
книги / Технология строительной керамики
..pdfжание оксидов железа, а в промытом песке — в 2 раза. Остающийся Fea0 3 (неподдающийся магнитной сепарации) представлен магнитными минералами (биотит, мусковит и др.), вросшими в виде прослоек в каолинит, полевой шпат или кварц, а также изоморфными примесями Fe к шпату. Для полного удаления железосодержащих минералов необходима напряженность магнитного поля 1433—1592 кА/м.
Для магнитной сепарации суспензий и шликера используют фер ромагнитные сепараторы 0600-5, СМ-488, ФОЛ-5, магнитные плиты
Твердые компоненты
Рис. 82. Схема непрерывного приготовления шликерных масс:
1 — сушильный барабан; 2 —• вальца; 8 струйная мельница; 4 — дозировочные
весы; |
5 стругач; |
б фрезерно-метательная (роторная) мельница; 7 насос; |
8 * - сито. |
|
|
ЭП-2ГГ |
и ЭП-31Г, |
Производительность сепаратора— 4—6 м3/ч при |
влажности шликера 32% и до 5,5 м8/ч при влажности 60—65%. По требляемая мощность 0,5—0,8 кВт. Хорошую очистку обеспечивают постоянные ферро-бариевые магниты, имеющие кольцевую форму диа метром 86,7 мм с напряженностью магнитного поля 275—300 эрстед.
Магниты укладывают на расстоянии 20 мм один от другого вдва ряда в углубления деревянного лотка, по которому протекает суспензия.
При получении сырьевых материалов в предварительно измель ченном виде с использованием оборудования непрерывного действия технологическая схема приготовления шликерных масс значительно упрощается (рис. 82).
Глина, каолин, бентонит разжижаются во фрезерно-метательной ро торной мельнице. Плотность суспензии контролируется и стабили зируется автоматическим плотномером РПСМ.
Каменистые материалы измельчаются до зерна размером 50—60 мкм в струйных мельницах. Для дозирования компонентов используются автоматические весы ДП0150-500, а также объемные дозаторы для суспензий и воды.
О б е зв о ж и в а н и е в р а с п ы л и т е л ь н ы х с у ш и л к а х . О б е з в о ж и в а
н и е с у с п е н з и й является трудоемким процессом. В настоящее время для обезвоживания широко используют распылительные сушил ки, позволившие сократить количество производственных операций по подготовке пресс-порошка с 10 до 3, а время приготовления порошка с 8— 12 ч до 2—3 мин. По конструктивным особенностям распыливаю-
щих устройств сушилки разделяют на три типа: с центробежным диском, струйно-распылительные (соплами) и «фонтанные».
Рис. 83. Схема распыли тельной сушилки (Минс кого КСМ):
/ — корпус; |
2 — форсунка |
подачи шликера; S — взрьш- |
|
ной клапан; 4 |
— топка; 5 — |
батарейный циклон; 6 — вен тилятор; 7 конвейер.
В сушилках первого типа суспензия распыляется быстровращающимся (7— 13 тыс. об/мин) распылительным диском. Теплоноситель {горячий воздух) подается в башню сверху или снизу или обоими способами одновременно. Порошок собирается в нижней конусной •части башни.
Всушилках второго типа суспензия распыляется в верхней части башни гидравлической форсункой, работающей под давлением. Теп лоноситель проходит через сушилку сверху вниз в одном направле нии с высушиваемым материалом.
Всушилках третьего типа суспензия распыляется гидравлической форсункой в нижней части башни, образуя «фонтан». Теплоноситель подается сверху.
По направлению движения теплоносителя и высушиваемого мате риала сушилки бывают прямоточные и противоточные. В противоточных сушилках получают порошки более крупные, чем в прямо точных, и с меньшим содержанием пыли. Наиболее крупнозернистый порошок получают в фонтанных сушилках.
На отечественных заводах используют распылительные сушилки конструкции Минского комбината строительных материалов (о ниж ней подачей шликера), ПКБ НИИСтройкерамики (с верхней или ниж ней подачей шликера) и Гипростройматериалов, рис. 83.
Диаметр распылительного сопла обычной форсунки — 3,5—7,6 мм, что исключает его засорение.
Влажность суспензии, подаваемой за сушку, обычно 43—48% (максимальная до 55%). Давление распыливания в сушилке Минского комбината до 2,8 МПа, ПКБ НИИСтройкерамики 1—2 МПа, Гипростройматерналов— 1,2— 1,4 МПа.
