
книги / Химическая технология неорганических веществ.-1
.pdfПроцесс образования дефектов имеет термодинамическую природу: система стремится минимизировать свою свободную энергию, а локализация избыточной энергии на дефектах термодинамически более выгодна, чем равномерное распределение упругих напряжений по всем связям кристаллической решетки. Появление дефектов, как правило, сопровождается существенными изменениями электронных свойств активированных веществ. Например, образуются электронные уровни в запрещенных зонах, запрещенные зоны сужаются, появляются электроны проводимости в полупроводниках, усиливаются электронно-донорные свойства анионов в полупроводниках и диэлектриках. Влияние всех этих изменений на каталитические свойства рассматривается электронной теорией катализа.
Систематические исследования по применению МХА для приготовления катализаторов выполнены в Ивановском химикотехнологическом институте. В этих исследованиях решалась проблема интенсификации взаимодействия между твердыми веществами и растворами, содержащими другие компоненты катализаторов. Механическая обработка ускоряла взаимодействие оксидов железа, цинка и алюминия с раствором хромовой кислоты. При обработке оксида алюминия в аммиачнокарбонатном растворе цинка, α- и γ-ок- сидов алюминия, а также оксида магния в аммиачнокарбонатном растворе меди наблюдалась сорбция ионов из раствора на поверхности твердого компонента. Такой технологический прием не только способствовал интенсификации взаимодействия компонентов, но и позволял регулировать некоторые эксплуатационные свойства катализаторов: их каталитическую активность, прочность, способность подвергаться формованию. Отмечено повышение активности цинкхромового катализатора в реакции синтеза метанола, сложного оксидного и магниймедного катализаторов в реакции паровой конверсии СО, алюмоникелевого катализатора в паровой конверсии углеводородов, а также увеличение прочности железохромового, алю- момедь-цинкхромового и алюмоникелевого катализаторов, цинкалюминиевой шпинели и оксида алюминия, используемых в качестве носителей. Помимо этого, α-оксид алюминия приобретал способ-
151
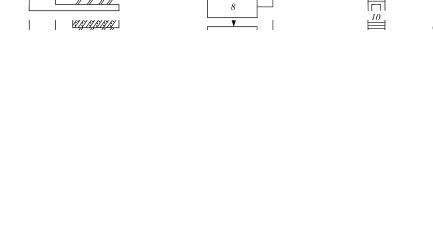
ность к формованию методом экструзии, что позволяло получать гранулы сложной формы. В результате исследований была предложена новая технология синтеза катализатора для среднетемпературной паровой конверсии СО, которая описана ниже.
Пример технологии катализатора, полученного механическим смешением
Технология катализатора СВД
Сульфованадат-диатомитовая контактная масса (катализатор СВД) предназначена для процесса окисления SO2 в SO3. Этот катализатор получают сухим смешением природного диатомита (носитель) и пиросульфованадата калия. Состав катализатора, мас. %: V2O5 – 6–7; K2O – 9–10; CaO – 2–3; SiO2 – 56–62; сульфаты в пересчете на SO42– –
18–19; Al2O3 + Fe2O3 – не более 5. Катализатор имеет пористость 0,2, удельную поверхность 4 м2/г, средний радиус пор – 250 нм. Используемый в качестве носителя диатомит представляет собой крупнопо-
Рис. 42. Технологическая схема производства катализатора СВД: 1 – сушилка КС; 2 – бункер; 3 – зубчатая дробилка; 4 – вибромельница; 5 – шаровая мельница; 6 – смеситель-гранулятор; 7 – реактор для получения раствора гидросульфата калия; 8 – сушилка; 9 – прокалочная печь; 10 – вибросито
152
ристый материал с высоким содержанием кремнезема и минимальным (менее 5 %) содержанием окислов железа и алюминия. В качестве сырья используют также технический оксид ванадия (V), сульфат калия и серную кислоту.
Технология катализатора СВД показана на рис. 42.
Диатомит сушат в сушилке «кипящего» слоя 1 горячим воздухом при 120–150 °С, затем его направляют в бункер 2. Технический оксид ванадия дробят в зубчатой дробилке 3, далее измельчают до размера частиц 200 мкм в вибромельнице 4. Смешение диатомита и оксида ванадия производят в шаровой мельнице 5. Смесь компонентов поступает в смеситель-гранулятор шнекового типа, куда подают также раствор гидросульфата калия, приготовленный в реакторе 7.
