
книги / Технология строительной керамики
..pdfтермическую стойкость, так как обладает более высоким коэффициен том термического расширения, чем стекловидная фаза. Зерна кварца диаметром более 10—30 мкм теряют часть прочности в результате по лиморфных превращений (рис. 5) и растрескиваются под действием напряжений, что уменьшает прочность изделий. Размер остаточных зерен кварца влияет на внутренние напряжения в материале изделий. Установлено, что при размере зерен кварца до 10 мкм напряжения между ними и стекловидной фазой составляют до 10,0 МПа. При размере зерен до 20 мкм за счет разности коэффициентов термического расширения (КТР) стеклофазы и кварца напряжения между стекловидной фазой и муллитом составляют всего 0,5— 1,2 МПа.
Кроме того, в результате модификационных превращений а-кварца в (3-кварц объем зерен кварца увеличивается на 0,02%, а возникающие напряжения на границе фаз возрастают до 30,0 МПа. Эти напряжения пропорциональны общей поверхности всех зерен кварца в единице объема изделий. Они достигают максимума, когда радиус зерен квар ца в 3 раза превышает толщину растворенного слоя. При этих услови ях растворяется около 70% первоначального содержания кварца в массе фарфора. По снижению кристаллической фазы материалы могут быть расположены в следующий ряд, независимо от того, получены они по керамической или стекольной технологии: тонкокаменные из
делия |
фаянс ->- твердый фарфор -> мягкий фарфор |
костяной |
|
фарфор ->• опаловое стекло |
стекло. |
|
|
Стекловидная фаза. При обжиге керамических изделий в различ |
|||
ных количествах образуется |
щелочеалюмосиликатный |
расплав, ко |
торый влияет на процессы формирования структуры изделий и их свойства. Застывший расплав образует стекловидную фазу черепка изделий как одну из его структурных единиц.
Стекловидная фаза в керамических изделиях характеризуется твердостью, жесткостью и хрупкостью. Для структурно чистой стек ловидной фазы свойственно хаотическое расположение структурных элементов, что придает ей большую изотропию свойств. Представляя собой переохлажденную жидкость, стекловидная фаза не имеет четко выраженной температуры плавления. Ей присущи все свойства, характерные для стеклообразного состояния вещества: изотропность свойств, отсутствие двойного лучепреломления, избыточный запас внутренней энергии, способность к обратимому твердению при перехо де из жидкого в твердое состояние. Хрупкость застывшей стеклофазы проявляется при вязкости более 1013 Па • с, т. е. при переходе в твер дое состояние. Стекловидная фаза, например, фарфора состоит, %: S i0 2 — 70—80; А12Оэ — 8 —16; КаО + Na20 — 8— 12.
В фарфоровом черепке основной непрерывной фазой является стек ловидная (в ней диспергированы другие фазы), в фаянсовом— глинистое вещество, образующее кристаллический скелет черепка, в котором диспергированы другие фазы, в том числе и стекловидная. В фаянсо вом черепке стекловидная фаза распределяется между кристаллами в виде тончайших пленок, обеспечивая их прочную связь.
Структурно стекловидная фаза фарфора представляет собой массу, проросшую мелкими субмикроскопическими кристаллами муллита.
В участках расположения полевошпатового расплава игольчатые крис
таллы муллита достигают длины |
10— 12 мкм, |
в единичных |
участках |
|
до 20—40 мкм. Муллит располагается в виде |
густой |
сетки |
и реже |
|
встречается в виде шагрени. |
|
|
,* |
|
Содержание стекломуллитовой |
фазы колеблется: |
в мягком фар |
форе оно составляет до 85%, в твердом фарфоре и электрофарфоре пони жается до 60%, в химически стойком — до 45%. Количество стекломуллитовой фазы в фарфоре особенно быстро увеличивается (от 40 до 70%) в интервале температур 1250—1370° С. В фаянсе стекломуллитовая фаза представлена слабее. В отличие от муллита, наблюдае мого в фарфоре, кристаллы муллита в фаянсовом черепке настолько тонкодисперсны, что выявляются только при рентгеноструктурном анализе.