Пневматический способ распыливания суспензии самый дорогой, с удельной затратой электроэнергии в 2,5—3 раза большей, чем при
распыливании диском. Его преимущество в более узком регулируемом факеле распыливания по сравнению с распиливанием диском. Всего в рабочей камере сушилки при распыливании суспензии осаждается 98 — 99,5% высушенного порошка и лишь 2—0,5% частичек, размером ме нее бОмкм, уносится и улавливается в пылеуловителях. Температура теплоносителя, подаваемого в камеру, 400—800° С. Продолжитель ность сушки 5—30 с. Производительность распылительных сушилок от 1,5 до 12 т/ч порошка.
Температура порошка на выходе из сушилки 50—60° С, влажность 6,0—8,5%.
Экономичность работы распылительных сушилок зависит главным образом от содержания сухого вещества в водной суспензии. Зави симость количества испаренной воды от содержания сухого вещества в суспензии приведена на рис. 84.
Расход воздуха на сушку зависит от его температуры и относитель ной влажности на выходе из сушилки. Зависимость удельного расхода воздуха в килограммах на 1кг испаренной воды от температуры воздуха, подаваемого в сушилку, и удельный расход тепла приведены на рис. 85.
Расход условного топлива 3—3,3 МДж/кг испаренной влаги, элект роэнергии 10—20 кВт на тонну порошка при конечной влажности порошка 6%.
Обезвоживание на фильтр-прессах. При обезвоживании по 1 ва рианту (см. технологическую схему) мембранными насосами суспензию подают в камерные фильтр-прессы. Влажность массы после фильтр прессов 22—24%. Давление поднимают медленно в течение первого часа до 0,5—0,6 МПа, доводя его ко второму часу до 1,0— 1,8 МПа. При максимальном давлении дают небольшую выдержку. Давление гидравлического затвора 1,1— 1,2 МПа. Фильтрат (ретурная вода) удаляется через фильтр-прессное полотно «бельтинг», капроновое или найлоновое полотно в сборный бассейн, оборудованный пропел лерной мешалкой. Поскольку фильтрат содержит до 2,5% и более твер дых частичек, то очищается он в специальной установке обработкой 5%-ным раствором полиакриламида. Осветленная вода возвращает
ся в производство.
Для повышения срока службы фильтр-прессного полотна на рамы фильтр-прессов надевают двойные дубленые полотна, которые предва рительно замачивают в теплой воде, обрабатывают 1,2%-ным раство ром соды при 85° С в течение 9 ч и промывают в моечном барабане. Дубление производят 1,5%-ным дубовым экстрактом при 85° С в те чение 5 ч. Дубленые полотна сушат, промывают в 0,8%-ном растворе медного купороса и в 0,3%-ном растворе хромпика. Продолжитель ность промывки 1 ч при 70—90° С. Периодичность промывки один раз в неделю. Расход полотна 1,4— 1,5 м2 на 1 т массы. Срок службы фильтр-прессного полотна «бельтинг» — 3 мес. (60—80 оборотов), капронового или нейлонового до 600 оборотов. Длительность цикла работы фильтр-пресса 4—8 ч.
Основной недостаток фильтр-прессов — периодичность работы, низкая производительность (до 0,5 т/ч), большая металлоемкость (около 9 т) и большие габариты (занимаемая прессом площадь около 9 м2).
Украинским НИИХиммаша разработан автоматический камерный фильтр-пресс ФПАКМ (рис. 86).
Основными рабочими элементами фильтр-пресса являются фильтру
ющие плиты 5 (в количестве 6 или |
12 в зависимости от типа |
пресса), |
||
расположенные между |
опорными |
плитами — верхней 1 2 и |
нижней |
|
1 6 . Механизм зажима |
плит 1 7 |
располагается под нижней |
плитой, |
|
он обеспечивает зажим |
плит за |
время от 30 до 60 с. Фильтровальная |
ткань 7 общей длиной от 17 до 50 м (ширина от 0,7 до 1,2 м) зигзаго образно проходит между фильтрующими плитами, огибая ролики 6 .
Общая поверхность фильтрации от 2,5 до 25 м2. Лента натягивается натяжным приспособлением 1 0 , установленным на верхней плите, а ее направление роликами 9. Фильтровальная ткань, пройдя привод передвижки ткани 4 , приводимый в действие электродвигателем, по ступает на очистку и мойку (регенерацию) в камеру 2 , оборудованную
скребками и форсунками для струйной промывки ткани. Фиксирован ное положение ткани по отношению к плитам обеспечивается направ ляющим роликом 3 . Время замены ткани 15—30 мин.
