
книги / Химическая технология неорганических веществ.-1
.pdf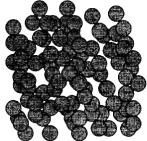
формирования. Основные параметры модели ХРС – число сфер N диаметра D в единице объема.
Сферы расположены в пространстве совершенно случайно и могут накладываться, образуя связную систему. Предполагается, что число N достаточно велико для проведения статистического анализа, позволяющего определять пористость ϕ хаотичной системы как вероятность нахождения произвольно выбранной точки вне пространства частиц. В этом случае, как показал Колмогоров, ϕ = exp(−V ) =
|
|
1 |
|
3 |
|
= exp |
− |
|
π D |
|
N , где V –суммарный объем всех сфер. |
|
|
||||
|
|
6 |
|
|
|
Для этого случая
Sуд′ = −π D2 N ϕ,
поэтому окончательно после исключения N получим
S′ |
= − |
6 ϕ ln ϕ |
. |
|
|
|
|||
уд |
|
D |
|
|
|
|
|
||
Полученное уравнение соответст- |
Рис. 35. Модель хаотично |
|||
вует модели ХРС-частиц. Аналогичное |
||||
уравнение для |
ХРС-полостей, т.е. для |
расположенных сфер |
губчатых структур, получается при простой замене ϕ на (1 – ϕ). Способы создания развитой пористой структуры:
1. Наиболее часто пористая структура катализатора (или носителя) формируется при его синтезе (получении). Следовательно, характеристики пористой структуры в этом случае зависят от технологического режима синтеза.
Например, при получении силикагеля, имеющего глобулярную структуру, используют следующие операции:
–образование золя (система частиц размером 3–100 нм, взвешенных в жидкой среде);
–застудневание золя в гель и созревание геля;
–промывка;
131
– сушка и прокаливание.
Каждая стадия оказывает влияние на формирование структуры. На размеры частиц золя оказывают влияние концентрация SiO2 и рН растворов. При низкой рН 1–2 образуются образцы с удельной поверхностью 600–900 м2/г.
2.Методы геометрического модифицирования (обработка паром, прокаливание). При прокаливании алюмосиликатов удельная поверхность уменьшается, размер пор существенно не меняется; при обработке паром резко увеличиваются размеры пор.
3.Физико-химическая модификация (используют специальные модификаторы структуры, какими для алюмосиликата являются соли ванадия и соли фосфора).
4.1.9. Отравление катализаторов
Это потеря активности под действием небольшого количества веществ, называемых контактными (каталитическими) ядами. Потеря активности происходит вследствие частичного или полного выключения активной поверхности катализатора.
Существует два вида отравления: истинное отравление и блокировка. Истинное отравление может происходить по химическому и адсорбционному типу. Отравление может происходить обратимо и необратимо. Существует благоприятствующее отравление. Примером отравления типа блокировки является зауглероживание.
4.1.10. Технология катализаторов, полученных осаждением
Этим методом получают до 80 % всех катализаторов и носителей. Метод осаждения позволяет в широких пределах изменять характеристики пористой структуры получаемых твердых веществ.
Методом осаждения могут быть получены контактные массы, содержащие в качестве активных веществ соли, гидроксиды, оксиды.
Осажденные катализаторы получают двумя способами в зависимости от используемого способа формовки.
132
Способ 1. Растворение – осаждение – фильтрование – промывка – сушка – прокаливание – измельчение – сухая формовка.
Способ 2. Растворение – осаждение – фильтрование – промывка осадка – формовка катализатора – сушка гранул – прокаливание.
Основной стадией является осаждение, т.е. процесс образования твердой фазы в результате химической реакции при сливании растворов исходных компонентов. Примеры:
1)Fe(NO3)3 + 3NH4OH = Fe(OH)3 + 3NH4NO3;
2)FeSO4 + (NH4)2CO3 = FeCO3 + (NH4)2SO4;
3)7(Na2O 3SiO2) + Al2(SO4)3 + 3H2SO4 = Na2O · Al2O3 · 21SiO2 +
+6Na2SO4 + 3H2O;
4)Na2O 3SiO2 + H2SO4 = 3SiO2 + H2O + Na2SO4.
Свойства осажденных катализаторов в значительной степени зависят от стадий осаждения, фильтрования, промывки осадка и сушки.
Влияние условий осаждения на свойства катализаторов
Условия осаждения влияют на свойства катализаторов, т.к. они определяют дисперсность, химический и фазовый состав осадков. Факторы, влияющие на состав и свойства осадков: рН, температура, концентрации растворов, порядок и скорость смешения растворов.