В изделиях из низкотемпературного фарфора структура плотная, однако муллитизация выражена слабее, чем у обычного фарфора. Мул лит в основной массе мелкий, субмикроскопический. Игольчатые крис таллы муллита размером 5— 10 мкм представлены реже и только в поле вошпатовых участках в виде шагрени и густого войлока. Содержание стекломуллитовой фазы колеблется от 42 до 45%. В грубокерамиче ских изделиях, обжигаемых при 950—1050° С, на долю стекловидной фазы приходится всего 8—10%, муллит не встречается. Влияние стеклофазы на физико-технические свойства керамического черепка опре деляется не только ее свойством, количеством, физико-химическими свойствами, но и соотношением кристаллической и стекловидной фаз. С повышением температуры и длительности обжига образование стеклофазы и количество ее интенсивно возрастает. Стекловидная фаза понижает термостойкость изделий, повышает их хрупкость и т. д.
Показатель преломления колеблется от 1,350 для фаянса до |
1,520 |
для фарфора. |
|
Газовая фаза является третьей структурной составляющей |
кера |
мического черепка. Она заполняет закрытые поры, которые всегда имеются в материале, даже с нулевой эффективной пористостью. При чиной образования газовой фазы является воздух, заключенный в порах, газообразные продукты дегидратации, диссоциации, декарбо низации, разложения сульфатов и сульфидов и других минералов, всегда присутствующих в исходном сырье, восстановления оксидов железа, окисления органических остатков в сырье и сажистого угле рода в порах, освобождения газов в процессе плавления компонентов массы и других процессов. Газовая фаза фарфора состоит из С 02 — 10 — 13%, Ог — 2—5 и N2 — до 85%. Количественно газовая фаза в фарфоре составляет в среднем 4—6% объема, но не более 7—9%, и за висит от количества закрытых пор.
Содержание открытых и закрытых пор зависит от степени уплот нения материала при обжиге. При достижении спекаемым материалом 85% относительной плотности пористость остается полностью откры той и только в незначительном количестве появляются закрытые поры. Сначала закрытая пористость появляется медленно, а затем быстрее. При достижении материалом 95% относительной плотности вся порис тость оказывается закрытой. Плотность и пористость черепка изделий
являются не только важнейшими качественными характеристиками, но и определяющими классификационными признаками керамических изделий.
Структура контактного (промежуточного) слоя. В формировании физико-технических свойств глазурованных изделий важное значение имеет контактный слой. Образование этого слоя неизбежно из-за зна чительной разности химических составов глазури и черепка. Чем больше эта разница, тем интенсивнее протекают процессы взаимодей ствия между ними. При этом осуществляются сложные процессы: проникновение расплава глазури в поры черепка; двустороннее пере мешивание расплавов глазури и жидкой фазы черепка; диффузия ком понентов глазури в черепок, и наоборот, растворение кристаллических фаз черепка в расплаве глазури, а также образование новых кристал лических веществ и газовых пузырьков. С повышением температуры при обжиге число и тип подвижных ионов глазури и черепка увеличи ваются, становится возможным движение ионов кислорода кристал лической решетки минералов и оксидов, понижается вязкость гла зури и повышается ее реакционная способность, что приводит к интен сивному взаимодействию с черепком и образованию контактного слоя.
На характер образования контактного слоя, прочность сцепления глазури с черепком и плотность самого слоя мало влияет содержание в глазури оксидов алюминия и кремния. Решающую роль в этом игра ют оксиды щелочных и щелочноземельных металлов, а также их соот ношение в составе глазури.
В глазурях с повышенным содержанием К20 интенсивность взаи модействия ее с черепком возрастает, что приводит к увеличению тол щины переходного слоя. Активно действует СаО глазури в процессах взаимодействия с черепком, глубоко проникая в него даже при срав нительно низких температурах и скоростном обжиге. А120 3 и Si02 за медляют протекание процессов, Fe20 3, переходя в процессе обжига в FeO, действует как сильный плавень, глубоко проникает в черепок, способствуя образованию муллита в переходном слое.
При образовании контактного слоя одновременно протекает два процесса: растворение черепка и глазури и диффузия растворенных компонентов в толщу глазурного покрова. В определенных темпера турных условиях достигается устойчивое соотношение, при котором растворение черепка и диффузия растворенных компонентов в глазурь взаимно уравновешиваются.
Состав промежуточного слоя отвечает соотношению черепок : гла зурь, как 60—65 : 40—35. Контактный слой содействует выравнива нию термических напряжений между глазурью и черепком, хотя, кроме КТР черепка глазури и промежуточного слоя, на величину напряже ний влияют пористость, минеральный состав, структура черепка, ус ловия обжига, тонина помола глазури, скорость охлаждения и дру гие факторы.
