
книги / Технология строительной керамики
..pdfПовышенное содержание свободного кремнезема указывает на наличие относительно большого количества песка в глинистом сырье, повышен ную пористость черепка и меньшую механическую прочность. Такое сырье мало или совсем непригодно для изготовления изделий сложного
профиля. |
, |
Для глин с повышенным содержанием глинозема |
(А120 3) требует |
ся более высокая температура обжига, при значительном интервале
между температурой начала спекания |
|
|
|
|||||
и плавления, что облегчает процесс |
|
|
|
|||||
обжига изделий, так как уменьшается |
|
|
|
|||||
возможность деформации (подвара) из |
|
|
|
|||||
делий. При пониженном содержании |
|
|
|
|||||
глинозема прочность изделий снижает |
|
|
|
|||||
ся. |
Для |
производства тонкостенных |
|
|
|
|||
многопустотных |
камней содержание |
|
|
|
||||
глинозема в глинах должно быть от 13 |
|
|
|
|||||
до 20%, |
кремнезема — от 50 до 75%. |
|
|
|
||||
При меньшем содержании глинозема |
|
|
|
|||||
сырье |
необходимо |
перерабатывать |
|
|
|
|||
тщательнее. |
|
|
|
|
|
|||
Оксиды железа встречаются в гли |
|
|
|
|||||
нах в виде окисных соединений (гема |
Рис. 24. Области расположения глин |
|||||||
тит, гидроксиды и др.), закисных (си |
||||||||
в зависимости от химического соста |
||||||||
дерит, анкирит, пирит |
и др.), закись- |
ва (по А. И. Августинику): |
||||||
окисных (магнетит, глауконит) и т. д. |
1 — глины для тонкой |
керамики и ог |
||||||
Они |
являются |
сильными плавнями, |
неупорных (шамотных) |
изделий; 2 — |
||||
глины для канализационных труб, пли |
||||||||
способствующими уменьшению темпе |
ток полов, каменных изделий; 3 — гли |
|||||||
ны для гончарных изделий; |
4 — глины |
|||||||
ратурного интервала спекания глины |
для черепицы; 5 — глины |
для строи |
||||||
и делают ее короткоплавкой (кроме |
тельного кирпича; 6 — глины для клин |
|||||||
керного кирпича. |
|
|
ферросиликатов). Изменяя печную сре ду от окислительной до восстановительной (на конечной стадии об
жига), можно в большей степени выявить действие железистых соеди нений как плавней. Эти соединения придают окраску изделиям после обжига от светло-кремовой до вишнево-красной в зависимости от содержания их в глине.
Сульфиды в легкоплавких глинах представлены главным образом пиритом (FeS) и марказитом (FeS2).
Оксиды кальция входят в состав глинистых материалов в виде из вестняков (СаС03), доломитов (CaMg (С03)2), сульфатов (CaSO^ и дру гих минералов. Будучи равномерно распределенными в глине и нахо дясь в тонкодисперсном состоянии, оксиды кальция уменьшают свя зывающую способность и понижают температуру плавления глины, делая ее короткоплавкой и затрудняя обжиг изделий из-за возможности подваров. При содержании в глине около 10% СаС03 она имеет ин тервал спекания 30—40° С. Интервал плавления глины может быть в таких случаях увеличен добавлением кварцевого песка. }
При температуре обжига изделий до 1000° С |
действие известня |
ка проявляется главным образом в изменении |
пористости и проч |
ности изделий и меньше как плавня. В результате диссоциации оксида
углерода пористость черепка изделий повышается при одновременном снижении прочности. Значительное содержание оксида кальция спо собствует осветлению изделий (кремовая, желтая окраска) даже в при сутствии оксидов железа. Так, при соотношении Fe20 3 к СаО не менее 0,4 цвет черепка после обжига светло-розовый, при 0,3 — желтый, при 0,2 — светло-желтый. Глины, содержащие известковые включения в ви де конкреций, должны быть очень тонко помолоты (величина частиц < 0,6 мм), а еще лучше подготовлены шликерным способом, гаранти рующим полное удаление включений.
Оксид магния (MgO) как плавень действует аналогично СаО, толь ко меньше влияет на интервал спекания глин.
Оксиды щелочных металлов (Na20 , К20) являются сильными плав- ■нями, способствуют повышению усадки, понижению температуры •образования расплава, уплотнению черепка изделий и повышению его прочности.
