
книги / Химическая технология неорганических веществ.-1
.pdfАктивными компонентами нанесенных катализаторов являются соли, оксиды, металлы. Активность нанесенного катализатора в кинетической области
А = Kуд Sк g,
где Kуд – удельная каталитическая активность; Sк – поверхность активного компонента, м2/г; g – содержание активного компонента в единице объема катализатора, г/м3.
Следовательно, активность нанесенного катализатора будет зависеть от дисперсности и количества нанесенного на носитель активного компонента, т.е. от способа приготовления. Количество активного компонента, которое наносится, определяется природой и структурой носителя, химическими свойствами активного компонента и условиями нанесения:
g = f (τ, rз, Sуд, ϕ, rп, Vп, ср, t, Dэ, µж, σ, θс, Ф, βкр),
где τ – время; rз – радиус зерна; Sуд – удельная поверхность; ϕ – пористость; rп – радиус пор; Vп – объем пор; ср – концентрация наносимого вещества в растворе; t – температура; Dэ – эффективный коэффициент диффузии; µж – вязкость раствора; σ – поверхностное натяжение; θс – угол смачивания; Ф – фактор формы; βкр – коэффициент кривизны пор.
Если поры носителя заполнены растворителем, то пропитка протекает по диффузионному механизму. Время диффузионной пропитки
τд = rз2(1 + Р) βкр/(Dэϕ),
где Р = а/(g – a), а – величина адсорбции, g – общее количество нанесенного каталитического вещества; при а = 0, Р = 0. Реальное время пропитки должно быть больше τд.
Поскольку в микрокапиллярах жидкость обладает аномальными свойствами, в этом случае
Dэ = D |
ϕ |
|
|
|
|
|
, |
2 |
|
|
|
r |
|
||
|
|
|
|
||||
|
(1+0,274 (1−ϕ)) |
|
+ 2,4 |
|
м |
|
|
|
r |
|
|||||
|
1 |
|
|
||||
|
|
|
|
|
п |
|
где rм – радиус диффундирующих молекул (частиц).
141
Если поры заполнены воздухом, то пропитка протекает по капиллярному механизму и в этом случае время пропитки
τк = 8rз2 µж/(σ rп cos θ).
В случае только пропитки g = срϕ, где g – количество вещества, которое может быть нанесено за одну пропитку, г/м3.
Продолжительность полной диффузионной пропитки, необходимой для равномерного распределения активного компонента по радиусу зерна катализатора, значительно больше времени капиллярной пропитки. Диффузионная пропитка малой продолжительности приводит к получению катализаторов корочкового типа.
Обычно пропитку осуществляют растворами, содержащими соединения активного компонента. Часто применяют соли, анионы которых можно легко удалить при термообработке (нитраты, карбонаты, ацетаты). При синтезе металлических катализаторов сначала получают оксиды, которые затем восстанавливают до металлов.
Если само активное вещество или его промежуточная форма малорастворимы, то пропитку проводят последовательно несколькими растворами, компоненты которых при взаимодействии образуют малорастворимые соединения (например, гидроксиды).
Известно несколько способов пропитки:
–метод окунания (однородность нанесения, большой расход реагентов);
–метод опрыскивания (неоднородность нанесения, экономия реагентов);
–пропитка с упариванием раствора;
–пропитка расплавом солей.
Влияние стадии сушки на распределение наносимого компонента
Пропитанные раствором активного компонента гранулы катализатора подвергаются сушке. Согласно существующим представлениям можно выделить три механизма переноса влаги в пористой среде
142
при изотермических условиях. Это диффузионный перенос пара под действием градиента парциального давления паров над мениском разной кривизны; капиллярное натекание из широких пор в узкие за счет разницы капиллярных давлений; пленочный перенос жидкости под действием градиента расклинивающего давления.
При сушке пропиточного катализатора может произойти перераспределение активного вещества по зерну катализатора. Наиболее значительное перераспределение вещества возможно при медленной сушке. В этом случае наблюдаются три стадии: на первой стадии освобождение порового пространства происходит путем испарения; на второй стадии поры носителя опорожняются как испарением жидкости, так и капиллярным натеканием; на третьей стадии сушка происходит в основном за счет пленочного переноса.