Структура контактного слоя различна. В одних случаях отсутству ют видимые признаки реакции, линия раздела черепок—глазурь четко выражена (например, литые фасадные плитки). На поверхности черепка на границах контактного слоя нет никаких фазовых изменений
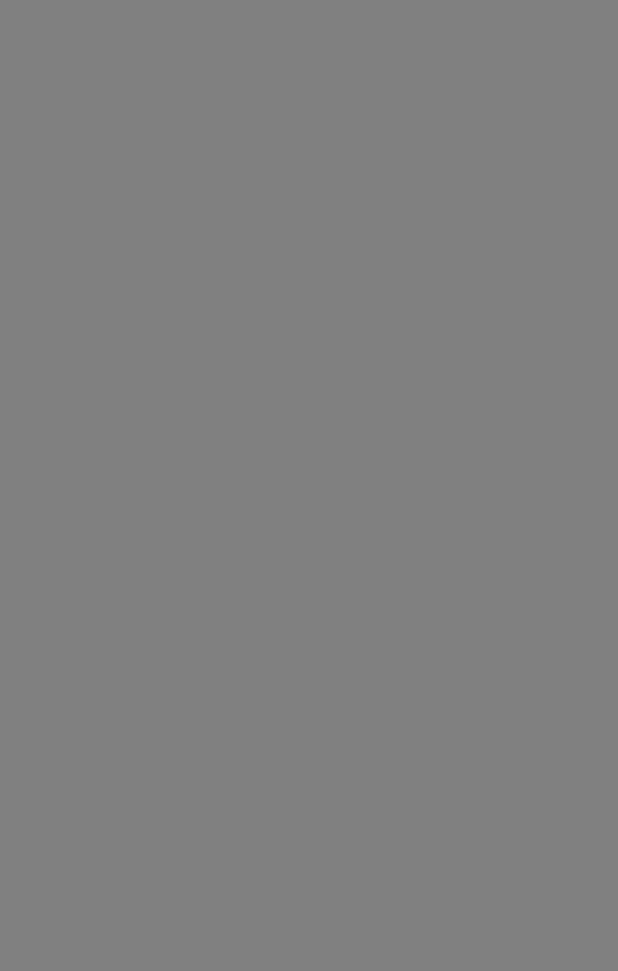
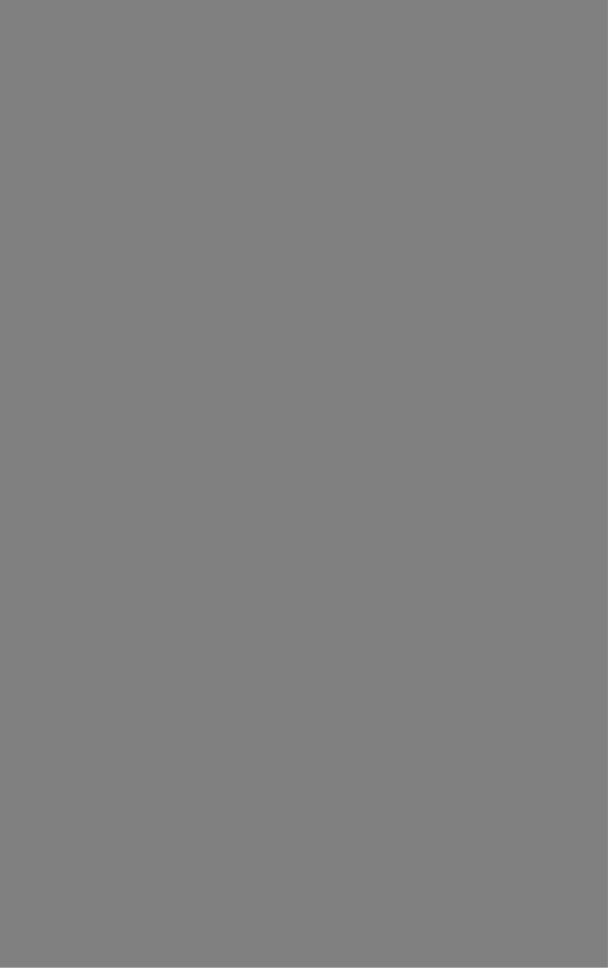
составу, который также может незначительно колебаться по толщине слоя глазури, что отражается на показателе преломления стекла, не сколько различном у контакта глазурь — воздух и глазурь — черепок.
1Г Кристаллическая фаза может быть представлена образованиями
двух типов — кристаллами-остатками шихты и кристаллами-новооб разованиями.