Наличие в глинистом сырье растворимых солей (до 1,5%) суль фатов и хлоридов натрия, магния, кальция, железа вызывает выцветы (белые налеты) на поверхности изделий, что не только портит внешний вид, но и способствует разрушению поверхностного слоя изделий.
Органические вещества всегда встречаются в легкоплавких глинах (до 15%). Крупные включения (корни и др.) удаляются при переработ ке глины, остальные выгорают при обжиге.
' Гранулометрический состав глинистого сырья характеризуется большим разнообразием:
Размер частиц
Менее 5 мкм |
8—60% |
5—50 мкм |
6—55% |
50—250 мкм |
1—22% |
Более 1000 мкм |
10% |
Кглинистой части относят фракции с размером частиц менее 5 мкм,
кпылеватой — от 5 до 50 мкм, к песчаной — от 50 мкм до 2 мм.
Для тонкостенных и крупноразмерных керамических камней с<> держание фракций меньше 2 мкм должно быть не ниже 24%, а для улучшения сушильных свойств — не выше 50%. Содержание фракций размером 2—20 мкм должно быть 30—47%. Увеличение размеров фрак ций до 10—20 мкм способствует лучшему уплотнению массы и повы шению прочности изделий. Содержание фракций размером более 20 мкм допускается в пределах 6—34%. Крупных фракций, в том числе и добавочных материалов, не должно быть более 2 мм в поперечнике.
Гранулометрический состав легкоплавких глин тесно связан с минералогическим составом. Частицы крупнее 10 мкм представлены главным образом остатками первичных минералов (кварц, полевой шпат, слюда и др.). Фракции 10—5 мкм представлены как в виде ос татков первичных минералов, так и в малых количествах вторичных; частицы менее 5 мкм в большинстве состоят из глинистых (каолинит, монтмориллонит) и других минералов вторичных образований.
С повышением дисперсности глин содержание S i0 2 увеличивается (пылевидные фракции). Далее количество его уменьшается за счет увеличения содержания А120 3 и Fe20 3. Частицы глины менее 1 мкм при
дальнейшем их разделении содержат А120 3 и Fe20 3 почти одно и то же количество. В более тонких фракциях повышается содержание Fe20 3, К20 и гумусовых веществ за счет уменьшения содержания СаО и Na20 . Глины, у которых глинистое вещество представлено минералами монтмориллонитовой группы, более тонкодисперсны, чем каолинитовые.
Частицы размером менее 5 мкм составляют глинистое вещество и определяют основные свойства глинистого сырья. Повышенное содержание частиц размером менее 5 мкм придает глинам повышенную сопротивляемость размоканию
в воде, высокую |
пластичность |
Таблица 5. Характеристика глин |
|
||||||
и чувствительность к сушке, |
|
||||||||
увеличивает воздушную и об |
|
Содержание частиц, % |
|||||||
щую усадку. При |
таких гли |
Материал |
|
пылевидных |
|||||
нах обычно вводят отощающие |
глинистых |
||||||||
|
и песчаных |
||||||||
|
(менее 5 мкм) |
||||||||
материалы — песок, шамот и |
|
|
(более 5 мкм) |
||||||
др. |
Содержание |
глинистого |
Тяжелая глина |
Свыше 60 |
40 |
||||
вещества в сырье для керами |
|||||||||
ческих камней должно быть не |
Глина |
60—30 |
40—70 |
||||||
Суглинок |
30—20 |
70-80 |
|||||||
менее 30%. Повышенное со |
тяжелый |
||||||||
держание |
пылевидной фрак |
средний |
20—15 |
80—85 |
|||||
ции |
в глинах |
повышает |
их |
мягкий |
15—10 |
85—90 |
|||
чувствительность |
к сушке |
и |
Супесь |
10—5 |
90—95 |
||||
обжигу, |
снижает |
прочность |
|
|
|
||||
изделий. |
|
|
|
|
|
|
|
Характеристика глинистого сырья в зависимости от содержания пылевидных фракций, песка и глинистых частиц приведена в табл. 5.
