
книги / Технология строительной керамики
..pdf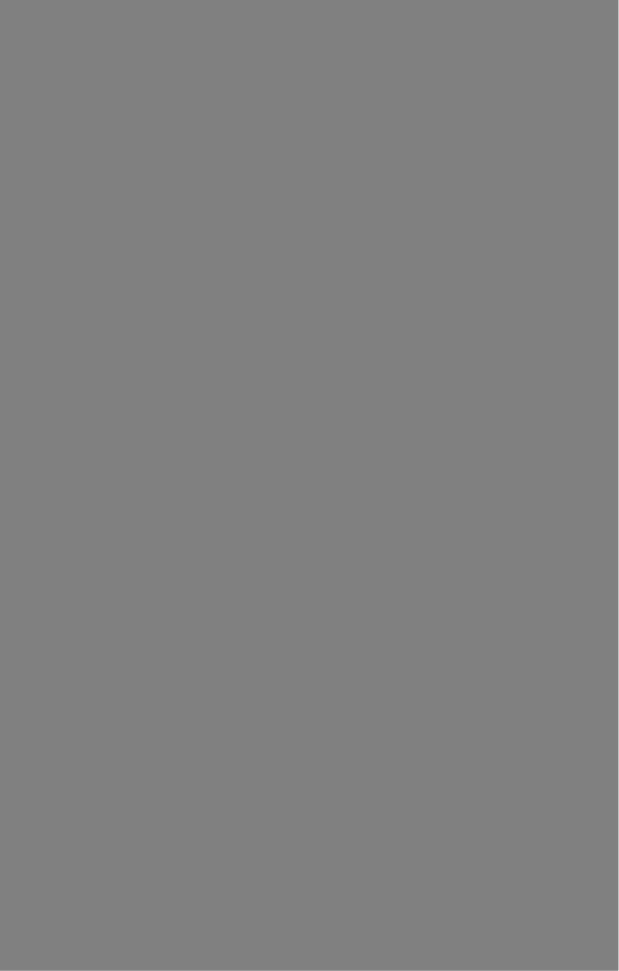
в черный, темно-зеленый и темно-коричневый цвет, рекомендуется -краситель вводить в прозрачную полевошпатовую глазурь, не содер ж ащ ую циркона.
Ангоб должен иметь хорошее сцепление с черепком, соответствовать •черепку по коэффициенту термического расширения и ложиться на черепок гладким, ровным слоем. Важнейшими показателями, харак теризующими свойства ангоба, являются его вязкость и плотность.
.Хорошее сцепление черепка с ангобом бывает, если в состав ангоба ■входит достаточное количество кремнезема, а усадка ангоба соответ ствует усадке черепка изделия.
Таблица 36. Составы цветных глазурей; % |
|
|
|
|
|
||
Материал |
|
|
Цвет глазури |
|
|
||
салатовый][ |
желтый |
]| |
розовый |
черный |
голубой |
||
|
|||||||
•Полевой шпат |
19,0 |
19,0 |
|
38,9 |
45,0 |
19,0 |
|
•Кварцевый песок |
19,0 |
19,0 |
|
21,0 |
26,0 |
19,0 |
|
Мел |
— |
— |
|
12,3 |
16,0 |
— |
|
Карбонат бария |
5,1 |
5,1 |
|
5,3 |
— |
5,1 |
|
•Оксид цинка |
2,8 |
2.8 |
|
4,6 |
— |
2,8 |
|
Циркон |
— |
5,4 |
|
14,0 |
— |
— |
|
•Глина пластичная |
5,4 |
|
1.9 |
— |
5.4 |
||
'•Каолин |
3,2 |
3,2 |
|
2,0 |
4,0 |
3,2 |
|
Вой фарфоровый |
— |
— |
|
|
9,0 |
— |
|
■Фритта |
47,0 |
47,0 |
|
|
“““ |
47,0 |
|
Красители (Дулевский завод) |
3,0 |
|
|
|
|
10,0 |
|
№ 38 |
— |
|
— |
— |
|||
№ 55 |
12,0 |
15,0 |
|
— |
— |
— |
|
№ 4 |
— |
— |
|
2,0 |
— |
— |
|
№ 1063 |
— |
— |
|
|
10,0 |
0,2 |
|
Оксид кобальта |
|
— |
|
|
3,5 |
|
|
Тонкость помола ангоба |
для изделий |
из |
шамотированных масс |
.характеризуется остатком на сите 10 000 отв/см2 2,8—3% , влажностью 35— 37%, плотностью 1,66— 1,63 г/см3.
