
книги / Химическая технология неорганических веществ.-1
.pdf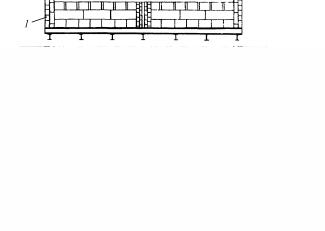
с линейным расположением электродов и печи с симметричным расположением электродов.
Эскиз одной из карбидных печей представлен на рис. 57.
Рис. 57. Закрытая карбидная печь с прямоугольной ванной: 1 – ванна; 2 – затвор; 3 – сальник; 4 – зонт; 5 – электрододержатель; 6 – механизм перемещения электродов; 7 – тракт шихтоподачи; 8 – механизм перепуска; 9 – электроды; 10 – короткая сеть; 11 – укрытие
Узел слива снабжен механизмом прожига летки, механизмом забивки летки и шуровочной машиной.
Слив проводят по графику. Не допустим перегрев расплава, охлаждение расплава. Расплав сливается с температурой 2070–2170 К.
Поскольку указанные выше реакции взаимодействия карбида кальция с Н2О, О2, N2 и СО2 приводят к снижению качества карбида (уменьшению литража), то необходимо эффективное охлаждение расплава карбида кальция.
В промышленности распространены три схемы охлаждения
идробления карбида кальция:
1.Слив в изложницы и последующее дробление застывших слитков в дробилках.
221
2.Разлив в мульдовый конвейер с последующим дроблением слитков в барабане.
3.Слив в грануляционный барабан, в котором происходит одновременное охлаждение и дробление.
В первой схеме используется особый режим охлаждения (медленное охлаждение в течение 24–48 ч). Полученные блоки размером до 1600 мм направляются в щековую или конусную дробилку (крупное дробление, затем среднее, фракция 25–80 мм). Выход 80–85 %. Недостатки схемы: значительные площади, сложная механизация.
Вторая схема более эффективна, чем первая. Однако она сложна
сточки зрения аппаратурного оформления.
Третья схема используется на технологических линиях, оборудованных мощными прямоугольными печами. Для охлаждения применяется барабан с тремя или шестью опорами диаметром 2–3 м, длиной 40–50 м, имеющий толщину стенки 16–20 мм, число оборотов – 8–12 в мин. Внутри барабана на расстоянии 15–20 м имеется насадка в виде лопастей, приваренных к внутренней поверхности по спирали. Выгрузка производится с помощью шнекового выгружателя. Куски более 80 мм задерживаются в барабане. Недостатки: большой расход воды (2000 м3/ч); потери литража (4–5 %); выход мелочи
(5–8 %).
5.6. Технология электрокорунда нормального
Электрокорунд нормальный – абразивный материал, содержащий 93–98 % минерала корунда α-Al2O3 и примеси. Корунд имеет высокую микротвердость 20–26 ГПа и высокую шлифующую способность.
Этот материал производят плавкой в дуговых электропечах шихты, состоящей из бокситов и углеродистого материала. В результате восстановительной плавки осуществляется перевод оксидов железа, кремния и титана в ферросплав. Оксид алюминия остается в невосстановленном состоянии и находится в печи в виде верхнего слоя расплава.
222
Во всем мире плавку ведут способом на блок, наплавляя 15– 30 г, корунда, который затем кристаллизуется в печи, извлекается, дробится и измельчается.
В России была разработана технология получения электрокорунда способом плавки на выпуск.
Мощность электропечей для плавки на блок до 4 МВ-А, на выпуск 10–15 МВ-А. Удельный расход электроэнергии 2500– 2900 кВт ч/т.
Освоение технологии плавки на выпуск было подготовлено многолетней работой по усовершенствованию плавки на блок: освоением агломерации боксита, использованием самоспекающихся электродов, механизацией загрузки шихты и автоматизацией систем регулирования процесса.
Плавка на выпуск позволила повысить мощность электропечей и улучшить качество электрокорунда (более однородный химический состав и микроструктура).
Электрокорунд нормальный перерабатывается в шлифовальные материалы (шлифзерна, шлифпорошки и микрошлифпорошки).
В технических требованиях к электрокорунду нормальному ограничивается содержание в нем Fe2O3 (не более 0,3–1,5 %), СаО (не более 0,3–1,6 %) и магнитного материала (не более 0,06–1,3 %).