При обычных условиях кристаллизации размеры твердых частиц зависят от пересыщения. Однако многочисленные исследования осаждения труднорастворимых осадков показали, что минимальный размер частиц не зависит от природы вещества и составляет 4 нм. Отсюда при ρист = 1500 кг/м3 и rг = 2 10–9 м максимальная величина
удельной поверхности Sуд = |
|
3 |
|
= 1000 м2/г. Реальная вели- |
|
|
|
||
r |
1000 ρ |
|
||
|
ист |
|||
|
г |
|
чина поверхности меньше, что обуславливается вторичными процессами агрегации первичных частиц, перекристаллизации (переконденсации).
133
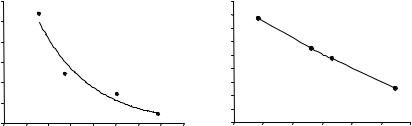
Значительное влияние на дисперсность осадков оказывают примеси продуктов неполного гидролиза (основных и кислых солей). С увеличением содержания продуктов неполного гидролиза величина поверхности уменьшается (размер частиц увеличивается). В случае силикагеля, обладающего кислотными свойствами, величина поверхности зависит от содержания катионов (рис. 36), в случае гидроксида алюминия, обладающего основными свойствами, – от содержания анионов (рис. 37).
A |
|
|
|
|
|
|
|
|
A |
|
|
|
|
|
|
600 |
|
|
|
|
|
|
|
|
450 |
|
|
|
|
|
|
500 |
|
|
|
|
|
|
|
|
400 |
|
|
|
|
|
|
|
|
|
|
|
|
|
|
350 |
|
|
|
|
|
|
|
|
|
|
|
|
|
|
|
|
|
|
|
|
|
|
|
400 |
|
|
|
|
|
|
|
|
300 |
|
|
|
|
|
|
300 |
|
|
|
|
|
|
|
|
250 |
|
|
|
|
|
|
|
|
|
|
|
|
|
|
200 |
|
|
|
|
|
|
|
|
|
|
|
|
|
|
|
|
|
|
|
|
|
|
|
200 |
|
|
|
|
|
|
|
|
150 |
|
|
|
|
|
|
|
|
|
|
|
|
|
|
|
100 |
|
|
|
|
|
|
100 |
|
|
|
|
|
|
|
|
50 |
|
|
|
|
|
|
|
|
|
|
|
|
|
|
|
|
|
|
|
|
|
|
0 |
|
|
|
|
|
|
|
B |
0 |
|
|
|
|
|
B |
0 |
1 |
2 |
3 |
4 |
5 |
6 |
7 |
8 |
0 |
2 |
4 |
6 |
8 |
10 |
12 |
Рис. 36. Зависимость величины |
Рис. 37. Зависимость величины |
||||||||||||||
удельной |
поверхности |
силикагеля |
удельной |
поверхности |
|
гидроксида |
|||||||||
от содержания Na+. А – удельная |
алюминия от содержания NO3–. А – |
||||||||||||||
поверхность, |
м2/г; В – содержание |
удельная поверхность, м2/г; В – со- |
|||||||||||||
|
|
Na+, мас. % |
|
|
|
|
держание NO3–, мас. % |
|
|||||||
|
Введение в состав гидроксида второго компонента приводит |
||||||||||||||
к росту размера поверхности. |
|
|
|
|
|
|
|
|
|||||||
|
Увеличение рН приводит к росту поверхности гидроксида алю- |
||||||||||||||
миния и снижению поверхности SiO2 × H2O. |
|
|
|
|
|
||||||||||
|
Влияние температуры на величину поверхности может быть |
||||||||||||||
различным |
(для |
Al(OH)3 |
c |
увеличением |
температуры |
Sуд |
увели- |
чивается).
На свойства осадков влияет способ осаждения. Осаждение можно вести: из гомогенной или гетерогенной среды, при постоянном или переменном рН, в периодическом или непрерывном режиме. Осаждение из гомогенной среды позволяет получить осадки равно-
134
мерного состава и размеров частиц. Например, получение осадка Ni(OH)2 при осаждении в растворе мочевины:
CO(NH2)2 + 3H2O = CO2 + 2NH4OH (при нагревании);
Ni(NO3)2 + 2NH4OH = Ni(OH)2 + 2NH4NO3.
При непрерывном режиме осаждения увеличиваются скорости процессов гидролиза и осаждения, а следовательно, увеличивается степень кристалличности осадка и его удельная поверхность.