Перед приготовлением глазурей полевой шпат и кусковой кварц предварительно промывают и обжигают: полевой шпат при 950— 1000° С, •а кварц при 1250— 1280° С. Если использовать оксид цинка и тальк, то их обжигают при 1280° С. Каолин обожженный получают при 1350— 1400° С. После обжига материалы сортируют и измельчают на бегунах с гранитными катками.
Мел дробят до величины кусков 50— 60 мм и сортируют, удаляя
.куски с железистыми соединениями и кремневой галькой. Помол оксида циркония пройзводят в шаровой мельнице мокрого помола до круп ности зерен 5—8 мкм. Соотношение диоксида циркония и уралитовых шаров“1 : 2. Продолжительность помола не менее 100 ч.
Глазурь приготовляют совместным помолом всех компонентов в шаровой мельнице при соотношении материала и мелющих тел 1 :1 -f- 2 и влажности 38— 45%, фарфоровых 40— 45% . Продолжительность помола 7—7,5 ч. Готовность глазури определяется по остатку на сите 10 000 отв/см2 не более 0,05—0,3% .
Перед подачей на глазурование глазурь проверяют по огневой пробе и другим показателям и корректируют, добавляя воду или глазурь, до плотности 1,48— 1,7 г/см3 в зависимости от вида изделий и способа глазурования.
Глазурь с плотностью более 1,68— 1,72 г/см3 используют для гла зурования изделий пульверизацией при влажности 37—38%. Плот ность фаянсовых глазурей 1,52— 1,54, остаток на сите 10 000 отв/см2
0,25—0,3% , полуфарфоровых — соответственно 1,48— 1,55 см3 и 0,15—
0, 2% .
Ангоб приготовляют по технологии приготовления глазури. Ангоб для изделий из шамотированных фаянсовых масс имеет остаток на сите 10 000 отв/см2 2,8— 3,0% при влажности 40—42%. Плотность ангоба 1,6— 1,64 г/см2.
Перед подачей на ангобирование корректируют влажность анго ба добавлением карбоксилметилцеллюлозы, декстрина, органического клея, желатина и других клеящих веществ, улучшающих сцеплениеангоба с поверхностью изделий.
Формование изделий. Формуют изделия в основном методом шликерного литья в гипсовых формах. Разработан (НИИСтройкерамика) также метод гидростатического прессования изделий.
I ; Метод шликерного литья, как один из способов формования ке рамических изделий в гипсовых формах, основан на способности глин давать устойчивые суспензии в дисперсионной среде, на реологических свойствах шликеров и на поглощении дисперсионной фазы капил лярами гипсовой формы с образованием на ее поверхности твердого слоя.
Способность |
шликера заполнять гипсовую форму обуславливается |
||
его текучестью |
(вязкостью), а воспроизводить конфигурацию фор |
||
мы — его |
литейными |
свойствами. Вода и электролиты обеспечивают |
|
шликеру |
требуемые |
свойства. |
|
Независимо от применяемого способа отливки изделий, механизм |
|||
набора (образования) |
стенки изделия в гипсовой форме одинаков. |
Он заключается в осаждении твердой фазы шликера на внутренней поверхности формы при одновременном поглощении жидкой фазы по рами формы.
