
книги / Технология строительной керамики
..pdf.лицовочных |
плиток являются светложгущиеся |
огнеупорные глины |
и каолины: |
Веселовская (марки ДЕИ и ДВ-0) |
и латненская (марки |
|1'"
1
»
_ 150
аб
.2
ЛТ*2) глины, черкасский бентонит, глуховецкий каолин мокрого обо гащения или просяновский каолин бухого обогащения, а также каолины — положений, новоселицкий, владимировский и др.
Рис. 80. Встроенные де тали:
а* б, о — плитки для мыль ниц; г, д — кронштейны; е — бумагодержатель для туале* та; ж — плитки для спичек.
В качестве отощающих добавок в массу вводят кварцевый песок Водолажского месторождения, политой и утельный, бой изделий, обожженный каолин, бой шамота, пирофиллит и др.
Иногда в массу вводят плавни чаще всего в виде полевого шпа та или пегматита, талька, нефелин-сиенита, перлита и реже известня ка (мраморной муки, мела, частично доломита) и др. В качестве элек
тролитов |
используют |
кальцинированную |
соду |
и жидкое стекло. |
||||
С о с т а в ы |
м а с с . |
Масса для фаянсовых облицовочных плиток содер |
||||||
жит около |
50% |
глинистых материалов (каолин, |
глина, |
бентонит), |
||||
10—25% кварцевого песка и до 35% боя изделий. |
|
|||||||
Таблица |
23. |
Шихтовые составы масс (двухкратный обжиг в туннельных печах), % |
||||||
|
|
|
|
|
|
Состав, % |
|
|
|
Компоненты |
|
|
|
|
|
|
|
|
|
|
|
1 |
2 |
3 |
4 |
5 |
Новоселовская глина |
|
|
|
|
|
|||
ДВ-1 |
|
|
|
27 |
21 |
30 |
31,4 |
25 |
ДВ-2 |
|
|
|
_ |
— |
— |
— |
— |
Латненская глина ЛТ-2 |
_ |
20 |
— |
|
— |
|||
Бентонит |
|
|
|
3 |
|
1 |
— |
3 |
Каолин просяновский |
20 |
10 |
30 |
25,7 |
24 |
|||
сырой |
|
|
|
|
|
|||
Кварцевый песок |
|
|
|
13 |
|
|
||
люберецкий |
|
— |
— |
— |
— |
|||
водолажский |
|
10 |
— |
— |
— |
— |
||
авдеевский |
|
— |
21 |
— |
— |
—> |
||
глуховецкий |
|
— |
— |
18 |
16,3 |
11 |
||
Бой |
|
|
|
22 |
15 |
|
26,6 |
25 |
политой и утельный |
— |
|||||||
шамота |
|
|
18 |
10 |
— |
— . |
12 |
|
Мел |
|
|
|
3 |
3 |
_ |
0,15 |
1 |
Сода |
|
|
|
0,1 |
0,1 |
0,3 |
0,2 |
|
Жидкое стекло |
|
0,35 |
0,4 |
0,2 |
0,2 |
0,35 |
Примерные составы масс, применяемые на заводах при двухкрат ном обжиге плиток, приведены в табл. 23. Обычно в массу сверх 100% вводят кальцинированную соду (0,1%) и жидкое стекло (0,2—0,4%).
Малоусадочные массы содержат пониженное количество глинистых материалов и повышенное количество отощающих добавок — шамота (капсельный бой) и отходов полуфабриката.
Составы масс по данным НИИСтройкерамики для плиток, обжигае мых по скоростным режимам в многоканальных роликовых печах, приведены в табл. 24.
Составы масс с небольшим содержанием пластичных компонен тов и низкой воздушной и огневой усадкой должны быть малочувстви тельны к резкому повышению температуры. Массы и глазури должны содержать минимальное количество свободной S i0 2 (до 20%) и иметь высокую теплопередачу.