При сжатых плитах суспензия поступает по трубопроводу под давлением до 1,5 МПа в коллекторы подачи 1 1 и 1 3 , на выходе которых
установлены автоматически открывающиеся клапаны. Привод пере
движки ткани, камера регенерации и опорная плита 1 8 установлены на общей раме 1 9 . После набивки пресса твердая часть остается в виде
тонкого слоя (время набора слоя — 100 с) на фильтровальной ткани,
а фильтрат, пройдя через ткань и перфорированное сито, направляется
вколлектор отвода 1 4 . Вода для отжима резиновых диафрагм подается насосом через коллектор 1 5 . Давление отжима диафрагмой до 1,2 МПа.
Осадок разгружают после прекращения подачи суспензии и раскрытия фильтр-пресса (зазор между плитами 45 мм).
Фильтровальная ткань, приведенная в движение приводом пере движки ткани, выносит слой (массу толщиной до 35 мм) на обе стороны фильтр-пресса, где он снимается скребками 8 и поступает на ленточ ные транспортеры 1 , расположенные по сторонам фильтр-пресса.
Принципиальная схема работы фильтрующих плит (без промывки осадка) приведена на рис. 87. Плита состоит из двух частей: рамы 4
и корпуса 2, в котором собирается фильтрат. Он имеет днище и дре нажное основание 9 в виде вкладышей и перфорированного листа.
В рамке формируется осадок. Между корпусом и рамкой расположена выпуклая резиновая диафрагма 5, предназначенная для отжима осадка.
При собранном прессе плиты сжаты между верхней упорной плитой 6 и нижней плитой 1 1 ; пресс заполняется суспензией. Фильтрат про ходит через ткань 1 и перфорированное сито в камеры фильтрата (I—V)
и далее в коллектор отвода 3 . Осадок отжимается резиновыми диафраг
мами, на которые подается вода насосной станцией через коллектор подачи 8 , а сливается вода из диафрагмированных камер обратным путем через коллектор давления 1 0 .
Регулируется гидравлика фильтр-пресса блоком клапанов 7, клапаном сброса 1 2 и клапаном коллектора давления 1 3 .
Общая мощность установленных электродвигателей от 17,5 до 35 кВт.
Процесс обезвоживания суспензии происходит непрерывно. Произ водительность фильтр-пресса в 6—8 раз больше обычного и состав
ляет до 80 кг массы на 1 ма фильтрующей поверхности. Размеры пресса с фильтрующей поверхностью полотна в 30 м2 следующие: длина 3,5, ширина 2,5 и высота 2,6 м.
Обезвоженная на фильтр-прессах масса в виде коржей толщиной до 30 мм поступает на ленточные прессы для проминки и формования брикетов, далее на последующую сушку в туннельных сушилках или на измельчение с помощью коржерезки перед сушкой в сушильном барабане.
Далее масса поступает в бункер на остывание и вылеживание в течение 8 ч и затем, после дробления на зубчатой дробилке — на тон кий помол, в дезинтеграторы или в ротационные мельницы непрерыв ного действия, дающие большой выход тонких фракций в готовом пресс-порошке при меньших затратах электроэнергии.
После просева на ситах-буратах или виброситах (сетка 36 и
64 отв/см2) порошок пропускают через электромагнитный |
сепаратор |
и далее подают в бункера для вылеживания на срок от 12 |
до 24 ч и |
усреднения по влажности, а затем — в расходные бункеры над прес сами. Зерновой состав пресс-порошка (%): зерен размером более 1 мм — 10— 15, от 1 до 0,5 мм — 20—26, от 0,5 до 0,25 мм — 25—30, менее 0,25 мм — 42—35. Фильтр-прессный способ подготовки пресспорошка наиболее трудоемкий и длительный, поэтому сейчас заменяет ся сушкой в распылительных сушилках.
Сухой способ подготовки массы предусматривает как раздельный помол компонентов массы, так и совместный на отдельных стадиях. Технологическая схема сухой подготовки массы приводится ниже.
При сухом способе подготовки пресс-порошков глинистые материа лы сушат в сушильном барабане. Более экономичным является ис пользование сушильных агрегатов, состоящих из роликовой или мо лотковой мельницы, воздушного сепаратора и циклона, в которых совмещены процессы сушки и помола глинистых материалов. По мольные установки работают по замкнутому циклу — после фракцио нирования продуктов помола в воздушных сепараторах более крупные фракции (чем допустимо) возвращаются на домол в мельницу. Для тон кого помола используются высокоскоростные машины — дробилки, мельницы ударно-отражательного типа, струйные и центробежные мельницы.
Тонкий помол отощающих материалов также производят в шаровых мельницах непрерывного действия (конических или цилинд рических), работающих по замкнутому циклу.