Скорость набора стенки изделия зависит от скорости поглощения
жидкой фазы |
шликера формой (проницаемость |
гипсовой |
формы |
2,5 10-9 — 5,0 |
• 10“ и л/см2), гранулометрического |
состава |
твердой |
фазы, соотношения твердой и жидкой фазы, а также от скорости диф фузии шликера и воды слоем образовавшегося черепка (проницаемость
слоя черепка (2,4— 3,0) 10~п л/см2).
Скорость набора стенки изделия нарастает пропорционально кор ню квадратному из времени и составляет, например, для полуфарфоровой массы 0,00134— 0,00163 г/(см2 • с).
В процессе набора черепка изделий большое значение имеют силы капиллярного давления, создающие мениски воды в порах гипсовой формы. В процессе фильтрации принимают участие как поры наимень шего диаметра (30—45 А), так и более крупные (до 100 А).
Скорость набора черепка возрастает с увеличением пористости гипсовой формы и замедляется, главным образом, сопротивлением
слоя черепка, образовавшегося на поверхности формы. Сопротивление гипсовой формы капиллярному давлению незначительно. Пористость
(42— 47%) и средний размер пор (0,38 ± |
0,01 нм) в черепке не зависят |
|||||||||||||
от структуры |
гипсовой |
формы. |
|
|
|
|
|
|
|
|
|
|
||
Скорость |
набора черепка при возрастающей |
пористости |
формы |
|||||||||||
и зависимость этой скорости от средних размеров |
пор в форме до- |
|||||||||||||
стигаетмаксимума при размере пор, при |
котором |
проницаемость |
на |
|||||||||||
бранного |
слоя |
уравнивается с проницаемостью |
формы |
(рис. |
ЮЗ). |
|||||||||
Повышенная влажность шликера снижает скорость набора череп |
||||||||||||||
|
|
|
|
|
ка. Скорость |
поглощения |
жид |
|||||||
|
|
|
|
|
кой |
фазы |
шликера |
пористыми |
||||||
|
|
|
|
|
стенками |
формы |
должна |
быть |
||||||
|
|
|
|
|
выше или равна скорости подхо |
|||||||||
|
|
|
|
|
да ее к поверхности формы. При |
|||||||||
|
|
|
|
|
значительном |
опережении |
ско |
|||||||
|
|
|
|
|
рости поглощения воды формой |
|||||||||
|
|
|
|
|
на наружном слое отливки обра |
|||||||||
|
|
|
|
|
зуется более |
уплотненный слой, |
||||||||
|
|
|
|
|
что связано с появлением внут |
|||||||||
|
|
|
|
|
ренних напряжений, |
отслаива |
||||||||
|
|
|
|
|
нием от стенки формы и появле |
|||||||||
|
|
|
|
|
нием |
трещин. При |
отставании |
|||||||
|
|
|
|
|
скорости |
поглощения воды по |
||||||||
|
|
|
|
|
следняя накапливается в поверх |
|||||||||
|
|
|
|
|
ностных слоях формы, что при |
|||||||||
|
|
|
|
|
водит к размыванию ее и прили |
|||||||||
Рис. 103. Зависимость скорости набора че |
панию изделия к форме. |
|
|
|||||||||||
|
Гранулометрический |
состав |
||||||||||||
репка от средней величины пар (/) и порис |
|
|||||||||||||
тости (2) гипсовой формы. |
|
твердой |
фазы |
также |
влияет на |
|||||||||
|
|
|
|
|
скорость набора стенок изделий. |
|||||||||
Она будет |
выше, |
если |
поверхностный |
слой |
изделия |
образуется из |
||||||||
частиц, не дающих плотной упаковки. |
Однако |
укрупнение |
помола |
|||||||||||
чрезмерно |
увеличивает |
скорость набора стенок, |
что приводит |
к не |
одинаковой толщине изделий и затрудняет регулирование процесса на бора стенки изделия. Перемол ж е шликера повышает содержание тон кодисперсных фракций, приводит к резкому снижению скорости набо ра стенок изделий и прилипанию изделий к форме.
В результате поглощения воды шликера формой образовавшийся слой стенки уплотняется, изделие дает усадку и отделяется от формы, что облегчает извлечение изделия из формы.