При расчете состава масс для скоростного обжига учитывают, что скорость нагрева возрастает в 15—20 раз, в результате чего усадка массы смещается на 80— 100Q С в область более высоких температур,
а ее абсолютная величина уменьшается на 0,8—0,9%. При этом сни-
жается вязкость расплава вследствие меньшего насыщения его А120з, Si02 и другими тугоплавкими компонентами, уменьшается содержа ние муллита в стеклофазе, увеличивается разница в кинетике усадки внешних и внутренних слоев изделия.
При современном скоростном обжиге плиток ввод в массу обыч ных плавней (полевого шпата, пегматита, талька) неэффективен из-за малого времени протекания процессов при пониженных температурах
Таблица 24. Шихтовые составы масс (при скоростном обжиге в щелевых печах)
|
Материал |
1 |
2 |
3 |
4 |
5 |
6 |
7 |
Глина |
|
— |
33 |
28 |
21 |
30 |
— |
28 |
Веселовская |
||||||||
латненская |
— |
— |
— |
20 |
— |
— |
— |
|
тулунская |
— |
— |
— |
— |
— |
10 |
— |
|
трошковская |
— |
— |
— |
— |
— |
30 |
|
|
обожженная |
— |
— |
— |
— |
— |
26 |
— |
|
Каолин |
|
|
|
|
|
|
|
|
просяновский |
— |
— |
14 |
10 |
— |
— |
14 |
|
сырой |
||||||||
обожженный |
— |
— |
11 |
— |
— |
— |
12 |
|
ангренский |
70 |
— |
— |
— |
— |
— |
— |
|
глуховецкий |
— |
14 |
— |
— |
— |
— |
— |
|
Песок |
кварцевый |
— |
17 |
28 |
21 |
15 |
10 |
28 |
Бентонит |
4 |
— |
— |
— |
— |
— |
— |
|
Бой |
|
— |
8 |
7 |
15 |
— |
14 |
7 |
плиточный |
||||||||
капсельный |
26 |
16 |
— |
10 |
— |
— |
— |
|
Эрклез |
|
— |
— |
11 |
— |
— |
— |
11 |
Шлак |
|
— |
— |
— |
— |
55 |
— |
— |
Тальк онотский |
— |
— |
— |
— |
— |
10 |
— |
|
Пегматит |
— |
4 |
— |
— |
— |
— |
*— |
|
Стеклобой |
— |
6 |
— |
— |
— |
— |
— |
|
Мел |
|
— |
2 |
— |
3 |
— |
— |
— |
Сверх |
100% |
0,1 |
0,15 |
0,1 |
0,2 |
0,24 |
— |
0,1 |
Сода |
кальцинированная |
|||||||
Жидкое стекло |
0,2 |
0,3 |
0,1 |
0,5 |
0,6 |
— |
0,1 |
|
Пирофосфат натрия |
|
™* |
|
|
0,06 |
0,22 |
|
обжига. Поэтому в качестве плавней вводят нефелин-сиенит, перлит, шлаки, мел и др.
Нефелиновый сиенит — горная порода, содержащая, %: 22,8 не фелина Na [Al2S i04]; 54,8 полевых шпатов; 17,2 пироксена, амфиболов и биотита; 3,3 магнетита, аппатита и титанита; 2,4 прочих минералов.
Перлиты — породы вулканического происхождения. Они содержат от 85 до 96% стекловидной фазы, которая включает более 1% воды. Остальная часть (15—4%) содержит плагиоклаз, пироксен, кварц, биотит, рудничные минералы и др.
Комплексный ввод плавней, состоящих из щелочесодержащих материалов (перлит или нефелин-сиенит) и материалов, содержащих щелочноземельные оксиды (мел, тальк, магнезит, металлургические шлаки и др.), позволяет снизить общее содержание плавней в массе на 10— 15%, при пониженных температурах обжига.