Таким образом, распределение активного компонента в сильной степени будет зависеть от того, на какой из стадий начинается кристаллизация растворенного вещества. Если это происходит на первой стадии (концентрация пропиточного раствора близка к концентрации насыщенного раствора), то происходит перераспределение с преимущественным выделением вещества на внешней поверхности гранул (корочковое распределение). При кристаллизации на второй стадии возможно отложение вещества преимущественно в устьях пор или в тонких порах (это нежелательно). Выделение вещества на третьей стадии обеспечивает наиболее равномерное распределение по всей поверхности пористого зерна.
При быстрой сушке перераспределения не происходит вследствие того, что не успевают протекать процессы капиллярного натекания, пленочного переноса и переконденсации. В этом случае активный компонент распределяется равномерно.
Регулируя технологический режим стадий пропитки и сушки, выбирая приемлемый носитель, можно получить различные случаи распределения активного вещества и его дисперсность. Различают четыре крайних случая распределения нанесенного активного компонента по зерну катализатора:
143
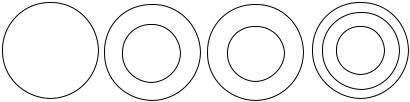
I |
II |
III |
IV |
I – для процессов, протекающих в кинетической области (равномерное распределение);
II – для процессов, протекающих во внутридиффузионной области (корочковое распределение);
III – для процессов во внутридиффузионной области при истирании или отравлении катализатора (распределение типа «яичного желтка»);
IV – для процессов в кинетической области при истирании или отравлении катализатора (распределение слоистое).
Катализаторы на носителях получают в виде таблеток, шариков или порошков.
Приведем примеры технологии катализатора, полученного методом нанесения.
Технология катализатора ГИАП-3
Катализатор ГИАП-3 используют для паровой, пароуглекислотной и паровоздушной конверсии углеводородов с целью получения технического водорода. Катализатор в невосстановленном виде содержит оксид алюминия в качестве носителя и оксид никеля в качестве каталитически активного вещества. Состав невосстановленного катализатора, мас. %: α-Al2O3 – 93, γ-Al2O3 – 1,9, NiO – 5,1. Катали-
затор выпускают в виде цилиндров Ц 14×14 мм, К 14×14×5 мм. Пористость гранул – 0,35, удельная поверхность – 5 м2/г.
Сырьем в производстве катализатора являются оксид алюминия, нитраты алюминия и никеля, азотная кислота.
144
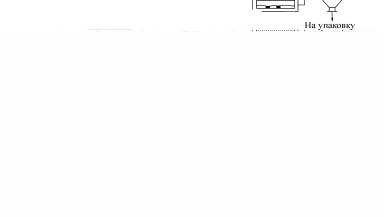
Технологическая схема (рис. 40) включает в себя получение гранул носителя, его пропитку и термическую обработку.
Рис. 40. Технологическая схема производства катализатора ГИАП-3: 1 – циклон; 2 – шаровая мельница; 3 – бункер; 4 – реактор разбавления; 5 – бегуны; 6 – формовочная машина; 7 – туннельная сушилка; 8 – шахтная печь; 9 – сита; 10 – пропиточный реактор; 11 – реактор для приготовления пропиточного раствора
Оксид алюминия пневмотранспортом через циклон 1 подают в шаровую мельницу 2, где он размалывается в течение 24–36 ч до размеров 20–30 мкм и затем поступает в бункер 3. Азотную кислоту концентрацией 45–47 % разбавляют в аппарате 4 дистиллированной водой до концентрации 19–29 %. Размолотый оксид алюминия и азотную кислоту загружают и перемешивают в смесительных бегунах 5 до образования густой однородной массы. Полученную массу формуют методом экструзии в формовочной машине 6, гранулы помещают на противни и на вагонетках сушат в тоннельной сушилке 7 в течение 10–12 ч. Далее гранулы носителя прокаливают в токе дымовых газов в печи 8, постепенно поднимая температуру до 1000– 1400 °С, и потом охлаждают воздухом. Прокаленный носитель отсеивают от мелочи и пыли на ситах 9 и помещают в пропиточный реактор 10. Пропитку осуществляют в течение 30–40 мин раствором,
145
приготовленным в реакторе 11. По окончании пропиточного цикла раствор удаляют и гранулы сушат путем подачи воздуха с температурой 300–350 °С. Далее их охлаждают и проводят повторную пропитку. После нанесения заданного количества NiO высушенный катализатор в этом же реакторе прокаливают при 450–500 °С в течение 5 ч, причем температуру от 300 °С до 500 °С поднимают постепенно со скоростью 50 °С в 1 ч. Заключительный этап – восстановление NiO до металлического Ni – осуществляют на заводе-потребителе.