При повышении содержания тонких фракций в шликере усадка увеличивается до 1% и выше. Поэтому при отливке изделий слож ной формы стремятся уменьшить усадку, чтобы снизить вероятность об разования внутренних напряжений и возможность образования трещин.
Интенсивность набора стенки (черепка) и качество отливки также линейно зависят от температуры шликера, содержания в нем воздуха,
количества и состава электролитов и |
др. Подогрев форм (до 60° С, |
но не выше) почти в два раза ускоряет |
набор стенки изделия. Темпе |
ратура обычного фарфорового шликера 40— 45° С является оптималь
ной, шамотированного шликера — 50—65° С. G повышением темпе ратуры шликера возрастает воздушная усадка изделий.
Вакуумирование шликера способствует удалению воздуха (2— 2,5% по объему), который может быть в нем по разным причинам: •адсорбированный твердой фазой и удерживаемый ее гидрофобными участками (микродисперсный воздух), механически захваченный при приготовлении и перемешивании (микродисперсный воздух), раство ренный в жидкой фазе. Вакуумирование шликера производят при давлении 40— 61,3 кПа. Вакуумирование шликера способствует уплотнению черепка отливки, уменьшению посечек, снижению брака при разъеме форм и после сушки.
Вакуумирование гипсовых форм также способствует сокращению сроков набора стенок изделий в 2— 4 раза.
С применением вибрации при отливке изделий (3000—6000 кол/мин) при амплитуде 0,2— 0,4 мм или обработке шликера ультразвуком понижается вязкость шликера, снижается на 1—2% влажность отливок и повышается их прочность. Предельное сопротивление сдвигу воз растает на 10—30%, предел прочности при изгибе после сушки на 20% . При вибрации улучшается структура изделий, уменьшается воз можность образования раковин в отливках при наборе стенок изде лий в 4— 5 раз по сравнению с отливкой обычным способом.
Отливка изделий под давлением в 0,2 МПа из обычного фарфо рового шликера сокращает время набора изделия в два раза, из шамотированного на 50%.
Новые гипсовые формы перед отливкой промывают 5%-ным раство ром соды или разбавленным водой шликером. Формы повторного ис пользования сушат до влажности 5— 6%. Все детали формы должны иметь одинаковую влажность. Максимально допустимая влажность рабочих форм 18—20%. Ускорению набора черепка при отливке спо собствует смачивание гипсовых форм водным раствором мочевины, вве дение в шликер вытяжек из бурого угля и соломы.
Отливка в формы из вакуумированного гипсового раствора спо собствует сокращению времени набора изделия на 16—27%, механи ческая прочность изделий повышается на 30—35%, удлиняется срок
службы форм. |
|
|
|
Отливают изделия в отдельных гипсовых формах, в |
формах, со |
||
бранных в |
батареи, |
и на конвейере. |
|
В зависимости от вида изделий шликерное литье выполняется |
|||
наливным, |
сливным |
и комбинированным (стержневым) |
способами. |
Н а л и в н ы м |
с п о с о б о м отливают тарельчатые унитазы, |
унитазы «Компакт» и другие компактные изделия с большой толщиной стенок.