При однократном обжиге требуется повышенная прочность и со противляемость размоканию высушенных плиток. В массах, содер жащих более 50% глинистых компонентов (каолин, глина, бентонит), эти показатели регулируют главным образом глинистой составляющей, пластифицирующими добавками (бентонитом, поверхностно-активными веществами и др.), тонкостью помола отощающих материалов, темпе ратурой и продолжительностью сушки.
Для уменьшения усадки плиток при однократном обжиге уменьшают содержание глинистых минералов и карбонатов в массах, увеличивают содержание обожженного каоли
Таблица 25.* |
Шихтовые составы масс |
на или шамота. Для снижения |
||||||||
(однократный обжиг) |
|
|
|
температуры обжига до |
960— |
|||||
|
|
|
|
|
|
1080° С в массы вводят больше |
||||
Компоненты |
1 |
2 |
3 |
4 |
плавней — нефелин-сиенита, пер |
|||||
|
|
|
|
|
|
лита. Составы масс в производст |
||||
Глина |
|
28 |
26 |
28 |
25 |
ве плиток однократного обжига |
||||
|
приведены в табл. 25. |
|
|
|||||||
Бентонит |
3 |
3 |
— |
— |
|
|
||||
Введение бентонита позволяет |
||||||||||
Каолин |
от |
20 |
23 |
20 |
25 |
|||||
мученный |
уменьшить |
количество |
глинис |
|||||||
Каолин |
обо |
17 |
|
20 |
|
тых компонентов на 3— 15% или |
||||
жженный |
|
|
полностью заменить их. Влияние |
|||||||
Песок |
квар |
|
|
|
|
|||||
22 |
10 |
23 |
15 |
бентонита |
проявляется |
в |
боль |
|||
цевый |
(бой |
|||||||||
Череп |
|
15 |
9 |
35 |
шей мере при одновременном вво |
|||||
плиток) |
12 |
де в массу |
(сверх 100%) |
барды |
||||||
Шамот |
(бой |
_ |
22 |
___ |
_ |
(0,5%). Повышению водоустойчи |
||||
капсельный) |
||||||||||
Мел |
(сверх |
— |
|
3 |
2 |
вости сухих плиток более чем в |
||||
100%) |
|
— |
2 раза также способствует ввод в |
|||||||
|
|
|
|
|
|
массу фосфата натрия (Na3P 0 4) |
||||
|
|
|
|
|
|
при наличии бентонита. |
|
|
При вводе в массу обожженного каолина (до 26—27%) снижается брак плиток при сушке и обжиге, улучшаются термические свойства плиток. Однако получение и помол каолина весьма трудоемкие про цессы, поэтому его заменяют в массе шамотом — измельченным капсельным боем. Для этого в состав капсельноймассы вводят 10— 15% сырого новоселицкого и положского каолина.
Замена части кварцевого песка шамотом позволяет повысить теп лопроводность и уменьшить термическое расширение при обжиге, повысить термостойкость плиток и снизить брак, вызванный появле нием мелких трещин.
При использовании фаянсового боя водопоглощение его должно быть не более водопоглощения обожженного каолина — 16%.
Пирофиллит, как и тальк, несколько снижает набухание плиток в процессе эксплуатации, хотя полностью не устраняет этого явле ния. Кроме того, пирофиллит, введенный в массу (до 10%), повышает сопротивляемость изделий растрескиванию (образованию цека гла зури). Волластонит повышает блеск глазури, не образует пузырей, наколов, отслаивания глазури и др. При вводе в массу до 40% волластонита снижается усадка плиток при сушке и обжиге, повышается прочность высушенных плиток до 2—2,7 МПа, снижается коэффициент
т
термического расширения, увеличивается максимально допустимая скорость обжига.
Подготовка массы (пресс-порошков). В производстве фаянсовых облицовочных плиток пресс-порошки готовят мокрым (шликерным) или сухим способами.