Технология катализатора АПК-2
Катализатор АПК-2 (палладированный оксид алюминия) используют для очистки хвостовых газов производства разбавленной азотной кислоты от оксидов азота, а также в других окислительных процессах. Катализатор состоит из 2 % Pd и 98 % γ-Al2O3. Палладий находится в мелкодисперсном состоянии. При малых (около 2 %) концентрациях покрытие поверхности приближается в среднем к моноатомному. Катализатор АПК-2 имеет следующие характеристики:
Размер гранул, мм |
12×12 |
Насыпная плотность, г/см3 |
1,1–1,2 |
Потери от разрушения гранул в месяц, % |
примерно 0,5 |
Получают АПК-2 по следующей технологической схеме
(рис. 41).
Таблетированный оксид алюминия через воронку загружают в аппарат 1, предварительно заполненный на 1/3 обессоленной водой, где проводят обессеривание. После загрузки носителя реактор полностью заливают водой, подают острый пар для нагревания и перемешивания массы, обрабатывая таким образом γ-Al2O3 в течение часа. В том же аппарате носитель отмывают до отсутствия серы в промывной воде, затем сушат его в сушилке 2 при 250–300 °С. Раствор Pd(NО3)2 получают в реакторе 3 разбавлением палладиевой «пасты» обессоленной водой до концентрации 86 г/л (в пересчете на Pd). В прямоточный барабанный смеситель 4, снабженный приводом для вращения барабана, загружают освобожденный от серы А12О3
146
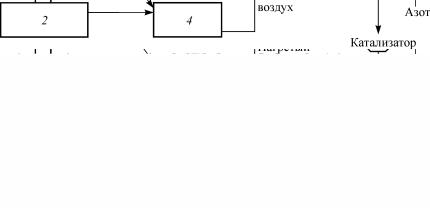
и подают раствор Pd(NО3)2. Количество подаваемой соли определяется содержанием Pd в готовом катализаторе. В процессе пропитки, которая продолжается 1 ч, активный компонент раствора полностью поглощается носителем.
Рис. 41. Схема производства катализатора АПК-2: 1 – аппарат для обессеривания носителя; 2, 5 – сушилки; 3 – реактор для приготовления раствора; 4 – пропиточный аппарат; 6 – прокалочная печь
Пропитанный носитель сушат горячим воздухом в аппарате 5 в течение 40 ч при 200–220 °С. Сушилка представляет собой полый цилиндрический аппарат с коническим днищем. Затем катализатор прокаливают в печи 6 при 380–400 °С в атмосфере азота, при этом соль разлагается: 2Pd (NО3)2 = 2PdO + 4NО2 + О2. Окончание прокаливания определяют по прекращению выделения оксидов азота. В среднем время, необходимое для полного разложения соли в указанных условиях, составляет примерно 60 ч. Катализатор охлаждают до 50–60 °С в токе азота и затаривают в чистые сухие герметично закрывающиеся барабаны. Катализаторная масса должна обеспечить очистку газа от оксидов азота до остаточного содержания NO, не превышающего 0,006 %.
147
4.1.12. Технология катализаторов, полученных механическим смешением компонентов
Особенностями технологии катализаторов, получаемых методом смешения, являются предварительное достаточно тонкое измельчение исходных компонентов, последующее тщательное смешение и прокалка смеси.
Основные стадии технологии: измельчение исходных компонентов, смешение, формовка гранул, сушка, прокаливание, отсев пыли.
Достоинством этого метода является отсутствие или малое количество стоков и вредных выбросов. Недостатки – трудность получения катализатора с высокой удельной поверхностью, высокие энергетические затраты.
Активность и селективность катализаторов смешения часто определяются не свойствами индивидуальных веществ (например, оксидов), а свойствами продуктов их взаимодействия. Поэтому процесс взаимодействия между компонентами с образованием химических соединений очень важен при получении катализаторов.
