности, которое может быть достиг нуто путем устранения частиц включений, содержащих трещи ны, или обедненных зон будет невелико, пока дисперсные части цы нестабильны под действием циклической нагрузки. Однако если дисперсные частицы удастся стабилизировать, целесообраз но будет устранять и растрескивание частиц включений и обед нение зон, чтобы достичь максимального сопротивления уста лости.
ГРАНИЦЫ ДВОЙНИКОВ
Известно, что границы двойников являются предпочтитель ными местами зарождения усталостных трещин. Недавно было проведено исследование влияния приведенного касательного на пряжения и ориентации направления скольжения в крупнозер нистых медных образцах. В этом материале очень много двой ников отжига, границы которых располагаются вдоль плоско
стей {111}.
Если касательные напряжения по плоскостям, параллельным этим границам, не максимальны, то трещины по ним не зарож даются. Вместо этого трещины развиваются по бороздкам полос скольжения внутри зерен. Вид таких полос скольжения показан на рис. 3, а.
Если по плоскостям, параллельным границам двойников, действуют максимальные касательные напряжения, а направле ние скольжения составляет с поверхностью значительный угол,
1 9 4
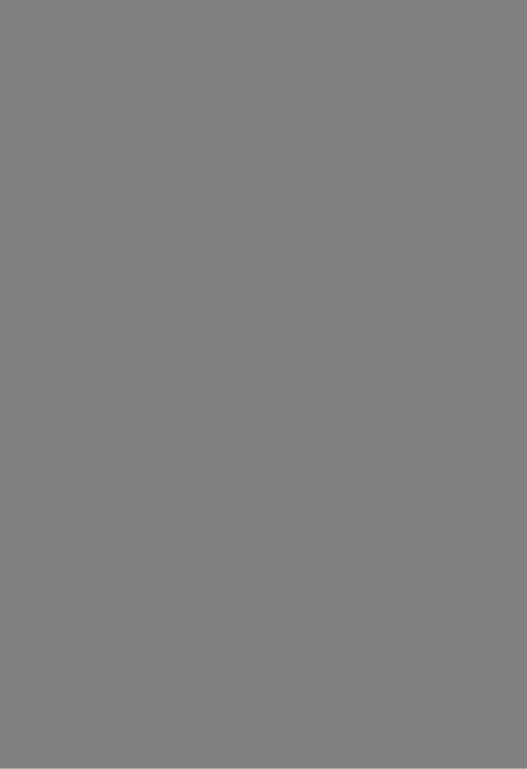
рядочного возвратно-поступательного движения дислокаций по близким плоскостям скольжения. Мы полагаем, что этот меха низм обязательно должен быть связан с условием легкого попе речного скольжения^ так как в материалах типа каменной соли, в которых поперечное скольжение затруднено, бороздки по по лосам скольжения не развиваются и усталостное разрушение отсутствует [4].
Роль легкого поперечного скольжения может заключаться в том, чтобы дать возможность сегментам краевых дислокаций, находящимся в плоскостях поперечного скольжения, легко пере мещаться внутрь кристалла, или к его поверхности и не мешать движению последующих дислокаций.
В третьем случае по плоскостям, параллельным двойнико вым границам, действуют максимальные напряжения, но на правление скольжения образует с поверхностью весьма малый угол. В монокристаллах в этом случае усталостные трещины не должны зарождаться [5]. Однако, как показано на рис. 3, в, по границам происходит чрезвычайно значительное смещение ма териала, приводящее к образованию трещин. Наблюдалось, что деформация данного типа наиболее развита у некогерентных ступенек вдоль границ двойников и что в этих местах активны также сопряженные системы скольжения. Вероятно, этот эф фект связан и со скольжением, параллельным границам, и со скольжением по сопряженным плоскостям скольжения.
Важно отметить, что ни в одном случае перемещения мате риала из поверхностных областей кристалла пустоты вблизи поверхности не развиваются. Кроме того, процесс образования интрузий весьма ограничен и не связан с перемещением мате риала с поверхности.
Эти наблюдения показывают, что либо плотность материала
вблизи полос скольжения, |
содержащих |
бороздки, снижается |
|
в результате присутствия |
большого числа |
дислокаций |
под по |
верхностью, либо материал перемещается |
и замещает |
объемы |
|
экструзий весьма сложным образом. |
|
|
ЗАКЛЮЧЕНИЕ
Приведенные выше примеры подтверждают большое значе ние особенностей микроструктуры в процессе зарождения уста лостных трещин. С расширением наших знаний о связи микро структуры со свойствами станет более ясно, какого повышения усталостной прочности можно ожидать.
Уже сейчас очевидно, что с повышением стабильности дисперсных частиц, определяющих прочность алюминиевых спла вов и препятствующих процессу поперечного скольжения, воз растает сопротивление материала зарождению усталостных трещин.