Выходящие из гранулятора гранулы влажностью 26–30 % сушат в ленточной сушилке 8 при 120 °С и затем прокаливают при температуре 400–580 °С в печи барабанного типа 9. В процессе прокаливания происходит образование пиросульфо-ванадата калия.
Технология катализатора на основе ферритов кальция и меди
Работами Ивановского государственного химико-технологиче- ского университета показано, что перспективными катализаторами паровой конверсии СО являются ферриты кальция и меди.
Традиционные методы получения ферритов, основаные на соосаждении гидроксидов и последующей термической обработке, имеют значительные недостатки, в частности необходимость применения высоких температур и большое количество стоков. Использование механохимической активации позволило снизить температуру термообработки, исключить образование стоков, а при использовании в качестве сырья металлических железа и меди избежать образования выбросов.
Показана высокая каталитическая активность новых катализаторов в реакции паровой конверсии СО:
153
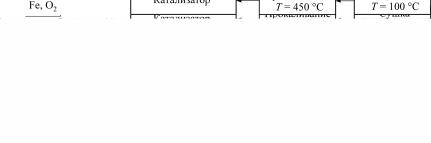
Состав и способ получения |
Степень превращения СО, %, |
|||
при температуре °С |
||||
катализатора |
||||
300 |
330 |
360 |
||
|
||||
|
|
|
|
|
При равновесии |
97,6 |
95,3 |
93,04 |
|
Ca2Fe2O5 – 90 %, CuFe2O4 – 10 % |
92,2 |
92,1 |
90,1 |
|
(МХА из безводных оксидов) |
|
|
|
|
Ca2Fe2O5 – 90 %, CuFe2O4 – 10 % |
91,6 |
92,4 |
90,5 |
|
(МХА из порошков металлов) |
|
|
|
|
Fe2O3 – 93 %, Cr2O3 – 7 % (по |
43 |
69,9 |
70,7 |
|
промышленной технологии) |
|
|
|
Принципиальная схема получения катализатора на основе ферритов представлена ниже
На первой стадии осуществляется механохимический синтез оксидов меди и железа. Механохимическое окисление происходит в присутствии пароаммиачновоздушной смеси по реакциям:
Cu + 4NH3 + H2O + 1/2O2 = [Cu(NH3)4](OH)2;
[Cu(NH3)4](OH)2 = CuO + 4NH3 + H2O.
В вибрационной мельнице процесс завершается за 45 мин. Синтез оксида железа осуществляется в кислородоазотной среде
в вибрационной мельнице за 140 мин.
На второй стадии проводят механохимический синтез ферритов при обработке смеси СuO, Fe3O4 и CaO также в вибрационной мельнице. Время активации составляет 45 мин.
154
Далее готовят пасту, которую формуют методом экструзии, гранулы сушат при 100 °С и прокаливают при 450 °С.
Катализатор паровой конверсии углеводородов
(ГИАП-16)
Катализатор состоит из оксидов никеля, алюминия, кальция, бария и др. В данной контактной массе отсутствуют соединения кремния, что выгодно отличает ее от катализатора ГИАП-5, поскольку в условиях конверсии кремнийсодержащие соединения выделяются из катализатора и оседают в трубопроводах, ухудшая их работу и вызывая аварийное состояние производства. ГИАП-16 более тугоплавкий, чем ГИАП-5, что дает возможность использовать его в более высокотемпературных процессах. Выпускают катализаторы марки А, где используют в качестве сырья оксид алюминия, и марки Б – на основе А1(ОН)3.
Разработана технология ГИАП-16 в виде цилиндрических колец серого или светло-серого цвета со следующими характеристиками:
Размер колец, мм............................................ |
15×6 |
Состав, мас. % |
|
NiO .................................................................. |
23–26 |
А12О3 ............................................................... |
44–52 |
MgO................................................................. |
13–17 |
ВаО................................................................. |
0,6–1,2 |
СаО................................................................. |
6–13 |
Насыпная плотность, г/см3 ........................... |
1 |
Суммарная пористость, %............................ |
15–40 |
Удельная поверхность, м2/г ......................... |
40 |
При конверсии с водяным паром углеводородного сырья, полностью очищенного от сернистых соединений, содержащего не менее 90 об.% СН4, при объемном отношении пар : газ = 2,0–2,2 : 1 и объемной скорости около 4000 ч–1 остаточное содержание метана в сухом конвертированном газе не превышает 40 % при 500 °С и 4 %
при 700 °С.