Формы собирают, скрепляют скобами, швы промазывают массой. Заливают шликер в форму через шланг, направляя струю по стенке воронки, в один прием за 1,5—2 мин. Сначала форму на 10—20 мм не доливают, чтобы дать свободно выйти воздуху. Доливают ее через 10— 15 мин. Обычно наливной способ применяют при батарейной отливке изделий. Гипсовые формы собирают в батареи по 16—20 шт. и скреп ляют металлическими стяжками. Заливают формы шликером через
воронки, установленные по углам и в середине батареи. Уровень шликера в воронках после заливки батареи должен быть на 20—30 см
выше верхнего края форм. Температура |
шликера перед заливкой |
25 ± 3° С. |
|
При наливном способе набор черепка |
происходит между двумя |
стенками гипсовой формы. Шликер непрерывно доливают в форму до полного заполнения формы массой. Через 1— 3 ч после набора формой стенки изделия требуемой толщины излишек шликера сливают, изделия
в формах выстаиваются 7— 16 ч для закрепления черепка, |
после чего |
их освобождают из форм, предварительно оправляют и |
прикрепля |
ют отдельно отлитые части — донышки к корпусу (унитаза). Разни мают формы при влажности изделий 20—22,5% . Гипсовые формы через 5—7 отливок поступают на сушку для снижения влажности до 5— 6%. Оборачиваемость гипсовых форм 30— 40 раз. Качество отливки повыша ется, если форма проще, с меньшим количеством деталей. Наливным способом также отливают изделия из шамотированных фаянсовых масс с толщиной стенки 25—45 мм (ванны, мойки и др.).
Наливной способ требует изготовления разборных форм сложной конфигурации. В этом его существенный недостаток.
С л и в н ы м с п о с о б о м отливают умывальные, столы и другие тонкостенные изделия. При сливном способе заполненные шликером формы выстаиваются 1— 3 ч до набора формой требуемой толщины стенки изделия (9— 11 мм). Время набора зависит от состава массы, ка чества шликера, влажности гипсовых форм, температуры помещения.
После набора стенки изделия излишек шликера сливают в чис тые отстойники, изделие выдерживают в форме 6— 16 ч для повышения прочности и снижения влажности до 22—24%, после чего вынимают из формы и зачищают влажной губкой. При сливном способе проис ходит односторонний набор стенки изделия, он наиболее простой, но не обеспечивает постоянной толщины стенки изделий. Сливной способ применяется при изготовлении изделий на конвейере и для
отливки тонкостенных изделий. |
|
К о м б и н и р о в а н н ы м |
с п о с о б о м отливают умываль |
ные столы (в зависимости от типа), писсуары и др. При комбинирован ном способе одни части изделия отливают наливным, другие — сливным способом. Соединяют части при оправке и компоновке изделий.
Изделия, освобожденные из гипсовых форм (независимо от спосо ба отливки), проходят первичную оправку, в которую входят: обрезка следов швов формы, обработка поверхностей и отверстий, приставка отдельно формуемых частей, нарезка резьбы (в унитазах) и др. Далее изделия оставляют на стеллажах или направляют в специальные каме ры и рольганговые конвейеры для подвяливания (до влажности 14— 18%), после чего вторично оправляют и направляют на сушку или дополнительное подвяливание для снижения влажности до 12— 14%.
Длительность подвяливания фарфоровых унитазов на рольганго вом конвейере 3,5— 4 ч при температуре теплоносителя 38— 42° С, умывальных столов на монорельсе при 25 dh 3° С — 24 ч.
При нижней подаче шликеров в форму улучшается качество ли тья, так как исключается захват воздуха в виде пузырьков. Возмож
ность захвата воздуха уменьшается при использовании специальных наконечников (рис. 104).