Лессы, лессовидные глины и суглинки представляют собой раз новидность глинистого сырья, в котором пылевидная фракция пред ставлена главным образом кремнеземом, карбонатом кальция, ок сидами железа. Микроструктура лессовидных пород (зернистая, агре гативная и агрегативно-зернистая) зависит от гранулометрического и химико-минералогического составов. Лессы всегда содержат глину, располагающуюся тонкой пленкой (2—30 мкм) на поверхности зерен. Лессы, глинистая часть которых представлена каолинитом, имеют зернистую структуру. Они обладают высокой пористостью, малой объемной массой, легко распадаются в воде. Лессы, глинистая часть которых представлена монтмориллонитом, имеют агрегативную струк туру и реже агрегативно-зернистую. Толщина глинистой пленки 2 — 10 мкм. Микроагрегаты размером 500—5 мкм более водостойки. Лессы, у которых в глинистой части преобладает слюда, а также содержится каолинит и монтмориллонит, имеют как зернистую, так и агрегативно зернистую структуру. Глинистые минералы и оксиды железа входят
в состав лесса |
в тонких фракциях — 5— 1 мкм. |
|
|
|
Естественная |
влажность лессов и лессовидных |
глин — от |
б до |
|
12%, |
обычных глин, суглинков и супесей — до 18, |
ленточных |
зыб |
|
ких |
глин — до |
35%. |
|
|
Глинистые материалы имеют значительные колебания объемной массы (1100—2000 кг/м8), теплопроводности (0,2326—0,8141 Вт/ (м X X РС), теплоемкости (0,7536—0,9211 кДж/(кг °С) и других показателей.
Глинистые материалы для кирпича и керамических камней должны иметь хорошую формуемость (число пластичности — не менее 7), обес печивать сушку и обжиг полуфабрикатов без деформаций и трещин, иметь воздушную усадку не более 6% для тощих глин, б— 10% — для глин средней пластичности и более 10% — для высокопластичных глин (число пластичности 15—25), обеспечивать после обжига достаточную пористость и другие свойства изделий (согласно требованиям ГОСТа).
Добавочные материалы. В производстве изделий стеновой керамики глинистое сырье сравнительно редко используется в чистом виде, чаще его используют совместно с различными добавочными материалами, которые разделяют на:
улучшающие формовочные свойства массы (высокопластичная гли на, поверхностно-активные вещества);
улучшающие условия обжига (золы ТЭС, шлаки, уголь); улучшающие сушильные свойства (шамот, песок, дегидратирован
ная глина, опилки); повышающие прочность и морозостойкость (бой стекла, пиритные
-огарки, железная руда); специального назначения, которые улучшают цвет изделий, предот
вращают выцветы, нейтрализуют вредное влияние природных вклю чений, имеющихся в глинах (красители, жидкое стекло и др.).
Отощающие добавки не должны содержать крупных частиц (более 2 мм), а содержание частиц размером менее 0,25 мм не должно превы
шать 20%. Фракций размером 0,3— 1 мм должно быть около 60%. Луч ше, если поверхность зерен отощителя шероховатая, а форма — не правильная. Использование мелкозернистого песка с повышенным со держанием пылевидных фракций может увеличить способность массы к расслоению. При вводе более 25% песка снижается марка изделий, повышается их хрупкость, а иногда и трещиноватость. При вводе в
глины пониженной пластичности более 18—20% опилок прочность изделий снижается. Разувлажняющие материалы (молотый бой сырца, предварительно высушенная глина, дегидратированная глина и др.) добавляют для понижения естественной влажности изделий. Количество вводимых выгорающих добавок зависит от их калорийности и состав ляет 60—80% количества топлива, необходимого для обжига.
В настоящее время большое внимание уделяется более широкому использованию в производстве строительной керамики отходов других производств — шлаков и зол ТЭЦ и ТЭС, годовой выход которых в стра не составляет более 70 млн. т (использование их не превышает 10%). Кроме того, ежегодно образуется до 150 млн. т отходов добычи и обо гащения твердых горючих ископаемых. Использование зол, шлаков, отходов углеобогащения позволяет сократить расход топлива на про изводство кирпича. Так, при вводе в шихту 15% золы почти полностью исключается ввод топлива (примерно 2—33% необходимого для об жига).
Такие добавки (BaC03, NaCl и др.) вводят в массы для борьбы о вредным влиянием известковых включений (дутика), борьбы с выцвета ми на поверхности изделий и улучшения других физико-технических свойств масс и изделий.