Так, при синтезе гидроксида алюминия из растворов основного серно-кислого алюминия и низкомодульного алюмината натрия были получены следующие характеристики пористой структуры образцов:
Показатель |
Непрерывный |
Периодический |
Удельная поверхность, м2/г |
способ осаждения |
способ осаждения |
260 |
182 |
|
Удельный объем пор, см3/г |
0,52 |
0,46 |
Средний радиус пор, нм |
7,6 |
8,5 |
Содержание SO42–, % |
0,45 |
1,35 |
Старение осадков
Свежие осадки обладают большой избыточной свободной энергией и потому нестабильны. С течением времени в них протекают различные процессы, объединяемые одним термином – старение (созревание). Различают два типа процессов старения: физическое и хи-
мическое.
При физическом старении состав осадка не меняется, а происходит усовершенствование его структуры и размеров кристаллов (частиц), десорбция примесей, захваченных при осаждении (старение осадка CaSO4).
При химическом старении происходит гидролиз основных солей алюминия и распад агрегатов. В дальнейшем возможно срастание малых первичных частиц в агрегаты.
135
Старение наиболее быстро происходит в гидротермальных условиях (в жидкой фазе при t > 100 °C).
Сушка осадков
Влияние условий сушки на свойства высушенных осадков зависит от следующих факторов: способа сушки; количества и природы примесей в высушиваемом материале; содержания воды во влажном осадке; температуры и скорости удаления воды; природы осадка или геля.
Существуют следующие способы сушки: конвективная, контактная, электрическая, распылительная, сублимационная.
Сушка перегретым паром дает возможность вести процесс в «мягких» условиях, что благоприятно сказывается на равномерности сушки.
Основным недостатком конвективного способа является подвод тепла к внешней поверхности, при этом возникает градиент температуры и влажности, а это приводит к неравномерному высушиванию материала.
Процессы, протекающие при сушке гелей
Формирование пористой структуры ксерогеля при сушке определяется соотношением сил капиллярного сжатия первичной структуры геля и сил сопротивления этому сжатию.
Гидрогель SiO2 представляет собой систему сферических частиц, окруженных ионно-гидратными оболочками, правильно расположенными в объеме.
В процессе сушки в устьях пор между частицами гидрогеля образуются мениски и возникают капиллярные силы. Сопротивление сжатию обусловлено образованием связей (контактов) между первичными частицами. Наиболее прочными являются кристаллизационные контакты, наименее прочными – коагуляционные контакты.
136
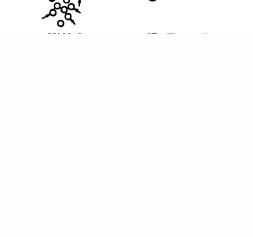
Кристаллизационные контакты обусловлены процессами зарастания. Процессу зарастания благоприятствует повышение температуры, увеличение длительности старения.
Различают три стадии процесса сушки гелей.
На первой стадии (рис. 38, а, б) происходит удаление жидкости с внешней поверхности зерна геля. Действие капиллярных сил приводит к всестороннему сжатию гранулы и уплотнению глобул и их агрегатов. На этой стадии наблюдается наиболее значительная усадка, что определяет величину пористости конечного продукта – ксерогеля. Когда сопротивление каркаса гидрогеля превысит силы капиллярного сжатия, фронт испарения переходит в объем гидрогеля и начинается вторая стадия сушки.
Рис. 38. Схема процессов, протекающих при сушке гидрогелей: а – д – последовательные стадии образования и перемещения менисков жидкой дисперсионной среды, стрелками показано направление действия капиллярных сил, двойные кружки – глобулы SiO2 с ионно-гидратными оболочками; е – стадия высокотемпературного спекания
На второй стадии сушки (рис. 38, в, г) фронт испарения перемещается в объем зерна. Происходит разрыв границы жидкости, и зерно разбивается на отдельные области, заполненные жидкостью. Число таких областей растет, размер их уменьшается. Капиллярные силы
137
возникают на границе областей (доменов). При уплотнении областей без объемной усадки зерна возникают крупные поры между доменами и мелкие поры внутри них.
На третьей стадии жидкофазные домены сохраняются лишь в местах контактов первичных частиц, в которых возможно кристаллизационное зарастание. На этой стадии сушки происходит разрушение сольватных оболочек, возможно сближение глобул.
Первый этап сушки определяет пористость, второй – распределение пор по размерам, третий – величину поверхности. Именно на третьей стадии возможно ее значительное уменьшение.