Более прогрессивной является технология шликерной подготовки масс с обезвоживанием суспензии массы в распылительных сушилках. Ее широко применяют на отечественных заводах и за рубежом. Помол компонентов массы осуществляют чаще всего раздельно, но на неко торых заводах применяется и совместный помол глинистых и каменис тых (отощающих плавней) материалов в шаровых мельницах мокрого помола. При раздельном помоле сырьевых материалов и различных вариантах тонкого помола добавок и обезвоживания суспензий применя ются такие примерные схемы подготовки пресс-порошка шликерным
способом (см. |
стр. 186). |
Р о с п у с к |
г л и н и с т ы х м а т е р и а л о в (каолина, глины, |
бентонита) при раздельном помоле осуществляют в мешалках верти кальных или горизонтальных, установках непрерывного действия и реже в шаровых мельницах. Порядок загрузки мешалок следую щий: сначала подают воду, затем включают пар и далее загружают каолин, глину, бентонит (при работающей мешалке). Воду добавляют из расчета, что при влажности суспензии 65—72% обеспечивается
быстрый роспуск глинистых материалов до |
величины |
частичек |
3— 10 мкм. Ускорению роспуска способствует |
подогрев |
суспензии |
до 45—559 С, для чего в мешалку подают пар под давлением 0,15— 0,25 МПа, а также вводят в массу поверхностно-активные вещества (ПАВ) (до 1% сульфитно-спиртовой барды), кубовые и дрожжевые остатки, триполифосфат натрия Na5P3OI0 и др.
Действуя как разжижители, ПАВ повышают текучесть суспензии при меньшей влажности, что улучшает условия транспортирования, ситовой и магнитной сепарации, а также повышают стабилизацию суспензии.
Продолжительность роспуска глинистых материалов в шаровой мельнице от 40—50 мин до 1,5—2,5 ч при соотношении материал — мелющие тела — вода, равном 1 : 0,5 : 1,5.
Готовность глинистой суспензии определяют, пропуская ее через вибросито с латунной сеткой с 3460 отв/сма (проход без остатка).
Т о н к и й п о м о л к а м е н и с т ы х м а т е р и а л о в осу ществляют в шаровых мельницах мокрого помола. На него приходится до 60—65% общего расхода электроэнергии, необходимой для подго товки пресс-порошка.
Шаровые мельницы футеруют кремневыми и реже фарфоровыми плитами. Толщина кремневых плит 75— 100 мм. Срок службы плит до 20 тыс. ч работы мельницы. С применением плит и кремневых или уралитовых мелющих тел масса не загрязняется железом. Износ крем невых шаров составляет 0,5—2% массы размалываемых материалов. Размеры мелющих тел от 30 до 90 мм. Шары диаметром менее 30 мм удаляют из мельницы. Для компенсации мелющих тел при каждой загрузке мельницы добавляют около 90 кг шаров.
Ф |
Ф |
Глина, |
Каолин |
бентонит |
|
I |
|
Сортировка |
Сортировка |
Ф |
Измельчение (вал* |
Измельчение до |
|
30 мм (стругач) |
новая дробилка) |
Электроочистка |
Электроочистка |
||
(подвесные |
(подвесные |
||
электромагниты) |
электромагниты) |
||
|
Ф |
Ф |
|
Хранение (бункер) |
Хранение (бункер) |
||
|
Ф |
Ф |
|
Дозирование |
Дозирование |
||
|
(весы) |
(весы) |
|
Вода |
|
_______________ |
|
I |
4 |
I |
|
* |
4 |
Пар |
|
Роспуск |
(мешалка, |
шаровая мельница)
Процеживание
(вибросито)
Электромагнитная сепара ция (магниты, феррофильтр)
Ф
Ф
Полевой; шпат или его заменители
I
4
Обжиг (печь)
Ф
Сортировка
(конвейер)
Промывка (моечный барабан)
Ф
Дробление (щековая, молотко вая дробилка)
Электроочистка
(подвесные
электромагниты)
Ф
Хранение (бункер)
Дозирование
(весы)
4___________
I
4
I вариант Сухой помол (струйная мельница)
Ф
Хранение (расходный бункер)
Ф
Дозирование (автоматические весы)
Ф
|
Ф |
Кварцевый |
Бой |
||
(череп) |
песок |
|
|
Ф |
гг * |
Сортировка |
Просев |
|
(конвейер) |
(вибросито) |
|
|
Ф |
|
Промывка |
|
|
(моечный барабан) |
|
|
„ |
Ф |
|
Дробление |
|
|
(щековая, молотко |
|
|
вая дробилка) |
4 |
|
|
Ф |
|
Электроочистка |
Электроочистка |
|
(подвесные |
(подвесные |
|
электромагниты) |
электромагниты)' |
|
|
Ф |
Ф |
Хранение (бункер) |
Хранение (бункер) |
|
Дозирование |
Дозирование |
|
(весы) |
(весы) |
|
|
I |
I |
|
* |
___________ 4__________ |
|
i |
|
I1 |
4 |
+ |
вариант |
Мокрый помол (шаровая мельница)
Процеживание
(вибросито)
Ф
Электромагнитная сепарация (магниты, феррофильтр)
Ф
Ф
Добавочные
материалы
(электролиты, сульфат кобальта
и др.)