Стендовые способы отливки изделий требуют больших производ ственных площадей (съем изделий с 1 м2 почти в 2 раза ниже, чем при
отливке изделий на конвейере), связаны с тяжелым |
|
|
|
|
|||||||||
физическим трудом, не позволяют автоматизировать |
|
|
|
|
|||||||||
процессы |
отливки |
изделий. Это вызывает необхо |
|
|
|
|
|||||||
димость организации отливки изделий на поточных |
|
|
|
|
|||||||||
механизированных и полуавтоматизированных ли |
|
|
|
|
|||||||||
ниях с применением литейно-подвялочных конвейе |
|
|
|
|
|||||||||
ров. Количество изделий, выпускаемых на конвей |
|
|
|
|
|||||||||
ерах |
различных типов, |
в |
настоящее время состав |
|
|
|
|
||||||
ляет: |
унитазов — до 70%, |
умывальных столов — |
|
|
|
|
|||||||
30%. |
|
|
|
|
|
|
|
|
|
|
|
|
|
Литейно-подвялочный конвейер для производст |
|
|
|
|
|||||||||
ва умывальных столов СМ-462А комбинированным |
|
|
|
|
|||||||||
способом представляет собой две параллельные, |
|
|
|
|
|||||||||
самостоятельно действующие секции |
(ветви), рас |
|
|
|
|
||||||||
положенные в два |
яруса |
(рис. 105). Между ними |
|
|
|
|
|||||||
располагается подвялочная часть конвейера. В каж |
|
|
|
|
|||||||||
дой секции уложены рельсовые пути, по которым |
|
|
|
|
|||||||||
перемещаются тележки. Поднимаются и опускают |
|
|
|
|
|||||||||
ся тележки с этажа на |
этаж |
гидроподъемником. |
|
|
|
|
|||||||
В рабочих камерах конвейера |
собирают и разбира |
|
|
|
|
||||||||
ют формы, заливают и сливают излишки шликера, |
|
|
|
|
|||||||||
набирают и закрепляют черепок, оправляют тыль |
конуе: |
|
|
||||||||||
ные части изделий |
и сушат гипсовые формы. |
|
|
|
|||||||||
В нижней и верхней кассетах, установленных |
1 — подача шликера; |
||||||||||||
2 — резиновый шлн- |
|||||||||||||
на тележке, |
монтируют гипсовые формы. Нижняя |
керопровод; 3 |
— сое |
||||||||||
форма может |
поворачиваться |
на 180°, верхняя — |
динительная |
муфта; |
|||||||||
4 — выпуск шликера; |
|||||||||||||
на 112°. Формы в процессе заливки,'набора черепка |
5 — отверстия |
кону |
|||||||||||
са; 6 |
— конус. |
|
|||||||||||
и закрепления черепка скреплены между собой |
|
|
|
|
|||||||||
автоматическим замком; открывающимся по копиру |
(шаблону). |
||||||||||||
Форма |
состоит |
из |
трех |
частей: |
верхней, |
нижней |
и |
пробки. |
|||||
В |
начале |
нижнего яруса |
конвейера рабочий |
осматривает |
и |
очи |
щает гипсовые формы, устанавливает воронки и колышки и заливает
Рис. |
105. Схема литейно-подвялочного конвейера СМ-462А: |
|
1 |
— |
гидротолкатель верхний; 2 — гидроподъемник; 3 — механизм слива шликера; |
4 |
— |
камеры; 5 — ’механизм заливки шликера; 6 — тележки; 7 — гидротолкатель ниж |
ний; |
8 — подвялочиый конвейер; 9 — пневмо подъем ни к; 10 — монорельс уборки |
отходов; / / —механизм съема изделий; /J?— транспортер возврата воронок и колышков.
шликером при помощи автоматически действующего механизма залив* ки. Полнота заливки контролируется специальным датчиком уровня.
Перемещаясь по рельсовым путям, тележка с формами |
прохо |
дит камеры набора стенки изделия, составляющие около 2/3 |
длины |
конвейера (от 24 до 36 позиций). При среднем ритме работы конвейера 4 мин продолжительность набора стенок изделий при температуре в камере 30— 40° С составляет 1,5 ч. Далее каретки с формами посту пают на автоматическое устройство, наклоняющее гипсовую форму для слива излишка шликера. Предварительно рабочий снимает во ронку и колышки с формы и прочищает отверстие для воздуха.
В конце нижнего яруса конвейера каретки с формами автомати чески подаются гидроподъемником на второй ярус конвейера и верх ним толкателем проталкиваются в камеру закрепления изделия. Продолжительность закрепления стенок изделия около 3 ч при 35— 50° С (для фарфора 5—7 ч). Теплоноситель подается на протяжении 28 позиций. При выходе кареток со второго яруса гидроподъемник опускает их вниз и они поступают на позицию автоматического раскры тия форм.
На позиции съема изделий рабочий заделывает наливные и слив ные отверстия, прокалывает отверстия для кронштейнов и сухарей, для кранов, оправляет тыльную и лицевую стороны, устанавливает и закрепляет гипсовую крышку (поддон), прокалывает водосливные отверстия.