Сырьем для получения электрокорунда являются бокситы. Могут использоваться не всякие бокситы, а только малокальциевые (содержание СаО не более 0,3 %). В сырье также должно содержаться определенное количество оксидов железа, кремния и титана.
Боксит Аятского месторождения содержит, %: Al2O3 – 44,5; SiO2 – 8,9; TiO2 – 2,3; Fe2O3 – 19,5. Важными характеристиками бок-
ситов являются: силикатный модуль MSiO2=>5–10; кальциевый модуль MCaO=>190–200; железистый модуль MFe2O3=>1,8.
Углеродистый восстановитель – малозольный антрацит или нефтяной кокс фракции ~ 5 мм. Корректировку расплава ведут с использованием фракции 3 мм. Часть углеродистого материала заменяют на алюминийсодержащий шлак (отходы производств цветной металлургии).
223
Теоретические основы производства электрокорунда
Основная цель плавки электрокорунда заключается в том, чтобы путем восстановления оксидов примесей получить в продукте высокое содержание оксида алюминия, образующего при застывании крупные кристаллы α-Al2O3.
Сравнение термодинамических характеристик оксидов железа, кремния, титана, алюминия и кальция показывает, что оксиды примесей, кроме оксида кальция, восстанавливаются при более низких температурах, чем оксид алюминия. Оксиды кальция и магния в условиях печи не восстанавливаются и переходят в продукт. Восстановление примесей протекает по реакциям:
– оксид железа:
3Fe2O3(тв) + СО(г) = 2Fe3O4(тв) + СО2(г) (в колошнике, колошник – слой шихты 1,5 м над расплавом);
Fe3O4 + СО(г) = 3FeO(г) + СО2(г) (в колошнике);
FeO + C = Fe + CO (10–15 % в колошнике, остальное в расплаве);
– диоксид кремния:
SiO2 + 2C(тв) = Si(ж) +2СО (Тнач = 1827 К), восстановленное же-
лезо способствует сдвигу равновесия реакции вправо, т.к. железо растворяет кремний, образуя ферросплав;
– диоксид титана: TiO2 переходит в Ti3O5, который восстанавли-
вается до Ti2O3, затем до TiO и, наконец, образуется Ti (Тнач = = 1159 К). Оксиды титана низшей валентности восстанавливаются
труднее, поэтому TiO2 восстанавливается не полностью.
Оксид алюминия Al2O3 может восстанавливаться углеродом при 2400 К, т.е. несколько выше температуры плавления оксида алюми-
ния 2323 К.
В России 80 % электрокорунда выплавляется с выпуском продуктов плавки через две отдельные летки. В электропечи наплавляется слой подины 1,7–1,9 м из электрокорунда.
Технологическая схема включает в себя следующие операции: подготовка и дозирование сырьевых компонентов, загрузка шихты,
224
плавка, выпуск электрокорунда и ферросплава, транспортировка, охлаждение и разбивка слитков.
Перспектива производства – переход на бокситоугольные брикеты, внедрение внепечного рафинирования расплава, механизация разливки.
6. ТЕХНОЛОГИЯ ПРОДУКТОВ ТОНКОГО НЕОРГАНИЧЕСКОГО СИНТЕЗА, ЧИСТЫХ ВЕЩЕСТВ И РЕАКТИВОВ
6.1. Основные принципы и методы получения чистых веществ и реактивов
За последние 30–40 лет резко изменилось понятие о чистом веществе и возросли требования к реактивам. Создана новая отрасль, занимающаяся производством особо чистых и сверхчистых веществ. Сейчас выпускаются сверхчистые материалы, в которых содержание отдельных примесей не превышает 10–8–10–10 %.
При производстве чистых веществ достаточно легко снизить содержание примесей до 0,1–1,0 % и даже до 0,01 %. Дальнейшая очистка является более сложной и трудоемкой.
Снижение содержания примесей ниже 10–3 % требует применения особых методов глубокой очистки, а для выработки особо чистых веществ возникает необходимость применения специально оборудованных помещений с тщательно очищенным воздухом, использования оборудования из особых материалов, применения специально очищенной воды; большие требования предъявляются при этом к одежде, защите рук работающих.
По существующей в стране классификации для химических реактивов установлена классификация: чистый (ч.), чистый для анализа (ч.д.а.), химически чистый (х.ч.), особо чистый (ос.ч.). Реактивы марки ч. используют в лабораторных работах учебного и производственного характера; ч.д.а. – для аналитических работ, выполняемых с большой точностью; х.ч. – для ответственных научных исследований, а также в аналитических лабораториях как вещества, по кото-
225
рым устанавливаются титры растворов; ос.ч. – это препараты для особых целей.