Ф
Дозирование
(весы)
I
______+
'Вода
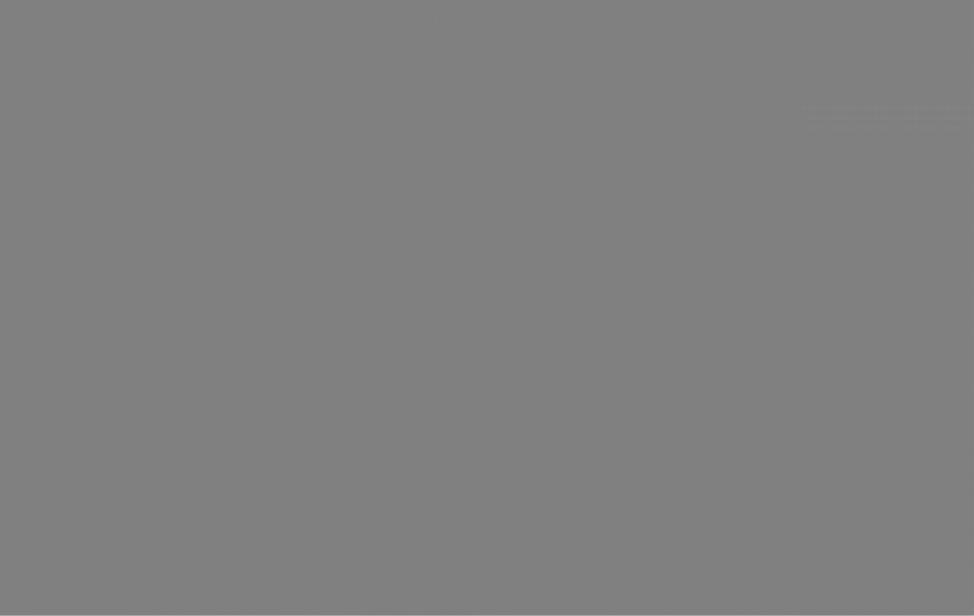
Весовое соотношение материала мелющих тел и воды 1 1,25 -г 1,5 : 1. Число оборотов шаровой мельницы зависит от ее размеров
|
Q C |
Л П |
I |
Г |
и находится в пределах от |
(по Андреасену) до |
|
(НИИСтрой кера |
мика) в минуту. Число оборотов барабана мельницы можно рассчитать по формуле:
п — - р - (5ф -+- 2),
где D — внутренний диаметр барабана; <р — коэффициент загрузки
(0,45—0,40).
Мелющие тела размалывают материал в результате соударений шаров (97—98%) и частично истиранием (3—2%). При малых оборо тах барабана мельницы помол происходит истиранием материала меж ду мелющими телами. Он малоэффективен, так как при этом сильно изнашивается футеровка. При частоте вращения выще «критической» (нормальная окружная скорость 90— 120 м/мин) содержимое мельницы прижимается центробежной силой к стенкам барабана и помол мате риала прекращается. Производительность шаровых мельниц повышает ся с увеличением скорости вращения барабана, но не более 70% кри тической.