§ 3. ПЕРЕРАБОТКА СЫРЬЯ И ПОДГОТОВКА МАСС (ПРЕСС-ПОРОШКОВ)
Технологические схемы производства. Свойства сырья, тип изделий, объем производства, способы подготовки сырьевых материалов опре деляют общие принципы технологических схем производства изде лий. Способы переработки сырья и подготовки массы — пластический, полусухой или шликерный — наиболее полно определяют различия технологических схем производства изделий, так как последующие процессы — формование (прессование), сушка и обжиг изделий— не имеют существенного различия.
Технологическая схема производства изделий с п л а с т и ч е с к и м способом подготовки массы, несмотря на сложность и длитель ность, наиболее распространена в промышленности стеновой керами ки. Примерная технологическая схема подготовки массы пластическим способом при вводе опилок и отходов углеобогащения приведена ни же:
Отходы углеобогащения |
Опилки |
I |
I |
I |
I |
Ящичный питатель |
Сито---- |
Ленточный транспортер |
|
I |
|
Сушильный барабан |
|
I |
|
+ |
|
Ленточный транспортер |
|
1 |
|
Ротационная мельница |
|
I |
|
Элеватор |
|
1 |
|
Бункер |
|
I |
|
]• |
|
Ленточный питатель |
|
Глина
I
*
-►Ящичный питатель
I
I
-►Транспортер
1
Вальцы грубого помола
i
Глиномешалка двух-
вальная
II
Вальцы дырчатые
1
Транспортер
1
Вальцы тонкого помола
I
Пресс ленточный
i
Резательный автомат
I
I
Транспортер
i
Сушильные вагонетки
1
Туннельная сушилка
I
Туннельная печь
I
+
Склад готовой продукции
Включение в схему сушильного барабана объясняется необхо димостью подсушки отходов углеобогащения, влажность которых
в зимний период достигает 12— 15%. Иногда в схему подготовки от ходов в начале ее включаются дробилки типа СМ-218, С-599, МД-54.
Технологическая схема производства изделий с п о л у с у х и м способом переработки сырья и подготовки массы применяется в про изводстве обыкновенного и эффективного кирпича, пустотелых камней при полусухом прессовании изделий, при использовании глинистого сырья пониженной пластичности и влажности примерно следующая:
Карьер глины
I
Автосамосвал
I
Глинорыхлительная машина
I
I
Ящичный питатель
*
Конвейер
J
Дезинтеграторные вальцы
1
Конвейер
I
|
Сушильный |
барабан или |
---------Теплоноситель из |
|
шахтная |
мельница |
подтопка |
|
1 |
|
|
|
Элеватор |
|
|
------------ |
^-Бункер кусковой глины |
|
|
|
{ |
|
|
|
Дезинтегратор, роторная |
|
|
|
мельница или бегуны |
|
|
|
I |
|
|
Транспортер |
Элеватор |
|
|
|
Сита |
|
|
|
I |
|
|
|
Бункер порошка |
|
|
|
I |
|
|
|
I |
|
Вода (пар) |
|
Двухвальный смеситель |
I
Дезинтегра Прессы торные
вальцы
I
Конвейер (возврат На обжиг
брака)
Сравнивая технологические схемы производства с полусухим й пластическим способами подготовки массы (шихты), следует от метить, что почти при одинаковых показателях по энергоемкости
(соответственно 22 и 23 кВт установленной мощности на 1 млн. шт. условного кирпича) показатели металлоемкости заводов полусухо го прессования почти в 3 раза выше (соответственно 8,9 и 23,5 т техно логического оборудования на 1 млн. шт. условного кирпича), а тру доемкость изготовления 1 тыс. шт. кирпича на 26—30% ниже, чем при пластическом способе подготовки массы и формовании. Количество во ды, подлежащей удалению при полусухом способе, в 4 раза меньше, чем при пластическом, что значительно (на 26—20%) снижает расход условного технологического топлива. Полусухой способ подготовки сырья требует на 30% меньше производственных площадей (при одинаковой мощности заводов) и на 20—24% меньше обслуживающего персонала, чем пластический. Сокращается также продолжительность производства изделий, что создает лучшие условия для автоматизации производства.