С 1965 г. в нашей стране используется маркировка особо чистых веществ, которая учитывает число и количество контролируемых и нормируемых примесей. Так, если в особо чистом веществе кон-
тролируются и |
нормируются только неорганические примеси, то |
в маркировке |
вещества может присутствовать такая запись |
«ос.ч. 10–5», что означает – в веществе контролируются и нормируются 10 неорганических примесей и их общее содержание не должно превышать 10–5 %. Если контролируются и нормируются только органические примеси, то марка может быть такой «оп – 3 ос.ч.». В случае контроля и нормирования тех и других примесей вещество маркируется так «оп – 3 ос.ч. 8–4».
Для получения неорганических веществ реактивной классификации наиболее приемлемы следующие пути:
1)использование для получения реактива сырья реактивной классификации (чистого сырья);
2)очистка технического вещества от примесей с получением препаратов реактивных классификаций;
3)комбинация 1-го и 2-го путей (один из видов сырья чистый, другой технический).
6.2.Практические методы очистки исходных веществ, промежуточных и конечных продуктов
Перекристаллизация – это наиболее распространенный метод очистки солей и органических соединений. Этот метод достаточно прост и эффективен.
Элементарная схема перекристаллизации такова: приготовление насыщенного раствора при нагревании, отделение нерастворимых примесей, кристаллизация чистого вещества при охлаждении. При охлаждении раствор оказывается пересыщенным по отношению к основному веществу, но ненасыщенным по отношению к примесям.
226
В действительности процесс сложнее, т.к. сопровождается рядом сопутствующих процессов (захват ионов и молекул – окклюзия, адсорбция примесных частиц на поверхности, образование твердых растворов – изоморфное замещение). Изоморфные вещества перекристаллизацией разделяются плохо. Например, алюмоаммонийные
квасцы трудно очистить с помощью перекристаллизации от Fe3+ (надо перевести Fe3+ в Fe2+).
Перекристаллизация характеризуется коэффициентом распределения
K = Nт/Nж,
где Nт – содержание примеси в твердом веществе;
Nж – содержание примеси в жидкой фазе.
Химическое осаждение – метод разделения, основанный на переводе примеси (или основного вещества) в осадок. Например, удаление примеси Fe3+ из NH4Cl действием NH4OH:
Fe3+ + NH4OH = Fe(OH)3 + 3NH4+.
Если реагент-осадитель образует малорастворимое соединение с ионами основного вещества и ионами примеси, то следует использовать различие в произведениях растворимости (ПР). Например, для удаления примеси Ва2+ из солей Sr2+ используют серную кислоту, т.к.
ПРBaSO4 = 0,87 10–10, a ПРSrSO4 = 2,8 10–7; ПР BaSO4 = [Ba2+ ] [SO42–].
Для очень тонкой очистки применяется метод соосаждения примесей. Например, для очистки раствора ZnSO4 от примеси As добавляют Fe2(SO4)3, а затем Zn(OH)2. Образующийся при этом осадок Fe(OH)3 адсорбирует примесь As.
Дистилляция и ректификация. Этими способами можно очи-
стить основное вещество от легколетучих или малолетучих примесей. При использовании метода ректификации теоретическое число тарелок, необходимое для заданного снижения содержания примеси, зависит от коэффициента относительной летучести разделяемых веществ.
Экстракция – извлечение одного из компонентов раствора с помощью не смешивающегося с раствором органического растворителя.
227
Экстракцию можно проводить из очень разбавленных растворов. При экстракции не происходит выделение в экстрагируемое вещество других веществ, поэтому экстрагируемое вещество может быть количественно выделено, и это используется в аналитической химии. Используемые в аналитической химии экстрагенты: диэтиловый эфир, хлороформ, амины, трибутилфосфат.
Ионный обмен и адсорбция широко применяются для глубокой очистки растворов и веществ от анионов и катионов, для чего используют аниониты и катиониты. Специально подобранные адсорбенты также находят применение в очистке веществ.
6.3. Классификация методов глубокой очистки веществ
Получение простых и сложных веществ в высокочистом состоянии заключается в глубокой их очистке от примесей. В процессе очистки важны два момента: глубина очистки и предотвращение загрязнения веществ материалом аппаратуры.