Приведем пример технологии катализатора, полученного методом осаждения.
Технология катализатора СТК-1
Катализатор СТК-1 используется в процессе высокотемпературной паровой конверсии СО, который проводится при 375–450 °С. Основой катализатора является магнетит Fe3O4, в который в качестве структурного промотора добавляют оксиды меди и хрома. В катализатор добавляются также небольшие количества оксидов алюминия и магния, которые играют роль текстурных промоторов. Формирование активного катализатора осуществляется в процессе восстановления исходной катализаторной массы смесью водорода и СО в присутствии водяного пара.
Исходная катализаторная масса имеет следующий состав,
мас. %: α-Fe2O3 – 75, Cr2O3 – 11, CuO – 3, Al2O3 – 5 и MgO – 6.
Выпускается катализатор в виде таблеток 5×5.
Сырьем в производстве катализатора СТК-1 являются нитрат железа (III), гидроксикарбонат меди (малахит), оксид хрома (VI), гидроксикарбонат магния и гидроксид алюминия. В качестве осадителя гидроксида железа используется аммиачная вода.
138
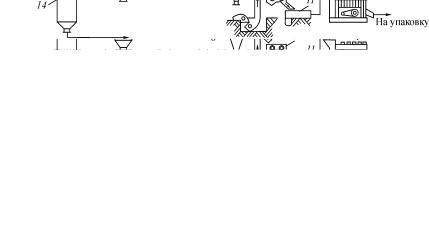
Процесс получения исходной катализаторной массы включает в себя следующие стадии: приготовление растворов нитрата железа и хромата меди, осаждение Fe(OH)3, смешение компонентов суспензии, сушка, приготовление массы и таблетирование.
В реакторе 1 (рис. 39) готовят раствор хромовой кислоты при 80–90 °С, затем медленно добавляют малахит. Параллельно в реакторе 2 готовят раствор нитрата железа. Осаждение Fe(OH)3 проводят в реакторе 3 при 60 °С, медленно при перемешивании добавляя в раствор нитрата железа аммиачную воду. Затем в декантаторе 5 отделяют осадок от раствора нитрата аммония и промывают водой. В реакторе 7 готовят суспензию гидроксидов и гидроксикарбоната магния, которую подают в распыпылительную сушилку 8. Сушку проводят при 400 °С в токе воздуха. Высушенный порошок поступает в смеситель, куда подают в качестве пластификатора графит. После смешения массу таблетируют в таблеточной машине 12.
|
|
|
|
|
|
|
|
|
|
|
|
|
|
|
|
|
|
|
|
Рис. |
39. Технологическая схема производства катализатора СТК-1: |
||
1, 2 |
– реакторы; 3 – реактор осаждения; 4 – насосы; 5 – декантатор; |
6, 14 – сборники; 7 – реактор-смеситель; 8 – распылительная сушилка; 9 – элеватор; 10 – бункер; 11 – смеситель; 12 – таблеточная машина;
13 – выпарной аппарат
139

При восстановлении исходной контактной массы в реакторе конверсии СО происходит переход α-Fe2O3 в Fe3O4, а оксиды меди и хрома образуют шпинель CuO Cr2O3, которая, в свою очередь, образует твердый раствор внедрения с Fe3O4.
4.1.11. Технология катализаторов, полученных нанесением
Преимущество этого метода заключается в том, что образуется меньше отходов, более эффективно используется активный реагент, метод прост. По этому методу процесс состоит из следующих стадий: 1) подготовка исходных веществ; 2) нанесение активного вещества на носитель; 3) сушка; 4) прокаливание (если нужно) с целью разложения или восстановления исходного вещества.
Существует три класса нанесенных катализаторов: адсорбцион-
ные, ионообменные и пропиточные. Часто первые два класса объе-
диняют под общим наименованием – сорбционные катализаторы. Пропиточными называют катализаторы, в которых взаимодействие между активным веществом и носителем мало и на стадии нанесения соединение находится в растворе в порах носителя. Бывают и промежуточные случаи, когда исходный компонент частично связан с носителем, а частично находится в порах его.
Отнесение катализатора к пропиточному или адсорбционному типу определяется величиной параметра Р, который следует из соотношения между количествами сорбированного активного компонента и компонента, остающегося в пористом пространстве в виде раствора
P = as Sуд ,
Vп cр
где аs – удельная величина сорбции, кг/м2, ср – средняя концентрация раствора в поровом пространстве, кг/м3.
При Р >> 1 имеем дело с сорбционным катализатором, при малом Р – с пропиточным.
140