Технологическую схему производства изделий со шликерным спо собом подготовки массы (жидкотекучее состояние) целесообразно при менять при использовании глинистого сырья повышенной влажности, которое легко размокает в воде и содержит каменистые включения, подлежащие удалению. Шликерный способ подготовки массы обеспе чивает наилучшее разрушение природной текстуры сырья. Основными технологическими переделами при шликерном способе подготовки массы являются:
Грубое измельчение
I
Г
Роспуск глины в воде
I
Г
Пропуск глинистой суспензии через решетку (сито) для отделения каменистых включений
II
Обезвоживание суспензии (в распылительных сушилках)
I
Проминка массы (при использовании распыли тельных сушилок—доувлажнение)
iI
Поступление массы па формование или полусухое прессование
Дозирование глинистых и добавочных компонентов массы и равномерная подача их на последующую переработку осуществляются ящичным питателем типа СМ-229, СМ-664, СМ-1090, СМК-78 (СМ-1091). Яшичные питатели не только дозируют, но и частично разрых ляют сырьевые материалы. Производительность питателей 25—35 м3/ч.
При использовании в производстве тяжелых комовых глин, а также при поступлении частично смерзшихся кусков над ящичным питателем устанавливают ножевой или роторный рыхлитель типа СМ-1031А производительностью до 25 м3/ч или виброрешетки.
Измельчение и тонкий помол. Сухие плотные глины с влажностью 8— 12% (или предварительно высушенные) измельчают на стругачах, дезинтеграторах, роторных и молотковых дробилках и бегунах.
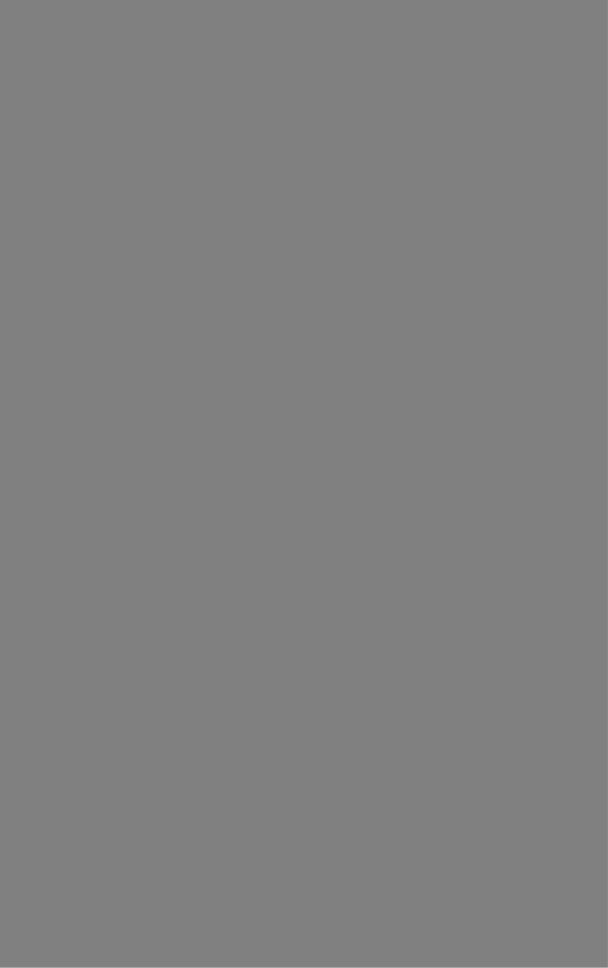
водительиость вальцов СМ-416А при скорости вращения валков 92,7 об/мин — до 40 м3/ч.
В камневыделительных дезинтеграторных вальцах (СМ-150) боль шой валок (диаметром 900 мм), со скоростью вращения до 60 об/мин, имеет гладкую поверхность, меньший валок (диаметром 600 мм), со скоростью вращения 600 об/мин, имеет на поверхности 6—8 стальных полос (бил), при помощи которых каменистые включения выбрасывают ся из глины или измельчаются, если попадают между валками. Зазор между поверхностью гладкого валка и выступающим (на 10— 12 мм) ножом не более 1—3 мм. Производительность вальцов — от 20 до
40м3/ч.
Увальцов грубого помола (СМ-1031А и др.) валки имеют различ
ную скорость вращения (один валок — 150, другой — 180 об/мин), что способствует лучшей переработке глины. Зазор между валками не должен превышать 7— 10 мм.
Лучшая переработка, в особенности зимой, достигается при соотноше нии размера комьев глины и щели между валками 4 : 1 и между диа метром валков и размером комьев глины 9 : 1 . Практически это до стигается установкой двух пар вальцов — грубого и тонкого помола.