Согласно современным представлениям процесс взаимодействия между твердыми частицами оксидов осуществляется за счет диффузии реагирующих молекул через слой продукта. Например, по модели Яндера взаимодействие вещества А с покрывающим веществом В происходит за счет диффузии молекул В к поверхности вещества А.
Исследования показали, что на глубину взаимодействия сухих оксидов оказывают влияние такие факторы, как кристаллическая структура оксидов, размер зерен компонентов, температура прокаливания смеси, время.
На взаимодействие между компонентами большое влияние оказывает также тонкое измельчение. Это влияние обусловлено тем, что взаимодействие осуществляется путем диффузии компонентов в местах соприкосновения зерен реагирующих веществ.
Тонкое измельчение достигается в барабанных, струйных и вибромельницах. В шаровой мельнице материал можно измельчить до
148
величины 50 мкм (0,05 мм). Для того чтобы получить частицы меньшего размера, необходимо значительно увеличить продолжительность размола. Струйные и вибромельницы позволяют интенсифицировать процесс тонкого измельчения.
При тонком измельчении происходит механическая активация твердых материалов. Механическая активация обусловлена: а) снятием диффузионных торможений вследствие обнажения свежей поверхности; б) нарушением структуры поверхностного слоя; в) образованием низкомолекулярных фрагментов, обладающих высокой подвижностью и реакционной активностью.
Другим способом интенсификации процессов взаимодействия компонентов смеси является проведение реакции в присутствии жидкой фазы (мокрое смешение). Возрастание скорости взаимодействия обусловлено в основном увеличением площади контакта реагирующих веществ.
Перспективным является механохимический метод активации, в соответствии с которым тонкий размол совмещается с воздействием реакционно-способной жидкой фазы и поверхностно-активных веществ. При этом способе высокодисперсные и прочные твердые тела с заданными свойствами получают, используя тонкодисперсное сырье, получаемое в присутствии ПАВ, и осуществляя смешение компонентов с помощью интенсивных механических и вибрационных воздействий.
Развитие механохимии началось с изучения процессов измельчения. Было обнаружено, что при измельчении меняются не только размеры частиц материала, но и их физико-химические свойства. Это послужило основанием для введения термина «механохимическая активация» (МХА). Измельчение веществ широко применяется в химической промышленности, в том числе при производстве катализаторов. Процессы, происходящие при механической обработке твердых веществ, подробно описаны в ряде монографий и обзоров. Можно отметить те изменения, которые при механохимической обработке способны оказать влияние на синтез катализаторов.
149
Вообще, физико-химические изменения, возникающие при МХА, являются следствием релаксации поля напряжений после интенсивных механических воздействий по различным каналам.
Наиболее подробно изучен канал релаксации поля напряжений, связанный с образованием свежей поверхности. Исследованию кинетики этого процесса посвящен целый ряд работ. Описаны как простейшие закономерности грубого измельчения, так и более совершенные модели тонкого измельчения, в которых учитываются импульсный характер механического воздействия и влияние механической активации на формирование свежей поверхности. Такие модели носят формальный характер и способны описать далеко не все экспериментальные результаты, особенно те, которые получены при изучении веществ с анизотропными свойствами. Детальное исследование химических свойств свежей поверхности показало, что МХА оксидов кремния, германия, олова и магния приводит к образованию на их поверхности различных центров, имеющих преимущественно радикальную природу. Описаны реакции взаимодействия этих центров с различными газами. Полученные данные можно использовать для прогнозирования процессов, протекающих при синтезе каталитических систем и модификации их поверхности.
Другим часто встречающимся каналом релаксации поля напряжений является образование дефектов кристаллической структуры
ивыход этих дефектов на поверхность кристаллитов. Многочисленные исследования, систематизированные в монографиях, показали, что именно образование дефектов, а не формирование свежей поверхности, является причиной повышения реакционной, в том числе
икаталитической, активности веществ в результате МХА. Существует мнение (основанное на косвенных данных), что дефекты кристаллической структуры и являются каталитически активными центрами. На наш взгляд, для выяснения причин влияния МХА на каталитическую активность необходимо проследить связь между физикохимическими особенностями дефектов и природой катализа, рассматриваемого как последовательность химических превращений катализатора и реагентов.
150