Умывальный стол с прикрышей передается на подвялочную часть конвейера, где 30 мин при 30— 55° С происходит подвяливание. Далее
изделия поступают на сушильной вагонетке в сушилку. |
|
|
Гипсовая форма после сушки при 55—60° С в продолжение |
1,5 ч |
|
поступает на |
позицию подготовки к заливке (в начале нижнего |
яру |
са), и цикл |
повторяется. |
|
Производительность конвейера — 220—240 тыс. умывальные сто лов в год при ритме 3,6—4 мин (ритм может изменяться от 3 до 6 мин). Конвейер обслуживает восемь рабочих,-Общая продолжительность отливки изделий — 6,5—8 ч.
Литейно-подвялочный конвейер СМ-461А (рис. 106) для отливки унитазов состоит из кран-балки для-съема кареток 1 , гидротолкателей
2 , механизма разработки форм 3 , кареток (130 шт.) 4 , устройства для очистки конвейера 5 , гипсовых форм (260 шт.) 6 , камеры подсушки
гипсовых форм 7, механизма сборки гипсовых форм на участке заливки
их 8 , механизма заливки форм 9 |
, |
увлажнителя 1 0 , |
мешалки |
(после зо |
|
ны набора стенки изделия) И , |
механизма слива излишка шликера 1 2 , |
||||
лотка 1 3 , гидроподъемников |
1 4 |
, |
основания 1 5 , |
площадок |
разборки |
форм 1 6 , механизма приема изделий!/7, привода конвейера 1 8 , шкафа
с гидроаппаратурой 1 9 , |
подвялочного рольганга 2 0 , шкафа с электро |
|||||||||||
аппаратурой 2 1 , |
площадки сборки форм 2 2 , площадки слива |
шлике |
||||||||||
ра |
2 3 . |
|
|
|
|
|
|
|
|
|
|
|
|
В |
литейную |
часть |
конвейера |
|
|
|
|||||
входят два яруса и три |
камеры, из |
|
|
|
||||||||
которых две (сушки гипсовых форм |
|
|
|
|||||||||
и набора стенки изделия) находят |
|
|
|
|||||||||
ся на верхнем этаже и одна (за |
|
|
|
|||||||||
крепления изделий) на нижнем. Гип |
|
|
|
|||||||||
совые |
|
формы |
|
устанавливают |
по |
|
|
|
||||
2 |
шт. |
|
на |
тележках-каретках |
|
|
|
|||||
(130 |
шт.), |
передвигающихся |
рит |
|
|
|
||||||
мично |
(через 4,0 мин) по рельсо |
|
|
|
||||||||
вым путям камер конвейера при |
|
|
|
|||||||||
помощи |
верхнего и нижнего |
гид. |
|
|
|
|||||||
равлических толкателей. Передают |
Рис. 107. Кривые изменения влажности |
|||||||||||
ся каретки с яруса на ярус гидро |
в процессе подвяливания: |
|
||||||||||
подъемниками. Съем изделий и пе |
/ |
*— в слое, обращенном к гипсовой форме; |
||||||||||
редача |
их |
на |
подвялочную |
часть |
2 |
— усредненная влажность; 3 |
— в верх |
|||||
нем слое. |
|
|||||||||||
конвейера |
осуществляется |
специ |
|
|
|
|||||||
альным |
механизмом. Эта часть конвейера состоит из камеры, |
обору |
дованной рольгангом с верхними и нижними рядами роликов. Верхний ряд роликов предназначен для передвижения поддонов с изделиями, нижний — для возврата поддонов к позиции съема изделий.