В промышленности также применяют гладкие, дырчатые вальцы
СМ-369А. Валки их полые, |
имеют овальные |
отверстия размером |
7 X 22 мм конической формы |
(расширяющиеся |
внутрь валков), рас |
положенные в несколько рядов по ширине валков, через которые про давливается измельченная глина. Диаметр валков — 1 м, ширина —
0,64 м. Скорость |
вращения валка на подвижных |
подшипниках 20,8, |
|
на неподвижных — 30 об/мин. Производительность |
вальцов — до |
||
40 т/ч. Они в 1,5 |
раза производительнее, в 4 раза |
менее |
металлоемки |
и в 1,8 раза экономичнее по потреблению электроэнергии, чем бегуны. Дырчатые вальцы устанавливают посде двухвального смесителя.
Наибольшее разрушение природной текстуры глинистого сырья достигается на гладких вальцах тонкого помола. Валки вальцов (СМ-23, СМ-24, СМК-102, СМ-696А, СМ-1096) имеют индивидуальные приводы. Валки вращаются с различной скоростью, и материал, попавший между ними, раздавливается и растирается. Соотношение скоростей вращения валков обычно от 1— 1,2 до 1— 1,5. Разность ско ростей вращения валков вальцов должна обеспечить деформацию сдвига глины от 5 до 15 см (в среднем 7 см) в зависимости от естественной структуры глины.
Стабильного тонкого помола достигают при ступенчатом измель чении массы (2—3 пары вальцов). Тонкость помола зависит от свойств сырья и вида изделий и обеспечивается расстоянием между валками:
|
Виды |
изделий |
|
Расстояние |
|
|
|
|
между вал* |
|
|
|
|
нами» мм |
Обыкновенный |
кирпйч и |
кирпич с |
небольшим ко- |
2—3 |
личеством пустот |
|
|
0,8—1,0 |
|
Дырчатый кирпич и камни с пустотностыо 25—40% |
||||
Тонкостенные |
керамические камни |
с размером, в |
|
|
5—10 раз превышающим размеры обыкновенного |
0,2—0,5 |
|||
кирпича, и пустотностыо 40—70% |
|
При поддержании зазора между валками 3 мм предел прочности кирпича при сжатии не превышает 9,8 МПа, при 2 мм — 14,7, при 1 мм — 26,46, при 0,5 мм — 34,30 МПа. Поддержание заданного раз мера щели между валками облегчается при оборудовании вальцов приспособлением для шлифовки валков (СМК-102).
Производительность вальцов составляет 12—25 м3/ч. Пропуск массы через 2—3 пары вальцов с успехом заменяет переработку на бегунах, особенно глин, засоренных известковыми включениями. Сте пень измельчения на нормально работающих вальцах с окружной ско ростью 10— 15 м/с и более при диаметре валков 1000 мм колеблется от 1:8
Рис. 6. Глинорастирочная машина РКД-1012а фирмы «Hendle».
до 1 12 (отношение размеров измельченных кусков материала к за гружаемым на дробление). На быстроходных вальцах с диаметром вал ков 400—600 мм и ширине зазора 1 мм степень измельчения 1 : 2,5—4.
В производстве пустотелых камней и других изделий, требующих тщательной переработки сырья, с успехом используют глинорастироч ные машины СМ-859, СМ-1241 и т. д. Производительность глинорастирателей составляет 4—25 м3/ч, глиномешалки с протирочной головкой (СМ-1238) — до 25 м3/ч. В глинорастирателе СМ-744 глина протира ется через отверстия в цилиндрической части, а включения накапли ваются в головке, откуда периодически удаляются при ее открыва нии.
Фирма «Hendle» (ФРГ) создала двухвальную глинорастирочную ма шину типа РКД-1012а, обеспечивающую измельчение, дробление, перемешивание и истирание глиняной массы (рис. 26). Машина со стоит из корпуса с перфорированным днищем, двух горизонтальных валов, вращающихся со скоростью 30—40 об/мин от индивидуальных приводов. На валах в шахматном порядке крепятся башмаки ротор ного типа 3 и башмаки-растиратели 2 . Процесс измельчения материала
проходит в три этапа. Вначале материал дробится башмаками-рото рами, затем растирается с помощью башмаков-растирателей и проти рается через решетку 1 . Расстояние между колодками ротора и решет
кой — 1 мм. Максимальная влажность перерабатываемого материа ла — до 60%.