155
Схема производства сводится к следующим операциям. В горячем паровом конденсате при температуре 70–90 °С в течение 30 мин растворяют нитрат никеля и оксид бария. В шнековом смесителе ведут 15–20 мин сухое перемешивание дозированных количеств гидроксокарбоната никеля, прокаленного оксида магния и гидроксида либо оксида алюминия. Далее в смеситель поступают растворы нитрата никеля и оксида бария, и совместное перемешивание компонентов продолжается еще 50–60 мин.
Избыточную влагу из пасты удаляют, включая паровой обогрев. Общее количество воды в массе должно быть таким, чтобы смесь приобрела консистенцию сметаны. Это соответствует влажности пасты в пределах 30–35 %. Далее пасту сушат на ленточной сушилке 4–5 ч при 100–120 °С до остаточной влажности не более 5 % и прокаливают при 380 °С до полного разложения солей (~12–15 ч). Смесь оксидов помещают в смеситель, где увлажняют паровым конденсатом, взятым в количестве 70 % от массы порошка. Увлажненную шихту уплотняют на вальцах в пластины, которые дробят до размеров частиц около 1 мм и, наконец, прессуют в кольца.
Увлажненная шихта должна быть стаблетирована не позднее чем через 1,5 ч с момента внесения воды во избежание начала процесса «схватывания» алюмината кальция, что приводит к резкому ухудшению качества катализатора. Спрессованные гранулы провяливают не менее 2–3 сут на воздухе, при этом идет частичная гидратация алюмината кальция за счет влаги, внесенной на стадии смешения. Заключительными операциями являются гидротермальная обработка таблеток при 90 °С, сушка их на воздухе в течение 8–12 ч, далее 4–5 ч при 100–120 °С и прокалка при 380 °С на протяжении 5 ч. Скорость подъема температуры не должна превышать 50 °С в 1 ч. Общее время термообработки с учетом подъема температуры составляет 15–16 ч.
4.1.13. Технология плавленых катализаторов
Плавленые катализаторы получают сплавлением исходных составляющих при высоких температурах. В технологии неорганиче-
156
ских веществ этим методом получают катализаторы окисления и синтеза аммиака.
Технология плавленых катализаторов включает в себя следующие стадии: приготовление шихты, расплавление компонентов, формование или охлаждение расплава, дробление массы до необходимых размеров.
Катализаторы, полученные плавлением, отличаются высокой прочностью, хорошей теплопроводностью, малой удельной поверхностью.
Металлические плавленые катализаторы выпускают в виде сеток, спиралей, стружки, сфер, получаемых при распылении расплава.
Платиновый катализатор окисления аммиака получают в виде сетки, сплетенной из проволоки диаметром 0,09 мм, число плетений
1024 на 1 см2. Состав проволоки, %: Pt – 92,5; Pd – 4; Rh – 3,5 (родий добавляется для увеличения устойчивости платиновой сетки, палладий увеличивает активность при пониженных температурах).
Приведем пример технологии плавленого катализатора.
Технология катализатора СА-1
Катализатором синтеза аммиака является металлическое железо, полученное восстановлением из оксидов. Катализаторы промотируются оксидами: Al2O3, CaO, K2O (трехпромотированный); Al2O3, SiO2, CaO, K2O (четырехпромотированный); Al2O3, SiO2, CaO, MgO, K2O (пятипромотированный).
Активность железных катализаторов мало изменяется при промотировании, однако растет устойчивость и, следовательно, срок службы катализаторов.
Рекомендуется содержание 3–4 % Al2O3 в катализаторе (меньше – снижается устойчивость, больше – снижается активность). Оксид алюминия препятствует срастанию кристаллов железа при высокой температуре. В то же время Al2O3, обладая кислыми свойствами, может удерживать на поверхности катализатора аммиак. Для нейтрализации кислотных центров в катализатор добавляют
0,7–1,7 % K2O.
157
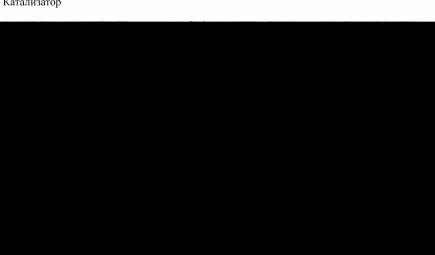
Одновременная добавка SiO2 и CaO (MgO) повышает активность катализатора.
Состав невосстановленного катализатора СА-1, %: Fe2O3 – 54–64; FeO – 29–36; Al2O3 – 3–4; K2O – 0,7–1,0; SiO2 – до 0,7; CaO – 2–3; MgO – до 0,7. Размер зерен гранулированного катализатора 3–5 мм,
дробленого 7–10; 10–15 мм; ρист = 4800 кг/м3; ϕсв= 0,1–0,3; Sуд = = 10–15 м2/г.