196
1. |
В г о о m Т. |
а. о. J. |
Inst. Met., |
1956, v. 84, p. 957. |
|
|
|
|
2. |
K e l l y A. |
a. F i n e |
M. Acta |
Met., 1957, v. 5, p. |
365. |
|
|
|
3. |
M a y A. N. |
Nature, 1960, v. 185, p. 303. |
|
|
|
|
||
4. |
M с E v i 1 у |
A. J. a. M a c h’l i n E. S. Fracture, |
Wiley, N. Y., |
and |
L., |
|||
1959, p. 450. [ Ма к |
И в л и А. Дж. мл., М э ч л и н Е. С. В |
сб. «Атомный меха |
||||||
низм разрушения». Металлургиздат, 1963, с. 455]. |
|
1959, v. 215, |
р. |
510. |
||||
5. |
Е b п е г М. L. a. B a c k o f e n |
W. A. Trans. АГМ'Е, |
Б. АТОМНЫЕ МЕХАНИЗМЫ
Д Ж . М И К И Н , Н . П Е Т Ч 1
АТОМНЫЕ АСПЕКТЫ РАЗРУШЕНИЯ
ХРУПКОЕ РАЗРУШЕНИЕ
В последние двадцать лет проблема хрупкого разрушения привлекает самое пристальное внимание исследователей в связи с изучением механизма разрушения. Это наиболее важная проб лема металловедения и хотя в наших знаниях все еще имеются определенные пробелы, однако можно с доверием относиться к общему направлению идей об атомном механизме разру шения.
Вконечном счете, следует полагать, что некоторый дислока ционный процесс может создать такие напряжения, которые вместо скольжения вызовут отделение одних атомов от других. Образуется трещина. Тогда возникает вопрос, будет ли эта тре щина распространяться катастрофически через кристалл как тре щина скола. Если это возможно, то происходит хрупкое разру шение.
Вточных расчетах условий, при которых разрушение будет иметь хрупкий, а не вязкий характер i[l—3], использовали не сколько особую модель образования трещины в результате слия ния дислокаций в плоских скоплениях, образовавшихся у границ зерен, или в результате слияния дислокаций, движущихся в пе
ресекающихся плоскостях.
Однако, для наших целей в данной работе мы используем простой приближенный расчет, в котором намеренно не затра гиваются отдельные детали процесса. Оценка этих деталей в об щей форме показала, что они не слишком существенны.
Предположим, что трещина раскрывается под действием растягивающего напряжения а/ у конца полосы скольжения или двойника длиной I (I приблизительно соответствует диаметру зерна), а напряжение трения решетки при продвижении дисло кации через кристалл, равно о0.
Образование полосы скольжения (или двойника) вызывает
превращение упругой деформации в пластическую |
в области |
шириной ~ / , расположенной на полосе скольжения |
(рис. 1). |
1 J. D. Meakin, N. J. Petch.
В этом случае упругая деформация является результатом раз ности напряжений (а/ — а0), которая создает пластический сдвиг в полосе скольжения, равный l(a f — о0)/2ц, где ц — мо дуль сдвига, а коэффициент 2 связан с переходом от растяги вающего к касательному напряжению. Следовательно, полоса скольжения (или двойник длиной i), в которой действует напря жение Of (в то время как напряжение, достаточное для движе ния изолированной дислокации равно лишь о0), эквивалентна дислокации мощностью /(о/ — сто)/2ц по каждому концу полосы, и ата дислокация будет каким-либо образом продвигаться по полосе скольжения (или двойнику) способом, зависящим от осо бенностей строения полосы.
Образование трещины соответствует |
в |
|
|
||||||
раскрытию этой дислокации. Если при- |
|
|
|||||||
/ |
|
/ |
|||||||
няТъ |
что доля энергии дислокации а 2 |
|
|||||||
переходит в поверхностную |
энергию |
/ |
|
/ |
|||||
трещины, то |
|
|
|
|
|
х/ |
2 |
/ |
|
|
|
|
|
|
|
|
/ |
|
|
|
а2 |
12 = 2ус, |
( 1) |
/ |
/ |
/ |
|||
|
|
8ц |
|
|
|
|
/ |
|
|
где |
с — глубина |
созданной |
клиновой |
* |
! |
|
|||
|
|
||||||||
|
трещины; |
поверхностная |
|
В |
|
||||
|
у — эффективная |
Рис. 1. Скольжение |
вдоль |
||||||
|
энергия |
этой |
трещины |
(если |
плоскости |
XY, снимающее |
|||
|
рассматривать |
ее |
на |
единицу |
упругую |
деформацию в об |
|||
|
ласти A B C D и образующее |
||||||||
|
длины |
трещины |
и |
дислока |
ступеньку |
пластического |
|||
|
ции). |
|
|
|
|
|
скольжения |
|
Если происходит хрупкое разруше ние, то эта трещина должна развиваться как трещина скола. За
метим, что для продвижения трещины должна действовать пол ная величина приложенного напряжения а/, в то время как для дислокационного процесса зарождения трещины должно быть приложено Оо до того, и<ак начнется какое-либо перемещение дис
локации, так |
что для зарождения трещины имеется только |
(о/— 0°). |
. г ,, |
Если применить критерии 1 риффитса и считать, что для об |
разования и развития трещины требуется одна и та же поверх
ностная энергия1, то условие |
хрупкого |
разрушения с учетом |
|
уравнения (1) окажется следующим: |
|
|
|
НУ \ 7 2 |
_ |
4ну |
|
° / = |
о |
( o r — |
(Jn) l ~ |
Если разрушение происходит при напряжении, равном пре
делу текучести, или при деформации, которая не зависит от раз- |
|
1 В самом начале зарождения трещины у имеет двоякое значение; |
если |
эта величина сохраняет это значение, то зародившаяся трещина всегда |
будет |
развиваться. |
1QQ |
|