К.IT . д. шаровых мельниц всего около 1 %, так как установлено
(М. А. Ребиндер, Г. С. Ходаков и др.), что только один из тысячи уда ров шара приводит к разделению частичек материала, энергия осталь ных ударов теряется на деформацию и нагрев материала и др.
Порядок загрузки мельницы прираздельном помоле следующий: сначала загружают кварцевый песок, затем шамот, глину до 7% или весь бентонит, после чего заливают воду из расчета влажности отощающих 58—60%, а затем после помола в течение 3—6 ч добавля ют бой.
При раздельном помоле мембранными насосами подают в сборную мешалку сначала приготовленную глинистую суспензию, а затем отощающие материалы.
При совместном помоле сырьевых материалов роспуск глинистых совмещают с помолом отощающих в шаровых мельницах. При этом сначала загружают каменистые материалы и около 5% глины или весь бентонит, если его вводят в массу. После 3,5—5,5 ч помола за гружают все глинистые материалы (глину и каолин) и электролиты (сода — 0,1% и жидкое стекло 0,2—0,35%). Продолжают совместный помол около 1 ч. Размолотые материалы пропускают через вибросито (400 отв/см2), электромагниты и подают в пропеллерные мешалки для промежуточного хранения. Тонина помола материалов массы харак теризуется остатком на сите 10 000 отв/см2 не более 5—6%. Суспензия в сборных мешалках имеет влажность 45—47% и находится в постоян ном движении, что препятствует его расслоению.
Ускорению размола способствуют добавки ПАВ, а также использо вание высокоглиноземистых (уралитовых), циркониевых и других высокопрочных мелющих тел. Действие ПАВ заключается в понижении твердости каменистых материалов, пептизации (разжижении) и стаби лизации суспензий.
Уралитовые мелющие телагцилиндрической (диаметр 30 мм и высота» 35—40 мм) или шаровидной (диаметр 35—40' мм) формы изготовляют из высокоглиноземистой-массы, (глинозема— 62,8%, глины— 30%г доломита.— 7,2%) и обжигают; при 1400— 1450° С. Водопоглощение уралитовых мелющих тел 0,03%, Уралитовые шары имеют плотность 3,6—3,7 г/см3, что увеличивает силу удара и ускоряет помол материала.
Уралитовые мелющие тела стойкие против износа. Если износ кремневых шаров составляет 0,5—2% массы размалываемых .материа лов, то уралитовых. только. 0,2:—0*25%,
Использование уралитовых.мелющих тел,.имеющих большую мае-, су и суммарную поверхность соприкосновения с размалываемым ма териалом, ускоряет размол более чем в 1,5 раза по сравнению с крем невыми шарами при меньшем износе — 0,25%^. что сокращает расход электроэнергии более чем в 2 раза.
При б и т о в о й' о ч и с т к е (просев и процеживание) отделяются посторонние примеси (корни), крупные частички материалов, частично улавливаются слюда и-аппаратное железо. Кроме того, ситовуюсепа
рацию используют для контроля |
степени' помола |
материалов массы |
и глазури. Наиболее тонкие сита, |
применяемые для процеживания |
|
керамических суспензий, шликеров и глазурей, |
характеризуются |
01, 008, 0063 (ГОСТ 3584—53). В промышленности, наряду с плоскими грохотами — вибраторами, широко применяют сита, K/VS (ГДР), фирмы Боултон (Англия), СМ-487А конструкции Харьковского ЦКБ, переносные вибросита ударного действия и др. Производительность сита до 12 т/ч. Конструкция многих типов сит предусматривает самоочистку, что является их большим преимуществом. Хорошо зареко мендовали себя, в работе вертикальные вибрационные сита с двойными полотнами (деками) с самоочисткой,. производительностью до 12. т/ч. Сетки сит изготовляют из фосфористой бронзы, хромоникелевой стали,, нейлона. Для процеживания жидких шликеров применяются сита с- размером ячеек.60 мкм, густых шликеров— не менее 200 мкм.