Выбор метода очистки определяется свойствами очищаемого вещества и примесей. Используемые в настоящее время методы глубокой очистки можно разделить на две группы: химические и физи- ко-химические. К наиболее распространенным физико-химическим методам относят ректификационный и кристаллизационный, а также ионный обмен и адсорбцию. Часто для получения веществ особой чистоты приходится использовать сочетание химических и физикохимических методов.
6.4. Химические методы глубокой очистки
Часть химических методов основана на переводе примеси либо в нерастворимое состояние, либо в растворимое с последующей отмывкой. Эффективные методы очистки металлов и оксидов металлов основаны на избирательном окислении или восстановлении. В качестве окислителей чаще всего используют кислород и галогены (хлор, иод).
228
При использовании в качестве окислителя кислорода, как правило, с его помощью химически связывают и удаляют примеси, содержащиеся в очищаемом веществе.
При использовании же галогенов почти всегда переводят в галогенид основное вещество. Затем полученный галогенид подвергается восстановлению водородом или термическому разложению. Часто для увеличения степени очистки промежуточное соединение – галогенид – подвергают дополнительной очистке физико-химическими методами. Поэтому галогенидный метод используют для глубокой очистки элементов, образующих летучие галогениды: бора, галлия, олова, мышьяка, сурьмы, висмута, молибдена, вольфрама (всего около 20 элементов).
Ряд элементов может быть очищен с использованием гидридного метода по схеме: перевод в гидрид, очистка гидрида, термическое разложение гидрида (например, Li через LiH). Гидриды образуют бор, углерод, кремний, олово, фосфор, мышьяк, свинец, сера, селен, теллур.
В последнее время большое значение приобретает метод получения высокочистых металлов и других материалов через металлоорганические соединения (МОС). Метод осуществляется по схеме: синтез МОС, очистка МОС, термическое разложение МОС.
Синтезированные МОС, как правило, содержат лишь примеси углеводородов и других МОС того же металла, но не содержат примесей других металлов. Термораспад МОС протекает при более низких температурах, что является большим преимуществом по сравнению с галогенидным методом.
К сожалению, получаемые распадом МОС элементы загрязнены углеродом. Поэтому этот метод наиболее целесообразно применять для очистки металлов, из которых углерод может быть удален восстановлением водородом.
При получении высокочистых металлов в виде порошков, пленок и покрытий применяют карбонильный метод (связывающий реагент СО). Этот метод обычно двухстадийный. Глубокая очистка возможна, т.к. образование карбонилов обладает высокой специфично-
229
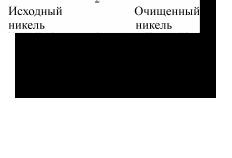
стью. Карбонильный метод используют для получения таких чистых металлов, как Fe, Co, Ni, Os, Mn, Re, Cr, Mo, W.
Особое место среди химических методов очистки занимает метод химических транспортных реакций (реакции переноса). Химическими транспортными реакциями называют гетерогенные обратимые реакции с участием газовой фазы, с помощью которых можно осуществить перенос вещества из одной части системы в другую, если между этими частями имеет место разность температур или давлений.
Этот метод широко используют при получении особо чистых веществ для полупроводниковой техники и радиоэлектроники. Очищаемое вещество взаимодействует с газообразным реагентом и образует газообразный продукт. Этот продукт переносится в другую часть реактора, где при других условиях происходит его разложение и выделяется чистое исходное вещество.
Например, при очистке никеля от других металлов и примесей используют следующие транспортные реакции:
Ni + 4CO = Ni(CO)4 + Q, |
T1 = 318–323 К; |
|
||
Ni(CO)4 = Ni + 4CO, T2 = 453–473 К. |
|
|||
|
В один конец стеклянной |
|||
|
трубки (рис. 58) помещается |
|||
|
никель, который необходимо |
|||
|
подвергнуть |
очистке. |
Из |
|
|
трубки |
откачивается воздух, |
||
|
после |
чего |
она заполняется |
|
|
оксидом углерода (II). В хо- |
|||
Рис. 58. Схема установки для проведе- |
лодном конце трубки проте- |
|||
ния транспортной реакции при нали- |
кает реакция образования тет- |
|||
чии градиента температур (Т2 > Т1) |
ракарбонила |
никеля. Газооб- |
||
|
разный тетракарбонил никеля диффундирует в горячий конец трубки, где под влиянием высокой температуры разлагается с образованием очищенного никеля и оксида углерода (II).
Для проведения транспортной реакции очищаемое вещество должно быть твердым или жидким, а химический реагент и продукт
230