Исходным сырьем являются малоуглеродистое железо; Al2O3;
SiO2; K2CO3; CaCO3; MgCO3.
Cырье (150 кг) плавят в индукционной печи 4 (рис. 43) мощностью 100 кВт при 1600 °С в течение 1,5 ч. При плавке вводят Al2O3 и SiO2. Затем расплав сливают в окислительный тигель 7 (с рубашкой). Окисление проводят при 1600–2000 °С в течение 0,5 ч, подавая кислород под давлением 0,04–0,08 МПа. При окислении вводят
Рис. 43. Технологическая схема производства катализатора СА-1: 1 – гирационное сито; 2 – обкаточный барабан; 3 – элеватор; 4 – индукционная печь; 5 – питатель; 6 – комбинированная дробилка; 7 – окислительный тигель; 8 – охлаждающий противень; 9 – бункер; 10 – циклон; 11 – бункер мелочи; 12 – электродуговая печь; 13 – тара для катализатора
158
карбонатные добавки. Плав по желобу сливают в противень 8 для охлаждения. На дно противня засыпают слой катализаторной мелочи. Охлажденный плав измельчают в комбинированной дробилке 6 (щековая и валковая). Полученные зерна неправильной формы элеватором подают в обкаточный барабан 2. Разделение по фракциям производят на гирационном сите 1. Пыль катализатора от гирационного сита, обкаточного барабана и дробилки пневмотранспортом подают в циклон 10 и далее в бункер 11 и электродуговую печь 12. Электроплавку в печи 12 ведут при 1600–1800 °С в течение 3 ч, затем плав охлаждают в противне и перерабатывают в катализатор.
Восстановление катализатора ведут азотоводородной смесью либо в колонне синтеза, либо в специальном аппарате по специальному режиму. При необходимости катализатор пассивируют в токе азота.
4.2. Технология адсорбентов
Адсорбция, т.е. процесс избирательного концентрирования веществ на поверхности или в объеме микропор твердого тела (адсорбента), является универсальным методом, позволяющим практически полностью извлечь примеси из газовой или жидкой среды.
В промышленности адсорбционный метод широко используют для: глубокой очистки и осушки технологических потоков; улучшения качества сырья и продуктов; разделения смесей веществ на компоненты; для защиты биосферы от вредных промышленных выбросов; для защиты человека от вредных веществ в атмосфере (противогазы).
Применение адсорбционного метода в промышленности началось с открытия русским аптекарем Т.Е. Ловицем в 1875 г. обесцвечивания обожженным углем винной кислоты за счет поглощения примесей.
Через 9 лет уголь стали применять для очистки сахарных сиропов, для очистки спирта от сивушных масел и очистки питьевой воды.
159
В1903 г. русским ботаником М.С. Цветом было открыто свойство избирательности адсорбции. Пропуская спиртовый раствор каротина – пигмента листьев – через слой силикагеля, М.С. Цвет обнаружил образование отдельных зон с окраской, которая характерна для каждого компонента.
ВПервую мировую войну возникла проблема защиты армии от отравляющих веществ (ОВ), которые были применены 22 апреля 1915 г. на реке Ипр против французских и английских войск. В результате работ под руководством Н.Д. Зелинского был создан противогаз на основе активных углей.
Вдальнейшем развитие теории и практики адсорбции происходило с участием американских ученых И. Ленгмюра, Берга и Брека, венгерского ученого – М. Поляни, английского – Р.М. Барера, голландского – Я.Х. де-Бура, русских – Н.А. Шилова, М.М. Дубинина, Н.В. Кельцева.
4.2.1. Технология углеродных адсорбентов (активных углей)
Активные угли – это пористые промышленные адсорбенты, состоящие в основном из углерода. Активные угли получают из различных видов органического сырья: твердого топлива (угли), дерева и продуктов его переработки, материалов животного и растительного происхождения (кости), скорлупы орехов и др.
Структура и химические свойства активных углей
Ранее активный уголь считали аморфной разновидностью углерода. Однако позднее с помощью рентгеноструктурного анализа было показано, что активный уголь состоит из мельчайших углеродных кристаллических частиц (кристаллитов) размерами 1–3 нм. Таким образом, сейчас активные угли относят к группе микрокристаллических разновидностей углерода. Графитовые кристаллиты состоят из плоскостей, беспорядочно сдвинутых друг относительно друга (рис. 44). Расстояние между слоями 0,344–0,345 нм (у графита –
0,3354 нм).
160