При включении конвейера рабочие на позиции сборки форм со бирают гипсовые формы. Для уплотнения гипсовых форм (вместо обмазки глиной вручную) используют шнур из губчатой техниче ской резины прямоугольного сечения (10 х 12 мм). Все гипсовые фор мы заменяют одновременно. Далее каретки с формами поступают на позицию автоматической заливки их шликером (6-я позиция, 24 мин). Через одну позицию производится автоматическая доливка шликера, увлажнение пистолетом-распылителем для предотвращения образова ния «корки» и передача далее в камеру набора стенки изделия. Продол жительность набора изделия на 30 позициях 1,3—2 ч. Для улучшения работы и повышения производительности конвейера на отдельных за водах (Славутский) сократили камеру сушки гипсовых форм, увели чивая количество позиций набора черепка. При этом в камеру сушки форм увеличивают подачу теплоносителя за счет отбора горячего воз духа с туннельной печи. Температура на участке набора черепка 30— 32° С. Перед сливом избытка шликера его слегка размешивают мешал кой. После слива шликера каретки гидроснижателем передаются на нижний ярус конвейера и гидротолкателем проталкивается через
камеру закрепления изделия — для полуфарфоровых масс 65 позиций 4— 5 ч, для фарфоровых масс — 7— 8,5 ч. Продолжительность'закреп ления стенок изделий может быть снижена, а качество закрепления повышено при использовании соплового дутья, направленого внутрь формы. Отсутствие обдува вызывает значительные перепады влажности (рис. 107). При преждевременном обдуве (ранее 2 ч после слива шлике ра) на изделиях могут появиться трещины-посечки. Обдув осущест вляют нагретым до 50° С воздухом, подаваемым со скоростью 7— 8 м/с.
После выхода из камеры каретки с формами подаются гидроподъ емником на верхний ярус конвейера на позиции оправки внутренней поверхности изделий и приставки деталей (7 позиций, продолжитель ностью 32 мин). После освобождения изделий из форм разобранные формы поступают на передаточных тележках в камеру подсушки (16 позиций). В камере сушки гипсовых форм температура 60— 65° С. Продолжительность сушки форм — 1 ч.
Перед загрузкой изделий на подвялочный рольганговый кон
вейер |
их предварительно оправляют. Продолжительность подвялива- |
ния 4 |
ч (до влажности 16— 17%) при 30— 35° С. После подвяливания |
изделия проходят окончательную оправку на оправочных столах. Общая продолжительность изготовления изделий на конвейере 8 ч.
Большая часть технологических операций — сборка гипсовых форм, заливка форм шликером, .слив излишка шликера, разборка форм, перемещение кареток с формами — выполняется автоматически. Но обработка верхнего вкладыша перед сборкой форм, обработка и оправка изделий, съем изделий с поддона, установка поддонов на рольганг, передача изделий на оправочные столы и ряд других опера ций выполняется вручную, что является недостатком конвейера.
Производительность конвейера СМ-461 А — 200— 220 тыс. унита зов в год. Конвейер обслуживает 10 человек.
Харьковским КБ Строймашина совместно с институтами НИИСтройкерамика и Гидростройматериалы разработан линейноподвялочный конвейер СМК-210 для литья унитазов козырькового типа «Компакт» и тарельчатого типа.
На конвейере предусмотрена автоматическая сборка форм, заливка шликера в формы, вакуум-слив избытка шликера с перемешиванием его перед сливом. Продолжительность операции (в мин): сушка форм 146, набор черепка 90, закрепление черепка 300, подвялка изделий 225. Производительность конвейера 384 изделия за 8 час.
На Куйбышевском заводе .Стройкерамика изготовлена конвейерная линия производства унитазов производительностью 500 тыс. изделий в год. Линия имеет одноэтажное расположение форм. Литейный агрегат включает четыре идентичные тележечные линии-заливки, набора и за крепления черепка, подвялки и сушки гипсовых форм. В начале и конце эти линии соединены транспортерами. Работа линии автоматизирована.
Метод гидростатического прессования. За последние годы были проведены большие исследования (НИИСтройкерамика) по освоению производства изделий из порошковых масс изостатическим (гидро статическим) прессованием. Массы используют того же состава, что и при литье изделий. Порошок получают в распылительной сушилке