При обычном тонком измельчении компоненты массы смешивают и увлажняют в бегунковых смесителях, пропуская ее через дезинтегра торы или молотковые мельницы. При влажности массы 6— 10% и более наиболее пригодными являются бесколосниковые мельницы. Добавка 1—4%-ного водного раствора ПАВ улучшает качество смешивания
и увлажнения |
порошков. |
С в о й с т в а |
п р е с с - п о р о ш к о в , полученных различными спосо |
бами, неодинаковые. Наибольшую объемную массу имеют пресс-порош ки, полученные в бегунах, которые кроме дробящего, создают также уплотняющее воздействие на материал.
Схема сухой подготовки массы
СКЛАД СЫРЬЯ
4 |
4 |
Полевой |
Череп |
(бой |
Глина |
Каолин |
|||
|
шпат или |
плиток, кап |
||
|
его замени |
селей) |
||
|
|
тели |
|
|
Сортировка |
Сортировка |
Сортировка |
Сортировка |
|
I |
4 |
Промывка |
Промывка |
|
Изме льчение |
Измельчение |
|||
(стругач, зубча |
(валковая дро |
(моечный |
(моечный |
|
тые вальцы) |
билка) |
барабан) |
барабан) |
|
I |
I |
4 |
4 |
|
4 |
4 |
|||
Сушка (сушиль |
Сушка (сушиль |
Дробление |
Дробление |
|
ный барабан) |
ный барабан) |
(бегуны) |
(бегуны) |
|
I |
4 |
1 |
I |
Т |
4 |
4 |
4 |
4 |
|
Тонкий помол |
Тонкий помол |
Тонкий помол (конические |
||
(дезинтегратор, |
|
шаровые мельницы |
||
ротационная |
|
непрерывного действия) |
||
мельница) |
|
|
|
|
1 |
|
|
4 |
|
V |
Магнитная |
|
|
|
Магнитная |
Магнитная очистка |
|||
очистка (подвес |
очистка (подвес |
(подвесные электромагниты) |
||
ные электромаг |
ные электромаг |
|
|
|
ниты) |
ниты) |
|
|
|
I
4
Кварцевый
песок
Просев
(вибросито)
Дозирование компонентов с увлажнением (бегунковые смесители)
4
Разрыхление пресс-порошка (молотковая мельница)
4
Просеивание (сита)
1
Электромагнитная очистка пресс-порошка
4
Хранение (бункера)
В ротационных и центробежных мельницах пресс-порошок насы щается воздухом больше, чем в бегунах, что приводит к некоторому уменьшению объемной массы.
Качество порошка, полученного в распылительной сушилке, выше качества порошка, полученного фильтр-прессным или другими спо собами. Зерна порошка из распылительных сушилок имеют сфериче скую форму, в порошке почти нет пылеватых частичек, а количество частичек больше 1 мм незначительно. Основная масса порошка (80%) представлена фракцией зерен размером 0,2—0,5 мм. Распределение частичек по диаметру в основном стабильно (рис. 88). Гранулометри ческий состав, форма частиц, отсутствие пылеватой фракции обеспе чивают высокую сыпучесть (51,6 г/с) в широком диапазоне влажности.
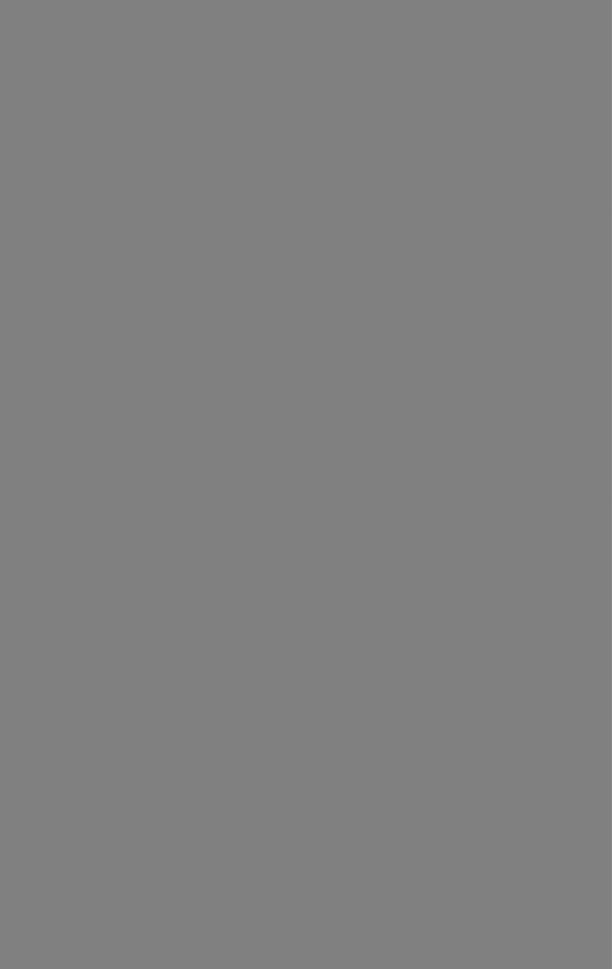