В глазурях обычно преобладают кристаллы первого типа. Это ос татки непрореагировавшего, не растворившегося в расплаве кварца, содержание которого не долж
|
но превышать 3%. |
|
|
Из кристаллов-новообразо |
|
|
ваний в глазури присутствует |
|
|
муллит и реже анортит и крис- |
|
|
тобалит |
в кайме оплавления |
|
зерен кварца. Кристаллов-но |
|
|
вообразований в обычной фар |
|
|
форовой |
глазури хорошего |
|
качества не должно быть. |
|
|
Газовые пузырьки округ |
|
|
лой формы размером от 10 до |
|
|
80 мкм располагаются ближе |
|
|
к контактному слою глазурь— |
|
Рис. 8. Расположение газовых пузырьков в |
черепок, |
реже во всей толще |
глазурном покрове при нанесении его слоем: |
глазури; |
пузырьки иногда со |
1 — тонким (120— 180 мкм); 2 — нормальным |
общаются друг с другом. В на |
|
(210—240 мкм); 3 — толстым (380—480 мкм). |
чале обжига основное коли |
|
|
чество пузырьков скопляется в контактном слое. Количество пузырьков в глазури возрастает с увеличением толщины ее слоя (рис. 8). С увели чением продолжительности и температуры обжига возрастает размер пузырьков и их количество в поверхностном слое глазури.
Общее количество пузырьков, располагающихся на площади в 1 мм2, может достигать 300 и более штук в зависимости от характера источников газовой среды: сохранившегося воздуха и паров воды, продуктов разложения минералов (диссоциации карбонатов), про дуктов сгорания топлива и т. д.
Газовые пузырьки в глазурном покрове снижают его качество и создают предпосылки для образования дефектов на поверхности глазури — пузыри, оспины, наколы, ухудшают микрорельеф поверх ности (шагрень глазури) и могут стать причиной образования микро трещин. Даже если глазурный покров не имеет газовых пузырьков, например, в фаянсовых изделиях, он пронизан мельчайшими порами, не обнаруживаемыми под микроскопом. Этим объясняется способ ность глазурного покрова пропускать пары воды и газов, что приводит к объемному расширению пористого черепка при его эксплуатации и к образованию вторичного дека глазури. Нарушение сплошности пони жает механическую прочность глазурного покрова (предел прочности при растяжении 20—50 МПа, теоретически возможный до 147,15 МПа) и снижает прочность изделий в 3—5 раз.
Метаморфизированные зерна черепка в глазури при высокой тем пературе обжига являются причиной вторичной кристаллизации мул лита, который частично снижает прозрачность и блеск глазури, вызы вая возникновение напряжений сжатия.
Вязкость глазури в период разлива зависит от состава ее и бывает в пределах 1,0—2,5 тыс. Па • с. Снижая содержание летучих компо нентов и вязкость расплава глазури, уменьшают содержание газовой фазы в глазури и улучшают рельеф поверхности.
Глазурование предварительно обожженных изделий (фаянс, фар фор по фаянсовой схеме), медленный подъем температуры и быстрое охлаждение изделий способствуют улучшению структуры и релье фа поверхности глазури. Глазурный покров повышает прочность из делий.
Структура глазурного покрова и его состав влияют на усадку, де формацию и белизну черепка. В зависимости от состава глазурь может тормозить усадку при обжиге (при высоком содержании оксидов каль ция, бария, стронция и т. д.) или способствовать увеличению усадки (при повышенном содержании оксида магния, полевого шпата) в пре делах 0,8— 1%. Это объясняется различием в температурах спекания и плавления, КТР, поверхностного натяжения. При одностороннем нанесении глазури на поверхность изделия (фаянсовые плитки) влия ние ее на черепок проявляется в большей мере, особенно на деформа цию.
§ 2. ФИЗИЧЕСКИЕ СВОЙСТВА
Физические свойства характеризуют особенности физического со стояния материала и глазурного покрова изделий.
Плотность характеризует степень заполнения объема материала веществом, из которого состоит этот материал, т. е. отношение массы материала к занимаемому им объему. Различают три вида плотности: истинную (удельная масса), кажущуюся (объемная масса) и относи тельную.
И с т и н н а я п л о т н о с т ь ( у д е л ь н а я м а с с а ) — это масса единицы объема абсолютно плотного материала (без пор). Она является физической константой для данного материала и зависит от химического состава, строения структурных элементов материала и плотности упаковки атомов в них.
Истинную плотность выражают отношением массы материала в су хом состоянии (г) к объему (см3) в абсолютно плотном состоянии.