Снижение влажности суспензии до 39—40% улучшает качество» порошка и плиток, повышает экономичность работы распылительной сушилки.
Однако при снижении влажности шликера понижается его теку честь и соответственно увеличивается время слива суспензии в шаро вой мельнице, а; также резко снижается производительность вибросит. На' Львовском керамическом заводе внедрено гидроциклонное (кроме вибросит) обогащение суспензий по схеме, приведенной на рис, 81.
Сливаемая из шаровой мельницы суспензия под давлением 0,8— 0,15 МПа подается в четыре параллельно подключенных гидроциклона диаметром 50 мм. Основная часть суспензии в результате обработки в гидроциклонах тонкодисперсная. Незначительное количество (около 0,01 %) легких примесей после удаления при пропускании через вибро сито с сеткой 900 отв/см8 также подается, в бассейн. Предварительное удаление примесей а помощью гидроциклонов обеспечивает высокую производительность вибросит.
Снижение влажности шликера позволяет уменьшить удельный расход тепла на приготовление пресс-порошка. Обогащение шликера
пониженной влажности в гидроциклонах сокращает время слива ша ровых мельниц в 1,2 раза по сравнению со сливом шликера влаж ностью 47— 48% непосредственно через вибросита, способствует эко номии латунной сетки, электроэнергии, трудовых затрат, повышает коэффициент полезного действия сушилки до 90% против 30—70%
обычных |
сушильных |
установок. |
М а г |
н и т н а я |
с е п а р а ц и я способствует снижению содер |
жания в массе красящих оксидов (железа, титана). Магнитная сепара ция основана на взаимодействии двух факторов: магнитной силы при тяжения и сопротивления частичек минералов, обусловленного тре-
Рис. 81. Схема гидроциклонного обогащения суспензии:
1 — ш аровая |
мельница; |
2 — вибросито; |
3 |
— бассейн; 4 — |
пропеллерная |
мешалка; |
5 — мембранный |
насос; 6 — маг |
|
нитный сепаратор; 7 — распылительная |
сушилка; 8 — гид- |
|||
роцнклон. |
|
|
|
7 |
нием частичек друг о друга, вязкостью жидкой среды, скоростью потока суспензии и магнитной восприимчивостью частичек.
В зависимости от магнитной восприимчивости |
(проницаемости) |
минералы, встречающиеся в керамическом сырье, |
разделяются на |
ферромагнитные (железо — 100,0, магнетит — 40,18 |
и др.), парамаг |
нитные (слабомагнитные — сидерит — 1,82, гематит — 1,32, циркон — 1,061, корунд — 0,83 и др.) и диамагнитные (немагнитные — гра нит— 0,40, кварц и рутил— 0,37, пирит— 0,23, доломит— 0,22 и др.).
В то время как ферромагнитные вещества могут быть отделены в слабомагнитном поле с напряженностью до 79,6 кА/м, для парамагнит ных материалов требуются сепараторы с напряженностью поля до 1800 кА/м с замкнутыми магнитными системами. Основными типами сепараторов для магнитной очистки сухих предварительно измельчен ных минералов (размер зерна 0,05—3 мм при влажности не более 1%) с сильным магнитным полем являются индукционные вальцевые, барабанные с крестовидным магнитом и дисковые.
В керамической промышленности получили распространение ин дукционные вальцевые одно-и двухступенчатые сепараторы с высокой напряженностью поля. Опыт использования таких сепараторов под тверждает возможность снижения содержания железа в полевом шпате в 5—7 раз.
Сухая магнитная сепарация пегматита при однократном про пуске через магнитный сепаратор СМ-2 снижает на 0,15—0,2% содер*