Диоксид циркона используют во фриттованных глазурях для глу шения глазури. По данным электронной микроскопии (О. С. ГрумГрижимайло), кристаллы циркона в глазури характеризуются корот копризматическим строением, имеют размеры от 0,1 до 0,5 мкм и рав номерно распределены на расстоянии 0,5— 1,0 мкм один от другого. Наблюдаются сростки кристаллов (по 2—4 и более). Все это хорошо глушит глазурь. Качество глушения глазури зависит не только от содержания в ней диоксида циркона, но и от соотношения других оксидов. Поэтому в качестве основного плавня фритты вводят В20 3
Таблица 26. Составы фритт для плиток, |
% |
|
|
|
|
|
||||
|
|
|
Двукратный обжиг в |
|
Политой обжиг п многоканаль |
|||||
|
Материал |
|
туннельных печах |
|
|
ных печах |
|
|||
|
|
|
|
|
|
|
|
|
||
|
|
|
1 |
2 |
3 |
4 |
\ |
2 |
3 |
4 |
Песок |
кварцевый |
30,6 |
31,2 |
30,4 |
20 |
36,7 |
34,2 |
34,2 |
26,2 |
|
Борная |
кислота |
— |
— |
— |
4,3 |
4 |
16,5 |
7,43 |
||
Бура кристаллическая |
14,8 |
24,5 |
23,8 |
— |
25,3 |
30,1 |
3 |
5,75 |
||
Циркон |
|
11,2 |
9,3 |
9 |
14 |
10,4 |
12,65 |
14,5 |
23,55 |
|
Оксид цинка |
4,6 |
4,2 |
4,1 |
8 |
1,2 |
1,2 |
3,5 |
5,9 |
||
Поташ |
|
|
6 |
3,5 |
2,8 |
— |
|
— |
5.2 |
— |
Мел |
|
|
1 |
2,1 |
1,5 |
8 |
— |
5,85 |
4,7 |
— |
Доломит |
|
3,2 |
7,3 |
9,1 |
— |
— |
— |
— |
— |
|
Каолин просяновский |
22,7 |
15 |
16,2 |
— |
14 |
11 |
П,2 |
5,9 |
||
Сода кальцинированная |
3 |
— |
0,5 |
— |
— |
— |
— |
— |
||
Гексафторсиликат натрия |
2,9 |
2,9 |
2,6 |
— |
— |
— |
1,4 |
2,68 |
||
Перлит арагацкий |
— |
— |
— |
50 |
— |
— |
— |
— |
||
Мрамор |
|
— |
— |
— |
— |
6,4 |
— |
— |
— |
|
Карбонат бария |
— |
— |
— |
1,4 |
1 |
2 |
— |
|||
Тальк онотский |
— |
— |
— |
— |
— |
— |
— |
7,34 |
||
Борат кальция |
— |
— |
— |
— |
— |
— |
— |
12,1 |
||
Карбонат |
калия |
— |
— |
— |
— |
— |
— |
— |
3,15 |
|
Сульфат |
кобальта (сверх |
0,02 |
0,02 |
|
— |
0,03 |
0,02 |
0,02 |
0,02 |
100%)
ввиде буры или гидроборацитов, при общем содержании щелочных оксидов 4—7%. Циркониевые глазури склонны к образованию на колов тем больше, чем ниже их вязкость и поверхностное натяжение при температуре разлива. Повышением вязкости и поверхностного натяжения при разливе, а также снижением температуры обжига устраняют этот дефект глазури. Замена циркониевой и стронциевой
глазури улучшает внешний вид плиток, повышает белизну, улучшает блеск, устраняет матовость, полосатость, серовато-зеленый оттенок на плитках.
При скоростном обжиге плиток хороший разлив глазури достигает ся как за счет повышения температуры обжига на 40—60° С против обычной, так и за счет изменения состава глазури. В глазури целе сообразно использовать материалы, не склонные к интенсивному газообразованию в процессе обжига. Лучше использовать глухие, маловязкие борноциркониевые глазури, обеспечивающие хороший разлив за короткое время нагрева. При этом вязкость глазури должна