Истинную плотность материалов, не растворимых в воде, но хоро шо ею смачиваемых, определяют в дистиллированной воде. Истинную плотность материалов, полностью или частично растворимых в воде,
или материалов, плохо |
смачиваемых |
водой, определяют в неполяр |
ной жидкости (толуоле, бензине и др.). |
||
К а ж у щ а я с я |
п л о т н о с т ь |
(объемная масса) — это отно |
шение массы материала ко всему занятому им объему, включая поры (г/см3). Объемная масса материала тем ниже, чем выше его пористость и ниже влажность.
О т н о с и т е л ь н а я п л о т н о с т ь — это объемная доля твердого вещества в материале. Ее определяют как отношение кажу щейся плотности к истинной. Если истинная и кажущаяся плотности
равны, материал |
является абсолютно плотным — стекло, вода |
и другие жидкости, |
некоторые пластмассы. Кажущаяся плотность |
керамических материалов (кроме ультралегковесных огнеупоров, легких заполнителей и т. д.) меньше истинной плотности.
Показатели плотности различных материалов
|
Истинная плот |
Кажущаяся |
|
ность (удель |
плотность (объ |
|
ная масса) |
емная масса) |
Фарфор твердый глазурованный |
2,42—2,60 |
2,26—2,50 |
Полуфарфор |
2,30—2,40 |
2,00—2,20 |
Фаянс |
2,45-2,60 |
2,20—2,50 |
твердый |
||
мягкий |
2,40—2,50 |
2,30—2,45 |
Тонкокаменные (химически стой |
2,1—2,8 |
1,92—2,50 |
кие) |
||
Кирпич |
2,60—2,7 |
1,5 —1,9 |
глиняный |
||
пористый |
2,60—2,70 |
0,70—1,40 |
Керамические камни |
2,60—2,70 |
1,25—1,40 |
Пористость керамических изделий определяется объемом пор в еди нице объема материала и выражается в процентах. Различают истин ную (общую), кажущуюся (открытую) и закрытую пористость.
И с т и н н а я п о р и с т о с т ь — это отношение суммы откры той и закрытой пористости к объему образца. Отношение истинной пористости образца до обжига и после обжига указывает на степень спекания материала при обжиге.
К а ж у щ а я с я п о р и с т о с т ь — это отношение объема пор, сообщающихся между собой и с внешним пространством и доступных для воды, к объему образца. Иногда открытая пористость может быть сквозной, что связано с повышенной водопроницаемостью черепка из делий. Открытая пористость обычно характеризуется величиной водопоглощения. Пористость снижается с повышением спекаемости ма териала при обжиге.
Пористость различных материалов,
Фарфор твердый Фаянс твердый
Тонкокаменныё (химически стойкие)
Полуфарфор Дренажные трубы Кирпич глиняный
Истинная
(общая)
4,1-7,9 12—30,0
о1 00 О 6—11
12—28 до 32
%
Кажущаяся
(открытая)
о 0 1 о сл
9—12,0
0,0-4,0 до 5
—
10—22
Истинная пористость полностью |
спекшейся |
керамики составляет |
||
3—5%, кажущаяся — менее 0,1—0,2%. |
|
|
||
З а к р ы т а я |
п о р и с т о с т ь |
— это отношение |
объема всех |
|
пор в материале, |
не сообщающихся |
с внешней |
средой |
(замкнутых), |
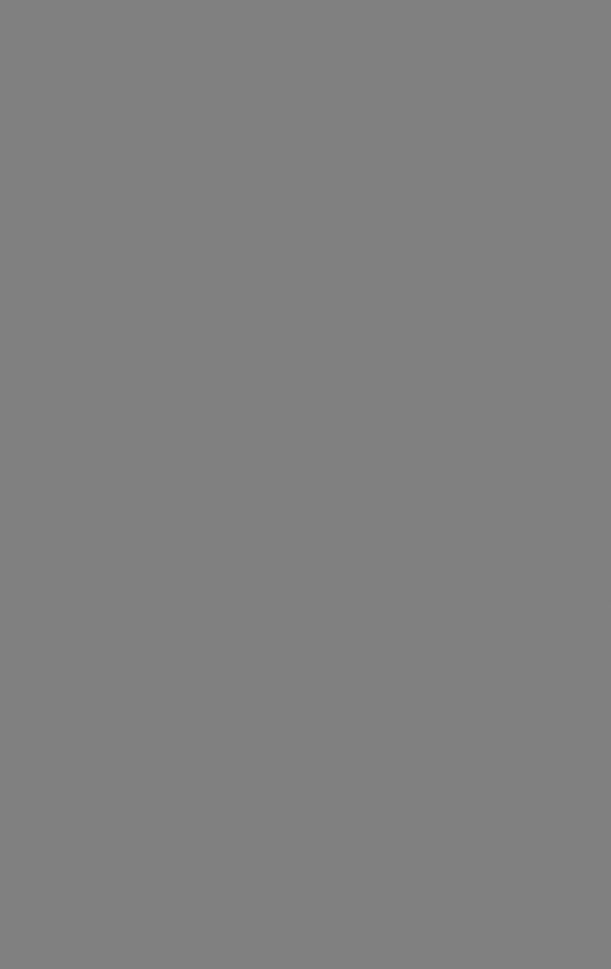
пористым (кирпич) черепком, характеризуются неравномерной по
ристостью, наличием |
волосных трещин, развитой |
сетью капилляров |
в переходном слое. В |
фаянсовом черепке и других |
пористых изделиях |
различают три вида пор: открытые протекаемые, открытые непротекаемые, закрытые (особенно в глазурях). Поры также характеризуются морфологическими признаками: размером, формой сечения (изометричные, щелевидные), степенью кривизны, шероховатостью стенок. Поры имеют изометричную и удлиненную щелевидную форму разме ром от 1 до 20 мкм. Щелевидные поры, например в санитарно-тех нических изделиях из фарфора, имеют ширину 1—5 и длину до 100 мкм. Небольшие поры имеют коническую форму. В микроструктуре удлиненные поры (до 160 мкм и более) сильно ослабляют прочность отдельных участков. Границы пор четко выражены. Наблюдаются также и более крупные поры (200—300 мкм). Большие неравномерные поры нежелательны, поскольку они ослабляют механическую проч ность черепка.
Генетически различают поры зерновой упаковки, воздушной и ог невой усадки, поры пузырения и сцепления, текстурные поры, поры в глазури (рис. 9) и т. д. Часто наблюдаемые поры вокруг непрореаги ровавших зерен кварца объясняются тем, что КТР стеклофазы в не сколько раз ниже КТР кварцевых зерен, что приводит к отрыву их от стеклофазы при охлаждении изделий.
Исследования поверхности пор при увеличении в 80 тыс. раз по казали, что поверхность пор покрыта равномерными круговыми воз вышениями диаметром около 35 мкм, что указывает на негомогенность
стеклофазы, содержащей кристаллы |
муллита. |
|
|
|
|
|
|||
По величине радиуса поры подразделяют на микропоры |
(радиус |
||||||||
2,5—5,0 мкм), переходные поры (радиус 5,0—100,0 мкм) |
и макропоры |
||||||||
(макрокапилляры) — диаметром более 200 мкм. Поры |
радиуса более |
||||||||
10 мкм называются некапиллярными, так как они заполняются |
водой |
||||||||
только при погружении материала в воду. Поры с меньшим |
|
радиусом |
|||||||
являются капиллярами и могут заполняться водой благодаря |
смачи |
||||||||
ванию их стенок, вследствие капиллярного подъема под |
действием |
||||||||
капиллярных сил, |
вызываемых |
поверхностным натяжением |
воды. |
||||||
В сквозных капиллярах радиусом меньше 10 мкм возможна |
капил |
||||||||
лярная конденсация, которая увеличивает поглощение |
(сорбцию) па |
||||||||
ров воды пористым черепком изделия. Увеличение пористости |
сопро |
||||||||
вождается увеличением не только количества, но и размера |
пор. |
||||||||
Количество пор, образующихся во время процесса |
спекания, яв |
||||||||
ляется функцией времени и температуры. |
В закрытых |
порах |
вслед |
||||||
ствие повышения температуры возникает положительное |
давление, |
||||||||
препятствующее уплотнению. |
|
|
|
|
|
|
|
|
|
Кинетика развития пор в фарфоре в зависимости от |
температуры |
||||||||
приведена на рис. |
10. При 1100° С структура черепка |
слегка |
уплот |
||||||
нена (рис. 10, а), чешуйчатые частицы собираются рядами, |
отдельные |
||||||||
участки пока не плавятся. При |
1200° С появляется |
стеклофаза, от |
|||||||
дельные участки частиц соединяются друг с другом, |
ясно просматри |
||||||||
ваются границы пор (рис. 10, б). При |
1250° С вследствие поверхност |
||||||||
ного натяжения уменьшается размер |
пор. |
Поры равномерно распре |